放电等离子烧结
放电等离子体烧结

放电等离子体烧结
放电等离子体烧结是一种先进的材料加工技术,通过放电等离子体的高温、高能量作用,实现材料的烧结和熔融,从而制备出具有优异性能的复杂形状零件。
这种技术在金属、陶瓷、复合材料等领域都有着广泛的应用。
放电等离子体烧结技术的原理是利用高压电场使气体放电产生等离子体,等离子体在电场的作用下加热材料并使其烧结。
这种烧结方式具有高温、高能量、高速等特点,可以实现材料的快速烧结和熔融,从而大大提高材料的致密性和机械性能。
在金属材料加工中,放电等离子体烧结可以实现对金属粉末的高效烧结,制备出高强度、高硬度的金属零件。
同时,还可以实现对金属表面的改性处理,提高金属的耐磨性和耐腐蚀性。
在陶瓷材料加工中,放电等离子体烧结可以实现对陶瓷粉末的快速烧结,制备出高强度、高韧性的陶瓷制品。
在复合材料加工中,放电等离子体烧结可以实现对复合材料的烧结和熔融,制备出具有优异性能的复合材料制品。
放电等离子体烧结技术具有许多优点,如烧结速度快、烧结温度高、烧结效果好等。
与传统的烧结方法相比,放电等离子体烧结可以大大缩短加工周期,提高生产效率,降低生产成本。
此外,放电等离子体烧结还可以实现对材料的局部加热和局部烧结,实现对复杂形状零件的加工,提高材料的利用率和加工精度。
随着科技的不断进步,放电等离子体烧结技术在材料加工领域的应用将会越来越广泛。
通过不断的研究和创新,放电等离子体烧结技术将会为材料加工领域带来更多的突破和进步,为人类社会的发展做出更大的贡献。
相信在不久的将来,放电等离子体烧结技术将会成为材料加工领域的重要技术,为人类创造出更多的奇迹。
《放电等离子烧结制备MAX-cBN复合材料》

《放电等离子烧结制备MAX-cBN复合材料》篇一一、引言在当前的工业应用中,高性能的复合材料以其卓越的物理和化学性能受到广泛关注。
其中,MAX-cBN(由MAX相陶瓷和立方氮化硼(cBN)组成的复合材料)因其高硬度、高热导率和良好的化学稳定性,在机械加工、电子封装和热管理等领域具有广泛的应用前景。
本文将详细介绍放电等离子烧结技术在制备MAX-cBN复合材料中的应用及其优势。
二、放电等离子烧结技术概述放电等离子烧结(SPS)技术是一种利用脉冲电流进行加热的固相烧结方法。
它利用强大的电场产生高能量密度等离子体,将颗粒间隙内的空气排净,通过产生的焦耳热直接作用于颗粒,从而达到烧结目的。
这种方法能够有效地减小颗粒尺寸、增强材料性能、缩短制备周期。
三、MAX-cBN复合材料的制备(一)材料选择与配比在制备MAX-cBN复合材料时,选择合适的MAX相陶瓷和cBN粉末是关键。
MAX相陶瓷具有优异的力学性能和热稳定性,而cBN则以其高硬度、高热导率和良好的化学稳定性著称。
通过合理的配比,可以获得具有优异性能的MAX-cBN复合材料。
(二)放电等离子烧结过程在放电等离子烧结过程中,首先将MAX相陶瓷和cBN粉末混合均匀,然后放入模具中。
通过施加一定的压力和电压,利用脉冲电流产生的高能量密度等离子体进行烧结。
在烧结过程中,颗粒间的结合力逐渐增强,形成致密的复合材料。
四、放电等离子烧结技术的优势(一)高效率:放电等离子烧结技术能够在短时间内完成烧结过程,大大缩短了制备周期。
(二)低能耗:由于等离子体直接作用于颗粒,使得能量利用率高,降低了能耗。
(三)提高性能:放电等离子烧结技术可以减小颗粒尺寸,增强材料性能。
同时,高能量密度等离子体的作用使得颗粒间的结合力增强,有利于获得致密的复合材料。
五、实验结果与讨论通过放电等离子烧结技术制备的MAX-cBN复合材料具有优异的性能。
X射线衍射(XRD)分析表明,材料具有明显的MAX相和cBN相的特征峰;扫描电子显微镜(SEM)观察发现,材料具有致密的微观结构,颗粒间结合紧密;硬度测试表明,材料的硬度远高于单一MAX相陶瓷或cBN;热导率测试也显示出了良好的导热性能。
实验九放电等离子体烧结(SPS)
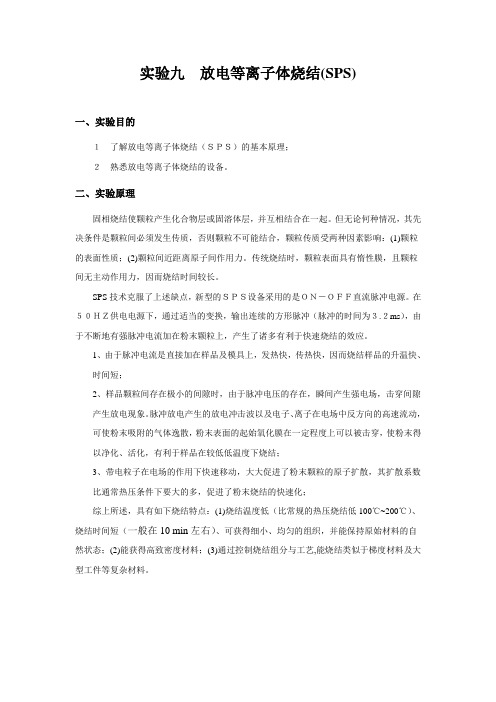
实验九放电等离子体烧结(SPS)一、实验目的1了解放电等离子体烧结(SPS)的基本原理;2熟悉放电等离子体烧结的设备。
二、实验原理固相烧结使颗粒产生化合物层或固溶体层,并互相结合在一起。
但无论何种情况,其先决条件是颗粒间必须发生传质,否则颗粒不可能结合,颗粒传质受两种因素影响:(1)颗粒的表面性质;(2)颗粒间近距离原子间作用力。
传统烧结时,颗粒表面具有惰性膜,且颗粒间无主动作用力,因而烧结时间较长。
SPS技术克服了上述缺点,新型的SPS设备采用的是ON-OFF直流脉冲电源。
在50HZ供电电源下,通过适当的变换,输出连续的方形脉冲(脉冲的时间为3.2ms),由于不断地有强脉冲电流加在粉末颗粒上,产生了诸多有利于快速烧结的效应。
1、由于脉冲电流是直接加在样品及模具上,发热快,传热快,因而烧结样品的升温快、时间短;2、样品颗粒间存在极小的间隙时,由于脉冲电压的存在,瞬间产生强电场,击穿间隙产生放电现象。
脉冲放电产生的放电冲击波以及电子、离子在电场中反方向的高速流动,可使粉末吸附的气体逸散,粉末表面的起始氧化膜在一定程度上可以被击穿,使粉末得以净化、活化,有利于样品在较低低温度下烧结;3、带电粒子在电场的作用下快速移动,大大促进了粉末颗粒的原子扩散,其扩散系数比通常热压条件下要大的多,促进了粉末烧结的快速化;综上所述,具有如下烧结特点:(1)烧结温度低(比常规的热压烧结低100℃~200℃)、烧结时间短(一般在10 min左右)、可获得细小、均匀的组织,并能保持原始材料的自然状态;(2)能获得高致密度材料;(3)通过控制烧结组分与工艺,能烧结类似于梯度材料及大型工件等复杂材料。
图1、SPS实验装置图图2、SPS烧结阶段图3、SPS烧结原理图4、原子扩散示意图5、SPS烧结过程放电机理三、仪器与药品仪器:SPS-1050药品:SPS可烧结的样品极多,大致可分以下几大类:作为实验演示,选用药品:Al2O3、SrFe12O19在氧化铝陶瓷基体中生成硬磁铁氧体粒子,通过控制工艺条件使氧化铝与硬磁铁氧体粒子在界面上形成部分固溶的复合材料。
放电等离子体烧结技术课件
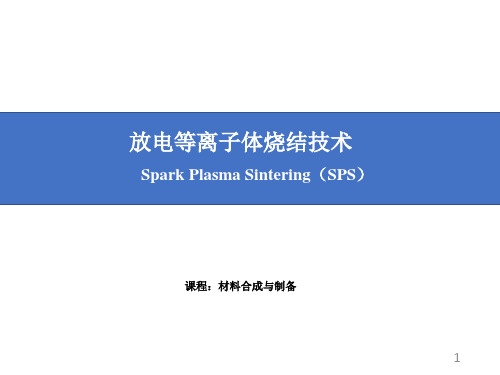
▪ 2000年6月武汉理工大学购置了国内首台SPS装置。 ▪ 随后上海硅酸盐研究所、清华大学、武汉大学等高校及科研机构也相继引进了
SPS装置, 用来进行相关的科学研究。
3
放电等离子体烧结(SPS)简介
由于其独特的烧结机理, SPS技术具有升温速度快、烧 结温度低、烧结时间短、节能环保等特点, SPS已广泛 应用于纳米材料、梯度功能材料、金属材料、磁性材料 、复合材料、陶瓷等材料的制备。
8
放电等离子烧结(SPS)的应用
将1700 C下用SPS分别烧结3 min和5 min的样品与常规方法在1500 C烧结 72 h的样品对比可以看出使用SPS方法得到的样品所用时间更短, 致密性更 好。
放电等离子体烧结技术
Spark Plasma Sintering(SPS)
课程:材料合成与制备
1
目录
1. 放电等离子烧结(SPS)简介 2. 放电等离子烧结(SPS)的基本原理 3. 放电等离子烧结(SPS)的优缺点 4. 放电等离子烧结(SPS)的应用
2
放电等离子体烧结(SPS)简介
SPS的发展
▪ 1930年, 美国科学家提出利用等离子体脉冲电流烧结原理, 直到1965年, 脉冲电流烧
结技术才在美、日等国得到应用。日本获得了SPS技术的专利, 但当时未能解决该 技术存在的生产效率低等问题, 因此SPS技术没有得到推广应用。
▪ SPS技术的推广应用是从上个世纪80年代末期开始的。 ▪ 1988年日本研制出第一台工业型SPS装置, 并在新材料研究领域内推广应用。 ▪ 由于SPS技术具有快速、低温、高效率等优点, 近几年国内外许多大学和科研机构
SPS烧结原理
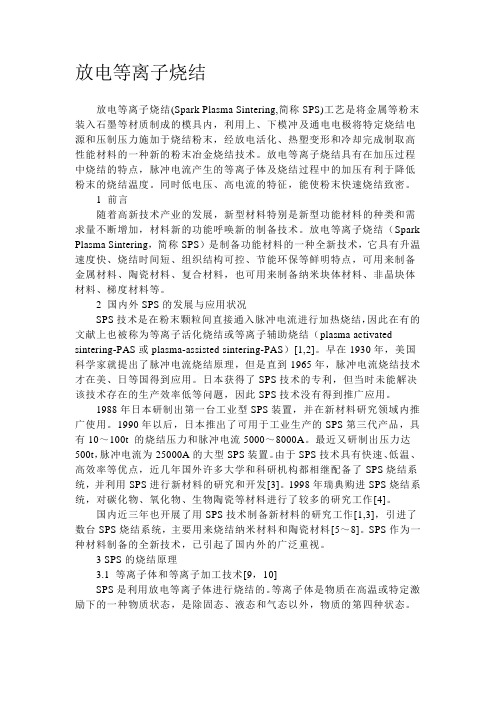
放电等离子烧结放电等离子烧结(Spark Plasma Sintering,简称SPS)工艺是将金属等粉末装入石墨等材质制成的模具内,利用上、下模冲及通电电极将特定烧结电源和压制压力施加于烧结粉末,经放电活化、热塑变形和冷却完成制取高性能材料的一种新的粉末冶金烧结技术。
放电等离子烧结具有在加压过程中烧结的特点,脉冲电流产生的等离子体及烧结过程中的加压有利于降低粉末的烧结温度。
同时低电压、高电流的特征,能使粉末快速烧结致密。
1 前言随着高新技术产业的发展,新型材料特别是新型功能材料的种类和需求量不断增加,材料新的功能呼唤新的制备技术。
放电等离子烧结(Spark Plasma Sintering,简称SPS)是制备功能材料的一种全新技术,它具有升温速度快、烧结时间短、组织结构可控、节能环保等鲜明特点,可用来制备金属材料、陶瓷材料、复合材料,也可用来制备纳米块体材料、非晶块体材料、梯度材料等。
2 国内外SPS的发展与应用状况SPS技术是在粉末颗粒间直接通入脉冲电流进行加热烧结,因此在有的文献上也被称为等离子活化烧结或等离子辅助烧结(plasma activated sintering-PAS或plasma-assisted sintering-PAS)[1,2]。
早在1930年,美国科学家就提出了脉冲电流烧结原理,但是直到1965年,脉冲电流烧结技术才在美、日等国得到应用。
日本获得了SPS技术的专利,但当时未能解决该技术存在的生产效率低等问题,因此SPS技术没有得到推广应用。
1988年日本研制出第一台工业型SPS装置,并在新材料研究领域内推广使用。
1990年以后,日本推出了可用于工业生产的SPS第三代产品,具有10~100t 的烧结压力和脉冲电流5000~8000A。
最近又研制出压力达500t,脉冲电流为25000A的大型SPS装置。
由于SPS技术具有快速、低温、高效率等优点,近几年国外许多大学和科研机构都相继配备了SPS烧结系统,并利用SPS进行新材料的研究和开发[3]。
放电等离子烧结技术

放电等离子烧结技术概述放电等离子烧结技术是一种利用放电等离子体瞬间高温作用,将微米尺寸的粒子连结成块状材料的先进烧结工艺。
该技术可应用于金属、陶瓷和高分子材料的制备,广泛应用于航空航天、汽车工业、电子器件等领域。
原理放电等离子烧结技术主要依靠高能电子束、激光束或电弧产生的等离子体,对粉末进行加热、熔化、溶胶-凝胶相变及凝固等过程。
其主要步骤包括放电等离子体生成、能量传递、粉末加热和冷却固化。
1.放电等离子体生成:通过施加电弧、电子束或激光束,将电能转化为热能,形成高电离度的等离子体。
此过程会产生高温和高压的环境,使粉末表面瞬间熔化。
2.能量传递:放电等离子体中的高能电子、电荷、能量和动量会在粉末中传递。
高能电子的轰击使粉末中的原子、分子发生能级跃迁,从而引发化学反应、电子交换和原子结构的变化。
这些能量和动量的传递是改变粉末性质、形成块状材料的关键。
3.粉末加热:放电等离子体释放的能量使粉末中的粒子加热,粒子间的距离减小,表面融化形成胶体。
同时,粉末中的化学反应使胶体具有一定的粘结力,使粉末颗粒开始结合。
4.冷却固化:当放电停止时,粉末开始冷却。
冷却过程中,胶体迅速凝固,形成粒子间的连接。
这些连接在冷却固化后形成比较牢固的固结区,从而构成块状材料。
优点和应用放电等离子烧结技术具有以下优点:•高效性:放电等离子体的高能量传输和快速冷却固化过程,使得烧结时间大大缩短,提高了生产效率。
•成型性:该技术可实现复杂形状、高密度、均匀结合的材料制备,满足不同行业的需求。
•可控性:通过调整放电参数和粉末性质,可以控制物质的相变过程和烧结结构,达到所需的性能要求。
•应用广泛:放电等离子烧结技术可应用于制备各种材料,包括金属、陶瓷和高分子材料。
在航空航天、汽车工业、电子器件等领域有着广泛应用。
发展趋势放电等离子烧结技术在材料科学和工程领域的研究和应用仍在不断发展。
未来的发展趋势有:1.新材料研究:随着新材料的涌现,放电等离子烧结技术将继续为新材料的研发和制备提供有力的手段。
放电等离子体烧结技术

1 放电等离子体烧结的工艺 1.1放电等离子体烧结的设备
一般放电等离子体烧结设备主要由三部分组成
产生单轴向压 力的装置和烧 结模具,压力 装置可根据烧 结材料的不同 施加不同的压 力;
脉冲电流发生 器,用来产生 等离子体对材 料进行活化处 理
电阻加热设备
材料合成与制备
SPS装置的结构示意图
图1 为其装置简图。图2 为SPS 的电压、电流及外加压力与烧结 时间的关系曲线。其电流曲线主要由三段组成: (1) 脉冲大电流; (2) 稳态小电流; (3) 停止放电间隙。在稳态电流阶段, 仅施加很小 的压力; 放电间隙阶段施加大压力。
分电流加热模具,使模具开始对试样传热,试样温度升高,
开始收缩,产生一定的密度,并随着温度的升高而增大,
直至达到烧结温度后收缩结束,致密度达到最大。
材料合成与制备
1.3 等离子体烧结工艺参数的控制
烧结气氛 烧结气氛对样品烧结的影响很大(真空烧结情况除外), 合适的气氛将有助于样品的致密化。
材料合成与制备
烧结温度 烧结温度的确定要考虑烧结体样品在高温下的相转变、
晶粒的生长速率、样品的质量要求以及样品的密度要求。一 般情况下,随着烧结温度的升高,试样致密度整体呈上升趋 势,这说明烧结温度对样品致密度程度有明显的影响,烧结 温度越高,烧结过程中物质传输速度越快,样品越容易密实。
但是,温度越高,晶粒的生长速率就越快,其力学性能就越差。而 温度太低,样品的致密度就很低,质量达不到要求。温度与晶粒大小 之间的矛盾在温度的选择上要求一个合适的参数。
业株式会社生产,SPS-1050)。
材料合成与制备
等离子体烧结技术的概念
等离子体 等离子体是宇宙中物质存在的一种状态,是除固、
放电等离子烧结炉原理

放电等离子烧结炉(SPS,Spark Plasma Sintering)是一种采用脉冲直流电场作为加热手段的烧结技术。
它通过在粉末颗粒间产生高速电子冲击,达到烧结粉末材料的目的。
其基本原理如下:
1. 放电初始阶段:在烧结炉内放置装有粉末材料的模具,通入惰性气体以保护炉界面,然后采用脉冲电源对模具施加电压。
由于电压作用,粉末颗粒间的接触点会产生低电压放电,形成微弧放电。
2. 电放电效应:微弧放电导致局部瞬间高温,使接触点附近的粉末颗粒熔化、蒸发、电浆化、局部氧化还原反应等,从而增加颗粒间接触面积和粘结强度。
此外,局部高温还会促使粉末材料发生晶格扩散、颗粒重排等,为烧结提供有利条件。
3. 电热效应:通过脉冲电流加热,模具表面和粉末材料产生焦耳热效应。
这种热效应可以在很短的时间内将材料加热到所需的烧结温度,从而大大缩短烧结过程的时间。
4. 烧结过程:在一定的烧结温度下,粉末材料中的颗粒间接触增加,并通过扩散、重排、再结晶等过程,形成更高密度的烧结体。
与传统烧结方法相比,放电等离子烧结技术能在更短的时间内得到更好的烧结效果。
整个放电等离子烧结过程具有烧结时间短、能量消耗低和烧结体性能优异等优点,广泛应用于金属、陶瓷、复合材料等领域。
- 1、下载文档前请自行甄别文档内容的完整性,平台不提供额外的编辑、内容补充、找答案等附加服务。
- 2、"仅部分预览"的文档,不可在线预览部分如存在完整性等问题,可反馈申请退款(可完整预览的文档不适用该条件!)。
- 3、如文档侵犯您的权益,请联系客服反馈,我们会尽快为您处理(人工客服工作时间:9:00-18:30)。
放电等离子烧结的机理与应用李崴20080403B013 海南大学材料与化工学院摘要:放电等离子体烧结(SPS)一种用于材料烧结致密化的新技术,作为一种快速烧结方式,近年来被广泛研究与应用。
本文针对SPS的发展概况,工作机理以及研究应用进行了简单介绍。
关键词:放电等离子烧结,发展,机理,应用0引言放电等离子烧结(SPS)是近年来发展起来的一种新型的快速烧结技术。
由于等离子活化烧结技术融等离子活化、热压、电阻加热为一体,因而具有升温速度快、烧结时间短、晶粒均匀、有利于控制烧结体的细微结构、获得的材料致密度高、性能好等特点。
该技术利用脉冲能、放电脉冲压力和焦耳热产生的瞬时高温场来实现烧结过程,对于实现优质高效、低耗低成本的材料制备具有重要意义,在纳米材料、复合材料等的制备中显示了极大的优越性,现已应用于金属、陶瓷、复合材料以及功能材料的制备。
目前国内外许多大学和科研机构利用SPS进行新材料的研究与开发,并对其烧结机理与特点进行深入研究与探索,尤其是其快速升温的特点,可作为制备纳米块体材料的有效手段,因而引起材料学界的特别关注。
本文将对SPS技术有关的机理和部分应用予以介绍和讨论。
1.SPS的发展概况放电等离子烧结技术,20世纪30年代美国科学家就提出了脉冲电流烧结原理。
1965年,脉冲电流烧结技术在美、日等国得到应用。
1968年该技术被称为电火花烧结技术日本获得了专利,但未能解决该技术存在的生产效率低等问题,并没有得到推广应用。
1979年我国钢铁研究总院高一平等自主开发研制了国内第一台电火花烧结机,用以批量生产金属陶瓷模具,产生了显著的社会经济效益,并出版了《电火花烧结技术》一书。
1988年日本研制出第一台工业型SPS装置,并推广应用于新材料研究领域。
1990年以后,日本推出了可用于工业生产的SPS 第三代产品,具有10-100t的烧结压力和5000-8000A的脉冲电流。
1998年瑞典购进SPS烧结系统,对碳化物、氧化物、生物陶瓷等材料进行了较多的研究工作。
我国从2000年起,武汉理工大学、北京工业大学、清华大学、北京科技大学、中科院上海硅酸盐所等单位也相继引进了日本制造的SPS设备,开展了用SPS技术制备新材料的研究工作,主要用来烧结纳米材料和陶瓷材料。
SPS作为一种材料制备的全新技术,已引起了国内外材料界的特别关注。
2.SPS系统的结构目前使用的SPS系统主要是日本制造的由3部分组成(图1):①产生单轴向压力的装置和烧结模,压力装置可根据烧结材料的不同施加不同的压力;②脉冲电流发生器,用来产生等离子体对材料进行活化处理;③电阻加热设备。
SPS与热压(HP)烧结有相似之处,但加热方式完全不同,它是利用直流脉冲电流直接通电烧结的加压烧结方法,通过调节脉冲直流电的大小控制升温速率和烧结温度。
整个烧结过程可在真空环境下进行,也可在保护气氛中进行,烧结过程中,脉冲电流直接通过上下压头和烧结粉体或石墨模具,因此加热系统的热容很小,升温和传热速度快,从而使快速升温烧结成为可能。
SPS系统可用于短时间、低温、高压(500-1 000 MPa)烧结,也可用于低压(20-30 MPa)、高温(1 000-2 000℃)烧结,因此广泛应用于金属、陶瓷和各种复合材料的烧结,包括一些用通常方法难以烧结的材料,如表面容易生成硬的氧化层的金属钛和铝,用SPS技术可在短时间内烧结到90%-100%致密。
图1放电等离子烧结系统示意图1.上电极2.下电极3.粉末4.下压头5.下电极6.模具图2等离子烧结的工艺流程3.放电等离子烧结机理SPS作为一种新颖而有效的快速烧结技术,已应用于各种材料的研制和开发,目前认为SPS过程除具有热压烧结的焦耳热和加压造成的塑性变形促进烧结过程外,还在粉末颗粒间产生直流脉冲电压,并有效利用了粉体颗粒间放电产生的自发热作用,因而产生了一些SPS过程特有的现象,如图3所示。
图3 SPS过程特有的现象SPS的烧结有两个非常重要的步骤,首先由特殊电源产生的直流脉冲电压,在粉体的空隙产生放电等离子,由放电产生的高能粒子撞击颗粒间的接触部分,使物质产生蒸发作用而起到净化和活化作用,电能贮存在颗粒团的介电层中,介电层发生间歇式快速放电,如图4所示。
等离子体的产生可以净化金属颗粒表面,提高烧结活性,降低金属原子的扩散自由能,有助于加速原子的扩散。
当脉冲电压达到一定值时,粉体间的绝缘层被击穿而放电,使粉体颗粒产生自发热,进而使其高速升温。
粉体颗粒高速升温后,晶粒间结合处通过扩散迅速冷却,电场的作用因离子高速迁移而高速扩散,通过重复施加开关电压,放电点在压实颗粒间移动而布满整个粉体,使脉冲集中在晶粒结合处是SPS过程的一个特点。
颗粒之间放电时会产生局部高温,在颗粒表面引起蒸发和熔化,在颗粒接触点形成颈部,由于热量立即从发热中心传递到颗粒表面和向四周扩散,颈部快速冷却而使蒸气压低于其他部位。
气相物质凝聚在颈部形成高于普通烧结方法的蒸发-凝固传递是SPS过程的另一个重要特点。
晶粒受脉冲电流加热和垂直单向压力的作用,体扩散、晶界扩散都得到加强,加速了烧结致密化过程,因此用较低的温度和比较短的时间可得到高质量的烧结体。
图4放电过程中粉末粒子对的模型4.放电等离子烧结的研究与应用4.1在陶瓷制备中的研究SPS烧结速度快,烧结时间短,既可以用于低温、高压(500-1000MPa),又可以用于低压(20 -30MPa)、高温(1000 -2000℃)烧结,因此可广泛地用于金属、陶瓷和各种复合材料的烧结。
在SPS过程中,样品中每一种粉末及其相互间的孔隙本身都可能是发热源,用通常方法烧结时所必需的传热过程在SPS过程中可以忽略不计,因此烧结时间可以大为缩短,烧结温度也可以显著降低。
所以SPS对于制备高致密度、细晶粒陶瓷是一种很有优势的烧结手段。
K. Yamazaki[1]用SPS方法初步制备出超细晶粒的WC2Co系金属陶瓷。
T. Nishimura[2]用SPS方法制备了α2Si3N4和β2Si3N4陶瓷,烧结温度为1500~1600℃,烧结时间5~7min,达到理论密度的98%以上,晶粒尺寸为150~200nm。
宋京红[3]等用放电等离子烧结制备了Si3N4/Al2O3纳米复相陶瓷。
在1450 ℃,当Si3N4质量分数为10%时,Si3N4/Al2O3纳米复相陶瓷的韧性达到5.261MPa m1/2。
陈刚[4]等以单质硼粉和石墨粉为原料,采用SPS制备了碳化硼陶瓷,使碳化硼的合成和致密化一次完成。
确定了得到致密度较高的碳化硼陶瓷适宜的SPS 工艺条件为烧结温1800℃、烧结压力40MPa、保温时间 6 min,升温速率100℃/min、两步保温。
张勇[5]等用添加了~203和Y2O3助烧剂的碳化硅微粉为原料,通过放电等离子烧结(SPS)技术快速制备了碳化硅陶瓷。
分析了材料致密化过程,并重点研究了烧结工艺参数对材料致密度和力学性能的影响规律。
结果表明,当SPS工艺参数的烧结温度和压力分别为1 600℃和50 MPa时。
经过5min的烧结,碳化硅陶瓷的致密度可达到99.1%,硬度为HV 2550,断裂韧性达8.34 MPa·m2。
弯曲强度达684 MPa。
李家亮[6]等分别以MgO–Al2O3或MgO–AlPO4作为烧结助剂,采用放电等离子体低温快速烧结方法制备了主相为α 相的Si3N4陶瓷材料,通过分析说明当采用4%(质量分数,下同)MgO–4%Al2O3烧结助剂时,1 400 ℃烧结的陶瓷样品的相对密度和弯曲强度达到最高,分别为81%和182 MPa,且随烧结助剂中Al2O3含量的增加,样品的相对密度和弯曲强度降低。
当采用4%MgO–16%AlPO4烧结助剂时,1300 ℃烧结的陶瓷样品的相对密度和弯曲强度分别达到96%和366.5MPa,且样品的相对密度和弯曲强度随烧结温度的升高而增大。
王操[7]等采用放电等离子烧结技术制备出直线透过率较高(波长为640nm时为51%,波长为2000nm时为84%)的高性能透明氧化铝陶瓷,并研究了样品在模具内部的位置对其光学性能的影响。
放电等离子烧结技术由于其特殊的烧结机理,使陶瓷能够在较短的时间内和相对较低的温度下实现致密化烧结,从而有效地抑制了陶瓷晶粒的长大。
1500℃SPS烧结的试样与1700℃热压烧结试样相比,其晶粒更加细小和均匀。
这可能就是SPS烧结试样的力学性能优于热压烧结试样的主要原因。
可见,放电等离子烧结是一种能够实现陶瓷快速致密化的新技术,并具有很大的优势。
4.2纳米材料的制备传统的热压烧结、热等静压等方法制备的纳米材料,很难保证激励的纳米尺寸,又达到完全致密化的要求。
利用SPS技术引起加热迅速,合成时间短,可抑制晶粒的粗化,因此有望获得致密的纳米材料。
尤其是机械合金化等非平衡方法获得的粉末,晶粒细化的同时引入的大量缺陷和亚结构,有利于合成介稳材料。
罗锴[8]等采用超细WC粉末和放电等离子烧结(SPS)方法,在1700℃下制备出无粘结相纯碳化钨硬质合金材料;该材料的密度可达15.626g/cm3,接近纯碳化钨密度,维氏硬度可达2720kg·f/mm2;在1700℃下,无粘结相纯碳化钨硬质合金材料晶粒粒径为200-300nm,与原料粉末粒径基本一致,再升高烧结温度后,出现晶粒长大及孔洞。
4.3梯度功能材料的烧结梯度功能材料(FGMs)是一种组成在某个方向上梯度分布的复合材料,各层烧结温度不同,利用传统的烧结方法很难一次烧成利用PVD,PCD等制备成本很高,很难实现工业化生产,而应用SPS方法可以很好的克服这一难点,SPS 可以制造陶瓷\金属,聚合物\金属以及其他耐热梯度、耐磨梯度、硬度梯度、到电梯度、介孔度梯度等材料。
梯度层可到10多层,实现烧结温度的梯度分布。
Shen[9]采用SPS法分别制备了交替层叠和梯度分布的TiN/Al2O3复合材料。
随着SPS技术的广泛使用新型梯度功能材料正不断问世,因此,用机械合金化制备纳米或非晶的复合粉末,采用非平衡的SPS快速烧结技术有望成为制备多种纳米复合材料或大块非晶合金的有效方法。
4.4电磁材料采用SPS技术还可以制作SiGe,PbTe,BiTe,FeSi,CoSb3等体系的热电转换元件,以及广泛应用于电子领域的各种功能材料,如超导材料、磁性材料,靶材,介电材料、贮氢材料、形状记忆材料、固体电池材料、光学材料等。
张东涛[10]等采用高能球磨和放电等离子烧结技术制备了致密纳米晶Sm2Co17烧结磁体,磁体的平均晶粒尺寸约为35nm,并且其结构为TbCu7结构。
制备的二元Sm2Co17各向同性纳米晶烧结磁体具有较好的磁性能。
磁体的剩磁为0.65T,矫顽力高达0.87T,剩磁比为0.6(>0.5),表明纳米晶之间存在着晶间交换作用。