陶瓷成型工艺
第四章 陶瓷工艺学 成型

颗粒大小和形状
一般地说颗粒愈细则比表面愈大,每个颗粒表面形成
水膜所需的水分愈多。此外,由细颗粒堆积而形成的毛细管 半径越小,产生的毛细管力越大,可塑性越高。 不同形状颗粒的比表面积是不同的,因而对可塑性的影 响也有差异。
液相数量和性质
可塑法成型基于坯 料有可塑性,成型 方法有雕塑、拉坯、 印坯、旋压、按压、
第一节 一、可塑成型工艺原理
可塑成型
(一)可塑泥团的成型性能
固相、液相及少量气相组成的弹性 —塑性系统。当 泥团受到外力作用而发生变形时,既有弹性性质又有 假塑性性质。生产中控制的两个重要参数:屈服值和 最大变形量。
应 力
σ
(二)成形工艺对流变特性的要求
泥料的流变特性,在成形工艺中,决定着泥料 的成形能力及其操作适应性,并通过屈服值和延展 量这两个重要参数进行描述。
注射、挤制、压制、
车坯和轧膜等操作
法。
三、旋压成形
1. 成形过程 旋压成形也称刀压成形。它是利用型刀和石膏模型进 行成形的一种方法。
成形时,取定量的可塑泥料,投入旋转的石膏模中, 然后将型刀慢慢压入泥料。由于型刀与旋转着的模型存
在相对运动,因此型刀以压挤和刮削的作用机理,随着
模型的旋转而把坯泥沿着石膏模型的工作面上展开形成
结构均匀,有一定的致密度;
成型过程应能多、快、好、省的组织生产。
成型是陶瓷生产过程的一个重要步骤。在成 型过程中形成的某些缺陷(如不均匀性等)仅靠烧结 工艺的改进是难以克服的。成型工艺已经成为制备 高性能陶瓷材料的关键技术,它对提高陶瓷材料的 均匀性、重复性和成品率,降低陶瓷制造成本具有
十分重要的意义。
第四章 成 型
陶瓷粉末成型工艺

陶瓷粉末成型工艺
陶瓷粉末成型工艺是一种将陶瓷粉末通过特定工艺加工成所需形状和尺寸的过程。
它通常涉及将粉末与有机粘结剂混合,然后通过压制或注射成型等方法获得具有一定形状和密度的坯体。
在陶瓷粉末成型工艺中,首先需要将陶瓷粉末与有机粘结剂进行混合,以便将粉末粘结在一起形成具有一定形状和强度的坯体。
这个过程中,需要根据粉末的特性和所需的坯体形状选择合适的有机粘结剂,并进行适量的添加。
接下来,将混合好的陶瓷粉末和有机粘结剂进行压制或注射成型。
压制成型是一种传统的陶瓷成型工艺,通过将混合好的料浆倒入模具中,然后施加压力使料浆成型。
注射成型则是一种较新的成型工艺,通过将混合好的料浆注入模具中,利用注射机的压力使料浆在模具内流动并充满整个模腔。
在成型过程中,需要控制压力、温度等工艺参数,以确保坯体具有足够的强度和尺寸精度。
同时,还需要注意防止出现开裂、气泡等缺陷。
最后,将成型的坯体进行脱脂和烧成处理。
脱脂是将坯体中的有机物排除的过程,通常需要在一定的温度和气氛下进行。
烧成是将脱脂后的坯体在高温下进行烧结的过程,以获得具有所需性能的陶瓷制品。
总之,陶瓷粉末成型工艺是一种复杂的制造过程,需要经过多道工序和严格的质量
控制才能获得高质量的陶瓷制品。
第四章 陶瓷工艺学 成型
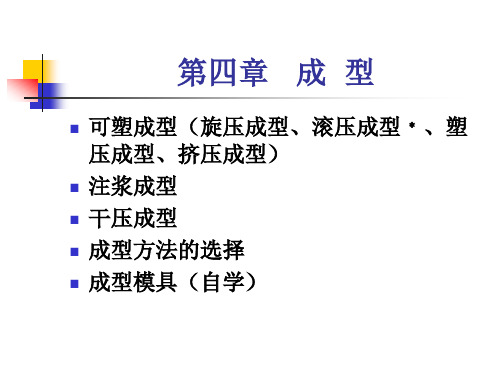
滚压过程的要求
滚压过程是指滚压头从开始接触泥料至离开坯体 表面的一段过程。这一过程所经过的时间只有几秒钟。 通常把这一短暂过程分为3个阶段,而各个阶段对压泥 的要求并不相同。
滚压过程的三个阶段:
布泥阶段:滚压头从开始接触泥料至定压前。泥料在模型 工作面上展布,要求滚压头的动作要轻,压泥速度要适当, 一般以6~7mm/s 为宜。如动作太重或速度过快则会压坏 模型或引起“鼓气”。若下压太慢,泥料容易粘住滚头。
成型就是将制备好的坯料用各种方法加工成具有一 定形状和尺寸的坯件(生坯)半成品。成型工序应满足 以下要求:
形状、尺寸(根据收缩率经过放尺后的尺寸); 一定的机械强度,以保证后继工序的进行; 结构均匀,有一定的致密度; 成型过程应能多、快、好、省的组织生产。
成型是陶瓷生产过程的一个重要步骤。在成 型过程中形成的某些缺陷(如不均匀性等)仅靠烧结 工艺的改进是难以克服的。成型工艺已经成为制备 高性能陶瓷材料的关键技术,它对提高陶瓷材料的 均匀性、重复性和成品率,降低陶瓷制造成本具有 十分重要的意义。
水量小些;
• 阳模滚压:水分少些、延伸性好(即变形量大些) • 阴模滚压:可塑性可稍差些,水分稍多 • 冷滚压:水分要少,可塑性要好 • 热滚压:要求不严
滚压头的温度:冷滚压和热滚压(120℃左右)
热滚和冷滚的工艺特点
热滚的滚头内部有电阻丝加热,用调压器调节温度, 加热的滚头与坯泥接触,能在表面产生一层蒸汽膜, 避免坯泥粘附滚头。滚头材料大都采用铸铁和普通 碳素钢,耐磨性较好,但滚头结构较复杂,维修操 作较麻烦,工人操作条件差,这是它的不足之处。
注射成型(Injection Molding)
注射成型可成型尺寸精度高、形状比较复杂的陶瓷部 件,易于自动化和大规模生产。
陶瓷挤出成型具体工艺

陶瓷挤出成型具体工艺
一、引言
陶瓷是一种古老而又神秘的材料,它的制作工艺也是千姿百态。
其中,陶瓷挤出成型工艺是一种常见的制作方法,它可以制作出各种形状的
陶瓷制品。
本文将详细介绍陶瓷挤出成型的具体工艺。
二、材料准备
在进行陶瓷挤出成型之前,需要准备好以下材料:
1.陶瓷粉末:根据需要制作的陶瓷制品的种类和规格,选择不同种类和粒度的陶瓷粉末。
2.添加剂:根据陶瓷粉末的特性和制品的要求,添加适量的助剂、增塑剂、润滑剂等。
3.水:用于制作陶瓷粉末的浆料。
4.挤出机:用于将陶瓷浆料挤出成型。
三、工艺流程
1.将陶瓷粉末和添加剂混合均匀,加入适量的水,制成陶瓷浆料。
2.将陶瓷浆料倒入挤出机的料斗中。
3.调整挤出机的压力和速度,将陶瓷浆料挤出成型。
4.将挤出成型的陶瓷制品放置在通风处晾干。
5.进行烧结处理,将陶瓷制品放入窑中进行高温烧结,使其变得坚硬、耐磨、耐高温。
四、注意事项
1.陶瓷粉末的选择和添加剂的使用要根据制品的要求进行调整,以保证制品的质量。
2.挤出机的压力和速度要适当,过高或过低都会影响制品的成型效果。
3.挤出成型后的陶瓷制品要放置在通风处晾干,以免出现开裂等问题。
4.烧结处理时,要根据陶瓷制品的种类和规格进行调整,以保证其质量和性能。
五、结语
陶瓷挤出成型是一种常见的陶瓷制作工艺,它可以制作出各种形状的
陶瓷制品。
在进行制作时,需要注意材料的选择和工艺流程的掌握,以保证制品的质量和性能。
希望本文能够对读者了解陶瓷挤出成型工艺有所帮助。
陶瓷成型工艺的方法有哪些

陶瓷成型工艺的方法有哪些
陶瓷成型工艺的方法包括:
1. 传统手工成型:通过手工捏、塑、切、揉等方式将陶土制成各种形状,如捏制、轮盘成型等。
2. 注模成型:将陶土糊状物注入模具中,经模具挤压、振动等工艺得到成型品。
常用的注模方法有挤压注模、振动注模等。
3. 轮压成型:将陶土放在陶轮上进行旋转,并利用手工或机械进行压制以得到成型品。
4. 模压成型:将陶土糊状物放在模具中,通过压制形成所需形状。
5. 粘土成型:使用粘土等材料通过模具粘结成型,如粘土胚、粘土模等。
6. 流延成型:将陶瓷糊状物放在提供有形状的流延板上,在板上形成所需厚度后,通过刮板或滚筒等工具将其刮平并使其具有一定的形状。
第21章 陶瓷成型工艺

第21章 陶瓷成型工艺成型方法的选择,首先取决于原料的性质,其次取决于制品的形状和大小。
陶瓷粉末首先经过预处理,然后再成型。
§21.1 预处理21.1.1 配料配料是陶瓷工艺中一道最基本的工序。
尽管这道工序比较简单,但它与以后各道工序直接有关,必须认真对待。
陶瓷组成稍有偏离,对一般陶瓷制品可能关系不大,但对电子陶瓷来说,影响却是很大的,这些影响会非常敏感地在组织结构上反映出来,而影响材料的介电性能。
在电子陶瓷工艺上,尤其是需要掺杂的陶瓷,有两个地方需要配料,其一是在原料烧块合成之前,其二是在成型之前。
原料烧块合成之前,多半是按化学分子式进行计算,称量配料。
成型之前,多半是按规定的瓷料的百分重量组成进行称量配料。
从普通化学知道:物质的重量(克)=该物质的克分子数⨯该物质的分子量,其中克分子数在化学分子式中注明,至于分子量可以从周期表上先查出原子量,然后按分子式加起来即可。
有了克分子数和分子量,就可以求出各原料的重量了。
为了配制任意重量的瓷料,对我们有意义的是各种原料的重量百分比。
设各原料的重量分别为w i ,各原料的克分子数分别为x i ,各原料的分子量分别M i ,那么我们就可以求出各原料的重量i i i M x w =有了各原料的重量,就可以求出各原料的重量百分比了。
设重量百分比为y i%100/⨯=∑ii i w w y 只要y 的总和非常接近于100,就可证明没有算错。
上面的料方计算,还要说明两点。
其一,原料是按纯度为100%设想,但一般原料都没有这么纯,有96%,有98%的不等,因此在计算时还要根据原料的纯度,换算成实际的原料重量。
设实际的原料重量为w ’,纯度为p 时,那么p w w /'=除了原料的纯度外,原料中多少还含有一些水分,如果称量前原科不是烘得很干的话要加以扣除,有些原料特别容易吸水,称量更要小心。
上面谈的是按化学分子式计算料方时的情况,实际的瓷料组成有的比较简单,有的比较复杂—除了主成分而外,还有很多加入物。
陶瓷成型工艺流程

陶瓷成型工艺流程
《陶瓷成型工艺流程》
陶瓷成型工艺是指将原料经过一系列的加工工序,最终成为陶瓷制品的过程。
其中,成型工艺是整个陶瓷制作过程中的重要一环,直接影响着陶瓷制品的成型质量和外观。
首先,成型工艺的第一步是原料的准备。
一般陶瓷的原料包括粘土、石英砂、长石等,这些原料要经过混合、过筛等工序,确保原料的均匀性和杂质的去除。
接下来是成型工艺的制胚工序。
这一步通常包括挤压成型、注塑成型、手工成型等工艺。
其中,挤压成型是利用成型机将原料挤压成一定形状的坯体,注塑成型是将原料注入成型模具中进行成型,而手工成型则是通过手工操作将原料成型为所需的形状。
不同的成型方式会直接影响到陶瓷制品的成型质量和成本。
成型工艺的下一步是干燥工序。
这一步是为了将成型后的坯体中的水分蒸发干净,使得坯体可以进一步进行烧制工序。
通常会采用自然晾晒或者利用烘干设备进行干燥处理。
最后,成型工艺的最后一步是修整工序。
这一步包括修整坯体表面、刻花、打磨等工序,使得坯体表面更加光滑,符合设计要求。
总的来说,《陶瓷成型工艺流程》是一个包括原料准备、制胚、
干燥和修整工序的系统工艺流程。
通过严谨的工艺流程和精细的操作,可以制作出高质量的陶瓷制品。
陶瓷注浆成型工艺流程
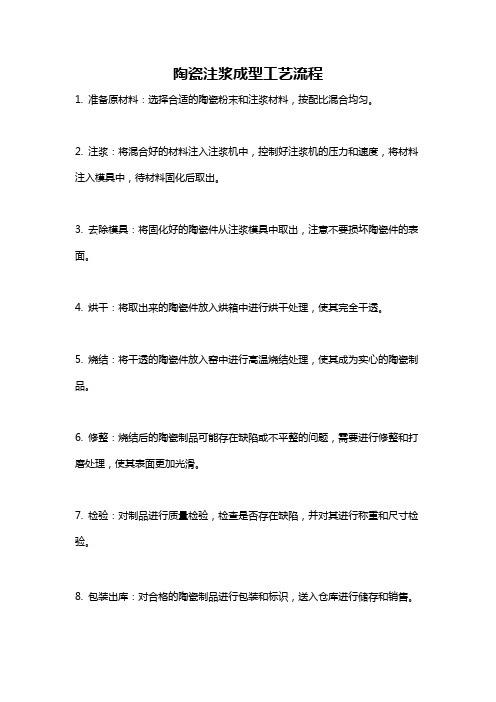
陶瓷注浆成型工艺流程
1. 准备原材料:选择合适的陶瓷粉末和注浆材料,按配比混合均匀。
2. 注浆:将混合好的材料注入注浆机中,控制好注浆机的压力和速度,将材料注入模具中,待材料固化后取出。
3. 去除模具:将固化好的陶瓷件从注浆模具中取出,注意不要损坏陶瓷件的表面。
4. 烘干:将取出来的陶瓷件放入烘箱中进行烘干处理,使其完全干透。
5. 烧结:将干透的陶瓷件放入窑中进行高温烧结处理,使其成为实心的陶瓷制品。
6. 修整:烧结后的陶瓷制品可能存在缺陷或不平整的问题,需要进行修整和打磨处理,使其表面更加光滑。
7. 检验:对制品进行质量检验,检查是否存在缺陷,并对其进行称重和尺寸检验。
8. 包装出库:对合格的陶瓷制品进行包装和标识,送入仓库进行储存和销售。
- 1、下载文档前请自行甄别文档内容的完整性,平台不提供额外的编辑、内容补充、找答案等附加服务。
- 2、"仅部分预览"的文档,不可在线预览部分如存在完整性等问题,可反馈申请退款(可完整预览的文档不适用该条件!)。
- 3、如文档侵犯您的权益,请联系客服反馈,我们会尽快为您处理(人工客服工作时间:9:00-18:30)。
粒度和粒度分布 压制大的坯件,粒料可适当粗些,较
小的坯件,粒料需稍细。粒度不当,成型 的坯件密度低,强度差。粒料过细,坯件 易出现起层(层裂)现象。 粒料的流动性
粒料的自然息角α越小,流动性越好。
第十三章成型原理与成型技术
13.3.2干压成型方法 (1)单向加压 (2)双向加压
13.3.3干压成型应注意的问题 坯件的密度称为成型密度。成型密度
愈均匀愈好。 控制因素: (1)成型压力的大小 (2)加压速度与保压时间
第十三章成型原理与成型技术
13.3.4干压成型的特点
由于坯料中含水或其它粘合剂比较少,干压 成型的坯体致密度高,尺寸比较精确,烧成收缩 小,瓷件的机械强度高,电性能好。主要用于圆 形、薄片状的简单形状制品。
第十三章成型原理与成型技术
13.4.3热等静压成型 对坯体加温加压同时进行,陶瓷致密度
更高.特点:
(1)适于压制形状复杂、大件且细长的新型 陶瓷制品。 (2)湿式等静压容器内可同时放入几个模具, 压制不同形状的坯体。 (3)可以任意调节成型压力。 (4)压制产品质量高,烧成收缩小,坯件致 密,不易变形。 (5)设备成本高,湿式等静压成型不易自动 化生产,生产效率不高。
第十三章成型原理与成型技术
第十三章成型原理与成型技术
13.1 注浆成型
它是利用石膏吸水性的一种成形方法。 此法适于生产一些形状复杂且不规则、 外观尺寸要求不严格、壁薄及大型厚胎 的制品。
对注浆成型所用的料浆,必须具备如 下性能:
流动性、稳定性(即不易沉淀和分 层)、触变性要小、含水量尽可能少、 渗透性要好、脱膜性要好、尽可能不含 气泡。
第十三章成型原理与成型技术
13.6注射成型
注射成型是将瓷粉和有机粘结剂混合
后,经注射成型机,在130~ 300℃温度下将瓷料注射到金属模 腔内。待冷却后,粘结剂固化,便 可取出毛坯而成型。(P51,图18-
1)
第十三章成型原理与成型技术
注射成型的特点
注射成型法可以成型形状复杂的制品。 毛坯尺寸和烧结后实际尺寸的精确度高, 尺寸公差在1%以内,而干压成型为 ±1%~2%,注浆成型法±5%。注射成 型工艺的周期为10~90s,工艺简单, 成本低,压坯密度均匀,适于复杂零件 的自动化大批量生产。但是它脱脂时间 较长,金属模具昂贵,设计较困难。
第十三章成型原理与成型技术
第十三章成型原理与成型技术
13.4等静压成型
等静压成型又称静水压成型,它是 利用液体介质不可压缩性和均匀传递压 力性的一种成型方法 。 冷等静压成型 热等静压成型
第十三章成型原理与成型技术
13.4.1湿式等静压成型 先将配好的坯料装入塑料或橡胶做
成的弹性模具内,置于高压容器内,密 封后,注入高压液体介质,压力传递至 弹性模具对坯料加压。然后释放压力取 出模具,并从模具取出成型好的坯件。
第十三章成型原理与成型技术
13.7轧膜成型
轧膜成型是将准备好的陶瓷粉料,拌以一定 量的有机粘结剂(如聚乙烯醇等)和溶剂,通 过粗轧和精轧成膜后再进行冲片成型。
轧膜成型的工艺流程如下:
第十三章成型原理与成型技术
粗轧是将粉料、粘结剂和溶剂等成分 置于两辊轴之间充分混合混练均匀,伴 随着吹风,使溶剂逐渐挥发,形成一层 厚膜。精轧是逐步调近轧辊间距,多次 折叠,90°转向反复轧练,以达到良好 的均匀度、致密度、光洁度和厚度。轧 好的坯片,在一定湿度的环境中储存, 防止干燥脆化,最后在冲片机上冲压成 型。
2.蜡浆的性能 (1)稳定性好 (2)可铸性好 (3)收缩率低
3.热压铸成型的特点 适用于外形复杂、精密度高的中小型制品。其
成型设备不复杂,模具磨损小,操作方便,生产 效率高。热压铸成型的缺点是,工序较繁,耗能 大,工期长,对于壁薄、大而长的制品不宜采用。
第十三章成型原理与成型技术
干压成型
除气、进热压铸机 浇成蜡饼存放
熟瓷粉是预先煅烧的瓷料。目的,除使反应 充分均匀之外,还可减少石蜡用量,降低烧 结收缩和变形。
石蜡是作为增塑剂使用,具有很好的热流动 性、润滑性和冷凝性。
表面活性物质—油酸、硬脂酸、蜂蜡等,使 瓷粉与石蜡更好地结合。这些表面活性物质 不仅能提高蜡浆的热流动性和冷凝蜡坯的强 度,而且可以减少石蜡的用量,防止瓷粉分 层。
注浆成型法 :
(1)空心注浆 (2)实心注浆
第十三章成型原理与成型技术
第十三章成型原理与成型技术
第十三章成型原理与成型技术
13.2热压铸成型
利用含蜡料浆加热熔化后具有流 动性和塑性,冷却后在金属模中凝 固成一定形状。
第十三章成型原理与成型技术
1.蜡浆的制备
熟瓷粉
预热
石蜡 表面活性物质
熔化
搅拌
将陶瓷粉体经过塑化、造粒,制备 成流动性好、粒配合适的粉料,装入模 具内,通过压机的柱塞施以外加压力, 使粉料压制成一定形状的坯体。
13.3.1塑化与造粒工艺
通过造粒工艺,把陶瓷粉料制成具 有良好流动性和一定强度的颗粒(同时
具有一定的粘性),以便干压成型。
塑化原理
第十三章成型原理与成型技术
传压液体可用水、甘油或重油等。 弹性模具材料应选用弹性好、抗油性好 的橡胶或类似的塑料。
第十三章成型原理与成型技术
第十三章成型原理与成型技术
13.4.2干式等静压成型 干式等静压成型的模具是半固定式
的,坯料的添加与坯件的取出都是在 干燥状态下操作。干式等静压成型模 具,两头(垂直方向)并不加压,适 于压制长型、薄壁、管状产品。
第十三章成型原理与成型技术
第十三章成型原理与成型技术
13.5挤压成型 将经真空练制的泥料,置于挤制机内,通过 挤制机的机嘴,挤压出各种形状的坯体。
13.5.1挤压成型泥料的性能要求
(1)粉料有足够的细度和圆润的外形。 (2)溶剂、增塑剂等用量要适当。
第十三章成型原理与成型技术
13.5.2挤压成型的特点
挤压成型适于连续化批量生产, 生产效率高,环境污染小,易于自动操 作。但机嘴结构复杂,加工精度要求高, 耗泥量多,制品烧成收缩大。挤压成型 适于挤制直径1~30mm的管、棒形制 品(细管壁厚小至0.2mm),或用以 挤制径幅800mm 、100~200孔 /cm2的蜂窝状、筛格式穿孔瓷筒。
第十三章成型原理与成型技术