冶金试验研究方法
粉末冶金材料的力学性能研究

粉末冶金材料的力学性能研究在现代材料科学领域,粉末冶金作为一种重要的制备方法,已经为各种行业提供了广泛应用的材料。
粉末冶金材料由于其特殊的微观结构和化学成分,具有独特的力学性能,因此对其力学性能进行深入研究具有重要意义。
本文将探讨粉末冶金材料的力学性能研究内容,以及常用的测试方法和技术。
一、粉末冶金材料的力学性能研究内容粉末冶金材料的力学性能研究内容涉及多个方面,包括材料的强度、韧性、硬度、疲劳寿命等参数。
下面将分别对这些参数进行介绍。
1. 材料的强度强度是材料在外力作用下抵抗破坏的能力。
对于粉末冶金材料来说,强度与其组织结构和成分密切相关。
通过研究不同加工工艺对材料强度的影响,可以优化材料的力学性能。
2. 材料的韧性韧性是材料在受力时发生塑性变形的能力。
粉末冶金材料通常具有较好的韧性,这是由于微观结构中存在着各向异性的孔洞,有利于能量的吸收和分散。
3. 材料的硬度硬度是指材料抵抗外力压入的能力,通常用于评估材料的抗磨性能和耐磨性。
粉末冶金材料的硬度可以通过给定的压缩试验进行评估,也可以通过显微硬度测试等方法进行测量。
4. 材料的疲劳寿命疲劳寿命是指材料在交变载荷下破坏的周期数。
粉末冶金材料的疲劳寿命与材料的强度、韧性、孔洞等因素有关。
通过研究材料的疲劳寿命,可以为工程应用提供依据。
二、粉末冶金材料力学性能测试方法和技术为了研究粉末冶金材料的力学性能,需要采用一些有效的测试方法和技术,下面列举几种常用的方法:1. 压缩试验压缩试验是评估材料强度和硬度的常用方法。
通过在标准条件下施加压缩荷载,可以测量材料在压缩过程中的应变和应力,从而得到材料的力学性能参数。
2. 弯曲试验弯曲试验通常用于评估材料的韧性。
通过在标准条件下施加弯曲力,可以测量材料在弯曲过程中的应变和应力,从而评估材料的韧性水平。
3. 疲劳试验疲劳试验用于评估材料在交变载荷下的疲劳寿命。
通过在交变载荷下对材料进行循环加载,可以确定材料的疲劳强度和疲劳寿命。
冶金物理化学研究方法 (下册) 第十一章 冶金熔体粘度测定

冶金物理化学研究方法 (下册) 第十一章
冶金熔体粘度测定
冶金熔体粘度测定是冶金科学中重要的实验测试方法之
一,它可以提供有关金属熔体的物理性质息,包括流动性、密度、温度、粘度等。
熔体粘度测试有助于了解金属熔体的流变行为,它是冶金工艺中的重要参数,也是评价冶金材料性能的重要参数。
冶金熔体粘度测定基于流变学原理,其实验原理是采用不同温度、不同流速的熔体,在一定时间内测量其粘度。
熔体流动时,摩擦阻力的大小取决于熔体的物理性质,特别是其粘度,测量熔体粘度的实验结果可以表示为熔体粘度曲线,可以从中推测出熔体的物理性质。
冶金熔体粘度测定的实验设备包括温度控制设备、流量计、粘度计等,主要用于控制熔体的温度和流量,测量熔体的粘度。
由于熔体流动时会产生高温,因此在实验时需要注意安全防护。
熔体粘度测定的实验过程主要包括样品的准备、测试环境的设置、实验过程的控制和结果的记录几个步骤。
首先,要把样品熔融,使其保持恒定的温度。
然后,使用流量计和粘度计来测量熔体的流速和粘度。
最后,将测试结果记录在实验报告中,测量熔体的粘度曲线。
冶金熔体粘度测定是一种重要的实验方法,可以提供有关金属熔体的物理性质的有价值的息,有助于了解冶金材料的流变行为,并且可以提供冶金工艺中重要的参数,为评价冶金材料性能提供重要参考。
微生物冶金研究及应用示例(可编辑
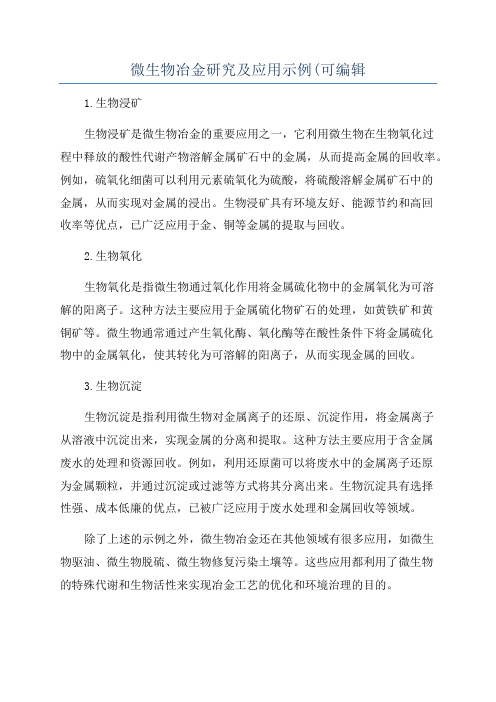
微生物冶金研究及应用示例(可编辑1.生物浸矿生物浸矿是微生物冶金的重要应用之一,它利用微生物在生物氧化过程中释放的酸性代谢产物溶解金属矿石中的金属,从而提高金属的回收率。
例如,硫氧化细菌可以利用元素硫氧化为硫酸,将硫酸溶解金属矿石中的金属,从而实现对金属的浸出。
生物浸矿具有环境友好、能源节约和高回收率等优点,已广泛应用于金、铜等金属的提取与回收。
2.生物氧化生物氧化是指微生物通过氧化作用将金属硫化物中的金属氧化为可溶解的阳离子。
这种方法主要应用于金属硫化物矿石的处理,如黄铁矿和黄铜矿等。
微生物通常通过产生氧化酶、氧化酶等在酸性条件下将金属硫化物中的金属氧化,使其转化为可溶解的阳离子,从而实现金属的回收。
3.生物沉淀生物沉淀是指利用微生物对金属离子的还原、沉淀作用,将金属离子从溶液中沉淀出来,实现金属的分离和提取。
这种方法主要应用于含金属废水的处理和资源回收。
例如,利用还原菌可以将废水中的金属离子还原为金属颗粒,并通过沉淀或过滤等方式将其分离出来。
生物沉淀具有选择性强、成本低廉的优点,已被广泛应用于废水处理和金属回收等领域。
除了上述的示例之外,微生物冶金还在其他领域有很多应用,如微生物驱油、微生物脱硫、微生物修复污染土壤等。
这些应用都利用了微生物的特殊代谢和生物活性来实现冶金工艺的优化和环境治理的目的。
总之,微生物冶金是一种创新的冶金技术,通过利用微生物的代谢能力和生物活性产物,实现对金属矿石的浸出、氧化、沉淀等过程,为冶金工业的发展提供了新的思路和方法。
微生物冶金在提高金属回收率、节能减排和环境保护等方面具有巨大潜力,将在未来得到更广泛的应用和推广。
冶金工程中的冶金反应数值模拟方法研究
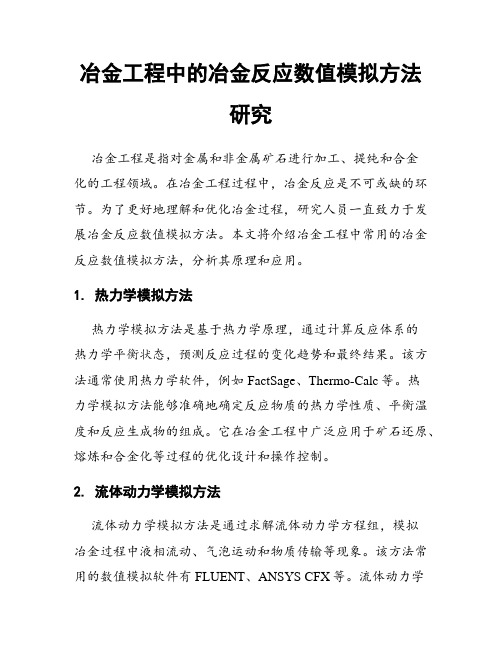
冶金工程中的冶金反应数值模拟方法研究冶金工程是指对金属和非金属矿石进行加工、提纯和合金化的工程领域。
在冶金工程过程中,冶金反应是不可或缺的环节。
为了更好地理解和优化冶金过程,研究人员一直致力于发展冶金反应数值模拟方法。
本文将介绍冶金工程中常用的冶金反应数值模拟方法,分析其原理和应用。
1. 热力学模拟方法热力学模拟方法是基于热力学原理,通过计算反应体系的热力学平衡状态,预测反应过程的变化趋势和最终结果。
该方法通常使用热力学软件,例如FactSage、Thermo-Calc等。
热力学模拟方法能够准确地确定反应物质的热力学性质、平衡温度和反应生成物的组成。
它在冶金工程中广泛应用于矿石还原、熔炼和合金化等过程的优化设计和操作控制。
2. 流体动力学模拟方法流体动力学模拟方法是通过求解流体动力学方程组,模拟冶金过程中液相流动、气泡运动和物质传输等现象。
该方法常用的数值模拟软件有FLUENT、ANSYS CFX等。
流体动力学模拟方法能够模拟冶金反应体系中的流体流动和传热过程,帮助优化冶金反应器的设计和操作条件。
3. 结构力学模拟方法结构力学模拟方法是通过求解结构力学方程,模拟冶金反应过程中的应力和变形现象。
该方法常用的数值模拟软件有ABAQUS、ANSYS等。
结构力学模拟方法能够模拟冶金反应器中的力学性能和损伤行为,帮助改善冶金反应器的结构设计和材料选择。
4. 多物理场耦合模拟方法多物理场耦合模拟方法是综合运用热力学、流体动力学和结构力学等方法,模拟冶金反应过程中的多种物理现象的相互影响。
该方法常用的数值模拟软件有COMSOL Multiphysics、ANSYS Workbench等。
多物理场耦合模拟方法能够更全面地揭示冶金反应过程中的物理规律和相互关系,为优化冶金工程提供全面的参考。
5. 人工智能模拟方法人工智能模拟方法是近年来发展起来的一种新型模拟方法,它基于机器学习和深度学习等技术,通过训练模型来模拟冶金反应过程。
冶金实验研究报告

冶金实验研究报告冶金实验研究报告摘要:该研究报告主要对某种冶金实验进行了详细的研究和分析。
通过对实验材料的选取、实验过程的控制和结果的分析,得出了一些重要的结论和建议。
研究表明,该实验在研究冶金过程和材料性能方面具有一定的启示和应用价值。
引言:冶金实验是现代冶金学研究的基础,通过对不同冶金材料进行实验研究,可以揭示材料的物理、化学和力学性质,为冶金工艺的改进和优化提供重要依据。
本次实验主要研究了某种金属材料的耐腐蚀性能和力学性能。
实验材料和方法:实验选择了一种常用的金属材料作为研究对象,通过一系列实验方法对其进行了测试。
首先,对材料进行了化学成分分析,以确定其组成和纯度。
然后,利用电化学测试仪器对材料进行了腐蚀实验,测量了其腐蚀速率和腐蚀形貌。
最后,利用力学测试仪器对材料进行了拉伸和硬度测试,得出了其力学性能参数。
实验结果:通过对实验数据的统计和分析,我们得出了一些重要的结果。
首先,材料的化学成分符合标准要求,具有一定的纯度。
其次,材料在腐蚀试验中表现出良好的抗腐蚀性能,腐蚀速率较低。
最后,材料的力学性能良好,具有较高的强度和硬度。
讨论与结论:本次实验结果表明,该材料在冶金应用中具有一定的优势和潜力。
其抗腐蚀性能好,可以在腐蚀环境中长期使用。
同时,它的力学性能优秀,可以满足一般工况下的要求。
然而,该材料的成本较高,需要在使用场景和经济效益之间进行权衡。
建议:根据本次实验的研究结果和分析,我们提出以下几点建议:首先,进一步研究和优化该材料的制备工艺,以提高材料性能和降低成本。
其次,对该材料在不同工况下的耐腐蚀性能进行深入研究,以确定其应用范围和限制条件。
最后,通过与其他材料进行比较和竞争,评估该材料在冶金领域的竞争力和市场前景。
结语:通过本次研究,我们对某种冶金实验进行了深入的研究和分析,得出了一些重要的结论和建议。
该实验在研究冶金过程和材料性能方面具有一定的启示和应用价值。
希望本次研究可以为冶金学研究和工业实践提供一定的参考和指导。
高密度粉末冶金成形方法研究及优化

高密度粉末冶金成形方法研究及优化一、引言高密度粉末冶金成形技术是一种通过在粉末表面施加压力和温度实现金属材料成形的加工工艺。
该技术具有高效率、低成本、高精度、可逆性和可重复性等优点。
因此,在改进传统的金属成形过程以及开发新型金属材料时,高密度粉末冶金成形技术已成为一种备受关注的重要研究领域。
二、高密度粉末冶金成形方法的分类高密度粉末冶金成形技术根据成形前后粉末状况的变化,可分为以下几种方法:1. 等静压成形 (HIP)等静压成形是一种将高密度金属粉末放入成型模具中,先以低压力进行预压,随后在高温和高压力的条件下加以成形的加工方法。
等静压成形方法可以制造出具有高密度和高性能的复杂形状金属零件,如滚轮轴承、配气机构、燃气轮机叶片等等。
2. 烧结成型烧结成型是一种通过在制备过程中在粉末中添加一些粘结剂,使得粉末在高温条件下粘结在一起,然后进行成形的方法。
这种方法可以制造出高精度、高可靠性和抗热性能强的机械结构件和高强度、低密度的材料。
3. 挤压成形挤压成形是一种通过将金属粉末放入旋转式模具中,在模具两端施加压力来实现成形的加工方法。
这种方法较其他成形方式更为简单,适用于制作一些规则结构的中间件、链接件和管道接头。
4. 等离子粉末成形等离子粉末成形是一种将金属粉末喷射到等离子体火焰中进行高温加热,通过表面张力形成液态金属,并恰当地加压形成零件的一种成形工艺。
等离子粉末成形方法操作简单、可加工出具有高密度、高强度和高耐磨性的金属零件。
三、高密度粉末冶金成形方法的优化为了进一步提高高密度粉末冶金成形技术的加工效率、成形质量和材料性能,需要进行相应的优化。
优化方案一:材料的合理选择选择合适的材料是决定高密度粉末冶金成形成功与否的关键因素之一。
高密度粉末冶金成形的理想材料是那些粒度大小适中、形状均匀、流动性能好而且作为粉末冶金材料的化学成分方面相同或相似的金属粉末。
因此,选择质量优良、粘度适中的金属粉末是高密度粉末冶金成形过程中一个非常重要的环节。
粉末冶金法制备铝基复合材料的研究
粉末冶金法制备铝基复合材料的研究粉末冶金法是一种制备金属基复合材料的有效方法,具有制备的复合材料成分均匀、性能优异、成本低廉等优点。
铝基复合材料作为一种高性能的金属基复合材料,在航空、汽车、机械等领域得到了广泛应用。
本文将围绕粉末冶金法制备铝基复合材料展开,探讨其制备工艺、性能评价、应用领域及未来发展趋势。
粉末冶金法制备铝基复合材料的工艺流程主要包括以下几个步骤:原材料准备:选用纯度较高的铝粉、增强相(如SiC、Al2O3等)及适量的粘结剂。
混合与压制:将原材料按照一定的比例混合,加入适量的润滑剂,然后压制成型。
烧结:将压制成型后的生坯在高温下进行烧结,使得铝粉与增强相充分融合。
热处理:对烧结后的材料进行热处理,以进一步优化材料的性能。
通过以上步骤,制备出具有特定形状和性能的铝基复合材料。
与传统的铸造方法相比,粉末冶金法具有更高的成分均匀性、更细的晶粒结构和更好的力学性能。
铝基复合材料因其具有优异的力学性能、耐腐蚀性和抗高温性能,在航空、汽车、机械等领域得到了广泛应用。
在航空领域,铝基复合材料主要用于制造飞机发动机零部件、机身结构件等。
其轻质高强的特点使得飞机能够减轻重量,提高飞行效率。
在汽车领域,铝基复合材料主要用于制造汽车零部件,如发动机缸体、活塞、齿轮等。
其高强度和抗疲劳性能能够提高汽车的安全性和使用寿命。
在机械领域,铝基复合材料可用于制造各种高强度、轻质的机械零件,如传动轴、支架、齿轮等。
其优良的耐腐蚀性和高温稳定性使得铝基复合材料成为理想的机械零件材料。
铝基复合材料的性能取决于其组成和制备工艺。
在力学方面,粉末冶金法制备的铝基复合材料具有高强度、高硬度、低塑性等特点,其力学性能优于传统铸造铝材。
耐腐蚀性方面,由于增强相的加入,铝基复合材料的耐腐蚀性能得到显著提高。
抗高温性能方面,通过选用合适的增强相和热处理工艺,可以使得铝基复合材料在高温下保持优良的性能。
随着科技的不断发展,粉末冶金法制备铝基复合材料在未来将面临新的挑战和机遇。
冶金实验研究方法
《冶金实验研究方法》报告学院:冶金与化学工程学院专业:13有色金属冶金学生:邹剑学号:6120130109指导教师:徐志峰课程:冶金实验研究方法热力学、动力学及工艺矿物学分析方法在冶金过程研究中应用一热力学1.1热力学概述冶金过程热力学使用热力学方法研究从矿石提取金属及其化合物的各种冶金过程的一门学科。
它是冶金过程物理化学的一个分支,从矿石提取金属可分为火法冶金、湿法冶金和电冶金,后者包括电炉冶炼、熔盐电解和水溶液电解,故也可分别包括在前二者之内。
冶金过程物理化学的发展是从火法冶金,特别是炼钢的热力学开始的,随着冶金工业的发展而扩大其内容,并已逐步深入到有色金属的火法和湿法冶金的研究。
1.2热力学分析方法在冶金过程研究中的应用冶金过程热力学研究范围十分的广,不仅包括冶金体系的热力学,同时也包含各种冶金过程中有关体系间的相互反应。
在实际生产中,运用热力学定律(dU−TdS−pdV≤SW′)和拉乌尔定律(P A=P A∗∙X A)、亨利定律(P B=k B∙X B)以及吉布斯自由能公式(G=U−Ts−PV)等定理公式求得反应是否可以发生。
在研究有色金属冶金时,冶金热力学涉及到了熔锍、熔渣、熔盐和水盐体系以及有机溶剂和离子交换树脂各个方面。
冶金热力学针对火法冶金来说,通过氧势图给出一系列金属化合物的标准生成自由焓与温度的关系,从而可以对不同化合物的相对稳定性作出定量比较,并可据以计算有关冶金反应的平衡常数。
而对湿法冶金来说,通过电位-pH图给出的某一金属的各种固态和溶解于溶液中的化合物的热力学平衡,也可以给出溶质和气相间的平衡。
这种图对于金属在给定条件下的浸取或腐蚀有一定参考和应用价值,例如湿法冶金中的高压氢还原法就是冶金热力学应用于生产实践的一个例子。
通常情况下,可以通过人为的干预达到提高反应速率、提高经济效益、节约生产成本的目的,从热力学的角度来看,可以通过调节反应条件使得标准自由焓变量尽可能成为较大的负值,越负反应进行得越剧烈也越明显,其次可以提高反应物的活度或者降低产物的活度,这些都可以在生产实践当中指导企业生产,以达到效益的最优化。
冶金物理化学研究方法
冶金物理化学研究方法冶金物理化学是一门应用自然科学原理和方法,研究金属及其化合物物相变化、热力学行为、动力学过程及其与环境相互作用的一门学科。
以下是冶金物理化学的主要研究方法:1.实验方法(1)热分析技术:通过观察热效应与时间、温度的关系,分析物质在加热或冷却过程中的物相转变和反应过程。
(2)X射线衍射技术:利用X射线衍射分析物质的晶体结构和物相组成。
(3)原子光谱技术:通过原子光谱分析物质中的元素组成。
(4)核磁共振技术:利用核磁共振技术分析分子结构和化学键信息。
(5)电子显微技术:通过电子显微镜观察材料的微观结构和形貌特征。
2.计算方法(1)量子化学计算:利用量子力学原理,计算物质的分子结构和化学键性质。
(2)热力学模型:建立热力学模型,描述物质的热力学性质和相平衡关系。
(3)动力学模拟:通过动力学模拟,研究物质反应动力学过程。
(4)蒙特卡洛方法:利用蒙特卡洛方法进行数值模拟和预测。
(5)有限元分析:通过有限元分析方法,对冶金过程中的物理化学现象进行数值模拟。
3.系统方法(1)系统科学:运用系统科学理论和方法,研究冶金过程中的整体性和复杂性。
(2)冶金过程模拟:通过冶金过程模拟,实现对冶金过程的优化和控制。
(3)数据挖掘与机器学习:利用数据挖掘和机器学习技术,对冶金过程进行预测和优化。
(4)过程控制与优化:通过过程控制与优化,提高冶金产品质量和降低能源消耗。
(5)绿色冶金:运用绿色冶金理念,实现冶金工业的可持续发展。
总之,冶金物理化学研究方法涵盖了实验方法、计算方法和系统方法等多个方面,这些方法在冶金工业中具有广泛的应用前景。
通过不断深入研究冶金物理化学现象和规律,可以推动冶金工业的发展和创新。
冶金试验研究方法-复习资料大合集
冶金试验研究方法期末复习资料2015年11月13日考试形式与范围考试形式:判断题:10题10分;不定项选择题:10题20分;简答题:6题30分;计算题:4题40分.考试范围:绪论试验设计误差分析与数据处理温场获得与测量气体净化与气氛控制真空技术固体电解质电池与其应用冶金材料物性测定电化学研究方法※回归试验、化学平衡、检测技术和论文撰写不考.一、绪论1. 研究工作的阶段划分与特点〔1〕实验室试验的特点:①规模小,测试手段先进,可采用小型标准设备〔仪器〕.其数据易于采集和处理.②条件容易控制,干扰因素较少,操作严格,试验结果的准确度高.③试样的物相组成与物理化学性质波动不大,试验数据重现性好.④分批试验,机动灵活,可在较大范围内进行探索.〔2〕扩大实验室试验特点:①大部或全部是连续操作,较接近工业生产要求;②规模较大,运行时间较长;③各环节之间的相互影响暴露得较充分,试验结果的可靠性更高;④原材料消耗较大,费用较高.〔3〕半工业试验:半工业试验设备应为生产设备的雏形或一个生产单位的雏形,应要求操作连续化、机械化或自动化,并配备将来工业生产设备同样需要的控制仪表.2. 研究工作的程序二、试验设计1. 试验设计是指为节省人力、财力、迅速找到最佳条件,揭示事物内在规律,根据实验中的不同问题,在实验前利用数学原理科学编排实验的过程.是以概率论与数理统计学为理论基础,以达到经济、科学地安排试验的目的〔正交设计法、优选法、均匀设计法等〕.2. 0.618法〔黄金分割法〕例:在某一生产工序中,需加入一种原料,其适宜加入量为1000~2000克,问最佳加入量是多少?解:若采用均匀试验法,间隔5克做一次试验,需做199次.但用0.618法只需做11次,具体做法如上图.具体步骤如下:先在1000~2000克之间的0.618<1>与其对称点0.382<2>处做第一组试验,其加入量分别为1618克和1382克.比较两点的结果,若<1>比<2>好,则删去小于1382克部分;再在1382~2000克之间做1618的对称点的试验,其加入量为1764克.<2000-1382> × 0.618 = 381.924 + 1382 = 1763.924g比较<1>和<3>的结果又可删去一部分,依此类推.这样每次都可去掉试验范围的38.2%,试验范围逐步缩小,经过11次试验就可求出最佳加入量.反之不用优选法,需要做199次才能求出最佳点,而与11次优选试验等效.3. 正交试验设计正交试验设计是利用已经造好的表格〔正交表〕安排试验和进行数据分析的一种方法.它适用于多因素的条件试验,可从少数的试验中判断影响因素的主次,可确定出较好的组合方案与进一步试验的方向.特点:均匀分散,整齐可比.正交实验设计的基本工具是正交表.常用的正交表有L8<27>、L12<211>、L9<34>、L27<313>、L16<45>、L8<4×24>、L18<2×37>等.各数码意义如下:因子〔因素〕:对试验指标可能会产生影响的原因称为因子,也可称为因素;水平:在试验中因子所选取的具体状态称为水平;L8<27>:正交表最多可以安排7因子二水平试验,共做八次.L9<34>:正交表最多可安排8因子3水平共做9次试验.因子水平表4. 极差分析与方差分析的比较极差分析方法简单,只需少量计算,经综合比较就可得到较优的组合方案.但该法没有考虑误差,也没有一个标准定量地判断因子的影响作用是否显著.而正交表的方差分析可以把因子水平变化引起试验数据间的差异同误差所引起试验数据的差异区分开来,并能定量的描述因子的影响作用是否显著.5. 冶金常用方法:优选法、正交试验设计、正交回归设计、混料回归设计、逐步回归设计、旋转回归设计等.三、误差分析与数据处理1. 误差的分类误差有不同的分类方法,就其性质和产主的原因,可将误差分为系统误差、偶然误差和过失误差三种.1〕系统误差〔恒定误差〕产生原因:①仪表未经校正;②测量方法不当;③化学试剂纯度不够;④观测者的习惯与偏见等而产生.特点:恒偏于一方,数值的大小按一定规律变化或者固定不变,它决定了测量结果的准确性.消除〔使之减小〕办法:①采用不同的实验技术或不同的实验方法;②改变试验条件;③调换仪器和试验人员;④提高化学试剂纯度.2〕偶然误差〔随机误差〕产生原因:某些无法控制的偶然因素影响的结果;测量仪器灵敏度的有限性;温度、压力等无法控制的微小变化.产生的原因一般不详,因而无法控制,但用同一仪器在同样条件下,对一个量做多次测量,若观测次数足够多,则可发现偶然误差完全服从统计规律.误差小的比误差大的出现几率大小相同,符号相反的正、负误差出现的几率近于相等.故误差出现的几率与误差大小有关,当没有系统误差时,无限多次测量结果的平均值可以代表真值.可见误差超过±3σ出现的几率只有0.3%,因此多次重复测量中个别数据误差的绝对值大于3σ时,这个数值可以舍弃.3〕过失误差是一种与实事不相符的误差,主要是由于粗枝大叶和操作不正确等原因所引起,如读错刻度、记录错误、计算错误等.此类误差无规律可寻,只要多加注意、细心操作就可避免.2. 可疑观测值的舍弃2.1. 拉依达3σ准则当观测次数大于10次,可用3σ准则舍弃可疑值,其依据如图2所示.图中误差超过∓3σ的数据的几率小于0.3%,所以在一组较多的数据中,对偏差大于3σ的数据可以舍弃.具体步骤是:首先算出一组数据的算术平均值和标准误差σ,然后比较是否大于3σ,若大于3σ即可舍弃,舍弃可疑值后再重新计算平均值和标准误差σ.2.2. 乔文涅法则在一组数据中,某数据与该组数据算术平均值的偏差大于该组数据或然误差的k倍时,可以舍弃.K值查表.3. 试验数据的表示方法试验数据的表示方法有列表法、作图法、方程式法三种.1、列表法列表法是将试验数据中的自变量与因变量的各个数值依一定的形式和顺序对应列出来.优点:简单易作、形式紧凑、数据清楚、便于参考比较,同一表内可以同时表示几个变量间的变化而不混乱.列表时一般包括表的序号、名称、项目、说明与数据来源等.2、作图法利用图形表达试验结果,实际上就是用形象来表达科学的语言.优点:能清楚地显示研究结果的变化规律和特点,如极大值、极小值、转折点、周期性、数量的变化速率以与其他奇异性等;形式简明直观便于比较;如果曲线作得足够光滑,可对变数做微分和积分,有时还可利用图形外推求得难以用试验获得的值,用途极为广泛.用途:<1> 求内插值;<2> 求外推值;<3> 作切线求函数的微商;<4> 求经验方程;<5> 求转折点和极值.3、方程式法用数学经验方程式表达试验结果时,不但方式简单,而且进一步试验设计和理论探讨可以提供依据和线索.数学经验方程式可用图解法和最小二乘法求得.对于多因素影响的函数式,可用正交回归、旋转回归、混料回归等方法求得.四、实验室温场的获得与测量1. 获得低温的方法绝热膨胀;节流过程;低温液体减压;稀释致冷;磁冷却2. 常用高温炉对比3. 电阻炉结构〔1〕炉壳:放有绝热材料〔2〕保温材料层:放有保温材料〔3〕炉衬:耐火材料为炉膛起保温作用,使炉膛达到要求的高温〔4〕电热体:将电能转化成热能〔5〕炉管:支撑发热体和放置试料〔6〕炉架:支撑整个炉体重量〔7〕接线柱:保证电源线与电热体安全连接对于不同的实验要求,炉体还可能包括密封系统,水冷系统等.4. 耐火材料的工作特性耐火材料的工作特性也就是使用性能,其主要指标有耐火度、荷重软化点、化学稳定性和热稳定性、热导率和导电性.①耐火度耐火度是耐火材料抵抗高温作用的性能.耐火度仅代表耐火材料开始熔化至软化到一定程度时的温度.因为绝大多数耐火材料由多种成分的矿物组成,没有固定的熔点,而是在一定温度范围内熔化的,只有高纯氧化物耐火制品的耐火度和熔点才比较接近.②荷重软化点耐火材料在使用中多少要受到载荷和应力作用,当达到一定温度时,耐火材料内部组织局部开始熔化,机械强度会急剧减低.为了查清这类变化,对耐火材料样品施加一定压力并以一定升温速度加热,当耐火材料塌毁〔以加压力方向收缩一定值作标志〕时的温度称为荷重软化点.荷重软化点表征耐火材料的机械特性,而耐火度表示其热性质.显然,耐火材料的实际使用温度不得超过荷重软化点,更不能超过耐火度.③热稳定性耐火材料在温度急剧变化条件下,不开裂、不破碎的性能叫热稳定性.残存线膨胀收缩的起因:烧成中的矿物变化和物理变化而引起的容积变化还未结束时发生的.这个变化值大,往往使高温下耐火材料龟裂、脱落.一般热膨胀高的制品往往抗热震性较差.④化学稳定性耐火材料在使用过程中,在高温条件下均与一定的气相、凝聚相〔如金属、炉渣〕相接触,在这样的条件下,耐火材料能否稳定存在,对实验过程和耐火材料作用都有重大影响.⑤热导率耐火材料的热导率表示其导热能力的大小,用导热系数λ表示,单位为:J/<m·h·℃>或W/<m·K>.其数值为物体中单位温度降度〔即1m厚的材料两侧温度相差1℃时〕,单位时间内通过单位面积传导的热量.耐火材料中矿物晶型变化将使热导率变化,最明显的例子是SiO2,0℃时结晶的二氧化硅热导率要比石英玻璃高几倍.⑥导电性一般耐火材料中除碳质、石墨、碳化硅、粘土质、炭化硅制品外,在室温下都是不良电导体.随温度升高,大多数耐火材料导电性提高,电阻率下降.最明显的是氧化锆.5. 耐火材料的结构特性气孔率:气孔率高,抗渣铁浸蚀能力差;机械强度低,不能承重但导热性差,可作绝热保温材料.透气性:与工作温度、气体特性和制品组织的均匀性等有关.为保证高温炉内的一定气氛,应选择透气性小的耐火材料.6. 常见耐火材料的特点冶金中常用的耐火材料:氧化物耐火材料;石墨和非氧化物耐火材料;其它耐火材料.氧化物耐火材料:熔融Al2O3再结晶的刚玉制品;石英质品;MgO制品;氧化钙制品;二氧化锆制品;石墨和非氧化物耐火材料:石墨;碳化物;氮化物、硼化物、硫化物、硅化物耐火材料;其它耐火材料:6.1. 熔融Al2O3再结晶的刚玉制品特点:化学稳定性、导热性、和电绝缘等性能均较好,不透气.高级制品由99.98%以上Al2O3制成.致密的刚玉制品具有良好的抗渣性、抗金属浸蚀性能.使用温度:耐火度可达2000℃,其最高使用温度为1900℃,适用于300℃/min的升温速度.薄壁优质坩埚可由室温直接置于1600℃高温中而不炸裂.应用:高温炉衬、电热体支架、炉管、热电偶保护套管、坩埚、坩埚座等.6.2. 石英制品石英玻璃是熔融SiO2的过冷体,快冷得到的玻璃状石英.特点:在单一氧化物中,石英玻璃的热膨胀系数最小.800℃以上,接近零.高温下,抗热震性好,透明,体积密度大,气孔率小,不透气,常用于真空系统.使用温度:室温至1000℃或更高温度下能保持玻璃体性状,常压下使用温度为1240℃左右,短时间使用温度可达1700℃,但在1000℃以上快速结晶而失透.缺点:它是指由介稳的玻璃态转变成结晶态,这种晶型转变多半是由石英玻璃表面粘附的杂质所促进的.此过程一旦开始,器皿会迅速损坏,在1000℃以上更容易进行.应用:坩埚、真空炉管、插入式热电偶保护管等.6.3. MgO制品特点:耐火度高,在氧化气氛中使用温度比刚玉高,还原气氛下只能在1700 ℃以下使用.使用温度:MgO熔点为2800 ℃,由于Mg蒸汽压大,真空条件下不宜超过1600 ℃-1700 ℃使用.氧化气氛比刚玉高.应用:坩埚、炉管与热电偶的电绝缘材料.缺点:易吸水而生成氢氧化物,可通过煅烧生成稳定的形态.6.4. 氧化钙制品特点:具有良好的抗金属性能.耐火度高,价格便宜.使用温度:CaO熔点2600℃,在1700℃以下其稳定性在氧化物中占首位.应用:坩埚材料缺点:CaO易吸收空气中水分成为Ca<OH>2而损坏,另外也不容易烧结,故未能广泛使用.人们一直在寻找解决吸水问题的办法.6.5. 二氧化锆制品特点:烧结ZrO2与某些氧化物结合,高温下有较高的导电性,可以作为高温炉的发热体.使用温度:ZrO2熔点为2700℃,系弱酸性氧化物,其耐火制品何种软化温度高于2000℃,经2200℃煅烧的ZrO2具有较高强度和热稳定性.在氧化性或弱还原气氛下工作均较稳定,高温时使用性能比刚玉强,应用:坩埚、炉衬与绝热材料.6.6. 石墨特点:石墨升华点高于4700℃,没有相变,热膨胀系数小,导热、导电率高,密度小,易加工,高温尺寸稳定,强度大,抗渣性好,所以在很多场合可充当优良的耐火材料.应用:用碳作还原剂的熔融还原反应和被碳饱和的熔体反应时,可以用石墨坩埚;研究金属熔体和炉渣之间的反应可用石墨坩埚.如避免石墨碳参与反应,可以用钼片内衬套在石墨坩埚里.石墨可以作为电极或电热体.使用的温度与气氛:石墨在中性或还原性气氛中是稳定的,在真空条件下可用到2000℃以上.用石墨注意的问题:缺点:石墨不能用于氧化性气氛不反应:石墨不能与金属发生反应;金属不能腐蚀石墨坩埚;石墨不会对金属渗碳从而改变反应体系成分.6.7. 碳化物从热力学上讲,碳化物没有相应的氧化物稳定.有些碳化物在氧化性气氛下由于表面形成了一层氧化物薄膜,阻止了进一步氧化,因而可在氧化气氛下使用至一定温度.如SiC在1000℃以下稳定是由于反应速度慢,在高于1140 ℃至1500 ℃稳定是由于生成了一层SiO2保护膜.TiC和ZrC等在高温时同样可以形成氧化物保护膜.很多碳化物在液态金属中有很大的溶解度,从而使金属玷污,故碳化物不适宜做液态金属的容器.6.8. 氮化物、硼化物、硫化物、硅化物耐火材料氮化物在高温时抗氧化能力较差,易被氧化形成氧化物.硼化物的抗氧化能力不强,在高温下不适于在氧化性气氛下使用.硼化物在真空中的稳定性很高,在2500K以上是唯一适合于真空下使用的耐火材料.硫化物:硫和金属形成一系列高稳定性的硫化物.但是,硫化物的稳定性比相应的氧化物小.在氧化性气氛下高温时要氧化成氧化物.在氮气气氛下很少反应.因为其分解产物为气体硫,高温时离解压大,一般不适合在真空条件下使用.硅化物:氧化性气氛中热力学不稳定,但以MoSi2为例,在氧化气氛中能形成一层二氧化硅保护膜,在空气中高温下直到熔点抗氧化性能很好.6.9. 高熔点金属材料实际应用中有钨〔W〕、钼〔Mo〕、铌〔Nb〕、钽〔Ta〕以与铂〔Pt〕、铱〔Ir〕、铑〔Rh〕、钌〔Rt〕.前四种易氧化,后四种抗氧化,可在氧化气氛中使用.钨熔点高达3337℃,高温下蒸汽压很低,可在真空、氮、氢或其它非氧化性气氛下稳定工作.钨坩埚一般用钨片在氩弧焊下制成,或用粉末冶金方法制成.钼熔点也较高,达2600℃,易加工成型,在非氧氛下工作温度可达2000℃,温度再高则易蒸发.钼坩埚用钼片在氩弧焊下制成.7. 耐火材料的工作稳定性7.1. 在氧化气氛中的稳定性耐火氧化物大多是其金属元素的最高价氧化物,在高温氧化气氛下是稳定的.如果在分解或蒸发温度以下工作,其氧化气氛中的最高温度可以接近其耐火度〔或熔点〕.但碳素耐火材料是不稳定的.7.2. 在H2和CO气氛下的稳定性氧化物耐火材料能否与氢起作用,可以通过热力学计算作出初步判断.钢铁冶金实验温度一般不高于1727℃大多数耐火氧化物在氢气氛下是稳定的.但1727℃下,SiO2与H2作用的P H2O蒸汽压稍高,其余氧化物的P H2O都不高.7.3. 在其它气氛下Al2O3在N2和HCl气氛中是稳定的,在高温下与HF气体发生反应生成AlF3.含S的气氛会微弱的腐蚀Al2O3.MgO 在N2气氛下可稳定至1700℃以上,卤素和S的气氛要腐蚀MgO.7.4. 在高温下的稳定性在高温、真空条件下,耐火材料本身的稳定性减小.在真空冶金中,由于体系的压力很低,促使了氧化物的分解.不宜于用于2000K以上的高温.7.5. 耐火氧化物对碳的稳定性〔1〕耐火氧化物被还原成金属的可能性.在一个大气压,2000℃以下常用耐火氧化物中只有SiO2、MgO有被碳还原成金属的可能.SiO2被还原是明显的.MgO在标准状态压力下高温时虽较难被碳还原,但因生成的Mg和CO都是气体,所以随着气相压力的降低反应易于进行.所以在真空碳热还原金属氧化物时,不能用MgO坩埚,而用石墨坩埚.〔2〕耐火氧化物被C还原成碳化物的可能性大多数耐火氧化物在1500℃以上与碳接触时容易生成碳化物.如果反应生成的CO不断地被排除,氧化物将不断地和碳反应生成碳化物.7.6. 耐火氧化物对液态金属的稳定性耐火氧化物在1000℃以上与液态金属接触时,金属易受污染,而耐火氧化物达到侵蚀.其反应通式如下XO固+Me液= MeO液+ X固液在实际场合,由于炉内气氛对液态金属的作用,对耐火氧化物也有影响.如铁金属的氧化,生成的<FeO>对很多耐火氧化物都有侵蚀作用.因此必须注意炉内气氛的间接、直接作用.7.7. 耐火氧化物对熔盐和炉渣的稳定性高温下,很多耐火材料易被熔盐或炉渣所侵蚀.熔点在600℃以下:用硬质玻璃作容器,但氟化物熔盐能与SiO2作用生成易挥发的SiF4,应当用白金坩埚.在1100℃以上:碱金属、碱土金属、氯化物、溴化物和碘化物等熔盐,都可用Al2O3、MgO、ZrO2质容器,氟化物则用石墨容器.碱金属的硝酸盐、硫酸盐、磷酸盐在高温下采用白金或石墨质容器.8. 电热元件电热元件的作用是把电能转化成热能,使被加热的样品达到所要求的温度,它决定炉子的工作能力和寿命.其性能包括:①最高使用温度;②电阻系数和电阻温度系数;③表面负荷与允许表面负荷.分类:①金属电热体;②非金属电热体. ← 注意使用温度和气氛最高使用温度:最高使用温度〔电热元件本身最高的承受温度〕= 炉温+〔50~150℃〕.炉膛的最高温度主要取决于电热元件的使用温度.电阻系数:电阻系数又叫电阻率,是指电热体当温度在20℃,1m长度的电热体1mm2端面所具有的电阻值,其单位:Ω•mm2/m.电阻温度系数:电热体的电阻随着温度变化而变化,衡量这个变化程度的叫电阻温度系数.可按下式计算:式中:ρ20为电热元件在20℃的电阻率,;α为电阻温度系数,℃-1;t为电热元件的工作温度,℃.表面负荷与允许表面负荷:指电热元件单位工作面积上分担的功率.在一定电热炉功率条件下,电热元件表面负荷选得越大,则电热元件用量就越少.但电热元件表面负荷越大,其寿命越短.实际上,只有选择得当,才能得到最佳效果.9 电热体的分类与特点9.1.金属电热体①铬镍合金和铁铬铝合金铬镍合金:铬镍合金的产品塑性好,具有抗氮能力,电阻系数、电阻温度系数、密度均较大.铁铬铝合金:电阻系数比铬镍合金高,电阻温度系数则较低,密度也低,耐热性能好,可以在氧化气氛下使用.要求:温度范围,可以在氧化性气氛中使用.二者可以在1000~1300℃范围内,空气中使用最多.它们抗氧化、价格便宜、易加工、电阻大和电阻温度系数小.注意:它们抗氧化因为在高温下由于空气的氧化能生成Cr2O3或NiCrO4阻止进一步氧化.②钨、钼、钽〔Mo、W、Ta〕纯金属电热体:可以在真空或适当气氛下获得更高的温度.其共同特点是电阻系数大,熔点高,抗氧化差〔一般不能用在空气状态中〕.钼:钼的常用温度为1600~1700℃.由于钼在氧化气氛下生成氧化钼升华,在空气中不能使用,在渗碳气氛下易渗碳变脆电阻系数也较高.因此仅能应用在高纯氢和氨分解气、无水酒精蒸汽和真空中.钨:熔点最高的金属,其熔点达到3400℃,最高使用温度为2500℃,常用温度为2200~2400℃.使用气氛为真空或经脱氧的氢气或惰性气体;钽:熔点达到2900℃,一般用在真空和惰性保护气氛中〔氮气中不能用〕钽的最高使用温度:2200℃,常用温度:2000~2100℃.③铂和铂铑合金〔Pt, Pt-Rh〕铂:多用于微型电热炉中,如卧式显微镜的微型加热炉,测定冶金熔体熔点的小型电炉与标定热电偶的小型电路中,使用温度为1300~1400℃,铂铑合金丝则可用到1600℃.铂电热体的优点:能经受氧化气氛,电阻系数小,升温导热快,电热性能稳定;缺点:不能经受还原性气氛与硅铁硫碳元素的侵蚀,价格十分昂贵.9.2. 非金属电热体①碳化硅电热体形状:常为棒状或管状,也有U型与W型.耐温度骤变性好,化学性能稳定,不与酸性材料反应;耐高温,在空气中常用温度为1450℃.SiC电热体不能在真空和氢气气氛中使用.如何延长其使用寿命:在使用过程中电阻率缓慢增大—老化,可以在1300 ℃将它浸于B2O3中并升温至1500℃,则其表面形成硼化膜,增加其使用寿命.〕②二硅化钼电热体为何MoSi2电热体可以在高温下,氧化性气氛中使用:因为在高温下,发热体表面生成MoO3挥发出去,从而在发热体表面形成致密的SiO2保护膜,阻止其进一步受到氧化."MoSi2疫":在低温下〔500~700℃〕、空气中使用时,会产生二硅化钼疫,即Mo被大量氧化而又不能形成SiO2保护膜.因而要避免该情况下使用.MoSi2适用于空气,可用于氮气、惰性气体中,但不能用于还原性气氛和真空中可使用到1200~1650℃.没有"老化"现象,可以在空气中长时间使用而电阻率不变,这是其特有的优点.③碳质电热体以碳系发热体做热源的高温炉最高使用温度可达3600℃,常用温度为1800~2200℃.为防止高温氧化而烧毁,应在保护气氛中〔氢气、氮气、二氧化碳、氩气〕和真空中使用.④铬酸镧〔LaCrO3〕发热元件铬酸镧发热元件是以铬酸镧为主要成分,在高温氧化气氛电炉中使用的电阻发热元件;其耗能少,可以精确控制温度.铬酸镧发热元件的优点是能够在大气气氛下使用到1900℃〔表面温度〕,可获得1850℃的炉温;能在氧化气氛下长期使用.适合于高精度温度的自动化控制,其炉温稳定度可在1℃之内.10 电热体重要参数〔1〕元件最高使用温度:电热元件最高使用温度是指电热体在干燥的空气中表面的最高温度,并非指炉膛温度.由于散热条件不同,一般要求炉膛最高温度比电热体最高使用温度低100℃左右为宜.〔2〕电热体的表面负荷:电热体的表面负荷是指电热体在单位表面积上所承担炉子的功率数.在一定炉子功率条件下,电热体表面负荷选的大,则电热体用量就少.但电热体表面负荷越大,其寿命越短,实际上只有选择适当,才能得到最佳效果.对不同电热体,在一定条件下〔散热条件、适用温度等〕都规定有允许的表面负荷值.11 电热丝的缠绕为了维持较长而均匀的高温区,在炉子热损失大的地方要把电热丝缠的密一些.卧式管式炉:两边密,中间疏.竖式管状炉:底下密,上头疏.12 管式电阻炉的设计制作电热丝匝数的确定:其中:n—匝数;L—电热丝总长;D—炉膛外径.该匝间距离是对于均匀缠绕而言的:式中H为加热带长度.对于炉子的不同使用方式〔卧式或竖式〕或对温度场的特殊要求,可以调整匝间距离.另外,边缘要留出引线余份.炉管外涂层:炉丝绕好后,为了避免匝间短路,一般用Al2O3〔不含SiO2>粉调水〔稍加些淀粉〕称糊状,涂在炉管外面,但不宜过厚,以免干裂脱落.涂层涂好后,先在空气中阴干,然后在烘箱烘干后便可装炉.炉壳:可用薄铁板制做,为使保温均匀,形状以圆筒形为好.对于1000℃以下的炉子,炉壳内可直接填充保温材料.对于1200℃以上的电阻丝炉,在靠近电热体部分,应该有一层耐火材料,其外层为保温材料.对于1200℃左右的电阻丝炉,耐火层厚度约为50~70mm,保温层厚度为100~130mm.如果加入的耐火、保温材料均为粉料,则在二者应该使用耐火陶瓷管隔开,以免二者掺混后在高温下发生造渣反应.关于恒温带的标定:在冶金实验研究中往往要进行恒温实验.但由于试样的大小,故要求炉膛内具有一定恒温精。
- 1、下载文档前请自行甄别文档内容的完整性,平台不提供额外的编辑、内容补充、找答案等附加服务。
- 2、"仅部分预览"的文档,不可在线预览部分如存在完整性等问题,可反馈申请退款(可完整预览的文档不适用该条件!)。
- 3、如文档侵犯您的权益,请联系客服反馈,我们会尽快为您处理(人工客服工作时间:9:00-18:30)。
废塑料在炼铁工艺中的应用主要内容1.问题的提出2.废塑料的优势3.废塑料的发展4.实验设计5.高炉喷吹塑料的经济效益6.高炉喷吹塑料的应用7.结语1 问题的提出高炉喷吹技术是现代高炉炼铁生产广泛采用的新技术,它也是现代高炉炉况调节所不可缺少的重要手段之一。
喷吹的燃料可以是重油、煤粉、粒煤、天然气或还原煤气,其中,喷吹煤粉日益受到世界各个国家或地区的高度重视。
高炉炼铁工艺中采用喷吹煤粉技术,早在1840年就由S.M.班克斯提出来,并于1840~1845年在法国进行了实际操作,因工艺方面的问题没有得到解决,结果未被推广应用。
后来又经过了一个多世纪,到了20世纪60年代初期,以北美为代表的许多地区再度试验了这一技术,其间还将原来的垂直螺旋给料改成了水平螺旋给料,尽管如此,还是以失败告终。
最后,在采用了粉体气力输送技术的基础上,喷煤才真正成为在工业上得到应用的技术。
这项技术在20世纪八十年取得了明显的进步,国外高炉喷煤量已达到200kg/t的大喷煤比,喷煤率(煤粉对燃料比的比率)达38%~40%,而且在英国克利夫兰厂的大喷煤试验中已经做到煤粉、焦炭各50%(煤300kg/t),近年来,我国高炉炼铁发展迅速,高炉喷煤的应用取得了较大进步。
重点大中型企业的喷煤比和总喷煤量都有较大的提高,2012年我国的平均煤比180kg/t。
经过最近十年的研究和实践,高炉喷煤技术水平日益提高,富氧喷煤技术得到普遍应用和氧煤喷吹技术日趋成熟,大大提高了提高煤粉的燃烧率,大幅度增加喷煤量。
随着高炉喷吹技术的不断发展,喷吹物料的种类也发生了较大的变化,复合喷吹是一项很有发展潜力的高炉冶炼新技术,日本和苏联已提出了综合燃料(如天然气+重油、重油+煤粉、高炉煤气和焦炉煤气+煤粉等)的概念,并成功地进行了工业喷吹。
在炼铁工业中,人们为了降低炼铁成本,采用喷吹煤粉代替部分焦炭的工艺,这早已是一项成熟的技术,将废塑料分类、清洗、干燥等处理后,制造成粒径为6毫米的颗粒,可以代替部分煤粉用于高炉炼铁。
喷吹进高炉的废塑料颗粒在炉内高温和还原气氛下,被气化成H2和CO,随热风上升的过程中,它们作为还原剂将铁矿石还原成铁。
其反应式见(1.1)和(1.2):风口区:C n H m+1/2O2=nCO+1/2mH2+Q1(1.1)气体上升过程:Fe2O3+nCO+mH2=2Fe+nCO2+mH2O+Q2(1.2)上面2 个反应式中Q1、Q2是反应生成热2、废塑料的优势:密度小, 保管和运输费用大;种类多、形状杂, 有袋状、薄膜状、瓶状, 以及模压成形的和泡沫塑料等等;材质种类多, 而且从外观很难判定其材质;废塑料在气化中产生的H2/CO比值要大于等量的煤粉,H2的扩散能力与还原能力均大于CO,因此用废塑料代替煤粉有利用于降低高炉焦比;同时由于塑料的灰分和硫含量很低,可以减少高炉的石灰用量,进而也减少高炉产渣量和炼铁成本;塑料的平均热值约为40.00GJ/kg,大于煤粉的热值(25.00~31.00GJ/kg),也有利于提高高炉的生产效率。
有关研究表明,废塑料在风口前端区的反应率比煤粉要好得多,这是因为煤粉的粒度仅为74um~100um,吹入风口后在高炉鼓风的作用下很快被燃烧、吹散,在风口前停留时间短,故还原气的反应率仅为40%~60%;而用废塑料制成的小颗粒在风口前端区的停留时间长,致使还原气的反应率可达80%~100%。
由于废塑料在高炉中的能量利用率分为还原剂和燃料两部分,而前者的利用率远高于后者的利用率,反应率高正是保证还原利用率和总利用率的必备条件。
此外,国外一些专家还认为,经过处理好的废塑料被喷入高炉后可以节约40%的焦炭,剩余60%的焦炭完全可以满足高炉炉料的透气性和承载载荷的需要。
3、喷吹塑料的发展国外对高炉喷吹废塑料的研究其起步比较早,德国和日本已经实现工业化。
德国的不莱梅钢铁公司是第一家把高炉喷吹废塑料的设想付诸实施的厂家。
该公司于1994年2月份进行了小规模的喷吹试验,于1995年6月在2号高炉(内容积2688m3)上建造了一套喷吹能力为7×104t/a的喷吹设备,要求塑料的氯含量<2%,金属含量<1%等( 其理化性能见表1)。
高炉喷吹结果表明:所喷入的废塑料对高炉冶炼过程的影响介于煤与重油之间,但是喷吹废塑料比较便宜。
除此之外,德国的克虏伯一赫施钢铁公司、蒂森钢铁公司以及克虏伯一曼内斯曼冶金公司的胡金根厂也在高炉上正式喷吹或进行半工业试验。
日本NKK公司在京滨厂1号高炉(4907m3)上开发利用废塑料代替部分焦炭用于炼铁技术获得成功,喷吹废塑料从1997年的3×104t扩大到1999年的4×104t,喷吹结果表明:废塑料的热利用效率达80%以上;废塑料与焦炭的配置比为1:1;喷吹量为200kg/t时,CO2的发生量减少12%;无有害气体产生,而且副产品--煤气还可以用于发电。
表1 塑料颗粒物化性能粒度<1.0cm缓慢落下细粒比(<250um) <10%剩余湿度<1.0wt%堆比重>0.3kg/L灼烧残渣<4.5(65℃)——其中金属含量<1.0wt%塑料含量>90.0wt%——其中聚烯烃含量>70.0wt%——其中工程塑料含量<4.0wt%与国外相比,我国在高炉喷吹废塑料这方面实际上还处于理论研究及可行性论证阶段。
其主要的制约因素为:(1)废塑料的收集和供应量不足,无分类措施,无法保证高炉喷吹的要求;(2)我国废塑料中聚氯乙烯(PVC)含量较高,分解后产生的氯元素严重地腐蚀炉衬;(3)开发投资大,德、日两国企业开发这一技术的费用折合人民币超过一亿元。
4、实验设计4.1废塑料和煤粉在高炉风温条件下燃烧率的比较实验原料:选用目前占国内塑料产量较大的废弃塑料聚乙烯PE、聚丙烯PP、聚苯乙烯PS、聚酯PET和废塑料混合料,选用3~5mm粒度。
煤粉选用高炉喷吹系统的成品煤,其无烟煤和烟煤各站50%,各试验物料成分和煤粉粒度分析如表2~4。
塑料的H/C比在0.067—0.168之间,远高于煤粉的0.054,废塑料的灰分也远低于煤粉。
表2 试验原料的化学成分原料W C W H W O W S W灰分PE 85.60 14.21 0.19PP 85.75 14.15 0.10PS 92.16 7.63 0.21PET 3.89 3.89 31.23 0.17混料85.71 13.68 0.43 0.17煤粉82.50 4.32 1.46 0.38 11.34表3 混料的比例种类PE PP PS PET比例/% 72.2 20.8 5.6 1.4表4 煤粉粒度分析40~100目100~200目>200目30.82 40.07 29.11燃烧实验:模拟风温1200℃和1250℃,燃烧试验设备和装置如图1所示,单一燃烧每次试样质量为0.5g,通人的空气流量1L/ min ;塑料颗粒和煤粉混合试验是把不同粒度的塑料颗粒和煤粉分别按不同的质量比混合,每次试样总质量为1.0g,通入的空气流量1L/ min,然后在1250℃下对混合试样进行燃烧试验。
气体分析仪所得的数据每10s取1次,通过计算绘制出燃烧率随时间变化的曲线,最后把这些曲线分类整理进行多方面多角度的对比,找出规律,并分析其原因。
主要结论如下:(1)废塑料气化燃烧快速反应时间明显早于煤粉。
在初期的剧烈反应使通入燃烧区的空气氧气不能维持充分燃烧.而生成的CO、CO2峰值和反应完成时间也明显早于煤粉。
(2)煤粉在1250℃下经尾气分析得知整个燃烧过程中都是完全燃烧.几乎没有CO生成,煤粉裂解产物少。
不断通人燃烧区的空气能提供足够充分燃烧的氧气,所以燃烧生成CO2,很少有CO生成,但其燃烧时间长。
(3)废塑料内含的C、H可燃基高于煤粉.四种废塑料的燃烧率平均高于煤粉20~25个百分点。
在同样条件下其燃烧时问快于煤粉10~15s.时间提高率达20%~30%。
(4)在富氧条件下废塑料的燃烧率的提高与煤粉相比并不明显,这是由于废塑料在高温快速裂解气化,与氧是气相反应,其燃烧机理与煤粉不同。
换言之,废塑料在不需富氧条件下仍可获取较高的燃烧率。
(5)无论在空气还是富氧条件下,废塑料颗粒越大,燃烧时间越长,燃烧速度越慢.4.2喷吹煤与废塑料时矿石的还原粉化性能试验原料及条件:矿石为首都钢铁公司炼铁厂原料,所有原料通过烘箱120 ℃下烘烤1 h 后,再经过破碎,然后把破碎后的矿石进行筛分。
原料的成分见表5。
喷吹用煤、废塑料和焦炭的成分分析见表6。
表5 矿石成分(质量分数)%炉料Fe FeO SiO2CaO MgO MnO S Al2O3烧结矿57.2 9.4 5.23 9.78 2.17 0.18 0.016 1.85球团矿62.7 1.5 11.20 0.20 1.30 0.16 0.027 1.91澳矿66.2 0.6 3.75 0.6 0.14 0.22 0.028 2.00巴西矿68.3 1.0 1.02 0.65 0.17 0.31 0.026 0.95 表6 原料的工业分析与元素分析(质量分数)%原料工业分析元素分析灰分挥发分固定碳水分S C H N O废塑料 6.26 90.05 3.69 0.06 76.41 13.06 0.45 3.76喷吹用煤10.79 8.26 80.95 0.57 80.98 3.47 1.05 3.14焦炭12.41 79.14 7.69 0.76试验时各种矿的质量不少于40 g ,混合矿总质量为500 g ,其中,巴西矿和澳矿各占10 %。
按首都钢铁公司1号高炉生产的水平,焦比定为360 kg。
由首都钢铁公司1号高炉生产的煤气成分为基础,主要考虑CO/ CO2的比例和氢气的体积分数因素。
试验时将CO 体积分数控制在25 % ,CO2体积分数分别选择为12 %、17 %和22 %时,H2的体积分数分别对应为5 %、9 %和13 %时进行试验。
试验反应时间根据高炉的实际生产情况确定,高炉内上部区域( ≤800 ℃)的反应时间为0.5~2 h ,中部区域(800~1000 ℃)的反应时间为2.5~3 h ,下部区域(1000~1500 ℃)的反应时间为0.7~3 h。
炉料粒度为(14±2) mm 和(8±2) mm,焦炭粒度为(20±2) mm和(14±2) mm。
为了模拟高炉,在向吊篮装料时,炉料按一层焦炭一层矿的顺序分层装入。
试验方法:为了模拟高炉喷吹煤和废塑料混合燃料时的高炉生产条件,得到具有普遍意义的炉料气固相反应试验数据,采用高温炉、制气装置及配气系统组成的试验装置。