金刚石刀具的磨损机理
机械研磨过程中金刚石刀具材料去除机理
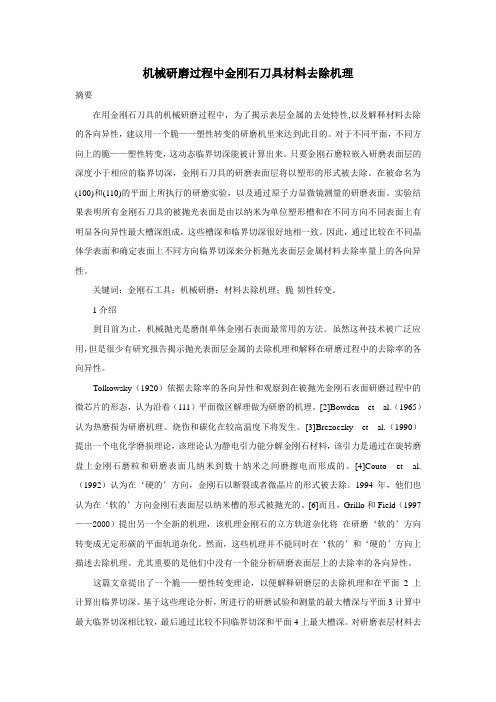
机械研磨过程中金刚石刀具材料去除机理摘要在用金刚石刀具的机械研磨过程中,为了揭示表层金属的去处特性,以及解释材料去除的各向异性,建议用一个脆——塑性转变的研磨机里来达到此目的。
对于不同平面,不同方向上的脆——塑性转变,这动态临界切深能被计算出来。
只要金刚石磨粒嵌入研磨表面层的深度小于相应的临界切深,金刚石刀具的研磨表面层将以塑形的形式被去除。
在被命名为(100)和(110)的平面上所执行的研磨实验,以及通过原子力显微镜测量的研磨表面。
实验结果表明所有金刚石刀具的被抛光表面是由以纳米为单位塑形槽和在不同方向不同表面上有明显各向异性最大槽深组成,这些槽深和临界切深很好地相一致。
因此,通过比较在不同晶体学表面和确定表面上不同方向临界切深来分析抛光表面层金属材料去除率量上的各向异性。
关键词:金刚石工具;机械研磨;材料去除机理;脆-韧性转变。
1介绍到目前为止,机械抛光是磨削单体金刚石表面最常用的方法。
虽然这种技术被广泛应用,但是很少有研究报告揭示抛光表面层金属的去除机理和解释在研磨过程中的去除率的各向异性。
Tolkowsky(1920)依据去除率的各向异性和观察到在被抛光金刚石表面研磨过程中的微芯片的形态,认为沿着(111)平面微区解理做为研磨的机理。
[2]Bowden et al.(1965)认为热磨损为研磨机理。
烧伤和碳化在较高温度下将发生。
[3]Brezoczky et al.(1990)提出一个电化学磨损理论,该理论认为静电引力能分解金刚石材料,该引力是通过在旋转磨盘上金刚石磨粒和研磨表面几纳米到数十纳米之间磨擦电而形成的。
[4]Couto et al.(1992)认为在‘硬的’方向,金刚石以断裂或者微晶片的形式被去除。
1994年,他们也认为在‘软的’方向金刚石表面层以纳米槽的形式被抛光的。
[6]而且,Grillo和Field(1997——2000)提出另一个全新的机理,该机理金刚石的立方轨道杂化将在研磨‘软的’方向转变成无定形碳的平面轨道杂化。
PCD刀具金刚石砂轮刃磨质量的研究

PCD刀具金刚石砂轮刃磨质量的研究PCD刀具在加工工件之前必须保证良好的刃口,金刚石砂轮刃磨是目前使用最广泛的方法。
研究表明,刃口质量越高,在工件加工表面刀具几何复映区交界处留下的刀痕越细,加工工件的表面光洁度越高。
因为刃口崩缺或扩展极易引起刀具磨损或损坏,降低刀具使用寿命。
刃口崩缺是金刚石刀具刃口质量的关键指标。
PCD刀具的刃磨机理:金刚石砂轮的磨粒不断冲击PCD材料,使PCD上的金刚石发生脆性破碎(包括晶内微细破碎、沿晶破碎和解理破碎)、滑擦磨损、刻划作用;热化学作用则是磨削过程中产生的高温使金刚石发生氧化或石墨化。
影响PCD刀具的刃口质量的因素很多,PCD复合片中金刚石微粉颗粒度、金刚石砂轮种类、设备性能及工装夹具刚性等。
1.PCD复合片中金刚石微粉颗粒度在其他条件相同的情况下,PCD材料的金刚石微粉颗粒度与刀具刃口崩缺呈正相关关系,即微粉粒度越大,刃口崩缺也越大。
同时,混合粒度的刃口崩缺小于粗颗粒的,更接近中粒度的,这是因为单纯的粗颗粒中间填充的是金属结合剂,而混合粒度是在粗颗粒之间既有结合剂又有其他细粒度级配。
在刃磨过程中砂轮金刚石的磨粒不断冲击PCD刀具刃口处,PCD刀具塑性较差,刃口处就会产生微观崩刃。
从微观方面分析,PCD刀具中的金刚石颗粒在被挤压、摩擦中出现脆性破碎并形成崩缺,而脆性破碎形成的崩缺大小与金刚石微粉颗粒度成正相关,粒度越大,刃口崩缺也越大。
此外,由于细砂轮的金刚石磨料硬度低于中、粗颗粒PCD中的金刚石微粒,磨料的刻划作用弱,但细砂轮的磨料易磨损和堵塞,磨削温度高时,滑擦和热化学作用占主导,这样就减小或消除了脆性破碎出现的较大崩口,故最终形成的刃口崩缺小于粒度尺寸。
2.金刚石砂轮种类刃口崩缺顺序:金属结合剂砂轮>陶瓷结合剂砂轮>树脂结合剂砂轮。
砂轮粒度大于W10时,刃口崩缺值对砂轮粒度很敏感,并随粒度增大而增大;当砂轮粒度小于W10时,刃口崩缺值对砂轮粒度不敏感。
金属结合剂金刚石砂轮磨粒在磨削过程中发生破碎以保持锋利状态,从而实现磨削,树脂结合剂金刚石砂轮表面会因为受热而发生变形,宜采用较低磨削速度,陶瓷结合剂是由多种材料配压而成,磨削过程中结合剂和金刚石磨粒容易集体脱落,致使PCD刀具表面处留下凹坑。
论述金刚石刀具超精密切削的机理丶条件和应用范围

金刚石刀具超精密切削的机理丶条件和应用范围
金刚石刀具是超精密切削中常用的刀具材料,其切削机理、条件和应用范围如下:
1.切削机理:
⏹金刚石刀具的切削刃非常锋利,在切削过程中能够实现“切入式切削”,
使切削力大大减小。
⏹金刚石的硬度极高,切削时不易被工件材料磨损,能够保持良好的切削刃
形状。
⏹金刚石的传热性能极佳,能够快速地将切削热量传递出去,从而降低切削
温度,减少热损伤。
1.切削条件:
⏹刀具刃口半径:为了实现超精密切削,需要将刀具的刃口半径减小到亚微
米级,以提高切削的精度和表面粗糙度。
⏹切削用量:为了减小切削力和热量,需要选择较小的切削深度和进给速度,
以提高切削效率。
⏹工件材料:金刚石刀具适用于加工各种硬材料,如淬火钢、硬质合金等。
但是,对于一些韧性较大的材料,需要进行预处理或选择其他刀具材料。
1.应用范围:
⏹金刚石刀具广泛应用于超精密切削领域,如光学零件、轴承、硬盘磁头、IC
芯片等高精度、高表面质量的零件加工。
⏹在加工过程中,金刚石刀具还可以用于制作各种微细结构,如微孔、微槽
等。
综上所述,金刚石刀具的超精密切削需要满足一定的条件,并具有广泛的应用范围。
超精密加工中的金刚石刀具及刀具磨损分析

理论与实践经济与社会发展研究超精密加工中的金刚石刀具及刀具磨损分析齐齐哈尔工程学院 武晓迪摘要:各种超精密加工应用中将金刚石用作切削工具已经成为现实,然而其目的与意义并没有得到实质性分析。
据此,本文对超精密加工中应用金刚石作为切削刀具的现实意义进行分析。
关键词:超精密加工;切削工具;刀具磨损一、技术背景分析使用高速超精密车床加工玻璃和硅等脆性材料时,当所施加的切削深度低于临界值时,则认为其处于延性模式,并且可以容易地加工而不会形成裂纹。
因此,对于这些材料的延性至脆性转变具有重要意义,在这些材料中,临界切削深度的大小取决于零件的特性而变化。
通常,单晶硅经常用在微机电系统(MEMS)中,在该系统中,最终将材料加工成优质产品,并进行超精密研磨和抛光操作。
尽管硅材料的行为在室温下很脆,但建议使用金刚石车削工具以延性模式加工硅。
这减少了由陶瓷材料的脆性断裂引起的损坏,并提高了最终零件的生产率。
使用金刚石工具对铜,铝和镍等有色金属材料进行高速加工,以评估工具的磨损,切削力和表面光洁度。
实验针对不同的切割速度进行,例如较低的150m/min的速度和较高的4500m/min的速度。
在较低的切削速度下观察到的刀具磨损率大于较高的切削速度。
这可能是由于以较高的速度减少了刀具与工件啮合的时间。
它还降低了工具和工件界面之间的化学亲和力。
具有高负前角的金刚石工具可用于以超精密精度精加工该材料。
二、金刚石作为切削工具的意义制备塑料模具的需求不断增加,而塑料模具是制造CD光学头的非球面透镜和照相机的智能透镜所必需的。
刀具的切削刃必须锋利且没有不规则形状,以加工高精度非球面。
基于工具的清晰度,单晶金刚石(SCD)和多晶金刚石(PCD)之间存在主要差异。
SCD工具的切削刃是均匀的且没有不规则性,而PCD工具的切削刃则显示出微观的不规则性,从而导致金刚石颗粒的去除。
与PCD工具相比,SCD工具的主要缺点是其磨损寿命短。
它还用于将铝基板加工成精细的镜面涂层,该涂层用于计算机存储系统的硬盘驱动器中。
金刚石刀具刃口的钝化原理
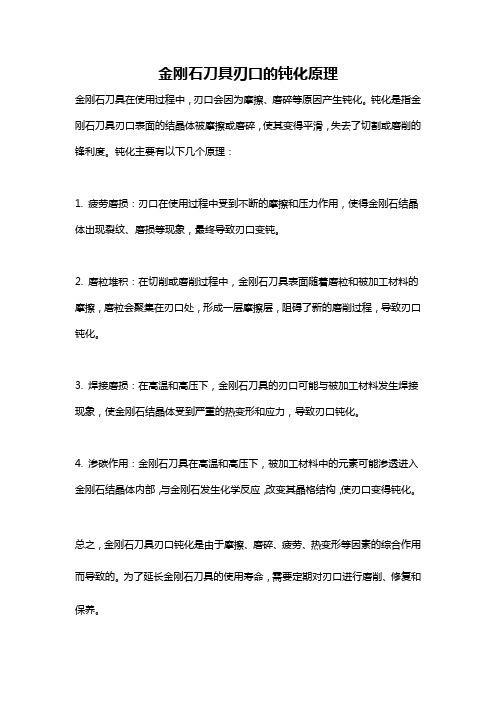
金刚石刀具刃口的钝化原理
金刚石刀具在使用过程中,刃口会因为摩擦、磨碎等原因产生钝化。
钝化是指金刚石刀具刃口表面的结晶体被摩擦或磨碎,使其变得平滑,失去了切割或磨削的锋利度。
钝化主要有以下几个原理:
1. 疲劳磨损:刃口在使用过程中受到不断的摩擦和压力作用,使得金刚石结晶体出现裂纹、磨损等现象,最终导致刃口变钝。
2. 磨粒堆积:在切削或磨削过程中,金刚石刀具表面随着磨粒和被加工材料的摩擦,磨粒会聚集在刃口处,形成一层摩擦层,阻碍了新的磨削过程,导致刃口钝化。
3. 焊接磨损:在高温和高压下,金刚石刀具的刃口可能与被加工材料发生焊接现象,使金刚石结晶体受到严重的热变形和应力,导致刃口钝化。
4. 渗碳作用:金刚石刀具在高温和高压下,被加工材料中的元素可能渗透进入金刚石结晶体内部,与金刚石发生化学反应,改变其晶格结构,使刃口变得钝化。
总之,金刚石刀具刃口钝化是由于摩擦、磨碎、疲劳、热变形等因素的综合作用而导致的。
为了延长金刚石刀具的使用寿命,需要定期对刃口进行磨削、修复和保养。
石材锯切机理与金刚石工具磨损机理的研究现状
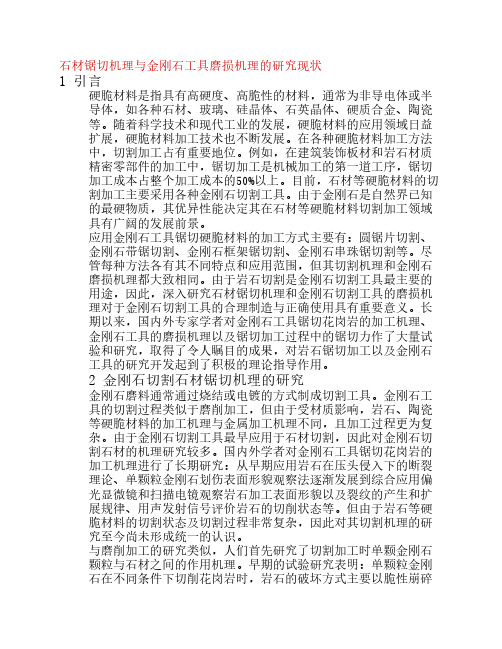
石材锯切机理与金刚石工具磨损机理的研究现状1 引言硬脆材料是指具有高硬度、高脆性的材料,通常为非导电体或半导体,如各种石材、玻璃、硅晶体、石英晶体、硬质合金、陶瓷等。
随着科学技术和现代工业的发展,硬脆材料的应用领域日益扩展,硬脆材料加工技术也不断发展。
在各种硬脆材料加工方法中,切割加工占有重要地位。
例如,在建筑装饰板材和岩石材质精密零部件的加工中,锯切加工是机械加工的第一道工序,锯切加工成本占整个加工成本的50%以上。
目前,石材等硬脆材料的切割加工主要采用各种金刚石切割工具。
由于金刚石是自然界已知的最硬物质,其优异性能决定其在石材等硬脆材料切割加工领域具有广阔的发展前景。
应用金刚石工具锯切硬脆材料的加工方式主要有:圆锯片切割、金刚石带锯切割、金刚石框架锯切割、金刚石串珠锯切割等。
尽管每种方法各有其不同特点和应用范围,但其切割机理和金刚石磨损机理都大致相同。
由于岩石切割是金刚石切割工具最主要的用途,因此,深入研究石材锯切机理和金刚石切割工具的磨损机理对于金刚石切割工具的合理制造与正确使用具有重要意义。
长期以来,国内外专家学者对金刚石工具锯切花岗岩的加工机理、金刚石工具的磨损机理以及锯切加工过程中的锯切力作了大量试验和研究,取得了令人瞩目的成果,对岩石锯切加工以及金刚石工具的研究开发起到了积极的理论指导作用。
2 金刚石切割石材锯切机理的研究金刚石磨料通常通过烧结或电镀的方式制成切割工具。
金刚石工具的切割过程类似于磨削加工,但由于受材质影响,岩石、陶瓷等硬脆材料的加工机理与金属加工机理不同,且加工过程更为复杂。
由于金刚石切割工具最早应用于石材切割,因此对金刚石切割石材的机理研究较多。
国内外学者对金刚石工具锯切花岗岩的加工机理进行了长期研究:从早期应用岩石在压头侵入下的断裂理论、单颗粒金刚石划伤表面形貌观察法逐渐发展到综合应用偏光显微镜和扫描电镜观察岩石加工表面形貌以及裂纹的产生和扩展规律、用声发射信号评价岩石的切削状态等。
影响单晶金刚石刀具的研磨的因素分析

影响单晶金刚石刀具的研磨的因素分析1金刚石刀具的研磨方法单晶金刚石刀具的制造工序一般包括选料、定向、锯割、开坯、装卡、粗磨、精磨和检验。
将选定的金刚石原石经定向后沿最大平面锯割开,可得到两把刀具的坯料,这样既能提高金刚石材料的利用率,又可削减总研磨量。
通过开坯可使刀具形状达到装卡(镶嵌或钎焊)要求。
开坯和粗、精磨加工均采纳研磨的方法。
金刚石的研磨加工在铸铁研磨盘上进行。
研磨盘的直径约为300mm,由材料组织中孔隙的形状、大小和比例均经过优化的研磨金刚石专用高磷铸铁制成。
研磨盘的表面镶嵌有金刚石研磨粉,其颗粒尺寸可从小于1m直到40m。
粗颗粒的金刚石粉具有较高的研磨速率,但研磨质量较差,因此粗磨时一般采纳粗粉,而精磨时则采纳尺寸小于1m的细粉。
研磨前,首先将金刚石粉与橄榄油或其它仿佛物质混合成研磨膏,然后涂敷在研磨盘表面,放置一段时间使研磨膏充分渗入研磨盘的铸铁孔隙中,再用一较大的金刚石在研磨盘表面进行来回预研磨,以进一步强化金刚石粉在铸铁孔隙中的镶嵌作用。
研磨时,一般将被研磨的金刚石包埋在锡斗中,只露出需研磨的面。
研磨时的研磨盘转速约为2500r/min,研磨压力约为1kg/mm2。
金刚石的研磨与其它刀具材料的加工有很大区分,其研磨机理至今尚未得到令人信服的阐释,影响研磨质量的因素也是多方面的。
下面就金刚石刀具研磨的一些工艺问题进行讨论。
2磨削量的影响因素通过试验发觉,磨削量与研磨条件的关系为V=kvp式中V研磨体积k磨削率v磨削速度p研磨压力此外,金刚石的磨向、磨料的粒度、磨粒在铸铁孔隙中的镶嵌情形等因素也会更改磨削率的大小,从而影响磨削量。
3研磨质量的影响因素金刚石硬度高、脆性大,研磨时虽然刀具表面粗糙度较易保证,但刀刃简单显现崩口,刀刃锯齿度不易降低。
超精密加工要求刀具刃口在500倍显微镜下察看无崩口,因此需要从各方面优化研磨过程,以获得平直完美的刀刃。
研磨粉粒度和研磨盘表面状态对研磨质量的影响可以看出,由于粗粉对刀刃的冲击性较大,研磨后刀刃锯齿度也较大,基本上难以研磨出无崩口的刀刃;而采纳细粉时,经过几分钟的研磨后刀刃即变得平直,锯齿度趋向于零。
金刚石切削黑色金属时刀具磨损机理的摩擦磨损试验
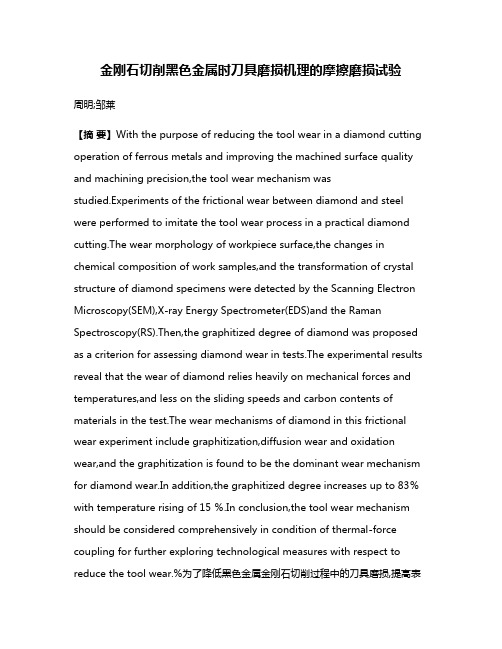
金刚石切削黑色金属时刀具磨损机理的摩擦磨损试验周明;邹莱【摘要】With the purpose of reducing the tool wear in a diamond cutting operation of ferrous metals and improving the machined surface quality and machining precision,the tool wear mechanism wasstudied.Experiments of the frictional wear between diamond and steel were performed to imitate the tool wear process in a practical diamond cutting.The wear morphology of workpiece surface,the changes in chemical composition of work samples,and the transformation of crystal structure of diamond specimens were detected by the Scanning Electron Microscopy(SEM),X-ray Energy Spectrometer(EDS)and the Raman Spectroscopy(RS).Then,the graphitized degree of diamond was proposed as a criterion for assessing diamond wear in tests.The experimental results reveal that the wear of diamond relies heavily on mechanical forces and temperatures,and less on the sliding speeds and carbon contents of materials in the test.The wear mechanisms of diamond in this frictional wear experiment include graphitization,diffusion wear and oxidation wear,and the graphitization is found to be the dominant wear mechanism for diamond wear.In addition,the graphitized degree increases up to 83%with temperature rising of 15 %.In conclusion,the tool wear mechanism should be considered comprehensively in condition of thermal-force coupling for further exploring technological measures with respect to reduce the tool wear.%为了降低黑色金属金刚石切削过程中的刀具磨损,提高表面加工质量和精度,对刀具磨损机理进行了研究.通过黑色金属金刚石摩擦磨损试验,模拟了实际切削过程中的刀具磨损行为;分别采用扫描电镜(SEM) 、X射线能谱仪(EDS)以及拉曼光谱仪(RS)对工件表面形貌、实验前后工件表面化学组分变化以及金刚石磨损表面的晶体结构转变进行了检测,同时提出了用石墨化程度作为试验过程中评价金刚石磨损的指标.试验结果表明:金刚石的磨损主要与机械力和温度有关,摩擦速度和工件材料中的含碳量对其影响相对较小;石墨化磨损、扩散磨损和氧化磨损等磨损机理共存,其中石墨化为导致金刚石磨损的主要原因.结合红外热像仪测温和热传导理论推算,近似获得了摩擦界面的真实温度,且随着温度升高15%,金刚石石墨化程度显著加剧83%.作者提出,应当综合考虑热-力耦合作用下的刀具磨损机理,以便进一步探寻抑制刀具磨损的工艺措施.【期刊名称】《光学精密工程》【年(卷),期】2013(021)007【总页数】9页(P1786-1794)【关键词】超精密加工;金刚石切削;黑色金属;摩擦磨损;磨损机理【作者】周明;邹莱【作者单位】哈尔滨工业大学机电工程学院,黑龙江哈尔滨150001;哈尔滨工业大学机电工程学院,黑龙江哈尔滨150001【正文语种】中文【中图分类】TG501.1;TH117.11 引言黑色金属由于具有其它材料难以替代的性能优势而在模具行业有着广泛的应用前景,其超精密加工的需求也日益增多。
- 1、下载文档前请自行甄别文档内容的完整性,平台不提供额外的编辑、内容补充、找答案等附加服务。
- 2、"仅部分预览"的文档,不可在线预览部分如存在完整性等问题,可反馈申请退款(可完整预览的文档不适用该条件!)。
- 3、如文档侵犯您的权益,请联系客服反馈,我们会尽快为您处理(人工客服工作时间:9:00-18:30)。
金刚石刀具的磨损机理
引言:由于金刚石材料的高硬度和各向同性使其磨损非常缓慢。
是一种理想的刀具材料。
为了充分发挥PCD刀具的切削性能,世界各国先后投入大量人力物力对PCD刀具进行研究。
1、金刚石刀具的磨损形态
金刚石刀具的磨损形态常见于前刀面磨损、后刀面磨损和刃口崩裂。
1、金刚石刀具的磨损机理
金刚石刀具的磨损机理比较复杂,可分为宏观磨损与微观磨损。
前者以机械磨损为主,后者以热化学磨损为主。
宏观磨损的基本规律如图,早期磨损迅速,正常磨损十分缓慢。
通过高倍显微镜观察,刃口质量越差及锯齿度越大,早期磨损就越明显。
这是因为金刚石刀刃圆弧采用机械方法研磨时,实际得到的是不规则折线如图,在切削力作用下,单位折线上压力迅速增大,导致刀刃磨损加快。
另一个原因是,当金刚石刀具的刃磨压力过大或刃磨速度过高,及温度超过某一临界值时,金刚石刀具表面就会发生氧化与石墨化,使金刚石刀具表面的硬度降低,形成硬度软化层。
在切削力作用下,软化层迅速磨损。
由此可见,金刚石刀具刃磨质量的高低会严重影响它的使用寿命与尺寸精度的一致性。
当宏观磨损处于正常磨损阶段,金刚石刀具的磨损十分缓慢,实践证明,在金刚石的结晶方向上的磨损更是缓慢。
随着切削时间的延长,刀具仍有几十至几百纳米的磨损,这就是微观磨损。
通过高倍显微镜长期观察以及用光谱与衍射分析后,金刚石刀具的微观磨损原因可能有以下3个:
1随着切削时间的不断延长,切削区域能量不断积聚,温度不断升高,当达到热化学反应温度时,就会在刀具表面形成新的变质层。
变质层大多是强度甚差的氧化物与碳化物,不断形成,不断随切屑消失,逐渐形成磨损表面。
2金刚石晶体在切削力特别是承受交变脉冲载荷持续作用下,一个又一个C原子获得足够的能量后从晶格中逸出,造成晶体缺陷,原子间引力减弱,在外力作用下晶格之间发生剪切与剥落,逐渐形成晶格层面的磨损,达到一定数量的晶格层面磨损后就会逐渐形成刀具的磨损表面。
3金刚石刀具在高速切削有色金属及其合金时,在长时间的高温高压作用下,当金刚石晶体与工件的金属晶格达到分子甚至原子之间距离时,引起原子之间相互渗透。
改变了金刚石晶体的表面成分,使得金刚石刀具表面的硬度与耐磨性降低,这种现象称为金刚石的溶解。
金刚石刀具的磨损程度与磨损速度则取决于金刚石原子在有色金属或在其它非金属材料原子中的溶解率。
实践证明,金刚
石刀具在切削不同的材料时,有不同的溶解率,也就是说金刚石刀具在不同切削条件下切削不同的工件材料,磨损速度与程度是不相同的,溶解率越大,金刚石刀具磨损就越快。
2、金刚石刀具的化学磨损
微切削加工用来制作具有光学表面质量的零件,目前只限于少数材料。
属于这一类的材料主要有高纯度铜、无硅铝合金和含磷量约为12%的非电流析出镍。
工业上很重要的铁基材料则由于单晶金刚石刀具的严重磨损而无法加工。
解决这一问题主要有三种可能的途径,也就是说,通过改进切削加工工艺、刀具材料和被加工材料。
金刚石刀具沉积硬质材料涂层则属于改进刀具材料。
涂层应能阻止金刚石与被加工材料的直接接触。
为了确定适宜的硬质材料涂层,首先应研究切削加工过程中刀具与工件之间存在的界面的相互作用。
切削加工Fe、Ni、Cr、Ti等(门捷列夫元素周期表第-族过渡金属)金属材料时,金刚石刀具则出现严重的化学磨损。
解释化学磨损的一种假设是过渡金属中存在非配对d电子。
过渡金属倾向于通过其d轨道与碳的p轨道
的重叠发生化学反应。
如果发生化学磨损,碳原子便从紧密金刚石晶格中脱除。
碳原子一脱离金刚石晶格:(1)就可能通过与其它碳原子的化合转变成一种软质石墨结构;(2)或与氧发生反应生成CO或CO2,与材料形成碳化物;(3)或扩散到材料中。
据Thornton和Wilks观察,在压力约为13.3Pa的真空中,以约10mmin的很低切削速度车削铁,单晶金刚石刀具磨损严重,刀具温度估计在200℃以下。
在这种情况下,金刚石的严重磨损只能归因于金刚石由刚出现的洁净铁表面所诱发的催化性石墨化。
为了理解洁净铁表面的催化作用,假设金刚石晶格中的碳与铁原子在切削加工时发生化学键合。
Thornton将此分为至少5种化学键合类型,
键合类型1和5分别相当于铁晶格或金刚石晶格中的原子键合;3相当于界面层的铁碳键合;而2和4相当于最上部铁或碳原子位置和紧接着的原子位置之间的化学键合。
键合类型4很有可能弱于其它键合类型。
利用磁控溅射工艺,通过优化沉积TiN、TiAlN和AlN涂层的工艺参数,涂层的成分可接近化学计量,硬度则可高达1460HV0.015到1940HV0.015不等。
厚度约为50nm的TiN、TiAlN和AlN薄膜涂层均呈现非常光滑的细晶表面。
平均粗糙度约为1.0nm。
如果涂层厚度≤50nm,则金刚石刀具的刃口钝化(R\par
通过在金刚石刀具上沉积TiN、TiAlN或AlN涂层,金刚石刀具在试验条件下微切削加工纯铁时的磨损可比未涂层金刚石刀具减少达50%。
3、问题建议
1金刚石刀具在使用时,除有锋利的刀刃外,还应当选取适当的刃区形式见下图,以增强刀刃强度。
2由于用机械方法加工制成的金刚石刀具用于镜面切削时,常常需要一个磨合期,即需要经过一段时间的切削过程,刀具才能达到最佳加工效果。
为了缩短或消除
磨合期,一般可用离子束溅蚀法、无损伤机械化学抛光法、真空等离子化学抛光法与热化学抛光法等研磨方法来解决。
3单晶金刚石各向异性,在不同晶面及不同方向上性能差异甚大,切削不同的材料,应有不同的定向。
4为了提高金刚石刀具的钎焊质量,应选用对金刚石润湿性较好的合金作为钎焊材料,也可适当添加Ti、Cr、V、Mo等元素,以改善在液相下合金焊料对金刚石表面的浸润性,实现焊料对金刚石的牢固粘结。
另外,钎焊必须在真空中惰性气体的保护下进行,钎焊温度应低于金刚石石墨化转变温度(800℃),而且钎焊时动作要快,以避免出现刀片开裂等现象。
刀片钎焊后可适当延长保温时间,
以消除钎焊应力。
5刀具宜采用逐渐减载的研磨工艺,既可保持较高的研磨效率,又可降低研磨后表面硬度的软化层深度,从而延长刀具的使用寿命。
单晶金刚石刀具则在高精密研磨盘上研磨,并选用较小的刃磨角与适当的偏向角,使用极细的金刚石研磨粉,采用精度高、运转平稳且振动小的研磨机床(如空气静压轴承研磨机)。
6金刚石刀具适宜在机床—工件—刀具系统刚性足够、转速高、功率大、振动小、平稳性好的组合机床或加工中心上切削有色金属及其合金、纤维增强金属(FRM)、纤维增强塑料(FRP)、碳纤维增强复合材料(CFRP)等连续表面。
金刚石刀具的检测和调刀应采用光学仪器等非接触式测量方法。