电线电缆生产工艺流程
电线电缆生产加工工艺流程

电线电缆生产加工工艺流程电线电缆是广泛应用于各个领域的电气设备,其生产加工工艺流程一般包括下面几个步骤:1.原材料准备:电线电缆的主要原材料包括导体、绝缘材料、护套材料等。
导体一般采用铜或铝等金属材料,绝缘材料可以是橡胶、聚乙烯、聚氯乙烯等。
在生产之前,需要对这些原材料进行检验和测试,确保其质量符合相关标准要求。
2.导体制造:导体是电线电缆的主要组成部分,其制造一般包括拉丝和挤压两个步骤。
首先,通过机械拉丝的方法将金属材料拉成所需的直径和长度;然后,将导体放入挤压机中,在高温下将绝缘材料覆盖在导体上。
3.绝缘层制造:绝缘层是为了保护导体,防止电线电缆发生漏电或短路等故障。
绝缘层的制造一般采用挤压或包带的方法。
挤压方法是将绝缘材料通过挤出机挤压到导体表面,形成所需的厚度;包带方法是通过固定的机器将绝缘材料缠绕在导体上,形成所需的绝缘层厚度。
4.护套制造:为了进一步保护电线电缆,阻止外界环境因素对其造成损害,需要制造护套。
护套一般采用PVC、PE等塑料材料制造,具有耐磨、耐化学腐蚀等特点。
护套的制造一般采用挤压的方法,将护套材料通过挤出机挤压到电缆外部。
5.终端接头制造:终端接头是电线电缆与设备连接的关键部分,其制造一般包括绝缘处理、绝缘套管的安装等步骤。
首先,需要对电缆导体进行绝缘处理,确保导体表面干净和光滑;然后,将绝缘套管安装到导体上,并进行压接或焊接等操作,使接头与设备连接紧密可靠。
6.检验和测试:在生产加工过程中,需要对电线电缆进行各项检验和测试,以确保其质量符合标准要求。
包括导体电阻、绝缘电阻、电力损耗、机械性能等方面的测试。
7.包装和贮存:最后,对生产好的电线电缆进行包装,以确保其在运输和贮存过程中不受损坏。
常用的包装方式包括盘装、卷装等。
以上是电线电缆生产加工的一般工艺流程,每个步骤的具体操作和细节会根据不同的产品类型和要求有所差异。
有效的生产加工工艺流程能确保电线电缆质量可靠,满足用户的使用需求。
35kv电缆生产工艺流程
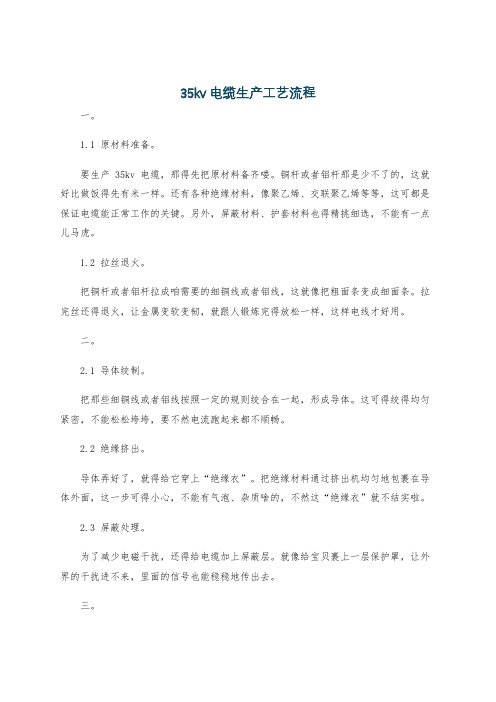
35kv电缆生产工艺流程一。
1.1 原材料准备。
要生产 35kv 电缆,那得先把原材料备齐喽。
铜杆或者铝杆那是少不了的,这就好比做饭得先有米一样。
还有各种绝缘材料,像聚乙烯、交联聚乙烯等等,这可都是保证电缆能正常工作的关键。
另外,屏蔽材料、护套材料也得精挑细选,不能有一点儿马虎。
1.2 拉丝退火。
把铜杆或者铝杆拉成咱需要的细铜线或者铝线,这就像把粗面条变成细面条。
拉完丝还得退火,让金属变软变韧,就跟人锻炼完得放松一样,这样电线才好用。
二。
2.1 导体绞制。
把那些细铜线或者铝线按照一定的规则绞合在一起,形成导体。
这可得绞得均匀紧密,不能松松垮垮,要不然电流跑起来都不顺畅。
2.2 绝缘挤出。
导体弄好了,就得给它穿上“绝缘衣”。
把绝缘材料通过挤出机均匀地包裹在导体外面,这一步可得小心,不能有气泡、杂质啥的,不然这“绝缘衣”就不结实啦。
2.3 屏蔽处理。
为了减少电磁干扰,还得给电缆加上屏蔽层。
就像给宝贝裹上一层保护罩,让外界的干扰进不来,里面的信号也能稳稳地传出去。
三。
3.1 成缆绞合。
把几根带有绝缘和屏蔽的线芯绞合在一起,组成电缆的缆芯。
这就跟拧麻花似的,得拧得好看又结实。
3.2 护套挤出。
给缆芯穿上一层厚厚的“防护服”,也就是护套。
这护套得耐磨、耐蚀,能保护电缆在各种环境下都能正常工作,风吹雨打都不怕。
生产 35kv 电缆可不是一件简单的事儿,每一个环节都得精心操作,容不得半点马虎。
只有这样,才能生产出高质量的电缆,为电力传输保驾护航!。
电线电缆工艺流程

电线电缆工艺流程电线电缆是现代通信和电力输送的重要组成部分,它们在各个领域中被广泛使用。
下面是一个基本的电线电缆工艺流程,以帮助我们更好地了解电线电缆的生产过程。
第一步,原材料准备。
电线电缆的主要原材料包括导线、绝缘层、外护层等。
这些材料需要经过一系列的检验和测试,确保其质量符合标准要求。
第二步,导线制造。
在导线制造过程中,通常会用到铜或铝等导电材料。
首先,将导电材料熔化,注入模具中,使其形成所需的导线形状。
然后,通过拉伸和退火等工艺,使导线获得所需要的导电性能。
第三步,绝缘层制造。
绝缘层主要用于保护导线,并防止电流泄露。
常用的绝缘材料有聚乙烯、聚氯乙烯等。
绝缘层的制造通常通过挤出工艺进行。
先将绝缘材料加热熔化,然后通过挤出机将其挤出成所需的绝缘层形状。
这个过程需要控制温度和挤出速度等参数,以保证绝缘层的厚度和质量。
第四步,绞合和编织。
在这个过程中,将多根绝缘处理后的导线绞合在一起。
绞合的目的是为了提高电缆的柔韧性和抗拉强度。
在绞合过程中,还会加入编织层,用于增加电缆的抗压能力和防护功能。
第五步,外护层制造。
外护层主要用于保护电缆免受外部环境的损害。
常用的外护材料有聚乙烯、聚氯乙烯等。
外护层的制造通常也是通过挤出工艺进行。
挤出机将外护材料加热熔化,并将其挤出成所需的外护层形状。
同样,控制温度和挤出速度等参数是关键,以保证外护层的厚度和质量。
第六步,成品检验。
制造完成的电线电缆需要经过一系列的检验和测试,确保其电气性能和物理性能符合标准要求。
这包括导体电阻、绝缘电阻、外皮厚度、机械强度等方面的检测。
最后一步,包装和出厂。
合格的电线电缆经过包装后,可以出厂销售。
包装形式一般有卷装、盘装等,根据不同的需求进行选择。
以上是一个基本的电线电缆工艺流程。
随着科技的发展,电线电缆的制造工艺也在不断改进和创新,以满足不同领域的需求。
电线电缆生产工序流程
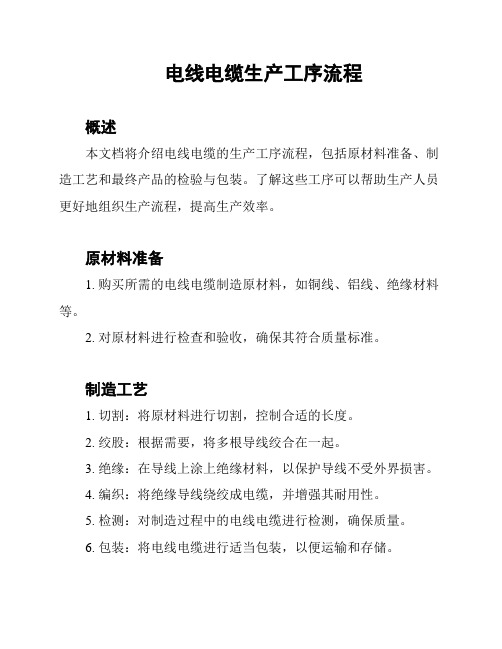
电线电缆生产工序流程
概述
本文档将介绍电线电缆的生产工序流程,包括原材料准备、制造工艺和最终产品的检验与包装。
了解这些工序可以帮助生产人员更好地组织生产流程,提高生产效率。
原材料准备
1. 购买所需的电线电缆制造原材料,如铜线、铝线、绝缘材料等。
2. 对原材料进行检查和验收,确保其符合质量标准。
制造工艺
1. 切割:将原材料进行切割,控制合适的长度。
2. 绞股:根据需要,将多根导线绞合在一起。
3. 绝缘:在导线上涂上绝缘材料,以保护导线不受外界损害。
4. 编织:将绝缘导线绕绞成电缆,并增强其耐用性。
5. 检测:对制造过程中的电线电缆进行检测,确保质量。
6. 包装:将电线电缆进行适当包装,以便运输和存储。
检验与包装
1. 对最终产品进行全面的质量检验,包括外观、电性能等方面。
2. 根据产品质量是否合格确定包装方式,如托盘、卷盘等。
3. 标注产品相关信息,如型号、规格、批次号等。
以上为电线电缆生产工序流程的简要介绍。
不同类型的电线电
缆可能会有略微的差异,请根据实际情况进行调整和补充。
电线电缆加工工艺流程
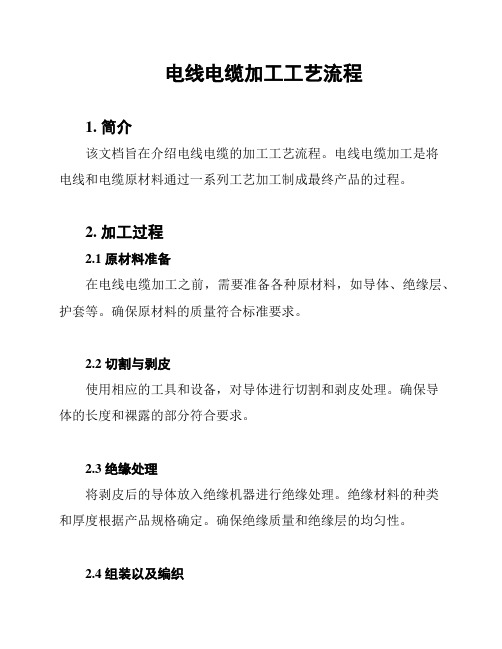
电线电缆加工工艺流程
1. 简介
该文档旨在介绍电线电缆的加工工艺流程。
电线电缆加工是将
电线和电缆原材料通过一系列工艺加工制成最终产品的过程。
2. 加工过程
2.1 原材料准备
在电线电缆加工之前,需要准备各种原材料,如导体、绝缘层、护套等。
确保原材料的质量符合标准要求。
2.2 切割与剥皮
使用相应的工具和设备,对导体进行切割和剥皮处理。
确保导
体的长度和裸露的部分符合要求。
2.3 绝缘处理
将剥皮后的导体放入绝缘机器进行绝缘处理。
绝缘材料的种类
和厚度根据产品规格确定。
确保绝缘质量和绝缘层的均匀性。
2.4 组装以及编织
将绝缘处理后的导体按照产品要求进行组装。
在某些情况下,
可能需要进行编织处理以增强电线电缆的耐用度和机械强度。
2.5 护套安装
对组装好的电线电缆进行护套安装。
护套可以提供保护、防水
和防腐功能。
确保护套安装的牢固性。
2.6 电线电缆测试
在完成加工工艺后,对电线电缆进行测试,包括电气性能测试、可靠性测试和耐久性测试等。
确保产品符合标准要求。
2.7 包装与存储
对通过测试的电线电缆进行包装,并按照规定进行标识和存储。
确保产品在运输和存储过程中不受损坏。
3. 结论
以上为电线电缆加工的基本工艺流程。
在实际操作中,可能会
根据产品的特殊要求和标准的变化进行相应的调整和改进。
电线电缆生产工艺流程
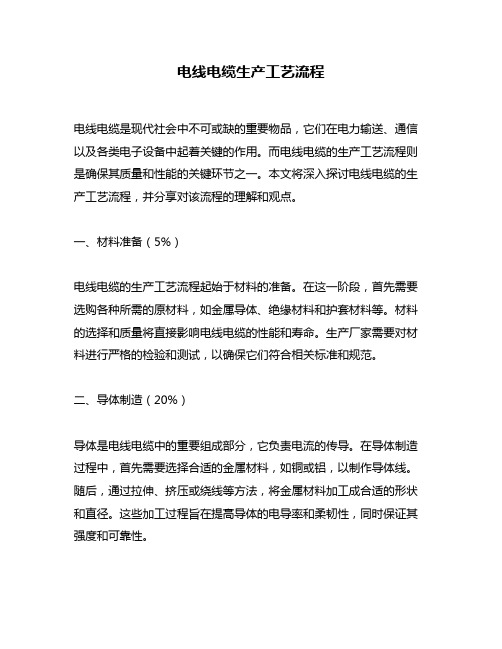
电线电缆生产工艺流程电线电缆是现代社会中不可或缺的重要物品,它们在电力输送、通信以及各类电子设备中起着关键的作用。
而电线电缆的生产工艺流程则是确保其质量和性能的关键环节之一。
本文将深入探讨电线电缆的生产工艺流程,并分享对该流程的理解和观点。
一、材料准备(5%)电线电缆的生产工艺流程起始于材料的准备。
在这一阶段,首先需要选购各种所需的原材料,如金属导体、绝缘材料和护套材料等。
材料的选择和质量将直接影响电线电缆的性能和寿命。
生产厂家需要对材料进行严格的检验和测试,以确保它们符合相关标准和规范。
二、导体制造(20%)导体是电线电缆中的重要组成部分,它负责电流的传导。
在导体制造过程中,首先需要选择合适的金属材料,如铜或铝,以制作导体线。
随后,通过拉伸、挤压或绕线等方法,将金属材料加工成合适的形状和直径。
这些加工过程旨在提高导体的电导率和柔韧性,同时保证其强度和可靠性。
三、绝缘处理(25%)绝缘是保护电线电缆导体的关键环节。
在绝缘处理阶段,导体被包覆在绝缘材料中,以防止电流外泄和短路等问题的发生。
常用的绝缘材料包括聚氯乙烯(PVC)、交叉链聚乙烯(XLPE)以及橡皮等。
绝缘材料的选择取决于电线电缆的具体应用环境和要求。
在绝缘处理过程中,绝缘材料需要经过挤出、浸渍、包覆等步骤,以确保其与导体的良好粘结和完整性。
四、编织护套(20%)编织护套是为电线电缆提供机械保护和防护的重要部分。
它既可以增强电线电缆对拉力和挤压的抵抗能力,又能够防止外界环境因素的侵入,如水、油和化学物质等。
通常,编织护套采用聚酯、聚酰胺或金属丝等材料制成。
编织护套的加工过程包括编织、包覆和压实等步骤,以确保其良好的柔韧性和抗剥离性。
五、成品检验和包装(15%)电线电缆的生产工艺流程的最后阶段是成品检验和包装。
在这一阶段,生产厂家将对电线电缆的质量和性能进行全面检验。
这包括导体电阻、绝缘电阻、耐压和耐热性能等方面的测试。
只有通过了严格的检验,电线电缆才能进入下一阶段的包装和出厂销售。
电线电缆制造的基本工艺流程
1.铜、铝单丝拉制电线电缆常用的铜、铝杆材,在常温下,利用拉丝机通过一道或数道拉伸模具的模孔,使其截面减小、长度增加、强度提高。
拉丝是各电线电缆公司的首道工序,拉丝的主要工艺参数是配模技术。
2.单丝退火铜、铝单丝在加热到一定的温度下,以再结晶的方式来提高单丝的韧性、降低单丝的强度,以符合电线电缆对导电线芯的要求。
退火工序关键是杜绝铜丝的氧化.3.导体的绞制为了提高电线电缆的柔软度,以便于敷设安装,导电线芯采取多根单丝绞合而成。
从导电线芯的绞合形式上,可分为规则绞合和非规则绞合。
非规则绞合又分为束绞、同心复绞、特殊绞合等。
为了减少导线的占用面积、缩小电缆的几何尺寸,在绞合导体的同时采用紧压形式,使普通圆形变异为半圆、扇形、瓦形和紧压的圆形。
此种导体主要应用在电力电缆上。
4.绝缘挤出塑料电线电缆主要采用挤包实心型绝缘层,塑料绝缘挤出的主要技术要求:4.1.偏心度:挤出的绝缘厚度的偏差值是体现挤出工艺水平的重要标志,大多数的产品结构尺寸及其偏差值在标准中均有明确的规定。
4.2.光滑度:挤出的绝缘层表面要求光滑,不得出现表面粗糙、烧焦、杂质的不良质量问题.4.3.致密度:挤出绝缘层的横断面要致密结实、不准有肉眼可见的针孔,杜绝有气泡的存在。
5.成缆对于多芯的电缆为了保证成型度、减小电缆的外形,一般都需要将其绞合为圆形。
绞合的机理与导体绞制相仿,由于绞制节径较大,大多采用无退扭方式。
成缆的技术要求:一是杜绝异型绝缘线芯翻身而导致电缆的扭弯;二是防止绝缘层被划伤。
大部分电缆在成缆的同时伴随另外两个工序的完成:一个是填充,保证成缆后电缆的圆整和稳定;一个是绑扎,保证缆芯不松散。
6.内护层为了保护绝缘线芯不被铠装所疙伤,需要对绝缘层进行适当的保护,内护层分:挤包内护层(隔离套)和绕包内护层(垫层)。
绕包垫层代替绑扎带与成缆工序同步进行。
7.装铠敷设在地下电缆,工作中可能承受一定的正压力作用,可选择内钢带铠装结构。
电线电缆生产工艺流程
电线电缆生产工艺流程电线电缆是现代电力工业和通信工业的重要组成部分,其生产工艺流程是一个复杂的过程。
下面就来详细介绍一下电线电缆的生产工艺流程。
第一步是原材料的准备。
电线电缆的主要原材料是铜或铝等金属导体,以及绝缘材料、护套材料等。
在生产过程中,首先需要将这些原材料进行筛选、分析和检测,确保其质量和性能符合生产要求。
第二步是导体的制备。
在制备金属导体时,需要将铜(或铝)棒材进行拉拔,以提高其导电性能。
拉拔过程包括铜棒材的预热、拉拔机的操作等。
拉拔后的铜棒材需要经过退火处理,以消除拉丝过程中产生的应力,同时提高导体的软化程度。
第三步是绝缘材料的处理。
绝缘材料主要分为固定绝缘和液态绝缘两种类型。
固定绝缘材料包括聚乙烯、聚氯乙烯等,液态绝缘材料常用的是油浸绝缘。
在生产过程中,需要将绝缘材料加热至一定温度,使其成为熔融状态,然后均匀地包覆在金属导体上。
这个过程需要保证绝缘材料的质量和均匀性,以及绝缘层的厚度和结构等。
第四步是护套的制作。
护套材料通常是由聚氯乙烯或聚乙烯等材料制成的。
护套的制作过程包括熔融成型、挤出、冷却等步骤。
在生产过程中,需要控制护套的厚度、硬度和强度等参数,以保证其对电线电缆的保护作用。
第五步是电线电缆的组装。
在组装过程中,需要将已经制备好的导体、绝缘材料和护套等组合在一起。
这个过程需要注意导体间的接触问题,以及绝缘层和护套的连接问题,确保电线电缆的正常运行和安全使用。
第六步是检测和验收。
在电线电缆生产过程中,需要进行各项性能和质量的检测。
这包括导体的电阻、绝缘层的电阻、外观质量等方面的检测。
通过这些检测,可以评估电线电缆的性能和质量是否符合生产要求。
以上就是电线电缆的生产工艺流程的简要介绍。
电线电缆的生产过程非常复杂,需要采用先进的生产设备和技术,以确保其质量和性能达到要求。
只有在严格控制每个环节的同时,才能生产出高质量的电线电缆产品,满足电力工业和通信工业的需求。
电线电缆的生产流程
电线电缆的生产流程电线电缆的生产流程电线电缆是现代工业中不可或缺的重要产品。
它们广泛应用于建筑、通信、能源传输等领域。
电线电缆的生产流程主要包括原材料准备、导体制造、绝缘层制作、编织、电线电缆成型和测试等环节。
下面将详细介绍电线电缆的生产流程。
首先,电线电缆的生产流程开始于原材料的准备。
常见的导体材料有铜和铝,它们需要经过冶炼、熔化、拉丝等工艺步骤来制备成导线。
而绝缘层通常使用塑料、聚乙烯等材料,这些材料需要经过混炼、挤出等工艺步骤制备成绝缘层。
导体制造是电线电缆生产流程的关键一步。
制造导体的工艺过程常见有拉丝和挤压两种方式。
拉丝是将金属材料经过一系列的拉伸、切割和拉伸等步骤,使其变细,并赋予其所需的导电性能。
挤压则是将金属材料通过挤出机加热到熔化状态,然后通过模具挤出成所需形状的导体。
在导体制造完成之后,需要进行绝缘层的制作。
绝缘层主要是为了避免导体与外界环境接触,起到保护导体的作用。
绝缘层制造通常采用挤出技术。
在挤出过程中,先将塑料颗粒加热到熔化状态,然后通过挤出机将熔融的塑料挤出成所需形状的绝缘层,接着经过切割、调整等工序,使其符合规定要求。
绝缘层制作完成后,还需要进行编织操作。
编织是指在绝缘层外面增加一层编织物,以增强电线电缆的机械强度和抗拉性能。
常见的编织材料有聚酯、尼龙等材料。
编织过程中,先通过特定的机械设备将编织物放置在绝缘层外面,然后通过加压、固定等工艺步骤将编织物与绝缘层相结合。
编织完成后,电线电缆进入成型环节。
成型是指将电线电缆按照设计要求的形状进行整形。
常见的成型方法有挤出和注塑两种。
挤出是将电线电缆通过模具挤压成所需形状,而注塑则是将电线电缆放入注塑机中,经热融、压力等工艺步骤,使其成型。
最后,电线电缆需要进行测试。
测试环节主要用于检测电线电缆的质量,以确保其符合国家标准和设计要求。
常见的测试项目包括导通测试、绝缘测试、耐压测试等。
测试结果将用于判断产品的质量,并进行相关的验收。
电线电缆生产工艺流程
电线电缆生产工艺流程1. 原材料准备电线电缆的生产过程首先需要准备各种原材料,包括金属导体、绝缘材料、护套材料等。
常用的金属导体有铜和铝,绝缘材料常用的有聚乙烯、聚氯乙烯等,护套材料常用的有聚氯乙烯、低烟无卤材料等。
原材料准备工作包括采购、检验、入库等。
2. 金属导体制造2.1 金属材料处理金属导体的制造通常需要对金属材料进行处理,例如铜材料需要进行电解精炼、连铸、轧制等工艺,铝材料需要进行电解精炼、铸造等工艺。
2.2 金属导体加工金属导体加工包括拉丝、绞合等工艺。
首先,将金属材料经过加热处理后进行拉丝,通过不断减小截面积,将金属材料拉制成所需的直径。
然后,将多根金属导体进行绞合,形成导体芯。
3. 绝缘材料制造3.1 绝缘材料生产绝缘材料的制造通常需要将原料进行混合、加热、挤出等工艺。
首先,将绝缘材料的原料按照一定比例进行混合。
然后,将混合后的原料加热熔化,形成熔融状态的绝缘材料。
最后,将熔融的绝缘材料通过挤出机挤出成所需的形状,例如圆形、扁平形等。
3.2 绝缘材料充电处理绝缘材料生产完毕后,需要进行充电处理。
充电处理是为了提高绝缘材料的电气特性,减少绝缘材料的电介质损耗。
充电处理通常采用高压直流电源,将绝缘材料放置在电场中进行处理。
4. 电缆成型4.1 导体编织在电缆成型过程中,需要对金属导体进行编织。
编织的目的是增加导体的柔软性和抗拉强度。
通常采用编织机对金属导体进行编织,形成编织层。
4.2 绝缘层挤出绝缘层挤出是将绝缘材料挤出到金属导体的表面,形成绝缘层。
挤出机将熔融的绝缘材料挤出到金属导体上,并通过冷却使其固化。
4.3 护套层挤出护套层挤出是将护套材料挤出到绝缘层的表面,形成护套层。
挤出机将熔融的护套材料挤出到绝缘层上,并通过冷却使其固化。
5. 电缆测试生产完成的电缆需要进行各种测试以确保质量符合要求。
常见的测试项目包括电气性能测试、物理性能测试、外观检查等。
例如,电气性能测试包括导体电阻测试、绝缘电阻测试、耐压测试等。
- 1、下载文档前请自行甄别文档内容的完整性,平台不提供额外的编辑、内容补充、找答案等附加服务。
- 2、"仅部分预览"的文档,不可在线预览部分如存在完整性等问题,可反馈申请退款(可完整预览的文档不适用该条件!)。
- 3、如文档侵犯您的权益,请联系客服反馈,我们会尽快为您处理(人工客服工作时间:9:00-18:30)。
一、电线电缆产品制造的工艺特性:?
1.大长度连续叠加组合生产方式?
大长度连续叠加组合生产方式,对电线电缆生产的影响是全局性和控制性的,这涉及和影响到:? (1)生产工艺流程和设备布置?
生产车间的各种设备必须按产品要求的工艺流
程合理排放,使各阶段的半成品,顺次流转。
设备配置要考虑生产效率不同而进行生产能力的
平衡,有的设备可能必须配置两台或多台,才能使生产线的生产能力得以平衡。
从而设备的合理选配组合和生产场地的布置,必须根据产品和生产量来平衡综合考虑。
?
(2)生产组织管理?
生产组织管理必须科学合理、周密准确、严格细致,操作者必须一丝不苟地按工艺要求执行,任何一个环节出现问题,都会影响工艺流程的通畅,影响产品的质量和交货。
特别是多芯电缆,某一个线对或基本单元长度短了,或者质量出现问题,则整根电缆就会长度不够,造成报废。
反之,如果某个单元长度过长,则必须锯去造成浪费。
? (3)质量管理?
大长度连续叠加组合的生产方式,使生产过程中任何一个环节、瞬时发生一点问题,就会影响整根电缆质量。
质量缺陷越是发生在内层,而且没有及时发现终止生产,那么造成的损失就越大。
因为电线电缆的生产不同于组装式的产品,可以拆开重装及更换另件;电线电缆的任一部件或工艺过程的质量问题,对这根电缆几乎是无法挽回和弥补的。
事后的处理都是十分消极的,不是锯短就是降级处理,要么报废整条电缆。
它无法拆开重装。
?
电线电缆的质量管理,必须贯串整个生产过程。
质量管理检查部门要对整个生产过程巡回检查、操作人自检、上下工序互检,这是保证产品质量,提高企业经济效益的重要保证和手段。
?
2.生产工艺门类多、物料流量大? 电线电缆制造涉及的工艺门类广泛,从有色金属的熔炼和压力加工,到塑料、橡胶、油漆等化工技术;纤维材料的绕包、编织等的纺织技术,到金属材料的绕包及金属带材的纵包、焊接的金属成形加工工艺等等。
?
电线电缆制造所用的各种材料,不但类别、品种、规格多,而且数量大。
因此,各种材料的用量、备用量、批料周期与批量必须核定。
同时,对废品的分解处理、回收,重复利用及废料处理,作为管理的一个重要内容,做好材料定额管理、重视节约工作。
?
电线电缆生产中,从原材料及各种辅助材料的进出、存储,各工序半成品的流转到产品的存放、出厂,物料流量大,必须合理布局、动态管理。
? 3.专用设备多?
电线电缆制造使用具有本行业工艺特点的专用
生产设备,以适应线缆产品的结构、性能要求,满足大长度连续并尽可能高速生产的要求,从而形成了线缆制造的专用设备系列。
如挤塑机系列、拉线机系列、绞线机系列、绕包机系列等。
?
电线电缆的制造工艺和专用设备的发展密切相关,互相促进。
新工艺要求,促进新专用设备的产生和发展;反过来,新专用设备的开发,又提高促进了新工艺的推广和应用。
如拉丝、退火、挤出串联线;物理发泡生产线等专用设备,促进了电线电缆制造工艺的发展和提高,提高了电缆的产品质量和生产效率。
?
二、电线电缆的主要工艺?
电线电缆是通过:拉制、绞制、包覆三种工艺来制作完成的,型号规格越复杂,重复性越高。
? 1.拉制?
在金属压力加工中.在外力作用下使金属强行通过模具(压轮),金属横截面积被压缩,并获得所要求的横截面积形状和尺寸的技术加工方法称
为金属拉制。
?
拉制工艺分:单丝拉制和绞制拉制。
?
2.绞制?
为了提高电线电缆的柔软度、整体度,让2根以上的单线,按着规定的方向交织在一起称为绞制。
绞制工艺分:导体绞制、成缆、编织、钢丝装铠和缠绕。
?
3.包覆?
根据对电线电缆不同的性能要求,采用专用的设备在导体的外面包覆不同的材料。
包覆工艺分:? A.挤包:橡胶、塑料、铅、铝等材料。
? B.纵包:橡皮、皱纹铝带材料。
?
C.绕包:带状的纸带、云母带、无碱玻璃纤维带、无纺布、塑料带等,线状的棉纱、丝等纤维材料。
?
D.?浸涂:绝缘漆、沥青等?
三、塑料电线电缆制造的基本工艺流程? 1.铜、铝单丝拉制?
电线电缆常用的铜、铝杆材,在常温下,利用拉丝机通过一道或数道拉伸模具的模孔,使其截面减小、长度增加、强度提高。
拉丝是各电线电缆公司的首道工序,拉丝的主要工艺参数是配模技术。
?
2.单丝退火?
铜、铝单丝在加热到一定的温度下,以再结晶的方式来提高单丝的韧性、降低单丝的强度,以符合电线电缆对导电线芯的要求。
退火工序关键是杜绝铜丝的氧化.。
3.导体的绞制?
为了提高电线电缆的柔软度,以便于敷设安装,导电线芯采取多根单丝绞合而成。
从导电线芯的绞合形式上,可分为规则绞合和非规则绞合。
非规则绞合又分为束绞、同心复绞、特殊绞合等。
? 为了减少导线的占用面积、缩小电缆的几何尺寸,在绞合导体的同时采用紧压形式,使普通圆形变异为半圆、扇形、瓦形和紧压的圆形。
此种导体主要应用在电力电缆上。
?
4.绝缘挤出?
塑料电线电缆主要采用挤包实心型绝缘层,塑料绝缘挤出的主要技术要求:? 4.1.偏心度:挤出的绝缘厚度的偏差值是体现挤出工艺水平的重要标志,大多数的产品结构尺寸及其偏差值在标准中均有明确的规定。
? 4.2.光滑度:挤出的绝缘层表面要求光滑,不得出现表面粗糙、烧焦、杂质的不良质量问题? 4.3.致密度:挤出绝缘层的横断面要致密结实、不准有肉眼可见的针孔,杜绝有气泡的存在。
?
5.成缆?
对于多芯的电缆为了保证成型度、减小电缆的外形,一般都需要将其绞合为圆形。
绞合的机理与导体绞制相仿,由于绞制节径较大,大多采用无退扭方式。
成缆的技术要求:一是杜绝异型绝缘线芯翻身而导致电缆的扭弯;二是防止绝缘层被划伤。
?
大部分电缆在成缆的同时伴随另外两个工序的完成:一个是填充,保证成缆后电缆的圆整和稳定;一个是绑扎,保证缆芯不松散。
?
6.内护层?
为了保护绝缘线芯不被铠装所疙伤,需要对绝缘层进行适当的保护,内护层分:挤包内护层(隔离套)和绕包内护层(垫层)。
绕包垫层代替绑扎带与成缆工序同步进行。
?
7.装铠?
敷设在地下电缆,工作中可能承受一定的正压力作用,可选择内钢带铠装结构。
电缆敷设在既有正压力作用又有拉力作用的场合(如水中、垂直竖井或落差较大的土壤中),应选用具有内钢丝铠装的结构型。
?
8.外护套?
外护套是保护电线电缆的绝缘层防止环境因素侵蚀的结构部分。
外护套的主要作用是提高电线电缆的机械强度、防化学腐蚀、防潮、防水浸人、阻止电缆燃烧等能力。
根据对电缆的不同要求利用挤塑机直接挤包塑料护套。
电缆(electric cable;power cable):通常是由几根或几组导线组成。