GB 超声波探伤标准
铝铸件超声波探伤标准
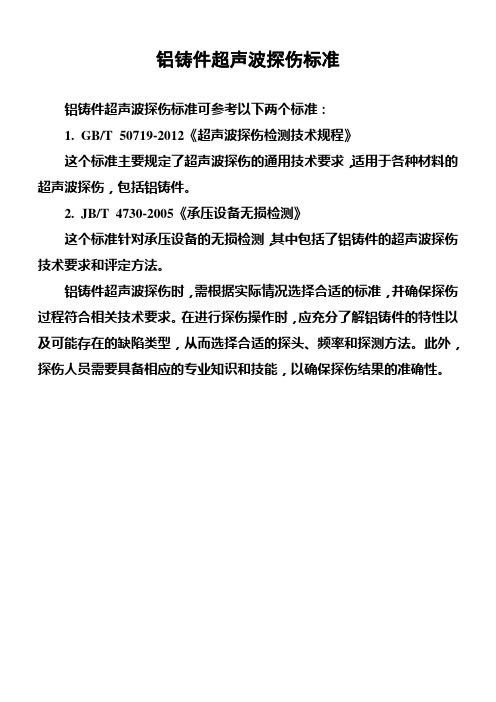
铝铸件超声波探伤标准
铝铸件超声波探伤标准可参考以下两个标准:
1. GB/T 50719-2012《超声波探伤检测技术规程》
这个标准主要规定了超声波探伤的通用技术要求,适用于各种材料的超声波探伤,包括铝铸件。
2. JB/T 4730-2005《承压设备无损检测》
这个标准针对承压设备的无损检测,其中包括了铝铸件的超声波探伤技术要求和评定方法。
铝铸件超声波探伤时,需根据实际情况选择合适的标准,并确保探伤过程符合相关技术要求。
在进行探伤操作时,应充分了解铝铸件的特性以及可能存在的缺陷类型,从而选择合适的探头、频率和探测方法。
此外,探伤人员需要具备相应的专业知识和技能,以确保探伤结果的准确性。
常用超声波探伤标准要求
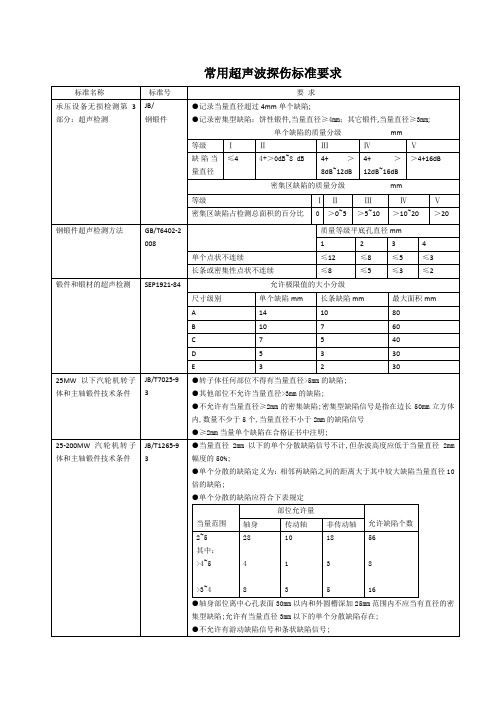
50~200MW汽轮发电机转子锻件技术条件
JB/T1267-93
●不允许有当量直径≥连续性缺陷信号和游动缺陷信号;
●当量直径小于2mm的缺陷不计,允许2~4mm缺陷存在,但相邻两缺陷的距离不小于其中较大缺陷直径的7倍;
●单个分散的缺陷应符合下表规定
允许极限值的大小分级
●不允许有游动信号和条状缺陷信号;
50~200MW汽轮发电机无中心孔转子锻件技术条件
JB/T8706-1998
●当量直径小于mm的缺陷不计,不允许有当量直径等于或大于mm连续缺陷信号和流动缺陷信号;
●在锻件中心φ150 mm范围内,不允许有当量直径大于mm100 MW以下转子锻件,不允许有当量直径大于mm的单个缺陷和大于或等于当量直径mm的密集缺陷信号;
≥3~4
3
1
4
8
总数
15
6
9
30
50MW以下汽轮发电机无中心孔转子锻件技术条件
JB/T 8705-1998
●小于当量直径2 mm的缺陷不计;
●不允许有连续性缺陷信号及游动信号;
●在中心φ150 mm范围内不允许有当量直径大于4 mm的缺陷和大于或等于当量直径mm的密集缺陷信号;
●外圆槽深加25 mm范围内不允许有当量直径大于4 mm的缺陷,其它区域允许有当量直径2~5mm分散的单个缺陷存在,但相邻两个缺陷的距离不小于其较大缺陷直径的5倍;
当量范围
部位允许量
允许缺陷个数
轴身
传动轴
非传动轴
2~5
其中:
>4~5
>3~4
28
4
8
10
1
3
GB超声波探伤标准
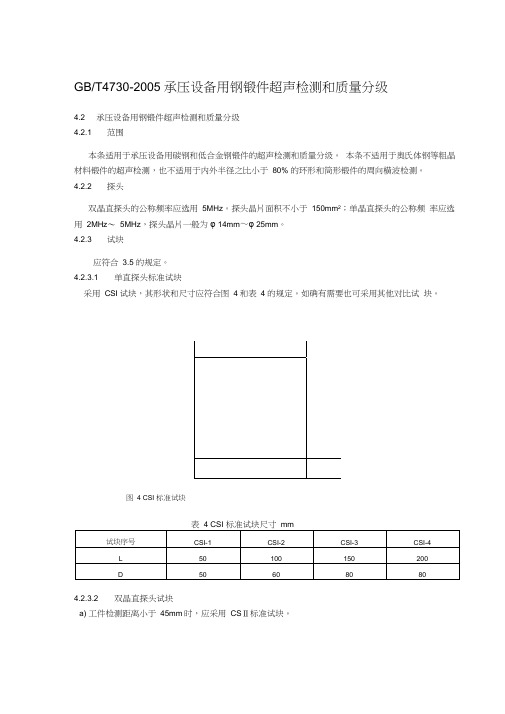
GB/T4730-2005 承压设备用钢锻件超声检测和质量分级4.2 承压设备用钢锻件超声检测和质量分级4.2.1 范围本条适用于承压设备用碳钢和低合金钢锻件的超声检测和质量分级。
本条不适用于奥氏体钢等粗晶材料锻件的超声检测,也不适用于内外半径之比小于80% 的环形和筒形锻件的周向横波检测。
4.2.2 探头双晶直探头的公称频率应选用5MHz。
探头晶片面积不小于150mm2;单晶直探头的公称频率应选用2MHz~5MHz,探头晶片一般为φ14mm~φ25mm。
4.2.3 试块应符合 3.5 的规定。
4.2.3.1 单直探头标准试块采用CSI试块,其形状和尺寸应符合图4和表 4 的规定。
如确有需要也可采用其他对比试块。
图 4 CSI 标准试块4.2.3.2 双晶直探头试块a) 工件检测距离小于45mm时,应采用CSⅡ标准试块。
b) CS Ⅱ试块的形状和尺寸应符合图 5 和表 5 的规定。
试块序号孔径检测距离L123456789 CSII-1φ251015202530354045 CSII-2φ3CSII-3φ4CSII-4φ64.2.3.3 检测面是曲面时,应采用CSⅢ标准试块来测定由于曲率不同而引起的声能损失,其形状和尺寸按图 6 所示。
4.2.4 检测时机检测原则上应安排在热处理后,孔、台等结构机加工前进行,检测面的表面粗糙度Rα≤ 6.3 μ m。
图 5 CS Ⅱ标准试块CSIII 标准试块图 7 检测方向 ( 垂直检测法 )4.2.5.3 横波检测 钢锻件横波检测应按附录 C (规范性附录 ) 的要求进行。
4.2.6 灵敏度的确定4.2.6.1单直探头基准灵敏度的确定4.2.5 检测方法4.2.5.1 一般原则 锻件应进行纵波检测,对筒形和环形锻件还应增加横波检测。
4.2.5.2纵波检测a ) 原则上应从两个相互垂直的方向进行检测, 尽可能地检测到锻件的全体积。
方向如图 7 所示。
其他形状的锻件也可参照执行。
超声波探伤标准GB11345-89

13.5 反射波幅位于Ⅲ区的缺陷, 无论其指示长度如何, 均评定为Ⅳ级.13.6 不合格的缺陷, 应予返修, 返修区域修后, 返修部位及补焊受影响的区域, 应按原探伤条件进行复验,复探部位的缺陷亦应按12 章评定.14 记录与报告14.1 检验记录主要内容: 工件名称、编号、焊缝编号、坡口形式、焊缝种类、母材材质、规格、表面情况、探伤方法、检验规程、验收标准、所使用的仪器、探头、耦合剂、试块、扫描比例、探伤灵敏度. 所发现的超标缺陷及评定记录, 检验人员及检验日期等. 反射波幅位于Ⅱ区, 其指示长度小于表 6 的缺陷也应予记录.14.2 检验报告主要内容: 工件名称、合同号、编号、探伤方法、探伤部位示意图、检验范围、探伤比例收标准、缺陷情况、返修情况、探伤结论、检验人员及审核人员签字等.14.3 检验记录和报告应至少保存7 年.14.4 检验记录和报告的推荐格式见附录 F.附录A标准试块的形状和尺寸( 补充件)注: 尺寸公差±0.1; 各边垂直度不大于0.05;C 面尺寸基准面, 上部各折射角刻度尺寸值见表A1,下部见表A2.附录B对比试块的形状和尺寸( 补充件)B1 对比试块的形状和尺寸见表B1.注: ①尺寸公差±0.1mm; ②各边垂直度不大于0.1; ③表面粗糙度不大于 6.3 μm; ④标准孔与加工面的平行度不大于0.05.附录C串列扫查探伤方法( 补充件)C1 探伤设备C1.1 超声波探伤仪的工作方式必须具备一发一收工作状态.C1.2 为保证一发一收探头相对于串列基准线经常保持等距离移动, 应配备适宜的探头夹具, 并适用于横方型及纵方型两种扫查方式.C1.3 推荐采用, 频率2-2.5Mhz, 公称折射角45°探头, 两探头入射点间最短间距应小于20mm.C2 仪器调整C2.1 时基线扫描的调节采用单探头按标准正文9.1 的方法调节, 最大探测范围应大于 1 跨距声程.C2.2 灵敏度调整在工件无缺陷部位, 将发、收两探头对向放置, 间距为 1 跨距, 找到底面最大反射波见图C1及式C1,调节增益使反射波幅为荧光屏满幅高度的40%,并以此为基准波高. 灵敏度分别提高8dB、14dB 和20dB 代表判废灵敏度、定量灵敏度和评定灵敏度.C3 检验程序C3.1 检验准备a. 探伤面对接焊缝的单面双侧;b. 串列基准线如发、收两探头实测折射角的平均值为β或K 值平均为K. 在离参考线( 参考线至探伤截面的距离L'-0.5P) 的位置标记串列基准线, 见图C2 及式C2.0.5P=δtg β(C1)或0.5P= δK (C2)C3.2 初始探伤C3.2.1 探伤灵敏度不低于评定灵敏度.C3.2.2 扫查方式采用横方形或纵方形串列扫查, 扫查范围以串列基准线为中心尽可能扫查到整个探伤截面, 每个探伤截面应扫查一遍.C3.2.3 标记超过评定线的反射波, 被判定为缺陷时, 应在焊缝的相应位置作出标记.C3.3 规定探伤C3.3.1 对象只对初始检验标记部位进行探伤.C3.3.2 探伤灵敏度为评定灵敏度.C3.3.3 缺陷位置不同深度的缺陷, 其反射波均出现在相当于半跨距声程位置见图C3. 缺陷的水平距离和深度分别为:(C3)(C4)C3.3.4 缺陷以射波幅在最大反射波探头位置, 以40%线为基准波高测出缺陷反射波的dB数作为缺陷的相对波幅, 记为SL±----dB.C3.3.5 缺陷指示长度的测定采用以评定灵敏度为测长灵敏度的绝对灵敏度法测量缺陷指示长度. 即进行左右扫查( 横方形串列扫查), 以波幅超过评定线的探头移动范围作为缺陷指示长度.C4 缺陷评定所有反射波幅度超过评定线的缺陷均应按标准正文第12 章的规定予以评定, 并按第13 章的规定对探伤结果作等级分类.附录D距离---- 波幅(DAC)曲线的制作( 补充件)D1 试件D1.1 采用标准附录B对比试块或其他等效形式试块绘制DAC曲线.D1.2 R 小于等于W2/4 时, 应采用探伤面曲率与工件探伤面曲率相同或相近的对比试块.D2 绘制步骤DAC曲线可绘制在坐标纸上( 称DAC曲线), 亦可直接绘制在荧光屏前透明的刻度板上( 称DAC曲线板).D2.1 DAC 曲线的绘制步骤如下:a. 将测试范围调整到探伤使用的最大探测范围, 并按深度、水平或声程法调整时基线扫描比例;b. 根据工件厚度和曲率选择合适的对比试块, 选取试块上民探伤深度相同或接近的横孔为第一基准孔, 将探头置于试块探伤面声束指向该孔, 调节探头位置找到横孔的最高反射波;c. 调节" 增益" 或" 衰减器" 使该反射幅为荧光屏上某一高度( 例如满幅的40%)该波高即为" 基准波高", 此时,探伤系统的有效灵敏度应比评定灵敏度高10dB;d. 调节衰减器, 依次探测其他横孔, 并找到最大反射波高, 分别记录各反射波的相对波幅值(dB);e. 以波幅(dB) 为纵坐标, 以探沿距离( 声程、深度或水平距离) 为横坐标, 将c、d 记录数值描绘在坐标纸上;f. 将标记各点连成圆滑曲线, 并延长到整个探测范围, 最近探测点到探距离O点间画水平线, 该曲线即为Φ3mm横孔DAC曲线的基准线;g. 依据标准正文表 3 规定的各线灵敏度, 在基准线下分别绘出判废线、定量线、评定线, 并标记波幅的分区;h. 为便于现场探伤校验灵敏度, 在测试上述数据的同时, 可对现场使用的便携试块上的某一参考反射体进行同样测量, 记录其反射波位置和反射波幅(dB) 并标记在DAC曲线图上.D2.2 DAC 曲线的绘制步骤如下:a. 同D2.1a;b. 依据工件厚度和曲率选择合适的对比试块, 在试块上所有孔深小于等于探测深度的孔中, 选取能产生最大反射波幅的横孔为第一基准孔;c. 调节" 增益" 使该孔的反射波为荧光屏满幅高度的80%,将其峰值标记在荧光屏前辅助面板上. 依次探测其它横孔, 并找到最大反射波, 地峰值点标记在辅助面板上, 如果做分段绘制, 可调节衰减器分段绘制曲线;d. 将各标记点连成圆滑曲线, 并延伸到整个探测范围, 该曲线即为Φ3mm横孔DAC曲线基准线; 定量灵敏度下, 如分别将灵敏度提高或降低6dB, 该线将分别代表评定或判废线.(A 级检验DAC基准线即为判废线);e. 将灵敏度提高(8-50mm提高到10dB,50-300mm提高10dB或8dB), 该线表示定量线. 在定量灵敏度下, 如分别将灵敏度提高或降低6dB, 该线将分别代表评定或判废线.(A 级检验DAC基准线即为判废线);f. 在作上述测试的同时, 可对现场使用的便携式试块上的某一参考反射体作同样测, 并将其反射波位置和峰值标记在曲线板上, 以便现场进行灵敏度校验.附录E声能传输损耗差的测定( 补充件)工件本身反射波幅度有影响的两个主要因素是材料的材质衰减和工件表面粗糙度及耦合情况的表面声能损失.超声波的材质衰减对普通碳钢或低合金网板材, 在频率低于3MHz声程不超过200mm时, 可以忽略不记, 或者一般来说衰减系数小于0.01dB/mm 时, 材质衰减可以不予考虑, 标准试块和对比试块均应满足这一要求.受检工件探伤时, 如声程较大, 或材质衰减系数超过上述范围, 在确定缺陷反射波幅时, 应考虑作材料衰减修整, 如被检工件表面比较粗糙还应考虑表面声能损失问题.E1 横波超声材质衰减的测量E1.1 制作与受检工件材质相同或相近, 厚度约40mm表面粗糙度与对比试块RB相同的平面型试块图E1.E1.2 采用工件检验中使用的斜探头按深度1:1 调节仪器时基扫描.E1.3 另选用一只与该探头尺寸、频率、角度相同的斜探头, 两探头按图E1 所示方向置于平板试块上, 两探头入射点间距离为1P,仪器调为一发一收状态, 找到接以最大反射波幅, 记录其波幅值Hi(dB).E1.4 将两探头拉开到距离为2P,找到最大反射波幅, 记录其波幅值H2(dB).E1.5 实际探伤中超声波总是往返的, 故双程的衰减系数αH可用下式计算:(E1)S1=40/COSβ+l' (E2)S2=80/COSβ+l'0 (E3)(E4)式中L0---- 晶片到为的距离, 作为简化处理亦可取l'0=l0, mm;△------ 声程S1、S2不考虑材质衰减时大平面的反射波幅dB 差, 可用公式计算或从该探头的D·G·S 曲线上查得,dB;由于S2 近拟为S1 的2 倍, 在声程大于 3 倍近场长度N时, △约为6dB.E1.6 如果在图E1 试块和RB对比试块的侧面测得波幅HZ,相差不过1dB, 则可不考虑工件的材质衰减.E2 传输损失差的测定E2.1 采用工件检验中使用的斜探头, 按深度比例调节仪器时基扫描.E2.2 选用另一与该探头尺寸、频率、角度相同的斜探头, 两探头按图E2 所示方向置于对比试块侧面上, 两探头入射点间距离为1P, 仪器调为一发一收状态.E2.3 在对比试块上, 找到接收波最大反射波幅, 记录其波幅值H1(dB).E2.4 在受检工件板材上( 不通过焊缝) 同样测出接收波最大反射波幅, 记录其波幅值H2(dB).E2.5 传输损失差△V为:△V=H1-H2-△1- △2 (E5)式中△1---- 声程S1、S2 不考虑材质衰减时大平面的反射波幅dB 差, 可用公式计算或从探头的D·G·S 曲线上查得,dB;S1---- 在对比试块中的声程,mm;S2---- 在工件板材中的声程,mm;△2-- 试块中声程S1 时与工件中声程S2 时的超声材质衰减差值,dB.如试块图E1 按E1 测量材质衰减系数小于0.01dB/mm, 此项可以不予考虑.附录F焊缝超声波探伤报告和记录( 参考件)焊缝超声波探伤报告焊缝超声波探伤记录附加说明:本标准由中华人民共和国机械电子工业部提出.本标准由全国无损检测标准化技术委员会归口.本标准由哈尔滨焊接研究所负责起草, 主要参加单位: 哈尔滨锅炉厂、劳动人事部锅炉压力容器检测研究中心.本标准主要起草人李生田、李家鳌、康纪黔、张泽丰、王梅屏.。
超声波探伤检测规程

超声波探伤检测规程一、总则适用范围:本规程适用各类锻(铸)件探伤检测依据:编制本规程的依据如下:委托书及有关工程技术检验要求设计图JB/T8290-2011压力容器无损检测标准,锻件质量级别所评定的超声检测。
GB/T7233.2-2023标准对铸件进行质量评级GB/T11345-2013钢焊缝手工超声波探伤Ⅱ级二、检测人员应是取得无损检测人员资格考委会颁发的超声Ⅱ级或Ⅱ级以上人员,对检查对象特征有足够的认识三、仪器、探头试块、耦合剂1、所用探伤仪器必须符合JB/T 8290-2011标准中7.3条关于仪器的要求2、所用探头必须符合JB/T 8290-2011标准中7.3条关于探头的要求3、所用试块为JB/T 8290-2011标准9.1.2条中CSK-ⅠA、CSK-ⅡA试块、CS-1、CS-2试块4、所用试块为GB/T 11345-2013标准中CSK-ⅢA试块。
5、所用试块为GB/T 7233.2-2023标准中CS-1-5、ZB300试块。
6、耦合剂:机油四、探伤1、采用纵波直探头,用CS-1和CS-2试块来调节探伤灵敏度和对缺陷定量、定位。
2、探伤灵敏度:由锻件技术要求或有关标准确定的一般不低于Φ2平底孔总量直径。
分两种:a.底油调节法b.试块调节法,常用底波调节法3、探伤时机:锻件应在热处理后进行探伤,对于带孔槽和台阶的锻件,探伤应在加工前进行。
4、扫查方式:原则上应在探测面上从两个相互垂直的方向进行全面扫查,扫查覆盖面应为探头直径的15%,探头移动速度不大于150mm/s。
扫查过程中要注意观察缺陷波的情况和底波的变化情况。
五、缺陷的测定(数量、大小、位置)扫查中发现锻件内部缺陷时要根据缺陷反射波高,测定缺陷当量大小位置,一般用当量法定量,计算法:6dB法。
锻(铸)件质量级别评定:1、根据JB/T 8290-2011标准中,表6-1、表6-2、表6-3对锻件进行质量评级。
2、根据GB/T 7233.2-2023标准对铸件进行质量评级。
超声波探伤检测规范

超声波探伤检测规范一.目的对回转支承产品配套使用的毛坯内部质量进行超声波探伤检测,以确保产品质量。
二.范围所有进厂回转支承毛坯(包括50Mn和42CrMo材料)三.检测标准检验方法依据GB/T 6402-2008≤钢锻件超声检测方法≥的规定进行检验,标准GB/T 6402-2008适用于脉冲反射式超声波检验法对厚度或直径大于100mm的碳钢及低合金钢一般锻件的超声波检测。
四.检测条件及探伤方法(1)环形毛坯锻件接触法检验时,一般在粗加工完成后,锻件表面粗糙度Ra 值应小于3.2um,表面应平整,无影响声耦合的氧化皮,赃物等附着物,并满足检验要求;(2)在探头与检测面之间,应使用合适的耦合剂;(3)根据锻件加工工艺,环形毛坯主要探测面为外圆百分之百检测,辅助探测为上下端面;(4)扫查方式为手工扫查,探头在检测面的扫查间距,应保证有15%的声束覆盖;(5)扫查速度即探头相对锻件的移动速度,应在150mm/s以下;(6)在毛坯粗加工到要求的表面粗糙度时,从毛坯外圆面及上下端面进行100%的扫查,同时为了避免耦合层厚度的影响,也进行变换探头频率探测,以便检测出缺陷。
a)探头频率选择频率选择:对于毛坯厚度较小时,应选择较大的探头频率以提高其检测分辨力,毛坯厚度较大时,应选择较小的探头频率以提高其穿透能力。
b)检验方案1、对于客户明确要求的毛坯,进行全检。
2、对于三个车间直径较大的毛坯,都进行一定数量的抽检探测,其满足的比例为:3、在实际操作过程中,对发现内部有质量缺陷的毛坯提供的毛坯进行加严检验。
五、合格判定(1)在探伤过程中,对发现有缺陷的毛坯,及时将其缺陷孔当量和缺陷实际位置计算出来,并记录备案,及时将其反馈于部门领导及车间与供应部门。
(2)当缺陷孔当量小于Φ2mm时,按照国标GB/T 6402-2008其毛坯不做废品处理,仍按正常工序加工,但及时对其进行追踪,观察其加工过程中的情况,将其型号、编号,及有关缺陷情况进行记录,以备案。
钢结构焊缝超声波探伤实施细则
1总则1.1适用范围本实施细则依据GB/T11345 - 89”钢焊缝手工超声波探伤方法和探伤结果的分级” 编制,适用于母材厚度不小于8mm的铁素体类钢全焊透熔化焊对接焊缝脉冲反射法手工超声波检验。
不适用于铸钢、奥氏体不锈钢焊缝,外径小于159mm的钢管对接焊缝,内径小于等于200mm的管座角焊缝及外径小于250mm和内外径比小于80%的纵向焊缝。
1.2检测人员1.2.1从事焊缝探伤的检验人员必须掌握超声波的基础技术,具有足够的焊缝超声波探伤经验,并掌握一定的材料、焊接基础知识。
1.2.2焊缝超声检验人员应按有关规程或技术条件的规定经严格的培训和考核,并持有相应项目的上岗证,从事相对应考核项目的检验工作。
1.3本实施细则不涉及抽样方法及验收标准,需要时应根据设计图纸或相应的验收规范等技术文件制定专用的工艺,明确具体的抽样方法及验收标准。
1.4必要时应根据具体的检测对象,针对具体的接头型式、板厚等编制工艺卡。
2探伤仪、探头及系统性能要求2.1探伤仪:使用A型显示脉冲反射式探伤仪,其工作频率范围应为1〜5MHz,探伤仪应配备衰减器或增益控制器,其精度为任意相邻12dB误差在±1dB内,步进级每档不大于2dB,总调节量应大于60dB,水平线性误差不大于1%,垂直线性误差不大于5%。
2.2探头2.2.1探头应有晶片尺寸、K值或折射角度、入射点刻度、型号、厂家等标志。
2.2.2晶片的有效面积不应超过500mm2,且任一边长不大于25mm。
2.2.3声束轴线水平偏离角应不大于2°2.2.4探头主声束垂直方向的偏离,不应有明显的双峰。
2.2.5斜探头的公称折射角6为45°、60°、70°或K值为1. 0、1.5、2. 0、2. 5, 折射角的实测值与公称值的偏差应不大于2°(K值偏差不应超过±0.1)。
如受工件几何形状或探伤面曲率等限制也可选用其它公称角度/K值的探头。
GB4730超声波探伤标准
GB/T4730-2005承压设备用钢锻件超声检测和质量分级4.2 承压设备用钢锻件超声检测和质量分级4.2.1范围本条适用于承压设备用碳钢和低合金钢锻件的超声检测和质量分级。
本条不适用于奥氏体钢等粗晶材料锻件的超声检测,也不适用于内外半径之比小于80%的环形和筒形锻件的周向横波检测。
4.2.2探头双晶直探头的公称频率应选用5MHz。
探头晶片面积不小于150mm2;单晶直探头的公称频率应选用2MHz~5MHz,探头晶片一般为φ14mm~φ25mm。
4.2.3试块应符合3.5的规定。
4.2.3.1单直探头标准试块采用CSI试块,其形状和尺寸应符合图4和表4的规定。
如确有需要也可采用其他对比试块。
图4 CSI标准试块表4 CSI标准试块尺寸 mm试块序号CSI-1 CSI-2 CSI-3 CSI-4 L 50 100 150 200D 50 60 80 804.2.3.2双晶直探头试块a) 工件检测距离小于45mm时,应采用CSⅡ标准试块。
b) CS Ⅱ试块的形状和尺寸应符合图5和表5的规定。
图5 CS Ⅱ标准试块表5 CS Ⅱ标准试块尺寸 mm试块序号 孔径 检测距离L123456789CSII-1 φ2 51015202530354045CSII-2 φ3 CSII-3 φ4 CSII-4φ64.2.3.3 检测面是曲面时,应采用CS Ⅲ标准试块来测定由于曲率不同而引起的声能损失,其形状和尺寸按图6所示。
图6 CSIII 标准试块4.2.4 检测时机检测原则上应安排在热处理后,孔、台等结构机加工前进行,检测面的表面粗糙度R α≤6.3μm 。
4.2.5检测方法4.2.5.1一般原则锻件应进行纵波检测,对筒形和环形锻件还应增加横波检测。
4.2.5.2 纵波检测a) 原则上应从两个相互垂直的方向进行检测,尽可能地检测到锻件的全体积。
主要检测方向如图7所示。
其他形状的锻件也可参照执行。
b) 锻件厚度超过400mm时,应从相对两端面进行100%的扫查。
常用超声波探伤标准要求[参考资料]
●≥2mm当量单个缺陷在合格证书中注明。
25-200MW汽轮机转子体和主轴锻件技术条件
JB/T1265-93
●当量直径2mm以下的单个分散缺陷信号不计,但杂波高度应低于当量直径2mm幅度的50%。
冶金设备制造通用技术条件(锻钢件超声波探伤方法)
YB/T036.10-1992
●密集缺陷:在钢中距离50mm的范围内,有5个以上大于或等于探伤灵敏度基准的缺陷波,称密集缺陷。
●条状缺陷:当缺陷反射波幅大于或等于探伤灵敏度基准波幅,长度大于或等于30mm的连续性缺陷,称条状缺陷。
标准号
要求
模锻锤和大型机械锻压机用模块技术条件
GB11880-89
●允许存在个别的、分散的、不大于当量直径¢2mm的冶金缺陷。
●在100cm2的面积内,当量直径¢2~¢4 mm的冶金缺陷不超过3个,其中¢3~¢4 mm的冶金缺陷只允许有1个。
●允许有2-4个小于当量直径¢2mm的冶金缺陷的密集区,但每区不得超过10cm3,每区之间距不得小于150mm。
●距中心孔表面75mm以外部位,允许有3个小于当量直径1.6mm的密集缺陷区,但密集区在任何方向的尺寸均应不大于20mm,并且任何两缺陷区间距离应不小于120mm。
●不允许有游动缺陷信号和条状缺陷信号。
50MW以下汽轮发电机转子锻件技术条件
JB/T7026-93
●小于当量直径2mm的缺陷不计。
●不允许有当量直径≥2mm的密集型缺陷密集型缺陷信号,连续性缺陷信号,及游动信号。
●允许有当量直径2~5mm分散的单个缺陷存在,但相邻两个缺陷的距离不小于其较大缺陷直径的5倍,总数量不得超过56个。
GB T 5777-1996 无缝钢管超声波探伤检验方法
无缝钢管超声波探伤检验方法Seamless steel pipe and tubing—Methods for ultrasonic testingGB/T5777-1996(eqv ISO9303—1989)前言本标准等效采用国际标准化组织ISO9303:1989(E)《用于压力目的的无缝和焊接(埋弧焊除外)钢管纵向缺陷的全周向超声波检测》,对GB4163—84《不锈钢管超声波探伤方法》和GB5777—86《无缝钢管超声波探伤方法》进行修订并将二者合并。
修订主要内容如下:1.如供需双方无特殊协议,各种用途钢管均改为双向探测,从而可更有效地保证探伤后钢管的实物质量。
2.对比试样上的人工缺陷级别的划分与ISO9303相同。
与GB4163相比,原第三级的7%改为8%,原第五级的15%改为12.5%。
与GB5777相比,增加一个最高级的3%,减少一个最低级的15%,原第四级的12%改为12.5%。
3.在技术内容上与ISO9303相比,增加了很有推广前途的电磁声检测新技术和对探伤设备综合性能的测试要求。
本标准可用于各种用途无缝钢管的超声波探伤检验。
本标准自1997年3月1日实施,同时代替GB4163—84和GB5777—86。
本标准的附录A是标准的附录。
本标准由冶金工业部提出。
本标准由全国钢标准化技术委员会归口。
本标准由首钢总公司特殊钢公司、上海第五钢厂负责起草。
本标准主要起草人:杨学智、刘丁柱、陈燕、王槐祥、倪秀美。
本标准1986年1月首次发布。
国际标准前言ISO(国际标准化组织)是一个国家标准团体(ISO成员体)的世界范围的联盟。
国际标准的准备工作通常是自始至终由ISO专业委员会进行。
每个成员体所感兴趣的题目属于哪个专业委员会即在该委员会中建立适当的组织。
国际组织、政府和非政府、以及ISO中的联络人,同样地参加工作。
ISO与国际电工技术委员会(IEC)合作仔细地研究电工技术标准化中的所有问题。
国际标准草案,同国际标准一样在通过ISO会议正式通过之前先由专业委员会成员体批准。
- 1、下载文档前请自行甄别文档内容的完整性,平台不提供额外的编辑、内容补充、找答案等附加服务。
- 2、"仅部分预览"的文档,不可在线预览部分如存在完整性等问题,可反馈申请退款(可完整预览的文档不适用该条件!)。
- 3、如文档侵犯您的权益,请联系客服反馈,我们会尽快为您处理(人工客服工作时间:9:00-18:30)。
GB/T4730-2005承压设备用钢锻件超声检测和质量分级
承压设备用钢锻件超声检测和质量分级
4.2.1范围
本条适用于承压设备用碳钢和低合金钢锻件的超声检测和质量分级。
本条不适用于奥氏体钢等粗晶材料锻件的超声检测,也不适用于内外半径之比小于80%的环形和筒形锻件的周向横波检测。
4.2.2探头
双晶直探头的公称频率应选用5MHz。
探头晶片面积不小于150mm2;单晶直探头的公称频率应选用2MHz~5MHz,探头晶片一般为φ14mm~φ25mm。
4.2.3试块
应符合的规定。
4.2.3.1单直探头标准试块
采用CSI试块,其形状和尺寸应符合图4和表4的规定。
如确有需要也可采用其他对比试块。
图4 CSI标准试块
表4 CSI标准试块尺寸 mm
试块序号CSI-1 CSI-2 CSI-3 CSI-4 L 50 100 150 200
D 50 60 80 80
4.2.3.2双晶直探头试块
a) 工件检测距离小于45mm时,应采用CSⅡ标准试块。
b) CS Ⅱ试块的形状和尺寸应符合图5和表5的规定。
图5 CS Ⅱ标准试块
表5 CS Ⅱ标准试块尺寸 mm
试块序号 孔径 检测距离L
1
2
3
4
5
6
7
8
9
CSII-1 φ2 5
10
15
20
25
30
35
40
45
CSII-2 φ3 CSII-3 φ4 CSII-4
φ6
4.2.3.3 检测面是曲面时,应采用CS Ⅲ标准试块来测定由于曲率不同而引起的声能损失,其形状和尺寸按图6所示。
图6 CSIII 标准试块
4.2.4 检测时机
检测原则上应安排在热处理后,孔、台等结构机加工前进行,检测面的表面粗糙度R α≤μm 。
4.2.5检测方法
4.2.
5.1一般原则
锻件应进行纵波检测,对筒形和环形锻件还应增加横波检测。
4.2.
5.2 纵波检测
a) 原则上应从两个相互垂直的方向进行检测,尽可能地检测到锻件的全体积。
主要检测方向如图7所示。
其他形状的锻件也可参照执行。
b) 锻件厚度超过400mm时,应从相对两端面进行100%的扫查。
注: 为应检测方向;※为参考检测方向。
图7 检测方向(垂直检测法)
4.2.
5.3 横波检测
钢锻件横波检测应按附录C(规范性附录)的要求进行。
4.2.6 灵敏度的确定
4.2.6.1 单直探头基准灵敏度的确定
当被检部位的厚度大于或等于探头的3倍近场区长度,且探测面与底面平行时,原则上可采用底波计算法确定基准灵敏度。
对由于几何形状所限,不能获得底波或壁厚小于探头的3倍近场区时,可直接采用CSI 标准试块确定基准灵敏度。
4.2.6.2 双晶直探头基准灵敏度的确定
使用CSII 试块,依次测试一组不同检测距离的驴3mm 平底孔(至少三个)。
调节衰减器,作出双晶直探头的距离一波幅曲线,并以此作为基准灵敏度。
4.2.6.3 扫查灵敏度一般不得低于最大检测距离处的矿2mm 平底孔当量直径。
4.2.7 工件材质衰减系数的测定
4.2.7.1 在工件无缺陷完好区域,选取三处检测面与底面平行且有代表性的部位,调节仪器使第一次底面回波幅度(B 1或B n )为满刻度的50%,记录此时衰减器的读数,再调节衰减器,使第二次底面回波幅度(B 或B m )为满刻度的50%,两次衰减器读数之差即为(B 1、B 2)或(B n 、B m )的dB 差值(不考虑底面反射损失)。
4.2.7.2 衰减系数(T<3N ,且满足,n>3N/T ,m=2n)按式(1)计算:
[]T n m a )(2/6B B 21---)(= (1)
式中:
a ——衰减系数,dB/m(单程);
)(m n B B -——两次衰减器的读数之差,dB ; T ——工件检测厚度,mm ;
N ——单直探头近场区长度,mm ; m 、n ——底波反射次数。
4.2.7.3 衰减系数(T≥3N)按式(2)计算
[]T B B a 2/6)(21--= (2)
式中:
)(21B B -——两次衰减器的读数之差,dB ; 其余符号意义同式(1)。
4.2.7.4 工件上三处衰减系数的平均值即作为该工件的衰减系数。
4.2.8 缺陷当量的确定
4.2.8.1 被检缺陷的深度大于或等于探头的3倍近场区时,采用AVG 曲线及计算法确定缺陷当量。
对于3倍近场区内的缺陷,可采用单直探头或双晶直探头的距离一波幅曲线来确定缺陷当量。
也可采用其他等效方法来确定。
4.2.8.2 计算缺陷当量时,若材质衰减系数超过4dB/m ,应考虑修正。
4.2.9 缺陷记录
4.2.9.1 记录当量直径超过φ4mm 的单个缺陷的波幅和位置。
4.2.9.2 密集区缺陷:记录密集区缺陷中最大当量缺陷的位置和缺陷分布。
饼形锻件应记录
大于或等于φ4mm当量直径的缺陷密集区,其他锻件应记录大于或等于φ3mm当量直径的缺陷密集区。
缺陷密集区面积以50mm×50mm的方块作为最小量度单位,其边界可由6dB法决定。
4.2.9.3 底波降低量应按表6的要求记录。
表6 由缺陷引起底波降低量的质量分级dB
4.2.9.4衰减系数。
4.2.10 质量分级等级评定
4.2.10.1单个缺陷的质量分级见表7。
4.2.10.2 缺陷引起底波降低量的质量分级见表6。
表7 单个缺陷的质量分级mm
4.2.10.3 缺陷密集区质量分级见表8。
4.2.10.4表6、表7和表8的等级应作为独立的等级分别使用。
4.2.10.5 当缺陷被检测人员判定为危害性缺陷时,锻件的质量等级为v级。