模具加工规范及规范流程图
模具开发流程规范

China Communication Technology 华之博讯无限1 目的通过对新模具开发制作过程的流程控制,确保模具开发制作在受控状态下进行,以提供给客户满意的产品。
2 范围适用于公司所有压铸、塑胶、五金模具的开发制作。
3 职责3.1 技术工程部3.1.1 提供需开发模具的产品3D图并根据出模条件进行必要的修改。
3.1.2 提出模具制作申请,走完签核流程。
提供产品材料、用途、模具寿命、模具交期等必要信息。
3.1.3 同工模部一起完成模具BOM的建立。
3.1.3 模具开发完成后根据试做结果提出改善需求。
3.2 工模部3.2.1 对产品3D图根据出模条件提出修改意见。
3.2.2 对模具开发费用进行评估并报价。
3.2.3 负责模具的结构设计、同技术工程部一起完成模具BOM的建立。
3.2.4 提出材料采购申请。
3.2.4 对模具进行加工制作,并进行不良修正。
3.2.5 提出模具试做申请。
3.2.5 模具图纸的存档和模具清册的建立。
3.3 压铸部:负责对新的压铸模具进行最佳状况的试做,并对不良状况提出修正意见。
3.4 注塑部:负责对新的塑胶模具进行最佳状况的试做,并对不良状况提出修正意见。
3.5 品管中心:负责对产品进行外观判定,重要尺寸的测量。
3.6 PMC : 负责提供客户的产品交期和交期的调整。
3.7 采购部:根据模具BOM对所需材料进行采买。
4 流程图5. 模具开发制作流程说明5.1 模具开发申请阶段5.1.1 技术工程部组织工模部、成型部门一起对需开模产品3D图进行开模评审,确定产品开模样式。
(包括产品材料、外观要求、模具寿命、交模日期、前后模仁分型面,浇注系统、顶出系统,冷却系统、抽芯机构,机台大小等)5.1.2 工模部根据开模评审结论对开模费用进行评估,并制作模具《模具报价表》给技术工程部,完成报价。
5.1.3 技术工程部提出模具开发申请,填写《模具、治具开发申请单》并附《模具报价表》走完签核流程交工模部进行模具制作。
模具加工规范及规范流程图

模具加工工艺及流程图一.拉延模1.OP10下模座-凸模一.模座毛坯铸件的龙铣数控加工方法. 1. 吊上毛坯铸件先光正合模用的安全平面,作为加工底面的基准.翻转模座加工底面,模具中心刻度线拉平取中按百位线加工底面,精加工底面时夹紧工件的压板,放松到轻微夹紧的状态精加工底面,保证底面加工精度, 精加工底面完成后打表测量底面四个角,检查底面平面度. 同时按图铣出十字键槽.铣基准边并打上钢印,并记录在案. 2. 模座毛坯铸件码槽已铸好的,按图检查码槽,不合尺寸的重新加工.如果码槽未铸出的在铣底面时一次加工到位.(注意一旦底面所有尺寸一次加工到位以后,不管正面够不够加工只能以底面基准为准,不能再偏中心,如果偏中心底面铣好的一些尺寸将全部报废.)3. 铣正面时按底面铣好的基准取中, 在加工前必须先测试2D 轮廓,导板确定是否够加工,验证程序是否正确。
验证正确后在数控上完成凸模2D 轮廓分模线, 安全平面,到底限位块安装面, 与压边圈配合的Y 向导板,与压边圈配合的X 向导板,按图纸尺寸加工. 导板高度方向铣穿不留台阶.精加工完成后按图纸坐标尺寸钻出3销基准孔,打上钢印,并记录在案.。
4. 压边圈加工好与下模座组立3D 成型面.因下模压边圈与下模座组立后, 3销基准孔会被挡住,为方便组立后取基准加工,可以在安全平面凸台上多钻两个对称的基准孔.2.OP10压边圈与压边圈配合的Y 向内导板 合模用的安全平面凸台压边圈安装的到底限位块凸模2D 轮廓分模线安全螺杆安装孔起重吊装用的起重棒共压型时合模机的顶杆过孔底面加工余量百位线加工好到百位线为100装模快速定位用的十槽,也控加工快速定位模具装定位,常用于冲压另件流水线装夹用固定模座的码槽,及装压板的压板面 凸模成型面模具的送料方向上下模连接板安装面 模座底面与压边圈配合的X 向内导板 3销基准孔与下模座配合的Y 向外导板安装面与上模座配合的Y 向外导板平衡块安装面与凸模2D 配合的压边圈2D 分模线压料用的拉延荊1. 压边圈按以上提到的铣底面的方法加工底面,同时把与与下模座配合的X 向导板安装面, Y 向导板安装面按图纸尺寸加工, 耐磨板安装背托不能铣掉.同时铣X 向,Y 向基准边,打上钢印并记录.2. 按底面基准边取中心加工正面与凸模2D 配合的压边圈2D 分模线, 在加工前必须先测试2D 轮廓,导板确定是否够加工,验证程序是否正确。
ISO9001模具管理控制程序(含流程图)

模具管理控制程序(ISO9001-2015)1.0目的确保控制工艺模具对零部件加工和装配的影响因素,确保满足产品技术要求。
2.0范围适用于所有产品模具的管理。
3.0定义与术语无4.0职责a.研发部:负责公司新模具与复制模具的采购,试模样品的验收及确认;b.生产部:负责安排模具的试模,及正确使用、维护保养等工作;5.0作业流程5.1模具需求研发部根据顾客的需求和生产的需求,及业务通知单、样品单、下模制造单,填写《开模打样工作令》经部门经理批准、副总经理核准后实施采购。
5.2模具的验收、转交a.供应商依《开模打样工作令》要求制模完成后,提交生产样品、制作工艺资料、给研发部。
b.研发部根据供应商提供的工艺资料与样品进行检验,并在《样品检验报告》上填写检验结果回传给供应商,检验合格后发放工艺资料、样品检验报告、提供样品给生产部。
c.供应商依据研发部确认合格的《样品检验报告》及工艺资料通知生产部进行试模验收,验收要求如下:1.试模材料规格是否正确,与定位是否相符,送料是否顺畅;2.模具工序内容是否与工艺文件相符;3.模具装夹是否顺畅,废料排屑是否堵料、易清理;4.模具对形状相似的产品是否有做防呆;5.产品摆放是否好拿好放、不粘模、易脱料。
d.试模合格后,模管员在供应商《模具移交单》上签名入库,并把《模具移交单》复印给研发部进行付款作业。
试模不合格的不予移交。
5.3模具管理a.模具入库管理1.模具入库时确认送货单及实物的数量,检查无误时进行入库2.入库的模具由修模组模管员登记于《模具台帐》中,并做好帐、物、卡相符。
b.使用管理1.使用模具时,架模组到模具房登记领用,在使用前检查是否有损坏现象;2.归还模具前,架模组应清理模具,模管员填写使用记录;3.入库的新模具在首次量产过程中发现产品不合格,且经确认是模具造成原因,写维修单形式退回供应商。
4.接收归还的模具时,模具保管员应将模具清洁上油后存放于专用模架,每2个月由模管员确认模具保管状态,并对模具(使用中、长期停用)进行防锈保养。
模具制造工程流程图_塑胶模

塑胶射出
业
务
(1) (2)
接单
决定模具编号 完成模咬具花规图格安书排
雕刻安排
管 (3) (4)决定自制、外包
与客-户1讨论 -2 -3
(5) Layout、检讨
理
(6)月别模具别日程表
大日程计划
月别生产计
(7)
划 模具别、自制
外包的区分现场备用
订货
模座 材料 (13)请购件加安工排分配讨论
加工工时 估算 (14) 完成
材料入库
(15) -1
中日程计划 交 零期 件管 管理 理表 卡 图面安排
-2
(16) 外包
自制
生产管理
设
计
制
(8) 设计计划
(17) 课别生产计划
(9) 与客户讨论
(1~6)
零件
(10)
(11)
设计
图面检查 (12)
CNC EDM 钻床
图面 零件清单 安排
搪床
车床
外包 铣
NC
雕刻 (19) 检查
咬花
钻孔 (20) 抛光
淬火
放电 (21) 零件Hale Waihona Puke 齐线切割(22) 装配
模具零件加工工艺流程图(底盖)
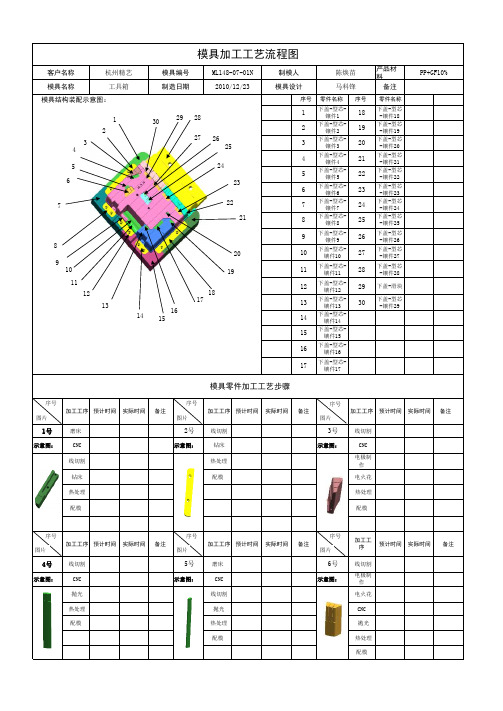
产品材料备注序号 零件名称序号零件名称1下盖-型芯-镶件118下盖-型芯-镶件182下盖-型芯-镶件219下盖-型芯-镶件193下盖-型芯-镶件320下盖-型芯-镶件204下盖-型芯-镶件421下盖-型芯-镶件215下盖-型芯-镶件522下盖-型芯-镶件226下盖-型芯-镶件623下盖-型芯-镶件237下盖-型芯-镶件724下盖-型芯-镶件248下盖-型芯-镶件825下盖-型芯-镶件259下盖-型芯-镶件926下盖-型芯-镶件2610下盖-型芯-镶件1027下盖-型芯-镶件2711下盖-型芯-镶件1128下盖-型芯-镶件2812下盖-型芯-镶件1229下盖-滑块13下盖-型芯-镶件1330下盖-型芯-镶件2914下盖-型芯-镶件1415下盖-型芯-镶件1516下盖-型芯-镶件1617下盖-型芯-镶件17加工工序 预计时间 实际时间备注加工工序 预计时间 实际时间备注加工工序 预计时间 实际时间 备注1号磨床 2号线切割 3号线切割示意图:CNC 示意图:钻床示意图:CNC 线切割 热处理 电极制作 钻床配模电火花 热处理 热处理配模配模加工工序 预计时间 实际时间备注加工工序 预计时间 实际时间备注加工工序 预计时间 实际时间备注4号线切割 5号磨床 6号线切割示意图:CNC 示意图:CNC 示意图:电极制作 抛光 线切割 电火花 热处理 抛光CNC配模热处理 抛光配模热处理配模制模人模具设计模具零件加工工艺步骤模具结构装配示意图:陈焕苗马科锋杭州精艺模具加工工艺流程图PP+GF10%ML148-07-01N 2010/12/23客户名称模具名称模具编号工具箱制造日期234578910111213141719202425262723222118166图片序号图片序号图片序号图片序号图片序号图片序号129302815。
模具开发流程图
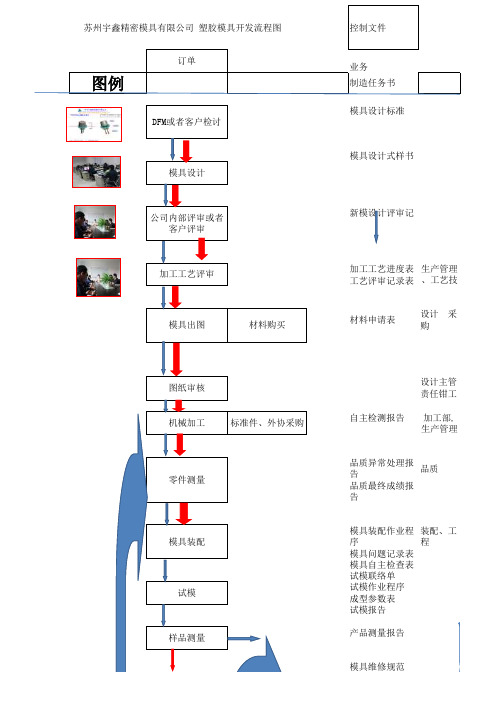
产品测量报告
加工、生 产管理
模具出货检测表 送货单
Ⅰ
ⅠⅡⅢⅣ ⅤⅥⅦ 采购
Ⅱ
Ⅲ
苏州宇鑫精密模具有限公司 塑胶模具开发流具设计
公司内部评审或者 客户评审
加工工艺评审
模具出图
材料购买
控制文件
业务 制造任务书 模具设计标准
模具设计式样书
新模设计评审记
加工工艺进度表 生产管理 工艺评审记录表 、工艺技
材料申请表
设计 采 购
图纸审核
机械加工
标准件、外协采购
零件测量
模具装配 试模
样品测量
设计主管 责任钳工
自主检测报告 加工部, 生产管理
品质异常处理报 告
品质
品质最终成绩报
告
模具装配作业程 装配、工
序
程
模具问题记录表
模具自主检查表
试模联络单
试模作业程序
成型参数表
试模报告
产品测量报告
模具维修规范
模具维修检讨 样品送客户确认
模具出货
试模、装 模具维修报告 配、工程
上下模作业流程图

上下模作业流程图一、目的本流程图旨在明确模具上下模的操作步骤和要点,以确保生产过程中的安全和稳定,提高生产效率。
二、流程图说明1、模具准备在进行上下模作业前,需先检查模具是否完好无损,各部件是否齐全。
如有异常,需及时进行处理。
2、安全检查在进行上下模作业前,必须进行安全检查。
包括但不限于检查液压系统、气压系统、电气系统等,确保没有安全隐患。
3、模具搬运搬运模具时,需使用合适的工具,如吊车、叉车等,确保安全稳妥。
同时,要遵循相应的安全操作规程,防止工伤事故发生。
4、模具定位将模具放置在指定位置后,需进行初步定位。
此时,要确保模具的安装面与机床的工作台之间贴合、平稳。
5、紧固模具通过螺栓等紧固件将模具与机床工作台牢固连接。
在紧固过程中,应注意力度适中,避免损坏模具及工作台。
6、调整与校准完成模具紧固后,需对模具进行进一步的调整与校准,以确保其位置准确、符合加工要求。
7、试运行在完成模具的上下模作业后,应进行试运行,以检查模具的运行情况及加工质量。
如有异常,需及时进行调整。
8、生产加工试运行无误后,即可开始进行批量生产加工。
在此过程中,操作人员应严格遵守操作规程,密切模具的运行状态。
9、下模作业生产加工完成后,需进行下模作业。
首先进行安全检查,确保无安全隐患。
然后按照解体顺序依次取下模具各部件。
10、清理与维护下模作业完成后,要对模具进行清理和维护。
包括清除杂质、清洗表面、检查损伤等,确保模具保持良好的状态。
11、存储与保管清理和维护完成后,应将模具存放在干燥、通风良好的库房内,避免阳光直射和潮湿环境对模具造成损害。
同时,要遵循相应的安全规定,防止意外事故发生。
三、总结本流程图详细描述了上下模作业的全过程,从模具准备到存储保管,每个环节都进行了详细的说明和要求。
通过明确流程图,有助于操作人员更好地掌握上下模作业的步骤和要点,提高生产效率和质量。
也确保了生产过程中的安全和稳定。
在实际操作中,应根据具体情况对流程图进行调整和完善。
冲压模具设计与制造规范

冲压模具设计与制造规范一.目的:统一公司模具设计规范,更好地配合加工单位,适应快速作业的需要。
二.范围:适用于本公司所有部门之作业。
三.权责:由各个部门编写文件之人员负责执行此规范。
四.内容:1.开模前相关作业程序:1-1 程序说明:新项目提出开模时,模具工程师必须先向业务或此项目负责人确认此项目预估的量能会有多少,之后再依照此量能特性加以分析,以最快速、经济、合理之要求达成最佳化冲压模具状态,以确保后续之量产能力。
模具开发前期制作冲压模具工程设计制作分析,此分析用意在于预见模具开发可能产生之问题点,将其整理以及早发现及早修正的形态为目的,其次安排各工程图面的合理性(包含单工程模具工程图面以及连续模料带图面)、考虑模具结构设计的安全以及正确性……等,另外依照评估后模具形式决定模具材质以及热处理特性,再规范定义各配件的使用时机,明确规划出最佳化模具的形式。
在模具制作期间,模具开发进度的掌控往往是造成一个新的项目是否有办法如期成行的一个重要症结点。
试模时实际的状况记录于试模检讨记录中,藉由实际的问题记录以及改善确认方式此套新开发的模具运行无误有量产能力,最后确认每个单件皆符合RD所设计的规范要求后,签认模具移交单以做模具验收的标准,而针对以上叙述以下用流程图加以说明:冲压模具级数及作业分类原则Design For Manufacture Report工程图以带图面确定工程模:各工程工序图连续模:料带图模具确定各工程模具结构图模具开发进度掌控模具开发进度表试模检讨改善记录FAI Report & Cpk Report模具确认模具验收办法2. 冲压模具级数、寿命定义及模具组织架构:2-1 冲压模具级数定义:各类冲压模具依照不同程度产能之要求,定义出三种级数冲压模具结构尺寸以及相关规定之设计形态,分别为每个月产能在50K以下少量产能型态的模具(定义为一般产能模具)50K~100K之间中产能型态之模具(定义为中产能模具)以及每个月100K以上产量之模具(定义为高产能模具),定义各级数产能模具如下表所示:由于模具在冲压过程中有一定的磨损、变形,为了保证产品的质量,冲压一定次数后就必须有一次模具保养,根据本厂内多年的现场统计,总结模具保养规律如下:2-3 冲压模具结构分类:冲压类模具可分为下料形式、冲孔形式、折弯形式、连续模具等,其模具结构、板材尺寸、模具材质规范如以下所示。
- 1、下载文档前请自行甄别文档内容的完整性,平台不提供额外的编辑、内容补充、找答案等附加服务。
- 2、"仅部分预览"的文档,不可在线预览部分如存在完整性等问题,可反馈申请退款(可完整预览的文档不适用该条件!)。
- 3、如文档侵犯您的权益,请联系客服反馈,我们会尽快为您处理(人工客服工作时间:9:00-18:30)。
模具加工工艺及流程图一.拉延模1.OP10下模座-凸模一.模座毛坯铸件的龙铣数控加工方法. 按模具中心刻度线拉平取中按百位线加工底面,精加工底面时夹紧工件的压板,放松到轻微夹紧的状态精加工底面,保证底面加工精度, 精加工底面完成后打表测量底面四个角,检查底面平面度. 同时按图铣出十字键槽。
铣基准边并打上钢印,并记录在案. 2. 模座毛坯铸件码槽已铸好的,按图检查码槽,不合尺寸的重新加工.如果码槽未铸出的在铣底面时一次加工到位。
(注意一旦底面所有尺寸一次加工到位以后,不管正面够不够加工只能以底面基准为准,不能再偏中心,如果偏中心底面铣好的一些尺寸将全部报废。
)3. 铣正面时按底面铣好的基准取中, 在加工前必须先测试2D 轮廓,导板确定是否够加工,验证程序是否正确.验证正确后在数控上完成凸模2D 轮廓分模线, 安全平面,到底限位块安装面, 与压边圈配合的Y 向导板,与压边圈配合的X 向导板,按图纸尺寸加工。
导板高度方向铣穿不留台阶.精加工完成后按图纸坐标尺寸钻出3销基准孔,打上钢印,并记录在案。
4. 压边圈加工好与下模座组立3D 成型面。
因下模压边圈与下模座组立后, 3销基准孔会被挡住,为方便组立后取基准加工,可以在安全平面凸台上多钻两个对称的基准孔.2.OP10压边圈与压边圈配合的Y 向内导板 合模用的安全平面凸台压边圈安装的到底限位块凸模2D 轮廓分模线安全螺杆安装孔起重吊装用的起重棒共4处压型时合模机的顶杆过孔底面加工余量百位线, 底面加工好到百位线为100豪米 装模快速定位用的十字键槽,也用在数控加工快速定位模具装模快速定位,常用于冲压另件流水线装夹用固定模座的码槽,及装压板的压板面 凸模成型面模具的送料方向上下模连接板安装面 模座底面与压边圈配合的X 向内导板3销基准孔1. 压边圈按以上提到的铣底面的方法加工底面,同时把与与下模座配合的X 向导板安装面, Y 向导板安装面按图纸尺寸加工, 耐磨板安装背托不能铣掉。
同时铣X 向,Y 向基准边,打上钢印并记录。
2。
按底面基准边取中心加工正面与凸模2D 配合的压边圈2D 分模线, 在加工前必须先测试2D 轮廓,导板确定是否够加工,验证程序是否正确。
验证正确后在数控上完成2D 轮廓的粗精铣。
3。
与上模座配合的X 向导板, Y 向导板先不用加工,待下模压边圈与下模座组立后粗精铣完3D 型面后,才粗精加工.4. 加工所有的配合导板面时按图纸尺寸过切0.06毫米方便钳工组立,2米以上的大型模具过切0。
15毫米,必须以打表测量后的尺为准。
5.在加工前必须先测试2D 轮廓,导板确定是否够加工,验证程序是否正确。
注意3销基准孔按图纸尺寸坐标加工,孔直径图纸未规定按10毫米直径,深度15毫米。
基准边统一钻在Y 负方向两处用于拉平工件定Y 向座标,X 向正方向一处定X 向座标,取中心。
三。
OP10下模凸模与压边圈组立图与下模座配合的Y 向外导板安装面与上模座配合的Y 向外导板平衡块安装面与凸模2D 配合的压边圈2D 分模线压料用的拉延荊耐磨板安装背托 安全螺杆通过孔与下模座配合的X 向外导板安装面与上模座配合的X 向外导板耐磨板安装背托耐磨板 平衡块板件限位器凸模与压边圈的组合3D 型面安全螺杆安装孔1。
下模凸模与压边圈组立好后按下模凸模基准孔加工3D 型面,在加工前必须先测试3D 型面外导板确定是否够加工,验证程序是否正确,验证正确后按程序单在粗铣数控机床上完成3D 型面的粗铣,外导板的粗铣。
外导板的粗铣后留0。
7毫米余量,25球刀,20球刀的预清角。
粗铣完成后把平衡块安装面加工到尺寸,并在压料板钻8毫米直径粗基准孔。
2.板件限位器安装面先不加工,待钳工调模确定位置后才加工。
3.粗铣完成后转精铣数控机床上完成型面的精加工,与上模座配合的X 向导板也叫外导板的精加工,与上模座配合的Y 向导板的精加工。
精加工完成后检查垂直度,垂直度控制在0。
03毫米以内.检查 导板尺寸是否达到图纸及工艺要求。
精加工完成后钻铰10毫米直径精基准孔,并打上钢印记录在案。
4.OP10上模凹模与压边圈配合的Y 向内导板与压边圈配合的X 向内导板 压边圈限位安全螺杆 与上模座配合的X 向外导板 与上模座配合的Y 向内导板提到的模座毛坯铸件的龙铣数控加工方法加工底面的.及底面上的其它尺寸.底面留余量二次加工的上模码槽面先不加工,待合模后最终确定闭合高度,底面二次加工到位后,才加工上模码槽面.2. 正面型面,导板,上模平衡块凸台面,上下模合模的安全平面,等加工面的加工,按底面基准取中心加工。
3. 在加工前必须先测试3D 型面外导板确定是否够加工,验证程序是否正确,验证正确后按程序单在粗铣数控机床上完成3D 型面的粗铣,外导板的粗铣。
外导板的粗铣后留0。
7毫米余量,25球刀,20球刀的预清角.粗铣完成后把平衡块安装面加工到尺寸,并在上模指定位置钻8毫米直径粗基准孔.4. 粗铣完成后转精铣数控机床上完成型面的精加工,与下模座配合的X 向导板也叫内导板的精加工,与上模座配合的Y 向导板的精加工。
精加工完成后检查垂直度,垂直度控制在0。
03毫米以内.检查 导板尺寸是否达到图纸及工艺要求。
精加工完成后钻铰10毫米直径精基准孔,并打上钢印记录5. OP10上模座与下模座合模总装配与下模座配合的X 向内导板上下模合模的安全平面下模限位器避让孔 上模凹模成型型面与下模座配合的Y 向外导板耐模板安装背托装夹用固定模座的码槽,及装压板的压板面 快速定位十字键槽 送料方向 快速定位十字键槽 上下模连接板安装面3销基准孔上模平衡块凸台面6.二.修边模 1下模座快速定位十字键槽工4处 上下模连接板安装面共8处模具装模快速定位,常用于冲压另件流水线共2处 下模导板与压料板导板配合关系共8处上模导板与下模导板配合关系共8处铸件的减重掏空,保证强度下降低成本废料刀安装面,共5处 凸模镶块安装面 基准孔指定加工位置凸台面,共3合模时放安全垫块,方便合模1.铣底面的加工按模座毛坯铸件的龙铣数控加工方法加工。
2. 正面的废料刀安装面,共5处,凸模镶块安装面,导柱孔安装面,基准孔指定加工位置凸台面,共3处,上下模合模的安全平面,码槽面,上下模连接板安装面,都按图纸尺寸一次加工到位。
3. 模具装模快速定位的V 型快速定位最后在数控加工.2.下模凸模导柱,共4处模具装模快速定位,常用于冲压另件流水线共2处导柱孔安装面及安装导柱的导柱孔,镗好孔后打入导柱厂标上下模合模的安全平面1. 下模龙铣加工完各安装面,与单独铣好底面后的凸模镶块,交钳工组立。
按模座上刻的正面十字中心线,与凸模镶块上的十字中心线重合来组立.十字中心线保丽龙制作准确,组立前不用先测试。
2. 如果组立前上数控测试,测试后按图点导柱孔坐标。
待转钳工预钻底孔,单边留5-6毫米余量。
3. 正面型面及轮廓加工前必须先测试余量,验证程序是否正确,验证正确后按程序单在粗铣数控机床上完成3D 型面的粗铣,2D 轮廓的粗铣并按图点导柱孔坐标。
待粗铣完成后转钳工预钻底孔,单边留5-6毫米余量。
4. 粗铣完成后转精铣数控机床上完成型面的精加工,2D 轮廓的精加工,精镗导柱孔。
5. 为保证切边模的加工精度2D 轮廓的精加工与导柱孔的精加工应同时一次加工.如果是切边带冲孔的模具,也要同时一次加工凹模套孔。
6. 图纸不特别规定的,导柱孔,导板的防反位置都在下模,F 向的右下角。
3.上模座废料刀块,一般单独加工型面刃口后钳工配组型面刃口 凸模镶块,单独铣好底面后组上下模座上加工型面及轮廓防反的导柱,在下模F 向的右下角,左右对称件也一样4.上模压料板5。
上模刀块与上模座组装图导套孔与导套,镗好导套孔后镶入导套切边刀块安装面切边刀块安装背托与上模压料板外导配合的内导板面上模冲头安装面,加工时实际尺寸改动,必须记录压料板2D 轮廓 压料板固定孔 耐磨板安装背托压料板底面压料板3D 大型面耐磨板6.上模座及切边刀块,异型冲头,压料板总装图上模的加工流程1.先把上模座的各加工面,安装面加工到尺寸。
加工好压料板的底面及与模座配合的导板面。
切边刀块型面比压料板高8毫米,作为刃口的切入量上模异型凸冲头,型面比压料板高8毫米,作为刃口的切入量,2D 轮廓线,加工时按程序,应对零加工不留余量与下模配合切料的上模废料刀口板件的切边2D 轮廓线,加工时按程序,应留0.3毫米余量 镶块接口2.机加工先铣好镶块底面及镶块背托,按模座上镶块每块的位置刻线,与每块镶块上的刻线配铣刀块接口。
每块镶块接口留0。
3毫米给钳工配组立。
3.模座上没有镶块刻线的,按图纸测量或上数控测试2D轮廓后配铣背托及接口。
如果组立前上数控测试,测试后按图点导柱孔坐标。
待转钳工预钻底孔,单边留5-6毫米余量4.把压料板及刀块都配组立好后,先把刀块装在上模上固定紧固,转数控在粗铣机床上完成刀块粗加工,拆下刀块组上压料板,完成压料板的粗加工,完成所有的粗加工后转机铣机床精加工。
先精加工好压料板然后吊出压料板在精加工刀块,精镗导套孔。
5.加工型面如型面不够加工,或抬高了必须记录准确的数值,好让工艺员下对策补救.6.注意装压料板时按图纸到底垫块厚度垫在压料板下面,有时为了方便加工2D轮廓,到底垫块厚度会比图纸高,厚度是多少必须明确标示,数控加工时垫块高多少就抬高多少加工.7。
总成剖视图压料板安装面及到底垫块安装面9。
OP20总装图合模时放安全垫块,方便合模三.OP30翻边模1.下模座翻边镶块安装面1.下模顶出器压料板的2D分模线耐磨板安装背托及耐磨板3.下模翻边刀块翻边刀块4.下模翻边刀块与压料板组合图5.上模座6。
上模座与上模镶块组合图压料板镶块安装面翻边凸模7。
OP30翻边模总装图翻边下模刀块与压料板的组合加工流程7.先把下模座的各加工面,安装面加工到尺寸。
加工好压料板的底面及与模座配合的导板面。
8.机加工先铣好镶块底面及镶块背托,钳工按模座上镶块每块的位置刻线,与每块镶块上的刻线对齐组立。
9.模座上没有镶块刻线的,按图纸测量或上数控测试2D轮廓后配铣背托及接口。
如果组立前上数控测试,测试后如果有导柱孔按图点出导柱孔坐标.待转钳工预钻底孔,单边留5-6毫米余量.10.把压料板及刀块都配组立好后,先把刀块装在下模上固定紧固,转数控在粗铣机床上完成翻边刀块2D分模线的粗精加工,拆下刀块组上压料板,完成压料板的2D分模线的粗精加工,把翻边刀块与压料板组立在下模上固定紧固,一起加工3D型面.11.在粗铣数控机床上完成型面,导板的粗铣,Q25。
Q20球刀的预清角, Q25.Q20球刀的预清角留0.3毫米余量上进行二次清角在精铣机床上加工.12.加工型面如型面不够加工,或余量太多需要抬高必须记录准确的数值,好让工艺员下对策解决由此引的问提点。