电镀铬层发花 呈灰色的处理方法
镀硬铬故障分析:镀层黑暗无光泽且表面全部有麻点

镀硬铬故障分析:镀层黑暗无光泽且表面全部有麻点(1)可能原因:三价铬离子过多原因分析:镀铬液中的三价铬离子是铬电沉积过程中Cr6+在阴极上还原产生的,与此同时,Cr3+在阳极上又将重新被氧化成Cr6+,所以,Cr6+在镀铬液中的含量在一定条件下可达到平衡,平衡时的浓度取决于阴、阳极面积之比,一般为SA:Sk=2:1。
Cr3+是阴极胶体膜骨架,是阴极胶体膜的主要成分,只有当镀铬液中含有一定的Cr3+时,铬的沉积过程才能正常进行。
普通镀铬液中三价铬的最佳含量取决于镀液的组成、工艺条件及杂质的含量,一般为2~4g/L(有资料报道:Cr3+含量大约为铬酸含量的l%~2%),不允许超过8g/L。
当Cr3+过低时,相当于SO42-含量偏高时出现的现象,使阴极膜不连续,镀液的分散能力差,而且硬度低、光泽性差、电流效率也较低,而且只有在较高的电流密度下才产生铬的沉积。
当Cr3+过高时,相当于SO42-含量不足,阴极膜增厚,不仅显著降低镀液的导电性,使槽电压升高,而且镀铬层的光亮度范围缩小,工件的尖端或边缘会出现烧焦,如果阴极电流密度较低时,会使工件深凹处镀不上铬,还会引起镀层产生暗色、脆性及斑点等。
严重时,只能产生粗糙、灰色镀层。
新配制镀液Cr3+的产生方法①采用大面积阴极电解。
电解的条件是阴极面积必须大于阳极面积,镀液中必须含有足够量的硫酸。
在电解时,阴极反应式为Cr2072-+14H++6e一→2Cr3++7H2O即阴极上发生Cr6+的还原,此反应若无硫酸存在,反应即刻停止。
阳极反应式为2Cr3++7H20一6e一→Cr2072-+14H+即阳极上发生Cr6+的氧化。
在阴极面积大于阳极面积的情况下,六价铬的还原趋势大于三价铬的氧化趋势,总的结果使三价铬含量升高。
相反,若在阴极面积小于阳极面积的情况下电解,则使三价铬的含量逐渐降低。
②用还原剂将Cr6+还原产生三价铬。
还原六价铬的还原剂有酒精、草酸和冰糖等,较为常用的是酒精(98%),用量为0.5ml/L。
电镀产生问题原因及对策

塑料制品表面电镀故障之成因及对策一、预处理及化学镀故障的排除待续!完完!三、循环测试故障的排除完五、焦磷酸盐闪镀铜常见故障的排除完六、氰化闪镀铜常见故障的排除八、氰化镀铜合金故障的排除完完九、光亮镀镍常见故障的排除一、ABS制品表面酸性镀铜故障的排除未完待续复杂形状塑料大件电镀麻点产生的原因及对策董兴华摘要从工艺试验和实际生产方面找出了复杂形状塑料大件电镀产生麻点的主要原因,分析了产生麻点的各种因素,提出了减少麻点产生的办法和消除对策。
关键词塑料件电镀麻点对策新研制的电熨斗,有空心手柄、商标凸耳、大平面面积的侧身、散热窗、大穴内空、螺孔、凹槽、盲孔、通孔、非镀绝缘等部位,上壳为ABS塑料,形状复杂,受镀面积10 dm2。
常规塑料件电镀的工艺弊病很多,分析如下:1 麻点产生之因麻点的产生,主要来源于:(1)基材缺陷;(2)镀液;(3)工艺;(4)挂勾。
1.1 基材缺陷基材产生的麻点由模具精度和成型工艺及操作等造成,分布无规则。
轻微的缺陷孔,可通过电镀的填平将其减轻。
稍轻的缺陷孔,可机械抛磨后进行电镀。
严重的缺陷孔,视用户要求酌情处理。
1.2 镀液及其相关性(1)镀液性能差。
镀液成分含量改变,如酸铜中CuSO4过低,氯离子过高,光亮剂失调(S类光亮剂),表面活性剂过少。
(2)镀液污染。
酸铜镀液被各种杂质污染,如镍、磷、一价铜、灰尘、有机物等杂质。
(3)水质不洁、清洗不良。
清洗水质中含有悬浮物、细绒、灰尘等,工件清洗不彻底,工件上的孔眼坑穴带入杂质溶液等。
(4)气源不洁,管路系统不良。
①由空气搅拌系统带入杂质,如大气中灰尘、细绒等,从气泵吸入口进入镀液;②不同镀种的镀液空气搅拌,共用同一气泵供气,且无溶液防回流装置操作,造成镀液交叉污染;③管道系统槽外部分送气,使用镀锌钢管,且低于镀液面安装,引起停气后镀液回流,腐蚀管道内壁,废物又被气泵送入镀槽,造成污染。
(5)过滤效率低。
过滤镀液的流量和滤芯截留杂质的能力不够,过滤出水管放置不当。
装饰性镀铬故障处理

装饰性镀铬故障处理1.各种常见故障的产生原因及其处理方法1.1覆盖能力差1.1.1产生原因(1)镀铬中铬酸浓度过低;(2)硫酸根比值过高或过低;(3)镀液中三价铬含量过高;(4)氯离子含量过高;(5)阳极表面有氧化膜电流弱;(6)入槽时电流密度太小;(7)底层表面钝化(镍钝化时)。
1.1.2处理方法(1)分析调整铬酸(标准含量200~250g/L)与硫酸(2~2.5g/L)质量浓度之比。
铬酸的质量浓度过低,就会导致均镀能力差,并出现露黄(镍)等缺陷。
(2)分析确认硫酸根含量高,可以适当增加铬酸的质量浓度或用碳酸钡去除,一般2g/L碳酸钡可除掉1g/L硫酸。
过低时,则补加硫酸至工艺要求。
一般硫酸根比值在(80~125):1范围内。
(3)以大面积阳极和小面积阴极进行电解,将三价铬含量降至工艺要求。
镀液中三价铬含量过高,不仅会影响均镀能力,还会出现雾状和蓝膜现象。
镀液中Cr3+的含量应控制在2~5g/L。
(4)除去氯离子一般采用较经济的电解法。
镀液中氯离子质量浓度超过0.5g/L时,均镀能力、电流效率和镀层的结合力都显著下降,同时铬层出现雾状及发花。
可加入硫酸银、碳酸银、氧化银等,使氯离子与银离子发生反应成氯化银沉淀,但成本较高。
一般多采用电解处理(液温7.°C),氯离子在阳极失去电子生成滤器溢出。
为防止氯离子的积累,配制镀液和补加应使用氯离子的质量浓度一般控制在0.03g/L以下。
(5)取出阳极板将其置于稀盐酸或氢氧化钠溶液中进行清洗,以除去黄色铬酸铅(氧化膜),使其呈活化状态。
(6)增大入槽电流密度。
电流密度及溶液温度对镀液性能(如均镀能力、电流效率等)影响很大。
必须严格控制在工艺范围内。
(7)从镀镍工序着手排除。
镀铬的均镀(覆盖)能力主要取决于溶液的组成和正确的操作,但中间镀层的质量和工艺流程是否合理也会对其有一定的影响。
当镀镍液中杂质含量过高时,在镀件德低电流部位铬沉积困难。
造成镀层不均。
三价铬电镀产品镀层表面长霉怎么办
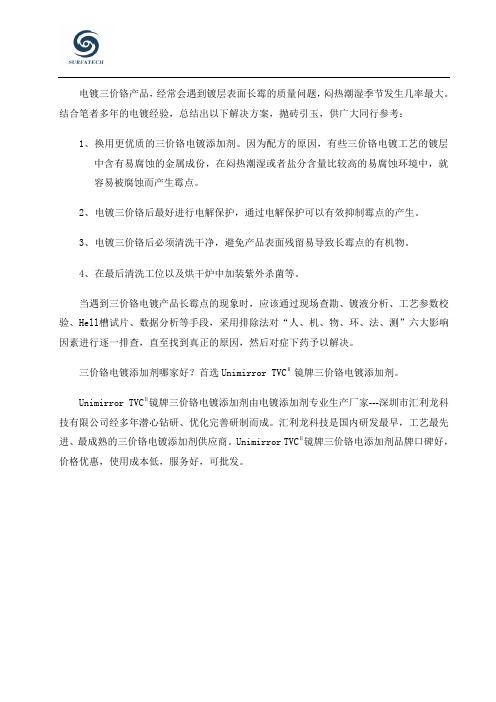
电镀三价铬产品,经常会遇到镀层表面长霉的质量问题,闷热潮湿季节发生几率最大。
结合笔者多年的电镀经验,总结出以下解决方案,抛砖引玉,供广大同行参考:
1、换用更优质的三价铬电镀添加剂。
因为配方的原因,有些三价铬电镀工艺的镀层
中含有易腐蚀的金属成份,在闷热潮湿或者盐分含量比较高的易腐蚀环境中,就
容易被腐蚀而产生霉点。
2、电镀三价铬后最好进行电解保护,通过电解保护可以有效抑制霉点的产生。
3、电镀三价铬后必须清洗干净,避免产品表面残留易导致长霉点的有机物。
4、在最后清洗工位以及烘干炉中加装紫外杀菌等。
当遇到三价铬电镀产品长霉点的现象时,应该通过现场查勘、镀液分析、工艺参数校验、Hell槽试片、数据分析等手段,采用排除法对“人、机、物、环、法、测”六大影响因素进行逐一排查,直至找到真正的原因,然后对症下药予以解决。
三价铬电镀添加剂哪家好?首选Unimirror TVCⅡ镜牌三价铬电镀添加剂。
Unimirror TVCⅡ镜牌三价铬电镀添加剂由电镀添加剂专业生产厂家---深圳市汇利龙科技有限公司经多年潜心钻研、优化完善研制而成。
汇利龙科技是国内研发最早,工艺最先进、最成熟的三价铬电镀添加剂供应商。
Unimirror TVCⅡ镜牌三价铬电添加剂品牌口碑好,价格优惠,使用成本低,服务好,可批发。
钢铁件产品电镀如何除去表面挂灰

钢铁件产品电镀如何除去表面挂灰
在钢铁件电镀过程中,常常遇见这样的情况:工件经过化学除油和电解除油后表面有一层挂灰,用手轻轻一抹就掉,如不抹去挂灰,电镀后光洁的表面易出现花斑。
挂灰的产生有如下几种情况:
1、材质本身含碳量较高,经过酸蚀等工序后,一部分铁被融解掉,剩下的碳组份形成挂灰。
2、工件在加工过程中使用的防锈油或润滑油中含有碳微粒,当吸附在工件表面的油被除掉后,碳微粒由于表面能很大,牢牢吸附在工件表面.形成挂灰。
3、工件加工后,由于存放时间长.空气中的尘埃吸附在油膜上,当油膜被除掉时,尘埃紧紧吸附在工件表面,形成挂灰。
现在大部分工厂对付挂灰的有效办法是手工擦洗,手工擦洗最大的问题是效率低,需要大量的人工。
下面有几种方法可去除挂灰,供参考:
1.硫酸30—50克/L
铬酐200—300克/L,
温度窒温
时间2—3分钟
该方法对环境污染大,废水处理成本高。
2、硝酸30—50克/L
双氧水5—15克/L
温度窒温
时间30---60秒
该方法在使用硝酸时酸雾大,需要强力抽风。
3、双氧水30—50克/L
草酸25—40克/L
硫酸5克/L
温度15—30℃
时间30---60秒
4、双氧水35—40克/L
氢氧化铵lO—15克/L
尿素5一lO克/L
苯甲酸0.5一l克/L
温度15—30’12
时间l—3分钟
该方法寿命较短。
电镀装饰镀铬中的发花故障处理

电镀装饰镀铬中的发花故障处理
装饰镀铬中的发花故障处理
摘要:在实际生产过程遇到的问题,现将其整理成文与大家分享。
我厂的车把是在直线电镀自动线上生产的,按常规的氰铜-亮镍-装饰铬工艺进行电镀。
长期以来镀铬生产一直正常,但从四月底开始,发现铬层发花。
为此,对镀铬溶液进行了调整,使溶液中各参数在工艺规范内。
铬酸280-300g/l
硫酸 2.4-2.7g/l
三价铬2-4g/l
XXX(产品名称略)0.04g/L
温度53-57℃
阴极电流密度15-30A/dm2
然后再经过六小时电解,但发花故障未排除。
于是,我们分析了几种可能引起镀铬层发花的因素:
1.XXX在抑制铬雾的同时也给抛光油灰的排除带来不便。
车把是管状零件,抛光油灰从孔洞进入后,难于去除。
在加温的铬酸溶液中溶出,逐步积累到-定程度,当零件进槽时沾上漂浮在液面的油灰,即产生不规则的花斑。
2.我厂配镀铬槽没有用去离子水而是用冷凝水,镀铬前的清洗为自来水。
长期生产,镀铬槽中氯离子积累过多,而XXX又抑制了阳极氯气的析出,使镀铬槽中氯离子含量超过200PPM,因此,镀铬层发花。
针对上述可能原因,我们对镀铬槽液进行了清理和电解,结果镀出的车把仍然发花。
在镀铬原因排除后,转而我们怀疑亮镍槽中初级光亮剂含量太高。
经用赫尔槽检查光亮镀镍溶液,结果亮镍槽完全正常。
金属电镀出现不良现象的原因与解决方法
钝化外观偏浅(呈蓝带黄或金黄)
孔位颜色过深
钝化外观不均
耐腐蚀性能达不到要求
孔位周围发白
孔位颜色过深,呈现焦黄色
钝化后工件发花(呈地图纹状)
1、pH值过高 2、药液杂质过多 3、槽液浓度偏低 ①PH值过高 ②时间过短 ③Cr3+浓度低
1、调整pH值 2、排去1/5旧槽液,重新以原液补充添加 3、补加A01-435DC ①加入适量硝酸 ②延长钝化时间 ③ 加入适量原液 ①加入硝酸 ②排污,补充建浴液 ③加强搅拌 ①加碱升高PH值
产品颜色过浅,呈金黄色而不是五彩
①PH值过高 颜色不均匀,产品出现花斑(地图状花纹) ②或杂质太多 ③槽液循环搅拌不良 孔位发白、工件边缘泛紫光 ①PH值过低
黑锌
不良现象 原因 1、PH值过低 2、槽液中铁离子过高 3、槽液温度过高 4、钝化时间过短 5、B剂浓度不足 6、电镀外观过于光亮 1、pH值偏低 2、温度偏高 3、钝化时间过短 4、搅拌不足 1、pH值偏低 2、钝化时间过长 3、槽液温度偏高 处理 1、校正酸度计,调整PH值至操作范围 2、更新部份槽液或重新建浴 3、降低槽液温度 4、延长钝化时间 5、适当补充B剂 6、调整电镀 1、调高pH值至操作范围 2、降低温度 3、适当延长钝化时间 4、增强搅拌 1、调高pH值至操作范围 2、缩短钝化时间 3、降低温度
1)镀液中锌离子浓度应维持在10~15g/L 2)保持槽液温度20~30℃ 3)见A项第2点 4)控制氢氧化钠浓度在100~150g/L保持氢氧化钠与锌离子浓 度之比在10~12之间。 1)分析调整。控制锌离子浓度在10~15g/L,氢氧化钠浓度与 锌离子的比值10~12为宜。 2)适量补加A02-350A光剂。 3)降低电流密度。 4)保持槽液温度20~30℃。 1)分析调整,控制锌离子浓度在10~15g/L,氢氧化钠浓度与 锌离子的比值10~12为宜。 2)根据霍尔槽试片,适量补加A02-350B光剂。 3)提高电流密度。 1)在工艺允许使用范围内提高锌离子浓度。 2)根据霍尔槽试片,适量补加A02-350A光剂。 3)加净化剂C或软水剂D。 4)加强前处理。 适当增加A02-350B用量;在过滤机加入锌粉及助滤剂硅藻土以除 杂
逐个分析:镀铬层发花、发雾的原因!
逐个分析:镀铬层发花、发雾的原因!造成铬层发花或发雾的原因很多,其中大多是底镀层或其他外部原因引起的。
如镀镍液中糖精太多;镍层抛光时的线速度;抛光过的零件镀铬前表面有油或有抛光膏;镀镍出槽时形成双性电极;镀铬时挂具弹得不紧;铜锡合金底层中锡含量太高;镀铬时的温度太高;镀铬电源波形有问题或镀铬液中氯离子过多等。
分析故障时,可以取一批在其他镀铬液中套铬,没有出现发花或发雾的零件浸入有故障的镀铬液中试镀,假使本单位没有其他镀铬液,可以将刚镀好的光亮镀镍(未经抛光)的零件,放在新配制的5%(重量)硫酸中浸2 min,进行充分的活化后直接套铬。
1假如这样套铬所得的铬层良好,不出现发花或发雾现象,那么故障起源于镀铬以前,与镀铬液及镀铬电源无关。
如果起源于镀铬以前,就要根据各单位的具体情况采取不同的措施。
如采用光亮镀镍直接套铬时,应检查镀镍液中糖精是否太多;镀好光亮镍出槽时是否有双性电极现象,亮镍出槽到镀铬相隔的时间是否过长和镀铬前的硫酸活化液浓度是否太稀或过高。
镀镍液中糖精太多造成铬层发花的现象,一般在零件的尖端和边缘较明显。
这时可用电解的方法纠正双性电极引起的铬层发花,有规则地出现在零件的一个侧面(即靠近镀镍出槽时另一阴极的侧面)。
这时要在镀镍出槽时关掉电源或把电流调至最小时取出零件,或者同时取出阴极上所有的零件进行检查和纠正。
零件镀好亮镍出槽到镀铬的时间相隔在2min之内,一般可以不必进行硫酸活化而直接套铬,若时间间隔在2min以上,那么最好用3%~5%的硫酸活化后套铬。
如果对活化液的浓度有怀疑时,可以按分析进行调整或更换新液。
2假如是零件镀暗镍或半亮镍抛光后套铬,特别要注意抛光轮的大小和零件抛光后的除油和活化。
由于镍层容易钝化所以抛光时抛光轮太大、转速太快或操作者抛光时把零件压在抛光轮上的力量较大,都将使镍层在抛光时温度升高而钝化。
在钝化的镍层上套铬,会出现发花的现象。
这种现象夏天更容易出现。
抛光后的零件,必须经过除油和活化。
镀铜镀层发花或发雾的原因与处理方法【干货技巧】
镀铜镀层发花或发雾的原因与处理方法是怎样的呢?下面小编为大家介绍一下。
(1)镀前处理不良,零件表面有油原因分析及处理方法:检查工件发花的部位,若工件的向下面或挂具上部的工件上出现发花现象,可能是清洗或镀液中有油而引起的。
光亮硫酸盐镀铜对油污特别敏感,不管是毛坯上的油在镀前处理时未除净,还是镀前的清洗水或镀液中有微量的油,甚至是操作人员的手触摸了镀前的零件,都会使铜镀层发花。
要确定故障的起源是否在镀前,用经过良好除油的工件进行对比试验,假使原来镀铜出现发花或发雾,采用良好的前处理后,镀层发花或发雾现象消失了,说明原来的镀前处理有问题,应加强镀前处理。
处理方法:加强镀前处理(2)清洗水或镀液中有油原因分析及处理方法:检查清洗水的水质情况,如清洗水是否干净、清澈,有无油污漂浮,槽壁是否干净,若清洗水槽和水质没有问题,最后检查镀液中是否有油,检查的方法如下:第一,从现象上判断(液面是否漂浮油污);第二,通过小试验判断,即取一定量的故障液做烧杯试验,先要使阴极板上能看到类似于生产中的故障现象,接着对试验液进行除油处理,另外再取相同体积的故障液进行双氧水一活性炭处理,然后分别进行试验(试验液经过处理后,需补充光泽剂)。
若用双氧水一活性炭处理过的镀液仍有发花或发雾,而经过除油处理的镀液不再出现发花或发雾,那么原镀液受到油的污染,应进行除油处理。
假如用双氧水一活性炭处理后的镀液和经过除油处理的镀液一样,都不出现发花或发雾,那么原镀液可能是有机杂质过多。
处理方法:①清洗水有油的处理方法a.用毛边纸吸附液面漂浮的油污,并擦拭槽壁上黏附的油污;b.将清洗水放空;c.用热化学除油液擦拭水槽内壁2次,并用干净水冲洗2次,并将槽内的积水放空;用10%H2S04擦拭槽内壁,再冲洗2次,将积水放空;d.注满水槽的水,检查液面,若无油污漂浮,即可使用,若仍有油污漂浮,按上述步骤再次清洗②镀液中油污的处理方法。
去除镀液中油类杂质,一般用乳化剂将油乳化,然后用活性炭将乳化了的油和过量的乳化剂吸附除去。
电镀装饰镀铬中的发花故障处理
装饰镀铬中的发花故障处理摘要:在实际生产过程遇到的问题,现将其整理成文与大家分享。
我厂的车把是在直线电镀自动线上生产的,按常规的氰铜-亮镍-装饰铬工艺进行电镀。
长期以来镀铬生产一直正常,但从四月底开始,发现铬层发花。
为此,对镀铬溶液进行了调整,使溶液中各参数在工艺规范内。
铬酸280-300g/l硫酸 2.4-2.7g/l三价铬2-4g/lXXX(产品名称略)0.04g/L温度53-57℃阴极电流密度15-30A/dm2然后再经过六小时电解,但发花故障未排除。
于是,我们分析了几种可能引起镀铬层发花的因素:1.XXX在抑制铬雾的同时也给抛光油灰的排除带来不便。
车把是管状零件,抛光油灰从孔洞进入后,难于去除。
在加温的铬酸溶液中溶出,逐步积累到-定程度,当零件进槽时沾上漂浮在液面的油灰,即产生不规则的花斑。
2.我厂配镀铬槽没有用去离子水而是用冷凝水,镀铬前的清洗为自来水。
长期生产,镀铬槽中氯离子积累过多,而XXX又抑制了阳极氯气的析出,使镀铬槽中氯离子含量超过200PPM,因此,镀铬层发花。
针对上述可能原因,我们对镀铬槽液进行了清理和电解,结果镀出的车把仍然发花。
在镀铬原因排除后,转而我们怀疑亮镍槽中初级光亮剂含量太高。
经用赫尔槽检查光亮镀镍溶液,结果亮镍槽完全正常。
这样铬槽和亮镍槽都完全正常,为什么镀铬后会发花呢?是不是镀亮镍后的回收液、清洗水或者镀铬前的弱腐蚀液、清洗水中含有油污和灰尘?经用肉眼和洁、纸检查,均未发现异常。
然后,我们采用手动跳工位的办法试验,当跳过二个亮操回收工位时,镀铬后不发花。
接连试了五挂均不发花。
尔后又试验几挂不跳过亮镍回收工位的,又全部发花。
这样镀铬发花的真正原因找到了,是亮镍回收槽的毛病。
因为亮镍回收槽长期使用,积累了过多的有机物和氯离子。
当镀好亮镍的零件浸入回收槽中,污染物将不同程度地吸附在亮镍层表面,致使镀铬后发生花斑。
最后,经清洗亮镍因收槽,更换回收水后,镀铬发花故障就消除了饰性镀铬故障及其处理方法:铬层发花或发雾可能原因原因分析及处理方法(1)镀镍液中糖精太多发花或发雾在工件的尖端和边缘较为明显。
- 1、下载文档前请自行甄别文档内容的完整性,平台不提供额外的编辑、内容补充、找答案等附加服务。
- 2、"仅部分预览"的文档,不可在线预览部分如存在完整性等问题,可反馈申请退款(可完整预览的文档不适用该条件!)。
- 3、如文档侵犯您的权益,请联系客服反馈,我们会尽快为您处理(人工客服工作时间:9:00-18:30)。
电镀铬层发花呈灰色的处理方法
现代电镀网3月24日讯:
在电镀装饰铬生产中常常碰到套铬层发花,铬镀层呈灰色无金属光泽的情况,而将铬镀层退除后下面的镍镀层表面是正常的。
这种故障形成的原因主要是:①光亮镍层本身的套铬性差,其中光亮镀镍的添加剂对镍镀层的套铬性有影响,如果镀镍光亮添加剂清洗性差,就会导致零件表面残留添加剂清洗不净,零件套铬后铬层发花。
②镀镍层在套铬之前钝化,这是电镀镍后的清洗时间过长导致了镀镍表面的钝化。
处理这种故障的方法有:选择套铬性好的光镍添加剂;在光亮镀镍后增加电镀无光泽镍或冲击镍等(镍镀液中不添加光泽剂,电镀时间控制在不影响光亮镍的光亮外观即可),无光泽镍由于没有添加剂而具有优良的清洗性和套铬性;在光亮镍后增加清洗工序确保清洗干净;同时注意缩短清洗时间防止镍层钝化;在镀铬前增加镍活化工序活化镍镀层,活化可以采用化学活化和电化学活化。
另外注意电镀自动线各槽停留时间不能调整可能导致电镀光亮镍后零件在水中的停留时间长,引起镍镀层钝化套铬后表面发花的问题,可以在停留时间较长的水槽中加入0.59/L~l9/L的NaHC03来避免镍表面钝化。