液态成形工艺基础
第一章 金属液态成形理论基础

第一节 液态金属充型能力与流动性
0、什么是液态金属的充型能力
1)定义:
液体金属充满铸型型腔,获得尺寸精确、轮廓清晰的 成型件的能力,称为充型能力。
2)充型能力对成型的影响
充型能力不足时,会产生浇不足、冷隔、夹渣、气孔 等缺陷。
3)影响充型能力的因素
充型能力首先取决于金属本身的流动性(流动能力),同 时又受铸型性质、浇注条件和铸件结构等因素影响。
一、铸件的凝固方式
在铸件凝固过程中,其断面上一般存在三个区 域:固相区、凝固区和液相区。
1、分类
依据对铸件质量影响较大的凝固区的宽窄划分 铸件的凝固方式为如下三类:
(1)逐层凝固
纯金属和共晶成分的合金在凝固过程中不存在液、固并 存的凝固区,随着温度下降,固体层不断加厚,液体不 断减少,直达铸件中心,这种凝固方式称为逐层凝固。
机械应力
二、铸件的变形及其防止
1、变形的原因:
铸件内部残余内应力。 只有原来受拉伸部分产生压缩 变形、受压缩部分产生拉伸变 形,才能使铸件中的残余内应 力减小或消除。
平板铸件的变形
杆件的变形
床身铸件的变形
粱形铸件的弯曲变形
2、防止措施:
减小应力; 将铸件设计成对称结构,使其内应力互相平衡; 采用反变形法; 设置拉肋; 时效处理。
2、冷裂纹的特征
裂纹细小,呈连续直线状,裂缝内有金属光泽或轻 微氧化色。
3、防止措施
凡是能减少铸件内应力和降低合金脆性的因素 均能防止冷裂。 设置防裂肋亦可有效地防止铸件裂纹。
防裂肋
三、合金的吸气性
液态合金中吸入的气体,若在冷凝过程中不能溢 出,滞留在金属中,将在铸件内形成气孔。
一)气孔的危害
气孔破坏了金属的连续性,减少了其承载的有效 截面积,并在气孔附近引起应力集中,从而降低 了铸件的力学性能。 弥散性气孔还可促使显微缩松的形成,降低铸件 的气密性。
材料成型内容要点(完整版)
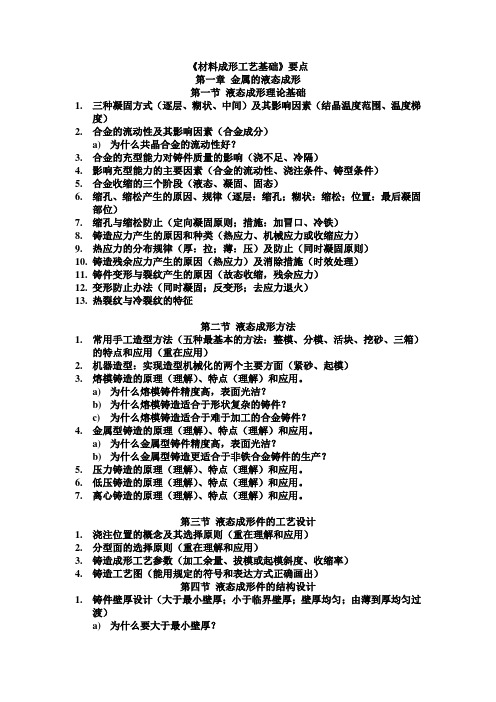
《材料成形工艺基础》要点第一章金属的液态成形第一节液态成形理论基础1.三种凝固方式(逐层、糊状、中间)及其影响因素(结晶温度范围、温度梯度)2.合金的流动性及其影响因素(合金成分)a)为什么共晶合金的流动性好?3.合金的充型能力对铸件质量的影响(浇不足、冷隔)4.影响充型能力的主要因素(合金的流动性、浇注条件、铸型条件)5.合金收缩的三个阶段(液态、凝固、固态)6.缩孔、缩松产生的原因、规律(逐层:缩孔;糊状:缩松;位置:最后凝固部位)7.缩孔与缩松防止(定向凝固原则;措施:加冒口、冷铁)8.铸造应力产生的原因和种类(热应力、机械应力或收缩应力)9.热应力的分布规律(厚:拉;薄:压)及防止(同时凝固原则)10.铸造残余应力产生的原因(热应力)及消除措施(时效处理)11.铸件变形与裂纹产生的原因(故态收缩,残余应力)12.变形防止办法(同时凝固;反变形;去应力退火)13.热裂纹与冷裂纹的特征第二节液态成形方法1.常用手工造型方法(五种最基本的方法:整模、分模、活块、挖砂、三箱)的特点和应用(重在应用)2.机器造型:实现造型机械化的两个主要方面(紧砂、起模)3.熔模铸造的原理(理解)、特点(理解)和应用。
a)为什么熔模铸件精度高,表面光洁?b)为什么熔模铸造适合于形状复杂的铸件?c)为什么熔模铸造适合于难于加工的合金铸件?4.金属型铸造的原理(理解)、特点(理解)和应用。
a)为什么金属型铸件精度高,表面光洁?b)为什么金属型铸造更适合于非铁合金铸件的生产?5.压力铸造的原理(理解)、特点(理解)和应用。
6.低压铸造的原理(理解)、特点(理解)和应用。
7.离心铸造的原理(理解)、特点(理解)和应用。
第三节液态成形件的工艺设计1.浇注位置的概念及其选择原则(重在理解和应用)2.分型面的选择原则(重在理解和应用)3.铸造成形工艺参数(加工余量、拔模或起模斜度、收缩率)4.铸造工艺图(能用规定的符号和表达方式正确画出)第四节液态成形件的结构设计1.铸件壁厚设计(大于最小壁厚;小于临界壁厚;壁厚均匀;由薄到厚均匀过渡)a)为什么要大于最小壁厚?b)为什么要小于临界壁厚?c)壁厚不均匀会产生什么问题?2.铸件壁间连接(圆角;避免锐角)3.铸件筋条设计(避免十字交叉)4.铸件外形设计和铸件内腔设计(理解;重在应用)5.结构斜度的设计(结构斜度与起模斜度的区别;重在应用)第二章金属的塑性成形第一节塑性成形工艺基础1.常用的六类塑性成形方法(轧制、拉拔、挤压、自由锻、模锻、板料冲压)2.与铸造比较,塑性成形法的最显著的特点(性能好,但形状不能太复杂)3.塑性变形对金属组织和性能的影响(冷变形条件下和热变形条件下;纤维组织及其性能特点)4.金属可锻性的衡量指标(塑性、变形抗力)及影响因素(成分;组织;温度)5.金属加热缺陷(过热、过烧、脱碳、过渡氧化)与碳钢始锻温度(低于固相线200℃)第二节热锻成形工艺1.自由锻基本工序(镦粗、拔长、冲孔、弯曲、切割、扭转)2.自由锻件结构工艺性3.模锻的基本原理(理解)及特点4.胎模锻的概念及特点(理解)第三节板料冲压1.两大类基本工序(分离工序和变形工序)2.冲裁的概念;冲裁变形过程(弹性变形阶段、塑性变形阶段、断裂分离阶段)及冲裁件断面特征(塌角或圆角带;光亮带;断裂带)3.切断的概念4.弯曲变形的特点(内:压;外:拉);弯曲的质量问题(弯裂;回弹);弯裂的防止办法(限制最小弯曲半径;弯曲线与纤维方向垂直);回弹的防止办法(模具角度比弯曲件角度小一个回弹角值)5.拉深的概念;拉深和冲裁工序所使用的凸、凹模之间的区别(间隙大小;圆角)拉深件质量问题(拉裂与起皱)6.拉深系数的概念及计算7.三类冲模的概念四种挤压方式第三章材料的连接成形第一节焊接成形工艺基础1.三大类焊接方法(熔化焊;压焊;钎焊);2.熔焊的冶金特点(理解)及保证焊接质量的基本措施(保护焊接区;渗加合金元素;脱氧脱硫);3.焊接接头的概念(焊缝加热影响区);4.焊接热影响区的概念(焊接过程中,焊缝两侧受焊接热作用而发生组织与性能变化的区域);5.低碳钢焊接热影响区的组成及其特点(熔合区;粗晶,性能差;过热区:粗晶,性能差;正火区:细晶,性能好;部分相变区:性能稍差);6.焊接应力与变形产生的原因(局部加热);7.防止和减少焊接应力的措施(焊前预热;焊接次序;焊后缓冷;焊后去应力退火);8.焊接变形的形式(收缩变形;角变形;弯曲变形;扭曲变形;波浪变形);9.防止和减小焊接变形的措施(刚性固定;反变形;焊接次序;焊前预热;焊后缓冷;矫正);10.焊接缺陷的种类及其检验方法(理解);第二节焊接方法1.焊条的组成及作用(焊芯和药皮;焊芯:作电极和焊缝的填充金属;药皮:稳定电弧燃烧;保护焊接区;渗加合金元素;脱氧脱硫);a)为什么焊条药皮中要加脱氧剂?2.两种重要的焊条(J422、J507);焊条选用原则(重在应用)3.埋弧焊的原理(理解)、特点和应用范围(水平位置焊接长直焊缝;大直径环形焊缝)b)埋弧焊的生产率为什么高于焊条电弧焊?c)埋弧焊与焊条电弧焊相比,为什么可以节省材料?d)埋弧焊为什么不能实现全位置焊接?4.氩弧焊的原理、特点及其应用;5.二氧化碳气体保护焊的原理、特点及其应用(注意与氩弧焊比较理解)e)二氧化碳保护焊时焊丝的成分有何要求,为什么?6.电渣焊的原理(电阻热)及其应用。
1-材料成形理论基础

材料成形工艺基础1第一章 材料成形理论基础液态成形--铸造 固态成形--锻造 固态连接--焊接21第一节 液态成形基础1、液态金属的结构液态金属在结构上更象固态而不是汽态,原子之间 仍然具有很高的结合能。
液态金属的结构特征 液态金属内存在近程有序的原子集团。
这种原子集团是不稳定 的,瞬时出现又瞬时消失。
所以,液态金属结构具有如下特 点: l)液态金属是由游动的原子团构成。
2)液态金属中的原子热运动强烈,原子所具有的能量各不相 同,且瞬息万变,这种原子间能量的不均匀性,称为能量起 伏。
3)由于液态原子处于能量起伏之中,原子团是时聚时散,时 大时小,此起彼伏的,称为结构起伏。
3第一节 液态成形基础1、液态金属的性质液态金属是有粘性的流体。
粘度的物理本质是原子间作 相对运动时产生的阻力。
表面张力:在液体表面内产生的平行于液体表面、且各 向均等的张力421.2铸件的凝固组织合金从液态转变成固态的过程,称为一次结晶 或凝固。
当液态金属冷却至熔点以下,经过一定时间的孕 育,就会涌现一批小晶核,随后这些晶核按原子规则 排列的各自取向长大,与此同时又有另一批小晶核生 成和长大,直至液体全部耗尽为止。
51.2铸件的凝固组织合金从液态转变成固态的过程,称为一次结晶 或凝固。
一次结晶从物理化学观点出发,研究液态金属的 生核Formation of stable nuclei 、长大Growth of crystals、结晶组织的形成规律。
凝固从传热学观点出发,研究铸件和铸型的传热过 程、铸件断面上凝固区域的变化规律、凝固方式与 铸件质量的关系、凝固缺陷形成机制等。
631.2铸件的凝固组织凝固组织分宏观和微观。
宏观组织:铸态晶粒的形态、大小、取向、分布 微观组织:晶粒内部的亚结构的形状/大小/相 对分布/缺陷等 晶粒越细小均匀,金属材料的强度和硬度越高,塑 性和韧性越好。
71.3铸件的凝固方式和控制铸件的工艺原则铸件的凝固方式逐层凝固方式(skin-forming solidification) 糊状凝固方式(mushy solidification) 中间凝固方式(middle solidification)。
材料成型技术基础第一章第五节与液态成形相关的新工艺、新技术简介

第五节与液态成形相关的新工艺、新技术简介一、模具快速成形技术快速成形(Rapid Prototyping,简称RP):利用材料堆积法制造实物产品的一项高新技术。
它能根据产品的三维模样数据,不借助其它工具设备,迅速而精确地制造出该产品,集中体现在计算机辅助设计、数控、激光加工、新材料开发等多学科、多技术的综合应用。
传统的零件制造过程往往需要车、钳、铣、刨、磨等多种机加工设备和各种工装、模具,成本高又费时间。
一个比较复杂的零件,其加工周期甚至以月计,很难适应低成本、高效率生产的要求。
快速成形技术是现代制造技术的一次重大变革。
(一)快速成形工艺快速成形技术就是利用三维CAD的数据,通过快速成形机,将一层层的材料堆积成实体原型。
迄今为止,国内、外已开发成功了10多种成熟的快速成形工艺,其中比较常用的有以下几种:1.纸层叠法—薄形材料选择性切割(LOM法)计算机控制的CO2激光束按三维实体模样每个截面轮廓对薄形材料(如底面涂胶的卷状纸、或正在研制的金属薄形材料等)进行切割,逐步得到各个轮廓,并将其粘结快速形成原型。
用此法可以制作铸造母模或用于“失纸精密铸造”。
2.激光立体制模法—液态光敏树脂选择性固化(SLA法)液槽盛满液态光敏树脂,它在计算机控制的激光束照射下会很快固化形成一层轮廓,新固化的一层牢固地粘结在前一层上,如此重复直至成形完毕,即快速形成原型。
激光立体制模法可以用来制作消失模,在熔模精密铸造中替代蜡模。
3.烧结法—粉末材料选择性激光烧结(SLS法)粉末材料可以是塑料、蜡、陶瓷、金属或它们复合物的粉体、覆膜砂等。
粉末材料薄薄地铺一层在工作台上,按截面轮廓的信息,CO2激光束扫过之处,粉末烧结成一定厚度的实体片层,逐层扫描烧结最终形成快速原型。
用此法可以直接制作精铸蜡模、实型铸造用消失模、用陶瓷制作铸造型壳和型芯、用覆膜砂制作铸型、以及铸造用母模等。
4.熔化沉积法—丝状材料选择性熔覆(FDM法)加热喷头在计算机的控制下,根据截面轮廓信息作X-Y平面运动和高度Z方向的运动,塑料、石腊质等丝材由供丝机构送至喷头,在喷头中加热、熔化,然后选择性地涂覆在工作台上,快速冷却后形成一层截面轮廓,层层叠加最终成为快速原型。
金属的液态成型

• 2. 球墨铸铁(简称球铁)
• ① 球墨铸铁球化、孕育处理 球铁是用灰口铸铁 成份的铁水经球化、孕育处理后制成的。为保证 球铁质量,生产中应注意下列几点:
• 球墨铸铁的化学成分选择 原铁水成分与灰口铸铁 原则上相同,但要求严格。
• 球化剂和孕育剂
• ②球墨铸铁的铸造性能和工艺特点
• 3.可锻铸铁
• 合理选择铸造合金
• 合理选用凝固原则
显微缩松
顺序凝固原则
阀体铸造方案
同时凝固原则
• (2)铸造内应力、变形和裂纹的形成和控制 • 铸件在凝固后继续冷却时,若在固态收缩阶段受
到阻碍,则将产生应力,此应力称为 铸造内应力。 它是铸件产生变形、裂纹等缺陷的主要原因。 • ① 铸造内应力形成过程 铸造内应力按其产生原 因,可分为热应力和机械应力两种。 • 热应力 铸件在凝固和冷却过程中,由于不同部位 不均衡的收缩而引起的应力称为热应力。 • 机械应力 铸件在固态收缩时因受到机械阻碍而形 成的应力,称为机械应力,也称收缩应力。 • ②铸件的变形与裂纹 当铸件中存有内应力时, 会使其处于不稳定状态。 • ③铸件变形、裂纹的控制 所有减少铸造内应力 的措施都有肋于控制铸件的变形和裂纹。
• ①金属型应保持合理的工作温度。
• ②为保护型腔和减缓铸型的传热速度,型腔表面和浇冒口 中要涂以厚度为0.2~1.0 mm的耐火涂料,以使金属液和 铸型隔开。
• ③因金属型无退让性,故应掌握好适宜的开型时间。
• ④为防止铸铁件产生白口组织,其壁厚一般应大于15 mm ,并控制铁水中碳、硅的质量分数不小于6%。
6.1.3 合金的偏析和吸气性
• 1.偏析 • 在铸件中出现化学成分不均匀的现象称为偏析。偏析使铸
件性能不均匀,严重时会造成废品。偏析分为晶内偏析和 区域偏析两类。 • 晶内偏析(又称枝晶偏析)是指晶粒内各部分化学成分不均 匀的现象。采用扩散退火可消除晶内偏析。 • 区域偏析是指铸件上、下部分化学成分不均匀的现象。为 防止区域偏析,在浇注时应充分搅拌或加速合金液冷却。 • 2.吸气性 • 合金在熔炼和浇注时吸收气体的性能称为合金的吸气性。
机械制造基础铸造成形培训课件ppt 125页.ppt

1)可以铸出内腔、外形很复杂的毛坯; 2)工艺灵活性大。几乎各种合金,各种尺寸、形状、 重量和数量的铸件都能生产;
3)成本较低。原材料来源广泛,价格低廉。
铸造的缺点:
1)铸造组织疏松、晶粒粗大,内部易产生缩孔、缩松、 气孔等缺陷。 2)铸件的机械性能较低。 3)铸造工序多,难以精确控制,使铸件质量不够稳定。
第1节 液态成形理论基础
2.1.1 金属的凝固 2.1.2 金属与合金的铸造性能 2.1.3 铸造性能对铸件质量的影响
2.1.1 金属的凝固
1. 液态金属的结构与性质
1)液态金属的结构:固态金属经加热变为熔融状态即得 液态金属,是由呈有序排列的游动原子集团组成,其结 构与原有固体结构相似,但热运动剧烈,温度越高,热 运动越剧烈,原子集团越小,游动越快。
4)劳动条件较差,劳动强度较大。
铸造在机械制造业中应用十分广泛,在各种类型的 机器设备中铸件占很大比重。如表2-1所示。
表2-1 各类机械工业中铸件重量比
机械类别
%
机床、内燃机、重型机器 风机、压缩机 拖拉机 农业机械 汽车
70~90 60 ~ 80 50 ~ 70 40 ~ 70 20 ~ 30
金熔点最低,故流动性最好。
而亚共晶合金,为中间凝固方 式,复杂枝晶阻碍流动,故流
图2-4铅锡合金的流动性与相图的关系
动性差,如图2-5b所示。
3)杂质和含气量。固态夹杂物使粘度增加,流动性下降; 如灰铁中的MnS;含气量越少,流动性越好。
2. 浇注条件
1)浇注温度越高,保持液态的时间越长,流动性越好; 温度越高,合金粘度越低,阻力越小,充型能力越强。 故提高浇注温度能有效提高充型能力;但过高吸气量和 总收缩大,易产生铸造缺陷。故在保证充型能力的前提 下温度应尽量低。生产中薄壁件常采用较高温度,厚壁 件采用较低浇注温度。
金属液态成形

材料成形技术基础第一章 金属液态成形金属液态成形(铸造):将液态金属在重力或外力作用下充填到型腔中,待其凝固冷却后,获得所需形状和尺寸的毛坯或零件的方法。
液态成形的优点:(1)适应性广,工艺灵活性大(材料、大小、形状几乎不受限制)(2)最适合形状复杂的箱体、机架、阀体、泵体、缸体等(3)成本较低(铸件与最终零件的形状相似、尺寸相近)主要问题:组织疏松、晶粒粗大,铸件内部常有缩孔、缩松、气孔等缺陷产生,导致铸件力学性能,特别是冲击性能较低。
分类:铸造从造型方法来分,可分为砂型铸造和特种铸造两大类。
其中砂型铸造工艺如图1-1所示。
图1-1 砂型铸造工艺流程图第一节金属液态成形工艺基础一、熔融合金的流动性及充型液态合金充满型腔是获得形状完整、轮廓清晰合格铸件的保证,铸件的很多缺陷都是在此阶段形成的。
(一)熔融合金的流动性1.流动性 液态合金充满型腔,形成轮廓清晰、形状和尺寸符合要求的优质铸件的能力,称为液态合金的流动性。
流动性差:铸件易产生浇不到、冷隔、气孔和夹杂等缺陷。
流动性好:易于充满型腔,有利于气体和非金属夹杂物上浮和对铸件进行补缩。
螺旋形流动性试样衡量合金流动性,如图1-2所示。
在常用铸造合金中,灰铸铁、硅黄铜的流动性最好,铸钢的流动性最差。
常用合金的流动性数值见表1-1。
表1-1 常用合金的流动性(砂型,试样截面8㎜×8㎜)2. 影响合金流动性的因素(1) 化学成份 纯金属和共晶成分的合金,由于是在恒温下进行结晶,液态合金从表层逐渐向中心凝固,固液界面比较光滑,对液态合金的流动阻力较小,同时,共晶成分合金的凝固温度最低,可获得较大的过热度,推迟了合金的凝固,故流动性最好;其它成分的合金是在一定温度范围内结晶的,由于初生树枝状晶体与液体金属两相共存,粗糙的固液界面使合金的流动阻力加大,合金的流动性大大下降,合金的结晶温度区间越宽,流动性越差。
Fe-C合金的流动性与含碳量之间的关系如图1-3所示。
介绍一种液态成形方法

介绍一种液态成形方法液态成形是一种以液体状态的原材料为基础,通过特定的工艺和设备,将材料注入模具中形成所需形状的制造方法。
在液态成形过程中,材料通常是高温和高压状态下,通过喷射、浇铸、聚合等方式进行加工。
一种常见的液态成形方法是注塑成形。
注塑成形是一种将液态塑料材料注入到模具中,并在一定时间内加热和压力作用下,使其快速冷却凝固,最终成为所需形状的制造工艺。
注塑成形具有成形速度快、灵活多变、产品精度高等优点,广泛应用于塑料制品的生产中。
注塑成形的步骤如下:1. 原料准备:首先需要根据产品的要求选择适当的塑料原料,并进行预处理,如加热、干燥等,确保原料的质量和流动性。
2. 模具制备:根据产品的形状和尺寸设计和制作相应的模具。
模具通常由两个部分组成,上模和下模,它们可以通过冷却装置进行加热或冷却。
3. 打开模具:将模具打开,上模和下模分离。
4. 注射料加入:将预处理好的塑料原料注入机器的料斗中,通过加热和压力作用,将塑料原料熔化。
5. 注射过程:将熔化的塑料材料通过注射机的喷嘴注入到模具的模腔中,并在一定的时间内保持加压状态。
6. 冷却凝固:待塑料材料填充满模腔后,开始进行冷却凝固。
模具的冷却系统可以加速塑料材料的冷却速度。
7. 打开模具:待塑料材料完全冷却并固化后,将上模和下模打开,取出成品。
8. 去除支撑物:对于一些复杂的产品,可能需要去除一些辅助支撑物或余料。
9. 完成产品:经过修整、打磨等工序后,最终得到符合要求的成品。
除了注塑成形,还有其他的液态成形方法,如挤压成形、热压成形、钣金成形等。
这些液态成形方法的原理和步骤各有差异,但都以液态材料为基础,通过特定的工艺将其成形为所需的产品形状。
液态成形方法具有很多优点。
首先,它可以制造复杂的形状和精密的尺寸。
其次,成形速度快,效率高,适用于大批量生产。
此外,液态成形方法还可以利用一些特殊的材料,如高分子材料、金属和合金等,制造出具有特殊性能和广泛应用的制品。
- 1、下载文档前请自行甄别文档内容的完整性,平台不提供额外的编辑、内容补充、找答案等附加服务。
- 2、"仅部分预览"的文档,不可在线预览部分如存在完整性等问题,可反馈申请退款(可完整预览的文档不适用该条件!)。
- 3、如文档侵犯您的权益,请联系客服反馈,我们会尽快为您处理(人工客服工作时间:9:00-18:30)。
凸台设计,活块,外部芯子
二、铸件内腔的设计
1 .应尽量减少型芯的数量,避免不必要的型芯。
悬臂支架,悬臂芯,工字型开式截面 使用自带芯砂的条件:开口式,没有内凹,开口直径D大于 高度H
2 .便于型芯的固定、排气和清理。
不合理
合理
芯子悬空,依靠芯撑来加固,下芯、合箱困难,芯子难以排气,铸后芯砂和 芯骨也难以取出。
4. 为便于造型、下芯、合箱及检验
③
铸件壁厚,应尽量使型腔及主要型
芯位于下箱。(2)
①
上
②
下
上 ①
下
②
管子堵头的分型方案
机床支柱的分型方案
三、铸造工艺参数的确定
1.机械加工余量和铸孔Machining Allowance
为切削加工而加大的尺寸称为机械加工余量
生产批量
最小铸出孔直径
灰口铸铁件
铸钢件
大量生产 成批生产 单件、小批生产
2 .铸件壁厚应均匀、避免厚大截面 热节,缩松缩孔,热应力
3 . 合理选择铸件截面形状
二、铸件壁的连接
1.铸件的结构圆角结晶方向 3.厚壁与薄壁间要逐步过渡
性
2.避免壁的交叉和锐
4.减缓筋、辐收缩的阻碍
角连接
五、铸件结构设计应考虑的其它问题
1 .铸造方法 2 .组合铸件的设计
压铸件结构设计
§4-3 液态成形工艺设计实例
若大平面结构位于上部,易产生砂 眼、气孔或夹渣、夹砂和浇不足等 缺陷。液体充型时间长,型腔表面 受热辐射作用强,产生型砂拱起和 开裂,甚至局部脱落。
薄壁结构的型腔对液体金属的充型 阻力大,若处于铸型上部,液体金 属的静压力小,充型不足造成浇不 足或冷隔等缺陷。
3.对于易产生缩孔的铸件,厚大部分应放在铸型的上部 或侧面。
12~15 15~30 30~50
30~50 50
2.起模斜度 为便于取芯,垂直于分型面的侧壁在制造模型时, Pattern Draft 必须做出一定斜度。
β1<β2 β < β1
3.铸造圆角 圆角半径一般约为相交两壁平均厚度的1/3~1/2。 4.铸造收缩率 Casting Shrinkage Allowance 通常灰铸铁为0.7~1.0%,铸造碳钢为1.3~2.0%,铝硅 合金为0.8~1.2%,锡青铜为1.2~1.4%。
②
1 选择分型面
2 确定加工余量
3 确定起模斜度
③
4 确定型芯及芯头尺
寸和位置
下
上
①
方便在铸件厚处直接安放冒口,实 现自下而上的顺序凝固。
若厚端在下部,则难以补缩。
4.应尽量减少芯子的数量。 P39 图1-41和1-42。 浇注位置的选择原则可概括为:两下一上一少。
二、分型面的选择
铸型的结合面
1. 分型面应选在铸件的最大截面处。 2. 应尽量使铸件的全部或大部置于同一砂箱。(2) 3. 应尽量减少分型面的数量,并尽可能选择平面分型。
2. 冒口 冒口是在铸型中设置的一个储存金属液的空腔。
明冒口 普通冒口
暗冒口
冒口
特种冒口
保温冒口 发热冒口 大气压力冒口 易割冒口
P45
§4-2 铸件结构设计
一、铸件外形的设计
1 .避免外部侧凹、凸起;
2 .凸台、筋条的设计应便于起模(b) 斜度 端盖 3 .分型面应尽量平直;
筋条、凸台等在起模方向投影
第四章 液态成形金属件的工艺设计
§4-1 砂型铸造工艺设计
铸造工艺图—将工艺设计的内容(工艺方案)用工艺符号 或文字在零件图上表示出来 所形成的图样。
铸造工艺设计内容
1.分型面的选择 2.浇注位置的选择 3.工艺参数的确定 4.浇、冒系统的设计
一、浇注位置的选择
浇注时,铸件在铸型中所处的空间位置
5 .型芯及芯头 型芯的功用是形成铸件的内腔、孔洞和形状复杂阻碍起模 部分的外形。
芯头的作用:
1)定位作用;
2)固定作用;
3)排气作用。
四、浇、冒口系统
1. 浇注系统 1)浇注系统的组成及作用
直液压阻浇体液住横流内速度浇引力力口并流浇外部浇和度口 入 以在杯将对口,分口凝和:横保规:之铸:主熔:固方将浇证定承引型除要渣控的向来道金的接入的了起进制顺,自,属时来直直向挡入金序调口它液间自浇接内渣直属。节浇提克内浇道冲浇作浇液铸口供服充包,击道用道流件杯足各满的缓,中。。入各的够种型金和还分型部金的流腔属金可配腔分属静动。液属挡液的温 2)浇注系统的常见类型
球墨铸铁 6
可锻铸铁 5
6~10
12
8
15~20
15~20
10~12
铝合金 3
铜合金 3~5
4
6~8
6
10~12
随着壁厚的增大铸件的强度随之增大,但
2)铸件的临界壁厚
当壁厚达到某一临界值时,由于缺陷的增 加,强度反而会下降,这一临界值就称作
临界壁厚。
在砂型铸造条件下,临界壁厚≈3×最小壁厚
在最小壁厚和临界壁厚之间就是适宜的铸件壁厚。
1.铸件的重要加工面和受力面应朝下或位于侧面 。
车床的床身导轨是主要工作面和重要加 工面,要求组织致密和硬度高,缺陷低, 因此,应将导轨面处于刑腔下部。
吊车卷扬筒的主要加工面为外圆柱面, 采用立位浇注,卷筒的全部圆周表面位 于侧位,保证其质量均匀一致。
2.应将面积较大的薄壁部位置于铸型下部,或使其倾斜 位置。
3 .大件或形状复杂件可采用组合结构。
三、铸件壁厚的设计
1 .合理设计铸件壁厚 1)铸件的最小壁厚
在一定铸造工艺条件下,所能浇注出 的铸件壁厚的最小值。
铸件尺寸 (mm)
<200×200 200×20~ 500×500 >500×500
铸钢 8
10~12 15~20
合金种类(砂型铸造)
灰口铸铁 5~6