最新精益生产全集七大浪费LeanToolwaste
精益生产之七大浪费

精益生产之七大浪费精益生产是一种以最小化浪费为目标,通过优化流程和提高效率来提高产品质量和客户满意度的管理方法。
在精益生产中,有七大浪费被认为是造成资源浪费和低效率的主要原因,它们是:过产、等待、运输、不合格、运动、库存和过程错误。
1. 过产(Overproduction):过产是指在没有实际需求的情况下进行生产活动,导致产品过度积压和资源浪费。
这不仅会给企业带来高成本,还会增加库存量和缩短产品寿命。
2. 等待(Waiting):等待是指生产过程中出现的不必要的停顿和延迟。
这可能是由于设备故障、物料不足、工人缺席等原因导致的。
等待会降低生产效率,增加生产周期,延迟产品交付。
3. 运输(Transportation):运输是指不必要的材料和产品的长距离运输。
这使得运输成为了一个独立的过程,需要额外的时间和资源。
这些额外的步骤可能会导致物料的损坏、遗失和延迟,进一步增加了生产成本。
4. 不合格(Defects):不合格是指生产中出现的错误、缺陷和质量问题。
不合格的产品需要进行修正、重新制造或报废,这增加了不必要的时间和资源。
这不仅会导致生产延误,还会降低产品质量和客户满意度。
5. 运动(Motion):运动是指工人在生产过程中进行不必要的移动和动作。
这可能是由于生产线布局不合理、工具和设备摆放不当等原因导致的。
这增加了工人的体力消耗,降低了生产效率,也增加了人为错误的可能性。
6. 库存(Inventory):库存是指未经加工的原材料和半成品的储存量。
过多的库存可能会导致资金占用、过期损失、储存空间浪费等问题。
此外,库存过多也会隐藏潜在的问题,如质量问题和需求变化的风险。
7. 过程错误(Processing):过程错误是指生产过程中出现的不必要的重复、增补和调整。
这可能是由于不合理的工艺流程、工具和设备的不良设计等原因导致的。
这会增加生产成本和时间,降低生产效率和产品质量。
有效管理和消除以上七大浪费是精益生产的关键。
精益生产的七大浪费概述

精益生产的七大浪费概述精益生产是一种管理哲学和方法论,旨在通过消除浪费来提高生产效率和质量。
在精益生产中,有七大浪费被广泛认可,包括:1. 运动:指的是任何不必要的移动或行动,例如工人需要频繁移动到不同的工作区域以完成任务。
精益生产鼓励将工作站布置得合理,以减少不必要的运动,从而提高效率。
2. 待料:指的是生产过程中等待原材料、工具或设备供应的时间。
这种等待会导致生产线停滞,降低生产效率。
精益生产鼓励将供应链优化,以减少待料时间。
3. 过产量:指的是生产超过需求的产品,或者在产品的某个阶段生产过多的零件。
过产量会导致库存积压、成本上升,甚至可能导致产品过期。
精益生产鼓励按需生产,以避免过产量的浪费。
4. 等待:指的是生产过程中因为等待其他任务完成而导致的停滞时间。
这种等待会导致生产线的延迟和低效。
精益生产鼓励优化工艺流程,减少等待时间。
5. 过度加工:指的是对产品进行超出需求或规格要求的加工步骤。
过度加工会增加生产成本和时间。
精益生产鼓励消除不必要的加工步骤,以提高效率和降低成本。
6. 错误:指的是在生产过程中出现的错误或瑕疵,例如产品缺陷或错误装配。
这些错误会导致废品产生和重工成本增加。
精益生产鼓励通过质量控制和错误预防来减少错误的发生。
7. 运输:指的是产品或物料在生产过程中频繁移动或运输的浪费。
这种浪费会增加时间和成本,同时也增加了损坏产品的风险。
精益生产鼓励优化布局和流程,减少不必要的运输。
通过有效地识别和消除这七大浪费,精益生产能够提高生产效率、降低成本,并提供更高质量的产品。
精益生产鼓励组织和管理层始终关注价值流,并持续改进以实现更高的效率和竞争力。
精益生产是一种以消除浪费为核心的管理哲学和方法论,旨在提高生产效率和质量。
在精益生产中,有七大浪费被广泛认可,并成为了改善生产流程的重要依据。
这七大浪费是运动、待料、过产量、等待、过度加工、错误和运输。
首先,运动是指不必要的移动或行动。
在生产过程中,员工频繁移动到不同的工作区域以完成任务会增加生产时间和劳动成本。
精益生产管理七大浪费详解

精益生产管理七大浪费详解丰田生产方式是彻底消除浪费的方法,消除浪费就能提高生产率。
制造现场的浪费是指「只会提高成本的要素」,存在’若不充分注意所有的地方浪费就会逐渐增加’的性质。
因此制造产品的作业中,需要有判断怎样的作业是浪费作业的能力。
通过丰田生产方式的教育来培养发现‘浪费’的眼光。
下面为大家进行精益生产管理七大浪费详解:1、过量生产的浪费超过生产计划或提前完成一点也不值得骄傲。
这只是在浪费的时候、生产了浪费的数量的浪费物品、制造了过盈生产的浪费。
现如今,所有企业为了实现将「需要的物品,在需要的时候,供给需要的数量」这种所谓的JIT(Just-In-Time)而展开着改善活动。
但是,对「需要的物品,在需要的时候,供给需要的数量」这句话的理解是多样的。
JIT生产方式所达到的状态是指在接到顾客订货的同时就开始生产,并使其在指定的时间到达到客户手中的状态即,发出仓库中存在的成品库存没有任何意义。
汽车的情况是,从确定汽车制造商的最终组装线计划时点开始生产,但是从调配材料或部品进行生产,然后将产品运送到各销售点和代理店,并完成各种手续到达顾客手中需要最小限度的时间。
「过量生产的浪费」是指进行顾客订货以外的生产。
尤其是无视日程计划的过盈生产更是荒谬。
还要完全否定「都能卖出去」的思想。
为此,是以改善的观点上所说的「以要求的TACT 进行生产」为大前提。
营业和生产管理部门只按照交易单位的信息来生产是不行的另外,制造部门若是认为以自己会社生产管理部门的日程计划进行生产就一点问题没有也是不行的。
不要忘记信息和日程计划都是以预测为基础的,是包含「过盈生产」风险的。
特别是各经销商店是以10台、20台这样的少数量来要货。
很多情况下生产管理部门是将这些少量订货以50和100的生产单位合并在一起下指示,发货时从中进行发送。
于是,剩余的数量抱着「会在什么时候发出去的」的安逸心态放置,结果在几年后的年末结算上却成为处理损失而进行了财务处理。
精益生产中的七大浪费

精益生产中的七大浪费消除七大浪费是精益生产的核心理念之一,七大浪费可用“TIM WOOD”表示(分别取7种浪费之英文首字母:运输、库存、动作、等待、过量生产、多余的工序、缺陷),以下对七大浪费作简要介绍。
一、七大浪费介绍第一种:运输的浪费主要表现为:车间布置采用批量生产,依工作站为区别的集中的水平式布置所致,无流线生产的观念。
第二种:库存的浪费主要表现为:管理者为了自身的工作方便或本区域生产量化控制一次性批量下单生产,而不结合主生产计划需求流线生产所导致局部大批量库存.库存的损害表现有:(1):产生不必要的搬运、堆积、放置、防护处理、找寻等浪费。
(2):使先进先出的作业困难.(3):损失利息及管理费用。
(4):物品的价值会减低,变成呆滞品。
(5):占用厂房空间,造成多余的工场、仓库建设投资的浪费.(6):没有管理的紧张感,阻碍改进.(7):设备能力及人员需求的误判。
第三种:动作的浪费主要因素表现为:生产场地不规划,生产模式设计不周全,生产动作不规范统一。
第四种:等待的浪费主要因素表现为:作业不平衡,安排作业不当、待料等。
第五种:过量生产的浪费主要因素表现为:管理者认为制造过多与过早能够提高效率或减少产能的损失和平衡车间生产力。
制造过多(早)的损害表现有:(1):提早用掉费用(材料费、人工费),不能创造利润。
(2):把“等待的浪费"隐藏起来,使管理人员漠视等待的发生和存在。
(3):自然而然地积压在制品,其结果不但会使制程的时间变长(无形的),而且会使现场工作的空间变大,机器间距离因此加大,逐渐地吞蚀利润。
(4):产生搬运,堆积的浪费,使得先进先出的作业产生困难。
第六种:多余的工序的浪费主要因素表现为:制造过程中作业加工程序动作不优化,可省略、替代、重组或合并的未及时检查.第七种:缺陷的浪费主要因素表现为:工序生产无标准确认或有标准确认未对照标准作业,管理不严密、松懈所导致。
二、以制造业为例,消除浪费之优先顺序优先级#1 过量生产这是7种浪费中最严重的一种,因为:a)它衍生出了另外的6种浪费b)它掩盖了真正的生产能力,从而导致你做出诸如转包工作或是在不必要的方面投资这样错误的决定。
精益生产之七大浪费
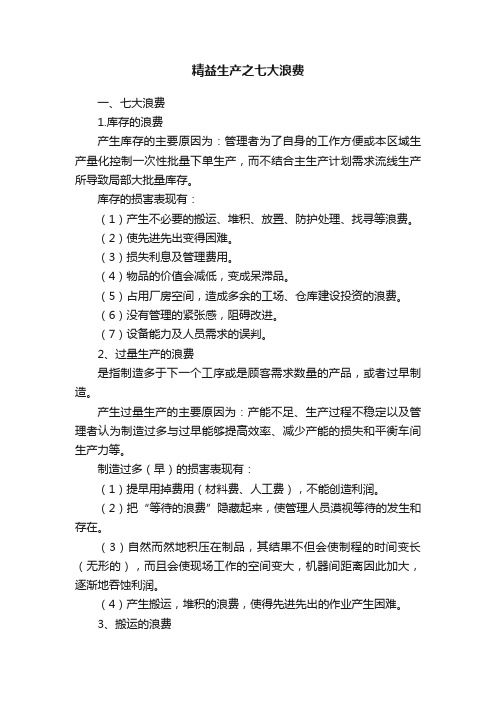
精益生产之七大浪费一、七大浪费1.库存的浪费产生库存的主要原因为:管理者为了自身的工作方便或本区域生产量化控制一次性批量下单生产,而不结合主生产计划需求流线生产所导致局部大批量库存。
库存的损害表现有:(1)产生不必要的搬运、堆积、放置、防护处理、找寻等浪费。
(2)使先进先出变得困难。
(3)损失利息及管理费用。
(4)物品的价值会减低,变成呆滞品。
(5)占用厂房空间,造成多余的工场、仓库建设投资的浪费。
(6)没有管理的紧张感,阻碍改进。
(7)设备能力及人员需求的误判。
2、过量生产的浪费是指制造多于下一个工序或是顾客需求数量的产品,或者过早制造。
产生过量生产的主要原因为:产能不足、生产过程不稳定以及管理者认为制造过多与过早能够提高效率、减少产能的损失和平衡车间生产力等。
制造过多(早)的损害表现有:(1)提早用掉费用(材料费、人工费),不能创造利润。
(2)把“等待的浪费”隐藏起来,使管理人员漠视等待的发生和存在。
(3)自然而然地积压在制品,其结果不但会使制程的时间变长(无形的),而且会使现场工作的空间变大,机器间距离因此加大,逐渐地吞蚀利润。
(4)产生搬运,堆积的浪费,使得先进先出的作业产生困难。
3、搬运的浪费不必要的搬运零件和产品,例如两个连续的生产工序,将产品在完成一个工序后,先运到仓库,然后再运到下一个工序。
较理想的情况是让两个工序的位置相邻,以便使产品能够从一个工序立即转到下一个工序。
产生搬运的主要原因为:车间布置采用批量生产,依工作站为区别的集中的水平式布置(也就是分工艺流程批量生产),无连续流生产的观念。
4、等待的浪费在生产过程中,操作员或者设备空闲。
产生等待的主要原因为:作业不平衡,安排作业不当、待料、品质不良等。
5、多余动作的浪费操作员所作的没有增值的动作,例如找零件,找工具、文件等。
产生多余动作的主要原因为:生产场地规划不好,生产模式设计不周全,生产动作不规范统一。
6、缺陷的浪费不良品和废品。
精益生产概述之七大浪费

精益生产概述之七大浪费精益生产是一种旨在消除浪费、提高效率和质量的管理方法。
在这个方法中,七大浪费被认为是导致资源浪费和低效率的主要原因。
因此,精益生产的目标是通过识别和消除这些浪费来实现生产过程的优化。
以下是精益生产中七大浪费的概述:1. 运输浪费(Transportation):指在生产过程中不必要的物料、产品或信息的运输。
这种浪费可能是由于生产线布局不合理、物料存放位置不当等导致的。
2. 库存浪费(Inventory):指在生产过程中过多的存储物料、产品或信息。
高库存不仅占用了宝贵的空间,还导致资金被束缚,增加了物料管理的复杂性。
3. 过程浪费(Process):指生产过程中的任何不必要的任务、步骤或动作。
这些浪费可能是由于不必要的检查、重复的手动操作或不必要的文件处理等原因造成的。
4. 动作浪费(Motion):指工人在生产过程中做出的不必要的动作或移动。
这些浪费可能包括在工作站之间来回移动、长时间等待或不必要的物料搬运等。
5. 等待浪费(Waiting):指在生产过程中由于等待而导致的停滞或不必要的停机时间。
这种浪费可能是由于生产过程中的停机、设备故障或不平衡的任务分配等原因造成的。
6. 蒙眬浪费(Over-processing):指在生产过程中对产品进行过度加工或处理,超出了产品要求或客户需求的范围。
这种过度加工不仅浪费资源,还可能导致产品成本增加。
7. 缺陷浪费(Defects):指生产过程中产生的不合格产品或错误。
这些缺陷可能导致产品退货、修复或重新制造,增加了成本和时间。
通过识别和消除这七大浪费,精益生产能够提高生产效率和质量,减少资源浪费和成本。
这种方法不仅适用于制造业,也可应用于服务业和其他组织。
通过优化流程,改进布局和减少浪费,组织可以实现更高的生产效率和更满意的客户。
精益生产是一个追求效率和质量的管理方法,它的目标是通过消除七大浪费来优化生产过程。
该方法最初由日本丰田汽车公司引入,并且已被广泛应用于不同的行业和组织。
精益生产办公室七大浪费
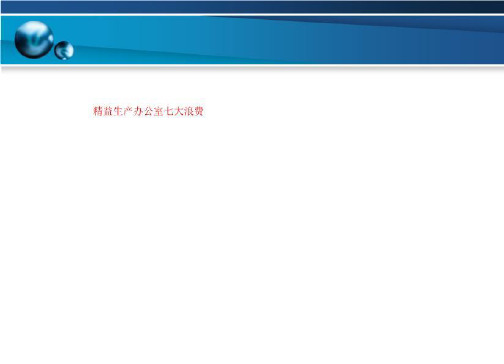
改 2工序和3工序颠倒的话
善 点
反转次数减少1次
5、动作的浪费
生产现场的作业动作不合理导致时间上的浪费。物品的取放、翻转、对准等。作业步行、弯 腰、转身等。
动作浪费的现象: 发动机合箱与装盖子处手压装配,不摇头、不转身、不插
发生原因:
秧 01.jpg
实施对策:
•工艺流程安排不合理 •没有实施标准作业 •人员的教育训练不足 •作业标准制定不合理
•以顾客需求的拉动生产 •一个流的生产
•客户订单的不准确 •生产计划安排有误
•看板管理的实施 •均衡化生产
管理要点:
•很多时候这种浪费往往不被现场监督者所重视,甚至被当成“超 产能手”受到赞扬
•生产能力过剩时,应尽量先考虑减少作业人员,但并非辞退人员, 而是更合理、更有效率地应用人员
7、库存的浪费
题 点
的方向
改 增加一个转向导轨,可减少一
善 点
名作业者
5、动作的浪费
附录:有关作业区域
关键是最合适・正常作业区域
6、生产过多(早)的浪费
产品变不成商品,没有任何价值
生产过多浪费的现象: 装配线转线处,曲柄加工的精车与后续挤螺纹之间
发生原因:
实施对策:
•人员过剩
•少人化作业
•设备稼动过剩 •生产批次大
•站立式作业才是真正的人性化管理(科学管理之父-泰勒)
4、加工本身的浪费
也称“过分加工的浪费”。一是指多余的加工,二 是指过分精确的加工。
加工本身浪费的现象: 曲柄精车粗糙度及配送中心机油泵齿轮穿架子等
发生原因:
•工艺的安排不合理 •作业内容偏离工艺文件 •模具治具不良 •作业没有标准化
实施对策:
精益生产的效率与七大浪费

精益生产的效率与七大浪费精益生产是一种以提高效率和消除浪费为目标的管理方式。
在精益生产中,有七大浪费被视为效率的根本敌人,它们分别是:过产出、等待、不必要的运输、过度加工、库存、不必要的动作和不必要的缺陷。
下面将逐一介绍这七大浪费及其对效率的影响,以及消除这些浪费的方法。
第一个浪费是过产出。
过产出指的是生产超过实际需求的产品或服务。
这会导致库存过剩,并增加了不必要的成本和风险。
解决这个问题的方法是通过精准预测,避免生产过多的产品。
同时,采用柔性生产方式和及时调整产能,以适应市场的实际需求。
第二个浪费是等待。
等待指的是等待时间过长,例如等待原材料、机器设备等。
这会导致生产过程中的停滞和延迟,并降低了效率。
减少等待时间的方法包括优化供应链,确保原材料的及时到达;同时,合理安排生产计划和生产线布局,避免机器设备的瓶颈和拥堵。
第三个浪费是不必要的运输。
不必要的运输指的是在生产过程中,产品或材料的运输距离过长或频繁。
这会增加运输成本和交付时间,降低效率。
减少不必要运输的方法包括优化物料搬运路径和方式,合理布局生产线,减少运输距离和次数。
第四个浪费是过度加工。
过度加工指的是对产品进行不必要的加工或处理。
这样做既增加了生产时间和成本,也增加了不必要的风险。
减少过度加工的方法包括优化工艺流程,消除不必要的工序和处理环节,确保产品的加工与客户需求一致。
第五个浪费是库存。
库存指的是多余的产品或材料存放在仓库中,这会增加仓储成本和风险。
减少库存的方法包括精确的需求预测,及时的生产计划和物料供应,以及有效的库存管理和控制。
第六个浪费是不必要的动作。
不必要的动作指的是工人在生产过程中进行的不必要的移动或动作,这会浪费时间和能量。
减少不必要动作的方法包括优化工作流程和工位布局,减少工人的不必要移动和转移。
第七个浪费是不必要的缺陷。
不必要的缺陷指的是在生产过程中出现的不符合质量要求的产品或材料。
这不仅会增加成本和风险,还会影响生产效率和客户满意度。