金属切削的变形过程 (2)
金属切削过程中的三个变形区
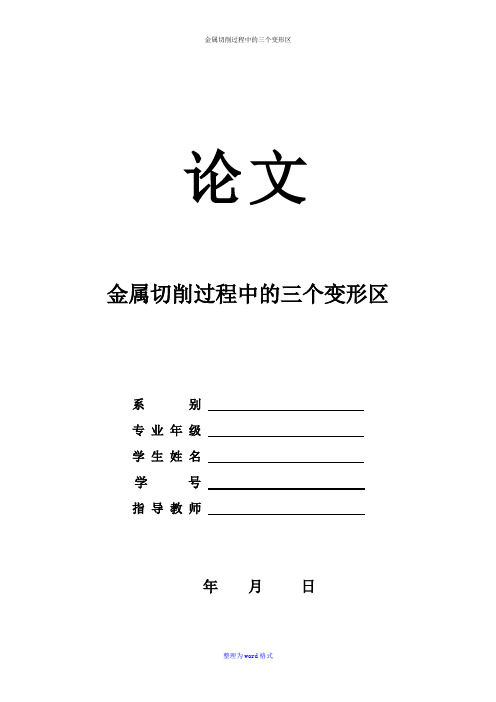
论文金属切削过程中的三个变形区系别专业年级学生姓名学号指导教师年月日金属切削过程中的三个变形区摘要:金属切削过程是指道具与工件相互作用形成切屑的过程,本文主要叙述了金属切削加工过程中的三个变形区的形成及相互联系,并分析了与这三个变形区有关的反映金属变形程度的相关参数,同时加以总结。
关键词:金属切削,三个变形区,金属变形程度Abstract: the process of metal cutting refers to tools and the workpiece interact to form a cutting process, this paper mainly describes the process of metal machining three deformation zone was formed and interconnected, and analyzed and the three deformation zone related to reflect the extent of metal distortion of the relevant parameters, at the same time to sum up.Keywords:metal cutting, three deformation zone, extent of metal distortion引言金属切削过程是机械制造过程的一个重要组成部分。
金属切削过程是指将工件上多余的金属层,通过切削加工被刀具切除而形成切屑并获得几何形状、尺寸精度和表面粗糙度都符合要求的零件的过程。
在这一过程中,始终存在着刀具切削工件和工件材料抵抗切削的矛盾,从而产生一系列现象,如切削变形、切削力、切削热与切削温度以及有关刀具的磨损与刀具寿命、卷屑与断屑等。
对这些现象进行研究,揭示其内在的机理,探索和掌握金属切削过程的基本规律,从而主动地加以有效的控制,对保证加工精度和表面质量,提高切削效率,降低生产成本和劳动强度具有十分重大的意义。
金属切削与刀具3个变形区
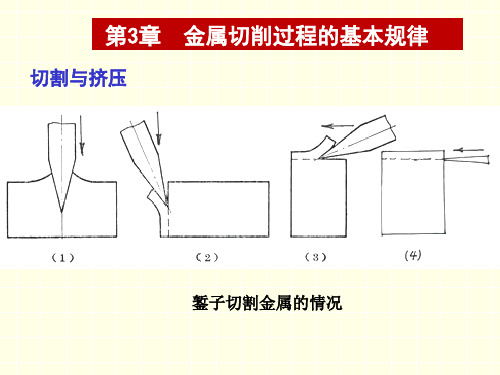
已加工表面的金属纤维被拉伸的又细又长,纤维方向平行 于已加工表面,金属晶粒被破坏,发生了剧烈的塑性变形,产 生加工硬化,表面残余应力,称之为加工变质层。
切屑的类型及控制
从变形观点出发,可将切屑归纳为四种形态:
切塑性材料 带状切屑
↓γ0 ↓v ↑ac ↑γ0↑v↓ac 切削平稳,力波动小 加工面光洁,断屑难
一般 Φ≈π/4 – β+γ0
γ0↑
, Φ↑→
Λh ↓ε↓
刀-屑接触区的变形与摩擦
切屑与前刀面的摩擦
大量实验表明:切屑与前刀面之间的摩擦存在着两种 不同性质的摩擦:粘结摩擦和普通摩擦。且主要的摩 擦形式为粘结摩擦。
Fn Ft
Fn
Fn ( 足 够大 )
F n ( 足 够大 ) Ft
F Ftt
峰点型接 触 (普 通摩擦)
二、变形程度的表示方法
1. 剪切角Φ :剪切面与切削速度方向之间的夹角。 2. 相对滑移ε:滑移距离Δs与单元厚度Δy之比。
ε=Δs/ Δy =NP/MK =(NK+KP)/MK =ctan Φ+ tan(Φ -γ0)
3. 切削厚度压缩比Λh :切屑厚度与切削层厚度的比值。
Λh=cos (Φ -γ0)/ sin Φ
摩擦,产生变形与回弹,造成纤维化和加工硬化。
厚 度 为 Δac 的 一薄层金属被 钝圆刃挤压塑 性变形后成为 已加工表面
ac
Δ ac
第三变形区的金属变形
三个变形区对切削加工的影响
第一变形区的切削变形对刀具产生较大 的切削抗力; 第二变形区主要对刀具产生(粘结)摩 擦阻力以及造成前刀面磨损;
第三变形区主要对工件已加工表面质量 产生重大影响。
第3 章
4技能训练应知篇之金属切削过程及其基本规律

(3)影响积屑瘤形成的因素 1)工件材料塑性大,加工时产生积屑瘤的可能 性大,加工脆性材料时,一般不产生积屑瘤; 2)切削速度过高或过低都不会产生积屑瘤,中 等速度范围内最易产生,如图4-9所示;切削速 度是通过切削热变化来体现 出对积屑瘤形成的影响的; 3)刀具前角大,能减小切 屑变形和切削力,降低切削 温度,能抑制积屑瘤产生或 减小积屑瘤的高度; 4)切削液可减少切削热和 图4-9 切削速度对 改善摩擦,抑制积屑瘤产生。 积屑瘤的影响
四、切削变形程度的衡量
衡量切削变形常用切削变形系数Λh、剪切应变ε 和剪切角 作为衡量切削变形程度的指标。 1.切应变ε(也称剪应变或相对滑移) 它是反映切削变形中金属滑 移本质的系数,切削层中m'n' 线滑移至m"n" 位置时的瞬时 位移为Δy,实际上Δy的值 很小,滑移量为Δs。滑移量 Δs越大,说明变形越严重。 由右图所示几何关系可得出 以下相对滑移关系表达式:
在整个刀-屑接触区内的正应力 分布情况是, 在刀刃处最大,离切削刃越远,前刀面上的 正应力越小,并逐渐减小到零。在前刀面刀 -屑接触区内,各点的正应力和切应力是不 相等的,所以,前刀面上各点的摩擦状态是 不同的,刀-屑摩擦系数也是变化的。且内 摩擦系数远远大于外摩擦系数的值。 一般切削条件下,来自粘结区的摩擦力约占 切削过程中总摩擦力的85%,可见,内摩擦 在刀-屑接触摩擦中起了主要作用,所以, 研究前刀面摩擦时应以内摩擦为主,这也是 切削摩擦不服从古典滑动摩擦法则的原因。
(2)第二变形区(也写成第II变形区) 是指刀-屑接触区域II。切屑沿前刀面流出 时进一步受到前刀面的挤压和摩擦,切屑 卷曲,使朝向前刀面的切屑底层金属呈纤 维化,流线方向基本上和前刀面平行。 (3)第三变形区(也写成第III变形区) 指刀-工接触区域III。已加工表面受到切削 刃钝圆部分与后刀面的挤压和摩擦,产生 径向和切向弹性与塑性变形,造成工件已 加工表层晶粒纤维化与加工硬化。 三个变形区里的切削变形互相牵连,切削变 形是整体行为,是在极短时间内完成的。
机械制造工程原理第二章
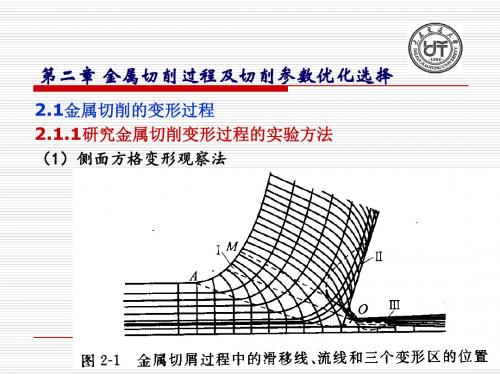
vc
Cv T ma p p f
m m n
kv
2.7 刀具的失效和切削用量的优化选择
2.7.5 切削用量的优化选择
(4)切削速度的选定
2.7 刀具的失效和切削用量的优化选择
2.7.5 切削用量的优化选择
(4)切削速度的选定
2.7 刀具的失效和切削用量的优化选择
2.7.6 刀具合理使用寿命的选择
2.5 切削力
2.5.3切削力的理论公式
Fc
s hDbD cos( o ) sin cos( o )
Fc C Fc a p Fc f Fp C F p a p p f
xF
x
y Fc y Fp yFf
2.5.4 切削力的经验公式(指数形式)F f
CFf a p f f
xF
2.5 切削力
2.5.4 切削力的经验公式(指数形式)
2.5 切削力
2.5.4 切削力的经验公式(单位切削力)
p CFc f 0.16
2.5 切削力
2.5.5 影响切削力的因素
(1) 工件材料的影响(强度、硬度、塑性) (2)切削用量的影响
1)切深和进给量 2)切削速度
2.5 切削力
tw tm tc tot (1)保证加工生产率最高的刀具使用寿命 t t C t m M tct m M m Ct tot M (2)保证加工成本最低的刀具使用寿命
T T
工序成本 切削成本 换刀成本刃磨 刀具消耗费用 辅助时间消耗费用
(3)保证加工利润率最大的刀具使用寿命 Pr
2.1.5剪切角 (1)作用在切屑上的力 (2)剪切角的计算
2.2 切屑的种类及卷屑、断屑机理
第三节金属切削过程中的变形
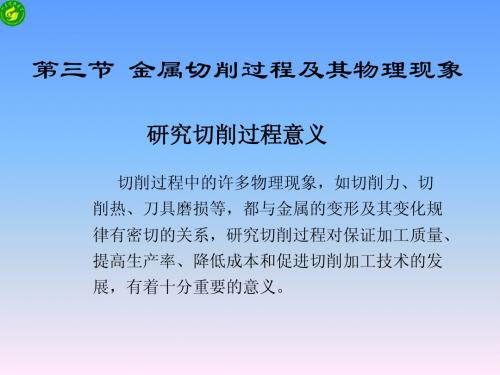
2、第二变形区(纤维化) 第二变形区(纤维化)
(2)剪切角Φ与前刀面上摩擦角β的关系 作用在切屑上的力有 前刀面上的法向力Fn、摩擦力Ff、剪切面上的正压力Fns和剪应力Fs。 简化后作用在切屑上的力 Fr为切削合力、 Φ为剪切角、 β是Fn与Fr之间的夹角摩擦角、Fz是切 削运动方向的分力、和Fy是与运动方向垂直的分力。
a)积屑瘤的形成 切削加工时,切屑与前刀面发生强烈摩擦而形成新鲜表面接触。当接触面具 有适当的温度和较高的压力时就会产生粘结(冷焊)。于是,切屑底层金属 与前刀面冷焊而滞留在前刀面上。连续流动的切屑从粘在刀面的底层上流过 时,在温度、压力适当的情况下,也会被阻滞在底层上。使粘结层逐层在前 一层上积聚,最后长成积屑瘤。 所以积屑瘤的产生以及它的积聚高度与 金属材料的硬化性质有关,也与刃前区 演示1 积屑瘤形成过程 演示2 演示3 的温度和压力分布有关。一般说来,塑 性材料的加工硬化倾向愈强,愈易产生 积屑瘤;温度与压力太低,不会产生积 屑瘤;反之,温度太高,产生弱化作用, 也不会产生积屑瘤。走刀量保持一定时, 积屑瘤高度与切削速度有密切关系。
二、切削层金属的变形
以直角自由切削方式切削塑性材料为基础模型研究切屑形成过程。
大量的实验和理论分析证明,塑性金属切削过程中切 屑的形成过程就是切削层金属的变形过程。
二、切削层金属的变形
1、变形区划分 2、第一变形区(剪切滑移) 第一变形区(剪切滑移) 3、第二变形区(纤维化) 第二变形区(纤维化) 4、第三变形区(纤维化与加工硬化) 第三变形区(纤维化与加工硬化)
1、变形区划分
根据实验,切削层金属在刀具作用下变成切屑的形态大体可划分为三个变形区 第一变形区(剪切滑移) 第二变形区(纤维化) 第三变形区(纤维化与加工硬化)
【机械制造基础课件】2.1切削过程中的变形--切削过程规律
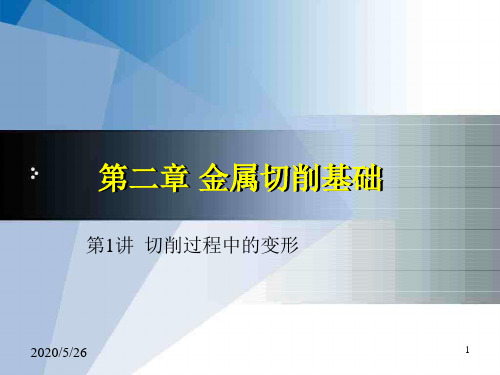
有时也呈纤维化,其方向平行已加工表面,也产生加工硬化 和回弹现象。
三个变形区汇集在切削刃附近,应力集中而又复杂。三个变 形区内的变形又相互影响。
2. 第一变形区内金属的剪切变形
金属在第一变形 区滑移过程
设切削层中某点P 向切削刃逼近, 到1点时切应力 达到材料
剪切屈服强度s( = s),1点向前 移动的同时,也 沿剪切方向滑移, 其合成运动轨迹 从1点运动到2点 而 不 是 2 点 , 22是滑移距离
2.1.3 刀屑接触区的变形与摩擦
根据前述,切屑沿前刀面流出时受到挤压和摩 擦,靠近前刀面的切屑底层进一步变成第二变形 区。
特征:
切屑底层晶粒纤维化,流速减慢甚至会停滞在前刀面上 切屑发生弯曲; 刀—屑接触区温度升高; 第二变形区的挤压和摩擦影响切屑的流出,从而影响第
一变形区金属的变形,影响剪切角的大小。
2.1 金属切削过程中的变形
切屑变形规律是切削过程中诸如切削力、切削热 和切削温度、刀具磨损等规律的重要理论基础。
2.1.1 切屑的种类及变化
金属切削刀具切除工件上的多余金属层,被切离工件的 金属以切屑 (Chip) 形式与工件分离。
由于不同工件材料和切削条件,切屑形态不同,常 见的切屑有四种类型。
偏挤压:金属材料一部分受挤压时 ,OB线以下金属由于母体阻碍,不能 沿AB线滑移,而只能沿OM线滑移.
F
B
O
a)正挤压
45° M A F
BO
b)偏挤压
切削:与偏挤压情况类似。弹性变
M
形→剪切应力增大,达到屈服点→产 生塑性变形,沿OM线滑移→剪切应
O F
பைடு நூலகம்
力与滑移量继续增大,达到断裂强度
切削过程

图1-35 卷屑槽的卷屑机理
15
图1-36
卷屑槽的截面结构
16
图1-37 卷屑槽方向
图1-38 刃倾角对排屑方向的影响
17
图1-39
C形屑折断形式
18
图1-40 精车时的长螺卷屑
19
图1-41 发条状切屑碰到工件切削表面上折断
20
图1-42 C形切屑撞在工件上折断
21
图1-43 切屑碰在后刀面上折断
①脆性刀具材料破损 刀具破损前,刀具切削部分无明显的塑性变形,称为脆性破 损。硬质合金、陶瓷、立方氮化硼和金刚石刀具材料的硬度 高、脆性大常发生脆性破损,一般表现分为以下几种形式: 崩刃、 碎裂、 剥落、热裂。
②塑性刀具材料破损 由于高温高压的作用,刀具会因切削部分发生塑性流动而迅 速失效,称为塑性破损。形式:卷刃(塑性变形使刀具几何 角度)变化)、烧刃(刀具材料金相组织变化)。
22
1.2.3 切削力
(1)切削力的来源
图1-44 切削力的来源
23
(2)切削合力和分力
切削力分解为三个互相垂直的分力: 切削力Fcc——切削合力在主运动方向上的分力, 或称切向分力。 背向力Fp—— 切削合力在垂直于工作平面上的分力, 或称径向力。 进给力Ff—— 切削合力在进给方向上的分力, 或称轴向力。
6
(4)剪切滑移变形的度量 一般采用剪切角φ 、变形系数∧h和剪应变ε 三个参 数来衡量。
图1-22 金属切削层滑移过程示意图
7
变形系数定义为切屑厚度hch与切削层厚度hD之比, 或用切削层长度lc与切屑长度lch之比。
图1-23 变形系数Λ h的计算参数
8
剪应变也称相对滑移,ε =NP/MK 。
第2章 金属切削过程
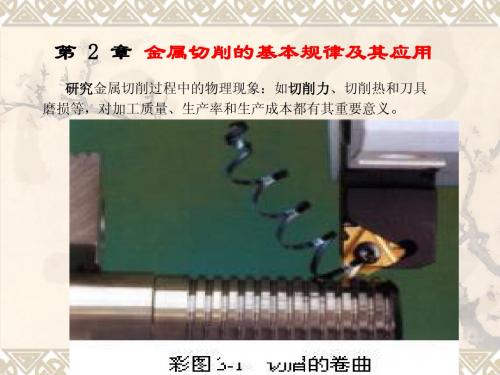
⑶主偏角 主偏角κ r 对主切削力影响不大,对吃刀抗力和进给抗 力影响显著( κr ↑—— Fp↓,Ff↑)
切削力/ N
2200
1800
1400 1000
κr - Fc
κr – Ff κr – Fp
FC—— 切削力(Fz) Ff—— 进给力(Fx) FP—— 背向力(Fy)
600 200 30 45 60
进给力Fx (Ff)
也称轴向分力,用Fx表示—总切削力在进给方 向的分力,是设计机床进给机构不可缺少的参数。 背向力 Fy(Fp) 也称径向分力,用Fy表示 —总切削力在垂直于
工作平面方向的分力,是进行加工精度分析、计算
系统刚度,分析工艺系统振动所必须的参数。
三个分力FC、Ff、FP与合力F 合力F =
2、切削温度的分布
★ 切削塑性材料 :
前刀面靠近刀尖处温度最高。
★ 切削脆性材料: 后刀面靠近刀尖处温度最高
750 ℃
刀 具
2.3.3 影响切削温度的主要因素
1.切削用量对刀具温度的影响
切削温度与切削用量的关系式为:
θ = Cθ VcZθ fyθ apxθ 三个影响指数 zθ >yθ >xθ ,说明切削速度对切削 温度的影响最大,背吃刀量对切削温度的影响最小。
C区是刀尖区,由于散热差,强度低,磨损 严重,磨损带最大宽度用VC表示 B区处于磨损带中间,磨损均匀,最大磨损 量VBmax;
3.边界磨损
N区处于切削刃与待加工表面的相交处,磨 损严重,磨损量以VN表示,此区域的 磨损也叫边界磨损
2.4.2 刀具磨损的主要原因
1. 硬质点磨损
工件材料中含有硬质点杂质,在加工过程中会将刀具表面划伤, 造成机械磨损。低速刀具磨损的主要原因是硬质点磨损。
- 1、下载文档前请自行甄别文档内容的完整性,平台不提供额外的编辑、内容补充、找答案等附加服务。
- 2、"仅部分预览"的文档,不可在线预览部分如存在完整性等问题,可反馈申请退款(可完整预览的文档不适用该条件!)。
- 3、如文档侵犯您的权益,请联系客服反馈,我们会尽快为您处理(人工客服工作时间:9:00-18:30)。
• 剪切角可采用快速落刀实验获得切屑 根部照片再测量得到,比较麻烦。
o
可编辑ppt
15
2、剪应变
• 平行四边形OHNM剪切变形为OGPM,按剪应变即相对滑移
关系有
• = s / y, 而 s = NP,y = MK 故
• =NP / MK = (NK+KP) / MK = ctg + tg(-0)
Ⅱ Ⅰ
Ⅲ
➢ 第Ⅱ变形区:靠近前刀面处 图 切削部位三个变形区 ,切屑排出时受前刀面挤压与 摩擦。此变形区的变形是造成前刀面磨损和产生积屑瘤的 主要原因。
➢ 第Ⅲ变形区:已加工面受到后刀面挤压与摩擦,产生变 形。此区变形是造成已加工面加工硬化和残余应力的主要 原因。
可编辑ppt
4
第Ⅰ变形区:
➢从OA线(始滑移线)金属开始发生剪切变形,到 OM线(终滑移线)金属晶粒剪切滑移基本结束, AOM区域叫第一变形区。
晶粒滑移示意图
可编辑ppt
滑移与晶粒伸长
12
• 卡片模型
• 切削层金属就象一摞卡片,在刀具作用下受剪应力后沿卡 片间滑移而成为切屑。滑移方向就是剪切面方向。
卡可片编模辑p型pt
13
三、变形程度的表示方法
剪切角 剪应变 变切削条件下,剪切角越大,剪切 面积越小,切屑厚度越小,变形越小。
➢变形系数能直观反映切屑的变形程度,且容易求得,生产中常用。
变形系数可求编法辑ppt
17
变形系数、剪切角和剪应变的关系
achcos(o)
ac
sin
2
2sino
1
coso
以上是按纯剪切观点提出的,而切削过程是复杂的,既
有剪切又有挤压和摩擦的作用。显然以上理论有局限性。
如=1时,ach=ac,似乎切屑没有变形,但事实上切屑有
相对滑移存在。也只当ξ>1.5时, ξ与ε基本成正比。
可编辑ppt
18
第三节 前刀面的挤压与磨擦及其对切屑变形的影响
coso sinΦcosΦ(o)
可编辑ppt
16
剪切变形示意图
3、变形系数
➢由实验和生产可知,切屑厚度 ach 大于切削层厚度ac,切屑长度 lch 小于 切削层长度 lc。 ➢长度变形系数L切削层长度lc与切屑长度lch之比L= lc/lch ➢ 厚度变形系数 a = ach/ ac ➢忽略切屑宽度的变化,有a=L= ➢ 大于1,值大表示切屑越厚越短,变形越大
➢特征是晶粒剪切滑移剧烈呈纤维化,纤维化方向平行前 刀面,有时有滞流层。
➢切屑与前刀面的压力很大,高达2~3GPa,由此摩擦象。
可编辑ppt
6
第Ⅲ变形区:
➢刀工接触区。
➢已加工表面受到刀具刃口钝圆和后刀面挤压和摩擦,晶 粒进一步剪切滑移。
第三章 金属切削的变形过程
第一节 研究金属切削变形过程的意义和方法
一、研究金属切削变形过程的意义
• 金属切削过程是指:通过切削运动,使刀具从工件上切下 多余的金属层,形成切屑和已加工表面的过程。即被加工 工件的切削层在刀具前面推挤下产生塑性变形,形成切屑 而被切下来的过程。
• 在这过程中产生一系列现象,如形成切屑、切削力、切削 热与切削温度、刀具磨损等,它们产生的根本原因是切削 过程中的弹性变形和塑性变形
切削层金属
1
2(3)
4
= s 合成运动
> s 合成运动
> s 合成运动
第一变形区
可编辑ppt
4以后 无剪应力 前刀面
切屑
9
❖ 金属在第一变形区滑移过程 切削层金属是在AOM区内通过剪应力产生滑移
变成切屑 (Chip) 的。 AOM区叫做第一变形区。 OA线叫始滑移线,OM线叫终滑移线。 其特征是晶粒的剪切滑移,伴随产生加工硬化。
可编辑ppt
10
晶粒滑移:切削层金属的变形,从晶体结构看,就是沿晶 格中晶面的滑移。
在一般速度范围内,第一变形区宽度仅0.20.02mm,
所以可看成一个面—即剪切面。
剪切面与切削速度之夹角 叫剪切角,以表示。
剪 切 面 切屑
c
刀具
可编辑ppt
11
假定金属晶粒为圆形,受剪应力后晶格中晶面滑移,粒变 椭圆形,AB变为长轴AB;随剪应力增大,晶格纤维化, AB成为纤维化方向 。但纤维化方向与晶粒滑移方向不一致 ,它们成一角。
• 金属切削变形过程的研究是金属切削原理的基础理论研究。
是适应生产发展的需要,有助于保证加工质量,提高生产
率和降低成本。
可编辑ppt
1
二、研究切削变形的实验方法
侧面变形观察法
高速摄影法
快速落刀法
SEM观察法
光弹性、光塑性实验法
其它方法,如:X射线衍射等
可编辑ppt
2
第二节 金属切削层的变形
一、 变形区的划分
• 金属在加工过程中会发生剪切和滑移,下图表示了金属的 滑移线和流动轨迹,其中横向线是金属流动轨迹线,纵向 线是金属的剪切滑移线。可划分为三个变形区
金属切削过程中滑可移编辑线p和pt 流线示意图
3
三个变形区
➢ 第Ⅰ变形区:即剪切变形 区,金属剪切滑移,成为切屑 。金属切削过程的塑性变形主 要集中于此区域。
➢有时也呈纤维化,其方向平行已加工表面,也产生加工 硬化和回弹现象。
➢三个变形区汇集在切削刃附近,应力集中而又复杂。三 个变形区内的变形又相互影响。
可编辑ppt
7
二、第一变形区内金属的剪切变形
设切削层中某点P向切削刃逼近,到1点时切应力达到材料 剪切屈服强度s( = s),1点向前移动的同时,也沿剪 切方向滑移,其合成运动轨迹从1点运动到2点而不是2点, 22是滑移距离
➢是切屑变形的基本区,其特征是晶粒的剪切滑移 ,伴随产生加工硬化。
第一变形区是金属切削变形过程中 最大的变形区,在这个区域内,金 属将产生大量的切削热,并消耗大 部分功率。此区域较窄,宽度仅 0.02~0.2㎜ 。
可编辑ppt
5
第Ⅱ变形区:
➢刀屑接触区
➢切屑沿前刀面流出时受到挤压和摩擦,使靠近前刀面的 晶粒进一步剪切滑移。
P点继续逼近刀刃,由于
硬化现象,剪应力增大,
因 此 P 点 经 过 1—2—3—
4,到达4点时剪切滑移
结束,沿平行前刀面方向
流出成为切屑。
可编辑ppt
8
R2 R1
ac
= m ax
l
f
45° M
45° 45° 45°
4
A P
B 1
3 4' 2 3'
c
= 2' s
O
位置 应力状态 流动方向
区域
P < s 切削速度v