环锭细纱机纺纱过程假捻技术的发展历史与现状-FZQC
环锭细纱机的技术进步

环锭细纱机的技术进步内容摘要:当代环锭细纱机在牵伸加压形式、卷捻技术、传动方式、长车和细络联以及紧密纺纱技术等有了很大的发展,已形成了高科技的环锭纺纱机。
本文对上述几个方面进行了详细的讨论。
关键词伸形式钢领钢丝圈高速锭子变频调速紧密纺纱技术目前全世界约有1.7亿枚棉纺环锭细纱机,800万头转杯纺,其它新型纺纱如喷气纺、涡流纺等容量很少。
但转杯纱产量占全部纱线市场的42%,环锭纱占56%,其它如喷气纺占2%。
环锭纺是传统纺纱方法,工艺技术十分成熟,是纺纱生产中占比例最大、又十分重要的纺纱方式。
新型纺纱技术虽然生产效率高、工艺流程短,品种、纱支适应性好,但成纱结构及性能不如环锭纱,所以在相当长的时期内不可能完全取代环锭纱,因此,环锭纺仍然是现代纺纱生产中最主要的纺纱方式。
在20世纪后半期,环锭纺纱技术有很大进步,细纱机锭速达到25000转/分,一台细纱机锭数已发展到1400锭,牵伸倍数230倍左右,在牵伸形式、加压、锭子、钢领钢丝圈、吸棉、纱管、胶辊、胶圈、传动技术等方面都有了很大发展,在细纱与自动络纱联合技术上也有了新的突破,有不少机型都形成了细络联。
代表国际先进水平的机型有瑞士立达公司、德国绪森公司、意大利马佐里公司及以德国青泽公司生产的各种新型环锭细纱机,在高速、高效、节能、机电一体化及自动控制自动化方面都已达到很高水平。
1999年巴黎展览会上,瑞士立达、德国绪森等公司展出了紧密纺环锭细纱机,这是环锭纺纱技术新的突破,紧密环锭纺纱技术是在细纱牵伸区以外,增加了凝聚细纱须条的机构,消除了加捻三角区,成纱质量更为优越:减少了细纱毛羽,提高细纱强力,改善了细纱条干,为下游工序提高织物质量,减少上浆负担、取消烧毛等创造了条件,与此同时,细纱制成率提高,飞花减少,对提高经济效益及改善生产环境都有明显作用。
我国FA500系列环锭细纱机,在贯彻重加压,强控制、大牵伸的工艺路线上,吸收了国外先进环锭细纱机的经验及特点,结合我国国情进行较大改进,结构比较合理,制造精度有所提高,设备运转可靠性、稳定性也有进一步提高,适纺性能强,纺纱质量进一步提高。
环锭细纱机的现状和发展趋向

环锭细纱机的现状和发展趋向赵伟【摘要】介绍了我国细纱机的发展历程,详述了细纱机在机架的长向桥接技术、牵伸系统、加捻卷绕系统和升降系统等方面进行的高速化、自动化及节能降耗技术改进,展望了环锭细纱机今后的发展方向.【期刊名称】《纺织科技进展》【年(卷),期】2017(000)012【总页数】3页(P30-31,41)【关键词】环锭细纱机;技术改进;节能降耗;发展方向【作者】赵伟【作者单位】陕西工业职业技术学院,陕西咸阳 712000【正文语种】中文【中图分类】TS103.2回顾我国近60年来的纺织工业历程,细纱机曾经出现过5次大的技术改进,从解放初期至70年代是以1291、1293为主,70至80年代以A512、A513为主,80至90年代以FA502、FA503为主,90年代至2000年以FA506、FA507为主,2000年以后逐步出现了长车。
每次改进,都在不同程度上推进了纱线质量的大幅度提高。
但是每次改进仅局限在牵伸及牵伸传动部分,对细纱机的横断面、结构、纵向部局、自动化、高速化、节能降耗等方面改进较少。
目前,我国各纺机企业均以仿制为主,缺少自己的基础研究,以仿制产品来调整的纺织工业,将使得我国的纺织工业永远落后于他人。
所以,未来的细纱机应该在吸收世界各国顶尖技术的基础上,联合大专院校,加强自主独立的基础理论研究,使得我们的纺机设备,特别是细纱机能在较短的时间内,赶上或超越世界先进水平。
细纱机技术从短机发展到长机,用了150-200年的时间,长车散件型到分段组装型,用了约40年,长车的分段桥接组装型,用了约10年,从散件型到分段组装型再到分段桥接组装型,这是细纱机的结构发展趋向。
分段桥接组装型,每6~8锭一节,中墙板以48锭为一段,细纱机的长向连接尺寸以龙筋为基准,锭子为免敲型,龙筋与中墙板的连接为销栓连接,其余相对位置均以龙筋为基准定相关尺寸,段安装在标准平台上下线,段与段之间的连接,以桥的安装形式进行连接,桥接件一般在装配车间进行粗装连接,便于现场组装与调整。
【VIP专享】新型纺纱技术的发展与传统环锭纺纱技术的进步

新型纺纱技术的发展与传统环锭纺纱技术的进步1 纺纱加工技术与发展概况纺纱是纺织产业链的第一道工序,其生产的纱线质量、品种与后续加工关系十分密切。
改革开放30年来,我国广大科技人员学习与消化吸收国外先进的纺纱加工技术,自主创新,有力地促进了我国纺纱加工技术的进步,突出反映在各种新型纺纱技术的推广应用和传统的环锭纺纱的技术进步,并已形成以下特点:a)以高纺纱速度、效率,低纺纱成本为特点的新型纺纱技术的应用,如转杯纺纱、喷气纺纱与涡流纺纱等。
b)以提高成纱质量、增强纱线强力、降低纱线毛羽为目的的,对纺纱过程中纤维的转移进行有效控制的纺纱新技术,如紧密纺纱等。
c)以改善织物风格和功能为目的,在纺纱过程中进行不同纤维的混纺、长丝与短纤复合纺纱等技术,如包芯纺、赛络纺、赛络菲尔纺等。
d)以为织物提供变化效果为目的的纺纱技术,如竹节纱、花式纱及多种有色纤维混纺纱等。
e)以提高织物柔软度、改善手感为目的纺纱技术,如无捻纱、低捻纱及中空纱等。
总之,纺纱加工技术的进步与发展,为纺织产品提供了丰富多彩的新型纱线,改变了20世纪70年代前使用原料单一、加工工艺落后、产品档次低、品种少的落后面貌,为提高人们的穿着质量作出了积极的贡献。
2新型纺纱的技术优势和产品的发展发展新型纺纱是近30多年来国内外纺纱技术进步的最大亮点。
国内外众多科技工作者致力于新型纺纱技术的研究,在许多重大关键技术上取得了突破,从而使各种新型纺纱加工技术得到发展与提高。
迄今为止,先后出现了转杯纺(Rotorspinning)、摩擦纺(Frictionspinning)、喷气纺(AirJetspinning)、喷气涡流纺(AirVortexspinning)、自捻纺(Selftwistspinning)等十多种新型纺纱,其中转杯纺、喷气纺、喷气涡流纺、摩擦纺等均已投入工业化生产。
目前,欧美国家把发展新型纺纱视作为纺纱加工技术进步的重要标志。
据报道:目前美国短纤纱的市场占有率是:转杯纱35%、喷气纱18%、摩擦纺纱8%、包缠纱5%、环锭纱34%,4种新型纺纱已占短纤纱市场的2/3,其中转杯纺纱已超过环锭纺纱,处于第一的位置。
环锭细纱机锭子发展的新动向

产线 。
4 3 柔性 化 .
4 结 论
高速 弹力丝 机 向高速化 、 自动化 、 柔性 化方 向发
展 。自动络筒 +高温热箱 +强制冷却再配上在线张 力控制系统的直线丝路型高速弹力丝机是新一代的 市场 化的 高速弹 力丝 机 。这样 的机器 对丝线 的生产 速度和质量都有 了较好 的保证 , 再加上其 他一些辅 助装置, 自 可 动地高速生产出高 品质的产品。
参考文献
1 B R G公司 . K A MA AF 2机样本 . 2 AR G公司 . S机样 本. B MA MP 3 RIT R. OA 1 1 机样本 . E E G L 20 4 瑞士 S M 公司 . P 一F S D 3 T机样本 . 5 印度 Hi o msn公 司.H S一1 0 A D 50 T机样本 .
向、 轴向支承分离的“ 分体式锭底” 。上 、 下支承的连
接结构 , 也从原来的刚性连接转变为各种各样的下
速下成品丝的高质量 , 特别是多孔细旦丝 , 必须优化 第l 罗拉 的位置 , 以减少丝的转折 , 减少丝的抖动和 丝条运行阻力 , 保证丝路 的稳定性 , 牵伸假捻区丝道 必须 是直 线丝 路 。
所 有 产 品均 采用 自动 络筒 的方 式 , 以适 应大 型
工厂用户的需求。全 自动络筒等被普遍使用 , 自 在 动化程度和生产效率等方面, 了更大 的提高。但 有 仅 仅采 用全 自动络 筒技 术 的加 弹机还 不 能满 足 某些 大型工厂大规模生 产的要求 , 户对 自动化程度 的 用 要求更高, 须采用全 自动的牵伸假捻生产车间 , 它包 括从原丝 的搬运 、 高温热箱、 吸气生头、 2热箱 到 第 卷绕锭位的吸气生头 、 动络筒等工序 , 自 牵伸假捻变 形后的筒子通过 自动运输车和后 面的包装线相 连 接, 实现前后工序间的 自动运送 ; 并结合在线张力检 测和微机的应用, D Y质量进行综合 的全 自动 对 T 动态测 试 ; 并对 加工 后 的筒 子进 行 自动分 级包 装 , 发
环锭细纱机的发展及改造方向探讨

消耗 、 耗 、 动生 产率 等有 密切关 系 。 能 劳
2 细纱 机
国产 第一 代 细 纱 机诞 生 在 2 O世纪 5 代 , O年 如
1 9 、 2 3型 , 牵伸 大约 在 1  ̄ 2 2 11 9 总 4 0倍 ;0世 纪 6 2 O 年代起 对 1 9 2 1型改进 , 牵伸 达到 2  ̄4 总 0 0倍 。“ ” 1 系列 细纱 机采用 双短 皮 圈牵伸 ; 英制 制式 , 罗拉 每节
8锭 , 距 2 .2 mm, 锭 22 5 每台标 准锭 数是 46锭 , 1 罗拉
采用 滑动 轴承 , 加压是 重锤 加压 , 粗纱 采用 托锭 。 2 0世纪 7 0年代 的 A5 2 A5 3系 列 是 国产 第 1、 1 二代 细纱机 , 用性有 所提 高 , 适 自动化 程度 有较 大提
21 年纪代饧识校 第 1 01 期
环锭细纱技术进步专题
一
环 锭 细纱 机 的发 展 及 改 造 方 向探 讨
孟 进, 张 凌
( 杭州二棉纱线有限公司 , 杭州 3 1o ) 1 2 3 摘 要: 阐述 了细纱机 的重要性 , 总结 了 国产 细纱技术 的发展情 况 , 提出环锭 细纱 机的技术 改造 主攻方
滑 ,0 m 锭距和 4 0 的标 准配置 , 7r a 2锭 粗纱 配置 吊锭 。 第 四代 细纱机 出现 在 2 世纪 , l 主要 特 点是 多锭
加 捻 卷 绕 系统 是 国产细 纱 机 比较 薄 弱 的 环节 , 也 是决 定细 纱机 能否 高速 的关 键 。采用 高速 节能锭 子 、 速钢领 和 钢丝 圈 , 择 合 理 的卷 装 尺 寸 , 装 高 选 加 气 圈控 制环 , 锭子 变速 均是 高速 化 的有效 措施 。 2 25 升 降系统 ..
新型纺纱技术的发展与传统环锭纺纱技术的进步
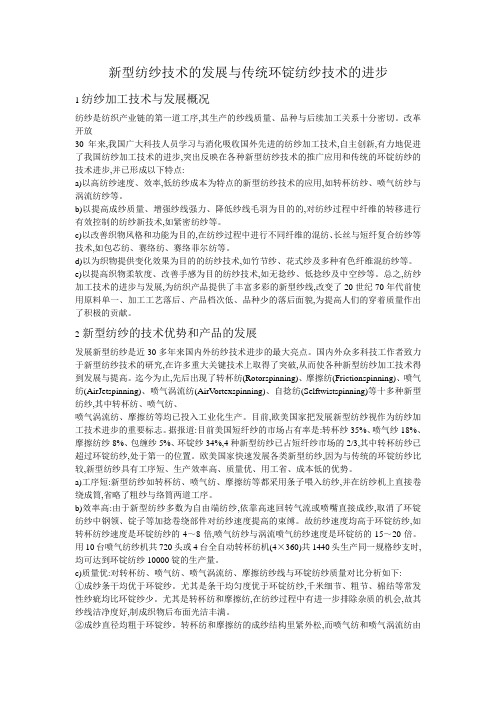
新型纺纱技术的发展与传统环锭纺纱技术的进步1 纺纱加工技术与发展概况纺纱是纺织产业链的第一道工序,其生产的纱线质量、品种与后续加工关系十分密切。
改革开放30年来,我国广大科技人员学习与消化吸收国外先进的纺纱加工技术,自主创新,有力地促进了我国纺纱加工技术的进步,突出反映在各种新型纺纱技术的推广应用和传统的环锭纺纱的技术进步,并已形成以下特点:a)以高纺纱速度、效率,低纺纱成本为特点的新型纺纱技术的应用,如转杯纺纱、喷气纺纱与涡流纺纱等。
b)以提高成纱质量、增强纱线强力、降低纱线毛羽为目的的,对纺纱过程中纤维的转移进行有效控制的纺纱新技术,如紧密纺纱等。
c)以改善织物风格和功能为目的,在纺纱过程中进行不同纤维的混纺、长丝与短纤复合纺纱等技术,如包芯纺、赛络纺、赛络菲尔纺等。
d)以为织物提供变化效果为目的的纺纱技术,如竹节纱、花式纱及多种有色纤维混纺纱等。
e)以提高织物柔软度、改善手感为目的纺纱技术,如无捻纱、低捻纱及中空纱等。
总之,纺纱加工技术的进步与发展,为纺织产品提供了丰富多彩的新型纱线,改变了20世纪70年代前使用原料单一、加工工艺落后、产品档次低、品种少的落后面貌,为提高人们的穿着质量作出了积极的贡献。
2新型纺纱的技术优势和产品的发展发展新型纺纱是近30多年来国内外纺纱技术进步的最大亮点。
国内外众多科技工作者致力于新型纺纱技术的研究,在许多重大关键技术上取得了突破,从而使各种新型纺纱加工技术得到发展与提高。
迄今为止,先后出现了转杯纺(Rotorspinning)、摩擦纺(Frictionspinning)、喷气纺(AirJetspinning)、喷气涡流纺(AirV ortexspinning)、自捻纺(Selftwistspinning)等十多种新型纺纱,其中转杯纺、喷气纺、喷气涡流纺、摩擦纺等均已投入工业化生产。
目前,欧美国家把发展新型纺纱视作为纺纱加工技术进步的重要标志。
据报道:目前美国短纤纱的市场占有率是:转杯纱35%、喷气纱18%、摩擦纺纱8%、包缠纱5%、环锭纱34%,4种新型纺纱已占短纤纱市场的2/3,其中转杯纺纱已超过环锭纺纱,处于第一的位置。
国内外环锭纺纱技术的发展与创新
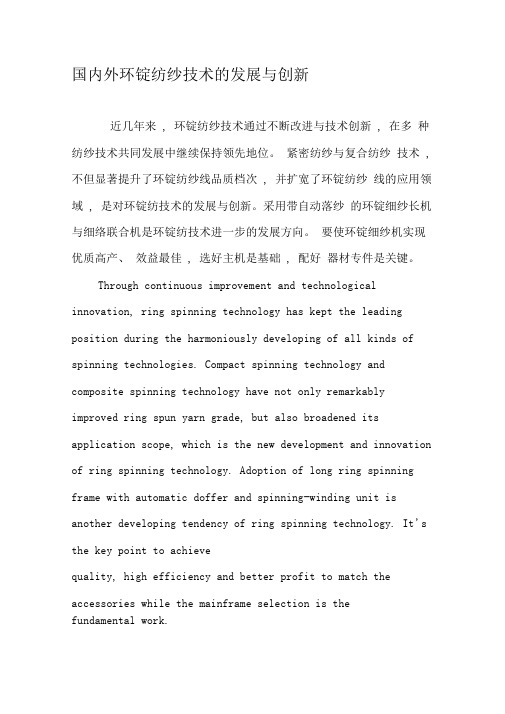
国内外环锭纺纱技术的发展与创新近几年来 , 环锭纺纱技术通过不断改进与技术创新 , 在多种纺纱技术共同发展中继续保持领先地位。
紧密纺纱与复合纺纱技术 , 不但显著提升了环锭纺纱线品质档次 , 并扩宽了环锭纺纱线的应用领域 , 是对环锭纺技术的发展与创新。
采用带自动落纱的环锭细纱长机与细络联合机是环锭纺技术进一步的发展方向。
要使环锭细纱机实现优质高产、效益最佳 , 选好主机是基础 , 配好器材专件是关键。
Through continuous improvement and technological innovation, ring spinning technology has kept the leading position during the harmoniously developing of all kinds of spinning technologies. Compact spinning technology and composite spinning technology have not only remarkably improved ring spun yarn grade, but also broadened its application scope, which is the new development and innovation of ring spinning technology. Adoption of long ring spinning frame with automatic doffer and spinning-winding unit is another developing tendency of ring spinning technology. It 's the key point to achievequality, high efficiency and better profit to match theaccessories while the mainframe selection is thefundamental work.环锭纺纱技术发展与创新的主要标志纺纱是纺织产业链的第一道工序 , 其产品质量档次、生产效率与加工成本在整个产业链中具有十分重要的地位 , 故国内外对纺纱技术的发展与创新技术的应用都十分重视与关注。
纺纱技术回忆与进展现状

紡紗技術回顧與發展現狀20世紀70年代曾出現了許多紡紗型式,如無撚紡紗、自撚紡紗、單噴嘴噴氣紡紗、包纏紡紗、離心紡紗、連續粘合紡紗等,而且在自由端紡紗中有許多種組合,如轉杯、靜電、摩擦紡,另外還有渦流紡紗。
同時,環錠紡繼續發展,涉足旋轉環和鋼絲圈裝置、單錠驅動、高牽伸裝置、雙粗紗紡和混合裝置。
縱觀今天的紡紗産業,能够看出雖然一些裝置已經成功,但少數爲花式紗的包纏紡和爲專業工業用市場的摩擦紡少有幸存。
其實,這些機器生産商也是正確的。
圖一归纳了要紧技術的紡位元數目和他們各自的紡紗市場份額。
顯然,當從安裝紡錠數目的觀點來看,環錠紡仍然是占支配地位的紡紗型式,其紡錠比安裝的轉杯紡多三倍左右。
若是以生産的紗産量來判斷的話,那麽顯然儘管安裝的轉杯紡錠僅是環錠紡的三分之一,但轉杯紡所生産的紗産量比環錠紡所生産的紗産量的三倍還多。
圖一:可能的短纖紡紗型式環錠紡環錠紡背後的技術已經维持許连年沒有大的改變了,但已經有了重要改進。
這些各自僅有略微優勢的改變則産生了如下的協同優勢:引進更長的機器減少了自動落紗的相對本钱;細紗機和絡紗機的結合再次加強了自動操纵的運用;引進自動落紗意味著落紗時間減少並且因此卷裝大小的重要性降低;在絡紗機上引進絞接意味著接紗點變得再也不突出,這再次提供了小卷裝的可能性;鋼領變小意味著對於有限的鋼絲圈速度(40米/秒),能够獲得更高的旋轉速度並且因此能够取得更高的加撚速度。
這些結合意味著環錠紡可能的最大速度從15000轉/分左右提升到25000轉/分左右。
還有其他一些取得部份成功的發展提議。
牽伸裝置:當雙皮圈牽伸占主導地位的時候,這種裝置能夠産生更高的牽伸。
近來展會上的機器能够運行70-100倍的牽伸,高牽伸的利用已在专门大程度上影響了整個裝置的經濟性。
單錠驅動:幾個生産商於20世紀80年代闡述了這種可能性。
雖然這種觀點在降低能耗、降低噪音和更好地操纵速度方面有優勢,但它卻需要更高的初始本钱和更大的紡錠尺寸。
- 1、下载文档前请自行甄别文档内容的完整性,平台不提供额外的编辑、内容补充、找答案等附加服务。
- 2、"仅部分预览"的文档,不可在线预览部分如存在完整性等问题,可反馈申请退款(可完整预览的文档不适用该条件!)。
- 3、如文档侵犯您的权益,请联系客服反馈,我们会尽快为您处理(人工客服工作时间:9:00-18:30)。
环锭细纱机纺纱过程假捻技术的发展历史与现状 黄建明 倪 远 上海申达进出口有限公司 上海东飞现代纺织技术研究所 摘要:通过专题检索美国和中国专利文献,了解前人对假捻技术的探索和贡献,在技术结构和纺纱效应方面,获得较为全面的认识,在了解以往与当前假捻技术专利状况的基础上,为新时期假捻技术的扩展应用和创新发展提供信息和技术支撑。
关键词:细纱机;加捻;捻度;假捻;张力;断头;低捻度纱;低扭矩纱;新结构纱线。
1、概述机器纺纱始于十八世纪的英国产业革命,十九世纪的20年代出现了锭帽纺纱机和环锭纺纱机。
在环锭纺纱技术发展的一百八十多年中,采用锭子、筒管、钢令、钢丝圈和导纱钩的基本加捻卷绕架构一直没有改变。
加捻使须条成为纱线,没有捻度就不成其为纱线。
“纺”字在广义上是指纺纱过程,在狭义上即为加捻。
所说的加捻对环锭纺而言是指筒管卷装和钢丝圈回转给予纱条的真实捻回,简称为真捻,除外,在纺纱过程中任何使纱条局部回转给予纱条的捻回都是假捻。
假捻使得纱条获得过程性或阶段性捻度,从时间或区段的角度看这些捻回是真实存在的,但由于纱条两个握持端均未有相位改变,在假捻点上下游的捻度相等相位相反,故在假捻过程结束时真实捻回归零。
现代纺纱流程中假捻技术最典型的应用是粗纱机锭帽,而在细纱工程中很少采用假捻技术。
在纺纱技术发展进程中,有资料记载的近数十年来,不断有假捻技术应用于细纱或精纺及捻线生产过程的技术方案被提出来,并申请专利。
追溯假捻技术最早何时开始在细纱机上应用是困难的事,不过近期笔者的一些检索会揭示某些罕为人知的历史资料,通过这些史实也许会引起业界一些新的思考。
2、前人的历史资料 2.1二十世纪30年代较早的一份资料是1931年提出的美国专利申请,这是一台带有钢令钢丝圈的锭帽式毛纺精纺机(见图1)。
本文发表于《纺织器材》 2012年第4期图1带有假捻机构的纺纱机其附加了一个独立驱动的回转假捻器L,通过滚盘84和传动带80进行驱动,即滚盘84同时传动锭子C、筒管F和假捻器L。
该发明是通过增加纺纱段的动态捻度来改善纱条动态强度,实现该发明说明书所记载的:提升纺纱速度和增大卷装容量的目的,其适用于精纺机和捻线机。
从图1可知,当时的纺纱技术尚未使用皮圈牵伸,只是由罗拉和压辊组成的简单罗拉牵伸72,但在图2的假捻器L上已有滚动轴承87的应用,图3的锭帽G上设有钢令R和钢丝圈H。
图2假捻器图3带有钢令钢丝圈的锭帽对于一个一共只有一百八十多年发展史的工业技术来说,八十年前的事情可以说是非常“古老”的事了。
令笔者感慨的是,这个二十世纪30年代的发明,虽然设计者可能已超过百岁,但相近的设计思想至今仍为当代人所用,这也许是传统行业的一个重要特征。
2.2二十世纪40年代1949 年美国专利第2590374号申请的设计人提出了多种在环锭细纱机的纺纱段实施假捻的技术方案。
图4和图5是在细纱机单侧车面上支承一根长轴8,采用蜗轮10蜗杆8a 传动方式联动驱动各锭位假捻器轮盘12或12a,以假捻轮盘的外周(图4中的12)或端面(图5中的12a)摩擦接触纱条2,使纱条2切向受力旋转获得假捻。
图4轮盘外周摩擦假捻装置图5轮盘端面摩擦假捻装置图6和图7是在细纱机单侧设置无接头循环龙带15,以龙带15外表面摩擦接触纱条2,使纱条2切向受力旋转获得假捻。
图6循环龙带假捻装置图7为图6的8a向视图该专利说明书提出,采用所述的技术方案可以在前罗拉钳口至假捻器之间设置比成纱更大的捻度(假捻),以便纺制低捻纱而降低断头。
同时其提到了几乎所有可能的优点,归纳为以下功能和优势:可以增大纺纱张力(采用较重的钢丝圈、缩小锭距、用较大直径的钢令、增加锭速),实现增加产量、增大卷装容量、纺更细的纱线、用更短的纤维纺纱及使成纱的品质更好。
二十世纪40年代的纺纱技术远不如今,工业技术方面可能很难得到一根真正意义上无接头的龙带,但历史文字记载的工艺技术理念丝毫不逊于今,除了未直接提及能耗外(当然当时还未开始注重环保问题)工艺参数对纺纱过程和成纱的关联与影响一一道明。
2.3二十世纪50年代一项1957的美国专利申请公开了一种利用多组双向皮带搓捻纱条进行假捻的假捻装置(图8图9)。
该发明通过龙带7驱动龙带轮6和齿轮8,由齿轮8传动两个被动齿轮9和两个主动皮带轮10,在两对主动皮带轮10和被动皮带轮12之间设有多组假捻皮带14,纱条通过导纱钩15引导进入多组异向移动的假捻皮带外表面之间,使纱条由假捻皮带的搓捻获得假捻,这种方式假捻效率较高。
该发明说明书所述的假捻效应是缩小纱条直径、降低成纱毛羽密度,使纱表面光滑。
图8 皮带搓捻假捻结构正视图图9皮带搓捻假捻结构侧视图该假捻技术方案可以作为实验室应用,但该假捻结构零部件多、结构复杂,操作维护都不便利,即使在半个世纪后的今天,依然难有工业化生产的应用价值。
2.4二十世纪60年代1961年一项美国专利申请的名称为假捻装置,其公开了一种采用双摩擦盘端面进行搓捻的假捻技术方案,图10所示的假捻结构由龙带12驱动龙带盘11,龙带盘11上的的两个皮带槽13和15通过皮带10传动一对假捻盘2和5作异向旋转,纱条1通过两个假捻盘之间的假捻点时,假捻盘的两个摩擦面3和4搓动纱条以轴心为中心转动,使纱条获得假捻。
图10 摩擦盘搓捻假捻结构2.5二十世纪80年代一项1980年的美国专利申请提出了一种利用喷气气流使假捻器中纱条旋转的技术方案(图11),在每个锭位的前罗拉钳口与导纱钩之间附加一套喷气假捻装置。
其说明书表述的发明目的包括:改善纺纱性能、不降低纺纱性能的同时降低半制品质量、不降低产量和质量的同时降低成纱捻度、提高产量、不降低产量或纺纱性能的同时改善成纱外观,从而可以通过纺制低捻纱而提高产量,或纺制更细的或更高品质的纱。
其特别提及用于纺制尼龙66纱,也给出了多个纺纱实例的数据。
图11喷气假捻装置2.6二十世纪90年代90年代国外申请人的一项中国发明专利申请,公开了一种采用连续移动带接触纱条表面给纱条假捻的方法和装置,专利文件明确说明其是对美国专利第2590374号发明思路的“潜在利用”,即本文上述1949年美国专利申请中循环龙带假捻形式(图6图7)的改进。
从图12-图14的具体结构上看,该方案将1949年美国专利申请中的扁平形龙带改为圆形,并使纱条与龙带的接触角增大,接触表面增加为龙带正反两面两个行程段,这带来了三个方面的好处:a、纱条接触角增大,假捻效率提高;b、同时减少了气圈张力向上游的传递;c、两个行程段反向接触平衡了纱条横向偏移。
由此带来了以下效应:在给定断头情况下增加锭速、纺制低捻纱;在给定纱支、捻度情况下降低断头;在给定纱支、锭速和捻度情况下用较低品质的原料纺纱;以及可纺制较细的纱支。
也由于纺纱区的减小而减少毛羽。
该方案用于环锭短纤维、毛纺、半精纺、合股、赛络纺及捻线。
另外该专利说明书特别指出,由于在纱线形成区捻度和张力的变化而导致纱条捻度分布更均匀,有益于纱线和织物条花的降低,有益于针织物上的起皱和线圈歪斜的减少(低扭矩)。
图12圆龙带双行程段假捻装置图13为图12的剖视图图14纱条与圆龙带的接触角2.7历史专利资料评述上述6个有关假捻技术的历史记载跨越了60多载纺纱历程,可见假捻工艺有着深厚的技术积淀。
6个案例包含了几种典型的假捻方法和技术结构,包括:机械中心旋转、喷气中心旋转、轮盘表面摩擦、龙带直线表面摩擦和皮带搓捻和轮盘搓捻等。
在不同的历史时期这些发明有着不同的发明目的,其中的一个基本目的始终围绕着环锭纺最大的技术瓶颈—纺纱张力与纱条强力间矛盾的产物—纺纱断头。
纺纱断头严重制约了环锭纺产能和纺纱成本,是环锭纺发展历程中业界不断致力于改善的重要课题。
同时前人对假捻的工艺技术和经济效应都有明确和详细的对应关联,假捻效应涉及到的产量、质量、原料、品种甚至下游应用等都一一表明,如纺纱断头、张力、捻度、锭速、输出速、强力、钢令直径、卷装容量、纱支、原料等级及外观毛羽,甚至用于赛络纺及减少针织物的起皱与线圈歪斜(纱线扭矩),虽然没有单列出节能一项,但产量一项已经包含着最大的节能效应。
这些假捻技术没有被应用,或者说假捻技术一直没有规模应用的原因有多种,技术成熟度问题、工艺必要性问题、投资与运行成本问题及下游市场应用问题等等。
3、新世纪的专利申请随着低捻度和低扭矩纱线技术和下游应用的逐步成熟,二十一世纪初有关假捻技术的中国专利申请大部分集中在低捻度和低扭矩纱的纺制方法和装置,以下的17件发明和实用新型专利申请部分已授权,部分处于公开或实审程序中。
具体见表1及图15至图33。
图15 02118588-单股无扭矩环锭图16 200510004306-单股环锭纱线的加工的方法与设备纱线的加工方法和装置图17 200880001539-工业生产纱及其纺织品图18 200910161586- 用于在环锭纱线上的方法和采用该方法的环锭纺纱机产生弯折假捻的方法和装置图19图20 200910161586-用于在环锭纱线上产生弯折假捻的方法和装置图21 200910195695-环锭细纱机图22 200910310274-一种生产低扭矩用的假捻器装置环锭纱线的纺纱装置图23 200920259605-假捻器加捻装置图24 200920259606-假捻器加捻传动装置图25 201010199611-一种环锭纺生产超柔赛络纺纱线的专用装置图26 201010210002-一种生产低扭图27 201010210142-生产低扭纱线的纺纱装置纱线的纺纱装置图28 201010210194-一种图29 201010237244-高强力生产低扭纱线的纺纱机低张力纺纱装置图30 201020561550- 图31 201110268082-一种新型涡流纱线假捻装置环锭纺的加工方法与装置图32 201110318801-一种光洁柔软纱 图33 201110318228-一种改变环锭纺的生产方法 纺纱段捻度的装置这些专利申请的假捻类型涉及轮盘表面搓捻、龙带直线表面摩擦、机械中心旋转和喷气中心旋转等假捻形式。
这些技术方案可以在实验室应用,有些也适于工业化生产。
其纺纱效应和应用性价比需要通过实践和对比作出综合评价。
4、假捻技术应用现状香港理工大学是较早利用假捻技术研发生产低扭矩纱的单位,从转杯纺到环锭纺、从分束纺到单股纺、从赛络纱到单纱,经历了十多年的研发历程,从其专利申请的阶段进程也可看出所作的努力,为低扭矩纱从实验室到工业化生产作出了贡献,并使采用假捻技术的低扭矩纱在增大附加值的情况下成功进入下游应用,使低扭矩纱成为一个行业认同的新型结构纱线品种,为此,其“低扭矩环锭单纱生产技术及其应用”项目获得“纺织之光”2009年度中国纺织工业协会科学技术奖一等奖、“单股无扭矩环锭纱线的加工方法与设备”项目获首届全国杰出专利工程技术项目称号。