铝合金阳极氧化与表面处理技术
铝合金阳极氧化与表面处理技术

铝合金阳极氧化与表面处理技术铝合金阳极氧化作为表面处理技术,可以极大地改善材料的物理和化学性能,提高其耐腐蚀性、抗冲击性和耐磨性等性能,是现代工业技术中一个重要的处理过程。
本文重点介绍了铝合金阳极氧化及其表面处理技术,并讨论了阳极氧化的实验与制备及其应用在工业上的相关研究。
铝合金阳极氧化是一种通过电化学方法在铝合金表面形成氧化膜的表面处理技术。
它将铝合金物理结构改变为氧化物,形成多层致密氧化膜,具有良好的耐腐蚀性、抗冲击性和耐磨性等性能。
铝合金阳极氧化主要是采用化学阳极技术,通过给铝合金涂覆特定种类的化学药剂来形成氧化膜的表面处理技术。
阳极氧化技术中的化学药剂包括氯离子、碳酸钠、氢氟酸,可以分别发挥不同的作用。
在铝合金阳极氧化实验中,首先需要对材料表面进行清洁,以确保表面可以以最佳效果氧化。
擦洗是铝合金阳极氧化前必须完成的一个关键环节,其目的是去除污垢、油污等,这样可以确保氧化过程中表面不被受到有害影响。
接下来,铝合金要经过酸浸或电解清洗,以充分去除表面的腐蚀物,然后才能进行阳极氧化。
擦洗后的表面必须完全干燥,铝合金放入阳极氧化槽中,溶液温度一般维持在比常温稍高一些的温度,在无氧、无腐蚀性气体的情况下,通过专门的电解装置将电流从阳极传入到铝合金的表面。
氧化过程中,也会加入一定量的药液,以增加氧化膜的硬度、厚度和耐腐蚀性等性能。
氧化完成后,铝合金表面的氧化膜具有不同的硬度、耐磨性和耐腐蚀性等特性,可以满足一定的应用要求。
此外,需要注意,氧化过程本身也可能会对铝合金的机械性能、力学性能和结构稳定性产生影响,因此,在进行阳极氧化前,需要对这些性能进行充分研究。
本文简要介绍了铝合金阳极氧化与表面处理技术,从处理过程、实验及制备方面讨论了氧化技术的研究和应用。
可以看出,铝合金阳极氧化是一种提升铝合金性能的重要技术,将在未来受到越来越多的关注和应用。
铝合金阳极氧化与表面处理技术

本章主要介绍了铝的表面处理技术在各个领域的应用,包括航空航天、汽车、 建筑、电子、家具等。通过实例说明了铝的表面处理技术在实际应用中的效果和 价值。
本章概述了铝的表面处理技术的现状和发展趋势,指出了目前存在的问题和 未来的发展方向。同时,也介绍了铝的表面处理技术在环保和可持续发展方面的 应用前景。
阳极氧化是一种通过外加电流使铝合金表面氧化形成一层致密氧化膜的过程。 该氧化膜具有高硬度、高耐腐蚀性等特点,可以有效提高铝合金的抗腐蚀性能和 耐磨性。在阳极氧化过程中,铝合金表面的氧化膜不断增厚,直至达到所需的厚 度。
表面预处理:去除铝合金表面的油污、锈迹等杂质,以提高氧化膜的附着力。 通电氧化:将铝合金置于电解液中,通过外加电流使表面发生氧,铝合金作为一种重要的金属材料,广泛应用于航空、建 筑、汽车、电子等领域。为了提高铝合金的耐腐蚀性、美观性和功能性,表面处 理技术显得尤为重要。在众多表面处理技术中,阳极氧化是一种常用的方法,可 以有效提高铝合金的抗腐蚀性能和表面硬度。本书将介绍《铝合金阳极氧化与表 面处理技术》这本书中的精彩摘录,帮助读者更好地了解铝合金阳极氧化的原理、 工艺和实际应用。
铝合金表面处理技术:本书不仅介绍了传统的表面处理技术,如涂装、电镀、化学镀等,还介绍 了许多先进的表面处理技术,如离子注入、纳米涂层、物理气相沉积等。这些技术为铝合金的表 面防护和装饰提供了多种解决方案。
铝合金阳极氧化和表面处理的工业应用:本书详细介绍了铝合金阳极氧化和表面处理技术在各个 领域的应用,包括航空航天、汽车制造、电子工业、建筑装饰等。这些实例为读者提供了实际操 作中的指导。
阅读感受
在我阅读《铝合金阳极氧化与表面处理技术》这本书的过程中,我深深地被 书中所涵盖的专业知识和深度所吸引。作为一本由化学工业社的专业书籍,这本 书无疑为我在理解和掌握铝合金阳极氧化与表面处理技术方面提供了宝贵的帮助。
铝合金阳极氧化及其表面处理

铝合金阳极氧化及其表面处理铝合金阳极氧化是铝合金材料常用的一种表面处理方法,它主要是通过利用阳极电位差,使氧原子和钙原子氧化成氧化物薄膜形成在铝合金表面,从而提供铝合金表面的耐腐蚀性能和外观美观度,使表面更具有耐磨性和防气孔能力。
当铝合金表面处理需要抗腐蚀、耐磨、抗气孔等性能时,阳极氧化可以满足要求。
铝合金阳极氧化的原理是利用分子氧的氧化还原反应,利用阳极电位差,氧原子和钙原子氧化成薄膜,形成在铝合金表面,起到保护作用。
所形成的氧化膜是稳定的,具有很强的抗腐蚀性和抗气孔性。
同时,铝合金阳极氧化的过程中,可以调整氧化膜厚度,改善表面光洁度和粗糙度,以满足表面性能要求。
铝合金阳极氧化工艺有多种,其中包括化学阳极氧化法、静电阳极氧化法和磁控溅射阳极氧化法等。
化学阳极氧化法是一种常用的阳极氧化处理方法,该方法主要是利用氧化剂和反应物的反应,使反应物在反应过程中形成自身的氧化膜,从而达到改善铝合金表面性能的目的。
但由于此方法操作过程复杂,需要在反应过程中控制反应条件,因此很少有工厂采用这种方法。
静电阳极氧化法是一种常用的处理技术,使用此方法可以在铝合金表面形成厚度比化学阳极氧化法薄的氧化膜,具有较高的耐磨性。
此外,由于反应速率相对较快,因此可以使用更低的温度来达到相同的效果。
磁控溅射阳极氧化法属于活性氧化方法,它是利用高速离子将氧化剂撞击在铝合金表面,氧化剂受到撞击时会被迅速氧化,从而形成一种厚度较薄的氧化膜,膜具有良好的抗冲击性和耐磨性,而且可以在普通条件下实现镀锌层效果,也可以改善表面摩擦性能。
除了铝合金阳极氧化之外,表面处理还可以采用其他技术,如络石抛光、热处理、激光处理、化学镀层和电镀等。
络石抛光,主要是利用磨削作用,在金属表面形成一定厚度的高光洁层,从而使金属表面更加平滑,并具有耐水性、耐酸碱性和耐腐蚀性。
热处理,是在一定温度、时间条件下,将金属表面热处理后,可以改变金属表面的光洁度、粗糙度和耐磨性,提高金属表面的耐腐蚀性和强度。
铝合金阳极氧化、电泳与喷涂的优缺点
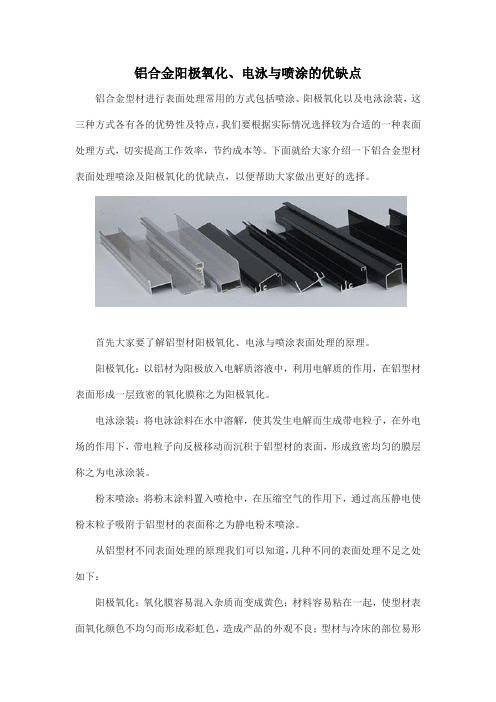
铝合金阳极氧化、电泳与喷涂的优缺点铝合金型材进行表面处理常用的方式包括喷涂、阳极氧化以及电泳涂装,这三种方式各有各的优势性及特点,我们要根据实际情况选择较为合适的一种表面处理方式,切实提高工作效率,节约成本等。
下面就给大家介绍一下铝合金型材表面处理喷涂及阳极氧化的优缺点,以便帮助大家做出更好的选择。
首先大家要了解铝型材阳极氧化、电泳与喷涂表面处理的原理。
阳极氧化:以铝材为阳极放入电解质溶液中,利用电解质的作用,在铝型材表面形成一层致密的氧化膜称之为阳极氧化。
电泳涂装:将电泳涂料在水中溶解,使其发生电解而生成带电粒子,在外电场的作用下,带电粒子向反极移动而沉积于铝型材的表面,形成致密均匀的膜层称之为电泳涂装。
粉末喷涂:将粉末涂料置入喷枪中,在压缩空气的作用下,通过高压静电使粉末粒子吸附于铝型材的表面称之为静电粉末喷涂。
从铝型材不同表面处理的原理我们可以知道,几种不同的表面处理不足之处如下:阳极氧化:氧化膜容易混入杂质而变成黄色;材料容易粘在一起,使型材表面氧化颜色不均匀而形成彩虹色,造成产品的外观不良;型材与冷床的部位易形成黑色或白色的斑点;电解液的温度过高或电解时间过长引起铝型材表面起白色不透明的粉状物;在氧化的过程中,如果型材掉下来,容易造成短路;在碱蚀时如果硫酸的浓度掌控不好,会使型材表面的耐腐蚀性降低;氧化膜表面还易形成烧伤、发白、发黑或呈暗色状等各种外观质量问题。
电泳涂装:在电泳涂装时如果不严格按照各个工艺流程的要求来操作,如烘烤时间过长、槽液受到污染、槽液的成分不合格等等,都会造成铝型材表面粗糙、起泡、针孔或缩孔、漆斑流痕、光泽度不高、型材表面漆膜不均匀、产生裂纹等各种表面缺陷。
粉末喷涂:如果原材料质量不好,有灰尘或杂质等混入,会在型材表面产生颗粒;压缩空气不洁净,混入了油污或水也会造成铝型材表面缩孔缺陷;原材料的配方中如果搭配不合理,会影响铝型材产品的硬度、耐冲击性、抗弯曲性等物理性能和耐化学性能;还会造成型材表面不上粉、颜色泛黄等外观不良。
铝合金表面处理
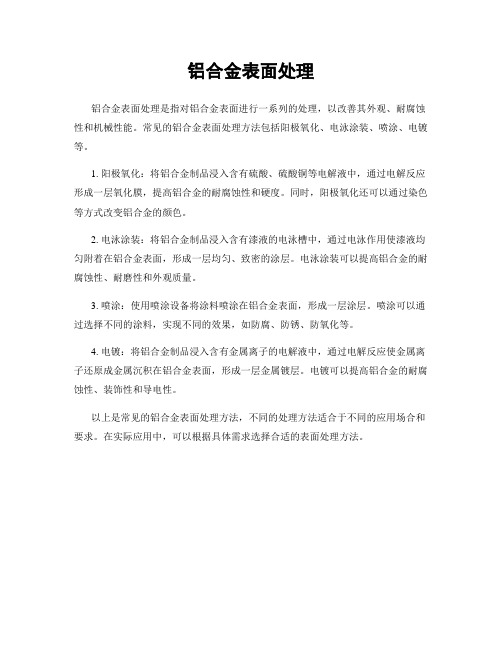
铝合金表面处理
铝合金表面处理是指对铝合金表面进行一系列的处理,以改善其外观、耐腐蚀性和机械性能。
常见的铝合金表面处理方法包括阳极氧化、电泳涂装、喷涂、电镀等。
1. 阳极氧化:将铝合金制品浸入含有硫酸、硫酸铜等电解液中,通过电解反应形成一层氧化膜,提高铝合金的耐腐蚀性和硬度。
同时,阳极氧化还可以通过染色等方式改变铝合金的颜色。
2. 电泳涂装:将铝合金制品浸入含有漆液的电泳槽中,通过电泳作用使漆液均匀附着在铝合金表面,形成一层均匀、致密的涂层。
电泳涂装可以提高铝合金的耐腐蚀性、耐磨性和外观质量。
3. 喷涂:使用喷涂设备将涂料喷涂在铝合金表面,形成一层涂层。
喷涂可以通过选择不同的涂料,实现不同的效果,如防腐、防锈、防氧化等。
4. 电镀:将铝合金制品浸入含有金属离子的电解液中,通过电解反应使金属离子还原成金属沉积在铝合金表面,形成一层金属镀层。
电镀可以提高铝合金的耐腐蚀性、装饰性和导电性。
以上是常见的铝合金表面处理方法,不同的处理方法适合于不同的应用场合和要求。
在实际应用中,可以根据具体需求选择合适的表面处理方法。
铝合金表面阳极氧化处理

铝合金表面阳极氧化处理铝合金表面阳极氧化处理是一种常见的表面处理技术,也被称为电化学氧化或阳极处理。
它是通过在铝合金表面形成一层氧化膜来改善其耐腐蚀性、硬度和耐磨性。
这种氧化膜通常具有良好的耐热性、耐磨性、绝缘性和美观性,因此广泛应用于航空、汽车、建筑、电子等行业。
铝合金表面阳极氧化处理的过程是将铝合金制品作为阳极,置于电解质溶液中,通电时在表面形成一层氧化膜。
电解质溶液通常是含有硫酸、草酸、硫酸铬等成分的溶液。
在电解质溶液中通电时,阳极表面的铝原子会与氧离子结合形成氧化物,这些氧化物会在阳极表面形成一层致密的氧化膜。
这种氧化膜的厚度、硬度和颜色等特性可以通过调整电解质溶液的成分、温度、电流密度等参数来控制。
铝合金表面阳极氧化处理的优点包括:1.提高耐腐蚀性:通过形成致密的氧化膜,可以有效地提高铝合金的耐腐蚀性,使其在恶劣环境下更加耐用。
2.提高硬度和耐磨性:氧化膜的硬度可以达到200-500HV,比铝合金本身的硬度高出数倍,因此可以有效地提高铝合金的耐磨性和耐划伤性。
3.美观性好:氧化膜的颜色可以根据需要进行调整,可以制成金色、银色、黑色、蓝色等不同颜色的氧化膜,从而提高铝合金制品的美观性。
4.绝缘性好:氧化膜具有良好的绝缘性能,可以用于制作电子器件、电解电容器等。
铝合金表面阳极氧化处理的缺点包括:1.成本较高:阳极氧化处理需要专门的设备和工艺,成本较高。
2.氧化膜厚度不易控制:氧化膜的厚度受到多种因素的影响,不易精确控制,可能会导致产品质量不稳定。
3.容易受到机械损伤:氧化膜的硬度虽然很高,但容易受到机械损伤,因此需要注意保护。
总的来说,铝合金表面阳极氧化处理是一种有效的表面处理技术,可以提高铝合金制品的耐腐蚀性、硬度和美观性,广泛应用于航空、汽车、建筑、电子等行业。
表面处理培训资料(铝合金)

表面处理培训资料第一篇:铝合金阳极氧化与表面处理技术第1章:引论铝合金阳极氧化目的:提高工件的表面硬度、及耐磨、耐腐蚀等性能,绝缘性能好,可以着色能显著改变和提高铝合金的外观和使用性能。
铝合金通过化学预处理,还可以进行电镀、电泳、喷涂等,赋予铝合金表面以金属镀层或有机聚合物涂层,进一步提高铝合金的装饰和保护效果。
1.2 铝合金表面处理技术铝合金表面处理技术有:表面机械预处理(机械抛光或扫纹等)、化学预处理或化学处理(化学转化或化学镀)。
电化学处理(阳极氧化或电镀等)、物理处理(喷涂、搪瓷珐琅化及其他物理表面改性技术)等。
现举例:通用工业用铝合金部件(机械部件、电器部件等)阳极氧化处理流程:脱脂碱洗出光封孔硬质阳极氧化法1.3 铝合金与阳极氧化不同成分的铝合金分别适合于不同目的的阳极氧化,比如铝-铜合金的阳极氧化性能(尤其是光亮阳极氧第2章铝的表面机械处理铝及其合金制品的外观和适用性在很大程度上取决于精饰前的表面预处理,机械处理是表面预处理的主要方法之一。
机械处理一般分为:抛光(磨光、抛光、精抛或者镜面抛光),喷砂(丸)、刷光、滚光等方法机械处理的目的:1)提供良好的表观条件,提高表面精饰质量2)提高产品品级3)减少焊接的影响4)产生装饰效果5)获得干净表面目前我公司采用的机械处理方式是:喷砂及拉丝喷砂的规格常采用80#或100#砂,部分采用320#砂拉丝的规格常采用150#或180#第3章化学抛光和电化学抛光光亮阳极氧化只有采用特殊的化学抛光和电化学抛光处理,才能保证在阳极氧化后有高镜面的表面质量常用的化学抛光工艺:磷酸—硫酸—硝酸常用的电化学抛光工艺:硫酸—铬酸、磷酸—硫酸—铬酸以及碳酸钠—磷酸三钠等第4章化学清洗和浸蚀化学清洗的目的:因为铝材在生产过程中使用润滑剂、轧制油,在机械抛光中使用抛光膏,在半成品存在中使用防锈油等必要的油脂;此外,铝材在操作过程中及转运过程中稍不注意,很可能黏附到不必要的机械设备的润滑、灰尘、杂质颗粒之污染物,严重的会形成污垢。
6061铝合金阳极氧化及其表面处理

6061铝合金阳极氧化及其表面处理6061铝合金是一种常见的铝合金材料,具有较高的强度和耐腐蚀性能。
为了进一步提升其表面性能,可以采用阳极氧化和其他表面处理方法。
阳极氧化是一种通过在铝合金表面形成氧化膜来改善其性能的方法。
该方法通常使用硫酸、草酸等强酸作为电解液,铝合金作为阳极,在一定的电流和温度条件下进行电解处理。
在电解过程中,阳极氧化会在铝合金表面形成一层致密的氧化膜,这层氧化膜具有较好的耐腐蚀性、硬度和附着力。
6061铝合金阳极氧化后的表面处理主要包括氧化膜封闭、染色和后处理等步骤。
氧化膜封闭是为了提高氧化膜的耐腐蚀性和耐磨性,常用的方法有热封闭和冷封闭两种。
热封闭是将阳极氧化后的铝合金制品放入高温炉中加热,使得氧化膜中的孔隙部分重新氧化,从而封闭孔隙,提高氧化膜的致密性。
冷封闭则是通过浸渍含有封闭剂的溶液,使封闭剂渗入氧化膜孔隙中,达到封闭孔隙的目的。
染色是为了改变铝合金表面的颜色,增加其装饰性和美观性。
染色一般在氧化膜封闭后进行,常用的染色方法有有机染料染色和无机染料染色两种。
有机染料染色是将铝合金制品浸泡在含有有机染料的溶液中,使染料渗入氧化膜孔隙中,使表面呈现出不同的颜色。
无机染料染色则是将铝合金制品浸泡在含有无机染料的溶液中,在一定的温度和时间条件下进行染色,形成一层致密的无机染料膜。
在阳极氧化和染色后,还可以进行一些后处理工艺,如密封处理和涂层处理。
密封处理是为了提高氧化膜的耐腐蚀性和耐磨性,常用的方法有热水密封和冷水密封两种。
热水密封是将经过阳极氧化和染色处理的铝合金制品放入热水中进行密封,使得氧化膜中的孔隙部分重新氧化,从而提高氧化膜的致密性。
冷水密封则是将经过阳极氧化和染色处理的铝合金制品放入冷水中进行密封,通过水的渗入填充氧化膜孔隙,达到密封的效果。
涂层处理是为了进一步提高铝合金制品的耐腐蚀性和耐磨性,常用的涂层材料有聚合物涂层和无机涂层两种。
聚合物涂层是将铝合金制品浸泡在含有聚合物涂层材料的溶液中,使涂层材料渗入氧化膜孔隙中,形成一层致密的聚合物涂层。
- 1、下载文档前请自行甄别文档内容的完整性,平台不提供额外的编辑、内容补充、找答案等附加服务。
- 2、"仅部分预览"的文档,不可在线预览部分如存在完整性等问题,可反馈申请退款(可完整预览的文档不适用该条件!)。
- 3、如文档侵犯您的权益,请联系客服反馈,我们会尽快为您处理(人工客服工作时间:9:00-18:30)。
铝合极氧化与表面处理技术第一章引论1.铝及铝合金的性能特点密度低;塑性好;易强化;导电好;耐腐蚀;易回收;可焊接;易表面处理2.简述铝合金的腐蚀性及其腐蚀形态1)腐蚀性:(1)酸性腐蚀:铝在不同的酸中有不同腐蚀行为,一般在氧化性浓酸中生成钝化膜,具有很好的耐蚀性,而在稀酸中有“点腐蚀”现象。
局部腐蚀;(2)碱性腐蚀:铝在碱性溶液中的腐蚀,碱能与氧化铝反应生成偏铝酸钠和水,然后再进一步与铝反应生成偏铝酸钠和氢气。
全面腐蚀;(3)中性腐蚀:在中性盐溶液中,铝可以是钝态,也可能由于某些阳离子或者阳离子的作用发生腐蚀。
点腐蚀。
2)腐蚀形态:点腐蚀,电偶腐蚀,缝隙腐蚀,晶间腐蚀,丝状腐蚀和层状腐蚀等点腐蚀:最常见的腐蚀形态,程度与介质和合金有关电偶腐蚀:接触腐蚀,异(双)金属腐蚀,在电解质溶液中,当两种金属或合金相接触(电导通)时,电位较负的金属腐蚀被加速,而电位较正的金属受到保护的腐蚀现象。
缝隙腐蚀:两个表面接触存在缝隙,该处充气溶解氧形成氧浓差原电池,使缝隙产生腐蚀。
晶间腐蚀:与热处理不当有关,合金元素或金属间化合物沿晶界沉淀析出,相对于晶粒是阳极,而构成腐蚀电池。
丝状腐蚀:丝状腐蚀是一种膜下腐蚀,呈蠕虫状在膜下发展,这种膜可以是漆膜,或者其他涂层,一般不发生在阳极氧化膜的下面。
丝状腐蚀与合金成分、涂层前预处理和环境因素有关,环境因素有适度、温度、氯化物;层状腐蚀:剥层腐蚀,也叫剥蚀。
3.铝合金表面处理技术包括哪几个方面?表面机械预处理(机械抛光或扫纹等)(2)化学预处理或化学处理(化学转化或化学镀等)(3)电化学处理(阳极氧化或电镀等)(4)物理处理(喷涂、搪瓷珐琅化及其物理表面技术改性)等。
搪瓷珐琅:将无机物的混合物熔融成不同熔点玻璃态物质。
4.铝合极氧化膜的特性有哪些?有:耐蚀性;硬度和耐磨性;装饰性;有机涂层和电镀层附着性;电绝缘性;透明性;功能性第二章铝的表面机械预处理1.预处理的目的:(1)提高良好的表观条件和表面精饰质量。
(2)提高产品品级。
(3)减少焊接的影响。
(4)产生装饰效果。
(5)获得干净表面。
2.磨光操作要求(1)磨料种类和粒度的选择:根据工件材料的软硬程度、表面状况和质量要求等选用;表面越硬或越粗糙则用较硬及较粗的磨料。
(2)磨光应分多步操作,工件压向磨轮的压力要适度。
(3)新磨轮在黏结磨料前应预先刮削使之平衡后才能粘结磨料。
(4)定期更换新磨料。
(5)根据不同的需要选择合金材料。
(6)选择适当的磨轮转速,一般控制在10~14m/s。
(7)磨光效果取决于磨料、磨轮的刚性和轮子的旋转速度、工件与磨轮的接触压力等因素,以及实践经验和熟练技巧等。
3.磨光和抛光的概念磨光:将布轮黏结磨料后的操作。
目的:去除工件表面的毛刺、划痕、腐蚀斑点、砂眼、气孔等表观缺陷。
;抛光:将抛光膏抹于软布轮或毡轮后的操作4.常见的问题和解决办法:常见问题:“烧焦”印。
原因:(1)磨光轮、磨料和抛光剂的选择不当;(2)抛光用力不当;(3)磨触时间过长;(4)磨触过热。
措施:(1)在稀碱溶液中进行轻微的碱蚀;(2)用温和的酸浸蚀:如铬酸-硫酸溶液,或者质量分数为10%的硫酸溶液加温后使用;(3)3wt%Na2CO3和2wt%Na3PO4,溶液在40~50℃温度下处理,时间为5min,严重的可延长至10~15min经上述处理清洗并干燥后,应立即用精抛轮或镜面抛光轮重新抛光。
预防:采用适当的磨光轮、抛光轮;采用适当的抛光剂;工件与抛轮的磨触时间要适当掌握。
第三章铝的化学预处理1.铝材的脱脂方法有哪些?工艺原理分别是什么?1)脱脂方法:酸性脱脂、碱性脱脂和有机溶剂脱脂。
目的:清除铝表面的油脂和灰尘等污染物,使后道碱洗比较均匀,提高阳极氧化膜的质量2)(1)酸性脱脂的作用机理:在以H2SO4、H3PO4和HNO3为基的酸性脱脂溶液中,油脂发生水解反应,生产甘油和相应的高级脂肪酸,达到脱脂的目的。
(2)碱性脱脂的作用机理:碱与油脂发生皂化反应,生成可溶性的肥皂,用皂化反应消除油脂与铝材表面的结合,达到脱脂的目的。
(3)有机溶剂脱脂的作用机理:利用油脂易溶于有机溶剂的特性进行,既能溶解皂化油,也能溶解非皂化油,具有很强的脱脂能力,且速度快,对铝无腐蚀性,达到脱脂的目的。
2.碱洗的目的、存在哪些缺陷?相应的对策应如何?1)目的:去除表面的赃物,彻底去除铝表面的自然氧化膜,显露出纯净的金属基体,为后续的表面处理主工序做好准备。
2)碱洗的三大缺陷:外观粗糙、斑点、流痕。
3)(1)外观粗糙:是碱洗法生产砂面铝材时常见问题,常是由原始铝材存在组织缺陷(粗晶或金属间化合物沉淀粒子大)引起;提高原始铝材的在组织质量才能从源头上解决问题。
原因:A:挤压用的铝棒原始晶粒尺寸大。
B:铝棒加热温度偏高或挤压速度太快。
C:采用的挤压机吨位偏小。
D:挤压后淬火不足。
E:碱洗速度太快。
对策:选用晶粒度复合国家标准的挤压铝棒;控制好挤压制品的出口温度;加强挤压后的淬火;合理控制碱洗速度等。
(2)斑点:是铝材表面处理的致命缺陷:中断后续工序或报废回炉处理。
原因:A:熔炼铸棒时加入回收铝的比例太高。
Al2O3熔点高达2050℃,熔炼时不熔化,仅是破碎;碱洗过程中的浸蚀导致雪花状腐蚀斑点。
对策:控制阳极氧化膜的回收铝的比例,应小于10%;熔体的精炼除渣,铸造前熔体静止约25min和熔体过滤等。
B:水中氯离子含量高。
当铝材的材质品质较差,而所用水的氯离子含量也较高时,碱洗或碱洗前后水洗都会显露出腐蚀斑点。
对策:改善原始铝材的材质;采用复合国家标准的自来水;改用硝酸或硝酸加硫酸除灰;在水槽镍加入1~5g/L HNO3也可有效抑制氯离子的腐蚀影响。
C:大气腐蚀。
铝材在沿海大气环境中放置约3天、腐蚀性气氛熔炼炉旁、阴雨天气等其表面常有腐蚀斑痕或斑点形成。
对策:缩短原始铝材转入阳极氧化的周期时间;带阳极氧化的原始铝材放置在环境干燥、空气良好的位置;对长时间放置或阴雨天,可对原始铝材进行适当的遮盖处理等。
D:挤压“热斑”。
铝材与出料台的导热良好的石墨辊相接触,因局部冷速不同,导致铝材有析出相(Mg2Si相,温度围400~250℃)形成,呈现间隔状斑点。
对策:控制挤压出料台的运行速度(应大于铝的挤出速度);采用导热效果差的其他耐热材料替代石墨辊;借枪风冷淬火力度;快速将挤压出口铝材降至250℃以下。
(3)流痕:碱洗工艺条件和操作不当造成碱洗流痕缺陷(碱洗速度太快和转移速度太慢)。
对策:A:加快转移。
B:降低碱洗槽液温度。
C:降低槽液中的NaOH浓度。
D:铝材装料过密,应适当减少。
3.除灰的目的是什么?铝合金表面除灰有哪几种方法?目的:去除表面挂灰,防止后道阳极氧化槽液的污染,提高氧化膜质量。
方法:硝酸除灰,硫酸除灰,4.氟化物砂面处理的缺陷和对策是什么?氟化物砂面处理是利用氟离子使铝材表面产生高度均匀、高密度点腐蚀的一种酸性浸蚀工艺。
缺陷与对策:(1)上表面有斑痕:槽沉淀物较多、氟离子浓度较低时,反应强度较弱,沉淀物在吕爱表面上沉积或停留过久,阻碍氟离子的正常腐蚀。
对策:清除槽过多的沉淀物、降低铝材密度、添加适量的氟化氢铵和添加剂,提高氟离子浓度,增加反应强度。
(2)表面不易起砂:槽液受前道酸脱脂的污染而使PH降低,氟离子和添加剂浓度不足。
对策:用氨水或氟化铵调节PH值、补加氟化氢铵和添加剂等。
(3)表面沙粒太粗:槽氟离子浓度太高或添加剂不足,或处理时间太长。
对策:采取相应的措施控制。
(4)表面光泽度有差异:槽工艺条件控制不当,或选用添加剂不适当,或铝材存在问题。
对策:采取相应的措施控制。
(5)局部不起砂:局部存在复合氧化膜。
对策:调整工艺流程,如磨光、抛光、重新酸洗或碱洗等。
第四章铝的化学抛光和电化学抛光1.简述化学抛光和电化学抛光的机理的异同点。
1)化学抛光:通过控制铝材表面选择性的溶解,使表面微观凸部比凹部优先溶解,达到表面平整和光亮的目的。
2)电化学抛光,又称电解抛光。
原理与化学抛光相似,依靠选择性溶解表面凸出部分而达到平整光滑,不同的是有外加电流作用,处理时间较短3)共同点:抛光机理相同;不同点:电化学抛光在处理过程中施加了电流,化学抛光使用的是化学氧化剂。
2.化学抛光和电化学抛光具有哪些优点?化学抛光和电化学抛光与机械抛光相比较,具有如下优点:(1)设备简单,工艺参数易调控,节省成本等以及表面更光亮;(2)可处理大型零部件或大批量的小型零部件,以及复杂形状的工件;(3)表面更洁净,无残留的机械抛光粉尘,具有良好的抗腐蚀性;(4)化学抛光的表面镜面反射率更高,金属质感也较好,表面不会形成粉“霜”。
3.简述化学抛光和电化学抛光的缺陷和对策。
1)化学抛光缺陷及对策(以磷酸-硫酸-硝酸工艺为例)(1)光亮度不足:铝材的成分影响、硝酸的含量影响等。
对策:采用高纯铝、控制硝酸的浓度,抛光前的铝材要干燥。
(2)白色附着物:铝溶解过多,需控制其在槽液中的含量。
对策:调整槽液中的溶铝量到正常围。
(3)表面粗糙:硝酸含量过高,反应过于剧烈;或Cu含量过高。
对策:应严格控制硝酸含量;提高材质部质量、减少添加剂量等。
(4)转移性腐蚀:化学抛光后转移到水洗过程中迟缓造成;对策:应迅速转移至水中进行清洗。
(5)点腐蚀:绿箭表面气体累积形成气穴而产生;或因硝酸或Cu含量偏低造成。
对策:应合理装料,增加工件倾斜度,加强搅拌使气体逸出。
清洗表面干净;控制硝酸含量等。
2)电化学抛光缺陷及对策(以磷酸-硫酸-铬酸工艺为例)(1)电灼伤:导电借助面积不足、接触不良、工件通电电压上升过快、电流密度瞬间过大等;对策:注意工件与电夹具接触良好、接触面积满足大电流需要,施加电压升压不宜过快等。
(2)暗斑:电流密度过低、电力线局部分布不均匀等对策:装料量不宜过多、避免电力线分布不到的死角区等。
(3)气体条纹:气体逸出造成对策:装料时使工件的每个面倾斜,装饰面垂直放置且朝向阴极、避免气体聚集等。
(4)冰晶状附着物:槽液中溶铝量太高或者磷酸含量高而形成磷酸铝沉淀。
对策:降低槽液中的溶铝量、或降低磷酸含量等第五章第六章铝阳极氧化与阳极氧化膜1.铝阳极氧化膜分类:(1)壁垒型:也叫屏蔽型或阻挡层氧化膜,紧靠金属表面,致密无孔、薄,厚度取决于氧化电压,不超过0.1μm,主要用于电解电容器。
(2)多孔型:由两层氧化膜组成,底层是阻挡层,与壁垒膜结构相同的致密无孔的薄氧化物层,厚度与电压有关;主体部分是多孔层结构,其厚度取决于通过的电量。
(阻挡层:指多孔型氧化膜的多孔层与金属铝分隔的,具有壁垒膜性质和生成规律的氧化层。
)2.多孔型氧化膜的厚度、结构和成分多孔型阳极氧化膜组成:阻挡层和多孔层;阻挡层的结构和形成规律相当于壁垒型氧化膜;多孔层的生成规律、结构和成分与阻挡层完全不同。