机械加工定位误差分析及菱形销设计
菱形销

菱形销23881====b b B d采用短定位销,工件认错面B 为第一定位基准工件上的内孔,21o o 及分别作为第二和第三定位基准 P51工作在夹具上定位时,工件上作为第一定位基准的底面B 没有基准位置误差,由于定位孔较浅,其内孔中心线由于内孔与底面垂直底误差而引起的基准误差也可忽略,但作为第二、三定位基准的21,o o 由于与定位销的配合间隙及两孔两销中心距误差引起的基准误差必须考虑。
考虑极端的情况:()LI d D o T T T o o +∆++==min 11''2'11位置δ ()LI d D LI o T T T T o o o +∆++=+==min 11'1''2'22位置δ 1D T -工件内孔1O 公差1d T —夹具短圆柱销公差min ∆—工件内孔1o 与圆定位销的最小配合间隙当工件内孔2o 的直径尺寸也最大,菱形定位销直径尺寸最小,工件两孔及夹具上两位销中心距均为L 时,可求角度误差()()()LS S o o o 2arctan 211'位置位置角度+=δ ()min 222∆++=d D o T T 角度‘δ2D T —工件内孔2o 的公差2d T —夹具上菱形销的公差min ∆—工件内孔2o 与菱形销最小配合间隙。
P52夹具上的定位销按oTd d 1-制造。
P38夹具尺寸公差占工件尺寸的31,018.07,021.0721====IT T IT T o o P231 短圆柱销 007.0,21min 007.0014.01=∆=--d菱形销 007.0013.0211--=d夹具间距007.034007.0±=±=L L 夹 ()mm T T d D o 038.0007.0007.0021.0min 111=++=∆++=位置δ ()mm T T T LI d D o 075.004.0007.0007.0021.0min 112=+++=+∆++=位置δ ()()()36231.0035.0arctan 2arctan 211'⨯+=+=L S S o o o 位置位置角度δ。
机械加工误差分析及应对策略

机械加工误差分析及应对策略1前言所谓机械加工精度是指机械零件在生产和加工过程中,其实际的几何参数和理想中的几何参数之间相符合的程度。
机械零件的几何参数一般包括了以下几个方面:位置、尺寸和形状。
机械零件的加工精度就包括了以上三个方面的内容。
首先是相互位置的精度,主要是用来判断机械零件对加工表面同基准间所产生的位置误差;其次是尺寸精度,尺寸精度则是用来判断对机械零件加工表面的同基准间所产生的尺寸误差;还有一个则是形状精度,形状精度主要用来判断对机械零件的整体几何形状所产生的误差。
事实上,在现实的机械加工生产过程中,由于各种各样的原因,任何一种加工方法所得到的机械零件的实际几何参数都不是绝对准确的,机械零件在加工过程中都会产生一些误差。
机械零件的加工误差就是指机械零件在加工过程中实施的几何参数与理想几何参数之间的差距和偏离的程度。
机械产品是由各种不同零件加工组合而成的,加强对机械零件由设计到加工,再到成品产出过程中的误差分析,提高机械零件在生产过程中的精度,对于提高机械产品的质量,增强机械产品的性能,提高机械生产商的市场竞争力具有非常重要的作用和意义。
2机械加工精度误差分析2.1加工原理误差加工原理误差是机械零件加工误差中最常见的误差类型之一。
所谓加工原理误差,就是指在机械零件加工过程中,由于采用了一些相类似的加工方法、刀具轮廓以及传动比等,来替代理论上的加工方法和工具,从而使得机械零件在实际的加工过程中产生了偏离理想参数的状况。
加工原理误差的出现主要有以下几个方面的原因。
首先,在现实的机械零件加工中采用了近似的加工运动。
通常我们在进行机床作业时,为了使工作表面符合我们加工的要求,我们就需要在加工工具和被加工对象上建立一定的关系,这种关系就被称之为运动关系。
在理论加工原理中,如果要达到完全准确加工精度,在实际的加工过程中就会出现很多不切实际的问题,对我们的生产加工带来很多困难,因此,在实际的加工中,我们往往会采取近似运动的加工方法,这样就导致了加工原理误差的产生。
定位误差分析(圆柱-菱形)
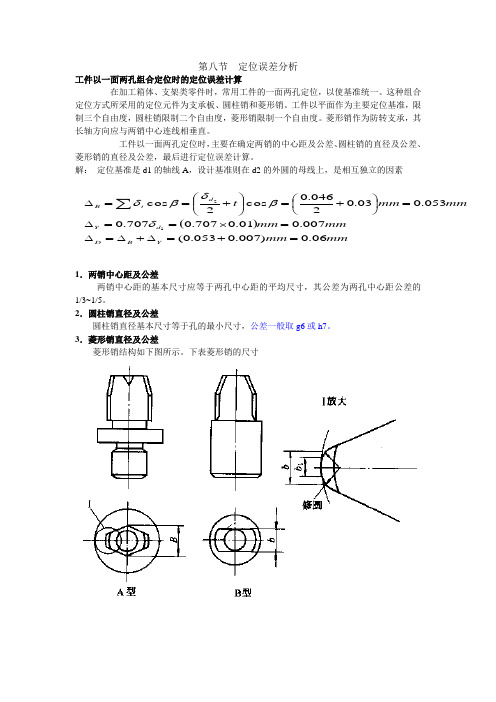
第八节 定位误差分析工件以一面两孔组合定位时的定位误差计算在加工箱体、支架类零件时,常用工件的一面两孔定位,以使基准统一。
这种组合定位方式所采用的定位元件为支承板、圆柱销和菱形销。
工件以平面作为主要定位基准,限制三个自由度,圆柱销限制二个自由度,菱形销限制一个自由度。
菱形销作为防转支承,其长轴方向应与两销中心连线相垂直。
工件以一面两孔定位时,主要在确定两销的中心距及公差、圆柱销的直径及公差、菱形销的直径及公差,最后进行定位误差计算。
解: 定位基准是d1的轴线A ,设计基准则在d2的外圆的母线上,是相互独立的因素1.两销中心距及公差两销中心距的基本尺寸应等于两孔中心距的平均尺寸,其公差为两孔中心距公差的1/3~1/5。
2.圆柱销直径及公差圆柱销直径基本尺寸等于孔的最小尺寸,公差一般取g6或h7。
3.菱形销直径及公差菱形销结构如下图所示。
下表菱形销的尺寸()mm mm mm mm mm mm t Y B D d Y d i B 06.0)007.0053.0(007.001.0707.0707.0053.003.02046.0cos 2cos 12=+=∆+∆=∆=⨯==∆=⎪⎭⎫ ⎝⎛+=⎪⎪⎭⎫ ⎝⎛+==∆∑δβδβδ菱形销直径可按下式计算,公差一般取h6d2=D2—X2min式中 D2—以菱形销定位孔的直径(mm);X2min —菱形销定位的最小间隙(mm)。
X2min 以下式计算式中 b ——菱形销圆柱部分的宽度(mm );D2——工件定位孔的最大实体尺寸(mm );a ——补偿量。
补偿量a 以下式计算 式中 δLD ——两孔中心距公差(mm );公差带宽度δL —— 两销中心距公差(mm )。
4.一面两孔定位的定位误差计算工件以一面两孔定位的定位误差计算与前述的计算方法基本相同。
但当某个加工精度的设计基准为两孔中心连线时,由于圆柱销和菱形销与两定位孔之间有间隙,两孔中心连线(设计基准)的变动可能有如图4-45所示四个位置。
2.5定位误差的分析与计算(二) 改

D2 min X 2 min 则 b 2a
式中
X 2 min—菱形销与孔之间的最小配合间隙,mm;
a—满足工件顺利装卸的补偿量,mm。
a TLD TLd 2
LOGO
2.5 定位误差的分析与计算(二)
菱形销圆柱部分的宽度b可查手册确定, 则由上式得
Y O 1O 2 δ d 2 sin( / 2)
LOGO
2.5 定位误差的分析与计算(二)
M1
d max /2
d min /2
工序尺寸A3的定位误差
δ d 2
M2 O
工件定位 外圆直径 由大变小
δ d
ΔY O 1O 2
δ d 2 sin( α/ 2)
ΔB与ΔY同向
δ 1 Δ D=Δ Y+Δ B= d [ +1] 2 sin(α/ 2)
LOGO
A3
M2
2.5 定位误差的分析与计算(二)
M1
d max /2
d m in /2
O
δ d 2
d max /2
d mi n /2
C1 C2
ΔY O 1O 2
δ d 2 sin( α/ 2)
工件定位 外圆直径 由大变小
δ d
δ 1 Δ D=Δ Y-Δ B= d [ -1] 2 sin(α/ 2)
复习
1.定位误差的概念
(1)基准不重合误差 △ B (2)基准位移误差 △Y
2.工件以平面定位误差计算
精基准平面定位时,一般认定△Y=0, △D=△B
3.以圆孔定位时的定位误差计算
LOGO
Page 2
2.5 定位误差的分析与计算(二)
机械制造工艺学——工件的定位
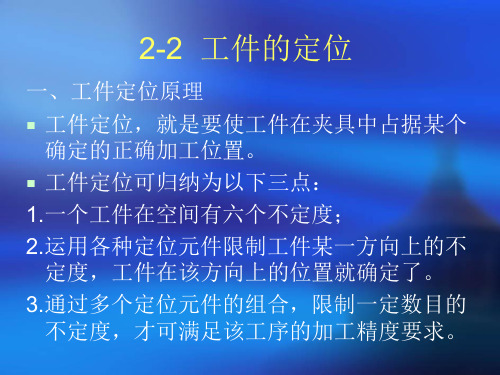
基准不重合误差:
(四)提高工件在夹具中定位精度的措施
即如何减少或消除基准位置误差和基准 不重合误差。
1、减少或消除基准位置误差的措施 (1)选用基准位置误差小的定位元件 A、以毛坯平面作为定位基准时,可以多点自
位支承取代球头支承钉。
B、以内孔和端面定位时,可应用浮动球面支 承,以减小轴向定位误差。
的定位元件,称为固定支承。
(2)可调支承:定位支承点的位置可以调节的 定位元件,称为可调支承。
主要用于以制造精度不高的毛坯面定位的场合。
(3)自位支承:定位支承点的位置随工件定 位基准位置变化而自动与之适应的定位元件, 称为自位支承。
自位支承一般只起一个定位支承点的作用。
2、辅助支承:只起提高工件支承刚性或辅助 定位作用的定位元件,称为辅助支承。
削边定位销的直径为
当以两个或两个以上的组合表面定位时,重 复定位可能造成不良后果。
为减少重复定位造成的加工误差,可采取如 下措施:
(1)改变定位元件结构
(2)撤消重复定位的定位元件:
(3)提高工件定位基准之间、定位元件定位 面之间的位置精度
二、定位元件的选择 定位表面不同,应选择不同的定位元件 (一)平面定位元件 1.主要支承:工件定位时起主要定位支承作用 (1)固定支承:定位支承点的位置固定不变
*为提高定位稳定性和刚度,以加工过的表面 定位时,可以出现重复定位。
三、定位误差的分析与计算
(一)定位误差及其计算方法
1、定位误差的概念及产生原因: *定位误差:指由于工件定位不准确,而造成
工序尺寸或位置要求方面的加工误差。
*上存在着公差范围内的差异。
2-2 工件的定位
一、工件定位原理
工件定位,就是要使工件在夹具中占据某个 确定的正确加工位置。
定位误差的分析计算

定位误差的分析计算为保证工件的加工精度,工件应有正确的定位,即除应限制工件必要的自由度使工件具有确定的位置外,还应使实施定位后所产生的误差在工件误差允许范围以内,实现工件安装时的定与准。
造成定位误差的原因有两个:一是由于定位基准与设计基准不重合,称基准不重合误差(定基误差)用△B表示;二是由于定位副制造误差而起定位基准的位移称为基准位移误差,用△Y表示。
(1)基准不重合误差的计算基准不重合误差因所选定位基准与工序基准不重合而引起,其值为两基准间的最大变化量(即两基面间公差),因此,计算时,可在确定认定位基准与工序基准的基础上,寻求两基面间的关系即可,具体分三步:①确定基准定位基准为该工序所选安装时定位的依据,并且一定在要求保证的工序尺寸方向上,作为已知条件在题目中说明或标注()于工序图;工序基准则为该工序用以表达加工表面(粗实线)位置尺寸的基准。
②基准是否重合经确认的定位基准与工序基准若为同一表面,则基准不重合误差△B=0;若不重合则需进行计算。
③基准不重合时的误差计算基准不重合误差为两基面间的最大变量。
因此,两基面间若有直接尺寸标注,则尺寸公差即为△B;若无直接尺寸,而只有间接尺寸,则需利用尺寸间关系如尺寸链进行求解。
若定位基准变动方向与对应工序尺寸不在同一方向,则需两基面间距离公差投影于工序尺寸方向,即△B=δs cosβ式中δs为定位基准与工序基准间尺寸公差β为基准间尺寸与工序尺寸之夹角(2)基准位移误差的计算基准位移误差△Y因定位副制造误差而起,因此,当定位副结构不同产生的基准位移误差计算。
①工件以平面定位工件若以粗基准平面定位,定位面与限位面间不可能有很好的贴合,但该定位方案往往出现在加工开始或加工要求不高情况下,故此时的误差也就不必计算。
工件若以加工过的精基准平面定位,则定位面与限位面间会有良好的接触状态,定位基面的位置可看成是不动的。
因此,基准位移误差为零,即△Y=0。
②工件外圆在圆孔中定位工件在外圆定位时,其定位基准为轴的中心线,定位基面为外圆柱面。
第三节定位误差的分析与计算
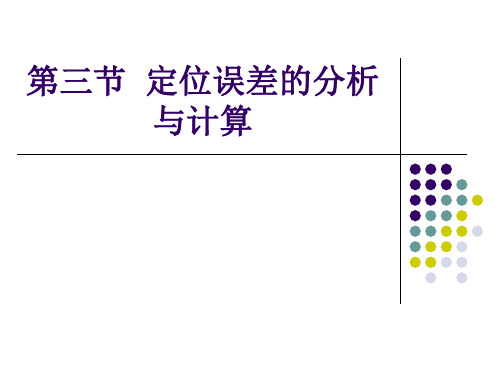
位置(A) 2L工tg工 角度(A) tg工
2、一面二孔定位 工件底面为第一基准,两孔O1、O2为第二、第三基准
2、一面二孔定位 第一定位基准:底面 没有基准位置误差 两孔O1、O2为第 二、第三基准, 由于制造及装配 误差, 定位基准 O1、O2存在位置 误差。
TD Td1 2
+ Td 2
30H 7 30
第三节 定位误差的分析 与计算
一、定位误差及其计算方法
(一)定位误差的概念及其产生的原因
例:如图所示,要在套 筒上钻一通孔,保证尺 寸H-TH0.
根据六点定位原理,用 套筒端面和内圆表面定 位消除五个自由度,使 工件获得正确位置; 定位元件:带支承垫圈 的定位销; 定位基准: 工序基准:
虽然套筒已在夹具中的 位置确定了,但由于工 件的内孔、外圆及定位 销的直径不可能制造得 绝对准确,工件内孔与 定位销之间存在间隙, 所以工件的内孔中心线 和外圆下母线均在一定 范围内变动,加工后的 一批工件的工序尺寸也 不同。造成在工序尺寸 上的加工误差。
例2、P51
存在基准不重合误差,忽略第二基准B面位置变动
定位(L) 位置(AB)+ 不重(O )cos -) (
1
定位(L)=L L=O1O2 O1O2
2 ( 0+o1o1 cos -)= TL1 TL2 cos -) ( 2
定位(H 2) 位置(O) 不重(D)
o1o2 Td / 2 Td / 2sin 2 Td / 2
Td 2 1 ( sin 1)
2
(四)圆锥表面定位时的定位误差
工件定位基准的位置误差为0,但在轴线方向的尺寸产生 定位误差
机械加工误差分析及措施
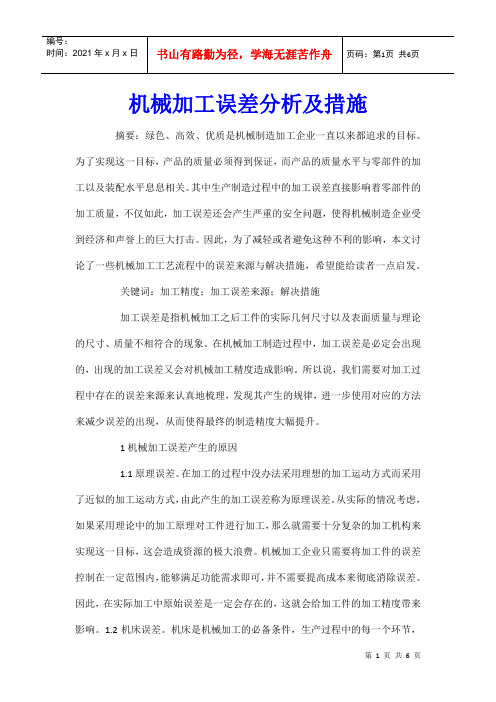
机械加工误差分析及措施摘要:绿色、高效、优质是机械制造加工企业一直以来都追求的目标。
为了实现这一目标,产品的质量必须得到保证,而产品的质量水平与零部件的加工以及装配水平息息相关。
其中生产制造过程中的加工误差直接影响着零部件的加工质量,不仅如此,加工误差还会产生严重的安全问题,使得机械制造企业受到经济和声誉上的巨大打击。
因此,为了减轻或者避免这种不利的影响,本文讨论了一些机械加工工艺流程中的误差来源与解决措施,希望能给读者一点启发。
关键词:加工精度;加工误差来源;解决措施加工误差是指机械加工之后工件的实际几何尺寸以及表面质量与理论的尺寸、质量不相符合的现象。
在机械加工制造过程中,加工误差是必定会出现的,出现的加工误差又会对机械加工精度造成影响。
所以说,我们需要对加工过程中存在的误差来源来认真地梳理,发现其产生的规律,进一步使用对应的方法来减少误差的出现,从而使得最终的制造精度大幅提升。
1机械加工误差产生的原因1.1原理误差。
在加工的过程中没办法采用理想的加工运动方式而采用了近似的加工运动方式,由此产生的加工误差称为原理误差。
从实际的情况考虑,如果采用理论中的加工原理对工件进行加工,那么就需要十分复杂的加工机构来实现这一目标,这会造成资源的极大浪费。
机械加工企业只需要将加工件的误差控制在一定范围内,能够满足功能需求即可,并不需要提高成本来彻底消除误差。
因此,在实际加工中原始误差是一定会存在的,这就会给加工件的加工精度带来影响。
1.2机床误差。
机床是机械加工的必备条件,生产过程中的每一个环节,零部件的每一次加工都需要机床的参与。
所以说,机床自身的误差直接作用于零部件的制造精确度。
机床的制造误差包括机床的导轨精度误差、主轴的回转误差以及传动链误差。
导轨是机床的最关键部件之一,它起到确定机床其他零部件的相对位置、为刀具等加工部件的运动提供基准等作用。
导轨的精度误差主要来源于导轨本身在制造时产生的误差、导轨安装不正确以及导轨在运动较长时间后产生的磨损。
- 1、下载文档前请自行甄别文档内容的完整性,平台不提供额外的编辑、内容补充、找答案等附加服务。
- 2、"仅部分预览"的文档,不可在线预览部分如存在完整性等问题,可反馈申请退款(可完整预览的文档不适用该条件!)。
- 3、如文档侵犯您的权益,请联系客服反馈,我们会尽快为您处理(人工客服工作时间:9:00-18:30)。
如前所述,为保证工件的加工精度,工件加工前必须正确的定位。
所谓正确的定位,除应限制必要的自由度、正确地选择定位基准和定位元件之外,还应使选择的定位方式所产生的误差在工件允许的误差范围以内。
本节即是定量地分析计算定位方式所产生的定位误差,以确定所选择的定位方式是否合理。
使用夹具时造成工件加工误差的因素包括如下四个方面:( 1 )与工件在夹具上定位有关的误差,称为定位误差Δ D ;( 2 )与夹具在机床上安装有关的误差,称为安装误差Δ A ;( 3 )与刀具同夹具定位元件有关的误差,称为调整误差Δ T ;( 4 )与加工过程有关的误差,称为过程误差Δ G 。
其中包括机床和刀具误差、变形误差和测量误差等。
为了保证工件的加工要求,上述误差合成后不应超出工件的加工公差δ K ,即Δ D + Δ A + Δ T + Δ G ≤δ K本节先分析与工件在夹具中定位有关的误差,即定位误差有关的内容。
由定位引起的同一批工件的设计基准在加工尺寸方向上的最大变动量,称为定位误差。
当定位误差Δ D ≤ 1/3 δ K ,一般认为选定的定位方式可行。
一、定位误差产生的原因及计算造成定位误差的原因有两个:一个是由于定位基准与设计基准不重合,称为基准不重合误差(基准不符误差);二是由于定位副制造误差而引起定位基准的位移,称为基准位移误差。
(一)基准不重合误差及计算由于定位基准与设计基准不重合而造成的定位误差称为基准不重合误差,以Δ B 来表示。
图 3 -61a 所示为零件简图,在工件上铣缺口,加工尺寸为 A 、 B 。
图3-61b 为加工示意图,工件以底面和 E 面定位, C 为确定刀具与夹具相互位置的对刀尺寸,在一批工件的加工过程中 C 的位置是不变的。
加工尺寸 A 的设计基准是 F ,定位基准是 E ,两者不重合。
当一批工件逐个在夹具上定位时,受尺寸S ±δ S /2 的影响,工序基准 F 的位置是变动的,F 的变动影响 A 的大小,给 A 造成误差,这个误差就是基准不重合误差。
显然基准不重合误差的大小应等于定位基准与设计基准不重合而造成的加工尺寸的变动范围,由图3-61b 可知:Δ B =A max-A min =S max-S min= δ SS 是定位基准 E 与设计基准 F 间的距离尺寸。
当设计基准的变动方向与加工尺寸的方向相同时,基准不重合误差就等于定位基准与设计基准间尺寸的公差,如图3-61 ,当S 的公差为δ S ,即Δ B = δ S (3-2 )当设计基准的变动方向与加工尺寸方向有一夹角(其夹角为β)时,基准不重合误差等于定位基准与设计基准间距离尺寸公差在加工尺寸方向上的投影,即Δ B = δ S × cos β (3-3)当定位基准与设计基准之间有几个相关尺寸的组合,应将各相关连的尺寸公差在加工尺寸方向上投影取和,即式中δ i ——定位基准与工序基准之间各相关连尺寸的公差(mm );β i ——δ i 的方向与加工尺寸方向之间的夹角(0 )。
式(3-4 )是基准不重合误差Δ B 的一般计算式.(二)基准位移误差及计算由于定位副的制造误差而造成定位基准位置的变动,对工件加工尺寸造成的误差, 称为基准位移误差,用Δ Y 来表示。
显然不同的定位方式和不同的定位副结构,其定位基准的移动量的计算方法是不同的。
下面,分析几种常见的定位方式产生的基准位移误差的计算方法:1 .工件以平面定位工件以平面定位时的基准位移误差计算较方便。
如图3-61 所示的工件以平面定位时,定位基面的位置可以看成是不变动的,因此基准位移误差为零,即工件以平面定位时Δ Y =02 .工件以圆孔在圆柱销、圆柱心轴上定位工件以圆孔在圆柱销、圆柱心轴上定位、其定位基准为孔的中心线,定位基面为内孔表面。
如图3-62 所示,由于定位副配合间隙的影响,会使工件上圆孔中心线(定位基准)的位置发生偏移,其中心偏移量在加工尺寸方向上的投影即为基准位移误差Δ Y。
定位基准偏移的方向有两种可能:一是可以在任意方向上偏移;二是只能在某一方向上偏移。
当定位基准在任意方向偏移时,其最大偏移量即为定位副直径方向的最大间隙,即Δ Y =X max=D max—d 0min= δ D + δ d0 +X min(3-5 )式中X max——定位副最大配合间隙(mm );D max——工件定位孔最大直径(mm );d 0min——圆柱销或圆柱心轴的最小直径(mm );δ D——工件定位孔的直径公差(mm );δ d0——圆柱销或圆柱心轴的直径公差(mm );X min——定位所需最小间隙,由设计时确定(mm )。
当基准偏移为单方向时,在其移动方向最大偏移量为半径方向的最大间隙,即Δ Y = (1/2 )X max= (1/2 )( D max-d 0min)= (1/2 )(δ D + δ d +X min)(3-6 )如果基准偏移的方向与工件加工尺寸的方向不一致时,应将基准的偏移量向加工尺寸方向上投影,投影后的值才是此加工尺寸的基准位移误差。
当工件用圆柱心轴定位时,定位副的配合间隙还会使工件孔的轴线发生歪斜,并影响工件的位置精度,如图3-63 所示。
工件除了孔距公差还有平行度误差,即式中L 1 ——加工面长度(mm );L 2 ——定位孔长度(mm )( 3 )工件以外柱圆在V 形块上定位工件以外圆柱面在V 形块上定位时,其定位基准为工件外圆柱面的轴心线,定位基面为外圆柱面。
若不计V 形块的误差,而仅有工件基准面的形状和尺寸误差时,工件的定位基准会产生偏移,如图3 -64a 、b 所示。
由图3-64b 可知,仅由于工件的尺寸公差δ d 的影响,使工件中心沿Z 向从O 1 移至O 2 ,即在Z 向的基准位移量可由下式计算式中δ d ——工件定位基面的直径公差(mm );α /2 —— V 形块的半角(0 )。
位移量的大小与外圆柱面直径公差有关,因此对于较精密的定位,需适当提高外圆的精度。
V 形块的对中性好,所以沿其X 方向的位移为零。
当用α =90 0 的V 形块,定位基准在Z 向的位移量可由下式计算如工件的加工尺寸方向与Z 方向相同,则在加工尺寸方向上的基准位移误差为Δ Y =O 1O 2=0.707δ d(3-10 )如在加工尺寸方向上与Z 有一夹角β,则在加工尺寸方向上的基准位移误差为(三)定位误差的计算由于定位误差Δ D 是由基准不重合误差和基准位移误差组合而成的。
因此在计算定位误差时,先分别算出Δ B 和Δ Y ,然后将两者组合而得Δ D 。
组合时可有如下情况:1 .Δ Y ≠ 0 ,Δ B =0 时,Δ D =Δ B (3-12 )2 .Δ Y =0 ,Δ B ≠ 0 时,Δ D = Δ Y (3-13 )3 .Δ Y ≠ 0 ,Δ B ≠ 0 时,如果工序基准不在定位基面上:Δ D = Δ B + Δ Y (3-14 )如果工序基准在定位基面上,Δ D = Δ B ±Δ Y (3-15 )“ + ”、“—”的判别方法为:①分析定位基面尺寸由大变小(或由小变大)时,定位基准的变动方向;②当定位基面尺寸作同样变化时,设定位基准不动,分析工序基准变动方向;③若两者变动方向相同即“ + ”,两者变动方向相反即“—”。
二、定位误差计算实例例3-1钻铰图3-65 所示的零件上φ 10H7 的孔,工件以孔定位,定位销直径求:工序尺寸50 ± 0.07mm 及平行度的定位误差。
解:(1)工序尺寸50 ± 0.07mm 的定位误差Δ B = 0mm( 定位基准与工序基准重合)按式(3-5 )得:Δ Y =δ D +δ d 0+Xmin =0.021+0.009+0.007= 0.037mm则由式(3-12)得Δ D=Δ Y = 0.037mm(2) 平行度0.04mm 的定位误差同理, Δ B = 0mm按式(3-7 )得:则平行度的定位误差为Δ D =Δ Y = 0.018mm例3-2 如图3-66 所示,用角度铣刀铣削斜面,求加工尺寸为39 ± 0.04mm 的定位误差。
解:Δ B = 0mm (定位基准与工序基准重合)按式(3-11 )得Δ Y =0.707 δ d cos β =0.707 × 0.04 × 0.866= 0.024mm按式(3-12 )得Δ D = Δ Y = 0.024mm例 3-3 如图 3-67 所示,工件以外圆柱面在 V 形块上定位加工键槽,保证键槽深度,试计算其定位误差。
解:Δ B = ( 1/2 )δ d = ( 1/2 )× 0.025= 0.0125mmΔ Y =0.707 δ d =0.707 × 0.025= 0.0177mm因为工序基准在定位基面上,所以Δ D = Δ B ±Δ Y ,经分析,此例中的工序基准变动的方向与定位基准变动的方向相反,取“—”号Δ D = Δ B —Δ Y =0.0177-0.0125= 0.0052mm例 3-4 如图 3-68 所示,以 A 面定位加工φ 20H8 孔,求加工尺寸40 ± 0.1mm 的定位误差。
解:Δ Y = 0mm (定位基面为平面)工序基准 B 与定 mm 位基准 A 不重合,因此将产生基准不重合误差Δ D = Δ B = 0.15mm例 3-5 如图 3-69 所示,工件以 d 1 外圆定位,加工φ 10H8 孔。
已知:求加工尺寸40 ± 0.15mm 的定位误差。
解:定位基准是 d 1 的轴线 A ,工序基准则在 d 2 的外圆的母线上,是相互独立的因素,可按式( 1-14 )合成三、工件以一面两孔组合定位时的定位误差计算在加工箱体、支架类零件时,常用工件的一面两孔定位,以使基准统一。
这种组合定位方式所采用的定位元件为支承板、圆柱销和菱形销。
一面两孔定位是一个典型的组合定位方式,是基准统一的具体应用。
1 .定位方式工件以平面作为主要定位基准,限制三个自由度,圆柱销限制二个自由度,菱形销限制一个自由度。
菱形销作为防转支承,其长轴方向应与两销中心连线相垂直,并应正确地选择菱形销直径的基本尺寸和经削边后圆柱部分的宽度。
图3-70 为菱形销的结构,表3-13 为菱形销的尺寸。
表 3-13 菱形销的尺寸(mm)d>3~6>3~6>8~20>20~24>24~30>30~40>40~50B d-0.5d-1d-2d-3d-4d-5d-6b 11233345b23455682 .菱形销的设计图 3-71 所示,当孔距为最大尺寸,销距为最小尺寸时,菱形销的干涉点发生在 A 、 B 。