锡珠的解决方案和分析
回流焊产生锡珠的原因及解决方案

回流焊产生锡珠的原因及解决方案在SMT生产工艺里面,经常会碰到经过回流焊过出来的板有锡珠,锡珠的产生,让产品的质量没有保证,让外观看起来不光滑。
那产生锡珠的主要原因是什么,我们又如何去解决它,这就是我今天写这篇文章的目的。
产生锡珠的主要原因是锡膏的问题。
详细分析请看下面分析。
焊锡珠现象是表面贴装生产中主要缺陷之一,它的直径约为0.2-0.4mm,主要集中出现在片状阻容元件的某一侧面,不仅影响板级产品的外观,更为严重的是由于印刷板上元件密集,在使用过程中它会造成短路现象,从而影响电子产品的质量。
因此弄清它产生的原因,并力求对其进行最有效的控制就显得犹为重要了。
焊锡珠产生的原因是多种因素造成的,在回流焊中的温度时间,焊膏的印刷厚度,焊膏的组成成分,模板的制作,贴片机贴装压力,外界环境都会在生产过程中各个环节对焊锡珠形成产生影响。
焊锡珠是在负责制板通过回流焊炉时产生的。
回流焊曲线可以分为四个阶段,分别为:预热、保温、回流和冷却。
预热阶段的主要目的是为了使印制板和上面的表贴元件升温到120-150度之间,这样可以除去焊膏中易挥发的溶剂,减少对元件的热振动。
因此,在这一过程中焊膏内部会发生气化现象,这时如果焊膏中金属粉末之间的粘结力小于气化产生的力,就会有少量焊膏从焊盘上流离开,有的则躲到片状阻容元件下面,再流焊阶段,温度接近曲线的峰值时,这部分焊膏也会熔化,而后从片状阻容元件下面挤出,形成焊锡珠,由它的形成过程可见,预热温度越高,预热速度越快,就会加大气化现象中飞溅,也就越容易形成锡珠。
因此,我们可以采取较适中的预热温度和预热速度来控制焊锡珠的形成。
焊膏的选用也影响着焊接质量,焊膏中金属的含量,回流焊焊膏的氧化物含量,焊膏中金属粉末的粒度,及焊膏在印制板上的印刷厚度都不同程度影响着焊锡珠的形成。
1:焊膏中的金属含量:焊膏中金属含量的质量比约为90-91%,体积比约为50%左右。
当金属含量增加时,焊膏的粘度增加,就能更有效地抵抗预热过程中气化产生的力。
波峰焊锡珠产生的原因及解决方案

波峰焊锡珠产生的原因及解决方案大家好,今天咱们聊聊波峰焊锡珠的事儿。
要说波峰焊,真的是电子制造中一个非常关键的环节。
它像是给咱们的电路板披上了一层“金色铠甲”,保护它不受外界的侵害。
但是,有时候,这个看似完美的过程会出现一些小麻烦,比如焊锡珠。
那么,这些焊锡珠到底是怎么来的呢?又该如何解决呢?接下来,就让咱们一探究竟吧。
1. 焊锡珠的成因1.1 焊接温度过高首先,我们得知道,焊锡珠通常是在焊接过程中出现的。
第一个大头原因就是焊接温度太高。
想象一下,你在厨房里做菜,火开得太猛,油锅里就会冒油花儿,烫得你跳脚。
波峰焊的情况也是类似,如果焊接温度过高,焊锡在碰到电路板的时候就容易挥发,导致焊锡珠的产生。
过高的温度不仅让焊锡液体挥发,还可能影响到板子的质量,简直就是一场灾难!1.2 焊锡液体过多再有一个原因就是焊锡液体的量过多。
就像你做饭时加了过多的盐,结果整锅饭都咸了。
在波峰焊中,如果焊锡液体的量过多,也会导致焊锡珠的产生。
这是因为焊锡液体在焊接过程中不能完全被板子吸收,最终就会形成多余的小珠子,挂在电路板上,这看起来真是让人哭笑不得。
2. 焊锡珠的解决方案2.1 调整焊接温度知道了问题的根源,咱们也有解决的办法。
首先要做的就是调整焊接温度。
试着把焊接温度降低一点点,看看效果如何。
焊接温度一般在240°C到260°C之间比较合适,大家可以根据自己的实际情况微调一下。
温度过高可不是好事,得适中才行。
你要记住,温度调得太高,锡珠飞溅,调得太低,又可能导致焊接不良,找准那个平衡点,才能让焊锡珠远离你的电路板。
2.2 控制焊锡液体量其次,焊锡液体的量也要控制好。
如果焊锡液体过多,就像是汤锅里的水太多,容易溢出来。
你可以通过调整焊锡槽的液面高度来控制焊锡的量。
合适的液体量不仅可以有效减少焊锡珠的产生,还能保证焊接的质量。
所以,控制好液体量也是非常关键的一个环节。
3. 板子的处理3.1 保持电路板干净除了以上两点,还得保证电路板的干净整洁。
PCB波峰焊后板面锡珠分析改善

PCB波峰焊后板面锡珠分析改善
一、PCB波峰焊后板面锡珠分析
1.由PCB波峰焊机产生的锡珠分析
PCB波峰焊机是一种智能电子焊接加工设备,它能够完成PCB板直角
双面焊接,也可以进行其他形状的焊接。
由于波峰焊机采用的是锡珠焊接
方式,因此波峰焊机产生的锡珠质量是影响焊接效果的重要因素,主要有
以下几方面:
(1)锡珠的质量和大小:锡珠的质量直接影响芯片安装的质量,而
大小则直接影响焊点的质量和表面完整性;
(2)焊点温度和焊接时间:焊接过程的温度和时间是影响焊接质量
的因素,若焊点温度过高或焊接时间过长,会使焊点出现裂纹和烧毁现象;
(3)抽灰膨胀率:在进行焊接时,由于抽灰膨胀率受温度变化而受
影响,并会使焊接条件变化从而影响焊接效果。
2.PCB波峰焊后板面锡珠分析
(1)高度稳定的锡珠:这类锡珠的高度和重量基本保持一致,在焊
后的表面上通常无明显的排列不整齐现象;
(2)宽小稳定的锡珠:此类锡珠比较均匀,在焊后的表面上能够看
到稍大一些的锡珠,但是也不会出现太大的不平整现象;。
锡珠的产生原因与解决措施

波峰焊接中溅锡珠的形成原因⑴ “小爆炸”理论波峰焊接中在 PCB 的焊接面及元件面上均可能产生锡珠飞溅现象。
普遍认为在 PCB 进入波峰之前有水汽滞留在PCB上的话,一旦与波峰钎料接触,在剧烈升温的过程中,就会在极短的时间内迅速汽化变成蒸汽,发生爆发性的排气过程。
正是这种剧烈的排气可能引发正处在熔融状态中的焊接点内部的小爆炸,从而促使钎料颗粒在脱离波峰时飞溅在PCB上形成锡珠。
在波峰焊接前PCB水汽的来源,杭州东方通信公司对此进行过专题研究和试验,归纳的结论如下:① 制造环境和PCB存放时间制造环境对电子装联的焊接质量有着很大的影响。
制造环境的湿度较重,或PCB包装开封较长时间后再进行贴片和波峰焊生产,或者PCB贴片、插装后放置一段时间后再进行波峰焊,这些因素都很有可能使PCB在波峰焊接过程中产生锡珠。
如果制造环境的湿度太大,在产品制造过程中空气浮动着水汽很容易会在PCB表面凝结,使PCB通孔中凝结有水珠,在过波峰焊时,通孔中的水珠经过预热温区后可能还没有完全挥发完,这些没有挥发完的水珠接触到波峰的焊锡时,经受了高温,就会在短时间内汽化变成蒸汽,而此时正是形成焊点的时候,水汽就会在焊料内产生空隙,或挤出焊料产生锡球。
严重的话就会形成一个爆点,并在它的周围分布有被吹开的细小的锡珠。
假如PCB在包装开封较长时间后再进行贴片和波峰焊,通孔中也会凝结有水珠;PCB完成贴片后或插装完成后放置了一段时间,也会凝结水珠。
同样的原因,这些水珠都有可能在波峰焊过程中导致锡珠产生。
因而,作为从事电子装联的企业,对制造环境的要求和对产品制造过程中的时间安排显得特别地重要。
贴片完成后的PCB应在24小时内完成插装并进行波峰焊,假如天气晴朗干燥,可以在48小时内完成。
② PCB阻焊材料和制作质量在PCB制造过程中所使用的阻焊膜也是波峰焊产生锡球的原因之一。
因为阻焊膜与助焊剂有一定的亲合性,阻焊膜加工不良常常会引起锡珠粘附,产生焊锡球。
锡珠产生的原因分析
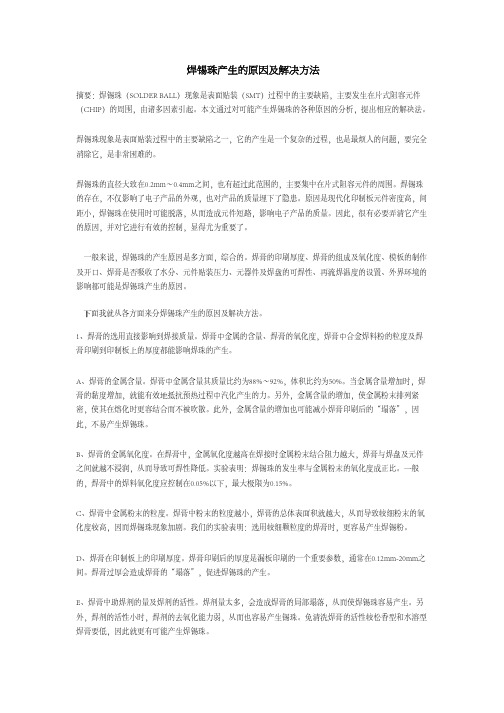
焊锡珠产生的原因及解决方法摘要:焊锡珠(SOLDER BALL)现象是表面贴装(SMT)过程中的主要缺陷,主要发生在片式阻容元件(CHIP)的周围,由诸多因素引起。
本文通过对可能产生焊锡珠的各种原因的分析,提出相应的解决法。
焊锡珠现象是表面贴装过程中的主要缺陷之一,它的产生是一个复杂的过程,也是最烦人的问题,要完全消除它,是非常困难的。
焊锡珠的直径大致在0.2mm~0.4mm之间,也有超过此范围的,主要集中在片式阻容元件的周围。
焊锡珠的存在,不仅影响了电子产品的外观,也对产品的质量埋下了隐患。
原因是现代化印制板元件密度高,间距小,焊锡珠在使用时可能脱落,从而造成元件短路,影响电子产品的质量。
因此,很有必要弄清它产生的原因,并对它进行有效的控制,显得尤为重要了。
一般来说,焊锡珠的产生原因是多方面,综合的。
焊膏的印刷厚度、焊膏的组成及氧化度、模板的制作及开口、焊膏是否吸收了水分、元件贴装压力、元器件及焊盘的可焊性、再流焊温度的设置、外界环境的影响都可能是焊锡珠产生的原因。
㆘面我就从各方面来分焊锡珠产生的原因及解决方法。
1、焊膏的选用直接影响到焊接质量。
焊膏中金属的含量、焊膏的氧化度,焊膏中合金焊料粉的粒度及焊膏印刷到印制板上的厚度都能影响焊珠的产生。
A、焊膏的金属含量。
焊膏中金属含量其质量比约为88%~92%,体积比约为50%。
当金属含量增加时,焊膏的黏度增加,就能有效地抵抗预热过程中汽化产生的力。
另外,金属含量的增加,使金属粉末排列紧密,使其在熔化时更容结合而不被吹散。
此外,金属含量的增加也可能减小焊膏印刷后的“塌落”,因此,不易产生焊锡珠。
B、焊膏的金属氧化度。
在焊膏中,金属氧化度越高在焊接时金属粉末结合阻力越大,焊膏与焊盘及元件之间就越不浸润,从而导致可焊性降低。
实验表明:焊锡珠的发生率与金属粉末的氧化度成正比。
一般的,焊膏中的焊料氧化度应控制在0.05%以下,最大极限为0.15%。
C、焊膏中金属粉末的粒度。
锡珠的产生原因及解决方法

锡珠的产生原因及解决方法锡珠的产生原因及解决方法锡珠现象是smt过程中的主要缺陷,主要发生在片式阻容元件的周围,由诸多因素引起。
它的产生是一个复杂的过程,也是最烦人的问题,要完全消除它,是非常困难的。
锡珠的直径大致在0.2mm——0.4mm之间,也有超过此范围的。
锡珠的存在,不仅影响了电子产品的美观,对产品的质量也有极大的隐患。
我们都知道现在smt工艺中的元件间距小,密度高,若是锡珠在使用时脱落,就可能造成元件短路,影响电子产品的质量。
因此,弄清锡珠产生的原因,并对它进行有效的控制,显得尤为重要了。
锡珠的产生原因是多方面造成的。
锡膏的印刷厚度、其组成及氧化度、模板的制作及开口都有可能造成锡珠现象,同时锡膏是否吸收了水分、元件贴装压力、元器件及焊盘的可焊性、再流焊温度的设置、外界环境的影响都可能是锡珠产生的原因。
下面吉田店铺就从各方面来分锡珠产生的原因及解决方法。
1、锡膏的金属氧化度。
在锡膏中,金属氧化度越高在焊接时金属粉末结合阻力越大,锡膏与焊盘及元件之间就越不浸润,从而导致可焊性降低。
锡珠的发生率与金属粉末的氧化度成正比。
一般的,锡膏中的焊料氧化度应控制在0.05%以下,最大极限为0.15%。
2、锡膏在印制板上的印刷厚度。
锡膏印刷后的厚度是漏板印刷的一个重要参数,通常在0.12mm——0.20mm之间。
锡膏过厚会造成锡膏“塌边”,促进锡珠的产生。
3、锡膏中助焊剂的量及焊剂的活性。
焊剂量太多,会造成锡膏的局部塌落,从而使锡珠容易产生。
另外,焊剂的活性小时,焊剂的去氧化能力弱,从而也容易产生锡珠。
免清洗锡膏的活性较松香型和水溶型锡膏要低,因此就更有可能产生锡珠。
4、此外,锡膏在使用前,一般冷藏在冰箱中,取出来以后应该使其恢复到室温后打开使用,否则,锡膏容易吸收水分,在再流焊锡飞溅而产生锡珠。
58回流焊中锡珠形成的原因及解决方法介绍|南昌回流焊原理2017-03-22 12:44 | #2楼波峰焊第一品牌【精极科技】深圳市精极科技有限公司成立于2002年8月,是一家以设计、生产、销售等工业仓储设备及柔性生产线设备为主的专业生产厂家,同时分销配套的防静电周边产品。
PCB波峰焊后板面锡珠分析改善
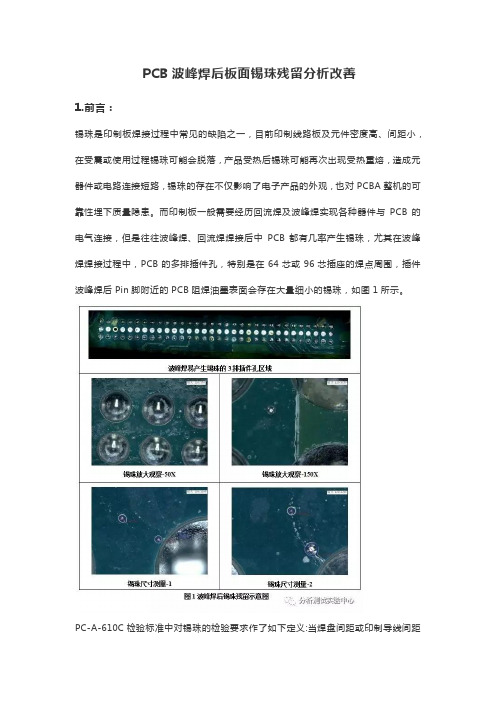
PCB波峰焊后板面锡珠残留分析改善1.前言:锡珠是印制板焊接过程中常见的缺陷之一,目前印制线路板及元件密度高、间距小,在受震或使用过程锡珠可能会脱落,产品受热后锡珠可能再次出现受热重熔,造成元器件或电路连接短路,锡珠的存在不仅影响了电子产品的外观,也对PCBA整机的可靠性埋下质量隐患。
而印制板一般需要经历回流焊及波峰焊实现各种器件与PCB的电气连接,但是往往波峰焊、回流焊焊接后中PCB都有几率产生锡珠,尤其在波峰焊焊接过程中,PCB的多排插件孔,特别是在64芯或96芯插座的焊点周围,插件波峰焊后Pin脚附近的PCB阻焊油墨表面会存在大量细小的锡珠,如图1所示。
PC-A-610C检验标准中对锡珠的检验要求作了如下定义:当焊盘间距或印制导线间距的尺寸为0.13mm时,锡珠直径不能超过0.13mm,或者在600mm范围内不能出现超过5个锡珠。
如图1,波峰焊生产后锡珠的直径存在一定的差异性,较小锡珠的直径在50μm左右,而较大的锡珠直径可达到185μm(超过标准要求0.13mm),如果不在波峰焊后对锡珠进行人工清理,锡珠的数量难以直接符合IPC-A-610C的接收标准要求。
波峰焊锡珠的残留降低了焊接的质量,增加了检验和返修的人工费用。
假如出厂的PCBA还存在着没有被检查出来的锡珠,有可能会影响设备的正常运行,而引起严重后果。
2.锡珠的粘附分析:锡珠的残留是由于阻焊油墨与锡珠间发生结合,所以锡珠残留机理分析的第一步应当对锡珠的结合界面观察分析。
使用扫描电镜观察锡珠微观形貌,使用X射线能谱仪对锡珠表面进行EDS元素分析,结果如图2所示。
由图2可知,测试板经波峰焊后,在扫描电镜的背散射成像模式下(样品成分信息观察),锡珠表面与阻焊表面均存在一层黑色异物,经元素分析未发现主要特征元素为C、O、Al、S、Cl、Cu、Sn,C(碳)含量(75.02%)、O(氧)含量(21.12%)明显偏高,说明黑色异物可能为波峰焊后锡珠表面残留的助焊剂。
解决锡珠的办法

解决锡珠的办法
从业SMT工艺的朋友最困扰的不良问题估计就是锡珠了,绝大部份是因为"pad尺寸/钢板开窗/零件焊脚三者的不匹配所造成的.简而言之,就是鍚太多了,零件与pad不需要的就会变成鍚珠.尤其是零件底部的鍚膏,没必要的,不需要太多.
其次,就是鍚膏(吸湿,回温不足)或者pcb(HASL PTH内残鍚)所造成的问题,但是这种的现象与上面鍚太多的现象不同,鍚珠会以散布的方式呈现,上面pad尺寸/钢板开窗/零件焊脚三者的不匹配的鍚珠则者会在零件旁依偎式的躲在零件边,很容易分辨的.
造成锡珠的原因:
1.锡膏回温时温湿度不达标,锡膏回温时间不够
2.PCB拆封时间过长,导致PCB受潮,生産过炉时産生锡珠,
3.锡膏印刷厚度偏标准上限,印刷偏移,印刷的不良品,洗板后残留锡粉
4.钢板开口数据有误,人员擦拭钢板时,在湿擦的过程中未能待清洁水完全挥发即开始印锡,造成锡膏扩散
5.人员抹到已印好锡膏的PCB,造成锡膏扩散
6.元件PART DATA高度设定不对,置件速度过快,造成置件压力过大
7.手摆元件造成印锡扩散,元件PAD设置与元件类型不符合
8.回流炉升温斜率过高,恒温时间过长。
- 1、下载文档前请自行甄别文档内容的完整性,平台不提供额外的编辑、内容补充、找答案等附加服务。
- 2、"仅部分预览"的文档,不可在线预览部分如存在完整性等问题,可反馈申请退款(可完整预览的文档不适用该条件!)。
- 3、如文档侵犯您的权益,请联系客服反馈,我们会尽快为您处理(人工客服工作时间:9:00-18:30)。
锡珠的解决方案和分析
焊锡珠现象是表面贴装过程中的主要缺陷之一,它的产生是一个复杂的过程,也是最烦人的问题,要完全消除它,是非常困难的。
焊锡珠的直径大致在0.2mm~0.4mm之间,也有超过此范围的,主要集中在片式阻容元件的周围。
焊锡珠的存在,不仅影响了电子产品的外观,也对产品的质量埋下了隐患。
原因是现代化印制板元件密度高,间距小,焊锡珠在使用时可能脱落,从而造成元件短路,影响电子产品的质量。
因此,很有必要弄清它产生的原因,并对它进行有效的控制,显得尤为重要了。
一般来说,焊锡珠的产生原因是多方面,综合的。
焊膏的印刷厚度、焊膏的组成及氧化度、模板的制作及开口、焊膏是否吸收了水分、元件贴装压力、元器件及焊盘的可焊性、再流焊温度的设置、外界环境的影响都可能是焊锡珠产生的原因。
下面我就从各方面来分焊锡珠产生的原因及解决方法。
焊膏的选用直接影响到焊接质量。
焊膏中金属的含量、焊膏的氧化度,焊膏中合金焊料粉的粒度及焊膏印刷到印制板上的厚度都能影响焊珠的产生。
A、焊膏的金属含量。
焊膏中金属含量其质量比约为88%~92%,体积比约为50%。
当金属含量增加时,焊膏的黏度增加,就能有效地抵抗预热过程中汽化产生的力。
另外,金属含量的增加,使金属粉末排列紧密,使其在熔化时更容结合而不被吹散。
此外,金属含量的增加也可能减小焊膏印刷后的″
塌落″,因此,不易产生焊锡珠。
B、焊膏的金属氧化度。
在焊膏中,金属氧化度越高在焊接时金属粉末结合阻力越大,焊膏与焊盘及元件之间就越不浸润,从而导致可焊性降低。
实验表明:焊锡珠的发生率与金属粉末的氧化度成正比。
一般的,焊膏中的焊料氧化度应控制在0.05%以下,最大极限为0.15%。
C、焊膏中金属粉末的粒度。
焊膏中粉末的粒度越小,焊膏的总体表面积就越大,从而导致较细粉末的氧化度较高,因而焊锡珠现象加剧。
我们的实验表明:选用较细颗粒度的焊膏时,更容易产生焊锡粉。
D、焊膏在印制板上的印刷厚度。
焊膏印刷后的厚度是漏板印刷的一个重要参数,通常在0.12mm-2.0mm之间。
焊膏过厚会造成焊膏的″塌落″,促进焊锡珠的产生。
E、焊膏中助焊剂的量及焊剂的活性。
焊剂量太多,会造成焊膏的局部塌落,从而使焊锡珠容易产生。
另外,焊剂的活性小时,焊剂的去氧化能力弱,从而也容易产生锡珠。
免清洗焊膏的活性较松香型和水溶型焊膏要低,因此就更有可能产生焊锡珠。
F、此外,焊膏在使用前,一般冷藏在冰箱中,取出来以后应该使其恢复到室温后打开使用,否则,焊膏容易吸收水分,在再流焊锡飞溅而产生焊锡珠。
2、模板的制作及开口。
我们一般根据印制板上的焊盘来制作模板,所以模板的开口就是焊盘的大小。
在印刷焊膏时,容易把焊膏印刷到阻焊层上,从而在再流焊时产生焊锡珠。
因此,我们可以这样来制作模板,把模板的开口比焊盘的实际尺寸减小10%,另外,可以更改开口的外形来达到理想的效果。
上图是几种推荐的焊盘设计:
模板的厚度决了焊膏的印刷厚度,所以适当地减小模板的厚度也可以明显改善焊锡珠现象。
我们曾经进行过这样的实验:起先使用0.18mm厚的模板,再流焊后发现阻容元件旁边的焊锡珠比较严重,后来,重新制作了一张模板,厚度改为0.15mm,开口形式为上面图中的前一种设计,再流焊基本上消除了焊锡珠。
件贴装压力及元器件的可焊性。
如果在贴装时压力太高,焊膏就容易被挤压到元件下面的阻焊层上,在再流焊时焊锡熔化跑到元件的周围形成焊锡珠。
解决方法可以减小贴装时的压力,并采用上面推荐使用的模板开口形式,避免焊膏被挤压到焊盘外边去。
另外,元件和焊盘焊性也有直接影响,如果元件和焊盘的氧化度严重,也会造成焊锡珠的产生。
经过热风整平的焊盘在焊膏印刷后,改变了焊锡与焊剂的比例,使焊剂的比例降低,焊盘越小,比例失调越严重,这也是产生焊锡珠的一个原因。
再流焊温度的设置。
焊锡珠是在印制板通过再流焊时产生的,再流焊可分为四个阶段:预热、保温、再流、冷却。
在预热阶段使焊膏和元件及焊盘的温度上升到120C-150C之间,减小元器件在再流时的热冲击,在这个阶段,焊膏中的焊剂开始汽化,从而可能使小颗粒金属分开跑到元件的底下,在再流时跑到元件周围形成焊锡珠。
在这一阶段,温度上升不能太快,一般应小于1.50C/s,过快容易造成焊锡飞溅,形成焊锡珠。
所以应该调整再流焊的温度曲线,采取较适中的预热温度和预热速度来控制焊锡珠的产生。
外界因素的影响。
一般焊膏印刷时的最佳温度为25C+3C,湿度为相对湿度60%,温度过高,使焊膏的黏度降低,容易产生″塌落″,湿度过模高,焊膏容易吸收水分,容易发生飞溅,这都是引起焊锡珠的原因。
另外,印制板暴露在空气中较长的时间会吸收水分,并发生焊盘氧化,可焊性变差,可以在120C-150C的干燥箱中烘烤12-14h去除水汽。
综上可见,焊锡珠的产生是一个极复杂的过程,我们在调整参数时应综合考虑,在生产中摸索经验,达到对焊锡珠的最佳控制。