聚氨酯胶黏剂设计方法
聚氨酯胶水配方
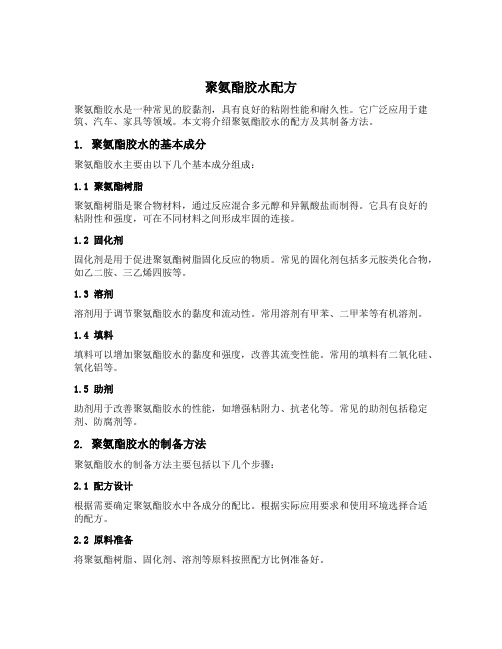
聚氨酯胶水配方聚氨酯胶水是一种常见的胶黏剂,具有良好的粘附性能和耐久性。
它广泛应用于建筑、汽车、家具等领域。
本文将介绍聚氨酯胶水的配方及其制备方法。
1. 聚氨酯胶水的基本成分聚氨酯胶水主要由以下几个基本成分组成:1.1 聚氨酯树脂聚氨酯树脂是聚合物材料,通过反应混合多元醇和异氰酸盐而制得。
它具有良好的粘附性和强度,可在不同材料之间形成牢固的连接。
1.2 固化剂固化剂是用于促进聚氨酯树脂固化反应的物质。
常见的固化剂包括多元胺类化合物,如乙二胺、三乙烯四胺等。
1.3 溶剂溶剂用于调节聚氨酯胶水的黏度和流动性。
常用溶剂有甲苯、二甲苯等有机溶剂。
1.4 填料填料可以增加聚氨酯胶水的黏度和强度,改善其流变性能。
常用的填料有二氧化硅、氧化铝等。
1.5 助剂助剂用于改善聚氨酯胶水的性能,如增强粘附力、抗老化等。
常见的助剂包括稳定剂、防腐剂等。
2. 聚氨酯胶水的制备方法聚氨酯胶水的制备方法主要包括以下几个步骤:2.1 配方设计根据需要确定聚氨酯胶水中各成分的配比。
根据实际应用要求和使用环境选择合适的配方。
2.2 原料准备将聚氨酯树脂、固化剂、溶剂等原料按照配方比例准备好。
2.3 混合反应将聚氨酯树脂和固化剂按照一定比例混合,并加入适量的溶剂进行搅拌反应。
反应时间和温度会影响胶水的性能,需要根据具体情况进行控制。
2.4 填料添加在混合反应过程中,适量的填料可以根据需要进行添加,提高胶水的黏度和强度。
2.5 助剂添加在混合反应过程中,根据需要可以添加适量的助剂,改善胶水的性能。
2.6 检测和调整制备好的聚氨酯胶水需要进行一系列的检测,如黏度、粘附力、耐久性等。
根据检测结果对配方进行调整,以获得符合要求的胶水产品。
3. 聚氨酯胶水的应用领域聚氨酯胶水广泛应用于以下领域:3.1 建筑领域聚氨酯胶水可用于建筑材料的粘接和密封,如玻璃、金属、石材等材料之间的连接。
3.2 汽车制造聚氨酯胶水可用于汽车零部件的粘接,如车身板材、挡风玻璃等。
聚氨酯胶粘剂配方
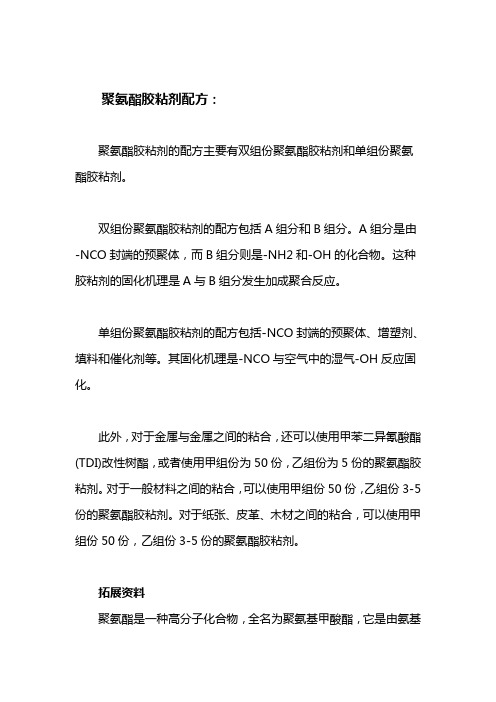
聚氨酯胶粘剂配方:
聚氨酯胶粘剂的配方主要有双组份聚氨酯胶粘剂和单组份聚氨酯胶粘剂。
双组份聚氨酯胶粘剂的配方包括A组分和B组分。
A组分是由-NCO封端的预聚体,而B组分则是-NH2和-OH的化合物。
这种胶粘剂的固化机理是A与B组分发生加成聚合反应。
单组份聚氨酯胶粘剂的配方包括-NCO封端的预聚体、增塑剂、填料和催化剂等。
其固化机理是-NCO与空气中的湿气-OH反应固化。
此外,对于金属与金属之间的粘合,还可以使用甲苯二异氰酸酯(TDI)改性树酯,或者使用甲组份为50份,乙组份为5份的聚氨酯胶粘剂。
对于一般材料之间的粘合,可以使用甲组份50份,乙组份3-5份的聚氨酯胶粘剂。
对于纸张、皮革、木材之间的粘合,可以使用甲组份50份,乙组份3-5份的聚氨酯胶粘剂。
拓展资料
聚氨酯是一种高分子化合物,全名为聚氨基甲酸酯,它是由氨基
甲酸酯连接的有机单元组成的聚合物。
聚氨酯有聚酯型和聚醚型两大类,可制成聚氨酯塑料(以泡沫塑料为主)、聚氨酯纤维(中国称为氨纶)、聚氨酯橡胶及弹性体。
软质聚氨酯主要是具有热塑性的线性结构,比PVC发泡材料有更好的稳定性、耐化学性、回弹性和力学性能,具有更小的压缩变型性。
隔热、隔音、抗震、防毒性能良好,因此用作包装、隔音、过滤材料。
硬质聚氨酯塑料质轻、隔音、绝热性能优越、耐化学药品,电性能好,易加工,吸水率低,主要用于建筑、汽车、航空工业、保温隔热的结构材料。
聚氨酯弹性体性能介于塑料和橡胶之间,耐油,耐磨,耐低温,耐老化,硬度高,有弹性,主要用于制鞋工业和医疗业。
聚氨酯还可以制作粘合剂、涂料、合成革等。
聚氨酯胶粘剂
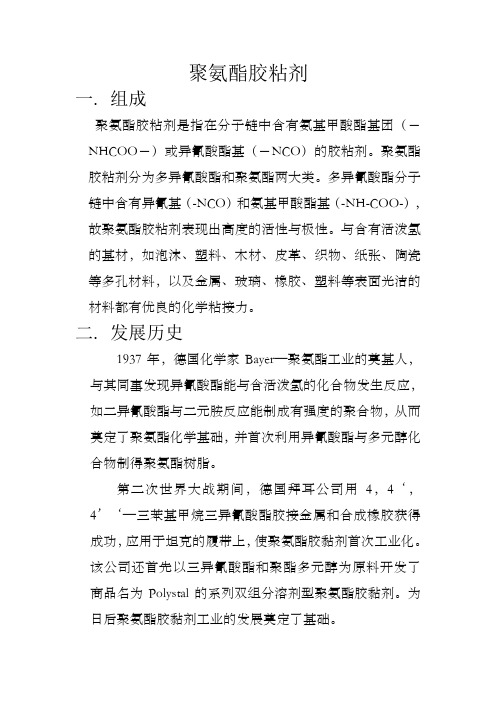
聚氨酯胶粘剂一.组成聚氨酯胶粘剂是指在分子链中含有氨基甲酸酯基团(-NHCOO-)或异氰酸酯基(-NCO)的胶粘剂。
聚氨酯胶粘剂分为多异氰酸酯和聚氨酯两大类。
多异氰酸酯分子链中含有异氰基(-NCO)和氨基甲酸酯基(-NH-COO-),故聚氨酯胶粘剂表现出高度的活性与极性。
与含有活泼氢的基材,如泡沫、塑料、木材、皮革、织物、纸张、陶瓷等多孔材料,以及金属、玻璃、橡胶、塑料等表面光洁的材料都有优良的化学粘接力。
二.发展历史1937年,德国化学家Bayer—聚氨酯工业的奠基人,与其同事发现异氰酸酯能与含活泼氢的化合物发生反应,如二异氰酸酯与二元胺反应能制成有强度的聚合物,从而奠定了聚氨酯化学基础,并首次利用异氰酸酯与多元醇化合物制得聚氨酯树脂。
第二次世界大战期间,德国拜耳公司用4,4‘,4’‘—三苯基甲烷三异氰酸酯胶接金属和合成橡胶获得成功,应用于坦克的履带上,使聚氨酯胶黏剂首次工业化。
该公司还首先以三异氰酸酯和聚酯多元醇为原料开发了商品名为Polystal的系列双组分溶剂型聚氨酯胶黏剂。
为日后聚氨酯胶黏剂工业的发展奠定了基础。
美国第二次世界大战后于1953年引进德国技术,开发了以蓖麻油和聚醚多元醇为原料的聚氨酯胶黏剂。
1968年,Goodyear公司开发了无溶剂型聚氨酯结构胶黏剂“,并成功地应用于汽车用玻璃纤维增强塑料的胶接。
1978年又开发了单组分湿固化型聚氨酯胶黏剂,1984年美国市场上又出现了反应型热熔聚氨酯胶黏剂。
日本于1954年引进德国和美国聚氨酯技术,1960年生产聚氨酯原料,1966年开始生产聚氨酯胶黏剂。
1975年日本光洋公司开发成功“乙烯类聚氨酯”水性胶黏剂,于1981年投入工业化生产。
目前日本聚氨酯胶黏剂的研究与生产十分活跃,与美国、西欧一起成为聚氨酯生产、出口大国。
三.聚氨酯胶粘剂的制备与配方1.多异氰酸酯胶粘剂(单组分)1.配制:将多异氰酸酯单体与溶剂按一定比例混合均匀,即可配制成多异氰酸酯胶粘剂(单组分)。
聚氨酯的粘接机理、粘接工艺及配方设计

聚氨酯的粘接机理、粘接工艺及配方设计聚氨酯的粘接机理、粘接工艺及配方设计概述:A、金属、玻璃、陶瓷等的粘接金属、玻璃等物质表面张力很高,属于高能表面,在PU胶粘剂固化物中含有内聚能较高的氨酯键和脲键,在一定条件下能在粘接面上聚集,形成高表面张力胶粘层。
一般来说,胶粘剂中异氰酸酯或其衍生物百分含量越高,胶粘层的表面张力越大,胶越坚韧,能与金属等基材很好地匹配,粘接强度一般较高。
含一NCO基团的胶粘剂对金属的粘接机理如下:金属表面一般存在着吸附水(即使经过打磨处理的金属表面也存在微量的吸附水或金属氧化物水合物),一NCO与水反应生成的脲键与金属氧化物之间由于氢键而螯合形成酰脲—金属氧化物络合物,一NCO 基团还能与金属水合物形成共价键等。
在无一NCO场合,金属表面水合物及金属原子与氨酯键及脲键之间产生范德华力和氢键,并且以TDI、MDI为基础的聚氨酯胶粘剂含苯环,具有冗电子体系,能与金属形成配价键。
金属表面成分较为复杂,与PU胶之间形成的各种化学键或次价键(如氢键)的类型也很复杂。
玻璃、石板、陶瓷等无机材料一般由Ah09、S02、CaO和Na20等成分构成,表面也含吸附水、羟基,粘接机理大致与金属相同oB、塑料、橡胶的粘接橡胶的粘接一般选用多异氰酸酯胶粘剂或橡胶类胶粘剂改性的多异氰酸酯胶粘剂,胶粘剂中所含的有机溶剂能使橡胶表面溶胀,多异氰酸酯胶粘剂分子量较小,可渗入橡胶表层内部,与橡胶中存在的活性氢反应,形成共价键。
多异氰酸酯还会与潮气反应生成脲基或缩二脲,并且在加热固化时异氰酸酯会发生自聚,形成交联结构,与橡胶分子交联网络形成聚合物交联互穿网络(IPI),因而胶粘层具有良好的物理性能。
用普通的聚氨酯胶粘剂粘接橡胶时,由于各材料基团之间的化学及物理作用,也能产生良好的粘接。
PVC、PET、FRP等塑料表面的极性基团能与胶粘剂中的氨酯键、酯键、醚键等基团形成氢键,形成有一定粘接强度的接头。
有人认为玻纤增强塑料(FRP)中含一OH基团,其中表面的一OH与PU胶粘剂中的一NCO 反应形成化学粘接力。
粘接性好的水性PU胶粘剂制作方法

水性胶粘剂的配制方法如下:
将100份Mn=2000的聚己二醇碳酸酯二醇,加入到50份温度为50℃的丙酮中,溶解均匀后,再加入15.58份双羟甲基丙酸,在搅拌并使温度保持在50~70℃的条件下,加入49份异佛尔酮二异氰酸酯,进行加聚反应,直至反应物中的NCO基含量不下降为止。
加入4.7份氢氧化钠中和成盐30min,接着加入233份水使之乳化30min,减压蒸除丙酮后制得水性聚氨酯胶粘剂(I)。
用该胶粘剂粘接木块/木块试件的拉伸剪切强度为7.7MPa,粘接PVC/木块试件为2.0MPa,粘接ABS/木块试件为2.0MPa,粘接Al/木块试件为7.9MPa和粘接钢/木块试件为3.0MPa。
如果用以甘油为起始剂制得的聚醚多元醇取代上述的聚己醇碳酸酯二醇,按照上述相同的合成方法制得的水性聚氨酯胶粘剂(Ⅱ)。
其对应的拉伸剪切强度分别为4.5MPa、1.4MPa、1.4MPa、4.9MPa和0。
上述两种水性聚氨酯胶粘剂的粘接性能对比见表所列。
mdi基水性聚氨酯胶粘剂的合成与性能研究

mdi基水性聚氨酯胶粘剂的合成与性能研究1概述mdi基水性聚氨酯胶粘剂(polyurethane adhesive)是一种穿透性胶粘剂,可以同时实现强度和附着力,是目前工业制造过程中广泛使用的胶粘剂之一。
一般来说,mdi基水性聚氨酯胶粘剂具有优异的机械强度、耐热强度、耐非常冷和高温环境耐久性,广泛应用于家具制造、汽车制造、家电机械以及建筑行业。
2合成过程MDI基水性聚氨酯胶粘剂的研制过程大致可分为以下几个步骤:(1)合成MDI基原料:用特殊的化学原料(如挥发性溶剂,四氯化碳,甲苯)经过精确控制合成反应,以生成MDI(氨基甲酰二苯甲醚)及其他MA(甲氨基苯甲酰二酸)等组份。
(2)合成溶剂:将MDI和MA混合,加入水或醇为溶剂制成合成水性溶液;(3)引入增强剂:注入胶粘剂合成溶液中的增强剂(如矿物油、溶剂油、界面活性剂等)可使该水性聚氨酯胶粘剂的机械之强度和粘接性能更为优异;(4)合成聚氨酯。
将上述各原料混合,加入所需的各种增强剂,利用连乳剂工艺或者聚氨酯柔性膜工艺,进行低温反应或高温反应,以生成具有高强度、高粘接力、耐环境及机械性能的富弹性水性聚氨酯胶粘剂。
3性能特点MDI基水性聚氨酯胶粘剂具有良好的粘接性能,能有效满足特定的粘接任务。
它具有良好的机械强度,耐冷热,抗紫外线等特性,能够提供更稳定的结构支撑,增强制造件整体的可靠性。
它还具有优异的耐热能力和附着力,有效提高了制件性能,确保了粘接件获得良好的湿稳定性。
此外,它不仅具有良好的抗化学腐蚀性能,而且还能有效降低上衣层渗透性,从而改善了产品的耐久性。
4结论MDI基水性聚氨酯胶粘剂具有优异的机械强度、耐热强度、耐非常冷和高温环境耐久性,对建筑行业,家具制造行业,汽车制造行业,家电机械行业等有很大的助力和作用。
同时,它还具有良好的抗化学腐蚀性能,抗紫外线能力,改善表面渗透性,能够持久耐久,更安全,满足现代行业多种需求。
高性能水性环保聚氨酯胶粘剂及施工工艺

高性能水性环保聚氨酯胶粘剂及施工工艺目前,世界合成胶粘剂发展的趋势突出表现为环保和高性能化[1]。
随着环保法规的日趋严格,各发达国家大力研制水性胶粘剂。
由于水性聚氨酯胶粘剂的综合性能优越,在各类水性胶粘剂中独树一帜,近年来受到国内外的广泛关注,特别是高性能水性聚氨酯胶粘剂的开发研究已成为热点课题。
1、水性聚氨酯水性聚氨酯是配制水性聚氨酯胶粘剂的基础物质和关键组分,它的性能直接决定胶粘剂的最终性能。
根据粒子所带电荷种类,水性聚氨酯可分为阴离子,阳离子,非离子三种类型。
水性聚氨酯的制备一般是先合成一定分子量的聚氨酯预聚体,然后在剪切力作用下将预聚体分散在水中。
目前其制备方法以亲水单体扩链、自乳化法为主(所谓亲水单体扩链法),即在聚氨酯预聚体的分子结构中引入亲水性扩链剂,所得聚合物无需外加乳化剂就能直接分散于水中形成水性聚氨酯。
亲水单体扩链法的合成工艺有溶剂法、预聚物分散水中扩链法、熔融分散缩聚法等。
早在四、五十年代,水性聚氨酯已有少量的研究,但由于贮存稳定性差等原因,这项研究工作进展不大,直到1972年德国Bayer公司正式将聚氨酯水分散液作为皮革涂料后,才开始迅速发展[8]。
据报道,1992年至1997年间水性聚氨酯的年平均增长率为8%[9]。
我国从70年开始研究水性聚氨酯,近年来研究工作也十分活跃[10]。
研制工作具有以下特点:(1)从产品结构来看,主要是乳液型,水溶性次之,胶乳型则不常见。
(2)从原料来看,多元醇主要用聚醚型,聚酯型次之,聚碳酸酯极少见。
异氰酸酯的品种更少,只有TDI,HDI、MDI仅见报道。
扩链剂多用醇类,胺类较少使用。
(3)从制备方法及种类来看,一般是自乳化,羧酸型、阴离子体系;外乳化,磺酸型,季铵盐型乳化体系较少;熔融分散,固体自发分散法等则未涉及。
(4)从理论与应用角度来看,着重应用开发,理论研究很少。
欲配制高性能水性聚氨酯胶粘剂,必须制备高性能水性聚氨酯。
大多数水性聚氨酯主要是线性热塑性聚氨酯,由于其涂膜没有交联,分子量较低,因而耐水性,耐溶剂性,胶膜强度等性能还较差。
聚氨酯胶粘剂配方
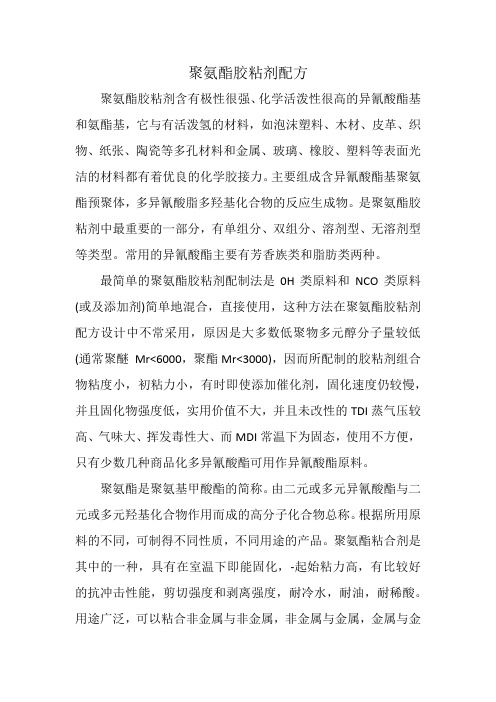
聚氨酯胶粘剂配方聚氨酯胶粘剂含有极性很强、化学活泼性很高的异氰酸酯基和氨酯基,它与有活泼氢的材料,如泡沫塑料、木材、皮革、织物、纸张、陶瓷等多孔材料和金属、玻璃、橡胶、塑料等表面光洁的材料都有着优良的化学胶接力。
主要组成含异氰酸酯基聚氨酯预聚体,多异氰酸脂多羟基化合物的反应生成物。
是聚氨酯胶粘剂中最重要的一部分,有单组分、双组分、溶剂型、无溶剂型等类型。
常用的异氰酸酯主要有芳香族类和脂肪类两种。
最简单的聚氨酯胶粘剂配制法是0H类原料和NCO类原料(或及添加剂)简单地混合,直接使用,这种方法在聚氨酯胶粘剂配方设计中不常采用,原因是大多数低聚物多元醇分子量较低(通常聚醚Mr<6000,聚酯Mr<3000),因而所配制的胶粘剂组合物粘度小,初粘力小,有时即使添加催化剂,固化速度仍较慢,并且固化物强度低,实用价值不大,并且未改性的TDI蒸气压较高、气味大、挥发毒性大、而MDI常温下为固态,使用不方便,只有少数几种商品化多异氰酸酯可用作异氰酸酯原料。
聚氨酯是聚氨基甲酸酯的简称。
由二元或多元异氰酸酯与二元或多元羟基化合物作用而成的高分子化合物总称。
根据所用原料的不同,可制得不同性质,不同用途的产品。
聚氨酯粘合剂是其中的一种,具有在室温下即能固化,-起始粘力高,有比较好的抗冲击性能,剪切强度和剥离强度,耐冷水,耐油,耐稀酸。
用途广泛,可以粘合非金属与非金属,非金属与金属,金属与金属,粘结力十分牢固。
其配方还体现在:一. 双组份的聚氨酯胶粘剂配方一:A组份甲苯二异氰酸酯(简称TDI)改性树酯(溶于醋酸乙酯成为溶液)100份B组份固化剂TDI的羟基化合物的改性物10~50份本法适用于金属与金属之间的粘合。
配方二:A组份100份B组份10份本法适用于一般材料之间的粘合。
配方三:A组份100份B组份5—10份本法适用于纸张、皮革、木材之间的粘合。
二、单组份的聚氨脂胶粘剂配方:蓖麻油38份甲苯二异氰酸酯11.75份苯乙烯49.75份过氧化二苯甲酰0.5份以上于20—80℃时溶化混合均匀。
- 1、下载文档前请自行甄别文档内容的完整性,平台不提供额外的编辑、内容补充、找答案等附加服务。
- 2、"仅部分预览"的文档,不可在线预览部分如存在完整性等问题,可反馈申请退款(可完整预览的文档不适用该条件!)。
- 3、如文档侵犯您的权益,请联系客服反馈,我们会尽快为您处理(人工客服工作时间:9:00-18:30)。
胶粘剂的设计是以获得最终使用性能为目的,对聚氨酯胶粘剂进行配方设计,要考虑到所制成的胶粘剂的施工性(可操作性)、固化条件及粘接强度、耐热性、耐化学品性、耐久性等性能要求。
1. 聚氨酯分子设计——结构与性能
聚氨酯由于其原料品种及组成的多样性,因而可合成各种各样性能的高分子材料。
例如从其本体材料(即不含溶剂)的外观性严主讲,可得到由柔软至坚硬的弹性体、泡沫材料。
聚氨酯从其本体性质(或者说其固化物)而言,基本上届弹性体性质,它的一些物理化学性质如粘接强度、机械性能、耐久性、耐低温性、耐药品性,主要取决于所生成的聚氨酯固化物的化学结构。
所以,要对聚氨酯胶粘剂进行配方设计,首先要进行分子设计,即从化学结构及组成对性能的影响来认识。
有关聚氨酯原料品种及化学结构与性能的关系。
2. 从原料角度对PU胶粘剂制备进行设计
聚氨酯胶粘剂配方中一般用到三类原料:一类为NCO类原料(即二异氰酸酯或其改性物、多异氰酸酯),一类为oH类原料(即含羟基的低聚物多元醇、扩链剂等,广义地说,是含活性氢的化合物,故也包括多元胺、水等),另有一类为溶剂和催化剂等添加剂。
从原料的角度对聚氨酯胶粘剂进行配方设计,其方法有下述两种。
(1).由上述原料直接配制
最简单的聚氨酯胶粘剂配制法是0H类原料和NCO类原料(或及添加剂)简单地混合、直接使用。
这种方法在聚氨酯胶粘剂配方设计中不常采用,原因是大多数低聚物多元醇分子量较低(通常聚醚 Mr<6000,聚酯Mr<3000),因而所配制的胶粘剂组合物粘度小、初粘力小。
有时即使添加催化剂,固化速度仍较慢,并且固化
物强度低,实用价值不大。
并且未改性的TDI蒸气压较高,气味大、挥发毒性大,而MDI常温下为固态,使用不方便,只有少数几种商品化多异氰酸酯如PAPl、Desmodur R、Desmodur RF、Coronate L等可用作异氰酸酯原料。
不过,有几种情况可用上述方法配成聚氨酯胶粘剂。
例如:(1)由高分子量聚酯(Mr5000-50000)的有机溶液与多异氰酸酯溶液(如 Coronate L)组成的双组分聚氨酯胶粘剂,可用于复合层压薄膜等用途,性能较好。
这是因为其主成分高分子量聚酯本身就有较高的初始粘接力,组成的胶粘剂内聚强度大; (2)由聚醚(或聚酯)或及水、多异氰酸酯、催化剂等配成的组合物,作为发泡型聚氨酯胶粘剂、粘合剂,用于保温材料等的粘接、制造等,有一定的实用价值。
(2).NCO类及OH类原料预先氨酯化改性
如上所述,由于大多数低聚物多元醇的分子量较低,并且TDI挥发毒性大,MDI 常温下为固态,直接配成胶一般性能较差,故为了提高胶粘剂的初始粘度、缩短产生一定粘接强度所需的时间,通常把聚醚或聚酯多元醇与TDI或MDI单体反应,制成端NCO基或OH基的氨基甲酸酯预聚物,作为NCO成分或OH成分使用。
3. 从使用形态的要求设计PU胶
从聚氨酯胶粘剂的使用形态来分,主要有单组分和双组分。
A.单组分聚氨酯胶粘剂
单组分聚氨酯胶粘剂的优点是可直接使用,无双组分胶粘剂使用前需调胶之麻烦。
单组分聚氨酯胶粘剂主要有下述两种类型。
(1)以一NCO为端基的聚氨酯预聚物为主体的湿固化聚氨酯胶粘剂,合成反应利用空气中微量水分及基材表面微量吸附水而固化,还可与基材表面活性氢基团反
应形成牢固的化学键。
这种类型的聚氨酯胶一般为无溶剂型,由于为了便于施胶,粘度不能太大,单组分湿固化聚氨酯胶粘剂多为聚醚型,即主要的含一OH原料为聚醚多元醇。
此类胶中游离NCO含量究竟以何程度为宜,应根据胶的粘度(影响可操作性)、涂胶方式、涂胶厚度及被粘物类型等而定,并要考虑胶的贮存稳定性。
(2)以热塑性聚氨酯弹性体为基础的单组分溶剂型聚氨酯胶粘剂,主成分为高分子量端OH基线型聚氨酯,羟基数很小,当溶剂开始挥发时胶的粘度迅速增加,产生初粘力。
当溶剂基本上完全挥发后,就产生了足够的粘接力,经过室温放置,多数该类型聚氨酯弹性体中链段结晶,可进一步提高粘接强度。
这种类型的单组分聚氨酯胶一般以结晶性聚酯作为聚氨酯的主要原料。
单组分聚氨酯胶另外还有聚氨酯热熔胶、单组分水性聚氨酯胶粘剂等类型。
B.双组分聚氨酯胶粘剂
双组分聚氨酯胶粘剂由含端羟基的主剂和含端NCO基团的固化剂组成,与单组分相比,双组分性能好,粘接强度高,且同一种双组分聚氨酯胶粘剂的两组分配比可允许一定的范围,可以此调节固化物的性能。
主剂一般为聚氨酯多元醇或高分子聚酯多元醇。
两组分的配比以固化剂稍过量,即有微量NCO基团过剩为宜,如此可弥补可能的水分造成的NCO损失,保证胶粘剂产生足够的交联反应。
4. 根据性能要求设计PU胶
若对聚氨酯胶粘剂有特殊的性能要求,应根据聚氨酯结构与性能的关系进行配方设计。
不同的基材,不同的应用领域和应用环境,往往对聚氨酯胶有一些特殊要求,如在工业化生产线上使用的聚氨酯胶要求快速固化,复合软包装薄膜用的聚氨酯胶粘剂要求耐酸耐水解,其中耐蒸煮软包装用胶粘剂还要求一定程度的高温粘接力,等等。
A.耐高温
聚氨酯胶粘剂普遍耐高温性能不足。
若要在特殊耐温场合使用,可预先对聚氨酯胶粘剂进行设计。
有几个途径可提高聚氨酯胶的耐热性,如:(1)采用含苯环的聚醚、聚酯和异氰酸酯原料;(2)提高异氰酸酯及扩链剂(它们组成硬段)的含量;
(3)提高固化剂用量;(4)采用耐高温热解的多异氰酸酯(如含异氰脲酸酯环的),或在固化时产生异氰脲酸酯;(5)用比较耐温的环氧树脂或聚砜酰胺等树脂与聚氨酯共混改性,而采用pN技术是提高聚合物相容性的有效途径。
B.耐水解性
聚酯型聚氨酯胶粘剂的耐水解性较差,可添加水解稳定剂(如碳化二亚胺、环氧化合物等)进行改善。
为了提高聚酯本身的耐水解性,可采用长链二元酸及二元醇原料(如癸二酸、1,6—己二醇等),有支链的二元醇如新戊二醇原料也能提高聚酯的耐水解性。
聚醚的耐水解性较好,有时可与聚酯并用制备聚氨酯胶粘剂。
在胶粘剂配方中添加少量有机硅偶联剂也能提高胶粘层的耐水解性。
C.提高固化速度
提高固化速度的一种主要方法是使聚氨酯胶粘剂有一定的初粘力,即粘接后不再容易脱离。
因而提高主剂的分子量、使用可产生结晶性聚氨酯的原料是提高初粘力和固化速度的有效方法。
有时加入少量三乙醇胺这类有催化性的交联剂也有助于提高初粘力。
添加催化剂亦为加快固化的主要方法。