金属切屑原理11
金属切削原理

金属切削原理一、引言金属切削是一种重要的加工方法,广泛应用于机械制造、航空航天、汽车制造等领域。
金属切削的原理是将金属材料通过刀具的切削力和磨擦力进行去除,从而得到所需形状和尺寸的工件。
本文将详细介绍金属切削的原理。
二、金属材料的物理特性金属材料具有高强度、高硬度、高塑性等特点。
在进行切削加工时,需要考虑到这些特性对加工过程和结果的影响。
1.硬度硬度是指材料抵抗外界力量侵蚀和破坏的能力。
在进行金属切削时,硬度会影响到刀具对材料的切削深度和速度。
硬度越大,材料越难被去除,需要采用更高强度和更耐磨损的刀具。
2.韧性韧性是指材料抵抗断裂和变形的能力。
在进行金属切削时,韧性会影响到刀具对材料的变形程度和断裂情况。
韧性越大,材料越容易被刀具弯曲和拉伸,需要采用更大的切削力和更耐磨损的刀具。
3.塑性塑性是指材料在受到外力作用下发生变形的能力。
在进行金属切削时,塑性会影响到材料的变形程度和表面质量。
塑性越大,材料越容易被切削并留下较光滑的表面。
三、切削力的产生金属切削过程中,主要有三种力对工件进行去除:正向切削力、侧向切削力和径向切削力。
这些力产生的原因如下:1.正向切削力正向切削力是指沿着工件表面方向施加在主轴上的推进力。
它是由于主轴上旋转的刀具与工件之间产生了摩擦而引起的。
2.侧向切削力侧向切削力是指垂直于工件表面方向施加在主轴上的推进力。
它是由于主轴上旋转的刀具与工件之间产生了摩擦而引起的。
3.径向切削力径向切削力是指垂直于工件表面方向施加在主轴上的推进力。
它是由于主轴上旋转的刀具与工件之间产生了摩擦而引起的。
四、切削过程中的热效应金属切削过程中,由于摩擦和变形,会产生大量的热量。
这些热量会对材料和刀具造成影响。
1.材料的热变形在金属切削过程中,由于高速旋转的刀具与工件之间产生了摩擦,会使得材料表面温度升高。
当温度达到一定值时,材料就会发生热变形,导致尺寸和形状发生变化。
2.材料的热软化在金属切削过程中,由于高速旋转的刀具与工件之间产生了摩擦,会使得材料表面温度升高。
金属切削原理与刀具的应用

金属切削原理与刀具的应用1. 金属切削原理金属切削是通过机床上的刀具对金属工件进行切削、铣削、车削、钻孔等加工过程。
在金属切削过程中,刀具与工件之间的相对运动产生切削力,使刀具将工件上的金属材料去除,从而实现对工件的加工。
以下是金属切削的基本原理:1.切削速度:切削速度是指刀具切削工件的速度。
切削速度的选择应根据工件材料、刀具材质和切削类型等因素来确定。
高速切削可以提高生产效率,但也会对刀具和工件产生一定的热影响。
2.进给量:进给量是指刀具在单位时间内前进的距离。
进给量的选择取决于工件表面的粗糙度要求、切削力和刀具的耐久度等因素。
3.切削深度:切削深度是指刀具切削时的最大切削量。
切削深度的选择应根据工件材料的硬度、刀具的尺寸和工艺要求来确定。
4.切削力:切削力是指刀具对工件施加的力。
切削力的大小受到切削参数、刀具材质和刀具几何形状的影响。
2. 刀具的应用刀具是金属切削过程中起到切削作用的工具。
不同的工件和切削任务需要选择合适的刀具来进行加工。
以下是常见的刀具及其应用:1.钻头:钻头用于钻孔加工,适用于加工圆孔和柱形孔。
常见的钻头有直柄钻头和 Morse 锥柄钻头两种。
2.车刀:车刀用于车削加工,常用于加工圆柱形工件的外轮廓。
车刀有内刀和外刀之分,可以用于精细车削和粗车削等不同工艺要求。
3.铣刀:铣刀用于铣削加工,可以用于多种铣削操作,如平面铣削、立体铣削、开槽铣削等。
铣刀可分为立铣刀、面铣刀和球形铣刀等。
4.刨刀:刨刀用于刨削加工,可以进行铺刨、面刨和纵切削等操作。
刨刀可根据切削刃的数量和类型来分类,如单刃刨刀、多刃刨刀和筷子刨刀等。
5.刀片:刀片用于各种切削加工,如割断、倒角、切割等。
刀片的种类繁多,根据刀片的应用需求和加工材料的类型来选择合适的刀片。
3. 刀具材料选择刀具材料选择是决定刀具性能的关键,不同的刀具材料有着不同的加工性能和适用范围。
以下是常见的刀具材料及其特点:1.高速钢(HSS):高速钢具有良好的耐磨性和耐热性,适用于中等切削速度和较硬的工件材料。
金属切削原理讲义及刀具
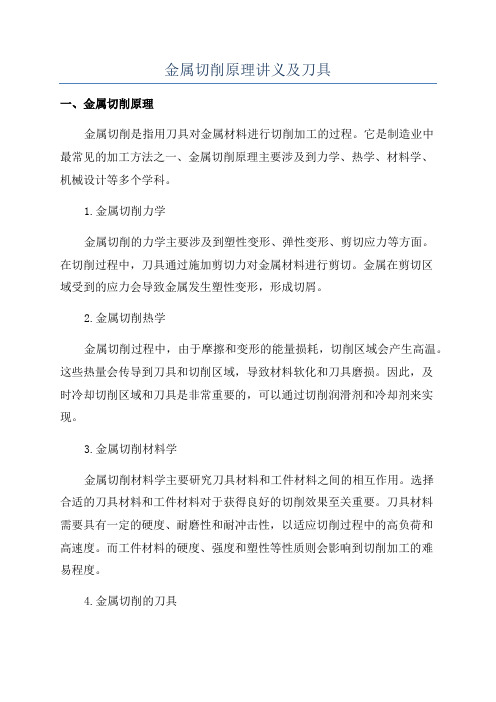
金属切削原理讲义及刀具一、金属切削原理金属切削是指用刀具对金属材料进行切削加工的过程。
它是制造业中最常见的加工方法之一、金属切削原理主要涉及到力学、热学、材料学、机械设计等多个学科。
1.金属切削力学金属切削的力学主要涉及到塑性变形、弹性变形、剪切应力等方面。
在切削过程中,刀具通过施加剪切力对金属材料进行剪切。
金属在剪切区域受到的应力会导致金属发生塑性变形,形成切屑。
2.金属切削热学金属切削过程中,由于摩擦和变形的能量损耗,切削区域会产生高温。
这些热量会传导到刀具和切削区域,导致材料软化和刀具磨损。
因此,及时冷却切削区域和刀具是非常重要的,可以通过切削润滑剂和冷却剂来实现。
3.金属切削材料学金属切削材料学主要研究刀具材料和工件材料之间的相互作用。
选择合适的刀具材料和工件材料对于获得良好的切削效果至关重要。
刀具材料需要具有一定的硬度、耐磨性和耐冲击性,以适应切削过程中的高负荷和高速度。
而工件材料的硬度、强度和塑性等性质则会影响到切削加工的难易程度。
4.金属切削的刀具刀具是金属切削过程中的重要工具,它直接与工件接触,对工件进行加工。
不同的切削操作需要使用不同类型的刀具。
常见的金属切削刀具包括刀片、铣刀、车刀和钻头等。
-刀片:刀片是金属切削中最为常用的刀具,它可用于车削、铣削、镗削等工艺。
刀片一般由高速钢制成,也有使用硬质合金和陶瓷材料制造的高级刀片。
-铣刀:铣刀是一种用于铣削操作的刀具。
它主要用于在工件上形成平面、槽口和曲面等形状。
-车刀:车刀是用于车削加工的刀具,它通过旋转刀具将工件上的旋转刀具切削掉。
-钻头:钻头是用于钻孔加工的刀具,它通过旋转切削力将工件上的孔切削掉。
以上只是金属切削原理及刀具的简要介绍,金属切削涉及的知识和技术极为广泛和复杂,需要深入学习和实践才能掌握。
通过不断的学习和实践,我们可以了解金属切削的原理和技术,并且选择合适的刀具进行加工,提高加工效率和质量。
2.王明玉,杨炯.金属材料切削原理与刀具[M].湖南大学出版社,2024.。
金属切削原理

金属切削原理金属切削是一种常见的金属加工方法,广泛应用于机械制造、航空航天、汽车制造等领域。
金属切削的原理是利用刀具对金属材料进行切削,从而得到所需形状和尺寸的工件。
在金属切削过程中,刀具与工件之间发生相对运动,刀具对工件进行切削,将金属屑削除,最终得到所需的工件形状。
金属切削的原理包括刀具、工件和切削速度等因素。
首先,刀具是金属切削的主要工具,其质量和形状对切削质量有着重要影响。
刀具的材料应选择硬度高、耐磨性好的材料,以保证刀具在切削过程中不易磨损。
此外,刀具的刃部形状和刃口角度也会影响切削力和切削质量。
其次,工件的材料和形状也会对切削过程产生影响。
不同材料的硬度、塑性等性质会影响切削时的刀具选择、切削力和切削质量。
另外,工件的形状和尺寸对切削过程中的切削力、切削稳定性等也有影响。
最后,切削速度是影响切削质量的重要因素之一。
切削速度的选择应考虑刀具材料、工件材料、切削方式等因素,以保证切削过程中的切削质量和刀具寿命。
在金属切削过程中,切削力是一个重要的参数。
切削力的大小和方向直接影响刀具的切削质量和刀具寿命。
切削力的大小受到切削速度、切削深度、切削宽度等因素的影响。
切削力的大小和方向可以通过切削力模型和实验测试来确定,以指导切削过程中的刀具选择、切削参数的确定等。
此外,切削温度也是金属切削过程中需要重点关注的问题。
切削过程中,刀具和工件之间的摩擦和变形会产生热量,导致切削区温度升高。
高温会影响刀具的硬度和耐磨性,同时也会影响工件的表面质量。
因此,控制切削温度是保证切削质量的重要手段之一。
总的来说,金属切削原理涉及到刀具、工件、切削速度、切削力、切削温度等多个方面的内容。
了解金属切削的原理,有助于合理选择刀具、确定切削参数,保证切削质量,提高加工效率。
同时,金属切削原理也为金属加工技术的发展提供了理论基础,推动了金属加工技术的不断进步。
金属切削原理课后习题答案

金属切削原理课后习题答案【篇一:金属切削原理与刀具(第四版)习题册答案】 class=txt>中国劳动社会保障出版社目录第一章金属切削加工的基本知识 (1)第一节切削运动 (1)第二节切削要素 (1)第二章金属切削刀具的基本知识 (3)第一节刀具材料 (3)第二节切削刀具的分类及结构 (4)第三节刀具的几何角度 (4)第四节刀具的工作角度 (6)第三章切削加工的主要规律 (7)第一节切削变形 (7)第二节切屑的类型与控制 (7)第三节积屑瘤 ....................................................................................................... .. 9第四节切削力与切削功率 (10)第五节切削热和切削温度 (12)第六节刀具磨损与刀具耐用度 (12)第四章切削加工质量与效率 (14)第一节工件材料的切削加工性 (14)第二节已加工表面质量 (14)第三节切削用量的选择 (15)第四节切削液 (16)第五章车刀........................................................................................................ (18)第一节焊接式车刀 (18)第二节可转位车刀 (18)第三节成形车刀 (20)第六章孔加工刀具 (21)第一节麻花钻 (21)第二节深孔钻 (22)第三节铰刀 ....................................................................................................... . (23)第四节镗刀 ....................................................................................................... . (24)第五节其他孔加工刀具 (24)第七章铣刀........................................................................................................ (26)第一节铣刀的种类及用途 (26)第二节铣刀的几何参数及铣削要素 (27)第三节铣削方式 (28)第八章拉刀........................................................................................................ (30)第一节拉刀的种类 (30)第二节拉刀的结构组成及主要参数 (30)第三节拉削方式 (31)第四节拉刀的使用与刃磨 (32)第九章螺纹刀具 (34)第一节螺纹车刀 (34)第二节丝锥和板牙 (35)第三节螺纹铣刀 (35)第四节塑性变形法加工螺纹 (35)第十章齿轮加工刀具 (37)第一节齿轮刀具的种类 (37)第二节齿轮滚刀 (37)第三节蜗轮滚刀 (38)第四节插齿刀 (39)第五节剃齿刀 (40)第十一章数控机床用刀具 (41)第一节数控车床用刀具 (41)第二节数控铣床用刀具 (42)第三节数控加工中心用刀具 (43)第一章金属切削加工的基本知识第一节切削运动一、填空题1.刀具、工件、主、进给2.待加工、已加工、过渡二、判断题三、选择题*1.b *2.c 3.a *4.a *5.a *6.b *7.a四、简答题写出下表中各种切削加工方法具备的主运动。
金属切削原理(基本理论)
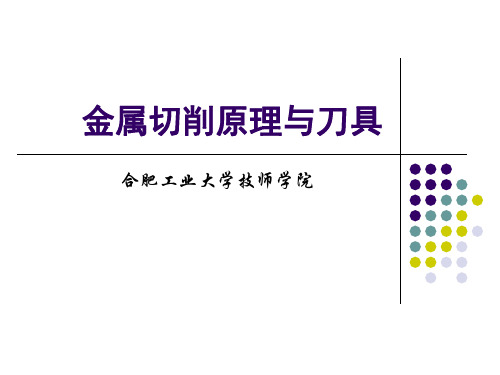
减小切屑与刀具前刀面的摩擦,并能降低切削温度,所以不易
产生积屑瘤。
积屑瘤对切削过程的影响
1. 影响刀具耐用度:
积屑瘤包围着切削刃,同时覆盖着一部分前刀面。积屑
瘤相对稳定时,可代替切削刃进行切削。切削刃和前刀面
都得到积屑瘤的保护,减少了刀具的磨损,提高刀具耐用
如铜、20钢、40Cr钢、1Crl8Ni9Ti等,随着工件材料的强
度和硬度的依次增大,摩擦系数μ略有减小;
这是由于在切削速度不变的情况下,材料的硬度、强度
大时,切削温度增高,故摩擦系数下降。
切削厚度ac增加时, μ也略为下降;如20钢的ac从0.
lmm增大到0. 18mm, μ从0 .74降至0 .72。因为ac增加
最后长成积屑瘤。
影响积屑瘤产生的因素:
①工件材料的影响:塑性高的材料,由于切削时塑性
变形较大,加工硬化趋势较强,积屑瘤容易形成;而
脆性材料一般没有塑性变形,并且切屑不在前刀面流
过,因此无积屑瘤产生。
②切削速度主要通过切削温度影响积屑瘤。
低速(Vc<3~5m/min)时,切削温度较低(低于
300℃),切屑流动速度较慢,摩擦力未超过切屑分子的结
工件母体分离,一部分变成切屑,很小一部分留在已加
工表面上。
第Ⅰ变形区
近切削刃处切削层内产生的塑性变形区——剪切滑移变形;
第Ⅱ变形区
与前刀面接触的切屑底层内产生的变形区——挤压变形;
第Ⅲ变形区
近切削刃处已加工表层内产生的变形区——已加工表面变形。
三) 第一变形区内金属的剪切变形
追踪切削层上任一点P,可以观察切屑的变形和形
系数ξ可直观反映切屑的变形程度,并且容易测量。
金属切削原理与刀具练习题111

金属切削原理与刀具练习题第一章刀具的基本定义切削运动和切削用量一、填空1.将工件上的被切削层转化成切屑所需要的运动是。
2.切削加工时与的相对运动称为切削运动。
3.切削运动分为和两类。
4.工件在切削过程中形成三个不断变化着的表面,即:表面、表面和表面。
5.切削用量是衡量和大小的参数,包括、三个要素。
6.金属切屑层的参数有、及。
7.车削外圆时,当主、副切削刃为直线,刃倾角为零度,主偏角小于90°时,切削层横截面为形。
8.当刃倾角为0°,主偏角为90°,切削深度为5mm,进给量为0.4mm/r时,切削宽度是mm,切削厚度是mm,切削面积是mm²。
二、判断1.使新的切削层不断投入切削的运动称为主运动。
()2.切削用量就是用来表征切削运动大小的参数,是金属切削加工之前操作者调整机床的依据。
()3.无论哪种切削加工,主运动往往不止一个。
()4.工件的旋转速度就是切削速度。
()5.工件每转一分钟,车刀沿着进给方向运动的距离称为进给量。
()6.由于在切削刃上各点相对于工件的旋转半径不同,所以切削刃上各点的切削速度也不同。
()7.主运动的特征是速度高,消耗的功率大。
()8.进给运动的速度较低,消耗功率小,可以是一个、两个或多个。
()9.进给量是衡量进给运动大小的参数。
()10.车削时工件的旋转运动是主运动;刨削时刨刀的往复直线运动是主运动。
()11.切削面积由切削深度和进给量决定。
()12.切屑层的参数通常在平行于主运动方向的基面内测量。
()三、选择1.在各种切削加工中,()只有一个。
A、切削运动B、主运动C、进给运动2.主切削刃正在切削着的表面称为()表面。
A、已加工B、待加工C、过渡3.车削加工的切削运动形式属于()A、工件转动,刀具移动B、工件转动,刀具往复运动C、工件不动,刀具作回转运动4.()的大小直接影响刀具主切削刃的工作长度,反映其切削负荷的大小。
A、切削深度B、进给量C、切削速度5.切削厚度与切削宽度随刀具()大小的变化而变化。
金属切削的基本原理

金属切削的基本原理金属切削的基本原理1. 引言金属切削作为一种重要的制造工艺,在现代工业中得到广泛应用。
了解金属切削的基本原理对于提高生产效率和产品质量至关重要。
本文将深入探讨金属切削的原理和相关概念。
2. 金属切削的定义和概述金属切削是指通过工具在金属材料上切削形成所需形状的制造过程。
这种切削通过将刀具与金属工件相对移动来去除材料,从而实现目标形状。
金属切削常用于车削、铣削、钻削等加工过程中。
3. 切削过程的基本元素金属切削包括以下基本元素:3.1 切削工具切削过程中使用的工具通常由坚固的材料制成,如高速钢、硬质合金等。
切削工具的类型和几何形状根据切削操作的需求而变化,比如刀片、铣刀、钻头等。
3.2 金属工件金属工件是经过切削加工的目标。
它可以是圆柱形、平面形或复杂形状的。
不同材料的切削特性也会影响切削过程的选择和参数设定。
3.3 切削速度切削速度是指工具切削过程中与工件接触部分的相对速度。
合适的切削速度可以提高加工效率和工件表面质量,但过高的切削速度可能导致工具磨损和加工表面粗糙度增加。
3.4 进给速度进给速度是指工具与工件相对运动的速度。
适当的进给速度可以控制切削过程中材料的去除率,同时避免过度磨损和切削力过大。
3.5 切削深度切削深度是指工具进入工件的深度,即每次切削过程中所移除的金属厚度。
切削深度的选择应根据工件的要求、切削力和工具稳定性等因素考虑。
4. 金属切削的力学原理金属切削的力学原理主要涉及三个力:切削力、切向力和主动力。
4.1 切削力切削力是指在金属切削过程中作用在切削工具上的力。
它由切削材料的去除、摩擦和变形引起。
切削力的大小和方向取决于切削工艺参数、切削材料和刀具等。
4.2 切向力切向力是指垂直于切削方向的力。
它使工件保持在切削位置,并防止工件偏离切削方向。
切向力的大小和方向直接影响切削的稳定性和表面质量。
4.3 主动力主动力是指在金属切削过程中将工具向工件施加的力。
它与切削深度和切削速度等直接相关。