切削参数的选择
切削参数选择

3/57
工程实训中心
2.进给速度 2.进给速度F (mm/min) 进给速度F (1)工件材料的强度和硬度越高,每齿进给量越小。 工件材料的强度和硬度越高,每齿进给量越小。 (2)工件表面粗糙度要求越高,每齿进给量越小。 工件表面粗糙度要求越高,每齿进给量越小。
加工中心综合实训
切 削 参 数 选 择
主讲:王 飞 主讲:
1/57
工程实训中心
讲授内容:
一、主轴转速 二、进给速度 三、切削参数参考表 四、零件加工顺序
Байду номын сангаас
2/57
工程实训中心
1.主轴转速 1.主轴转速n(r/min) 主轴转速n r/min)
1000v 主轴转速一般根据切削速度V来选定。 主轴转速一般根据切削速度V来选定。 n = πd
6/57
工程实训中心
(13)调头装夹,用平行垫铁保证上下表面的平行度 13)调头装夹, 14) (14)确定工件坐标系 15)铣平面, (15)铣平面,保证工件厚度尺寸 16) (16)确定所用刀具的长度补偿 17)去除余量,利用以加工完毕的外表面, (17)去除余量,利用以加工完毕的外表面,精确确定工件坐标系 18) (18)按要求加工各轮廓
7/57
工程实训中心
8/57
工程实训中心
F = f ⋅Z ⋅n
Z
常用进给速度参考表: 常用进给速度参考表:
4/57
工程实训中心
3.高速钢立铣刀加工铝材切削参数参考表: 3.高速钢立铣刀加工铝材切削参数参考表: 高速钢立铣刀加工铝材切削参数参考表
5/57
工程实训中心
3.零件加工步骤: 3.零件加工步骤: 零件加工步骤
切削参数选择
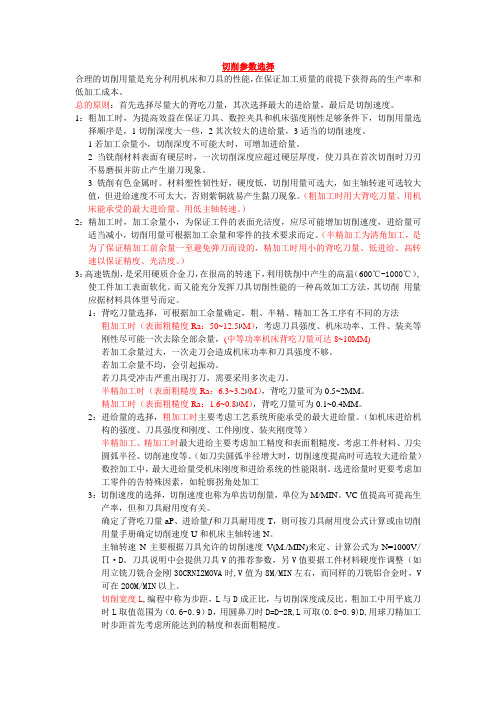
切削参数选择合理的切削用量是充分利用机床和刀具的性能,在保证加工质量的前提下获得高的生产率和低加工成本。
总的原则:首先选择尽量大的背吃刀量,其次选择最大的进给量,最后是切削速度。
1:粗加工时,为提高效益在保证刀具、数控夹具和机床强度刚性足够条件下,切削用量选择顺序是,1切削深度大一些,2其次较大的进给量,3适当的切削速度。
1若加工佘量小,切削深度不可能大时,可增加进给量。
2当铣削材料表面有硬层时,一次切削深度应超过硬层厚度,使刀具在首次切削时刀刃不易磨损并防止产生崩刀现象。
3铣削有色金属时。
材料塑性韧性好,硬度低,切削用量可选大,如主轴转速可选较大值,但进给速度不可太大,否则紫铜就易产生黏刀现象。
(粗加工时用大背吃刀量、用机床能承受的最大进给量、用低主轴转速。
)2:精加工时,加工佘量小,为保证工件的表面光洁度,应尽可能增加切削速度,进给量可适当减小,切削用量可根据加工佘量和零件的技术要求而定。
(半精加工为清角加工,是为了保证精加工前佘量一至避免弹刀而设的,精加工时用小的背吃刀量、低进给、高转速以保证精度、光洁度。
)3:高速铣削,是采用硬质合金刀,在很高的转速下,利用铣削中产生的高温(600℃-1000℃),使工件加工表面软化。
而又能充分发挥刀具切削性能的一种高效加工方法,其切削用量应据材料具体型号而定。
1:背吃刀量选择,可根据加工佘量确定,粗、半精、精加工各工序有不同的方法粗加工时(表面粗糙度Ra:50~12.5µM),考虑刀具强度、机床功率、工件、装夹等刚性尽可能一次去除全部佘量,(中等功率机床背吃刀量可达8~10MM)若加工佘量过大,一次走刀会造成机床功率和刀具强度不够。
若加工佘量不均,会引起振动。
若刀具受冲击严重出现打刀,需要采用多次走刀。
半精加工时(表面粗糙度Ra:6.3~3.2µM),背吃刀量可为0.5~2MM。
精加工时(表面粗糙度Ra:1.6~0.8µM),背吃刀量可为0.1~0.4MM。
机械加工中数控机床刀具切削参数的选择方法

机械加工中数控机床刀具切削参数的选择方法引言:数控机床作为现代制造业中不可或缺的关键设备, 切削参数的选择直接影响加工质量和效率。
机械加工中,数控机床刀具的切削参数选择是非常重要的一个环节,它直接影响到加工质量、加工效率和刀具寿命。
因此,正确选择切削参数对于提高加工效率和降低加工成本具有重要意义。
本文将介绍机械加工中数控机床刀具切削参数的选择方法。
一、切削速度的选择切削速度是数控机床刀具切削过程中最重要的一个参数,对于切削质量、切削力、切削温度等方面都有直接影响。
选择切削速度主要取决于工件材料的硬度、切削刃口的材料和硬度以及数控机床的能力。
一般来说,硬度较高的材料需要较低的切削速度,而硬度较低的材料则可以选择较高的切削速度。
在合理范围内选择切削速度,不仅可以提高加工效率,还可以保证刀具寿命和加工质量。
切削速度的选择应根据材料和刀具的特性进行调整,经验公式可以作为初步的参考。
二、进给率的选择进给率是切削过程中刀具每单位时间切削的长度,也是衡量切削效率的重要指标。
进给率的选择应考虑切削工艺、切削质量要求以及刀具的特性。
通常情况下,进给率过大容易导致过载,切削力过大,切削质量下降;进给率过小则会浪费加工时间,低效率。
因此,选择合适的进给率对于保持加工质量和提高加工效率至关重要。
在选择进给率时,应考虑切削深度、材料的硬度以及机床的刚性等因素。
三、切削深度的选择切削深度是刀具进入工件的深度,它直接影响加工效率和切削力。
切削深度的选择应根据工件材料的硬度、机床的刚性、刀具的强度等因素综合考虑。
对于硬度较高的材料,一般采用较小的切削深度以减小切削力,避免刀具损坏。
而对于硬度较低的材料,可以适当增加切削深度以提高加工效率。
切削深度的选择过大或过小都会对加工效果带来不利影响,应根据实际情况进行综合考虑。
四、切削角度的选择切削角度是切削刃部分与工件接触的角度。
切削角度的选择要根据切削力、切削声音、加工精度等因素进行综合考虑。
数控机床切削参数的选择与优化
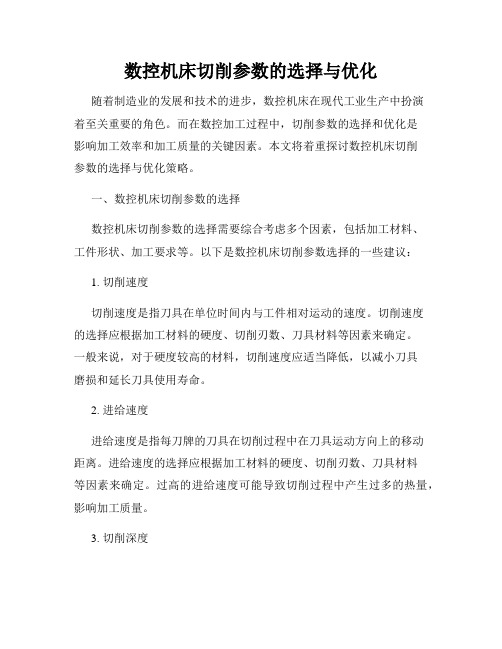
数控机床切削参数的选择与优化随着制造业的发展和技术的进步,数控机床在现代工业生产中扮演着至关重要的角色。
而在数控加工过程中,切削参数的选择和优化是影响加工效率和加工质量的关键因素。
本文将着重探讨数控机床切削参数的选择与优化策略。
一、数控机床切削参数的选择数控机床切削参数的选择需要综合考虑多个因素,包括加工材料、工件形状、加工要求等。
以下是数控机床切削参数选择的一些建议:1. 切削速度切削速度是指刀具在单位时间内与工件相对运动的速度。
切削速度的选择应根据加工材料的硬度、切削刃数、刀具材料等因素来确定。
一般来说,对于硬度较高的材料,切削速度应适当降低,以减小刀具磨损和延长刀具使用寿命。
2. 进给速度进给速度是指每刀牌的刀具在切削过程中在刀具运动方向上的移动距离。
进给速度的选择应根据加工材料的硬度、切削刃数、刀具材料等因素来确定。
过高的进给速度可能导致切削过程中产生过多的热量,影响加工质量。
3. 切削深度切削深度是指刀具在切削过程中与工件接触的最大深度。
切削深度的选择应考虑加工材料的硬度、切削刃数、刀具材料等因素。
较小的切削深度可以减小切削力和切削温度,提高加工精度。
4. 切削方式切削方式包括铣削、车削、钻削等。
选择合适的切削方式可以提高加工效率和加工质量。
对于不同形状的工件,应选择适合的切削方式,以确保切削过程的稳定和切削力的均匀分布。
二、数控机床切削参数的优化除了选择合适的切削参数外,优化切削参数也能提高加工效率和加工质量。
以下是一些常用的数控机床切削参数优化策略:1. 刀具润滑刀具润滑是切削过程中的重要环节,它能减小切削力和摩擦,并提高刀具的使用寿命。
选择合适的切削液类型和使用方法有助于减少切削过程中的热量积累和切削力的产生。
2. 切削力监测与控制通过切削力的监测和控制,可以实时了解加工过程中的切削负荷情况,从而优化切削参数的选择。
采用合适的传感器和控制系统,能够更好地预测和调节切削过程中的切削力,提高加工效率和加工质量。
刀具及切削参数选择
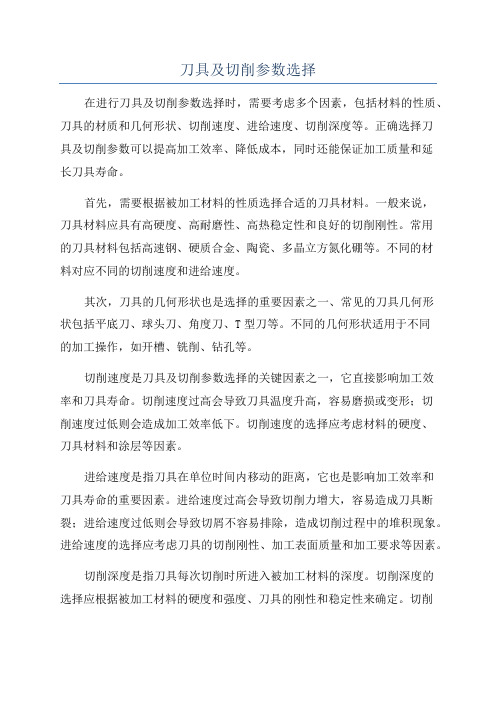
刀具及切削参数选择在进行刀具及切削参数选择时,需要考虑多个因素,包括材料的性质、刀具的材质和几何形状、切削速度、进给速度、切削深度等。
正确选择刀具及切削参数可以提高加工效率、降低成本,同时还能保证加工质量和延长刀具寿命。
首先,需要根据被加工材料的性质选择合适的刀具材料。
一般来说,刀具材料应具有高硬度、高耐磨性、高热稳定性和良好的切削刚性。
常用的刀具材料包括高速钢、硬质合金、陶瓷、多晶立方氮化硼等。
不同的材料对应不同的切削速度和进给速度。
其次,刀具的几何形状也是选择的重要因素之一、常见的刀具几何形状包括平底刀、球头刀、角度刀、T型刀等。
不同的几何形状适用于不同的加工操作,如开槽、铣削、钻孔等。
切削速度是刀具及切削参数选择的关键因素之一,它直接影响加工效率和刀具寿命。
切削速度过高会导致刀具温度升高,容易磨损或变形;切削速度过低则会造成加工效率低下。
切削速度的选择应考虑材料的硬度、刀具材料和涂层等因素。
进给速度是指刀具在单位时间内移动的距离,它也是影响加工效率和刀具寿命的重要因素。
进给速度过高会导致切削力增大,容易造成刀具断裂;进给速度过低则会导致切屑不容易排除,造成切削过程中的堆积现象。
进给速度的选择应考虑刀具的切削刚性、加工表面质量和加工要求等因素。
切削深度是指刀具每次切削时所进入被加工材料的深度。
切削深度的选择应根据被加工材料的硬度和强度、刀具的刚性和稳定性来确定。
切削深度过大会导致切削力增大,容易造成刀具断裂;切削深度过小则会导致加工效率低下。
此外,还需要考虑刀具的冷却方式和切削液的选择。
刀具在切削过程中会产生大量的热量,如果不及时冷却,会导致刀具温度过高,影响刀具寿命。
常见的冷却方式包括气体冷却、液体冷却和固体冷却等。
切削液的选择应考虑被加工材料的性质和切削过程中的润滑和冷却效果。
综上所述,刀具及切削参数选择是一个综合考虑材料性质、刀具几何形状、切削速度、进给速度、切削深度、冷却方式和切削液等多个因素的过程。
刀具及切削参数选择
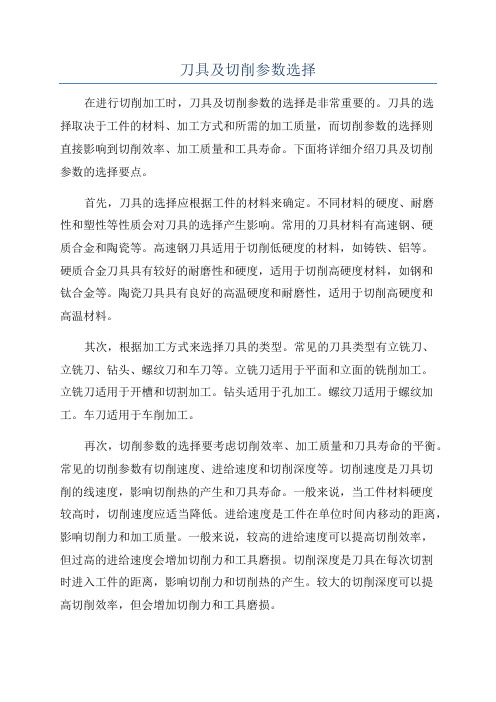
刀具及切削参数选择在进行切削加工时,刀具及切削参数的选择是非常重要的。
刀具的选择取决于工件的材料、加工方式和所需的加工质量,而切削参数的选择则直接影响到切削效率、加工质量和工具寿命。
下面将详细介绍刀具及切削参数的选择要点。
首先,刀具的选择应根据工件的材料来确定。
不同材料的硬度、耐磨性和塑性等性质会对刀具的选择产生影响。
常用的刀具材料有高速钢、硬质合金和陶瓷等。
高速钢刀具适用于切削低硬度的材料,如铸铁、铝等。
硬质合金刀具具有较好的耐磨性和硬度,适用于切削高硬度材料,如钢和钛合金等。
陶瓷刀具具有良好的高温硬度和耐磨性,适用于切削高硬度和高温材料。
其次,根据加工方式来选择刀具的类型。
常见的刀具类型有立铣刀、立铣刀、钻头、螺纹刀和车刀等。
立铣刀适用于平面和立面的铣削加工。
立铣刀适用于开槽和切割加工。
钻头适用于孔加工。
螺纹刀适用于螺纹加工。
车刀适用于车削加工。
再次,切削参数的选择要考虑切削效率、加工质量和刀具寿命的平衡。
常见的切削参数有切削速度、进给速度和切削深度等。
切削速度是刀具切削的线速度,影响切削热的产生和刀具寿命。
一般来说,当工件材料硬度较高时,切削速度应适当降低。
进给速度是工件在单位时间内移动的距离,影响切削力和加工质量。
一般来说,较高的进给速度可以提高切削效率,但过高的进给速度会增加切削力和工具磨损。
切削深度是刀具在每次切割时进入工件的距离,影响切削力和切削热的产生。
较大的切削深度可以提高切削效率,但会增加切削力和工具磨损。
此外,还应考虑冷却润滑剂的选择和使用。
合适的冷却润滑剂可以降低切削热的产生,减小工具磨损,提高加工质量。
综上所述,刀具及切削参数的选择需要考虑工件材料、加工方式和所需加工质量。
合理选择刀具类型和切削参数可以提高切削效率、加工质量和工具寿命。
在实际应用中,还需要根据具体情况进行调整和优化。
常用刀具的切削参数
常用刀具的切削参数刀具切削参数是指在切削过程中,对刀具进行设置和调整的一系列参数。
这些参数包括切削速度、进给速度、切削深度、切削角度等,它们的选择和调整直接影响到切削效果和刀具寿命。
下面是常用刀具的切削参数的一些介绍:1. 切削速度(Cutting Speed):切削速度是指刀具在切削过程中移动的速度,一般用单位时间内刀具切削的长度来表示。
切削速度的选择取决于工件材料的硬度和切削材料的种类。
一般来说,硬度较高的材料需要较低的切削速度,而硬度较低的材料则可以使用较高的切削速度。
2. 进给速度(Feed Rate):进给速度是指刀具在切削过程中每分钟进给到工件上的距离。
进给速度的选择取决于工件的材料和切削操作的要求。
较低的进给速度可以获得更好的切削质量,而较高的进给速度可以提高生产效率。
3. 切削深度(Depth of Cut):切削深度是指刀具切削时每次切削进入工件的深度。
切削深度的选择需要考虑工件材料的硬度和切削工具的强度。
一般来说,较硬的材料需要较小的切削深度,而较软的材料则可以选择较大的切削深度。
4. 切削角度(Cutting Angle):切削角度是指刀具切削刃与工件表面之间的夹角。
切削角度的选择取决于工件材料的硬度和切削操作的要求。
一般来说,较硬的材料需要较大的切削角度,而较软的材料则可以选择较小的切削角度。
5. 切削液(Cutting Fluid):切削液是在切削过程中起冷却、润滑和清洁作用的液体。
切削液的选择取决于切削材料的种类和切削条件的要求。
常见的切削液有切削油、切削液和切削蜡等。
6. 切削力(Cutting Force):切削力是指切削过程中刀具对工件施加的力。
切削力的大小受到切削参数的影响,包括切削速度、进给速度、切削深度和切削角度等。
合理选择切削参数可以降低切削力,提高切削效率和刀具寿命。
7. 切削温度(Cutting Temperature):切削温度是指刀具和工件在切削过程中产生的热量。
数控机床加工不同硬度材料的最佳切削参数选择方法
数控机床加工不同硬度材料的最佳切削参数选择方法引言:数控机床作为现代制造业中的重要设备,广泛应用于各种工业领域。
在加工过程中,选择合适的切削参数对于实现高效、高质量的加工非常重要。
本文将介绍数控机床加工不同硬度材料的最佳切削参数选择方法,以帮助读者在实践中获得更好的加工效果。
一、硬度对切削参数的影响切削硬度是指材料对刀具切削时的硬度,硬度越高通常表明切削难度越大。
硬度对切削参数的选择有以下几个方面的影响:1. 切削速度:硬度较低的材料可以使用较高的切削速度,以提高加工效率。
而对于硬度较高的材料,则需要采用较低的切削速度,这样能减少切削时的磨损,提高刀具使用寿命。
2. 进给速度:硬度较低的材料可以采用较大的进给速度,以加快切削进程。
而对于硬度较高的材料,需要降低进给速度,以减少切削时的切屑形成和排出的困难。
3. 切削深度:对于硬度较低的材料,可以选择较大的切削深度,以减少加工时间。
而对于硬度较高的材料,则需要采用较小的切削深度,以避免刀具过度磨损和工件变形。
二、选择最佳切削参数的方法正确选择切削参数可以提高加工效率、降低成本,并保证加工质量。
以下是一些建议的方法:1. 参考切削参数手册:数控机床切削参数手册是宝贵的参考资料,其中列出了不同硬度材料的推荐切削参数。
可以根据工件材料的硬度,查找手册并参考建议的切削参数进行调整。
2. 经验法则:经验法则可以作为初步选择切削参数的参考。
例如,对于硬度较低的材料,可以尝试切削速度为材料硬度的2倍,进给速度为材料硬度的0.5倍,切削深度为3mm。
然后根据实际情况进行微调。
3. 切削试验:切削试验是一种有效的方法,可以根据试验结果来选择最佳切削参数。
在实际加工之前,可以准备一块与工件材料相似的试验材料,进行切削试验,并记录加工时间、表面粗糙度、切削力等参数。
根据实验结果调整切削参数,以得到最佳加工效果。
4. 刀具选择:选择合适的刀具也是选择最佳切削参数的重要因素。
数控铣削加工工艺中切削参数的选择与优化
数控铣削加工工艺中切削参数的选择与优化数控铣削加工工艺中的切削参数在数控铣削加工工艺中,切削参数的选择对于加工过程和零件的最终质量具有重要影响。
本文将介绍数控铣削加工工艺中常见的切削参数,包括切削深度、主轴转速和进给速度。
1.切削深度切削深度是指刀具在工件上切削的垂直距离,通常以槽深、孔深等方式表示。
在数控铣削加工中,切削深度的选择需要考虑工件的材质、硬度和刀具的切削性能等多个因素。
切削深度的合理选择可以影响加工效率、刀具磨损和零件质量。
一般情况下,对于材质较软、硬度较低的工件,可适当加大切削深度;而对于材质较硬、硬度较高的工件,则应适当减小切削深度。
2.主轴转速主轴转速是指机床主轴每分钟旋转的圈数,它直接影响到切削过程中的切削速度和切削力。
在数控铣削加工中,主轴转速的快慢可以影响加工效率、表面粗糙度和刀具磨损。
主轴转速的选择应综合考虑工件的材质、硬度和刀具的切削性能。
一般情况下,对于材质较软、硬度较低的工件,可选择较高的主轴转速;而对于材质较硬、硬度较高的工件,则应选择较低的主轴转速。
此外,还需要根据刀具的切削性能选择合适的转速,以避免刀具磨损和零件质量的下降。
3.进给速度进给速度是指在加工过程中,机床工作台或刀具在给定时间内移动的距离。
它影响到切削过程中的切削厚度和切削效率。
在数控铣削加工中,进给速度的选择需要考虑工件的材质、硬度和刀具的切削性能。
一般来说,对于材质较软、硬度较低的工件,可选择较高的进给速度;而对于材质较硬、硬度较高的工件,则应选择较低的进给速度。
此外,还需要根据刀具的切削性能选择合适的进给速度,以确保切削过程的稳定和零件质量的提高。
在选择进给速度时,还需注意机床的额定负载和运动惯性等因素的影响。
如果进给速度过高,可能会导致机床负载过大,从而影响机床的稳定性和使用寿命。
因此,在选择进给速度时,需要进行实验和调整,以确保达到最佳的加工效果。
总之,数控铣削加工工艺中的切削参数选择需要综合考虑工件的材质、硬度和刀具的切削性能等因素。
切削参数优化范文
切削参数优化范文一、切削参数的选择和优化方法切削参数的选择和优化是一个复杂的过程,需要考虑到被加工材料的硬度、切削工具的材质和几何形状、切削速度和进给速度等因素。
常用的切削参数包括切削速度、进给速度、切削深度和切削宽度。
(一)试刀法试刀法是一种常用的切削参数选择的方法,通过试刀来确定最佳的切削参数。
试刀前需保证刀具采用合适的刀尖半径,试刀时应逐步调整切削速度、进给速度、切削深度和切削宽度,记录下每种参数对加工表面质量的影响,最终选择最佳的切削参数。
(二)试件法试件法是另一种常用的切削参数选择的方法,通过在试件上进行不同切削参数的加工,然后测量加工表面的质量指标,如表面粗糙度、加工硬度等,最终选择最佳的切削参数。
试件的材料和几何形状需要与实际加工件相似,以确保试削结果的准确性。
(三)数值模拟法数值模拟法是一种现代化的切削参数优化方法,通过建立数值模型,通过数值模拟分析不同切削参数对加工过程和加工表面质量的影响。
数值模拟法可以有效地提前预测切削参数对加工结果的影响,减少试刀试件的数量和试验时间,提高优化的效率和准确性。
二、切削参数的优化步骤切削参数的优化包括参数的选择和调整两个步骤。
(一)参数的选择1.切削速度的选择:切削速度的选择需要考虑材料的硬度、切削工具的材质和几何形状等因素。
一般来说,对于硬度较高的材料,需要选择较低的切削速度;对于切削刚度较低的加工工具,应采用较低的切削速度。
2.进给速度的选择:进给速度的选择需要考虑到切削力和加工表面质量。
较大的进给速度会增加切削力,但可以提高加工效率;较小的进给速度可以获得较好的表面质量,但加工效率较低。
在实际操作中,需要综合考虑进给速度和加工效率的平衡。
3.切削深度和切削宽度的选择:切削深度和切削宽度的选择需要考虑到刀具的切削能力和加工表面质量的要求。
在选择切削深度和切削宽度时,需要确保切削力在刀具的切削能力范围内,并满足加工表面质量的要求。
(二)参数的调整在确定了初步的切削参数之后,还需要进一步调整和优化。
- 1、下载文档前请自行甄别文档内容的完整性,平台不提供额外的编辑、内容补充、找答案等附加服务。
- 2、"仅部分预览"的文档,不可在线预览部分如存在完整性等问题,可反馈申请退款(可完整预览的文档不适用该条件!)。
- 3、如文档侵犯您的权益,请联系客服反馈,我们会尽快为您处理(人工客服工作时间:9:00-18:30)。
Application range
“Start value”
Utilize the potential of ap - to reduce number or cuts fn - for shorter cutting time vc - for best tool life Compensation of cutting speed for tool life
切削参数 –
公式
Vc= 3.14 xD xRPM 1000 V=Vc xap xfr(mm3/min) L Time= fr xN Vc xap xfr xkc P= 60037.2 F力=Kc xfr xap T= F力 x(D/2) =P x9549/RPM
练习: 车削奥氏体不锈钢外圆, 工件硬度HB200, 工件直 径75mm,切深3mm,走刀 量0.2mm/r, 切削速度 230m/min, 材料单位切削 力为2900N/mm2,加工长 度为100mm
G90G54G40G17G49 S1000M03 G00Z100. G00X0Y0. G01Z0.F500 G01Y10. #1=0 WHILE[#1GE-20] DO1 G03Z[#1-1] I0. J-10. #1=#1-1 END1 G03I0.J-10. G01X0.Y0. G00Z100. M30
Tool life (Mins.) Correction factors
Speed range
10 min. tool life 15 min. tool life 30 min. tool life
The basis of a tool lifeΒιβλιοθήκη 主样本金属切削技术指南
FANUC系统螺旋插补铣孔程序
ap fn vc
1 2 3
Depth of cut
(inches)
Feed
(inches/rev)
Cutting speed
(surface feet/min)
Workpiece materials Application type Machining conditions
A.刀片盒和CoroKey
切削参数 –
参数选择的方法
一、根据刀片盒选择切削参数 二、参考样本上切削参数一栏中的切削速度推荐值 三、Cutting data module切削参数选择器
A.刀片盒和CoroKey
Complete information on CoroKey label for correct application of insert Product-specific cutting data
切削参数
车削与镗削:车削速度Vc, 刀片切深ap每转走刀量fn; 车削与镗削 铣削: 铣削:铣削速度Vc, 铣刀轴向切深ap, 径向切深ae,每齿走刀量fz; 钻削:钻削速度Vc, 钻头每转进刀量fr 钻削
切削参数
Q = ap x fr (z) x Vc
切削参数 –
切削速度
Q = ap × fn × vc