三相炼钢电弧炉
电弧炉炼钢课件PPT

五、电炉工艺流程图
第一章.电弧炉的电器设备 §1—1 电弧概念与交流电弧特性
一.电弧基础 电弧炉热源—电弧:决定炉内热工状况和 设备的电器特性。
1.电弧是一种气体放电现象。在两电极间加 上一定的电压,就能自行放电。放电时两 电极间的气体被电离,出现大量带电质 点—自由电子和正离子,电极间出现导电 通道,电流密度达KA∕cm2,气体达几千摄 氏度。
⑶ 石墨的电阻系数和温度变动的相依关系较复杂。 在1400℃下的电阻系数和室温下的相同,而金属 的电阻系数却总是随温度升高而增大的。
⑷ 石墨的导热性能好而热膨胀系数较低,使石墨抗 热震性能较好,降低了电极中的热应力。
⑸ 在石墨表面温度大于400℃后会和氧气结合。氧 化量与气体中的氧含量、气体流速和暴露时间有 关。在温度大于600℃后,氧化过程激烈。
主要内容
❖ 电炉炼钢及其发展 ❖ 电弧炉的电器设备 ❖ 电弧炉炉体构造与炉衬 ❖ 电弧炉炼钢原材料 ❖ 碱性电弧炉冶炼工艺 ❖ 超高功率电弧炉和直流电弧炉 ❖ 典型钢种冶炼 ❖ 电炉新技术、新工艺
绪论:电弧炉炼钢及其发展
一、电弧炉
目前,世界上电炉钢产量的95%以上都是由电弧炉生 产的,因此电炉炼钢主要指电弧炉。
P1—单位时间的热损失,即熔化期内的平均电能损失。 采用钢渣混出的方法,或先出大部分渣再出钢。
(FeO)+ Ca = (CaO) + [Fe]
二.装料 由炉底、炉壁和炉盖三部分组成。
5~4ml∕100g,氮降低到0. (2)停泵、破空,软吹氩大于3分钟;
1.装料前的炉料计算 由于自动功率调节器的作用,电极始终要与炉料保持一定距离,所以电极随着炉料的熔化而不断下降。
⑵ 当有炉渣形成后,电弧增长并变得稳定些,电弧 被炉渣包围的部分越大时,电弧电压和电流的波 形越接近于正弦形。
电弧炉炼钢概述

电弧炉炼钢冶金备件概述通常所说的电炉炼钢是指电弧炉(EAF: Electric Arc Furnace)炼钢,特别是碱性电弧炉炼钢(炉衬用碱性镁质耐火材料),电弧炉是采用电能作为热源进行炼钢。
传统电弧炉炼钢原料以冷废钢为主,配加10%左右的生铁。
冶金备件现代电弧炉炼钢除废钢和冷生铁外,使用的原料还有直接还原铁(DRI, HBI)、铁水、碳化铁等。
按电流特性,电弧炉可分为交流和直流电弧炉。
交流电弧炉以三相交流电作电源,利用电流通过3根石墨电极与金属料之间产生电弧的高温来加热、熔化炉料。
冶金备件直流电弧炉是将高压交流电经变压、整流后转变成稳定的直流电作电源,采用单根顶电极和炉底底电极。
通常用电弧炉的额定容量、公称容量来表示电弧炉的大小。
冶金备件一般认为,电弧炉的公称容最(炉壳直径)40t (4. 6m)以下的为小电炉,50t (5.2m)以上的为大电炉。
1981年,国际钢铁协会提议按电弧炉的额定功率分类电弧炉。
对于50t以上的电弧炉分类: 额定功率100~ 200kV •A/t为低功率电弧炉、200 ~ 400kV •A/t为中等功率、400 ~ 700kV . A/t 为高功率、700 ~ lOOOkV . A/t为超高功率(UHP: Ultra High Power)电弧炉。
对于UHP技术,近年来有炉子容量趋大、功率水平提高的趋势,国外个别电弧炉的功率水平巳超过lOOOkV •A/t, 将其称为超超髙功率(SUHP)电弧炉。
交流电弧炉超髙功率化后可加速废钢熔化,缩短熔化时间,改善热效率和总效率。
但随着电炉功率越来越髙,同时也出现了电弧稳定性差、电源闪烁、炉壁热点等问题,从而使直流电弧炉得到了发展。
冶金备件直流电弧炉比交流电弧炉的单位电耗、电极单耗和耐火材料单耗都低,并且直流电弧炉不存在“冷点”问题。
冶金备件20世纪90年代是直流电弧炉的年代,全世界已经投产和正在建设的50t以上直流电弧炉已超过100台。
电弧炉炼钢发展历史及前景1

绪论 电炉炼钢及其发展
电炉是采用电能作为热源进行炼钢的炉子的统 称。 按电能转换热能方式的差异,电炉可分为: 电渣重熔炉—利用电阻热; 感应熔炼炉—利用电磁感应; 电 子 束 炉—依靠电子碰撞; 等 离 子 炉—利用等离子弧; 电 弧 炉—利用高温电弧,不包括加热炉、热 处理炉等。
电炉流程与转炉流程比较,具有以下特点:
①电炉流程投资省,占地面积小,建设周期 短; ②资源问题:随着国民经济的发展,铁矿石、 焦煤等资源将日益匮乏,而废钢资源则会不 断积累,因此从长远看电炉流程具有优势; ③环保问题:电炉流程产生的CO2、NOx、 SOx等有害气体量较高炉-转炉流程少;
三. 电炉炼钢的优势
目前我国高附加值优质产品,也就是能盈利的 电炉钢品种包括: a)转炉流程不适合生产的高合金钢、高温合 金、大型铸锻件用钢; b)转炉流程能够生产但目前在国内产量还是 不大的一些合金钢钟,如轴承钢、齿轮钢、弹 簧钢等; c)过去仅能用转炉流程生产的、现代电炉流 程也能生产的一些品种,如高附加值的板材 (薄板、中板、厚板); d)优质碳素钢(特别是中、高碳钢)和低合 金钢(包括使用量很大的螺纹钢)。
世界粗钢总量与电炉钢产量
时间 总钢产/ 亿吨 电炉钢比 /%
197 0 6.0 14.2
198 0 7.16 22.0
199 0 7.7 27.5
200 0 8.47 33.8
200 2 9.03 34.5
200 3 9.63 35
200 4 10.6 36
即2000前一直在7.0~8.5亿间徘徊, 2002、2004 年才分别突破9、10亿吨,2005年达到11.07亿吨。
由钢产量与产品结构变化看电炉发展
叙述酸性三相电弧炉的熔炼过程

叙述酸性三相电弧炉的熔炼过程酸性三相电弧炉是一种用于熔炼金属的高温设备,其工作原理是将电能转化为热能,通过电弧的高温使金属材料熔化。
下面是酸性三相电弧炉的熔炼过程的详细叙述。
首先,将待熔金属材料放入电弧炉中,可以是废旧钢铁、废钢杂铁、再生资源和一些合金材料等。
然后,炉门关闭,并且加入适量的炉渣,炉渣主要由石灰、萤石和氧化铁等成分组成,目的是吸收金属中的非金属杂质。
接下来,开始通电。
电流通过电极流过材料,产生强大的电弧,从而产生高温。
在熔炼过程中,电弧产生的温度可以达到数千摄氏度,足以将金属材料熔化。
炉渣在高温下开始融化,并慢慢吸附杂质。
同时,由于电弧的高温作用,金属材料也开始熔化,变成液态。
在炉内,金属材料被搅拌均匀,以提高熔炼效果。
熔化的金属下沉到炉底,形成金属池。
然后,通过倒钢装置,将熔化的金属顺利倾倒到后续工序中,用于制造新的金属制品。
在熔炼过程中,炉膛内的温度和压力都会受到严格控制。
通过监测炉内的温度和电弧的强度,可以确保炉内的温度适宜,熔炼效果良好。
熔炼结束后,电弧炉停止通电。
金属池中残留的炉渣被排出,为下次熔炼做好准备。
炉体冷却之后,可以开启炉门,取出熔炼完成的金属。
酸性三相电弧炉的熔炼过程具有以下优点:能耗低、产能高、炉渣质量好、操作简单、适用于各种金属材料的熔炼等。
总结起来,酸性三相电弧炉通过电弧高温将金属材料熔化,并通过适当的炉渣控制来去除其中的杂质。
通过精确的温度和电弧强度控制,可以确保金属材料完全熔化,并在炉底形成金属池,方便后续处理。
这种熔炼过程在金属工业中得到广泛应用,为金属制品的生产提供了重要的原材料。
电弧炉冶炼的基本原理

电弧炉冶炼在钢铁工业中的应用
钢的熔炼与精炼
电弧炉是钢铁工业中用于熔炼和精炼钢的主要设备,通过电弧的高温将铁矿石、 废钢铁等原料熔化为钢液,并进行脱硫、脱磷等精炼处理。
特殊钢生产
电弧炉在特殊钢生产中具有重要作用,可以生产高合金钢、不锈钢等高品质特殊 钢材,满足汽车、航空航天、石油化工等领域的需求。
电弧炉冶炼在其他领域的应用
03 电弧炉冶炼工艺
电弧炉冶炼的原料和配料
原料
电弧炉冶炼的原料主要包括废钢铁、生铁、直接还原铁、合 金元素等。这些原料需要根据不同的冶炼需求进行配比,以 满足产品成分的要求。
配料
配料是电弧炉冶炼的关键环节,需要根据所炼钢种的成分要 求,精确计算各种原料的加入量,以确保最终产品的质量。
电弧炉冶炼的操作工艺流程
还原
在氧化结束后,通过加入还原剂(如硅铁 、锰铁等),对钢液进行还原,以调整其 成分。
电弧炉冶炼的工艺参数控制
温度控制
电弧炉冶炼过程中,温度是非常关键的参数。通过对电弧 电流、电压的控制,以及向炉内吹入氧气的量等手段,实 现对温度的精确控制。
成分控制
根据所炼钢种的成分要求,通过精确计算和控制各种原料 的加入量,以及加入合金元素的种类和数量,实现对钢液 成分的精确控制。
属的纯度和质量。
电弧炉冶炼与其他冶炼方法的比较
01
02
03
氧气转炉法
电弧炉冶炼与氧气转炉法 相比,具有熔化率高、生 产效率高、能耗低等优点 ,但成本较高。
感应炉法
电弧炉冶炼与感应炉法相 比,具有熔化速度快、熔 体成分均匀、能耗低等优 点,但设备投资较大。
真空熔炼法
电弧炉冶炼与真空熔炼法 相比,具有熔化速度快、 熔体纯净度高、能耗低等 优点,但生产效率较低。
电弧炉炼钢
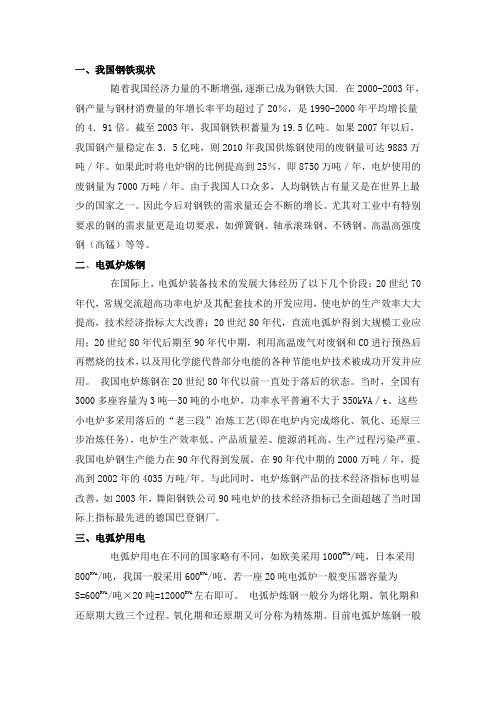
一、我国钢铁现状随着我国经济力量的不断增强,逐渐已成为钢铁大国. 在2000-2003年,钢产量与钢材消费量的年增长率平均超过了20%,是1990-2000年平均增长量的4.91倍。
截至2003年,我国钢铁积蓄量为19.5亿吨。
如果2007年以后,我国钢产量稳定在3.5亿吨,则2010年我国供炼钢使用的废钢量可达9883万吨/年。
如果此时将电炉钢的比例提高到25%,即8750万吨/年,电炉使用的废钢量为7000万吨/年。
由于我国人口众多,人均钢铁占有量又是在世界上最少的国家之一。
因此今后对钢铁的需求量还会不断的增长。
尤其对工业中有特别要求的钢的需求量更是迫切要求,如弹簧钢、轴承滚珠钢、不锈钢、高温高强度钢(高锰)等等。
二、电弧炉炼钢在国际上,电弧炉装备技术的发展大体经历了以下几个价段:20世纪70年代,常规交流超高功率电炉及其配套技术的开发应用,使电炉的生产效率大大提高,技术经济指标大大改善;20世纪80年代,直流电弧炉得到大规模工业应用;20世纪80年代后期至90年代中期,利用高温废气对废钢和CO进行预热后再燃烧的技术,以及用化学能代替部分电能的各种节能电炉技术被成功开发并应用。
我国电炉炼钢在20世纪80年代以前一直处于落后的状态。
当时,全国有3000多座容量为3吨—30吨的小电炉,功率水平普遍不大于350kVA/t。
这些小电炉多采用落后的“老三段”冶炼工艺(即在电炉内完成熔化、氧化、还原三步冶炼任务),电炉生产效率低、产品质量差、能源消耗高、生产过程污染严重。
我国电炉钢生产能力在90年代得到发展,在90年代中期的2000万吨/年,提高到2002年的4035万吨/年。
与此同时,电炉炼钢产品的技术经济指标也明显改善,如2003年,舞阳钢铁公司90吨电炉的技术经济指标已全面超越了当时国际上指标最先进的德国巴登钢厂。
三、电弧炉用电电弧炉用电在不同的国家略有不同,如欧美采用1000KVA/吨,日本采用800KVA/吨,我国一般采用600KVA/吨。
铸造合金及其熔炼 第九章 电弧炉炼钢

为了促使脱碳反应进行,需要创造一定的温度条件。 在较低的钢液温度下,碳被氧化得少,铁被氧化得多,而 在较高的温度下,碳被氧化得多,铁被氧化得少。这种变 化是由于碳-氧亲和力与铁-氧亲和力随着温度的变化而改 变的结果。图9-8是碳的氧化反应和铁的氧化反应的生成 自由能图。由图可见,当温度超过一定值(1000℃)以后, 碳-氧的亲和力就超过铁-氧的亲和力。因此,在炼钢生产 上规定,在氧化期中,只有在钢液温度超过一定的温度 (热电偶温度为1530℃)时,才可以吹氧和加矿石脱碳。
5、还原期 、 还原期的任务是脱氧、脱硫和调整钢液温度及化学成 分。 扒除氧化渣后,首先往熔池中加入锰铁进行预脱氧。 通过预脱氧可以快速除去钢液中的部分氧化亚铁。这样就 能减轻后来通过炉渣进行脱氧的任务,加速整个还原期的 过程。 在还原的过程中进行钢液的脱氧和脱硫。脱氧和脱硫 是同时进行的。还原渣有两种:白渣和电石渣。 白渣:石灰、氟石、碳粉 电石渣:石灰、氟石、碳粉
1)炉渣的碱度和氧化性 ) 为了促使脱磷反应进行,应造高碱度和强氧化性的 炉渣。图9-5表明炉遭碱度和渣中FeO含量对磷在炉渣中和 钢液中的分配比值的影响。分配比值愈高,表明钢液中的 磷转移到炉渣中去的愈多,即脱磷效果愈好。由图可见, 随着炉渣碱度和氧化亚铁含量的提高 ,磷的分配比值也 增大,但是当碱度超过3. 0以上时,进一步提高碱度并不 能将磷的分配比提得更高。实际上。炉渣碱度太高时,使 得炉渣的粘度增大,反而会使脱磷效果降低。
4、电极升降机构 、
在炼钢过程中,为了使电极能灵敏地、频繁地上下 运动,以便随时调节通过电极的电流,达到稳定电弧的目 的。对电极的升降是实现自动控制的;由自动控制电器系 统操纵液压阀,以驱动使电极升降的液压缸,从而使电极 作向上或向下运动。
三相电弧炉炼钢操作规程

三相电弧炉炼钢操作规程总则1. 本规程适用于5吨和15吨碱性三相电弧炼钢炉(以下简称电炉)的炼钢操作。
2.规程是生产技术领域中的法规,是实际操作的重要依据,是确保产品质量的主要技术文件,务必融会贯通,严格执行。
3.为确保正常炼钢和钢液质量,冶炼前必须对炉衬、炉盖、出钢槽、盛钢桶进行例行检查。
在下述情况下,不得冶炼锻制钢锭、电工纯铁、高合金钢、高强度和超高强度级别、三级以上探伤要求、对气体、夹杂有严格要求以及有其它特殊要求的钢种;3.1大修炉后的前5炉,中修炉后的前3炉;3.2 冷停炉超过24小时后的第一炉,有特殊要求的前2炉;3.3炉衬损坏严重、接近中修或炉坡、渣线修补面积超过1/5时;3.4新出钢槽第一次使用或出钢槽修补面积大于1/3时;3.5 新砌的盛钢桶、长期没有使用的旧盛钢桶、修补量较大的旧盛钢桶第一次使用。
4.冶炼高合金钢和一些有特殊要求的钢种时,要考虑该炉前1~2炉钢液成分对本炉的影响,同时也要考虑冶炼高合金钢后,对下炉化学成分的影响。
如有不良影响,要与相关部门联系修改计划。
5.送电前应仔细检查水冷、机电、风动、液压和测温系统等是否正常。
易脱落的电极及接头及时处理。
6. 出钢后,炉底原则上不允许有残留钢液。
7. 凡跟钢、渣接触的工具都应干净、干燥。
操作平车、平台干净,电炉周围场地干净、干燥、整齐、道路畅通。
通用规程氧化法冶炼1. 原、辅材料及配件1.1 所用原材料必须符合“炼钢原材料及辅助材料技术条件”严禁有毒、有害、易燃、易爆物以及对钢液质量有害的金属和非金属进入炉内。
1.2应根据所炼钢种冶炼方法、原材料成份、前炉钢对本炉钢的影响、冷停炉时间长短的影响、吹氧助熔的需要、计划钢产量等进行仔细计算,拟制配料单,配碳量应保证全熔化后氧化沸腾脱碳的需要,生铁配入量不得超过炉料重的15%,不足之碳量可配入电极块或冶金焦碳补足。
1.3所配炉料大小块度应合适,配比为:大块料20~40%,中块料30~40%,小块料(包括钢屑)30~50%。
- 1、下载文档前请自行甄别文档内容的完整性,平台不提供额外的编辑、内容补充、找答案等附加服务。
- 2、"仅部分预览"的文档,不可在线预览部分如存在完整性等问题,可反馈申请退款(可完整预览的文档不适用该条件!)。
- 3、如文档侵犯您的权益,请联系客服反馈,我们会尽快为您处理(人工客服工作时间:9:00-18:30)。
520
10
5000
300
7.50
550
7.80
530
6000
9.00
520
9.40
510
根据电弧炉功率水平的高低,将电弧炉划分为:(低功率、中等功率)普通功率(RP)、高功率(HP)、超高功率(UHP)电弧炉。电弧炉功率水平用变压器的额定容量(kV‧A)与电炉公称容量(t)或实际出钢量(t)之比来表示。
1981年,国际钢铁协会建议的电炉分类标准(大于50t电炉)
低功率电炉100~200 kV‧A/t
中等功率电炉200~400 kV‧A/t
高功率电炉400~700 kV‧A/t
超高功率电炉700~1000 kV‧A/t
-出处:电炉炼钢新工艺新技术与质量控制实用手册
三相炼钢电弧炉
型号
炉壳内径
(mm)
额定容量
(t)
变压器容量
(kvA)
变压器二次电压
设备总重
(t)
HX-1.5
2100
1.5
1250
210-104
16.6
2200
HX-3
2500
3
2200
220-110
37
2700
Hx-5
3000
5
3200
240-121
66
3240
HX-8
3400
8
3200
240-121
额定功率
KW
中频频率
Hz
熔炼铸钢1600℃
熔炼铸铁1450℃
熔化率
t/h
单位电耗kw.h/t
熔化率
t/h
单位电耗kw.h/t
1
500
1000
500
0.76
789
0.79
750
800
1.20
640
1.23
610
1.5
750
1000
500
1.10
650
1.13
620
1000
1.50
600
1.60
575
2
70
HX-10
3500
10
5500
260-139
91
8000
HX-15
3800
15
6300
260-139
95
10000
280-100
HX-20
4200
20
9000
280-100
1
92
10000
4600
30
16000
353-137
243
18000
22000
480-230
1100
0.70
1.2
500
500
1250
1.00
1100
1.40
1.8
800
500
1250
1.80
1100
2.50
2.4
1000
500
1250
2.20
1100
3.00
3.6
1500
500
1250
3.30
1100
4.60
5.0
2000
500
1250
4.50
1100
6.30
大中容量钢壳熔化炉
额定容量
t
25000
436-184
HX-40
4700
40
16000
353-137
245
5000
31500
489-201
中频铜熔化炉
额定容量
t
额定功率
KW
中频频率
Hz
熔炼紫铜
熔炼黄铜
工作温度
℃
熔化率
t/h
工作温度
℃
熔化率
t/h
0.3
160
1000
1250
0.30
1100
0.40
0.6
250
1000
1250
0.50
1000
500
1.40
610
1.50
585
1200
1.70
570
1.80
560
3
1500
500
2.40
640
2.50
610
1800
2.80
610
2.90
590
5
2000
500
3.00
585
3.10
560
3000
4.50
560
4.70
54
7
3500
500
5.30
550
5.50
530
4000
6.00
540