SPC与常规控制图培训课件.pptx
SPC与常规控制图培训课件PPT(共 58张)

2×C54×0.1573054×(0.9973-0.157305) =0.00268
规则7连续15点在中心线正负1σ 之间
0.6826815 =0.00326
常用控制图的种类
常用质量控制图可分为两大类: (1)计量值控制图包括:
均值-标准差控制图,均值-极差控制图, 中位数-极差控制图,单值-移动-极差控制图。 (2)计数值控制图包括:
SPC与常规控制图
——控制图概念
又叫管理图或休图。它是判断和预报生产过程中 质量状况是否发生异常波动的一种有效的方法。
可用3σ原则确定控制图的控制线(Control Lines)
CL=μ UCL=μ+3σ LCL=μ-3σ
控制图的基本原理
控制图是把造成质量波动的六个原因(人机料法 环、测量等)分为两个大类:随机性原因(偶然 性原因)和非随机性原因(系统原因)。这样, 我们就可以通过控制图来有效地判断生产过程质 量的稳定性,及时发现生产过程中的异常现象, 查明生产设备和工艺装备的实际精度,从而为制 定工艺目标和规格界限确立可靠的基础,使得过 程的成本和质量成为可预测的,并能够以较快的 速度和准确性测量出系统误差的影响程度。
3点中2个点子在中心线同一侧的2σ ~ 3σ 范围之内,另外一 个点子落在控制界限任何处,发生这种情况的概率为
2×C32×0.02142×(0.9973-0.0214) =0.00268
控制图上的信号解释
规则6:连续5点中有4点落在中心线同一侧 的1σ 以外。
点子落在1σ ~ 3σ 之间的概率为 ( 3 ) ( 1 ) 0 . 9 9 8 6 5 0 0 . 8 4 1 3 4 5 0 . 1 5 7 3 0 5
SPC培训课件(PPT 90页)

接不良数等。 计件型数据和计点型数据合称为计数型数据。它们
可被计数,从而用来记录和分析。
12.01.2020
11
科华咨询
统计方法应用基础----基本的统计量
n 子组大小。单个子组中子组观测值的个数 k 子组数 X 质量特性的观测值(可用X1,X2,X3…表示单个 观测值) X 子组平均值的平均值
经分析发现,该工序最重要的是需要模具的相关方面被保证,如模具的安 装需到位,冲压过程需防止模具松动和磨损等。产品特性最重要的是冲压整 形的高度和宽度两个尺寸,如果这两个尺寸不能保证将导致产品报废。
12.01.2020
计量型 正态分布
数据的”分布”
二项分布(计数)
计数型 泊松分布(计件)
6
科华咨询
质量具有变差
“世界上没有两片完全相同的树叶”——“不同” 是绝对的,相同是相对的。
即使是机器生产,但产品质量仍具有变异 ——过程的单个输出之间不避免的差别。
公差制度的建立,就是承认“变差”的标志。
概率1.35% 概率可能为1.35%的几十、几百倍
根据小概率事件原理:出界就判异。
12.01.2020
27
科华咨询
控制图的两种错误
第一种错误
质量特性 x
α
虚发警报的错误 概率为α
12.01.2020
第二种错误
UCL
β
CL LCL
漏发警报的错误 概率为β 28
科华咨询
控制图的两种错误
间距增大(增加上下控制限的距离) α 减少,β 增加
p 子组不合格品率 p=子组中的不合格品数/子组大小
P 平均不合格品率
统计过程控制(SPC)与常规控制图PPT课件

防 3.SPC不仅用于生产过程﹐而且可用于服务
过程和一切管理过程
5
SPC发展简史
过程控制的概念与实施过程监控的方法在 1920S由美国的休哈特(W .A. Shewhart)提 出﹐二战后期在军工部门推行﹔
1950-1980段在美国工业中消失﹐由戴明 (W .Edwards Deming)博士将SPC引入日 本在30年的努力下﹐日本一跃而居世界质 量与生产率的领先地位
统计过程控制(SPC)与 常规控制图
1
整体概述
概况一
点击此处输入相关文本内容 点击此处输入相关文本内容
概况二
点击此处输入相关文本内容 点击此处输入相关文本内容
概况三
点Байду номын сангаас此处输入相关文本内容 点击此处输入相关文本内容
2
第一讲 SPC历史简介和SPC判断标准
3
1.SPC(Statistical Process Control)
判稳准则
1. 连续25个点子都在控制界限内 2. 连续35个点子至多有1个点子落在控制界限外 3. 连续100个点子至多有2个点子落在控制界限外
不符合上述三原则的概率为﹕
α 1=0.0654 α 2=0.0654 α 3=0.0654
13
4.控制图判断准则
(a) 连续9点出现在中心线的单侧
α=0.0038
SPC能给所有人带来好处﹕ 对操作者﹕可用SPC方法改进工作 对管理者﹕可用SPC方法消除在生产部门
与质量管理部门间的矛盾 对领导者﹕可用SPC方法控制产品质量﹐
减少返工与浪费
4
1.SPC(Statistical Process Control)
2024版SPC培训教材全课件
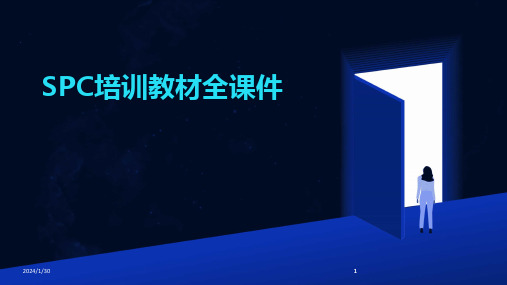
假设检验的基本概念
明确假设检验的定义、原假设与备择假设的设立原则及两类错误 的含义。
参数假设检验
掌握正态总体均值、方差的假设检验方法及步骤,理解t检验和F 检验的原理及应用场景。
非参数假设检验
了解非参数假设检验的适用条件及常用方法,如秩和检验、符号 检验等。
16
方差分析、回归分析应用举例
方差分析
掌握方差分析的基本原理、计算步骤及结果解释,理解其在多因素实验设计中的应用。
化。
大数据在SPC中的应用
大数据技术的不断发展将为SPC提供更丰富的数据来源和分析手段,有助于提高SPC的 应用效果。
2024/1/30
SPC在服务业的拓展
随着服务业的不断发展,SPC的应用领域将逐渐拓展到服务业领域,为服务业的质量管 理提供新的思路和方法。
36
下一讲预告及预备知识
2024/1/30
01
02
03
04
明确数据收集目标
根据业务需求,明确所需数据 的类型、范围和质量要求。
2024/1/30
制定数据收集计划
设计合理的数据收集流程,包 括数据源选择、采集频率、存
储方式等。
执行数据收集
运用合适的数据收集工具和技 术,按照计划进行数据采集。
数据质量监控
建立数据质量评估机制,确保 数据的准确性、完整性和一致
下一讲内容
下一讲将介绍SPC在企业中的实际应 用案例,包括不同行业和不同场景下 的SPC应用实践。
预备知识
为了更好地理解下一讲内容,建议学 员提前了解相关行业的生产流程和质 量管理要求,以及SPC在实际应用中 的挑战和解决方案。
37
THANKS
感谢观看
2024/1/30
SPC统计过程控制培训(PPT64页).pptx

4.1.1 正态分布曲线
f (x)
y
2
1
(
x
)
2
2
e ( x , 0)
2
---平均值
--- 标准差
4.1.2 正态分布的参数 、
4.1.3 正态分布的特点
• 曲线以 x = 直线为轴,左右对称 • 曲线与横坐标轴所围成的面积等于1
其中 在±范围内的面积占68.26 % 在±2范围内的面积占95.45 % 在±3范围内的面积占99.73 %
例:疵点数、沙眼数等
3、总体和样本(子组)
3.1 总体 研究对象的全体 总体含量记为 N
3.2 样本(子组) 总体中的部分样品 样本含量记为 n
4、常见的典型分布
4.1 正态分布 —— 计量值数据 4.2 二项分布 —— 计件值数据 4.3 泊松分布 —— 计点值数据
4.1 正态分布
X ~ N(, 2)
不同类型控制图的适用范围
适用范围
计 产品批量较大,稳定正常工序 量 产品批量较大,稳定正常工序 数 据 产品批量较大,稳定正常工序
每次只能得一个数据,见效快
计
样本含量可以不等
件 样本含量相等
计
样本含量相等
点 样本含量可以不等
用符号表示的控制图
X?R 图 均值极差图ቤተ መጻሕፍቲ ባይዱ
X桽 图 均值标准差图
X桽 图 中位数极差图
4 . 3 泊松分布: (常见于计点分布) 二项分布的极限分布 — P()
• 分布列
•P(均X值、x方)差和标x e准差 , (x 0,1,)
x!
均值: E(X)= ;
方差: V(X)= ;
标准差:
;
SPC统计过程控制培训课程(PPT97页).pptx

“”及“”风险定义
根据控制限作出的判断也可能产生错误。可能产生的错误
有两类。
第一类错误是把正常判为异常,它的概率为,也就是说 ,工序过程并没有发生异常,只是由于随机的原因引起了数据 过大波动,少数数据越出了控制限,使人误将正常判为异常。 虛发警报, 由于徒劳地查找原因并为此采取了相应的措施,从 而造成损失. 因此, 第一种错误又称为徒劳错误.
普通原因/异常原因
~
基础的统计量——平均值X、中位数X、极差R 标准偏差、S
1、数据的种类
计量型
特点:可以连续取值也 称连续型数据。
如:零件的尺寸、强度、 重量、时间、温度等
计数型
特点:不可以连续 取值,也称离散型数据 。
如:废品的件数、缺陷数
2、波动(变差)的概念:
波动的概念是指在现实生活中没有两件东西是完全一样的。生产 实践证明,无论用多么精密的设备和工具,多么高超的操作技术,甚至 由同一操作工,在同一设备上,用相同的工具,生产相同材料的同种产 品,其加工后的产品质量特性(如:重量、尺寸等)总是有差异,这种 差异称为波动。公差制度实际上就是对这个事实的客观承认。
消除波动不是SPC的目的,但通过SPC可以对波动进行预测和控制 。
波动的原因:
材料
机器
人员
• 正常波动:是由普通(偶然)
原因造成的。如操作方法的微 小变动、机床的微小振动、刀 具的正常磨损、夹具的微小松 动、材质上的微量差异等。正 常波动引起工序质量微小变化, 难以查明或难以消除。它不能 被操作工人控制,只能由技术、 管理人员控制在公差范围内。
原料
PROCESS
测量 结果
针对产品所做的仍 只是在做SQC
二、SPC的目的
SPC培训讲义(PPT 109页)

(Moving Range)
13
变差的普通原因和特殊原因
普通原因:是指过程在受控的状态下,出现的具 有稳定的且可重复的分布过程的变差的原因。普 通原因表现为一个稳定系统的偶然原因。只有过 程变差的普通原因存在且不改变时,过程的输出 才可以预测。
特殊原因:(通常也叫可查明原因)是指造成不 是始终作用于过程的变差的原因,即当它们出现 时将造成(整个)过程的分布改变。只有特殊原 因被查出且采取措施,否则它们将继续不可预测 的影响过程的输出。
D3=0.000
8
系列 1
R图
系列 2
4
D4=2.115
0
1
2
3
4
5
6
7
8
9
10
11
12
13
14
15
16
17
18
19
20
21
22
23
24
25
系列 1
编号 1 2 3 4 5 6 7 8 9 10 11 12 13 14 15 16 17 18 19 20 21 22 23 24
日期/时间
9/6 9/6 9/6 9/6 9/6 9/6 9/6 9/7 9/7 9/7 9/7 9/7 9/7 9/8 9/8 9/8 9/8 9/11 9/11 9/11 9/11 9/11 9/12 9/12 8:00- 9:00- 10:- 11:00- 13:30- 14:30- 15:30- 8:00- 9:00- 10:00- 11:00- 13:30- 15:30- 10:30- 13:30- 14:30- 15:30- 8:00- 9:00- 10:00- 11:00- 13:30- 8:00- 13:309:00 10:00 11:00 12:00 14:30 15:30 16:30 9:00 10:00 11:00 12:00 14:30 16:30 11:30 14:30 15:30 16:30 9:00 10:00 11:00 12:00 14:30 9:00 14:30
SPC与常规控制图培训课件

SPC与常规控制图培训课件1. 介绍SPC(Statistical Process Control,统计过程控制)是一种常用的质量管理工具,通过收集和分析过程数据来监控和控制生产过程中的变异性。
常规控制图是SPC的重要组成部分,用于识别过程是否处于控制状态。
本课件将介绍SPC与常规控制图的基本概念、使用方法和应用实例。
2. SPC的基本原理SPC的基本原理是通过收集过程数据并运用统计方法分析这些数据,从而判断过程是否处于控制状态。
SPC的主要目标是降低过程的变异性,确保产品的质量稳定。
3. 常见的常规控制图3.1 控制图的基本结构控制图通常由中心线、上限线和下限线组成。
中心线代表过程的平均值,上限线和下限线代表了过程的可接受变异范围。
3.2 均值控制图均值控制图用于监控过程的平均值是否处于控制状态。
常用的均值控制图包括平均值图、移动平均图和指数加权移动平均图。
3.3 范围控制图范围控制图用于监控过程的变异性是否处于控制状态。
常用的范围控制图包括范围图和标准差图。
3.4 异常值控制图异常值控制图用于检测过程中的异常值。
常见的异常值控制图包括箱线图和帕累托图。
4. 常用的统计方法4.1 均值与标准差均值和标准差是用来描述数据集中趋势和分布的统计指标。
均值代表数据的中心位置,标准差代表数据的离散程度。
4.2 相关性分析相关性分析用于确定两个变量之间的关系强度和方向。
常用的相关性分析方法包括皮尔逊相关系数和斯皮尔曼相关系数。
4.3 回归分析回归分析用于确定两个变量之间的函数关系。
常用的回归分析方法包括线性回归和多项式回归。
5. SPC的应用实例5.1 制造业中的SPC应用在制造业中,SPC被广泛应用于监控生产过程中的变异性,降低次品率和提高产品质量。
通过使用常规控制图,制造商可以及时发现并纠正生产过程中的异常情况。
5.2 服务业中的SPC应用在服务业中,SPC可以用于监控服务过程中的变异性,提高服务质量和满意度。
- 1、下载文档前请自行甄别文档内容的完整性,平台不提供额外的编辑、内容补充、找答案等附加服务。
- 2、"仅部分预览"的文档,不可在线预览部分如存在完整性等问题,可反馈申请退款(可完整预览的文档不适用该条件!)。
- 3、如文档侵犯您的权益,请联系客服反馈,我们会尽快为您处理(人工客服工作时间:9:00-18:30)。
准则: 在点子随机排列的情况下
1、连续25个点子都在控制界限内; 2、连续35个点子至多有1个点子落在控制 界限外;
3、连续100个点子至多有2个点子落在控 制界限外;
符号上述情况之一就认为过程处于稳态。
以规则1为例分析,规则1发生判断过程不 稳的概率。记d为界外点数,假设过程是稳 泰的,则
控制图上的信号解释
有很多信号规则适用于所有的控制图 主要最常见的有以下几种:
规则1:超出控制线的点
UCL LCL
控制图上的信号解释
规则2:连续9点在中心线一侧
UCL CL LCL
P( 中心线出现长为9的链)=2*(0.9973 /2)9=0.0038
控制图上的信号解释
规则3:连续6点上升或下降
画出有初始控制界限的的控制图,并将样本 统计量x和R逐一描点在图上,然后,用折线连接 起来。对超出控制界限的样本点要进行分析,若 是系统原因引起的要加以剔除。然后利用剩余的 样本统计量重新修正控制界限。
例1:某厂制作1879个线圈,其阻抗值的质量要求 为(15±2)Ώ.今从其制造过程中,按时间顺序 随机抽取n=5的20组样本,测得其阻抗值如表所 示。是画出X-R控制图。
3点中2个点子在中心线同一侧的2σ~ 3σ范围之内,另外一 个点子落在控制界限任何处,发生这种情况的概率为
2×C32×0.02142×(0.9973-0.0214) =0.00268
控制图上的信号解释
规则6:连续5点中有4点落在中心线同一侧 的1σ以外。
点子落在1σ~ 3σ之间的概率为 (3) (1) 0.998650 0.841345 0.157305
UCL
LCL
P(6点趋势)= 2 (0.9973)6 0.00273 6!
规则4:连续14点中相邻点上下交替
选择14点模拟试验,得出概率为0.0027
控制图上的信号解释
规则5:连续3点中有2点落在中心线的同一侧的2σ~ 3σ
点子落在中心线一侧2σ~ 3σ之间的概率为
(3) (2) 0.998650 0.977250 0.0214
SPC与常规控制图
——控制图概念
又叫管理图或休图。它是判断和预报生产过程中 质量状况是否发生异常波动的一种有效的方法。
可用3σ原则确定控制图的控制线(Control Lines)
CL=μ UCL=μ+3σ LCL=μ-3σ
控制图的基本原理
控制图是把造成质量波动的六个原因(人机料法 环、测量等)分为两个大类:随机性原因(偶然 性原因)和非随机性原因(系统原因)。这样, 我们就可以通过控制图来有效地判断生产过程质 量的稳定性,及时发现生产过程中的异常现象, 查明生产设备和工艺装备的实际精度,从而为制 定工艺目标和规格界限确立可靠的基础,使得过 程的成本和质量成为可预测的,并能够以较快的 速度和准确性测量出系统误差的影响程度。
控制图的基本原理(统计观点)
工序的加工过程稳定时,加工精度的 偏差服从正态分布,加工偏差落在3σ 范围内的概率是99.73%,据此作横线 图,标出相应区域,然后把统计加工 精度数据按时间顺序标在图上,判断 工序是否稳定。
判稳准则
思路:描一个点子未出界,不能判稳,因 为这里有两种可能 1)过程本来处于稳态 2)漏报 但是如果连续有许多点子打在界内,情况 就大不相同了,这时漏报的可能性就大为 减少,从而可能认为过程是出于稳态的
不合格率控制图(p), 不合格数控制图(pn), 单位缺陷数控制图(u), 缺陷数控制图(c)。
控制图的作法
计量值控制图仅讨论( X-R)图的作法。 X-R图是建立在正态分布基础上的。它由 X
控制图和R控制图组成,前者用来判断生产 过程中的均值是否处于或保持在所要求的 统计控制状态,后者用来判断生产过程的 波动是否处于或保持在所要求的统计控制 状态。
• 作图步骤为: 1)收集数据。根据选定的特性值,按一定的时间间
隔,抽取一个容量为n的样本,共取k个样本,一般要
求k≥25,n=4,5。
2)计算每一个样本的均值与级差,其中xij表示第i 个样本第j个观察值,用xi与Ri分别表示第i个样本的 均值与级差。
3)计算k个样本均值的均值与级差的均值。记
k
P(连续25点,d=0)=(0.99735)25=0.935385 P(连续25点,d>0)=1-P(连续25点,d=0)
=1-0.935385=0.064685=a1 同样地a2=0.0041, a3=0.0026
判异准则
思路:小概率事件原理 休哈特思想:
1、点出界就判异; 2、界内点排列不随机判异。
解:
1)搜集数据
从工序中每日定时搜集5个数据,记入表中。
X
n 系数
2)计算小组平均值:
xi
15.3
14.5 514.915.123)计算总体平均值:
X 15.12 14.20 15.06 15.033 20
4)计算总体级差 R 2.9 2.2 3.9 2.605 20
因此,发生这种情况的概率为
2×C54×0.1573054×(0.9973-0.157305) =0.00268
规则7连续15点在中心线正负1σ之间
0.6826815 =0.00326
常用控制图的种类
常用质量控制图可分为两大类: (1)计量值控制图包括:
均值-标准差控制图,均值-极差控制图, 中位数-极差控制图,单值-移动-极差控制图。 (2)计数值控制图包括:
5)计算的控制界限 X 图: CL 15.033 UCL 15.033 0.577 2.605 16.536 LCL 15.033 0.577 2.605 13.53
R图
CL R 2.605
UCL D4 R 2.115 2.605 5.510
LCL为负值,无意义令。 LCL=0 。
k
x xi / k R Ri / k
i1
i1
4)、计算x图与R图的上下控制界限
式中 : A2 ,D3,D4 ——是由样本大小n确定的 系数,可由下表查得。当n≤6时,D3为负值,而R 值为非负,此时LCL实质不存在。此时,可令 LCL=0作为下控制线。
•表 控制图用系数表
A2
D3
D4
5)、绘制控制图并加以修正