第12章压铸模设计实例与结构图例
压铸模具设计与制造

④、在压铸成型后,保证压铸件顺利从压铸模中脱出,且推出模体后,应无变 形、破损等现象的发生; ⑤、模具具备的强度和刚度承受压射力以及内浇口速度对模具的冲击; ⑥、在压铸过程中,控制和调节模具的热交换和热平衡; ⑦、最大限度发挥压铸机成型效率。
二、压铸模设计的基本原则
⑴、充分了解压铸件的用途和与其它结构件的装配关系,并根据压铸件的 结构特点、使用性能,在模具设计时分清主次,突出模具结构的重点以及结合模 具加工的工艺性,合理选择模具的分型面、型腔数量和布局形式、压铸件的推出 形式和侧向脱模形式。 ⑵、了解现场模具实际的加工能力,如现有的设备和可协作单位的装备情况, 以及操作人员的技术水平,结合实际地设计出符合现场加工能力的模具结构形式。
第二节
一、压铸模设计概述
压铸模设计基础
压铸时,压铸模、压铸机、压铸合金通过压铸工艺参数的相互联系协 调,共同完成压铸件的压铸成型过程。压铸模在压铸生产过程中的作用 如下: ①、确定浇注系统,特别是内浇口位置和导流方向以及排溢系统的 位置,它们共同决定着熔融金属的填充条件和成型状况; ②、压铸模是压铸件的复映,决定了压铸件的形状和精度; ③、模具成型表面的质量直接影响压铸件的表面质量以及脱模阻力 的大小;
2、 压铸模的分类
根据所使用的压铸机类型的不同,压铸模主要有以下几种基本结构形式: ⑴、热压室压铸机用压铸模 ⑵、立式冷压室压铸机用压铸模 ⑶、全立式压铸机用压铸模 ⑷、卧式冷压室压铸机用压铸模
五、压铸模具设计的发展趋势
为了适应用户对模具制造的短交货期、高精度、低成本的迫切要求,模具设 计必然会有如下发展趋势: ⑴、模具设计由经验设计阶段向理论计算和计算机辅助设计方向发展, CAD/CAM/CAE技术广泛用于制模业,使模具结构更趋科学合理,极大地提高模具加 工精度,缩短模具设计加工周期,减少产品开发时间。 ⑵、模具CAD/CAE/CAM正向集成化、三维化、智能化和网络化方向展; ⑶、提高模具标准化水平和模具标准化利用率; ⑷、模具向着精密、复杂、大型化的方向发展; ⑸、基于知识的工程(KBE)技术。
压铸模具结构设计

•回位 銷
•射嘴
• 機台設定最小厚度+10≦模具總厚度≦機台設定最大厚度-10
PPT文档演模板
压铸模具结构设计
• 四yout設計
••1.固定外模
•2.斜度配 •3. 斜銷 •4.滑塊入子 •5.冷卻孔 •6.固定模仁 •7.可動模仁 •8.料管 •9.湯口套
PPT文档演模板
•Y斷面圖(冷室型) •10.擋板 •11.滑塊座 •12.底板 •13.可動外模 •14.頂針 •15.頂針板 •16.頂針壓板 •17.分流子
• (10)每一套模具頂針直徑尺寸不宜太多種,允許範圍內直
徑
應盡量加大.
(11)按需求設置雙節頂針,扁頂針,套筒頂針.
(12)頂出裝置與滑塊等抽芯機構發生干涉時須安裝頂出
板
先行回位機構
(13)頂出行程一般為15~25mm(考慮產品頂出分模面
5~10mm)
PPT文档演模板
压铸模具结构设计
• 四.6.冷卻系統
PPT文档演模板
压铸模具结构设计
• 四.3.真空結構
•真空壓鑄機構
1.排氣口連接於
最後
充填位置. 2.排氣口連接於 模流最難充填位 置. 3.排氣口最小斷 面高度和截面積 要滿足充填需求 4.為達最佳效果 試模後修改為必 要.考慮修改方 PPT文档演模板
压铸模具结构设计
• 四.4.成型入子
•2).滑塊座:連接並帶動型芯在模具滑槽內運動
•3).傳動元件:帶動滑塊座作抽芯或插芯動作.一般用斜銷或油缸.
•4).限位元件:使滑塊在合模或開模後停留在要求位置.
•
斜度配:合模後壓緊滑塊,防止壓鑄時受壓力後退位
移.
•
檔 塊:使滑塊開模後停留合適位置.
压铸件结构设计 ppt课件
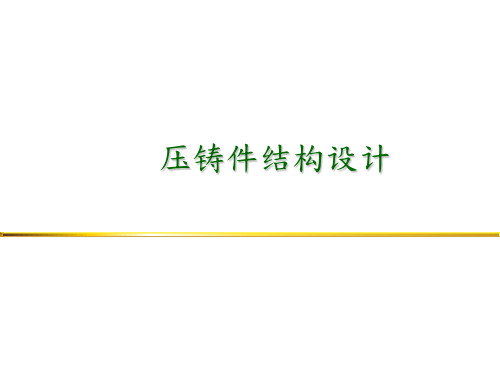
好的案例
说明
深入模穴尽量位置于 制品之同一方向。
型模固定侧之心型形 状﹐应避免因收缩而
固着。
压铸件结构设计
不好的案例
好的案例
说明
切面肉厚较厚处所﹐ 增强肋之厚度应与肉 厚均一。
肉厚需有均一之厚度 。
压铸件结构设计
不好的案例
好的案例
说明
为使深入之增强肋脱 模容易﹐尽量使用最 大之退缩倾斜﹒
阶级部角隅应尽量放 大R来连接。
压铸件结构设计
不好的案例
好的案例
说明
T形切面之接合面将 产生凹陷﹐在心型侧 边缘设置锲入改善之 。
由于型模构造更改﹐ 避免"A"部肉厚过薄 。
压铸件结构设计
压铸件结构设计
压铸件结构设计
同一产品内壁厚应尽量保持一致,且应 平滑过渡,不然容易产生卷气影响产品 强度,壁厚突然过度还会导致厚的地 方产生收缩,粘模,影响外观。
压铸件结构设计
铜合金
D
铝合金
L
锌合金 镁合金
脱模斜度查询表
压铸件结构设计
压铸件结构设计
压铸件结构设计
压铸件结构设计
压铸件结构设计
一般来说,除外模具分型面处外,产品上两壁相连处不管是钝角还是锐角 ,都需要做倒圆角处理。适当圆角不但有利于产品的成型,防止产品 开裂,还能有效的延长模具的寿命。当铸件的内角必须为清角时,应按 以下图片所示做产品结构。
压铸件结构设计
压铸件结构设计
压铸件结构设计
压铸件结构设计
压铸件结构设计
压铸件结构设计
内容大纲
产品的壁厚(模具成型的基础) 产品的拔模(模具脱模的保障) 产品的圆角(模具寿命的关键) 加强筋的设计(结构优化的手段)
压铸机结构及原理ppt课件
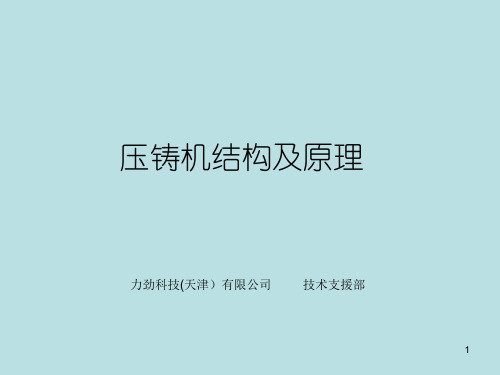
力劲科技(天津)有限公司 技术支援部
1
冷室压铸机结构
如图1-5所示为卧式冷室压铸机构成图,它由柱架、 机架、压射、液压、电气、润滑、冷却、安全防护 等部件组成。按机器零、部件组成的功能分类,我 们将卧式冷室压铸机分成合模、压射、液压传动、 电气控制、安全防护五大类。下面以力劲机械厂有 限公司生产的DCC280卧式冷室压铸机为例进行结 构分析。
模具冷却水观察窗--16 压射冲头-- 17
压射液压缸-- 18 快压射蓄能器-- 19
增压蓄能器-- 20 增压油路板组件-- 21 压射油路板组件-- 22
4
一、合模机构
合模机构主要起到实现合、开模动作和锁紧模具、顶出产品的作用。它主要由定型座 板、动型座板、拉杠(哥林柱)、曲肘机构、顶出机构、调型(模)机构等组成。图1-6 为合型(模)机构结构简图。
13
压铸机液压系统主要由液压泵、合开型(模)液压缸、顶出液压 缸、压射液压缸、调型(模)液压马达、液压控制元件、液压蓄 能器、过滤器、空气滤清器、热交换器组成。如图1-11所示为力 劲机械厂有限公司生产的DCC280液压传动系统部装图。
图1-11 DCC280液压传动系统部装图 1--液压泵 2--冷却器 3--主油箱 4--润滑泵 5--压射回油油箱 6--压射油路尾板组件7— 压射油路板组件8--顶出油路板组件(1) 9--顶出油路板组件(2) 10--空气滤清器14 11--调型(模)液压马达 12--合开型(模)油路板组件
9
4、曲肘润滑系统 曲肘是压铸机十分重要的运动构件。为了使其运动副的磨损减小,必须在运动副表面保持 适当的清洁的润滑油膜,而过量供油与供油不足同样有害,会产生附加热量、污染和浪费。 力劲机械厂有限公司生产的压铸机曲肘部分的润滑采用的是集中润滑系统。所谓集中润滑 系统,是由一个油泵提供一定排量、一定压力的润滑油,为系统中所有主、次油路上的分 流器供油,而由分流器将油按所需油量分配到各润滑点;同时,由控制器完成润滑时间、 次数和对故障报警、停机等功能,以实现自动润滑的目的。卧式冷室压铸机曲肘的润滑一 般选用脱压润滑泵,如图1-9所示,它有如下特点:
压铸模具课程案例

(三)其它缺陷 ➢裂纹 ➢孔穴 ➢缩孔 ➢铸件变形 ➢擦伤
Home
B
B
35
Introduction
第一篇:压铸原理及常用压铸合金
第四章 常用压铸合金
第一节 对压铸合金的要求
1)高温下有足够的强度和可塑性,无热脆性(或热脆性小)。 2)尽可能小的线收缩率和裂纹倾向,以免压铸件产生裂纹,使压
1)力学性能、抗拉强度 2)工作环境状态 3)精度要求 (2)工艺性能好 1)铸造工艺性; 2)机械加工工艺性; 3)表面处理工艺性。 (3)经济性好
Home
B
B
43
第一篇:压铸原理及常用压铸合金
第四章 常用压铸合金
第二节 压铸合金分类及主要性质 4. 锌合金成分控制 (1)标准合金成分
Introduction
Introduction
Home
B
B
39
Introduction
第一篇:压铸原理及常用压铸合金
第四章 常用压铸合金
第二节 压铸合金分类及主要性质
锌 合 金 的 应 用
Home
B
B
40
Introduction
第一篇:压铸原理及常用压铸合金
第四章 常用压铸合金
第二节 压铸合金分类及主要性质
一、锌合金 (二)锌合金成分控制 1 锌合金的特点
第一篇:压铸原理及常用压铸合金
第三章 液态金属充填铸型的特点
第二节 充填缺陷
➢术语含义 ➢分类 ➢危害性
一、金属液充填缺陷形成机理 (一)金属液流动缺陷 ➢ 型腔未被完全充满 ➢ 型腔被充满
Home
B
B
26
第一篇:压铸原理及常用压铸合金
压铸模课件

六、推出与复位机构 推出机构是将压铸件从模具的成形零件上脱出的机构;复位机构是指 在模具合模时,将推出机构回复到原始位置的机构。它包括推出、复
位和先复位、限位及导向零件,如图3-1中的推杆24、26、29、推杆
固定板34、推板33、复位杆30、推板导柱32和推板导套31等。 七、加热与冷却系统 因压铸件的形状、结构和质量上的需要,在模具上常需设置冷却和加 热装置,以达到压铸模的热平衡。 八、其他 除前述结构组成外,模具内还有其他如紧固用的螺钉、销钉,以及定 位用的定位件等。
6)分型面的选择应保证侧向活动型芯能顺利抽出、型芯放置方便及镶嵌件 安放方便。 上述原则对分型面的选择是重要的,但在实际设计中,要同时满足上述各 项原则是困难的,这时应在保证生产出合格压铸件的前提下,力求模具结 构简单、制造方便、成本低。
二、成形零件的设计 压铸模的成形零件在压铸成形过程中,受到高温、高压和高速的金属
2)整体镶块台阶尺寸见表3-2。
注:1.根据受力状态台阶可设在四侧或长边两侧。 2.组合镶块的台阶H和C,根据需要可选用表内尺寸系列。如在同一套板安装空 内组合镶块,其基本尺寸L则指装配后全部组合镶块的总外形尺寸。
3)组合式成形镶块固定部分长度见表3-3。
(2)圆型芯的主要尺寸圆型芯的主要尺寸见表3-4。
钉紧固的模具。如图3-10c所示,当镶块为圆柱形或型腔较浅时的模
具采用螺钉紧固,若是非圆形镶块时只适合于单型腔模具。 图3-11为镶块的其他固定方法。图3-11a所示为台阶和圆柱销定位螺 钉紧固,主要用于多件镶块的模具中;图3-11b所示为圆柱面定位, 压入镶块后,用螺钉将支承板与套板紧固,便于模具加工和更换易损 部位。
标注制造公差后得
同理,型腔深度尺寸
压铸模设计实例(tupian)
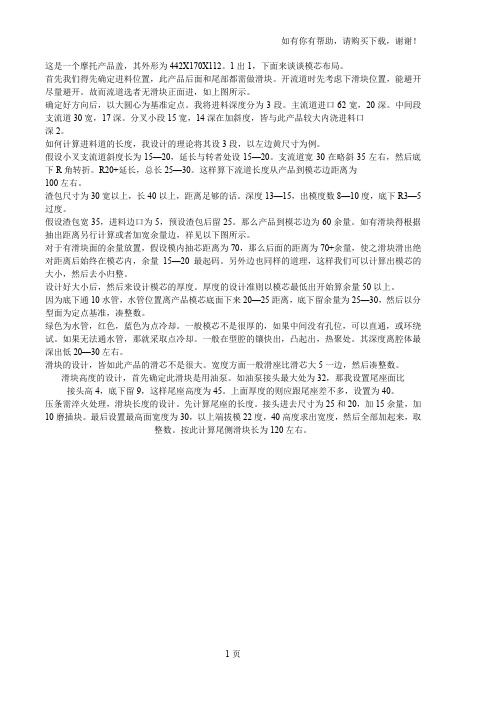
这是一个摩托产品盖,其外形为442X170X112。
1出1,下面来谈谈模芯布局。
首先我们得先确定进料位置,此产品后面和尾部都需做滑块。
开流道时先考虑下滑块位置,能避开尽量避开。
故而流道选者无滑块正面进,如上图所示。
确定好方向后,以大圆心为基准定点。
我将进料深度分为3段。
主流道进口62宽,20深。
中间段支流道30宽,17深。
分叉小段15宽,14深在加斜度,皆与此产品较大内浇进料口深2。
如何计算进料道的长度,我设计的理论将其设3段,以左边黄尺寸为例。
假设小叉支流道斜度长为15—20,延长与转者处设15—20。
支流道宽30在略斜35左右,然后底下R角转折。
R20+延长,总长25—30。
这样算下流道长度从产品到模芯边距离为100左右。
渣包尺寸为30宽以上,长40以上,距离足够的话。
深度13—15,出模度数8—10度,底下R3—5过度。
假设渣包宽35,进料边口为5,预设渣包后留25。
那么产品到模芯边为60余量。
如有滑块得根据抽出距离另行计算或者加宽余量边,祥见以下图所示。
对于有滑块面的余量放置,假设模内抽芯距离为70,那么后面的距离为70+余量,使之滑块滑出绝对距离后始终在模芯内,余量15—20最起码。
另外边也同样的道理,这样我们可以计算出模芯的大小,然后去小归整。
设计好大小后,然后来设计模芯的厚度。
厚度的设计准则以模芯最低出开始算余量50以上。
因为底下通10水管,水管位置离产品模芯底面下来20—25距离,底下留余量为25—30,然后以分型面为定点基准,凑整数。
绿色为水管,红色,蓝色为点冷却。
一般模芯不是很厚的,如果中间没有孔位,可以直通,或环绕试。
如果无法通水管,那就采取点冷却。
一般在型腔的镶快出,凸起出,热聚处。
其深度离腔体最深出低20—30左右。
滑块的设计,皆如此产品的滑芯不是很大。
宽度方面一般滑座比滑芯大5一边,然后凑整数。
滑块高度的设计,首先确定此滑块是用油泵。
如油泵接头最大处为32,那我设置尾座面比接头高4,底下留9,这样尾座高度为45。
压铸模设计
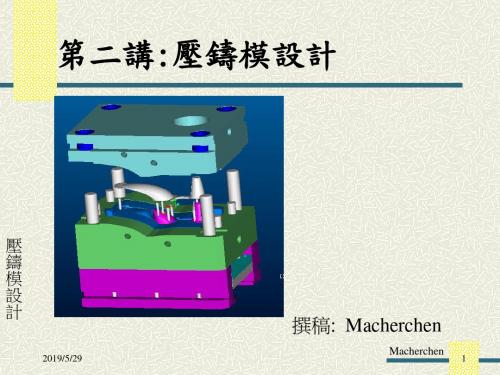
鑄 模 設
為基準,減去斜度值及加工余量,另一端按脫模斜度 相應增大.
計
2019/5/29
Macherchen
25
三.壓鑄模零部件設計
d 中心距尺寸:
CM=(1+K’) CZ (CM )±δZ/2 =[(1+K’) CZ] ±δZ/2
中心距尺寸在加工製造和磨損過程中不受影響及上下
壓
偏差對稱分布.
鑄
模
設
計
2019/5/29
Macherchen
26
三.壓鑄模零部件設計
e 成型中心邊距尺寸: 1). 磨損後增大的成型中心邊距
(C’M )±δZ/2 =[(1+K’) C’Z -△/24 ] ±δZ/2
2). 磨損後減小的成型中心邊距
壓
(C’M )±δZ/2 =[(1+K’) C’Z +△/24 ] ±δZ/2
壓 鑄 模 設 計
2019/5/29
Macherchen
13
三.壓鑄模零部件設計
(3)避免銳角的鑲拼
壓 鑄 模 設 計
2019/5/29
Macherchen
14
三.壓鑄模零部件設計
(4)防止熱處理變形的鑲拼
壓 鑄 (5)便於更換維修的鑲拼 模 設 計
2019/5/29
Macherchen
15
三.壓鑄模零部件設計
3)壓鑄件上和模具上的中心距尺寸均采用雙向等值正負偏差,它
壓
們的基本尺寸為平均值.
鑄
模
設
計
2019/5/29
Macherchen
20
三.壓鑄模零部件設計
3. 影響壓鑄件尺寸精度的因素:
- 1、下载文档前请自行甄别文档内容的完整性,平台不提供额外的编辑、内容补充、找答案等附加服务。
- 2、"仅部分预览"的文档,不可在线预览部分如存在完整性等问题,可反馈申请退款(可完整预览的文档不适用该条件!)。
- 3、如文档侵犯您的权益,请联系客服反馈,我们会尽快为您处理(人工客服工作时间:9:00-18:30)。
6mm的铸件的金属液流速应该在30~37m/s,我们取充型
速度33m/s;当铝合金铸件的壁厚6mm时,推荐的金属液 填充型腔时间为在0.056~0.084s,我们取0.063s作为计算 依据;选择的压射比压为50MPa。
(铸件(铝合金)的重量计算如下: V=V1+V2 =24.2+52.5
=76.7 cm³
课程名:压铸模设计 书名:压铸工艺与模具设计
2013年4月 李成凯
复习回顾: 1.调温系统
2.压铸模零件的材料选择及热处理要求
3.压铸模的失效分析 4.压铸件的缺陷分析与排除措施
本次课内容: 压铸模设计过程及实例
一.压铸模分类
通常按模具结构上的某一特征 进行分类,可分为单分型面和多分型 面压铸模、侧向分型抽芯机构压铸模、螺纹旋出机构∑K·F主 =K(F铸+F浇+F余+F溢) F铸=πR² P=3.14×〔(0.175/2)2-(0.131/2) ² )×50Mpa =7.93×105N =793KN F浇=1×8×3×50Mpa =1.2KN F余=πR² p=3.14×(0.04/2)2×50 Mpa =62.8KN F涨=(F铸+F浇+F余+F溢)×P=857KN F涨—涨型力 F铸—铸件产生的涨型力 F浇—浇注系统产生的涨型力 F余—余料产生的涨型力 F溢—溢流槽产生的涨型力 锁模力计算如下:F≥K F涨=943KN;K—安全系数,取1.1 故锁模力大于或等于943KN的压铸机均可选用,因此,决定选用 国产J116D系列卧式冷压室压铸机
序
号
类别
压铸件
尺寸
计算公式
模具尺寸
1
1500 1
径
0.25 150.750
0.25 154.770
向
2 型 腔 尺 寸 3 深 度 4
1540 1
0 7 0 .36
0 240 .52
7.040 0.09
24.120 0.13
1 1400
5 径 向 型 芯 尺 寸 7 高 度
(六)成型零件的尺寸计算 成型零件中直接决定压铸件几何形状的尺寸称为成型尺寸,计算成型尺寸的 目的是为了保证压铸件的尺寸精度,为了保证压铸件的尺寸精度在所规定的公差 范围内,在计算成型尺寸时,主要以压铸件的基本尺寸、偏差值以及偏差方向作 为计算依据。 成型零件工作尺寸的计算的几条原则: 1)压铸件和成型零件尺寸取单向公差,按入体原则标注; 2)成型零件取平均收缩率、平均制造公差(取零件公差的1/4)、平均磨损 量(取零件公差的1/6) 。 3)压铸件与成型零件尺寸标注方法: 轴类尺寸采用基轴制,标负差;孔类尺寸采用基孔制,标正差;中心距尺寸 公差带对称分布,标正负差;压铸件原尺寸不是按这个规定,要按此规定改成单 向公差 材料铝合金受阻收缩率0.4%~0.6%,计算时取0.5%。零件公差都没有标注, 按IT14级计算。即7mm的公差为0.36;24mm的公差为0.52;34mm的公差为0.62 ;131mm、140mm、150mm和154mm的公差为1mm。
140.700 0.25
131.650 0.25
6
1 1310
7 0 0.36
240 0.52
7.040 0.09 24.120 0.13
8
(七)压铸模结构 压铸模由动模和定模组成,定模部分固定在压铸机固定板上,与压 室相连接动模部分安装在压铸机动模固定板上,与开合模机构相连。动 定模闭合后形成密闭的型腔及浇注系统通道。 本压铸模的基本组成: 1.成型零件 2.结构零件 包括支承固定零件和导向合模零件。支承固定零件使模具能够安装 到压铸机上;导向合模零件保证合模是正确定位和导向。 3.浇注系统 4.排溢系统 5.推出与复位机构 6.其它 如紧固件、定位件等。
(一)压铸件的工艺分析 从所给的零件图可知,该零件的形状是圆环型,压铸件最大外轮廓尺 寸为175mm,内径尺寸131mm,端环高度7mm,硅钢片铁芯叠厚20mm, 总高度34mm。它是带嵌件的铸铝件。铸件壁厚均匀,平均壁厚约为6mm, 大于铝铸件的最小壁厚0.5mm。铸件总重量为885克,其中纯铝(Al-1)183 克,压铸件的表面粗糙度和尺寸要求精度不高,整体形状比较简单,体积 较大。压铸铝合金铸造性能好,密度小,比强度高,耐腐蚀性,耐磨性, 导热性,导电性好以及良好的切削性能。纯铝铸造性能差,容易氧化,压 铸过程中易发生粘模现象,给压铸工艺带来一定程度的不便。但纯铝的电 磁性能符合电动机的要求而常用于压铸电动机转子。
(五)压铸机的预选 压铸机是压铸生产的专用设备,设计压铸模时必须熟悉压铸机的特性 和技术规范,通过必要的计算,选用合理压铸机,以发挥其最大的效益。 1.压射比压的确定 吊扇转子压铸件,压铸合金为纯铝,铸件平均厚度为6mm,且压铸件的 结构简单。依据有关资料铝合金的压射比压应该在40~60MPa,我们初步选 用50 Mpa。 2.压铸机锁模力的确定 锁模力的作用主要是为了克服充型时,型腔内产生的压力(涨型力) ,以锁紧模具的分型面,防止金属液飞溅,保证铸件的尺寸精度,涨型力 计算过程如下:
G=ρV≌207g V1—槽总体积 V2—端环体积 内浇口截面积设计原理是熔融金属尚未凝固而填充完毕
。
1.浇口 计算公式:
Ag
G t vn
式中:Ag—内浇口截面积(m2) G—通过内浇口的金属液,即铸件质量加溢流槽(kg) ρ —合金的液态比重(kg/m3)
2
0.207 2400 0.07 37 5
(4)模具安装部位的尺寸,应符合所选用的压铸机规格,压室安装孔径和深度
须严格检查。 (5)分型面上除导套孔外,所用模具制造过程中的工艺孔,螺钉孔都应堵塞,
并与分型面平齐。
(三)分型面的设计方案 (1) 第一种方案如图a,分型面作在硅钢片铁芯的右边,大部分型腔处于动模,
开模时,压铸件随动一起移动,最后由推出机构推出;由于电机转子的特殊性,
3.横浇道的尺寸确定 选用梯形横流道,扁梯形横浇道的尺寸计算:
b=3Ag/h=3×41.5/10=10.5mm b—横浇道长边尺寸(mm) h≥(1.5-2)b0 =12mm Ag—内浇口截面积(cm² ) α(出模斜度)=15° γ(圆角半径)=2~3mm h—横浇道厚度,本模具选用三股内浇口,横浇道也应为3股,所以 横浇道的厚度为4mm. b0—铸件平均厚度
4.15 10 m 41.5m m2
vn—内浇口充填速度(m/s)
t—填充时间(s) 显然,式中
浇口的厚度和宽度的确定: 根据计算值,内浇口的总面积是41.5mm2。内浇口的宽度取10mm,内 浇口的厚度取1.4mm。
vn和t的是确定内浇口截面积的关键。
2.直流道 卧式压铸机的压铸模可以说没有直流道,或者说直流道与 压室内径是一致的,一般根据工艺上所需的比压、浇注的金属 量和选定的内浇口充型速度来确定。 直浇道一般由压铸机上的压室和压铸模上的浇口套组成,在直浇 道中压射结束后留下的一段金属,通常称为余料,其结构如图所示。 直浇道的直径按所需比压确定。根据所选的压铸机的压室比压,取 D=40mm,直浇道的厚度(指余料厚度)一般为其直径的1/2或1/3, 这里取H=15m。为了使直浇道凝料从浇口套中顺利取出,可在靠近 分型面一端长度为10~15mm范围内孔处设有1°30´~2°的脱模斜 度,压室和浇口套的内孔,应在热处理和精磨后,在沿轴线方向进 行研磨,其表面粗糙度要求达到0.4μm以上。 此外,浇口套的厚度查有关资料可取5~10mm整体制成,根据经 验取浇口套的厚度为8mm。 直浇道和浇口套的结构形式见压铸模总装图。
压铸模的工作过程是: 1.转子片称重。 2.将转子冲片装在假轴上,并套上活块,旋紧螺母。 3.将串好转子片的假轴置于压铸模定模内。 4.合模,动模向定模靠近,合模后,将挡板插入动模套板内。 5.浇料,将熔化的、合格的铝液浇入压室。 6.压射,压射冲头向前推进,熔融合金经模具上的浇注系统充填型腔。 7.保压、凝固,在压力下凝固。 8.冷却,自然冷却亦可风冷。 9.开模,压铸机带动动模板移动,动模板带动动模套板移动,动模套板带动挡 板移动,挡板带动假轴移动,将转子从定模内拉出。 10.工人把转子与假轴一起从模具上取下。冲头复位,完成一个压铸循环。 11.模外手动抽芯,工人手工去掉浇注系统凝料,将转子从假轴上退下
二、.压铸模设计的主要内容和步骤
1.对压铸件进行工艺分析,并制订压铸工艺规程; 2.选择分型面及浇注排溢系统的设计; 3.确定压铸模的结构; 4.绘制压铸模装配图;
5.绘制压铸模零件图。
三、实例
本设计(论文或其他)应达到的要求:
1、设计说明书一份,不少于10000字。
2、产品模具图纸一套,其中装配图1张,A0或A1图纸打 印;全部非标零件图,A3或A4图纸打印。
综合所述,该铸件的铸造工艺性较好,适合用压铸方法生产。
吊扇铸铝转子 1.铸铝;2.转子冲片
(二)压铸模总装的技术要求 1.压铸模装配应注明的技术要求 (1)模具的最大外形尺寸320×320×325mm (2)压铸机型号J116D
(3)压铸零件选用的合金材料为纯铝Al-1
(4)压室直径 d=40mm,压射比压55MPa (5)最小开模行程64mm
不能像其他压铸件直接推出。
a)
b)
图3-1分型面
(2) 第二种方案如图b,分型面作在硅钢片铁芯的左边,大部分 型腔处于定模,开模时,压铸件不能理解随动一起移动,而要延时 ,由动模拉出定模,人工取出。 综上所述,结合电机转子的特殊性,选择第二种分型面的设计
方案较为合理。
(四)浇注系统设计 查表可知铝合金密度为2.7g/cm³ ,铝合金液态时密度为 2.4g/cm³ ;一般铝合金的充型速度在20~60m/s,壁厚为
(八)零件设计
动模套板
定模套板
12.2压铸模结构图例 1.平面分型、推管推杆推出结构 2.阶梯分型、推杆推出结构 3.卸料板推杆两次推出结构 4.曲面分型推杆推出结构 5.阶梯分型斜销抽芯的结构