试模需知
试模操作规程
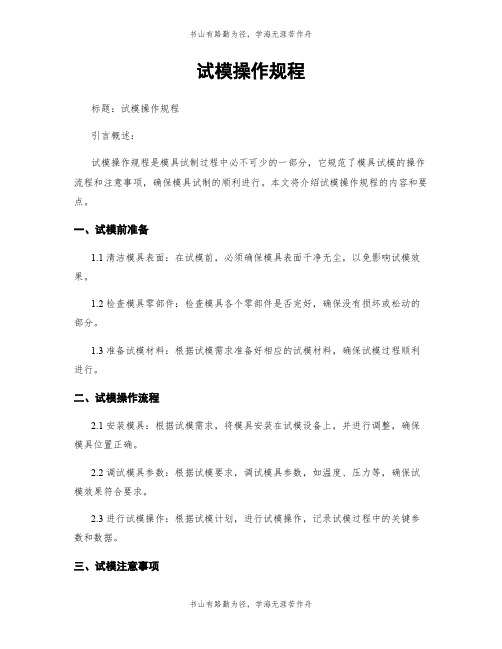
试模操作规程标题:试模操作规程引言概述:试模操作规程是模具试制过程中必不可少的一部分,它规范了模具试模的操作流程和注意事项,确保模具试制的顺利进行。
本文将介绍试模操作规程的内容和要点。
一、试模前准备1.1 清洁模具表面:在试模前,必须确保模具表面干净无尘,以免影响试模效果。
1.2 检查模具零部件:检查模具各个零部件是否完好,确保没有损坏或松动的部分。
1.3 准备试模材料:根据试模需求准备好相应的试模材料,确保试模过程顺利进行。
二、试模操作流程2.1 安装模具:根据试模需求,将模具安装在试模设备上,并进行调整,确保模具位置正确。
2.2 调试模具参数:根据试模要求,调试模具参数,如温度、压力等,确保试模效果符合要求。
2.3 进行试模操作:根据试模计划,进行试模操作,记录试模过程中的关键参数和数据。
三、试模注意事项3.1 注意安全:在试模过程中,要注意安全,避免发生意外事故,确保人员和设备安全。
3.2 注意保养:试模结束后,要对模具进行及时的清洁和保养,延长模具的使用寿命。
3.3 注意记录:在试模过程中,要及时记录关键参数和数据,为后续的模具改进提供参考。
四、试模结果评估4.1 分析试模效果:根据试模数据和效果,对试模结果进行评估,找出问题和改进方向。
4.2 提出改进建议:根据试模结果评估,提出模具改进的建议和方案,优化模具设计和制造。
4.3 总结经验教训:总结试模过程中的经验教训,为以后的试模操作提供参考和借鉴。
五、试模操作规程的优化5.1 定期更新规程:根据试模操作的实践经验,定期更新和优化试模操作规程,保持其适应性和有效性。
5.2 培训操作人员:对试模操作规程进行培训,提高操作人员的操作水平和规范性。
5.3 持续改进:不断改进试模操作规程,提高模具试制效率和质量,实现模具制造的持续发展。
结语:试模操作规程是模具试制过程中的重要指导文件,正确遵守和执行试模操作规程,可以确保模具试制的顺利进行,提高模具试制效率和质量。
试模步骤及注意事项
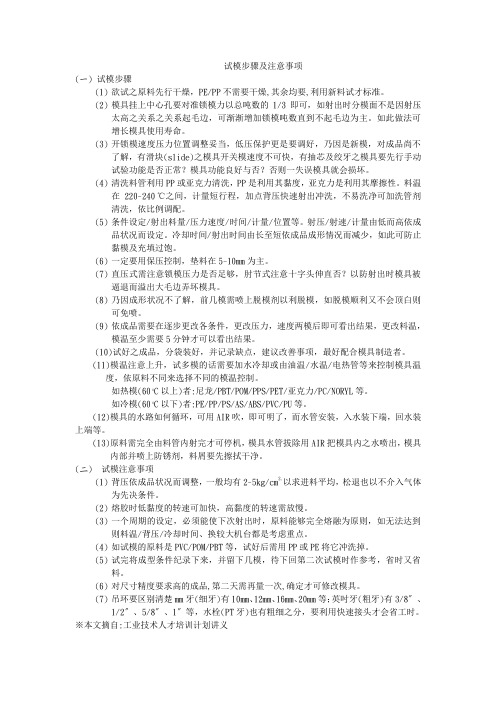
试模步骤及注意事项(一)试模步骤(1)欲试之原料先行干燥,PE/PP不需要干燥,其余均要,利用新料试才标准。
(2)模具挂上中心孔要对准锁模力以总吨数的1/3即可,如射出时分模面不是因射压太高之关系之关系起毛边,可渐渐增加锁模吨数直到不起毛边为主。
如此做法可增长模具使用寿命。
(3)开锁模速度压力位置调整妥当,低压保护更是要调好,乃因是新模,对成品尚不了解,有滑块(slide)之模具开关模速度不可快,有抽芯及绞牙之模具要先行手动试验功能是否正常?模具功能良好与否?否则一失误模具就会损坏。
(4)清洗料管利用PP或亚克力清洗,PP是利用其黏度,亚克力是利用其摩擦性。
料温在220~240℃之间,计量短行程,加点背压快速射出冲洗,不易洗净可加洗管剂清洗,依比例调配。
(5)条件设定/射出料量/压力速度/时间/计量/位置等。
射压/射速/计量由低而高依成品状况而设定。
冷却时间/射出时间由长至短依成品成形情况而减少,如此可防止黏模及充填过饱。
(6)一定要用保压控制,垫料在5~10mm为主。
(7)直压式需注意锁模压力是否足够,肘节式注意十字头伸直否?以防射出时模具被逼退而溢出大毛边弄坏模具。
(8)乃因成形状况不了解,前几模需喷上脱模剂以利脱模,如脱模顺利又不会顶白则可免喷。
(9)依成品需要在逐步更改各条件,更改压力,速度两模后即可看出结果,更改料温,模温至少需要5分钟才可以看出结果。
(10)试好之成品,分袋装好,并记录缺点,建议改善事项,最好配合模具制造者。
(11)模温注意上升,试多模的话需要加水冷却或由油温/水温/电热管等来控制模具温度,依原料不同来选择不同的模温控制。
如热模(60 O C以上)者:尼龙/PBT/POM/PPS/PET/亚克力/PC/NORYL等。
如冷模(60 O C以下)者:PE/PP/PS/AS/ABS/PVC/PU等。
(12)模具的水路如何循环,可用AIR吹,即可明了,而水管安装,入水装下端,回水装上端等。
试模操作规程
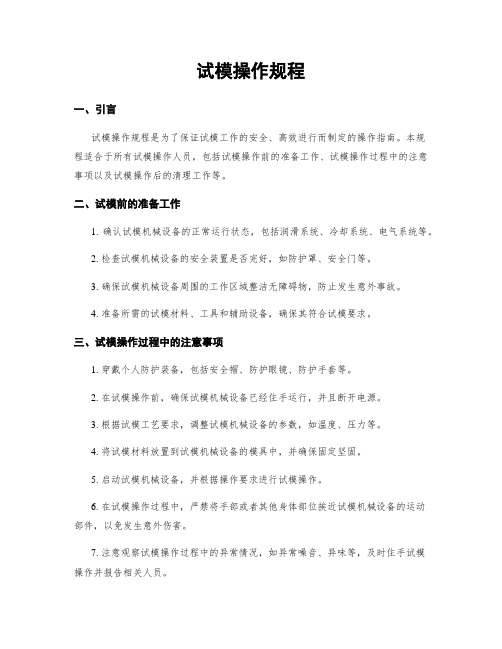
试模操作规程一、引言试模操作规程是为了保证试模工作的安全、高效进行而制定的操作指南。
本规程适合于所有试模操作人员,包括试模操作前的准备工作、试模操作过程中的注意事项以及试模操作后的清理工作等。
二、试模前的准备工作1. 确认试模机械设备的正常运行状态,包括润滑系统、冷却系统、电气系统等。
2. 检查试模机械设备的安全装置是否完好,如防护罩、安全门等。
3. 确保试模机械设备周围的工作区域整洁无障碍物,防止发生意外事故。
4. 准备所需的试模材料、工具和辅助设备,确保其符合试模要求。
三、试模操作过程中的注意事项1. 穿戴个人防护装备,包括安全帽、防护眼镜、防护手套等。
2. 在试模操作前,确保试模机械设备已经住手运行,并且断开电源。
3. 根据试模工艺要求,调整试模机械设备的参数,如温度、压力等。
4. 将试模材料放置到试模机械设备的模具中,并确保固定坚固。
5. 启动试模机械设备,并根据操作要求进行试模操作。
6. 在试模操作过程中,严禁将手部或者其他身体部位挨近试模机械设备的运动部件,以免发生意外伤害。
7. 注意观察试模操作过程中的异常情况,如异常噪音、异味等,及时住手试模操作并报告相关人员。
8. 在试模操作完成后,将试模机械设备住手运行,并断开电源。
9. 等待试模机械设备冷却后,谨慎取出试模制品,避免烫伤或者其他意外伤害。
四、试模操作后的清理工作1. 清理试模机械设备周围的工作区域,清除杂物和试模材料的残留物。
2. 检查试模机械设备的模具和其他部件是否有损坏或者磨损,如有需要及时更换或者修复。
3. 对试模机械设备进行定期保养和维护,保证其正常运行。
4. 将试模材料、工具和辅助设备归位整理,妥善保管。
五、安全注意事项1. 严禁未经培训的人员进行试模操作。
2. 在试模操作过程中,严禁酒后操作或者疲劳驾驶。
3. 在试模操作过程中,严禁将试模机械设备用于非法用途。
4. 在试模操作过程中,严禁拆卸或者修改试模机械设备的安全装置。
试模操作流程标准规范
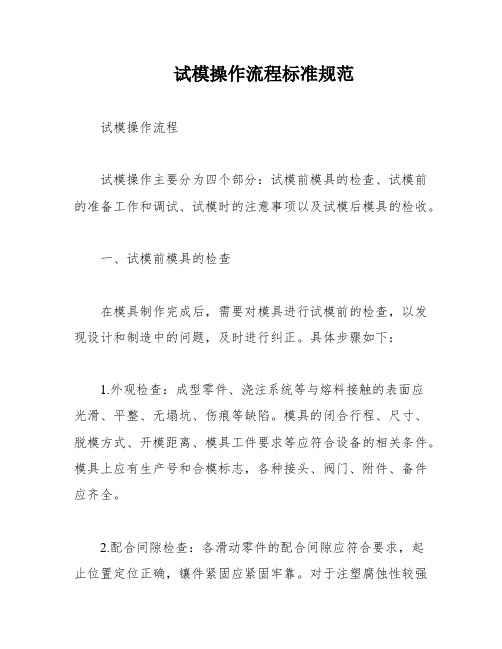
试模操作流程标准规范试模操作流程试模操作主要分为四个部分:试模前模具的检查、试模前的准备工作和调试、试模时的注意事项以及试模后模具的检收。
一、试模前模具的检查在模具制作完成后,需要对模具进行试模前的检查,以发现设计和制造中的问题,及时进行纠正。
具体步骤如下:1.外观检查:成型零件、浇注系统等与熔料接触的表面应光滑、平整、无塌坑、伤痕等缺陷。
模具的闭合行程、尺寸、脱模方式、开模距离、模具工件要求等应符合设备的相关条件。
模具上应有生产号和合模标志,各种接头、阀门、附件、备件应齐全。
2.配合间隙检查:各滑动零件的配合间隙应符合要求,起止位置定位正确,镶件紧固应紧固牢靠。
对于注塑腐蚀性较强的注塑模,其模具型腔的表面应镀铬和防腐处理。
模具的外观部分不应当有锐角,大、中型模具应有起吊用的吊孔、吊环。
3.承压零件检查:互相接触的承压零件,应有合理的承压面积和承压方式,避免直接承受挤压。
模具的稳定性良好,有足够强度,工作时应受力匀衡,行动平稳。
二、试模前的准备工作及调试试模是为了检查模具制作的质量好坏,能否生产出合格产品来。
在试模前需要进行准备工作和调试。
1.原料检查:应检查所用原料是否符合要求,不符合要求的应进行处理或更换。
欲试之原料先行干燥,PE、PP、POM不需干燥其余均要,利用新料试才标准。
2.模具挂上中心孔:要对准锁模力以总顿数的1/3即可,如射出时分模面不是因射压太高之关系起毛边,可渐渐增加锁模顿数直到不起毛边为止。
这样做可以增长模具使用寿命。
3.加热温度调试:根据选定的工艺参数将料筒和喷嘴加热至合适温度,判断温度是否合适的最好方法,是在喷嘴与模具主流道脱开时,用较低的注射压力,使熔料自喷嘴中缓慢流出,再观察料流流出情况。
三、试模时的注意事项在试模过程中需要注意以下事项:1.观察模具的闭合情况:将模具缓缓合拢,合模后各结合面均应接触紧密,不得出现间隙。
2.检查顶出脱模机构:开模时顶出脱模机构应保证顺利脱模,以便取出塑件和浇注系统废料。
试模注意事项

试模过程注意事项一、前言当我们接到一副新模具需打样试模时,我们总是渴望能早一些试出一个结果且祷求过程顺利以免浪费工时并造成困扰。
但在此我们必须提醒二点:第一、模具设计师及制造技师有时也会发生错误,在我们试模时若不提高警觉,可能会因小的错误而产生大的损害。
第二、试模的结果是要保证以后生产的顺利。
若在试模过程中没有遵循合理的步骤及做适当的记录,即无法保障量产时的顺利进行。
我们更强调的是「模具运用顺利的话将迅速增加利润的回收,否则所造成的成本损失会更甚于模具本身的造价」。
二、试模前的注意事项1. 了解模具的有关资料:最好能取得模具的设计图面,详予分析,并约得模具技师参加试模工作。
2. 先在工作台上检查其机械配合动作:要注意有否刮伤,缺件及松动等现象,模向滑板动作是否确实,水道及气管接头有无泄漏,模具之开程若有限制的话也应在模上标明。
以上动作若能在挂模前做到的话,就可避免在挂模时发现问题,再去拆卸模具所发生的工时浪费。
3. 当确定模具各部动作得宜后,就要选择适合的试模射出机,在选择时应注意(a射出容量()导杆的宽度(c)最大的开程(d)配件是否齐全等。
一切都确认没有问题后则下一步骤就是吊挂模具,吊挂时应注意在锁上所有夹模板及开模之前吊钓不要取下,以免夹模板松动或断裂以致模具掉落。
模具装妥后应再仔细检查模具各部份的机械动作,如滑板、顶针、退牙结构及限制开关等之动作是否确实。
并注意射料嘴与进料口是否对准。
下一步则是注意合模动作,此时应将关模压力调低,在手动及低速的合模动作中注意看及听是否有任可不顺畅动作及异声等现象。
4. 提高模具温度:依据成品所用原料之性能及模具之大小选用适当的模温控制机将模具之温度提高至生产时所须的温度。
俟模温提高之后须再次检视各部份的动作,因为钢材因热膨胀之后可能会引起卡模现象,因此须注意各部的滑动,以免有拉伤及颤动的产生。
5.若工厂内没有推行实验计划法则,我们建议在调整试模条件时一次只能调整一个条件,以便区分单一条件变动对成品之影响。
试模步骤及注意事项 1

试模步骤及注意事项 1. 欲试之原料务必先行干燥 2. 模具挂上,中心孔要对准确无误,锁模力视模具大小及投射面积大小而进行调整.当射出时分模面不是因为射压过高而产生毛边,可逐渐加大锁模力,直到不起毛边为主,如此可延长模具使用寿命.锁模压力选在50-70之间,不得大于95为佳. 3. 开关模速度,压力,位置,距离调整妥当,低压保护必须调校好,这是基于对新模不了解,有滑块之模具开关模速不可太快,有抽心的模应用手先行试验其功能是否正常,否则因一时失误,将导致模具的损坏. 4. 设定成型条件,包括射出料温,压力,速度,时间,位置,计量距离等.射压,速度,计量由低而高依成型状况而定,射出时间,冷却时间由长至短,依成品情形而减速少,如此可防止粘模及过度充填. 5. 适当选调背压,注意垫料量在0.5CM-1.0CM为宜,这样无论是新模或产品品质及机台的安全使用都有必要.1.注意肘节十字头是否伸直,以防射出时模具被逼退而溢出毛边造成模具损伤.2. 前几模应喷脱模剂,如脱模顺利,不致产品顶白,变形则可免喷.3. 依成品需要,修改各成型条件,如对压力,速度调整1-2模便可看出,如对模温,料温调整,要5分钟左右方可看出结果,避免因急燥而不断变更成形条件,影响试模质量.4. 试模中应注意模温的上升,试多模时应加冷却水,依据料质选择料温.5. 背压依成品状况而调整,松退距离以不介入空气为原则,储料中原料粘度低,转速可较快,原料粘度高应放慢,注意用背压时,转速越快,原料的熔融越均匀,但应注意其有无熔胶过热现象.6. 料管的料要完全射完后方可停机,必要时必须清洗料管,吹干模具冷却水路之冷却水,擦干净模腔料屑,喷防锈油.7. 填写试模报告,首件确认表,记录各成型条件,当第二次试模时,参考模具不良状况及欲修改的地方,均需作好记录射出成型的操作条件一. 关模压:原则上应大于塑胶射入模内的总压,以不出毛边为基准. 二. 压力和速度有部分相同的关系作用于模内,目的使原料进入模内能均匀,撤底,适量的充满各角落.太低会短射,缩水,太高有毛边,过饱,粘模.烧焦,易损模具及内应力高等不良现象. 三. 速度:速度的快慢决定原料在模具浇道内及成品中之状况,快有毛边,过饱.烧焦,粘模,慢了出现短射,缩水,结合不良易断等. 四. 温度:原料不同,温度各异太低溶胶颜色不均,成品内应力增大,因温度过低增压过高,可能引起螺杆断裂,过高,产品有毛边,又因冷却产生温差,引起收缩;原料会分解,变黄,变色,易断裂.冷却时间变长,气不容易排出,会有瓦斯气. 五. 背压:螺杆在旋转加料时后退之阴力称为背压.其作用使原料在输送压缩中更加紧密.能使原料的空气,水份从螺杆后排出,使溶胶中不含影响成品表面的气体成份.低会有气泡,表面银纹.高会过热,结块,溢胶,周期长,螺杆不退.同时松退的应用很重要:背压高时务必用松退并注意距离,要不介入空气及不溢胶为准则. 六. 模温高低及冷却时间的长短,影响成品的粘模,缩水,尺寸公差,表面亮度,周期等,应依实际情况而适时调整.另压克力,PC如成品肉厚时要有模温,才不会产生气泡及应力.(因肉厚冷热不均)BMC的成型要点BMC是以特殊途不饱和聚脂为主之热固硬化性树脂,具有优良的电气绝缘特性,耐热性,耐燃性,高机械强度尺寸安定性.耐蚀性,耐水性,收缩稳定性等.为各种热固硬化性成型材料中最高级品. 其加工成型条件如下: 1. 成型温度:成型温度与MBC热固性聚脂塑胶之流动性及其所选择加工成型机械加工方式有极度大之关系因素.温度在140℃-170℃2. 成型时间:加工成型时间与当时模具正确温度及成品的肉厚,形状有关,一般硬化程度可由表面光泽予以段定, 3. 成型压力:成型压力视而不见所选择加工成型机械与方式而定,材料加工后,成品表面光泽时之压力,其压力在20-200KG/CM2 4. 储存:MBC材料庆置18℃以下之冷暗处,使用后剩余品应予密闭保存,一般正常使用可存放一个月,外在之温度与MBC之软,硬将影响其储存期.如使用冷藏将延长BMC之寿命. 5. 用途:应用在各种电气产品,通信资问心无愧机零件,汽车类零件,电动工具绝缘披覆,超大型静音马达,食品餐具等均广泛应用.NL-9成型重点1. 尼龙的成型,其成型厚度对收缩率有较大影响.模温高,收缩会增大.射压调整很重要,并应注意其前收缩和后收缩.对尺寸要求严格的成品更应重视. 2. 烘料:因尼龙的吸湿性最大.放置久了,极难烘干,原料应先进先用,避免放置过久.同时未烘干的原料切勿进入下料口.因会使原料在螺牙上卷曲卡住.造成不加料,所以说要常注意烘料桶的料是否低于警界线,如低于就得加料以免料烘不干. 3. 尼龙属高温水性,易熔解,但固化也快.其融点温度与成型温度相差5-10℃而己,因此造成其变化范围较窄. 4. 其粘度低,容易流涕,加热温度在控制要注意,防止固化溢料,松退要注意应用.勿用背压. 5. 尼龙对温度依存性很大,射出速度要快.防止原料的硬化.太薄处易冷化引起充填不饱.结晶化也低.造成成品有透明性. 6. 尼龙的润滑性好,耐冲击好,但尺寸安定较差,属于工程塑胶. 7. 尼龙成型螺杆选择上要压缩比大特别留意止逆环的磨损程度应低于5-10条,如磨损过多,造成加料不稳或不加料.影响原料的供输如果磨损要速更换止逆环.以免加长周期影响生产进度及浪费电源8. 尼龙加色粉会造成加料不顺,应注意其有无色粉粘于螺牙上,必要时要加滑石粉给予排除,参考用量:1KG+0.5G滑石粉. 9. 尼龙参考成型条件:模温:60-80度,料管温220-260度,烘料80-110度,2-4H,软化点:220度。
试模操作规程
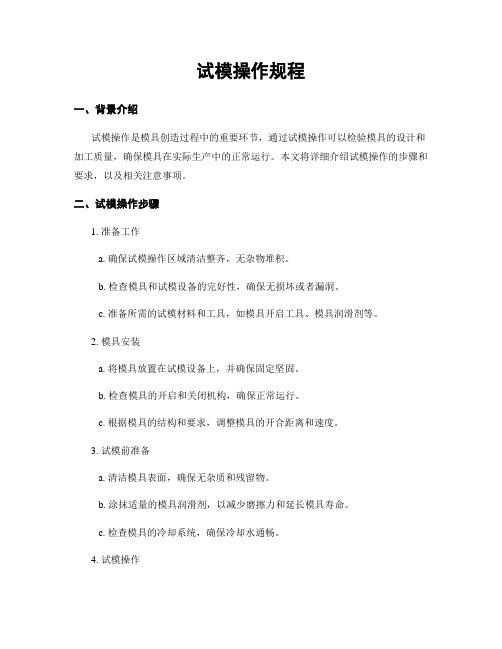
试模操作规程一、背景介绍试模操作是模具创造过程中的重要环节,通过试模操作可以检验模具的设计和加工质量,确保模具在实际生产中的正常运行。
本文将详细介绍试模操作的步骤和要求,以及相关注意事项。
二、试模操作步骤1. 准备工作a. 确保试模操作区域清洁整齐,无杂物堆积。
b. 检查模具和试模设备的完好性,确保无损坏或者漏洞。
c. 准备所需的试模材料和工具,如模具开启工具、模具润滑剂等。
2. 模具安装a. 将模具放置在试模设备上,并确保固定坚固。
b. 检查模具的开启和关闭机构,确保正常运行。
c. 根据模具的结构和要求,调整模具的开合距离和速度。
3. 试模前准备a. 清洁模具表面,确保无杂质和残留物。
b. 涂抹适量的模具润滑剂,以减少磨擦力和延长模具寿命。
c. 检查模具的冷却系统,确保冷却水通畅。
4. 试模操作a. 打开试模设备的电源,确保电气系统正常工作。
b. 按照试模操作顺序,挨次进行模具开合、注塑、冷却等操作。
c. 观察模具运行状态,注意是否有异常声音或者震动。
d. 根据试模结果,调整模具参数,如温度、压力等。
5. 试模后处理a. 关闭试模设备电源,断开电气连接。
b. 将试模产生的零件进行检查和测量,确保质量符合要求。
c. 清洁模具和试模设备,避免杂质积累和腐蚀。
d. 记录试模操作过程中的关键参数和问题,以备后续参考。
三、试模操作要求1. 安全第一:在进行试模操作前,必须穿戴好个人防护装备,如安全帽、防护眼镜、防护手套等。
2. 操作规范:按照试模操作步骤进行操作,不得随意更改操作顺序或者参数设定。
3. 环境整洁:保持试模操作区域的整洁,确保无杂物干扰试模操作。
4. 设备维护:定期对试模设备进行维护保养,确保设备的正常运行和安全性。
5. 质量控制:对试模产生的零件进行严格检查和测量,确保质量符合要求。
6. 参数记录:记录试模操作中的关键参数和问题,以便后续分析和改进。
四、注意事项1. 遵守操作规程,严禁擅自更改试模操作步骤或者参数设定。
试模应注意什么

3.調整壓力及射出量以求生產出外觀令人滿意的成品,但是不可跑毛邊尤其是還有某些模穴成品尚未完全凝固時,在調整各種控制條件之前應思考一下,因為充模率稍微變動,可能會引起甚大的充模變化。
記錄且研判數據以做為修改模具及生產條件之需要,且為未來量產時之參考依據。
1.使加工運轉時間長些,以穩定熔膠溫度及液壓油溫度。
2.按所有成品尺寸的過大或過小以調整機器條件,若縮水率太大及成品顯得射料不足,也可資參考以增加閘口尺寸。
3.各模穴尺寸的過大或過小予以修正之,若模穴及閘口尺寸尚屬正確,那麼就應試改機器條件,如充模速率,模具溫度及各部壓力等,並檢視某些模穴是否充模較慢。
4.要耐心的等到機器及模具的條件穩定下來,即பைடு நூலகம்中型機器可能也要等30分鐘以上。可利用這段時間來查看成品可能發生的問題。
5.螺桿前進的時間不可短於閘口塑料凝固的時間,否則成品重量會降低而損及成品之性能。且當模具被加熱時螺桿前進時間亦需酌予加長以便壓實成品。
6.合理調整減低總加工週期。
7.把新調出的條件至少運轉30分鐘以至穩定,然後至少連續生產一打全模樣品,在其盛具上標明日期、數量,並按模穴分別放置,以便測試其確實運轉之穩定性及導出合理的控制公差。(對多穴模具尤有價值)。
4.提高模具溫度:
依據成品所用原料之性能及模具之大小選用適當的模溫控制機將模具之溫度提高至生產時所須的溫度。
俟模溫提高之後須再次檢視各部份的動作,因為鋼材因熱膨脹之後可能會引起卡模現象,因此須注意各部的滑動,以免有拉傷及顫動的產生。
5.若工廠內沒有推行實驗計畫法則,我們建議在調整試模條件時一次只能調整一個條件,以便區分單一條件變動對成品之影響。
- 1、下载文档前请自行甄别文档内容的完整性,平台不提供额外的编辑、内容补充、找答案等附加服务。
- 2、"仅部分预览"的文档,不可在线预览部分如存在完整性等问题,可反馈申请退款(可完整预览的文档不适用该条件!)。
- 3、如文档侵犯您的权益,请联系客服反馈,我们会尽快为您处理(人工客服工作时间:9:00-18:30)。
模具的调试1.塑料选用在试模之前,首先遇到的就是采用什么原料来进行注射成形的问题。
在产品设计时,根据塑件的用途及要求,确认了材料的规格型号,并且在模具设计时,依照塑料的特点进行结构设计和料道设计,以满足注射成形的需要。
试模前也有必要对所选用的原料性能及工艺特性进行全面了解。
用于注射成形的通用塑料,主要有聚苯乙烯、聚乙烯、聚丙烯、ABS四种,这四种材料在当前生产中约占全部注射成形塑料80%以上,其中前三种约占70%。
试模用料力求与制品设计要求一致,这样便于成形注射及对样品的检查和验收。
但是如果在试模所在地一时难以寻求牌号完全一致的原料,也可以代用料来完成试注射。
尤其是在头次试模,目的在于检验模具的基本结构、制件的成形状况和壁厚状况时,可以这样做。
但是,在选取代用料时要掌握一个原则:原料性能要基本相近;收缩率大小要基本一致。
如果原料的成形收缩率大小不同时,要在试模后进行核算,以求检验所需要的数据。
值得注意的是:在使用代用料进行试模的过程中,如果发生注射不满、顶出不顺、成形不理想等现象时,不要轻易对模具进行修改,而要认真分析此现象是否因原料特性的不同而产生的避免轻意修改模具而产生副作用。
2.烘干处理原料选用后,在试模前要进行原料预干燥处理。
各种塑料的干燥方法,应根据塑料性能和具体条件进行选择。
对于单纯是吸湿的塑料,如SAN、PMMA、ABS、PVC等可用热风干燥器,或者料斗干燥器,在75-85℃时进行干燥。
对于吸水率高的聚酰胺(尼龙)要采用真空烘箱干燥。
聚碳酸酯吸水率虽然较小,但只要有少许水分就会造成水解,水解后相对分子质量下降,使成型制件变得很脆,因此应该在120℃干燥10h以上,并需要采用料斗干燥器或红外线加热器进一步干燥。
试模前的原料干燥是一个重要的工序,不能认为试模提供的制件只是样件不是产品而忽略之。
有时因为原料干燥效果不好,造成样件表面缺陷无法发现,增加试模次数,造成不必要的经济损失。
3. 工艺条件的选择试模的目的之一是要寻找合理的注射条件,原料不同,工艺条件也就不相同。
在首次注射时要根据制件的特点及选用原料的型号,尽量选择理论方面趋于合理的工艺条件。
要从基本工艺条件入手,假定模具结构及尺寸是合理的,试注射中,针对模具特点,对工艺条件逐步进行调整。
(1) 注射量注塑机的注射量是指设备对空注射(无模具)条件下,注射螺杆或柱塞杆作一次注射行程时,注射装置所达到的注射量、注射量有两种表示方法: ①用注射出的熔料的体积(cm3)表示; ② 以聚苯乙烯为标准,用注射熔料的重量(g)表示。
在实际注射中,塑料的密度随着温度、压力变化而变化,对非结晶型塑料(PVC、PC、PS、ABS、PMMA)密度变化约为7%,而结晶型塑料(PE、PP、PA等),密度变化为15%左右,加之注射中必然产生的注射回流现象,因而等重量的塑料在塑化温度和常温下制品的体积有差异,并且实际注射量必须小于理论注射量。
Q = a Qt=aAs S=a Ds2 Sπ/4式中 Q—实际注射量(cm3);Qt: 理论注射量(cm3)a 注射量修正系数,通常在0.7- 09范围内;As 螺杆端截面积(cm2);Ds 螺杆直径(cm)S 螺杆最大注射行程(cm)。
值得一提的是,当完成一次试模后,所选用的注射量应当做详细的记录,以便为下一次试模或正式生产中计算螺杆移动距离及调整工艺条件提供准确的参考数据。
(2) 注射压力注塑机的注射压力是指在注射中的螺杆或柱塞端面处作用于熔料单位面积上的力,其单位为bar。
而实际注射压力是要克服熔料流经喷嘴、浇道和模腔等处的流动阻力。
注射压力与塑料性能、塑化方式、塑化温度、模具温度、流动阻力、制品形状及制品精度等因素均有密切的关系。
一般情况下,薄壁制品的注射压力高于厚壁制品。
粘度高的制品注射压力高于易流动的制品。
根据经验适当调整注射压力值。
(3) 注射速度、注射速率和注射时间注射速度,是指注射时,螺杆或柱塞移动速度(cm/s)。
注射速率,是指单位时间内熔料从喷嘴射出的理论容量(cm3/s)。
注射时间,是指螺杆或柱塞作一次注射所需要的时间(s)它们之间有如下关系Qz = Qt:/t =πDs2 S/4t=π Ds2 Vz / 4式中 Qz — 注射速率(cm3/s);S — 注射行程(cm);t — 注射时间(s)Vz — 注射速度(cm/s);Qt — 理论注射量(cm3)。
注射速度的快慢直接影响到制品质量和生产效率。
注射速率低,制品易产生冷接缝,密度不均,制品内应力大等。
合理地提高注射速度,可以减少熔料在模腔内的温度降,改善压力传递效果,保持制品密度均匀和精度。
尤其对一些薄壁、流长比大的制件采用高速注射更为有利。
但是,注射速度过高,熔料离开喷嘴后会产生不规则流动,产生大的剪切热,常常烧焦物料。
因而注射过程中,注射速度应根据树脂性能、工艺条件、制品形状、壁厚、模具等情况来确定。
对此,下表可供参考。
常用注射速率、注射时间表当高速注射结束时,马上进入注射保压阶段,注塑机的保压压力由小流量、高压油泵提供。
该压力能在浇口尚未冻结时消除制件中的凹陷和空隙。
国前,注射保压实际设定时间是根据经验确定。
如果能绘制出模腔内“压力一时间关系图”,就可以较精确地预测保压时间。
(4) 背压及螺杆转速1) 背压指螺杆塑化物料时,推向其前端的熔融物料对螺杆产生的反压力。
背压对注射成形的影响主要体现在物料塑化效果和塑化能力两方面。
增大背压提髙熔体的密实程度,同时剪切作用增强,塑化效果提高。
但塑化能力却降低。
为了满足生产需要,必须提高螺杆转速来予以补偿。
背压大小与塑料品种,喷嘴种类和加料方式有关。
一般情况下,背压的使用范围为34~275 Bar,其中下限值适用于大多数塑料。
选择背压时应注意以下事项:① 采用直通喷嘴和后加料方式时,应采用较低的背压,否则易发生流延现象;采用阀式喷嘴和前加料方式时,背压可取大一些。
② 对于热敏性塑料(如硬聚氯乙烯、聚甲醛、聚氟氯乙烯等),背压应取低些;对于高黏度塑料,为防止系统过载,也不宜使用较大背压。
③在保证塑化质量和熔体密实度的情况下,尽量使用低背压。
2) 螺杆转速 螺钎转速也是影响塑化能力和塑化效果的重要参数。
转速提高可以提高塑化能力。
但螺杆转速超过一定数值后,由于物料在机筒内受热时间太短,反而使塑化质量变差。
因此,对每种物料都有一个较合适的转速范围,需根据实际情况而定。
对此,表下提供的背压和螺杆转速可供选择参考。
(5) 注射料温度及模具温度塑料加工温度是其注射成形的重要工艺参数。
温度的高低是根据塑料性质以及制品结构复杂程度决定的。
1) 料温 料温主要取决于机筒和喷嘴两部分的温度。
机筒及喷嘴温度的选用原则如下① 机筒温度应保持在塑料粘流温度以上和分解温度以下某一适当范围。
在满足要求的条件下,尽量选低值。
通常情况下,为高于熔点10~50℃。
② 机筒温度与模具结构特点有关,对于薄壁,大流长以及带有嵌件的制品.选用较高的机筒温度。
③ 为了避免流延现象,喷嘴温度可略低于机筒最高温度,但不能太低,否则会使熔体发生早凝,堵住喷嘴。
④ 对于螺杆注塑机,当注射行程接近理论最大注射行程时,由于螺杆后退使其起塑化作用的部分相对变短因此应使机筒后段(靠加料斗)温度相应提高,以保证槊化质量。
⑤ 判断料温是否合适,可观察对空注射料流的外观。
如果料流均匀,光滑,无泡,色泽均匀,则说明料温合适;如料流毛糙,有银丝或变色,说明料温不合适。
2) 模具温度 模具温度指和制品接触的模腔表壁温度,它直接影响熔体的充模流动行为,制品的冷却速度和成形后的制品性能。
根据塑料品种不同,注射成形中需用的模具温度也不相同。
如果模具温度选择得合理,并且分布均匀,可以有效的改善熔体的充模流动性能、制品的外观质量以及一些主要的物理和力学性能。
① 为了保证制品具有较髙的尺寸精度,防止变形,模温必须低于塑料的热变形温度。
② 对于高粘度的塑料,如FC、PPO等,为了提高充模性能,需要采用较高的模具温度。
对于粘度低、流动性好的塑料,如PE、PP、PS、PA等,可用较低的模温,以缩短生产周期。
③ 对于厚壁制品,因充模和冷却时间长,若模温过低,也容易使制品内部产生真空泡和较大的应力,所以不宜采用太低的模具温度。
④ 对于某些塑料品种和制品形状,出于脱模的需要,应采用较高的模具温度。
注射工艺参数的选择也可利用国内已开发的塑料注射成形及模具设计专家系统进行工艺查询以帮助确定试模工艺。
4 试模工艺条件倾向性在实践中,针对不同制品特征,试模时选择工艺条件有倾向性1)板状类制件 板状制件的特征是成形面积大,型腔浅,需要较大的合模力。
因而,这类制件在注射之前,必须认真地校核合模力大小是否符合实际需要。
同时,由于受力面积大,可能造成型腔模板在大跨距支承下的弯曲变形,甚至当这种弹性变形超过极限值时,会使模具造成损坏。
因面,最好采用多级注射法,并且随时观察制件中心部位厚度尺寸。
一方面探索能够使熔料充满型腔的最小压力,同时寻找合理的料温以防止产品的翘曲变形。
2)框架型制件 框架型制件的特点是成形投影面积不大,但是型腔复杂,依靠各类加强肋使制件整体强度得到加强。
在首次试注射中,推荐用高料温、低中压注射工艺条件。
在料量选用上不得少于欲用量的8%,这样可以弥补框架式制件不易充满的缺陷。
反之,如果采用高压注射,很容易造成填充过实过量,镶块缝内充入原料,使肋、条等处被夹在型腔内,无法继续进行试模。
这是框架型制件模具试模次数偏多的主要原因之-。
例如,电视机前壳模具,制件重量在I000g以上,在4000g以上的注塑机上成形,型腔复杂,肋条多,如果初次注射不采用上述方法进行,很容易走弯路,甚至无法连续进行。
试生产一段时间后,可根据制品的缺陷进行工艺调整,以求得合理。
3) 深腔形制件型腔深度大于制件长边的2/3时,被称为深腔。
这种制件的特点是工作面可能是内腔,也可能是外腔,致使开模时,制件可能留在定模方,也可能留在动模方。
这时试注射方式要有所考虑。
当需要制件留在定模一方时,依靠安装在定模上的反顶脱模装置将其推出型腔,这时必须采用一次性注满型腔,使制件尽可能完整。
反之,制件缺料过多,导致脱模板无法起作用,欲清除型腔内残缺不全的制件,将是十分困难的。
例如,双缸洗衣机内筒制件,内表面为工作面,模具开启时,制件留在型腔内,由液压缸反顶装置将制件脱出型腔,采用多级注射的方法,一次性充满型腔,效果很好。
当需要制件留在动模一方时,情况不同,即使有不完整的制件留在动模型芯上,清理比较方便,所以不必要一定过量注射。
总之,制件的形状多种多样,模具整体结构和镶拼方式各不相同,巧妙地选用工艺条件及特点,可以使试模顺利进行,并且保护模具不受损坏。
采用各种方式试模,都要掌握一个基本原则,即每一次注射间隔时间要尽可能短,以力求注射连续性。