金属材料3D打印综述
金属3D打印技术

低温是其最大技术优势,整个打印过程的初始温度是150°C,焊接过
程中摩擦和塑性变形的产热可使局部温度达到200°C左右,
UAM技术可将多种金属材料连接在一起,还可以将传感器、合金纤维
等那些对温度敏感的低熔点材料或电子器件嵌入其中。
大尺寸。除了低温,该技术还拥有优于其他金属打印技术的工件尺寸,
用UAM打印工件的尺寸最大可达6x6x3英尺,且加工出来的工件表面光洁
3D
XX大学 增材制造学院
金属3D打印技术
Metal 3D printing technology
XXX
目录
CONTENTS
01 / 概述 02 / 粉末床熔合工艺 03 / 材料喷射工艺 04 / 直接能量沉积工艺 05 / 材料挤压工艺 06 / 其它成型工艺
1
PART ONE
概述
金属3D打印
工艺分类
金属3D打印技术主要有4类
粉末床熔合
直接金属激光烧结 DMLS 选择性激光熔化SLM 电子束熔化EBM
材料喷射
纳米颗粒喷射NPJ 粘结剂喷射BJ 立体喷墨打印3DP
直接能量沉积
激光近净成型LENS 电子束增材制造EBAM
材料挤压
熔融沉积FDM 熔丝制造FFF
2
PART ONE
粉末床熔合工艺
有较快的成型速度和较高的表面质量。
超声波固结 UAM 通过频率高达20,000Hz的超声波施加在金属片上,借助超声波的振
荡能量使两个需焊接的表面摩擦,构成分子层间的熔合,然后以同样的原 理逐层连续地焊接金属片,并同时通过机械加工来实现精细的三维形状, 从而形成坚实的金属物体。
超声波固结 UAM
AM的技术优势
冷喷涂金属打印(Cold Spray Metal Printing) 澳大利亚SPEE3D公司的超音速3D沉积技术
3D打印金属材料的力学性能研究报告

3D打印金属材料的力学性能研究报告一、引言3D 打印技术作为一项具有创新性和变革性的制造工艺,在各个领域都展现出了巨大的潜力。
其中,金属 3D 打印更是因其能够制造复杂形状、高性能的金属部件而备受关注。
然而,要确保 3D 打印金属部件在实际应用中的可靠性和安全性,对其力学性能的深入研究就显得至关重要。
二、3D 打印金属材料的种类及特点目前常见的 3D 打印金属材料包括钛合金、铝合金、不锈钢、镍基合金等。
钛合金具有高强度、低密度、良好的耐腐蚀性等优点,常用于航空航天领域的零部件制造。
铝合金则具有良好的导热性和导电性,在汽车制造和电子行业有广泛应用。
不锈钢因其优异的耐腐蚀性和机械性能,适用于制造各种工业零部件。
镍基合金则在高温环境下表现出色,常用于航空发动机等高温部件的制造。
三、3D 打印金属材料的力学性能测试方法(一)拉伸试验拉伸试验是评估金属材料力学性能最基本的方法之一。
通过对标准试样进行拉伸,测量其屈服强度、抗拉强度、延伸率等参数,从而了解材料的强度和塑性。
(二)硬度测试硬度测试可以快速评估材料的表面硬度,常见的方法有布氏硬度、洛氏硬度和维氏硬度等。
(三)疲劳试验疲劳试验用于测定材料在循环载荷作用下的寿命和疲劳强度,对于承受动态载荷的部件来说,这是一项关键的性能指标。
(四)冲击试验冲击试验可以衡量材料在冲击载荷下的韧性和抗断裂能力。
四、3D 打印金属材料力学性能的影响因素(一)打印工艺参数打印过程中的激光功率、扫描速度、扫描间距、层厚等工艺参数会直接影响材料的微观结构和力学性能。
例如,较高的激光功率和较慢的扫描速度可能导致材料过度熔化,产生孔洞等缺陷,从而降低力学性能;而较小的扫描间距和层厚则有助于提高材料的致密度和力学性能。
(二)粉末质量粉末的粒度分布、形状、化学成分等对打印质量和力学性能有重要影响。
粒度均匀、球形度高的粉末有利于提高铺粉的均匀性和流动性,从而获得性能更优的打印部件。
(三)后处理工艺打印后的热处理、热等静压等后处理工艺可以消除残余应力、改善微观结构,进而提高力学性能。
国内外金属3D打印材料现状与发展

3、应用领域
3D打印金属材料在航空航天、汽车制造、医疗等领域得到广泛应用。例如, 在航空航天领域,3D打印金属零件可有效降低制造成本和提高制造效率。在医疗 领域,3D打印金属材料可用于制造定制的医疗器械,如定制的钛合金假肢。
三、关键技术
1、材料改性
为了提高3D打印金属材料的性能,需要进行材料改性研究。例如,通过添加 合金元素对材料进行微合金化处理,以提高其力学性能和耐腐蚀性。
谢谢观看
四、金属3D打印工艺的特点和应 用
金属3D打印工艺的特点在于其成型原理和打印流程。金属粉末或金属丝在激 光或其他能源的作用下熔化,然后逐层堆积形成三维实体。这种工艺可以实现高 精度、高复杂度的制造,同时具有快速制造和个性化定制的优势。
在实际应用中,金属3D打印工艺被广泛应用于航空航天、汽车制造、医疗等 领域。例如,在航空航天领域,金属3D打印技术可以制造出高性能的零部件和发 动机,从而提高航空器的性能和安全性;在汽车制造领域,金属3D打印技术可以 用于制造轻量化零部件和复杂结构件,从而提高汽车的性能和燃油效率;在医疗 领域,金属3D打印技术可以用于制造个性化的人体植入物和医疗器械,从而提高 医疗效果和患者的生活质量。
一、金属3D打印材料的基本概念、 特点和应用
金属3D打印是一种快速成型的制造技术,它通过层层叠加的方式将金属材料 逐层打印成具有特定形状和结构的物体。这种技术具有制造复杂、灵活性强、生 产周期短等优点,被广泛应用于航空航天、汽车制造、医疗等领域。
二、国内外金属3D打印材料的现 状
目前,国内外在金属3D打印材料领域的研究已经取得了一定的成果。钛合金、 铝合金、不锈钢等金属材料已经被广泛应用于金属3D打印。在市场前景方面,随 着金属3D打印技术的不断发展和成本的逐渐降低,其应用领域将进一步扩大,市 场规模也将持续增长。
3d打印金属材料

3d打印金属材料3D打印金属材料。
3D打印技术作为一种新兴的制造方式,正在逐渐改变着传统制造业的格局。
在过去,3D打印主要应用于塑料、陶瓷等材料的制造,但随着技术的不断进步,如今已经可以实现对金属材料的3D打印。
金属材料的3D打印具有许多优势,例如制造复杂结构件、节约材料、缩短制造周期等,因此备受关注。
本文将就3D打印金属材料的技术原理、应用领域以及发展趋势进行探讨。
首先,我们来了解一下3D打印金属材料的技术原理。
金属3D打印是利用金属粉末作为原料,通过激光熔化、电子束熔化等方式,逐层堆积并熔化金属粉末,最终形成所需的金属零件。
这种制造方式可以实现对金属材料的高精度加工,同时也可以制造出复杂的内部结构,满足了传统加工方式无法实现的加工需求。
在技术上,金属3D打印的关键在于控制熔化过程中的温度、速度等参数,以确保所制造出的零件具有良好的力学性能和表面质量。
其次,我们来看一下金属3D打印的应用领域。
目前,金属3D打印已经被广泛应用于航空航天、汽车制造、医疗器械等领域。
在航空航天领域,金属3D打印可以制造出轻量化、高强度的航空零部件,提高了飞行器的性能和安全性。
在汽车制造领域,金属3D打印可以制造出复杂结构的汽车零部件,提高了汽车的性能和节能性。
在医疗器械领域,金属3D打印可以制造出个性化的假体和植入物,满足了患者个性化治疗的需求。
可以说,金属3D打印已经成为了制造业的一个重要组成部分,为各个领域带来了巨大的变革。
最后,我们来探讨一下金属3D打印的发展趋势。
随着金属3D打印技术的不断成熟,未来金属3D打印将更加普及和成熟。
首先,金属3D打印的成本将进一步降低,使得更多的中小型制造企业也能够享受到金属3D打印带来的便利。
其次,金属3D打印的材料种类将会不断丰富,包括钛合金、不锈钢、铝合金等,满足不同领域的制造需求。
再次,金属3D打印的制造速度将会进一步提高,使得大批量、高效率的生产成为可能。
可以预见,金属3D打印将会在未来的制造业中扮演着越来越重要的角色。
金属3d打印
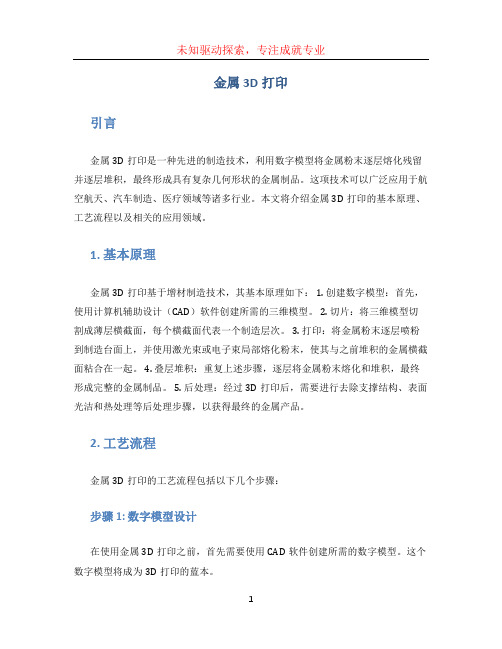
金属3D打印引言金属3D打印是一种先进的制造技术,利用数字模型将金属粉末逐层熔化残留并逐层堆积,最终形成具有复杂几何形状的金属制品。
这项技术可以广泛应用于航空航天、汽车制造、医疗领域等诸多行业。
本文将介绍金属3D打印的基本原理、工艺流程以及相关的应用领域。
1. 基本原理金属3D打印基于增材制造技术,其基本原理如下: 1. 创建数字模型:首先,使用计算机辅助设计(CAD)软件创建所需的三维模型。
2. 切片:将三维模型切割成薄层横截面,每个横截面代表一个制造层次。
3. 打印:将金属粉末逐层喷粉到制造台面上,并使用激光束或电子束局部熔化粉末,使其与之前堆积的金属横截面粘合在一起。
4. 叠层堆积:重复上述步骤,逐层将金属粉末熔化和堆积,最终形成完整的金属制品。
5. 后处理:经过3D打印后,需要进行去除支撑结构、表面光洁和热处理等后处理步骤,以获得最终的金属产品。
2. 工艺流程金属3D打印的工艺流程包括以下几个步骤:步骤1: 数字模型设计在使用金属3D打印之前,首先需要使用CAD软件创建所需的数字模型。
这个数字模型将成为3D打印的蓝本。
步骤2: 材料准备根据所需金属材料的要求,准备相应的金属粉末。
这些金属粉末的粒径应该符合打印设备的要求。
步骤3: 打印参数设置根据所用设备和材料的要求,设置打印参数,如打印层厚、激光功率、扫描速度等。
步骤4: 3D打印将金属粉末逐层喷粉到制造台面上,并使用激光束或电子束局部熔化金属粉末,逐层堆积金属制品。
步骤5: 后处理将打印完成的金属制品进行去除支撑结构、表面光洁和热处理等后处理步骤,以获得最终的金属产品。
3. 应用领域金属3D打印在不同行业的应用日益广泛,以下是金属3D打印的几个主要应用领域:3.1 航空航天金属3D打印可以制造复杂的航空发动机部件和飞机结构。
其优势在于可以减少部件数量并提高性能,同时降低整体重量。
3.2 汽车制造金属3D打印可以制造汽车发动机部件、制动系统和排气系统等。
金属3d打印原理

金属3d打印原理金属3D打印原理。
金属3D打印是一种先进的制造技术,它通过逐层堆叠金属粉末或金属丝材料,利用激光束或电子束等热源进行熔化,实现金属零件的快速制造。
与传统的加工方法相比,金属3D打印具有高效、灵活、精密等优势,因此在航空航天、汽车制造、医疗器械等领域得到了广泛的应用。
金属3D打印的原理主要包括以下几个方面:首先,金属3D打印的原始数据是由CAD软件生成的三维模型。
设计师通过CAD软件设计出产品的三维模型,然后将其转换为STL文件格式,STL文件包含了产品的三维几何信息,是金属3D打印的原始数据。
其次,金属3D打印的工艺参数设置是关键。
在进行打印之前,需要根据所选择的金属材料、打印设备和零件的几何形状等因素,确定合适的工艺参数,包括激光功率、扫描速度、层厚度等,这些参数的设置直接影响着打印质量和效率。
然后,金属3D打印的工艺流程包括预处理、打印和后处理三个阶段。
在预处理阶段,需要对金属粉末进行均匀分布和压实,以保证打印过程中的稳定性和精度;在打印阶段,激光束或电子束根据预先设定的路径,逐层熔化金属粉末或金属丝,形成零件的实体结构;在后处理阶段,需要对打印出的零件进行去除支撑结构、热处理、表面处理等工艺,以提高零件的力学性能和表面质量。
最后,金属3D打印的质量控制是至关重要的。
在打印过程中,需要通过实时监测和控制激光功率、温度、气氛等参数,以保证打印质量;同时,还需要对打印出的零件进行非破坏性检测、金相分析等质量检验,以验证零件的完整性和性能。
总的来说,金属3D打印是一种基于数字化设计和快速成型技术的先进制造方法,它的原理包括原始数据的生成、工艺参数的设置、工艺流程的控制和质量控制等方面。
通过不断的技术创新和工艺改进,金属3D打印技术将能够实现更高效、更精密、更可靠的金属零件制造,为制造业的发展带来新的机遇和挑战。
3D打印技术发展综述

3D打印技术发展综述3D打印技术是新兴的制造技术。
就其技术特征而言,一是依据三维CAD设计数据,采用液体、粉末、丝、片等材料逐层累加的方式制造实体零件,故也称作增材制造技术;二是不仅可以制造出任意复杂形状的零件,还大大减少了加工工序,缩短了加工周期,故也称作快速成型技术。
3D 打印技术为21世纪最具代表性制造技术之一,使制造工艺、技术、模式产生了根本性变化,越来越受到工业界和投资界的关注,不仅推动了经济发展,也影响着人类生活方式。
目前,3D打印技术已在多个领域,如电子产品、工业设计、汽车、航天、建筑、生物医疗及珠宝首饰、鞋类等领域的个性化定制得到应用。
由于多方面的瓶颈与挑战,3D打印技术的进一步扩展应用仍受到限制。
推动其发展并扩展其应用领域方面,该技术正在朝着提升打印速度和精度、扩展或开发新材料的方向上发展。
本文在技术、材料等方面进行了探究分析。
1 3D打印发展趋势3D打印技术的局限与挑战主要表现在:一是速度、效率和精度存在严重冲突,3D打印速度提升的同时打印成品精度不尽人意;二是受打印机工作原理的限制,考虑了打印精度的同时打印效率远不适应大规模生产需求;三是由于打印材料的制约,很多金属材料、陶瓷材料等打印件相比传统工艺仍存在致密度低和内应力大等问题。
3D 打印的成型材料多采用有机高分子材料,选择局限性较大,成型品物理特性较差。
看到3D打印技术和产业的发展前景,大企业致力创新高效、高精度的打印技术发展,主要有四种:一是CLIP技术,即“连续液界面生产工艺”;二是PolyJet技术,即光固化三维打印;三是MSL技术,即微立体光刻;四是超材料打印技術。
2 技术研发2.1 高速度、高精度的光固化3D打印(CLIP)现有光固化成型方法是利用液态树脂,层层构筑物体结构,即先打印一层,矫正外形,再灌入树脂,再重复之前的步骤,打印速度和精度不可兼得。
2021年3月20日,Carbon3D公司的Tumbleston等人在美国Science杂志上发表了一项具有颠覆性的3D打印新技术:CLIP技术,即“连续液界面生产工艺”,其工作原理为:在底部有一个能通过紫外线和氧的窗口,紫外线使树脂聚合固化,而氧气起阻聚作用,这两个矛盾体使得靠近窗口部分的树脂聚合缓慢仍呈液态,这一区域称为“死区”。
3D打印技术在核电领域的发展应用情况综述

3D打印技术在核电领域的发展应用情况综述AbstractIn recent years,metal 3D printing technology has developed rapidly. As a new generation of manufacturing technology,it can realize the rapid,high quality,efficient,economic,intelligent and flexible manufacturing of any complex shape parts without the limitation of the complexity of the parts structure. At present,the typical 3D printing processes mainly include arc additive manufacturing,electron beam selective melting,metal laser near net forming and laser selective melting forming. Through in-depth comparison of the typical 3D printing processes,grasping their design ideas,and directly applying them to the nuclear power industry,it has a very good development prospect and significant strategic significance,which is important to promote technological progress and equipment performance improvement Significance.Key words3D printing technology;Nuclear power equipment1 3D打印技术简介3D打印又叫增材制造(AM),于20世纪90年代开始发展,目前已趋成熟。
- 1、下载文档前请自行甄别文档内容的完整性,平台不提供额外的编辑、内容补充、找答案等附加服务。
- 2、"仅部分预览"的文档,不可在线预览部分如存在完整性等问题,可反馈申请退款(可完整预览的文档不适用该条件!)。
- 3、如文档侵犯您的权益,请联系客服反馈,我们会尽快为您处理(人工客服工作时间:9:00-18:30)。
金属零件3D打印技术现状及研究进展摘要:简述了国内外的金属零件3D打印技术的研究现状及最新进展,包括选区激光烧结(Selective Laser Sintering,SLS)、直接金属粉末激光烧结(Direct Metal Laser Sintering,DMLS)、选区激光熔化(Selective Laser Melting,SLM)技术、激光近净成形(Laser Engineered Net Shaping,LENS)技术和电子束选区熔化(Electron Beam Selective Melting,EBSM)技术,具体介绍了金属零件3D打印技术研究热点和难点以及具体应用,并对SLM技术现状、存在问题和发展趋势进行了分析。
关键词:金属零件3D打印;选区激光熔化;直接制造The Status and Progress of Manufacturing of Metal Parts by3D Printing TechnologyAbstract:This paper presents the research status and new progress of the metal parts manufactured by3DP Technologies,including Selective Laser Sintering(SLS),Direct Metal Laser Sintering(DMLS),Selective Laser Melting(SLM),Laser Engineered Net Shaping(LENS) and Electron Beam Selective Melting(EBSM).At last,the authors analyze the main research hotspots,problems and oriented applications of metalparts manufactured by3DP Technologies in detail,The status-in-art,problems and developing prospect of these technology are also discussed. Key words:metal parts3DP technologies;selective laser melting;direct manufacturing1.引言3D打印技术正在快速改变传统的生产方式和生活方式,作为战略性新兴产业,美国、德国等发达国家高度重视并积极推广该技术。
不少专家认为,以数字化、网络化、个性化、定制化为特点的3D打印技术为代表的新制造技术将推动第三次工业革命。
3D打印技术,就是在计算机中将3D CAD模型分成若干层,通过3D打印设备在一个平面上按照3D CAD层图形,将塑料、金属甚至生物组织活性细胞等材料烧结或者黏合在一起,然后再一层一层的叠加起来。
通过每一层不同的图形的累积,最后形成一个三维物体金属零件3D打印技术作为整个3D打印体系中最为前沿和最有潜力的技术,是先进制造技术的重要发展方向。
随着科技发展及推广应用的需求,利用快速成型直接制造金属功能零件成为了快速成型主要的发展方向。
目前可用于直接制造金属功能零件的快速成型方法主要有:包括选区激光烧结(Selective Laser Sintering,SLS)技术、直接金属粉末激光烧结(Direct Metal Laser Sintering,DMLS)、选区激光熔化(Selective Laser Melting,SLM)技术、激光近净成形(Laser Engineered Net Shaping,LENS)技术和电子束选区熔化(Electron Beam Selective Melting,EBSM)技术,。
国外对金属零件3D打印技术的理论与工艺研究相对较早,且在近几年已有多家公司推出商品化的设备。
而国内的研究主要集中在基础的工艺,华南理工大学的研究重点是SLM技术,清华大学以EBM技术为主,南京航空航天大学和华中科技大学主要研究选区激光烧结技术,近期也涉及到SLM工艺。
西北工业大学深入研究了LENS工艺。
本文就直接制造金属功能零件的快速成型的主要方法进行了归纳总结。
2.金属零件快速制造技术分类2.1选区激光烧结(SLS)选择性激光烧结技术(SLS)最初是由美国德克萨斯大学奥斯汀分校的Carl Deckard于1989年在其硕士论文中提出的,选区激光烧结,顾名思义,所采用的冶金机制为液相烧结机制,成形过程中粉体材料发生部分熔化,粉体颗粒保留其固相核心,并通过后续的固相颗粒重排、液相凝固粘接实现粉体致密化。
美国DTM公司于1992年推出了该工艺的商业化生产设备SinterSation。
德国的EOS公司在这一领域也做了很多研究工作,并开发了相应的系列成型设备。
国内有如华中科技大学、南京航空航天大学、西北工业大学、中北大学和北京隆源自动成型有限公司等,多家单位进行SLS的相关研究工作,也取得了重大成果。
2.1.1SLS技术原理及其特点整个工艺装置由粉末缸和成型缸组成,工作粉末缸活塞(送粉活塞)上升,由铺粉辊将粉末在成型缸活塞(工作活塞)上均匀铺上一层,计算机根据原型的切片模型控制激光束的二维扫描轨迹,有选择地烧结固体粉末材料以形成零件的一个层面。
完成一层后,工作活塞下降一个层厚,铺粉系统铺上新粉,控制激光束再扫描烧结新层。
如此循环往复,层层叠加,直到三维零件成型(如图1所示)。
图1SLS工艺采用半固态液相烧结机制,粉体未发生完全熔化,虽可在一定程度上降低成形材料积聚的热应力,但成形件中含有未熔固相颗粒,直接导致孔隙率高、致密度低、拉伸强度差、表面粗糙度高等工艺缺陷,在SLS半固态成形体系中,固液混合体系粘度通常较高,导致熔融材料流动性差,将出现SLS快速成形工艺特有的冶金缺陷——“球化”效应。
球化现象不仅会增加成形件表面粗糙度,更会导致铺粉装置难以在已烧结层表面均匀铺粉后续粉层,从而阻碍SLS过程顺利开展。
由于烧结好的零件强度较低,需要经过后处理才能达到较高的强度并且制造的三维零件普遍存在强度不高、精度较低及表面质量较差等问题。
在SLS出现初期,相对于其他发展比较成熟的快速成型方法,选择性激光烧结具有成型材料选择范围广,成型工艺比较简单(无需支撑)等优点。
但由于成型过程中的能量来源为激光,激光器的应用使其成型设备的成本较高,随着2000年之后激光快速成形设备的长足进步(表现为先进高能光纤激光器的使用、铺粉精度的提高等),粉体完全熔化的冶金机制被用于金属构件的激光快速成形。
选择性激光烧结技术(SLS)已被类似更为先进的技术代替。
2.2直接金属激光成形(DMLS)SLS制造金属零部件,通常有两种方法,其一为间接法,即聚合物覆膜金属粉末的SLS;其二为直接法,即直接金属粉末激光烧结(DirectMetalLaserSintering,DMLS)。
自从1991年金属粉末直接激光烧结研究在Leuvne的Chatofci大学开展以来,利用SLS工艺直接烧结金属粉末成形三维零部件是快速原型制造的最终目标之一。
与间接SLS技术相比,DMLS工艺最主要的优点是取消了昂贵且费时的预处理和后处理工艺步骤。
2.2.1直接金属粉末激光烧结(DMLS)的特点DMLS技术作为SLS技术的一个分支,原理基本相同。
但DMLS技术精确成形形状复杂的金属零部件有较大难度,归根结底,主要是由于金属粉末在DMLS中的“球化”效应和烧结变形,球化现象,是为使熔化的金属液表面与周边介质表面构成的体系具有最小自由能,在液态金属与周边介质的界面张力作用下,金属液表面形状向球形表面转变的一种现象.球化会使金属粉末熔化后无法凝固形成连续平滑的熔池,因而形成的零件疏松多孔,致使成型失败,由于单组元金属粉末在液相烧结阶段的粘度相对较高,故“球化”效应尤为严重,且球形直径往往大于粉末颗粒直径,这会导致大量孔隙存在于烧结件中,因此,单组元金属粉末的DMLS具有明显的工艺缺陷,往往需要后续处理,不是真正意义上的“直接烧结”。
为克服单组元金属粉末DMLS中的“球化”现象,以及由此造成的烧结变形、密度疏松等工艺缺陷,目前一般可以通过使用熔点不同的多组元金属粉末或使用预合金粉末来实现。
多组分金属粉末体系一般由高熔点金属、低熔点金属及某些添加元素混合而成,其中高熔点金属粉末作为骨架金属,能在DMLS中保留其固相核心;低熔点金属粉末作为粘结金属,在DMLS中熔化形成液相,生成的液相包覆、润湿和粘结固相金属颗粒,以此实现烧结致密化。
2.2.2直接金属粉末激光烧结(DMLS)的问题作为SLS技术的一个重要分支的DMLS技术尚处在不断发展和完善的过程之中,其烧结的物理过程及烧结致密化机理仍不明了,不同金属粉末体系的激光烧结工艺参数仍需摸索,专用粉末的研制与开发还有待突破。
因此,建立金属粉末直接激光烧结过程的数学、物理模型,定量研究DMLS烧结致密化过程中的烧结行为和组织结构变化,成为粉末冶金科学与工程研究中的重要内容之一。
DMLS中,金属粉末的物性对于烧结质量有着及其重要的影响,相同的工艺参数条件下,不同的粉末体系的烧结效果往往有很大的区别。
把握粉末体系的物性,为其选择最优化的工艺参数,是DMLS的最基本、最重要的要求。
大量研究表明,影响DMLS质量的三个关键物性参数主要为:烧结特性、摊铺特性和稳定性。
2.3选区激光熔化(SLM)SLM的思想最初由德国Fraunhofer研究所于1995年提出,2002年该研究所对SLM技术的研究取得巨大的成功。
世界上第一台SLM设备由英国MCP(Mining and Chemical Products Limited)集团公司下辖的德国MCP-HEK分公司已于2003年底推出。
为获取全致密的激光成形件,同时也受益于2000年之后激光快速成形设备的长足进步(表现为先进高能光纤激光器的使用、铺粉精度的提高等),粉体完全熔化的冶金机制被用于金属构件的激光快速成形。
例如,德国著名的快速成形公司EOS公司,是世界上较早开展金属粉末激光烧结的专业化公司,主要从事SLS金属粉末、工艺及设备研发。
而该公司新近研发的EOSINTM270/280型设备,虽继续沿用“烧结”这一表述,但已装配200W光纤激光器,并采用完全熔化的冶金机制成形金属构件,成形性能得以显著提高。
目前,作为SLS技术的延伸,SLM术正在德国、英国等欧洲国家蓬勃发展。
即便继续沿用“选区激光烧结”(SLS)这一表述,实际所采用的成形机制已转变为粉体完全熔化机制。
2.3.1选区激光熔化的原理SLM技术是在SLS基础上发展起来的,二者的基本原理类似。