压力角计算及公式
齿轮压力角

齿轮压力角渐开线及渐开线齿轮当一直线沿一圆周作纯滚动时,此直线上任一点的轨迹即称为该圆的渐开线,该圆称为渐开线的基圆,而该直线则称为发生线。
图1齿轮压力解析图如图1:AK——渐开线基圆,rbn-n:发生线θK:渐开线AK段的展角用渐开线作为齿廓的的齿轮称为渐开线齿轮。
渐开线齿轮能保持恒定的传动比。
渐开线上任一点法向压力的方向线(即渐开线在该点的法线)和该点速度方向之间的夹角称为该点的压力角。
显然,图2中的图2αk即为渐开线上K点的压力角。
由图可知:cosαk=ON/OK=rb/Rk参考文献:卢玉明.机械设计基础.高等教育出版社,1998齿轮模数“模数”是指相邻两轮齿同侧齿廓间的齿距t与圆周率π的比值(m=t/π),以毫米为单位。
模数是模数制轮齿的一个最基本参数。
模数越大,轮齿越高也越厚,如果齿轮的齿数一定,则轮的径向尺寸也越大。
模数系列标准是根据设计、制造和检验等要求制订的。
对於具有非直齿的齿轮,模数有法向模数mn、端面模数ms与轴向模数mx 的区别,它们都是以各自的齿距(法向齿距、端面齿距与轴向齿距)与圆周率的比值,也都以毫米为单位。
对於锥齿轮,模数有大端模数me、平均模数mm和小端模数m1之分。
对於刀具,则有相应的刀具模数mo等。
标准模数的应用很广。
在公制的齿轮传动、蜗杆传动、同步齿形带传动和棘轮、齿轮联轴器、花键等零件中,标准模数都是一项最基本的参数。
它对上述零件的设计、制造、维修等都起著基本参数的作用(见圆柱齿轮传动、蜗杆传动等)。
齿轮计算公式:分度圆直径d=mz m 模数z 齿数齿顶高ha=ha* m齿根高hf=(ha*+c*)m齿全高h=ha+hf=(z ha*+c*)mha*=1 c*=0.25图片中的应该两箭头之间距离是渐开线标准直齿圆柱齿轮的基本参数和几何尺寸的计算一、渐开线标准直齿圆柱齿轮各部分名称1、齿顶圆:通过轮齿顶部的圆周。
齿顶圆直径以d a表示。
2、齿根圆:通过轮齿根部的圆周。
压力角计算公式

2.2滚子摆动从动件盘形凸轮机构的设计如图2所示滚子摆动从动件盘形凸轮机构,摆杆摆动中心C ,杆长为l ,机架OC 长为b ,从动件处于起始位置时,滚子中心处于B 0点,摆杆与机架OC 之间的夹角为0ψ,当凸轮转过ϕ角后,从动件摆过ψ角,滚子中心处于B 点。
分析代换后的平面连杆机构OABC ,得从动杆BC 上B 点位移、速度、加速度矢量式:0()()(π)OA OA AB AB l l b l θθψψ+-=--e e i e(9)式中2220arccos()2b l b r lbψ+-= ()()(π)OA OA AB AB AB b o l l l ωθωθωψψ+=--g g g (10)22200()()()(π)(π)OA OA AB AB AB AB AB AB b b l l l l l ωθωθεθεψψωψψ--+=------e e g g e (11)注意,在文献[1]』中,从动件的角速度、角加速度在回程时为负,推程时为正,而此处逆时针为正,顺时针为负,所以引用公式时,须添加负号。
据矢量方程式(8)(9)(10)式推导可得:00(1)sin()tan (1)cos()bABbl b l ωψψωθωψψω-+=--+ 当tan 0AB θ≥时,arctan(tan )AB AB θθ=当tan 0AB θ<时,πarctan(tan )AB AB θθ=+20200cos (1)cos()cos (1)cos()sin()b AB AB AB b b AB AB AB b l l b l l ωθψψθωωεθψψθψψθωω⎡⎤--++⎢⎥⎣⎦=--+++++AB 杆的方向亦即从动件受力方向,从动件运动垂直于CB 杆方向,凸轮机构压力角为:π2o AB a ψψθ=--- (12)图2摆动滚子盘形凸轮机构的演化Fig.2 Evolution of disk cam with oscillating rollerM 点处曲率半径为AB l r τρ=-即:20200cos (1)cos()cos (1)cos()sin()b AB AB b b AB AB AB b l r b l l τωθψψθωρωεθψψθψψθωω⎡⎤--++⎢⎥⎣⎦=---+++++ (13)凸轮实际廓线上M 点的向径为:(π)()o AB b l r τψψθ=+---r'i e e将该向径反方向旋转ϕ角,即得凸轮处于初始位置时点M 的向径:()(π)()o AB b l r τϕψψϕθϕ=-+-----r e e e (14)将式(14)分别点乘i j 和,得凸轮实际廓线的直角坐标方程:cos cos()cos()sin sin()sin()o AB o AB x b l r y b l r ττϕψψϕθϕϕψψϕθϕ=-++--⎫⎬=-+++--⎭(15)。
棘轮的基本参数和计算公式
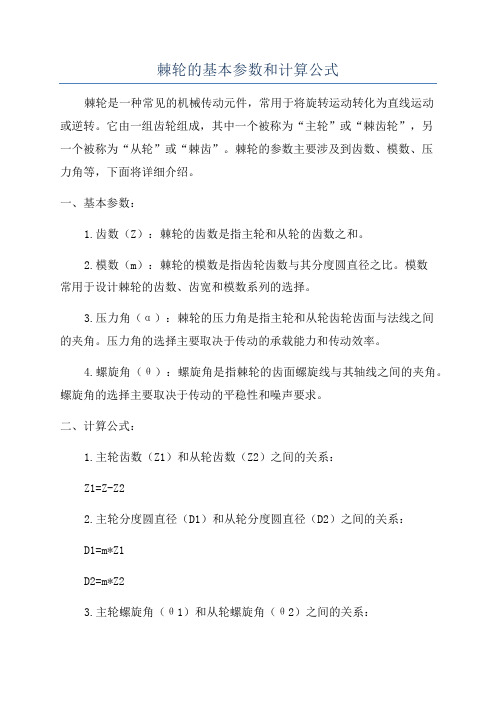
棘轮的基本参数和计算公式棘轮是一种常见的机械传动元件,常用于将旋转运动转化为直线运动或逆转。
它由一组齿轮组成,其中一个被称为“主轮”或“棘齿轮”,另一个被称为“从轮”或“棘齿”。
棘轮的参数主要涉及到齿数、模数、压力角等,下面将详细介绍。
一、基本参数:1.齿数(Z):棘轮的齿数是指主轮和从轮的齿数之和。
2.模数(m):棘轮的模数是指齿轮齿数与其分度圆直径之比。
模数常用于设计棘轮的齿数、齿宽和模数系列的选择。
3.压力角(α):棘轮的压力角是指主轮和从轮齿轮齿面与法线之间的夹角。
压力角的选择主要取决于传动的承载能力和传动效率。
4.螺旋角(θ):螺旋角是指棘轮的齿面螺旋线与其轴线之间的夹角。
螺旋角的选择主要取决于传动的平稳性和噪声要求。
二、计算公式:1.主轮齿数(Z1)和从轮齿数(Z2)之间的关系:Z1=Z-Z22.主轮分度圆直径(D1)和从轮分度圆直径(D2)之间的关系:D1=m*Z1D2=m*Z23.主轮螺旋角(θ1)和从轮螺旋角(θ2)之间的关系:θ1 = tan^-1[(tanα) / (cosα - (Z1 / Z2))]θ2 = tan^-1[(tanα) / (cosα - (Z2 / Z1))]4.主轮齿宽(b1)和从轮齿宽(b2)之间的关系:b1 = b / cosθ1b2 = b / cosθ25.主轮螺旋线的半径(r1)和从轮螺旋线的半径(r2)之间的关系:r1 = (D1 / 2) / cosθ1r2 = (D2 / 2) / cosθ2其中,b为齿轮的齿宽。
这些公式可以帮助我们计算和设计棘轮的各项参数。
需要注意的是,棘轮的选择和设计应根据具体应用需求,包括承载能力、传动效率、平稳性和噪声要求等综合考虑。
齿轮传动的计算
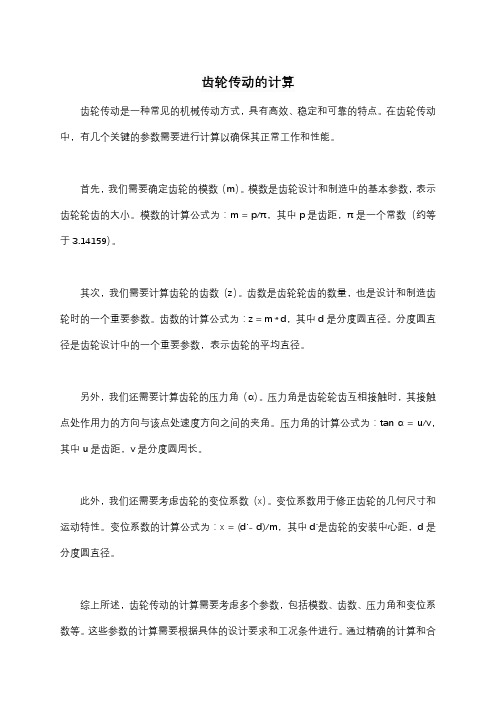
齿轮传动的计算
齿轮传动是一种常见的机械传动方式,具有高效、稳定和可靠的特点。
在齿轮传动中,有几个关键的参数需要进行计算以确保其正常工作和性能。
首先,我们需要确定齿轮的模数(m)。
模数是齿轮设计和制造中的基本参数,表示齿轮轮齿的大小。
模数的计算公式为:m = p/π,其中p是齿距,π是一个常数(约等于3.14159)。
其次,我们需要计算齿轮的齿数(z)。
齿数是齿轮轮齿的数量,也是设计和制造齿轮时的一个重要参数。
齿数的计算公式为:z = m * d,其中d是分度圆直径。
分度圆直径是齿轮设计中的一个重要参数,表示齿轮的平均直径。
另外,我们还需要计算齿轮的压力角(α)。
压力角是齿轮轮齿互相接触时,其接触点处作用力的方向与该点处速度方向之间的夹角。
压力角的计算公式为:tan α = u/v,其中u是齿距,v是分度圆周长。
此外,我们还需要考虑齿轮的变位系数(x)。
变位系数用于修正齿轮的几何尺寸和运动特性。
变位系数的计算公式为:x = (d'- d)/m,其中d'是齿轮的安装中心距,d是分度圆直径。
综上所述,齿轮传动的计算需要考虑多个参数,包括模数、齿数、压力角和变位系数等。
这些参数的计算需要根据具体的设计要求和工况条件进行。
通过精确的计算和合
理的选择,可以确保齿轮传动的正常工作和良好的性能。
压力角计算及公式
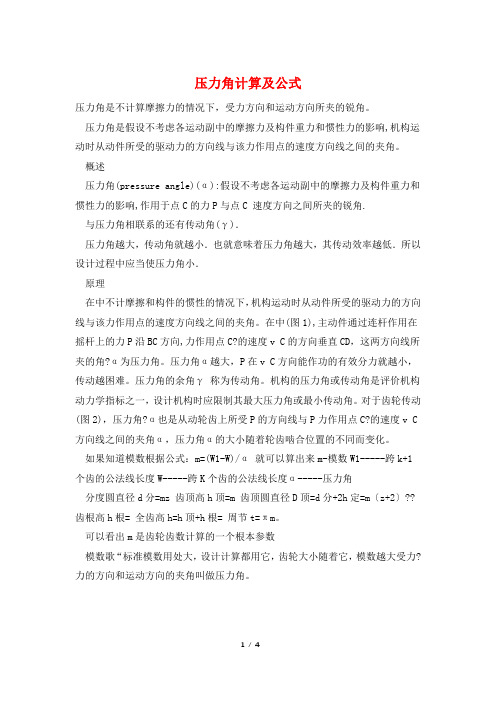
压力角计算及公式压力角是不计算摩擦力的情况下,受力方向和运动方向所夹的锐角。
压力角是假设不考虑各运动副中的摩擦力及构件重力和惯性力的影响,机构运动时从动件所受的驱动力的方向线与该力作用点的速度方向线之间的夹角。
概述压力角(pressure angle)(α):假设不考虑各运动副中的摩擦力及构件重力和惯性力的影响,作用于点C的力P与点C 速度方向之间所夹的锐角.与压力角相联系的还有传动角(γ).压力角越大,传动角就越小.也就意味着压力角越大,其传动效率越低.所以设计过程中应当使压力角小.原理在中不计摩擦和构件的惯性的情况下,机构运动时从动件所受的驱动力的方向线与该力作用点的速度方向线之间的夹角。
在中(图1),主动件通过连杆作用在摇杆上的力P沿BC方向,力作用点C?的速度v C的方向垂直CD,这两方向线所夹的角?α为压力角。
压力角α越大,P在v C方向能作功的有效分力就越小,传动越困难。
压力角的余角γ称为传动角。
机构的压力角或传动角是评价机构动力学指标之一,设计机构时应限制其最大压力角或最小传动角。
对于齿轮传动(图2),压力角?α也是从动轮齿上所受P的方向线与P力作用点C?的速度v C 方向线之间的夹角α,压力角α的大小随着轮齿啮合位置的不同而变化。
如果知道模数根据公式:m=(W1-W)/α就可以算出来m-模数W1-----跨k+1个齿的公法线长度W-----跨K个齿的公法线长度α-----压力角分度圆直径d分=mz 齿顶高h顶=m 齿顶圆直径D顶=d分+2h定=m〔z+2〕??齿根高h根= 全齿高h=h顶+h根= 周节t=πm。
可以看出m是齿轮齿数计算的一个根本参数模数歌“标准模数用处大,设计计算都用它,齿轮大小随着它,模数越大受力?力的方向和运动方向的夹角叫做压力角。
同一条渐开线上位置不同,压力角就不一样,接近基圆压力角较小,离基圆越远,压力角越大,即越接近渐开线起点,压力角越小,基圆上的渐开线上点的压力角为零。
压力角计算及公式精选文档

压力角计算及公式精选文档TTMS system office room 【TTMS16H-TTMS2A-TTMS8Q8-压力角是不计算摩擦力的情况下,受力方向和运动方向所夹的锐角。
压力角是若不考虑各运动副中的摩擦力及构件重力和惯性力的影响,机构运动时从动件所受的驱动力的方向线与该力作用点的速度方向线之间的夹角。
概述压力角(pressure angle)(α):若不考虑各运动副中的摩擦力及构件重力和惯性力的影响,作用于点C的力P与点C 速度方向之间所夹的锐角.与压力角相联系的还有传动角(γ).压力角越大,传动角就越小.也就意味着压力角越大,其传动效率越低.所以设计过程中应当使压力角小.原理在中不计摩擦和构件的惯性的情况下,机构运动时从动件所受的驱动力的方向线与该力作用点的速度方向线之间的夹角。
在中(图1),主动件通过连杆作用在摇杆上的力P沿BC方向,力作用点C?的速度v C的方向垂直CD,这两方向线所夹的角?α为压力角。
压力角α越大,P在v C方向能作功的有效分力就越小,传动越困难。
压力角的余角γ 称为传动角。
机构的压力角或传动角是评价机构动力学指标之一,设计机构时应限制其最大压力角或最小传动角。
对于齿轮传动(图2),压力角?α也是从动轮齿上所受P的方向线与P力作用点C?的速度v C方向线之间的夹角α,压力角α的大小随着轮齿啮合位置的不同而变化。
如果知道模数根据公式: m=(W1-W)/α 就可以算出来 m-模数 W1-----跨k+1个齿的公法线长度 W-----跨K 个齿的公法线长度α-----压力角分度圆直径d分=mz 齿顶高h顶=m 齿顶圆直径D顶=d分+2h定=m(z+2)??齿根高h根= 全齿高h=h顶+h根= 周节t=πm。
可以看出m是齿轮齿数计算的一个基本参数模数歌“标准模数用处大,设计计算都用它,齿轮大小随着它,模数越大受力?力的方向和运动方向的夹角叫做压力角。
同一条渐开线上位置不同,压力角就不一样,接近基圆压力角较小,离基圆越远,压力角越大,即越接近渐开线起点,压力角越小,基圆上的渐开线上点的压力角为零。
斜齿轮齿轮设计公式
斜齿轮齿轮设计公式
斜齿轮是一种常见的传动元件,其齿轮的设计需要满足一系列的要求,包括传动比、传动效率、齿轮强度、齿形等方面。
因此,斜齿轮的设计需要考虑多个因素,并结合实际应用情况进行综合评估。
斜齿轮的设计公式主要包括以下几个方面:
1. 齿数计算公式
齿数是斜齿轮设计的基础参数之一,其计算公式如下:
z = (mπcosα)/(2sinβ)
其中,z为齿数,m为模数,α为压力角,β为斜齿角。
2. 齿距计算公式
齿距是指相邻两齿轮齿顶之间的距离,其计算公式如下:
p = πm/(2sinβ)
其中,p为齿距。
3. 齿宽计算公式
齿宽是指齿轮的轴向长度,其计算公式如下:
b = d*cosβ/(tanα+ tanβ)
其中,d为齿轮的分度圆直径。
4. 模数计算公式
模数是指齿轮的公称尺寸,其计算公式如下:
m = d/z
其中,d为齿轮的分度圆直径,z为齿数。
5. 压力角计算公式
压力角是指齿轮齿面上法线与轴线间的夹角,其计算公式如下:
tanα= (tanβ+ βcosβ)/(cosβ- βsinβ)
其中,β为斜齿角。
6. 斜齿角计算公式
斜齿角是指齿轮齿面上的切线与轴线间的夹角,其计算公式如下:
tanβ= (cotα- λ)/(1 - λcotα)
其中,λ为齿顶高与模数的比值。
以上是斜齿轮齿轮设计中常用的公式,通过这些公式可以对斜齿轮的设计进行计算和优化,从而得到满足要求的齿轮结构。
压力角α的计算公式
压力角α的计算公式压力角是力学中的一个重要概念,用于描述物体受力时的力线与物体表面法线之间的夹角。
压力角的计算公式可以通过以下方式推导得出:我们需要了解一些相关的基本概念。
在力学中,我们常常用到力的分解,即将一个力分解为两个分力,一个沿着物体表面法线方向,另一个沿着物体表面切向方向。
这两个分力分别称为法向力和切向力。
当物体受到外力作用时,外力的方向可以与物体表面法线方向不一致。
此时,我们需要计算这个外力对物体产生的压力,即外力在物体表面法线方向上的分量。
这个分量就是压力角的定义。
假设有一个外力F作用在物体上,其方向与物体表面法线方向之间的夹角为α。
为了计算压力角,我们需要将这个外力F进行分解,将其分解为法向力Fn和切向力Ft。
根据三角函数的定义,我们可以得到外力F在物体表面法线方向上的分量Fn与外力F的关系:Fn = F * cosα其中,Fn表示外力F在物体表面法线方向上的分量,F表示外力的大小,α表示外力方向与物体表面法线方向之间的夹角。
通过上述公式,我们可以得到压力角α的计算公式:α = arccos(Fn / F)接下来,我们可以通过一个具体的例子来说明压力角的计算过程。
假设有一个物体受到一个大小为50N的外力作用,外力方向与物体表面法线方向之间的夹角为30度。
我们需要计算这个外力在物体表面法线方向上的分量,即压力角。
我们需要将该外力进行分解,得到法向力和切向力。
根据三角函数的定义,我们可以计算出外力在物体表面法线方向上的分量:Fn = F * cosα = 50N * cos30度≈ 43.3N接下来,我们可以根据压力角的计算公式计算压力角α:α = arccos(Fn / F) = arccos(43.3N / 50N) ≈ arcc os(0.866) ≈ 30.96度因此,该外力在物体表面法线方向上的分量的大小为43.3N,压力角为30.96度。
压力角是力学中一个重要的概念,它能够帮助我们理解物体受力时的分布情况。
标准齿轮计算公式
标准齿轮计算公式首先,我们来看一下齿轮的基本参数。
齿轮的主要参数包括模数、齿数、齿宽、压力角等。
其中,模数是齿轮的重要参数之一,它表示齿轮齿数与直径的比值,通常用符号m表示。
齿数则表示齿轮上的齿的数量,用符号z表示。
齿宽是齿轮齿面的宽度,用符号b表示。
压力角是齿轮齿面上法线方向与齿轮轴线的夹角,通常取20°或25°。
接下来,我们将介绍标准齿轮的计算公式。
在齿轮设计中,最常用的是齿轮的基本参数计算公式,包括模数、齿数、齿宽等。
这些参数的计算公式如下:模数m的计算公式为:m = (π D)/ z。
其中,D为齿轮的分度圆直径,z为齿数。
齿宽b的计算公式为:b = m (z1 + z2)/ 2。
其中,z1和z2分别为两个相啮合齿轮的齿数。
齿轮的分度圆直径D的计算公式为:D = m z。
其中,m为模数,z为齿数。
压力角α的计算公式为:tanα = ((tanβ1 + tanβ2)/ 2)/ cosγ。
其中,β1和β2分别为两个相啮合齿轮的压力角,γ为法向变位系数。
以上是标准齿轮的基本参数计算公式,通过这些公式可以计算出齿轮的各项参数,为齿轮传动系统的设计提供基础数据。
除了基本参数的计算外,齿轮传动系统中还需要考虑齿轮啮合的几何参数。
齿轮啮合的几何参数包括齿顶高、齿根高、齿顶圆直径、齿根圆直径等。
这些参数的计算公式如下:齿顶高h的计算公式为:h = m。
其中,m为模数。
齿根高hf的计算公式为:hf = 1.25 m。
其中,m为模数。
齿顶圆直径da的计算公式为:da = m (z + 2)。
其中,m为模数,z为齿数。
齿根圆直径df的计算公式为:df = m (z 2.5)。
其中,m为模数,z为齿数。
通过以上公式的计算,可以得到齿轮啮合的几何参数,进一步完善齿轮传动系统的设计。
总结一下,本文介绍了标准齿轮计算的基本原理和方法,包括齿轮的基本参数计算公式和齿轮啮合的几何参数计算公式。
这些公式为齿轮传动系统的设计提供了重要的参考数据,希望能对读者有所帮助。
渐开线齿轮参数计算公式
渐开线齿轮参数计算公式
渐开线齿轮是一种常见的齿轮类型,其齿廓曲线为渐开线。
渐开线齿轮由于其较小的齿面接触应力和更平稳的齿轮传动特性而广泛应用于各种机械设备中。
渐开线齿轮的参数计算是设计和制造渐开线齿轮的重要步骤。
以下是一些常见的渐开线齿轮参数计算公式:
1. 模数(M)的计算公式:
M = d / z
其中,d为齿轮的基圆直径,z为齿轮的齿数。
2. 基圆直径(d)的计算公式:
d = M * z
3. 分度圆直径(D)的计算公式:
D = d + 2 * M * (cosα + β)
4. 压力角(α)的计算公式:
tanα = (tanφ - φ) / cosφ
其中,φ为压力角的推荐值。
5. 齿顶高(h_a)的计算公式:
h_a = M * (1 + 1 / sinα)
6. 齿根高(h_f)的计算公式:
h_f = M * (1.25 - 1.27 * cosα)
7. 齿顶高系数(hn)的计算公式:
hn = ha / M
8. 齿根高系数(hf)的计算公式:
hf = hf / M
除了上述公式外,还有一些其他的参数计算公式,如齿廓曲线的计算、齿间角的计算等。
这些公式可以根据具体的设计要求和齿轮的应用场景进行调整和优化。
渐开线齿轮参数的计算对于保证齿轮的精度和传动效率至关重要。
合理选择和计算渐开线齿轮的参数可以提高齿轮的寿命和传动稳定性,减少噪声和振动,确保机械设备的正常运行。
因此,在设计和制造渐开线齿轮时,工程师们需要仔细研究和计算各个参数,以保证齿轮的性能满足设计要求。
- 1、下载文档前请自行甄别文档内容的完整性,平台不提供额外的编辑、内容补充、找答案等附加服务。
- 2、"仅部分预览"的文档,不可在线预览部分如存在完整性等问题,可反馈申请退款(可完整预览的文档不适用该条件!)。
- 3、如文档侵犯您的权益,请联系客服反馈,我们会尽快为您处理(人工客服工作时间:9:00-18:30)。
压力角是不计算摩擦力的情况下,受力方向和运动方向所夹的锐角。
压力角是若不考虑各运动副中的摩擦力及构件重力和惯性力的影响,机构运动时从动件所受的驱动力的方向线与该力作用点的速度方向线之间的夹角。
概述折叠编辑本段
压力角(pressure angle)(α):若不考虑各运动副中的摩擦力及构件重力和惯性力的影响,作用于点C的力P与点C速度方向之间所夹的锐角.
与压力角相联系的还有传动角(γ).
压力角越大,传动角就越小.也就意味着压力角越大,其传动效率越低.所以设计过程中应当使压力角小.
原理折叠编辑本段
在平面连杆机构中不计摩擦和构件的惯性的情况下,机构运动时从动件所受的驱动力的方向线与该力作用点的速度方向线之间的夹角。
在曲柄摇杆机构中(图1),主动件通过连杆作用在摇杆上的力P沿BC方向,力作用点C?的速度v C的方向垂直CD,这两方向线所夹的角?α为压力角。
压力角α越大,P在v C方向能作功的有效分力就越小,传动越困难。
压力角的余角γ 称为传动角。
机构的压力角或传动角是
评价机构动力学指标之一,设计机构时应限制其最大压力角或最小传动角。
对于齿轮传动(图2),压力角?α也是从动轮齿上所受驱动力P的方向线与P力作用点C?的速度v C方向线之间的夹角α,压力角
α的大小随着轮齿啮合位置的不同而变化。
压力角
压力角
如果知道模数根据公式: m=(W1-W)/α 就可以算出来m-模数W1-----跨k+1个齿的公法线长度 W-----跨K个齿的公法线长度α-----压力角
分度圆直径d分=mz 齿顶高h顶=m 齿顶圆直径D顶=d分+2h定=m (z+2)??齿根高h根= 全齿高h=h顶+h根= 周节t=πm。
可以看出m是齿轮齿数计算的一个基本参数
模数歌“标准模数用处大,设计计算都用它,齿轮大小随着它,模数越大受力?力的方向和运动方向的夹角叫做压力角。
同一条渐开线上位置不同,压力角就不一样,接近基圆压力角较小,离基圆越远,压力角越大,即越接近渐开线起点,压力角越小,基圆上的渐开线上点的压力角为零。
分度圆上的压力角20°
如果分度圆的压力角越小,其基圆离分度圆就很近,这样齿根变短且齿根很瘦,牙齿所能承载的力量较小,如果分度圆压力角>20°,基圆离分度圆就远了,齿根也厚了,壮实有力了,但是齿顶变尖了且传动费劲了,不过为了加强牙齿力量有时也采用大压力角(如汽车上的某些齿轮α=°.
我国规定分度圆标准压力角是20°
压力角歌“齿形压力角各处不一样,标准压力角20°定在分圆上,增大压力角齿顶变尖根变壮”。
滚子摆动从动件盘形凸轮机构的设计
如图2所示滚
子摆动从动件盘形
凸轮机构,摆杆摆
动中心C ,杆长为l ,
机架OC 长为b ,从动件处于起始位置时,滚子中心处于B 0点,摆杆与机架OC 之间的夹角为0ψ,当凸轮转过ϕ角后,从动件摆过ψ角,滚子中心处于B 点。
分析代换后的平面连杆机构OABC ,得从动杆BC 上B 点位移、速度、加速度矢量式:
0()()(π)OA OA AB AB l l b l θθψψ+-=--e e i e (9)
式中222
0arccos()2b
l b r lb ψ+-=
()()(π)OA OA AB AB AB b o l l l ωθωθωψψ+=--g g g (10)
22
2
00()()()(π)(π)
OA OA AB AB AB AB AB AB b b l l l l l ωθωθεθεψψωψψ--+=------e e g g e (11)
注意,在文献[1]』中,从动件的角速度、角加速度在回程时为负,推程时为正,而此处逆时针为正,顺时针为负,所以引用公式时,须添加负号。
图2摆动滚子盘形凸轮机构的演化
据矢量方程式(8)(9)(10)式推导可得:
00(1)sin()tan (1)cos()b AB
b l b l ωψψωθωψψω-+=--+ 当tan 0AB θ≥时,arctan(tan )AB AB θθ=
当tan 0AB θ<时,πarctan(tan )AB AB θθ=+
20200cos (1)cos()cos (1)cos()sin()b AB AB AB b b AB AB AB b l l b l l ωθψψθωωεθψψθψψθωω⎡⎤--++⎢⎥⎣⎦=--+++++
AB 杆的方向亦即从动件受力方向,从动件运动垂直于CB 杆方向,凸轮机构压力角为:π2
o AB a ψψθ=--- (12) M 点处曲率半径为AB l r τρ=-即:
20200cos (1)cos()cos (1)cos()sin()b AB AB b b AB AB AB b l r b l l τωθψψθωρωεθψψθψψθωω⎡⎤--++⎢⎥⎣⎦=---+++++ (13)
凸轮实际廓线上M 点的向径为:
(π)()o AB b l r τψψθ=+---r'i e e
将该向径反方向旋转ϕ角,即得凸轮处于初始位置时点M 的向径: ()(π)()o AB b l r τϕψψϕθϕ=-+-----r e e e (14)
将式(14)分别点乘i j 和,得凸轮实际廓线的直角坐标方程: cos cos()cos()sin sin()sin()o AB o AB x b l r y b l r ττϕψψϕθϕϕψψϕθϕ=-++--⎫⎬=-+++--⎭ (15)。