塑胶模具设计CAD排位的步骤及注意事项
塑胶模具排位的过程
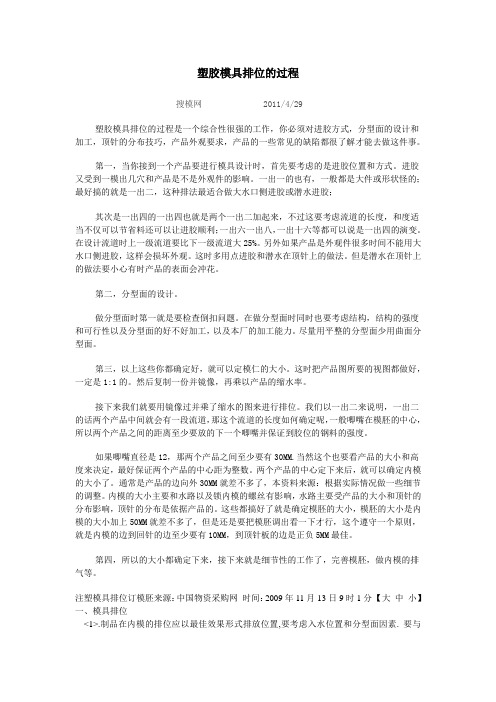
塑胶模具排位的过程搜模网 2011/4/29塑胶模具排位的过程是一个综合性很强的工作,你必须对进胶方式,分型面的设计和加工,顶针的分布技巧,产品外观要求,产品的一些常见的缺陷都很了解才能去做这件事。
第一,当你接到一个产品要进行模具设计时,首先要考虑的是进胶位置和方式。
进胶又受到一模出几穴和产品是不是外观件的影响。
一出一的也有,一般都是大件或形状怪的;最好搞的就是一出二,这种排法最适合做大水口侧进胶或潜水进胶;其次是一出四的一出四也就是两个一出二加起来,不过这要考虑流道的长度,和度适当不仅可以节省料还可以让进胶顺利;一出六一出八,一出十六等都可以说是一出四的演变。
在设计流道时上一级流道要比下一级流道大25%。
另外如果产品是外观件很多时间不能用大水口侧进胶,这样会损坏外观。
这时多用点进胶和潜水在顶针上的做法。
但是潜水在顶针上的做法要小心有时产品的表面会冲花。
第二,分型面的设计。
做分型面时第一就是要检查倒扣问题。
在做分型面时同时也要考虑结构,结构的强度和可行性以及分型面的好不好加工,以及本厂的加工能力。
尽量用平整的分型面少用曲面分型面。
第三,以上这些你都确定好,就可以定模仁的大小。
这时把产品图所要的视图都做好,一定是1:1的。
然后复制一份并镜像,再乘以产品的缩水率。
接下来我们就要用镜像过并乘了缩水的图来进行排位。
我们以一出二来说明,一出二的话两个产品中间就会有一段流道,那这个流道的长度如何确定呢,一般唧嘴在模胚的中心,所以两个产品之间的距离至少要放的下一个唧嘴并保证到胶位的钢料的强度。
如果唧嘴直径是12,那两个产品之间至少要有30MM.当然这个也要看产品的大小和高度来决定,最好保证两个产品的中心距为整数。
两个产品的中心定下来后,就可以确定内模的大小了。
通常是产品的边向外30MM就差不多了,本资料来源:根据实际情况做一些细节的调整。
内模的大小主要和水路以及锁内模的螺丝有影响,水路主要受产品的大小和顶针的分布影响,顶针的分布是依据产品的。
塑胶模具设计开发流程

塑胶模具设计开发流程1. 概述塑胶模具设计开发是塑胶产品生产的重要环节之一。
它涉及到模具设计、制造、调试等多个步骤,需要密切配合各个环节的工作方能顺利完成模具开发。
本文介绍了塑胶模具设计开发的流程,以及每个环节的具体内容。
2. 设计需求确认在进行塑胶模具设计开发之前,首先需要进行设计需求的确认。
这包括了对产品的理解、功能要求、生产批量、材料选择等方面的确认。
设计需求的确认是保证后续设计、制造工作的基础,必须与产品开发团队充分沟通,确保设计的准确性和可行性。
3. 模具设计3.1 概念设计概念设计是模具设计的第一步,它是将设计需求转化为具体形式的过程。
在概念设计中,设计师会进行产品结构的初步构思,确定产品的整体布局、形状、尺寸等方面的要求。
概念设计通常使用手绘或三维建模软件进行,以得到初步的设计方案。
3.2 详细设计在概念设计确定之后,设计师需要进行详细设计。
详细设计包括模具的几何形状设计、材料选择、零件分解、加工工艺等方面的设计。
详细设计通常使用CAD (计算机辅助设计)软件进行,以便将设计方案转化为可供制造的模具图纸。
3.3 模具流程分析在进行详细设计之前,设计师需要对模具的流程进行分析。
这包括模具的注塑工艺、模具的射出过程、模具的冷却系统等方面的分析。
通过模具流程分析,设计师可以确定模具的结构特点、加工精度要求等,以便进行详细设计。
4. 模具制造4.1 材料采购在开始制造模具之前,需要采购所需的模具材料。
模具材料通常选择具有高强度、耐磨性、耐腐蚀性等特点的金属材料,如钢材等。
材料采购需要与供应商进行沟通,确保所采购的材料符合设计要求。
4.2 CNC加工模具制造通常采用CNC(计算机数控)加工技术。
CNC加工可以高效、精确地进行模具零部件的加工,提高模具的制造精度和效率。
在CNC加工过程中,需要根据详细设计图纸进行加工,并进行必要的质量检测。
4.3 组装与调试在完成模具零部件的加工之后,需要进行模具的组装与调试工作。
塑胶模具设计CAD排位的步骤及注意事项

塑胶模具设计CAD排位的步骤及注意事项塑胶模具2D排位图步骤及注意事项一、排组立图的步骤1、把产品的3D图文件转到2D图档上,需将倒勾或有机构处做剖面,要注意比例问题。
(1:1比例);2、转到2D图文件上的产品图要加缩水和镜像。
注意:完成以上两步骤后必须检查,可以测量产品在加缩水前后的同一地方,来检查缩水加的是否正确;3、排组立前要定成品基准线。
即把产品上boss或大平面等易找到的特征定X,Y,Z三轴,特征的寻找需尽量接近于成品中心,若是两上下盖相配合,基准则尽量为同一点。
成品基准线相对模具中心要为整数;4、依照成品基准线把模仁排出来。
步骤与表示重点:a、删除成品上的虚线;b、如侧视图为剖面要将侧视图的实线改为虚线,仅留剖面处为实线;c、要把成品的分型面表示出来,重点表示主分型面,斜销,滑块处分型面。
分型面上的插破,靠破也需表示;d、还需把模仁拆入子处表示清楚,正视图入子遍界用黄色线表示,且入子沉头也需表示。
入子与入子间要避免有薄铁现象,一般不可小于1mm。
(模仁需拆入子部位一般为整体不好加工处或肋较深处及一些boss处)。
5、排顶针,水路,最后排模仁螺丝。
要注意三者不能干涉,三者间距不小于3mm,拆入子时也要一同考虑.以下为顶针,水路,螺丝的排列重点:a、顶针要排在成品不易脱模处,如成品的边缘、肋及塑料较深处。
顶针的尺寸要尽量选择大的,以增加强度。
顶针舆成品形状间距应不小于0.6-1mm,以避免薄铁现象。
b、排水路的宗旨是可以尽快的带走模温,以达到冷却效果。
直通的水路效果最好。
C、模仁螺丝一般排四个,位置要尽量对称。
6、排模仁要注意强度问题,产品边缘距模仁边缘应不小于20mm,模仁边缘距模架边缘的距离要按模具大小而定,大模具要50mm以上,小模具为30-50mm (天地侧350mm以下视为小模具)。
有特殊要求的要个别对待。
二、排位1. 成品在内模的排位应以最佳效果情势排放位置,要思量入水标位置和分型面因素。
最全注塑模具设计步骤以及注意事项的讲解
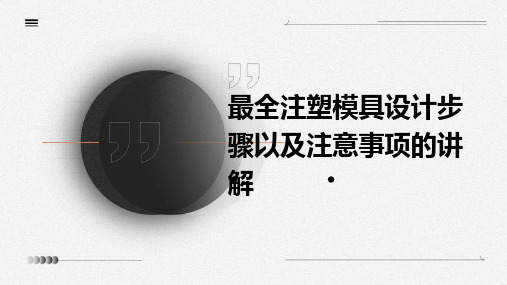
控铣削等加工方法,确保型芯、型腔的加工精度和表面质量。
02
浇口套、定位圈等关键零件加工工艺
采用高精度磨削、研磨等加工方法,保证零件的尺寸精度和形位公差。
03
导柱、导套等导向零件加工工艺
采用无心磨床、外圆磨床等高精度磨削设备,确保导向零件的精度和耐
磨性。
装配顺序和调试方法论述
装配顺序
遵循先下后上、先内后外的原则,先进行模架等支撑零件的装配,再进行型芯、型腔等成型零件的装配,最后进 行浇口套、定位圈等关键零件的装配。
根据模具结构确定加热装置的安装位置, 确保加热均匀且不影响模具其他功能。
油温机/水温机:适用于大型模具,加热 均匀,稳定性好。
03
06
考虑加热装置与冷却系统的协调,避免相 互干扰。
温度控制精度要求及实现途径
01
温度控制精度要求
02
根据制品要求确定温度控制精度,一般要求在±2℃ 以内。
03
对于高精度制品,温度控制精度要求更高,可达 ±1℃以内。
03
04
加强与客户和同行的沟 通和合作,不断提升服 务水平和市场竞争力。
培养高素质的人才队伍 ,为公司的可持续发展 提供有力保障。
感谢观看
THANKS
常见故障排查技巧和经验分享
常见故障排查技巧
介绍常见的注塑模具故障排查技巧,如检查模具磨损、清洗模具等。
经验分享
分享行业专家在注塑模具故障排除方面的经验和案例,提高读者解决问题的能力。
预防性维护策略推广
预防性维护策略
阐述预防性维护在注塑模具管理中的重要性 ,提出定期维护、保养和检查等策略。
推广实施
调试方法
在装配过程中,采用试装、试模等方法进行调试,确保模具各部件的配合精度和动作顺畅。对于复杂模具,还需 进行多次试模和调整,以达到最佳状态。
塑胶模具设计流程

塑胶模具设计流程塑胶模具设计流程是一个关键的环节,它涉及到塑胶制品的生产和制造。
在生产过程中,合理的模具设计能够确保产品的质量和生产效率,因此模具设计非常重要。
以下是塑胶模具设计流程的详细步骤:1. 确定产品需求和规格:首先,需要明确需要制造的塑胶产品的形态和尺寸。
这一步需要考虑到产品所需的功能和外观,并以此制定出产品的设计规格。
2. 设计零件的3D图形:根据产品的规格,进行3D建模。
这里需要考虑到零件的大小、形状以及所需的精度。
3. 设计模具的结构:根据设计好的产品零件图像,进行模具结构的设计。
这步骤需要注意到模具的材料和结构,以确保产品在生产过程中能够达到预期的精度和质量。
4. 绘制详图:在设计过程中,需要制定详细的图纸和标注以确保在制造和加工过程中的准确性。
5. 模拟和测试:在设计好模具之后应该进行模拟和测试来检验模具的可行性。
这将确保商品是可制造的和能够在预料的框架下运行,同时也会检查所有的元素的互相作用,以确保模具是符合制品要求的。
6. 加工和制造:当模具设计完毕后,就可以进行模具制造和加工工作。
模具可以手工制造,也可以使用模具加工正确的中心工具,确保模具的准确性和持久性,并确保制品的精度。
7. 维护和修理:在模具使用过程中,会存在损坏或磨损的情况,这时需要对模具进行维护和修理工作来确保模具的持续使用和准确性。
总结:上述步骤是塑胶模具设计流程的基本步骤。
通过合理的模具设计和制造,可以为塑胶制品的生产过程提供高效和低成本的解决方案。
所以,模具设计和制造是生产塑胶制品的重要环节,需要重视。
塑胶模具设计规范

模具设计规范(此规范主要应用于手机模具)一、模具排位1、根据产品大小、结构、产量、精密程度、材料或客户要求等因素确定模穴,如1X1、1X2等。
2、当几个产品出在同一套模具中时,考虑进胶的均匀性,应将大的产品排在中间位置,小的产品置于两边。
确保冲胶平衡,保证产品尺寸的精确性。
3、当几个分型面不规则的产品在同一模具中时,排位必须充分考虑其分型面连接的顺畅,且容易加工。
4、一模多穴模具中,当有镶拼,行位等结构时,不得使其发生干涉。
5、排位多时应综合模具每一方面,对流道,是否镶拼,行位,顶出,运水等结构要有一个全局性思考。
6、排位时产品在模上的定位基准要和产品图的基准一致,当一模出一件时,可以考虑以产品对称方向处分中。
7、内模钢料和模胚的大小尺寸如下图所示。
8.产品大小和胶位厚度有较大相差时尽量不要出在同一套模具中。
9.模具方铁高度尽量订做标准高度。
10.模胚型号和中托司使用情况一定要写清楚(细水口需注明SP长度)11.必要时需注明模胚吊模孔移位情况12.考虑需不需开精框及内模料材料和规格(确定后模要不要镶大呵,如需要则一起订料,此为粗料.)二、模具系统设计一)、行位系统当塑胶产品确定前后模开模方向后,有下列情况时一般会采用行位或斜顶等结构:1)、相对出模方向塑胶产品上有倒扣或零度面;2)、产品的出模斜度不够蚀纹的角度;3)、保证特殊的外观面不能有夹线。
1、后模行位:1)、后模行位统一做镶件压块,行位压块用螺丝固定,行位压块材料为油钢淬火至HRC48-52°。
2)、所有与行位相对运动的零部件的滑动面(包括行位底耐磨片,压条,铲基斜面)须锣(磨)油坑,油坑可为平行四边行、V形或圆环形。
3)、行位铲机钢材整体采用738H,在铲机斜面上镶耐磨片,耐磨片可突出斜面0.5mm,耐磨片厚度为6mm(如下图),材料为油钢,淬硬至HRC48-52°。
康铨公司的铲基采用国产S136淬硬至HRC46-50°。
塑胶模具设计注意事项

29;订原身留模架注意导柱和导套的长短及吊环孔的位置(有要求的模架需出2D模架图)。
30;设计人员后期与钳工模具跟踪工作要融洽,第一时间为钳工服务,不能有怠慢,拖延,不理不管等态度,相互尊重;对钳工所提 出的模具质疑要认真对待,分析,从中吸取经验和不足。
31;设计人员以后出模具新图纸时,一定要把司筒或镶针高度及大小,以及镶针或司筒是否要定位(异形),多根镶针或司筒要用编号 标注并在模仁中对号入座 这些都在图纸中表示出来,也减少日后查数.
32; 3030以上的模具都加边锁(模具定位) 4040以上的模具都加防压块(保护分型面) 4040以上模框要做方形精定位(模架定位) 3030以上三板模A板与托料板要加弹簧(辅助开模、减轻尼龙棒阻力),并且唧嘴要做斜度1-2度斜度(减轻唧嘴摩擦阻力及寿 命),采购模具标准件按照《苏州慈泓模具配件》里标准采购(公司自建有3D标准零件库)
刀具半 径R
R1
R1.5 R2 R3
R4Байду номын сангаас
R5 R8
加工深 度mm
4以下 10以下
15
30
40 50 100 以下 以下 以下
电极注意事项
1. 注意基准、取数方向(四面分中还是单边取数、分型面碰数 还是底面取数)。
2. 根据胶位的深度、宽度,确认精粗公(一般精工单边火花位 0.1mm,粗工单边火花位0.2mm,特殊情况0.3mm)
27;2D线割图需简单明了,把不要割的多余线条全部删除(如图形复杂需放简单的形状线,以便区分方向和线割位置),线割图形必 须有基准角表示,我们必须严格规定;红色为线割线 绿色为分中或单边靠线;模具线割图必须出到位,不要出现漏割、错割现 象,以免给线割人员带来返工,浪费加工时间,(如出现以上线割投诉将按绩效扣分)。
塑料模具设计流程

塑料模具设计流程在塑料制品生产过程中,塑料模具设计是至关重要的一环。
一个优秀的塑料模具设计可以直接影响产品的质量和生产效率。
因此,塑料模具设计流程的规范性和科学性对于产品的质量和生产效率具有重要的意义。
下面将介绍塑料模具设计的一般流程。
首先,塑料模具设计的第一步是需求分析。
在这一阶段,需要与客户充分沟通,了解客户对于塑料制品的需求和要求。
同时,还需要对产品的使用环境、使用要求等进行全面的了解和分析。
只有充分了解了客户的需求和产品的使用环境,才能够进行下一步的设计工作。
第二步是产品设计。
在这一阶段,需要根据客户的需求和产品的使用环境,进行产品的结构设计和外观设计。
通过CAD等设计软件进行三维建模,进行产品的形状、尺寸等设计。
同时,还需要进行产品的注塑工艺分析,确定产品的注塑工艺参数,为后续的模具设计提供依据。
第三步是模具结构设计。
在这一阶段,需要根据产品的设计要求,进行模具的结构设计。
包括模具的分型、冷却系统、顶出机构等设计。
同时,还需要进行模具的强度分析,确保模具在使用过程中不会发生断裂或变形等现象。
通过模具结构设计的工作,可以为后续的模具加工和调试提供依据。
第四步是模具加工和调试。
在这一阶段,需要根据模具设计图纸,进行模具的加工和装配。
同时,还需要进行模具的调试工作,包括模具的开合试模、产品的成型试验等工作。
通过模具加工和调试的工作,可以确保模具在使用过程中能够正常工作,同时也可以为产品的生产提供保障。
最后一步是模具的验收和交付。
在这一阶段,需要对模具进行全面的验收工作,包括模具的尺寸精度、成型质量等方面的检验。
只有通过了验收工作,模具才能够交付给客户使用。
同时,还需要对模具进行使用说明书的编写,为客户的使用和维护提供指导。
总的来说,塑料模具设计流程是一个系统工程,需要在每一个环节都进行严格的把控和管理。
只有通过科学规范的设计流程,才能够设计出优秀的塑料模具,为客户的生产提供保障。
希望本文的介绍能够对塑料模具设计有所帮助。
- 1、下载文档前请自行甄别文档内容的完整性,平台不提供额外的编辑、内容补充、找答案等附加服务。
- 2、"仅部分预览"的文档,不可在线预览部分如存在完整性等问题,可反馈申请退款(可完整预览的文档不适用该条件!)。
- 3、如文档侵犯您的权益,请联系客服反馈,我们会尽快为您处理(人工客服工作时间:9:00-18:30)。
塑胶模具设计CAD排位的步骤及注意事项塑胶模具2D排位图步骤及注意事项一、排组立图的步骤1、把产品的3D图文件转到2D图档上,需将倒勾或有机构处做剖面,要注意比例问题。
(1:1比例);2、转到2D图文件上的产品图要加缩水和镜像。
注意:完成以上两步骤后必须检查,可以测量产品在加缩水前后的同一地方,来检查缩水加的是否正确;3、排组立前要定成品基准线。
即把产品上boss或大平面等易找到的特征定X,Y,Z三轴,特征的寻找需尽量接近于成品中心,若是两上下盖相配合,基准则尽量为同一点。
成品基准线相对模具中心要为整数;4、依照成品基准线把模仁排出来。
步骤与表示重点:a、删除成品上的虚线;b、如侧视图为剖面要将侧视图的实线改为虚线,仅留剖面处为实线;c、要把成品的分型面表示出来,重点表示主分型面,斜销,滑块处分型面。
分型面上的插破,靠破也需表示;d、还需把模仁拆入子处表示清楚,正视图入子遍界用黄色线表示,且入子沉头也需表示。
入子与入子间要避免有薄铁现象,一般不可小于1mm。
(模仁需拆入子部位一般为整体不好加工处或肋较深处及一些boss处)。
5、排顶针,水路,最后排模仁螺丝。
要注意三者不能干涉,三者间距不小于3mm,拆入子时也要一同考虑.以下为顶针,水路,螺丝的排列重点:a、顶针要排在成品不易脱模处,如成品的边缘、肋及塑料较深处。
顶针的尺寸要尽量选择大的,以增加强度。
顶针舆成品形状间距应不小于0.6-1mm,以避免薄铁现象。
b、排水路的宗旨是可以尽快的带走模温,以达到冷却效果。
直通的水路效果最好。
C、模仁螺丝一般排四个,位置要尽量对称。
6、排模仁要注意强度问题,产品边缘距模仁边缘应不小于20mm,模仁边缘距模架边缘的距离要按模具大小而定,大模具要50mm以上,小模具为30-50mm(天地侧350mm以下视为小模具)。
有特殊要求的要个别对待。
二、排位1. 成品在内模的排位应以最佳效果情势排放位置,要思量入水标位置和分型面因素。
要与成品的外形大小、深度成比例。
2. 成品到精框边的间隔:A)小件的成品:间隔为25mm—30mm之间,成品之间为15mm—20mm,如镶件有则为塑胶原料25mm左右,成品间有流道的最少要15mm;B)大件的成品:距边为35—50mm,有镶件最小为35mm,如1件钢件出多件流产物,则其之间的间隔应12—15mm左右。
成品长度在200mm以上,宽度在150mm以上其产物距边应不少于35mm。
3. 成品排位时选择基准的原则:A)优先选取具明显特徵(如柱位、碰形成空洞、骨位中)的部门分中。
B)若选取PRO/E 3D基准时,要注明CSO或CSI或DTM的名字。
C)形状特别,难于确定基准的成品,要与CAM会商再确定其基准。
D)成品基准与模胚中心肯定是要为整数,并在示明尺寸时于数码上加方框以示区别。
4. 排位时确定内模精框X、Y坐标方向的原则:若内模精框长宽尺寸差明显,必须取较长一方之方向为X轴方向放置模胚排位,以共同工场机床加工方向,减少堕落概率。
三、订模胚1. 尽量采用尺度模胚(LKM尺度或鸿丰尺度)。
A)由工字模改直身模时,不要移动方铁,要直接在方铁上锣码模坑。
B)不尺度模胚要颠末主管赞成并要在排位图上塑胶扇骨子电子供应厂商注明。
2. 用CH型和CT型模胚要做码模坑,高度和宽度为25—35mm左右,长度按模胚的高度确定。
3. 弹弓孔直径应大于弹弓直径1—2mm之间,藏入B板深度最少为20至30mm。
4. 出模胚加工图,要由模胚供应商加工唧嘴孔(法兰)、弹簧孔、方型辅助器安装凹位或爹把边钉孔等;大的模胚(800X800)需加工撑头孔(包孕底部的螺钉孔)、斜方避空孔、斜方青铜器镶件、斜方色仔、行位、行位压板、运水、运水桶等;细水口模胚还须加工水口拉杆、弹弓胶孔、拉胶孔、塞打螺钉孔等;出模胚加工图前请徵询工场要求,按照工场现实事情量决议需要加工物件。
5. 大水口模胚为2730以上的模胚,A板的厚度应为精框的深度加25mm—35mm之间,B板的厚度为精框深度加50mm—70mm之间;模胚在2525以下,A板的厚度为框深加25mm—30mm左右,B板为40mm—50mm之间。
6. 细水口模胚A板的厚度为框深加30—40mm之间,B板厚度为框深度加50—60mm之间。
(大、细水口模胚规格可参照龙记模胚资料)。
四、订料1.开料原则:A)不新塑胶外壳供应需精磨的镶件的开料尺寸=现实数+3—5mm(此数要尽量与钢料供应商的规格相符);B)精磨的开料尺寸=现实数+余量(如:+0.3/-0);C)Y-CUT镶件的开料尺寸=现实数+5mm(一边)+5mm(相邻边)+20mm(对边)+20mm(对边之相邻边);D)需加硬的镶件的开料尺寸=现实数+10mm (精磨不计算在内)。
2.模具钢料要按成品的分子化合物塑料性子订料(包孕啤塑胶料)。
如:A)啤PVC的产物要视乎花纹的结构可选用GS083H、S136、S136H、铍铜为内模质料。
B)啤透明料、POM料、锦纶料、ABS料、K搪料等内模用料为GS083HS136、S136H的等钢料(注:用S136H、GS083H与S136等钢料建造的模具除特别环境下最好不焊接,要是焊接,则需烧不异质料并且要回火)。
C)除啤有酸性或透明胶料外,其它成品内模用料为P5、P20、738、718型号钢材。
D)内模水口铁常用钢材为黄牌料。
E)行位料、斜枕料和行位压板凡是为738料(除行位不做镶件外)。
F)合金模全部用8407质料(包孕内模料),方便加硬。
G)行位底或斜位需镶硬件时,质料要用738钢料。
3、其他预设、加工要求:①A板与B板离隙为0.1mm(即内模料塑胶模具总的高度大于A、B板精框深度全体0.1mm)。
中、大型模具A、B板离隙为0.5mm。
回针高度应比AB 板离隙小0.05—0.2mm (即凳仔方高度+B板高度+离隙高度-离隙0.05~0.2mm-底针板及垃圾钉高度=回针长度)。
②模胚顶面(拉令孔即吊模孔)要打上本厂与客户编号对照表编号,打字唛最少要用12mm的字唛,打上的字唛要工整。
③撬模角全部锣在B板四个角上,做等边三角学形,深度4—5mm及倒R 或倒角。
④模胚上所有运水出进口需打上1 IN--1OUT—2 IN--2 OUT等。
⑤码模孔间隔和牙的规格按注塑几规格确定。
⑥上下模料和模胚的要求如次:A)模料底、模框四边做约1mmX1mm的45%%d倒角。
B)A、B板模面要按内模料数量在框边出5mm锣一直径1/2"mm,深0.5mm 的圆位,用打内模编号,方便对号装嵌,A板按1、2、3打上字唛,B板按01、02、03打上字唛。
上下模料则面临A板、B板字唛位置需打上本厂编号(XXXX),上模编号为XXXX--1、2、3,下模编号为XXXX--01、02、03。
上下模编号必须对称(即上模为1,下模为01作为一盒)。
上下模打字唛位锣长为30mm、宽为8mm、深为0.5mm坑位,打上5.0mm的新塑胶外壳供应字唛,内模编号应按客户供给雕刻上或打上编号。
C).上下模框许可差为%%p0.02mm,上下模料曲尺许可公役为%%p0.02mm,上下模料尺寸公役为%%p0.02mm。
⑦走模时,外表要干净,内模要喷上防锈油。
五、画模架时的注意事项:1、KO孔一般放在模具的正中,当有多个时,它们之间的间距一般为100mm。
2、支撑柱应尽量往模具中心排即靠着KO孔,且尺寸尽量做大。
要注意不能和顶针,斜销等机构干涉。
相比较下,天地侧比左右侧更需要支撑柱。
3、当顶针小于2mm时,模具需加EGP。
但也有特殊要求的。
位置放在模具的天地侧。
4、吊模孔在舆其它机构不干涉的情况下要放在模板中间,如有干涉则要移位,并要标注尺寸。
5、当模具天地侧长度超过350mm时,需增加顶出板螺丝和ST,且在下固定板舆模脚之间要加锁左右各两个M10螺丝。
6、如一副模架的模板都很厚超过标准模架所列出的模板厚度的中间数字,那么GP需加大一绩。
如是不标准模架,天地侧或左右侧有拉长,那么GP需加大一绩。
三板模GP的算法是:GP在公母模板分型面以下的长度等于成品料骨的总长度加上30-40mm。
7、三板模中的小拉杆的放置位置在模具的左右侧。
小拉杆行程的计算为料骨总长度加上15-20mm。
8、三板模中的树脂开闭器的放置位置尽量在模具的左右侧。
9、模具一般需加RP弹簧,弹簧孔的算法为顶出距离乘2再加10mm,弹簧长度为弹簧孔长度再加10mm。
10、如产品有倒勾,需要走斜销,滑块等机构。
成品进点的侧视需做局部放大。
斜销和滑块要尽量在侧视图上都表示出来。
11、组立图的布图重点和标注重点:组立图正视需表示模仁,模仁螺丝,顶针,水路,斜销,滑块,流道,进点,灌咀,定位环,KO孔,支撑柱,EGP,小拉杆,树脂开闭器,回位销弹簧,定位块等。
同样侧视也需表示遮些。
组立图的标注重点为模架要加工的地方,有模架大尺寸及各模板尺寸,吊模孔位置,GP,RP,EGP,KO孔,支撑柱,模仁尺寸,顶出板螺丝,ST,小拉杆,树脂开闭器,灌咀,定位环及成品基准线等。
六、尺寸标注:1.在尺寸标注过程中要注意以下几点:a. 转图时的比例要正确。
b. 标注之前要舆组立图做重迭工作,检查2D,3D是否一致。
c. 局部放大图的放大比例倍数要以2,4,5,10比例去放大。
一般先把1:1的图标注完,再标局部放大图。
标局部放大图时尺寸线要炸开。
被放大处要有尺寸舆放大图相对应,以便检查。
d. 标注完一个零件要检查标注原点是否正确。
2.标注的重点尺寸:a. 模仁开粗尺寸b. 模仁顶针,水路,螺丝位置尺寸,如模仁较复杂需单独用一张图表示。
c. 模仁上产品大尺寸,及放电深度。
d. 公母模仁插靠破处尺寸,并在尺寸后注明插靠破。
e. 需放电加工处的尺寸。
拔模斜度尺寸。
f. 模仁上有斜度的线割孔尺寸,如斜销,斜度入子等。
g. 模板需标注的尺寸有:模框尺寸,顶针,水路,螺丝,灌咀孔,三板模进点流道,斜销滑块的相应地方,定位块等。
3.其它a. 图框要保持1:1比例,如需放大要注明放大比例。
b. 相对应的零件要尽量放在一个图框内。
如母模仁要和母模入子放一起,滑块要和滑块相对应的零件放一起,模板不可以和模仁,入子之类零件放同一图框。
c. 零件在图框中的排布要以编号依次放置。
d. 图框的编号以组立图-模板图-模仁图依次编下去。
e. 完成一张图要把设计人,完成日期等相关事项注明上去。
f. 依客户产品2D图纸建3D,要把建完的3D转成2D,依据客户提供的2D 图纸重新标注一遍,检查是否一致,有公差范围的尺寸用不同颜色表示。
且标注图要存档。
七、审图时要注意以下几点:1、检查组立图是否有机构干涉。
2、检查模仁,模板等零件是否少尺寸。
3、检查相配合零件的配合尺寸。