玛钢管材电镀锌常见问题
热镀锌常见的质量缺点及产生原因
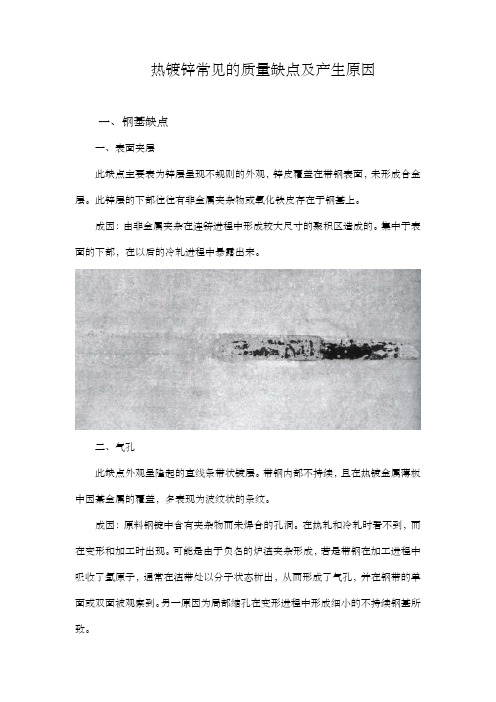
热镀锌常见的质量缺点及产生原因一、钢基缺点一、表面夹层此缺点主要表为锌层呈现不规则的外观,锌皮覆盖在带钢表面,未形成合金层。
此锌层的下部往往有非金属夹杂物或氧化铁皮存在于钢基上。
成因:由非金属夹杂在连铸进程中形成较大尺寸的聚积区造成的。
集中于表面的下部,在以后的冷轧进程中暴露出来。
二、气孔此缺点外观呈隆起的直线条带状镀层。
带钢内部不持续,且在热镀金属薄板中因棊金属的覆盖,多表现为波纹状的条纹。
成因:原料钢锭中含有夹杂物而未焊合的孔洞。
在热轧和冷轧时看不到,而在变形和加工时出现。
可能是由于负名的炉渣夹杂形成,若是带钢在加工进程中吸收了氢原子,通常在渣带处以分子状态析出,从而形成了气孔,并在钢带的单面或双面被观察到。
另一原因为局部缩孔在变形进程中形成细小的不持续钢基所致。
3、孔洞此缺点表现为贯穿带钢上下表面的材料不持续的外观。
成因:材料破裂的结果。
在热轧时,若是带钢横断面局部经受的压力过大,使其应变超过了钢的塑性(应变能力),就会出现孔洞。
带钢愈薄,这种情形就愈明显。
一般情形下,钢中的气孔、粗大的夹杂或轧入的异物、或轧前钢表面存在严峻的机械操作,均会引发带钢横截面强度减弱。
4、氧化铁皮缺点此缺点外观呈镀层下陷的细小的凹坑状和浮雕状,是在热轧时氧化铁皮坑和疤被轧入钢基内而引发。
氧化铁皮虽然可在酸洗时除掉,但不能肃除。
这些缺点的外观呈点状、线状,也可能呈大范围的片状。
残余氧化铁皮在酸洗时如未洗掉则在冷轧时被轧入表面,它们也呈点状、线状和大范围的片状,一般无规则地散布在带钢表面。
成因:在热轧带除鳞时由高压不压力不足造成的。
在热轧时残余的氧化铁皮被轧入带钢;在酸洗不足的情形下冷轧时被轧入。
二者的形态和散布密度不相同。
五、原板擦伤此缺点外观分为两种状态:1)热轧、酸洗、冷轧划痕多为沿轧制方向的沟状条纹,其划痕的镀锌层往往因合金层生长速度较快而致使该处镀层较厚。
在沟槽内一般无氧化铁皮存在。
成因:带钢热轧或冷轧时板面有金属屑碎片,这些金属碎片被推到其端部而形成缺点。
镀锌钢管锌层附着力差的原因分析及改进措施

镀锌钢管锌层附着力差的原因分析及改进措施发表时间:2017-10-24T16:51:44.217Z 来源:《防护工程》2017年第15期作者:陈凯张琦罗先锋[导读] 足够的烘干时间,合适的镀锌温度,良好的储存条件。
在这样条件下的锌层附着力为最佳。
浙江金洲管道科技股份有限公司浙江湖州 313000 摘要:镀锌钢管在使用过程或弯曲过程中会出现锌层开裂等缺陷,本文以实例的形式,给出了锌层附着力差产生的原因,并提出了相应的改进措施。
优化工艺,得到了镀锌层附着力优良的产品关键词:镀锌钢管;附着力;弯曲引言镀锌钢管现今主要的生产方式分为电镀锌法和热浸镀锌法。
由于热浸镀锌法在生产效率上和产品质量上有着明显的优势而被广泛采用。
本文所述的镀锌钢管均为热浸镀锌法生产出来的产品。
镀锌钢管由于其表面的锌层在酸碱环境下具有抵抗锈蚀的能力,使得其在流体输送和气体输送方面有着重要的应用。
但在实际环境中可能会出现各种情况比如环境恶劣,遭受碰撞或者不可抗力等因素导致锌层的开裂以及剥落,而这些缺陷将直接影响产品的可靠性和安全性,所以采取有效的改进措施是必要的。
1 附着力的定义及检验方法附着力是指两种不同物质接触部分的吸引力。
镀锌钢管锌层附着力是指镀锌层与焊接钢管表面结合在一起的牢固程度。
在成品检验过程中,我们用钢管弯曲机将镀锌钢管弯曲90°,观察锌层有没有发生剥落作为锌层附着力好坏的判断依据。
镀锌管弯曲试验过程如下图1和下图2所示:图22 附着力差的表现及原因分析将规格为DN25×2.8的镀锌钢管放在钢管弯曲机上进行弯曲。
试验时,弯曲试样不带填充物,弯曲半径为钢管外径的8倍,使之弯曲90°,焊缝位于弯曲方向的外侧。
试验后,观察弯曲方向的锌层,发现有锌层开裂及起皮现象,故判定为附着力不合格。
镀锌层开裂见下图3:对其分析产生的原因,从生产过程一直到试验过程,都有其产生锌层附着力不合格的风险。
图32.1镀锌层本身与铁基体的附着力不好,导致镀锌层开裂和脱落。
电镀锌杂质污染故障分析及排除方法(最新版)

( 安全技术 )单位:_________________________姓名:_________________________日期:_________________________精品文档 / Word文档 / 文字可改电镀锌杂质污染故障分析及排除方法(最新版)Technical safety means that the pursuit of technology should also include ensuring that peoplemake mistakes电镀锌杂质污染故障分析及排除方法(最新版)1故障状况某电镀车间一直使用氰化电镀锌工艺,共有两槽氰化镀锌溶液约1000L。
年初,1号槽镀液逐渐泛黄,溶液粘稠、浑浊,锌沉积速度很慢,锌镀层灰暗。
用30%硝酸溶液出光后,镀件表面呈黑褐色,彩钝后表面呈雾状,且无光泽。
按电镀过程中带入铬酸,产生六价铬的污染问题处理,加入0.1g/LNa2S2O4,未见好转,又加入2g/LNa2S 和2g/L活性炭进行沉淀吸附过滤,锌镀层也未见有明显好转,而且生产故障继续恶化。
连续生产的2号镀液槽,不久又出现了同样的故障。
重新配制500L镀液,生产一段时间后镀液的颜色又逐渐变黄,锌镀层灰暗,无论是硝酸出光,还是低铬酸出光,表面均呈黑褐色,零件孔眼部位呈亮白色,钝化后严重发雾,无光泽,不足1月已经很难镀出合格产品。
操作者按1.5g/L加入Na2S也未有大起色,已无法正常生产。
2故障诊断镀液外观颜色异常,是否是操作带入铬酸所致?为此,作者做了如下工艺试验:吸取镀液5ml,用蒸馏水稀至50ml,以1∶1硫酸酸化破坏锌络合物,用20%氢氧化钠溶液调整pH值在9左右,使锌生成氢氧化锌沉淀,并过滤。
将滤液用100%硫酸调pH值至5~6后,加入二苯碳酰二胺(0.1g溶于50ml乙醇溶液加入10%硫酸200ml)铬显色剂5ml。
结果滤液无明显颜色变化,这说明没有六价铬污染。
镀锌常见质量问题及其解决方法
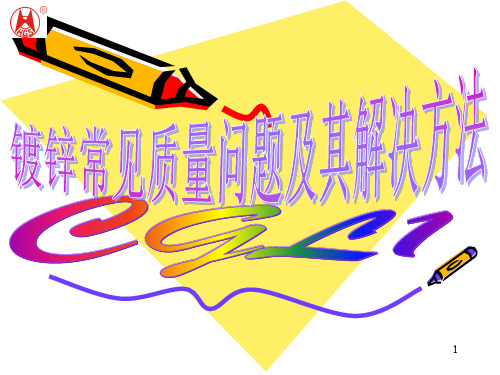
11
• 六、板面点块状露钢 • 常见原因:1、炉内局部气氛不合要求:炉区 常见原因: 、炉内局部气氛不合要求: 漏气、漏水或开机前吹扫不干净。 2、炉区 漏气、漏水或开机前吹扫不干净。 、 NOF段造成板面氧化。3、进炉前的板存在锈 段造成板面氧化。 、 段造成板面氧化 蚀或是板面有水、油等其它污染物。 、 蚀或是板面有水、油等其它污染物。4、若JC 快冷风机处有较多锌灰或锈皮, 快冷风机处有较多锌灰或锈皮,则启用快冷风 机后也容易露钢。 机后也容易露钢。
13
• 八、锌渣痕带露钢:带钢板面附有锌渣 锌渣痕带露钢: 条状、片状), ),其中又有针孔状露钢 (条状、片状),其中又有针孔状露钢 或块状露钢,多出现在下表面, 或块状露钢,多出现在下表面,呈不规 律的线条状居多,有时某个局部稍多, 律的线条状居多,有时某个局部稍多, 侧或D侧 目前原因尚不清楚。( 。(从 如O侧或 侧。目前原因尚不清楚。(从 侧或 沉辊划伤会造成露钢的情况看, 沉辊划伤会造成露钢的情况看,下表面 锌渣痕露钢是否为钢板在炉内造成比如热张力辊)
14
• • • • • • • • • •
锌层脱落
– 缺陷特征
由于锌层粘附性能不好,在进行机械咬合或球冲试验时, 由于锌层粘附性能不好,在进行机械咬合或球冲试验时,带钢表面 出现的严重锌层与钢基分离的现象称锌层脱落。 出现的严重锌层与钢基分离的现象称锌层脱落。在生产线上也可以直接 看到锌层局部呈块状与钢基分离、锌层掉落的现象。 看到锌层局部呈块状与钢基分离、锌层掉落的现象。 2、产生原因 、 原板存在擦、划伤、锈蚀等缺陷; 原板存在擦、划伤、锈蚀等缺陷; 轧机乳化液太脏,带钢表面残留物偏高; 轧机乳化液太脏,带钢表面残留物偏高; NOF炉温偏低,不能有效的灼烧掉带钢表面的残留物; 炉温偏低, 炉温偏低 不能有效的灼烧掉带钢表面的残留物; NOF空燃比设定不合理 或烧嘴变形), 空燃比设定不合理(或烧嘴变形),NOF呈强氧化气氛; 呈强氧化气氛; 空燃比设定不合理 或烧嘴变形), 呈强氧化气氛 H2掉或机组恢复生产时 掉或机组恢复生产时HN置换时间不够; 置换时间不够; 掉或机组恢复生产时 置换时间不够 炉压偏低,炉门吸风; 炉压偏低,炉门吸风; 炉子密封状况不好; 炉子密封状况不好;
金属电镀出现不良现象的原因与解决方法
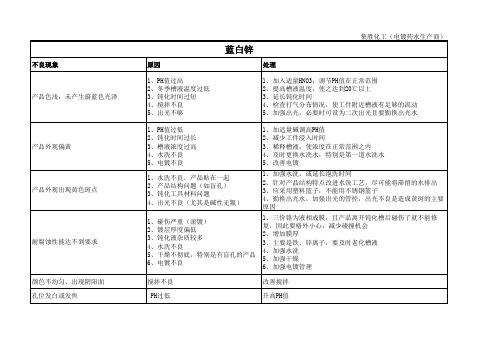
钝化外观偏浅(呈蓝带黄或金黄)
孔位颜色过深
钝化外观不均
耐腐蚀性能达不到要求
孔位周围发白
孔位颜色过深,呈现焦黄色
钝化后工件发花(呈地图纹状)
1、pH值过高 2、药液杂质过多 3、槽液浓度偏低 ①PH值过高 ②时间过短 ③Cr3+浓度低
1、调整pH值 2、排去1/5旧槽液,重新以原液补充添加 3、补加A01-435DC ①加入适量硝酸 ②延长钝化时间 ③ 加入适量原液 ①加入硝酸 ②排污,补充建浴液 ③加强搅拌 ①加碱升高PH值
产品颜色过浅,呈金黄色而不是五彩
①PH值过高 颜色不均匀,产品出现花斑(地图状花纹) ②或杂质太多 ③槽液循环搅拌不良 孔位发白、工件边缘泛紫光 ①PH值过低
黑锌
不良现象 原因 1、PH值过低 2、槽液中铁离子过高 3、槽液温度过高 4、钝化时间过短 5、B剂浓度不足 6、电镀外观过于光亮 1、pH值偏低 2、温度偏高 3、钝化时间过短 4、搅拌不足 1、pH值偏低 2、钝化时间过长 3、槽液温度偏高 处理 1、校正酸度计,调整PH值至操作范围 2、更新部份槽液或重新建浴 3、降低槽液温度 4、延长钝化时间 5、适当补充B剂 6、调整电镀 1、调高pH值至操作范围 2、降低温度 3、适当延长钝化时间 4、增强搅拌 1、调高pH值至操作范围 2、缩短钝化时间 3、降低温度
1)镀液中锌离子浓度应维持在10~15g/L 2)保持槽液温度20~30℃ 3)见A项第2点 4)控制氢氧化钠浓度在100~150g/L保持氢氧化钠与锌离子浓 度之比在10~12之间。 1)分析调整。控制锌离子浓度在10~15g/L,氢氧化钠浓度与 锌离子的比值10~12为宜。 2)适量补加A02-350A光剂。 3)降低电流密度。 4)保持槽液温度20~30℃。 1)分析调整,控制锌离子浓度在10~15g/L,氢氧化钠浓度与 锌离子的比值10~12为宜。 2)根据霍尔槽试片,适量补加A02-350B光剂。 3)提高电流密度。 1)在工艺允许使用范围内提高锌离子浓度。 2)根据霍尔槽试片,适量补加A02-350A光剂。 3)加净化剂C或软水剂D。 4)加强前处理。 适当增加A02-350B用量;在过滤机加入锌粉及助滤剂硅藻土以除 杂
镀锌常见缺陷的原因分析及解决办法
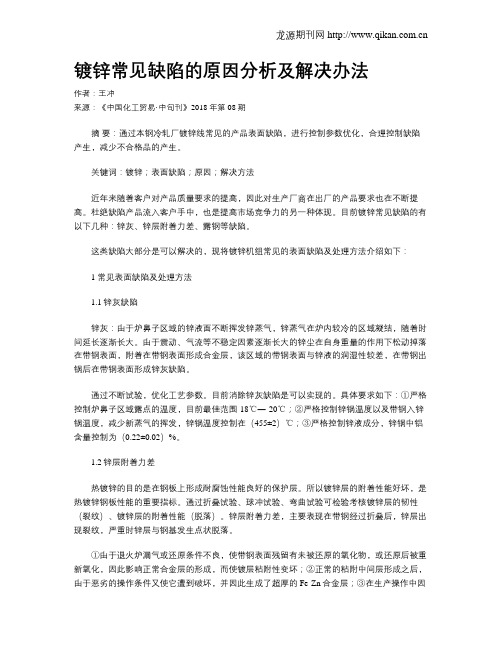
镀锌常见缺陷的原因分析及解决办法作者:王冲来源:《中国化工贸易·中旬刊》2018年第08期摘要:通过本钢冷轧厂镀锌线常见的产品表面缺陷,进行控制参数优化,合理控制缺陷产生,减少不合格品的产生。
关键词:镀锌;表面缺陷;原因;解决方法近年来随着客户对产品质量要求的提高,因此对生产厂商在出厂的产品要求也在不断提高。
杜绝缺陷产品流入客户手中,也是提高市场竞争力的另一种体现。
目前镀锌常见缺陷的有以下几种:锌灰、锌层附着力差、露钢等缺陷。
这类缺陷大部分是可以解决的,现将镀锌机组常见的表面缺陷及处理方法介绍如下:1 常见表面缺陷及处理方法1.1锌灰缺陷锌灰:由于炉鼻子区域的锌液面不断挥发锌蒸气,锌蒸气在炉内较冷的区域凝结,随着时间延长逐渐长大。
由于震动、气流等不稳定因素逐渐长大的锌尘在自身重量的作用下松动掉落在带钢表面,附着在带钢表面形成合金层,该区域的带钢表面与锌液的润湿性较差,在带钢出锅后在带钢表面形成锌灰缺陷。
通过不断试验,优化工艺参数。
目前消除锌灰缺陷是可以实现的。
具体要求如下:①严格控制炉鼻子区域露点的温度,目前最佳范围-18℃―-20℃;②严格控制锌锅温度以及带钢入锌锅温度,减少新蒸气的挥发,锌锅温度控制在(455±2)℃;③严格控制锌液成分,锌锅中铝含量控制为(0.22±0.02)%。
1.2锌层附着力差热镀锌的目的是在钢板上形成耐腐蚀性能良好的保护层。
所以镀锌层的附着性能好坏,是热镀锌钢板性能的重要指标。
通过折叠试验、球冲试验、弯曲试验可检验考核镀锌层的韧性(裂纹)、镀锌层的附着性能(脱落)。
锌层附着力差,主要表现在带钢经过折叠后,锌层出现裂纹,严重时锌层与钢基发生点状脱落。
①由于退火炉漏气或还原条件不良,使带钢表面残留有未被还原的氧化物,或还原后被重新氧化,因此影响正常合金层的形成,而使镀层粘附性变坏;②正常的粘附中间层形成之后,由于恶劣的操作条件又使它遭到破坏,并因此生成了超厚的Fe-Zn合金层;③在生产操作中因温度、锌液中铝含量和浸时间控制不当,使中间粘附层没有来得及形成,从而造成镀层的粘附力下降;④清洗效果不好,表面残存大量的油脂、氧化铁皮退火炉参数未及时调整。
镀锌管质量问题赔偿标准
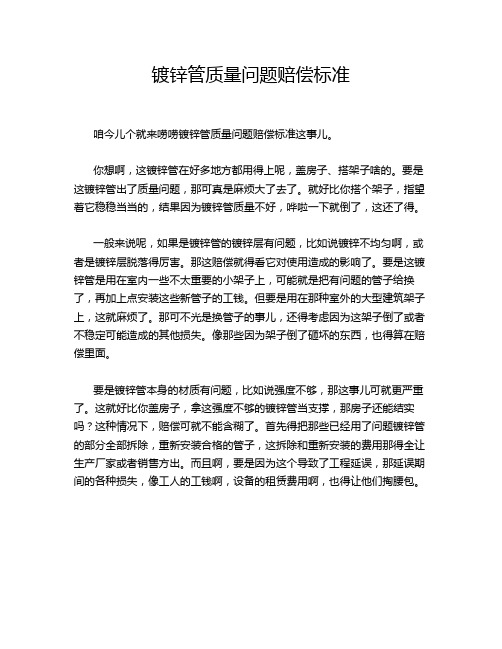
镀锌管质量问题赔偿标准咱今儿个就来唠唠镀锌管质量问题赔偿标准这事儿。
你想啊,这镀锌管在好多地方都用得上呢,盖房子、搭架子啥的。
要是这镀锌管出了质量问题,那可真是麻烦大了去了。
就好比你搭个架子,指望着它稳稳当当的,结果因为镀锌管质量不好,哗啦一下就倒了,这还了得。
一般来说呢,如果是镀锌管的镀锌层有问题,比如说镀锌不均匀啊,或者是镀锌层脱落得厉害。
那这赔偿就得看它对使用造成的影响了。
要是这镀锌管是用在室内一些不太重要的小架子上,可能就是把有问题的管子给换了,再加上点安装这些新管子的工钱。
但要是用在那种室外的大型建筑架子上,这就麻烦了。
那可不光是换管子的事儿,还得考虑因为这架子倒了或者不稳定可能造成的其他损失。
像那些因为架子倒了砸坏的东西,也得算在赔偿里面。
要是镀锌管本身的材质有问题,比如说强度不够,那这事儿可就更严重了。
这就好比你盖房子,拿这强度不够的镀锌管当支撑,那房子还能结实吗?这种情况下,赔偿可就不能含糊了。
首先得把那些已经用了问题镀锌管的部分全部拆除,重新安装合格的管子,这拆除和重新安装的费用那得全让生产厂家或者销售方出。
而且啊,要是因为这个导致了工程延误,那延误期间的各种损失,像工人的工钱啊,设备的租赁费用啊,也得让他们掏腰包。
我有个朋友就遇到过这样的事儿。
他承包了一个小工程,用了一批镀锌管,结果那镀锌管质量特别差。
刚开始还没发现,等搭了一半的架子,那管子就开始变形了。
你说这多坑人呐。
他找那供应商理论,供应商刚开始还想耍赖呢。
我朋友就说:“你这管子质量这么差,就像给我送了一堆软面条来当建筑材料,这能行吗?”后来啊,经过协商,供应商把有问题的管子都给换了,还赔偿了一部分因为延误工期造成的损失。
在确定赔偿标准的时候,还得看双方有没有什么合同约定。
要是合同里写得明明白白的,那就按照合同来,这就简单多了。
可要是没写呢,那就得参考一些行业标准或者惯例了。
不过这行业标准有时候也不是那么好界定的,还得具体问题具体分析。
镀锌故障处理培训资料
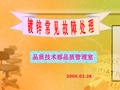
钝化前必须先出光。 出光液为3~5%硝酸
低铬彩虹色钝化常见故障和处理方法
调整在工 艺规定的 pH值范围
pH值不当
硫酸偏低
补充硫 酸或硫 酸盐
改善镀层结 晶和出光液
不出现们彩虹色 彩虹色极淡
镀层本身 光亮度差 钝化时间短
低铬彩虹色钝化常见故障和处理方法
补充硝酸或 硫酸 钝化液老化 pH值偏高 用活 性碳 处理
可能原因
光亮剂含量偏低 pH值偏高或偏低 镀液的温度有点高
氯化钾镀锌常见故障处理方法
低电流密度区镀层发暗 可能原因
光 亮 剂 含 量 偏 低 氯 化 钾 含 量 偏 低 镀 液 的 温 度 偏 高 重 金 属 杂 质 污 染
氯化钾镀锌常见故障处理方法
可能原因
前处理不良
有机杂质多
镀层有条纹 或斑点
锌酸盐镀锌常见故障处理方法
可能原因
阳极面积小 及时补充锌板
碱含量低 补碱
阳极钝化 锌含量下降
阳极Da大
镀件面积大
工件面积为阳极面积的 1/2
氯化钾镀锌常见故障处理方法
氯化钾镀锌配方
• 氯化锌 60~80 g/l • 氯化钾 180~220 g/l • 硼酸 25~35 g/l • ZB—85 15~20 ml/l • pH值 4.5~5.5 • 温度 10~30℃ • 阴极电流密度 0.5~3.0 A/dm2
氢氧化钠 10~20 g/l 硫化钠 3~7 g/l 温度 室温 时间 5~15s
铬酸酐 150~200 g/l 碳酸钡 2~4 g/l 温度 室温 时间 5~15s 磷酸三钠 60 温度 室温 时间 5~15s g/l
银白色
蓝白色
蓝白色
锌镀层的白色钝化
- 1、下载文档前请自行甄别文档内容的完整性,平台不提供额外的编辑、内容补充、找答案等附加服务。
- 2、"仅部分预览"的文档,不可在线预览部分如存在完整性等问题,可反馈申请退款(可完整预览的文档不适用该条件!)。
- 3、如文档侵犯您的权益,请联系客服反馈,我们会尽快为您处理(人工客服工作时间:9:00-18:30)。
玛钢管件电镀锌常见问题解析引言:近日,我应邀前往山西某玛钢加工基地的镀锌车间处理电镀故障,总结了一些经验,在此分享给大家,希望同行朋友们指正。
一、玛钢材料的特性
可锻铸铁俗称玛钢,马铁.蠕墨铸铁的生产过程是:首先浇注成白口铸铁件,然后经可锻化退火(可锻化退火使渗碳体分解为团絮状石墨)而获得可锻铸铁件。
可锻铸铁的化学成分是: wC=2.2%~2.8%,wSi=1.0%~1.8%,wMn=0.3%~0.8%,wS≤0.2%,wP≤0.1%
可锻铸铁的组织有二种类型:
铁素体(F)+团絮状状石墨(G);珠光体(P)+团絮状石墨(G).
二、玛钢管件氯化钾镀锌工艺流程
酸洗-- 二联水洗-- 除油--三联水洗--活化--水洗-- 氯化钾镀锌(滚镀)-- 回收--二联水洗--出光--六价蓝白钝化-- 二联水洗-- 热水洗--烘干
以上工艺流程为标准的自动线工艺,一般手动线没有这么完善的流程,一般为
酸洗-- 三联水洗-- 氯化钾镀锌(滚镀)-- 回收--水洗--六价蓝白钝化-- 二联水洗-- 热水洗--烘干
三、玛钢管件镀锌的常见故障原因解析
1、低区发黑无镀层
低区发黑镀层薄或无镀层其实就是深镀能力差导致的,一般改善镀液的深镀能力即可解决。
在日常生产中,保持氯化钾的浓度为220-240g/L氯化锌45-50g/L硼酸30-35g/L,其中氯化钾偏低或偏高都会对低区产生一定影响。
当氯化钾偏低时,导致整体电流效率下降,甚至低区无电流通过,则难以上镀;当氯化钾偏高时,虽然提高了镀液的电导率,但同时也会增大高区的阴极极化值,造成高低区镀层厚度相差大,降低了镀液的分散能力。
氯化锌的含量跟钾盐应保持着特定的比例,一般为4-4.5/1氯化锌高时,高区上镀较快,影响低区的电沉积速度,氯化锌偏低时,造成镀液中锌离子浓度偏低,会在阴极上表面造成浓差极化,过多的电子因得不到锌离子而在镀件上聚集,易造成高区烧焦,低凹处无镀层。
硼酸的含量直接影响镀液PH的稳定,在电解中不断的补充H以平衡析出的OH。
硼酸的含量在常温时30-35为最佳。
PH升高导致深镀能力差。
2、镀层发黄或变色
如镀件出槽时呈米黄色,经过硝酸出光后能洗净,则为表面有少量的有机物,只要钝化后不变色,镀件表面的有机物不会太多,不影响镀层质量。
但在实际生产中由于镀液中添加剂的使用会产生大量的有机分解产物,如镀液维护不当,就会造成镀件表面有机产物过多,影响后处理钝化膜的形成,耐蚀性能下降,导致变色。
同时当铁离子在镀液中的浓度达到25mg/L时,由于铁的电极电位比锌正,在大的电流密度下(高区)优于锌先沉积到镀件。
在出光和钝化过程中,铁离子都会与硝酸根反应Fe+HNO3=Fe(NO3)2+H2,形成棕黑色,难以形成完整的钝化膜。
钝化液的工作时间和PH及钝化液的浓度也会对表面色泽产生明显的影响,六价蓝白钝化没有三价稳定,如有条件的话,建议采用三价钝化工艺。
3、镀层脆性大、掉锌
由于玛钢件表面较为粗糙,镀层的微观结构和表面光洁的电镀件有一定差别,有极少量的掉锌亦属正常。
锌层的脱落归根结底是镀层的脆性大或结合力不好。
影响镀层脆性的因素主要有:
(1)电流密度从生产效率上来讲,电流密度越大,锌层沉积越快,生产效率高。
但电流密度过大时镀层结晶粗糙,易脱落,同时也影响镀层抗蚀性能。
(2)光亮剂的浓度光亮剂在镀层表面形成吸附薄膜。
这层吸附膜阻碍了锌离子进入阴极表面放电,同于极化作用使锌镀层结晶尺寸变小、细致。
光亮剂浓度低时,阴极极化作用小,对低电流区一般没有影响,但对高电流区影响较大,易产生暗色镀层。
当浓度高时,产生较强的阴极极化作用,明显扩展了电流使用范围。
但过高会使镀层产生蓝雾状,镀层脆性大。
4、镀层阴阳面
导致镀层阴阳面的因素有很多,其主要原因通常有
(1)电流分部不均在阳极面积不足时会导致阳极电流密度过大,电流分部不均。
低区电流过小,难以上镀。
(2)柔软剂与光亮剂的比例以联兴公司(Zinc 781)为例,柔软剂除了对光亮剂有增溶作用外,还有改善低区镀层光亮的作用。
当镀液中柔软剂不足或光亮剂过量时,会导致低区发暗,形成镀层阴阳面。
(3)铜、铅杂质的影响,铜、铅杂质来源于氯化锌和以铅锌矿冶炼的锌板。
铜、铅的电极电位比锌负,多沉积在电流密度小的位置(低区)。
导致低区上镀暗或低区发灰发暗。
结束语:关于玛钢管件镀锌的很多细节问题难以一并论述清楚,该工艺的稳定性也取决于许多的人为操作因素。
在企业数据化管理的今天,我们电镀企业也应力求有自己的工艺管理标准和数据参数。
另外由于镀锌价格低廉,有部分厂家在采购材料时往往力求低价,而有很多的故障原因是因为不合格的材料所引起的,得不尝失。
如在处理镀液时,活性炭的质量会直接影响处理后的效果,粉末的木质活性炭和颗粒状的活性炭在使用过程中的结果是完全不同的。
参考文献:实用镀锌技术倪百祥2010
电镀手册第三版向荣胡如南张允诚2008。