冲压工艺案例分析讲解
冲压工艺技术创新案例
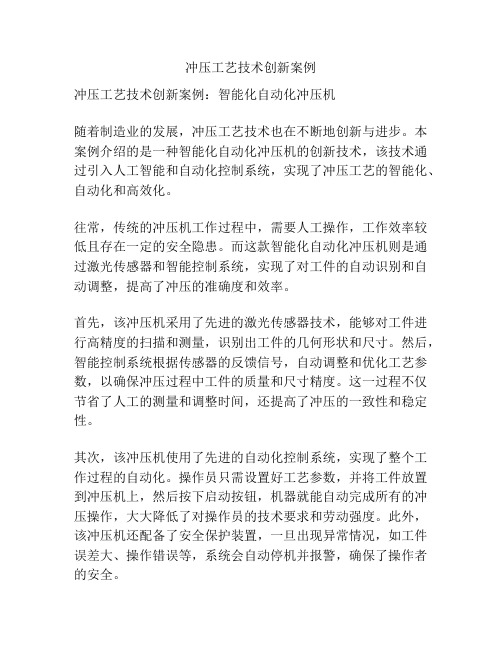
冲压工艺技术创新案例冲压工艺技术创新案例:智能化自动化冲压机随着制造业的发展,冲压工艺技术也在不断地创新与进步。
本案例介绍的是一种智能化自动化冲压机的创新技术,该技术通过引入人工智能和自动化控制系统,实现了冲压工艺的智能化、自动化和高效化。
往常,传统的冲压机工作过程中,需要人工操作,工作效率较低且存在一定的安全隐患。
而这款智能化自动化冲压机则是通过激光传感器和智能控制系统,实现了对工件的自动识别和自动调整,提高了冲压的准确度和效率。
首先,该冲压机采用了先进的激光传感器技术,能够对工件进行高精度的扫描和测量,识别出工件的几何形状和尺寸。
然后,智能控制系统根据传感器的反馈信号,自动调整和优化工艺参数,以确保冲压过程中工件的质量和尺寸精度。
这一过程不仅节省了人工的测量和调整时间,还提高了冲压的一致性和稳定性。
其次,该冲压机使用了先进的自动化控制系统,实现了整个工作过程的自动化。
操作员只需设置好工艺参数,并将工件放置到冲压机上,然后按下启动按钮,机器就能自动完成所有的冲压操作,大大降低了对操作员的技术要求和劳动强度。
此外,该冲压机还配备了安全保护装置,一旦出现异常情况,如工件误差大、操作错误等,系统会自动停机并报警,确保了操作者的安全。
最后,该冲压机还具备远程监控和数据分析功能。
智能控制系统可以实时监控冲压过程中各项参数的变化,并将数据上传到云平台进行分析和处理。
生产管理人员可以通过电脑或手机随时查看设备的运行状态和生产数据,及时调整和优化工艺参数,提高生产效率和产品质量。
该智能化自动化冲压机的应用在某汽车零部件制造企业中,取得了显著的成果。
相比传统的冲压机,该冲压机实现了全自动化操作,大幅度提高了生产效率,减少了劳动力成本。
同时,冲压产品的质量和尺寸精度也得到了极大的提高,满足了汽车行业对零部件的高质量要求。
总之,智能化自动化冲压机的出现,不仅改变了传统冲压工艺的操作方式,提高了生产效率和产品质量,同时还为冲压工艺的发展带来了新的机遇。
冲压 精益改善 案例

冲压精益改善案例冲压精益改善案例:提高生产效率与降低成本一、案例背景某汽车零部件制造公司主要生产汽车覆盖件、结构件等产品,其中冲压工艺是生产过程中的重要环节。
然而,在过去的几年中,公司面临着生产效率低下、成本高昂的问题。
为了解决这些问题,公司决定引入精益生产理念,对冲压生产线进行全面改善。
二、问题分析在引入精益生产之前,公司对冲压生产线进行了详细的问题分析。
主要问题包括:1. 设备布局不合理,物料流转不顺畅;2. 生产线不平衡,部分工序产能过剩,部分工序等待时间过长;3. 员工操作不规范,导致产品质量不稳定;4. 设备维护不到位,故障率较高。
三、改善措施针对以上问题,公司采取了以下改善措施:1. 对设备布局进行优化,实现物料流转的顺畅。
通过调整设备布局,减少物料在生产线上的搬运距离和时间,提高生产效率。
2. 调整生产线平衡,提高产能。
对各工序进行产能评估,调整设备配置和工艺流程,使各工序产能基本平衡,减少等待时间。
3. 制定操作规范,提高员工操作水平。
通过培训和指导,使员工掌握正确的操作方法,提高产品质量稳定性。
4. 加强设备维护保养,降低故障率。
建立设备维护保养制度,定期对设备进行检查和保养,减少设备故障对生产的影响。
四、实施效果经过一段时间的改善实施,公司取得了以下成果:1. 生产效率提高:通过优化设备布局和调整生产线平衡,生产效率提高了30%。
2. 成本降低:改善后,减少了不必要的浪费和等待时间,降低了生产成本。
3. 产品质量提升:通过规范员工操作和提高设备维护保养水平,产品质量得到了显著提升。
4. 员工满意度提高:改善后的生产线更加人性化和高效,提高了员工的工作满意度和归属感。
5. 企业竞争力增强:通过精益改善,公司在汽车零部件市场上获得了更高的竞争力。
客户对公司的产品和服务更加满意,订单量不断增加。
五、总结与展望通过本次冲压精益改善案例的实施,公司成功地提高了生产效率、降低了成本、提升了产品质量、提高了员工满意度,并增强了企业的竞争力。
●02.冲压SE分析典型案例图册-冲压●

件号 item
5401111/2222
现状及问题 点 problem
提案理由
①需要追加、变更 ②品质问题 qulity ③性能、技能改善
版本 edition
④成本、投资费用 ○ ⑤作业性改善
分析单位department of analysis:
分 析analysis
检 查check
分析日期 the date of analysis: 管理编号:
前轮鼓包中段(左)
件号
item
现状及问题 点 problem
提案理由
①需要追加、变更
④成本、投资费用
②品质问题 qulity
○ ⑤作业性改善
③性能、技能改善
版本
edition
对策及要求事项
MEASUREMENT
分析单位department of analysis:工艺所
分 析analysis 检 查check 确 认validate
分析单位Department:工艺所 分析analysis 检查check 确认validate
分析日期:
对策及要求事项 MEASUREMENT
冲压press
工艺
焊接weld 涂装coating
总装assembly
总工艺师technologist
①
跟踪情况 ②
result ③
④
小搭接面分布在角部, 工装制造困难。
零件名称 PARTNAME
置物板边段加强件(左)
件号 ITEM
现状及问题点 PROBLEM
5401715
提案理由
①需要追加、变更
④成本、投资费用
②品质问题 qulity ○ ⑤作业性改善
制造工艺改进与优化案例分享工作总结

制造工艺改进与优化案例分享工作总结在制造业的发展历程中,制造工艺的改进与优化始终是企业提升产品质量、降低成本、提高生产效率的关键途径。
通过对制造工艺的不断探索和创新,许多企业成功地实现了转型升级,增强了市场竞争力。
以下将为大家分享几个具有代表性的制造工艺改进与优化案例,并对其进行总结和分析。
一、案例一:某汽车零部件制造企业的冲压工艺优化在某汽车零部件制造企业中,冲压工艺是生产汽车车身零部件的重要环节。
然而,原有的冲压工艺存在着模具磨损严重、生产效率低下、废品率高等问题。
为了解决这些问题,企业组织了专门的工艺改进团队。
首先,团队对模具结构进行了重新设计。
通过采用先进的CAD/CAE 软件进行模拟分析,优化了模具的受力分布,减少了模具在冲压过程中的变形和磨损。
同时,选用了更高强度和耐磨性的模具材料,延长了模具的使用寿命。
其次,对冲压工艺参数进行了优化。
通过大量的实验和数据分析,确定了最佳的冲压速度、压力和温度等参数,提高了冲压件的成型质量和尺寸精度。
此外,引入了自动化生产设备,实现了冲压过程的自动化上下料和搬运,大大提高了生产效率,降低了人工劳动强度。
通过以上一系列的改进措施,该企业的冲压工艺得到了显著优化。
模具的使用寿命提高了 50%,生产效率提高了 30%,废品率降低了20%,为企业带来了显著的经济效益。
二、案例二:某电子制造企业的 SMT 贴片工艺改进SMT(Surface Mount Technology)贴片工艺是电子制造中的关键工艺之一。
在某电子制造企业中,SMT 贴片工艺存在着贴片精度不高、生产良率低、设备故障率高等问题。
针对贴片精度不高的问题,企业引进了高精度的贴片机,并对贴片程序进行了优化。
通过精确的坐标定位和贴片路径规划,提高了贴片的精度和一致性。
为了提高生产良率,加强了对原材料的质量控制。
严格筛选电子元器件的供应商,确保元器件的质量和可靠性。
同时,优化了 PCB (Printed Circuit Board)板的设计,提高了 PCB 板的可制造性。
冲压工艺与模具设计实例

冲压工艺与模具设计实例首先,汽车门板是汽车外部的重要组成部分,其工艺要求较为严格,所以在生产过程中需要采用冲压工艺来完成。
在进行冲压工艺设计时,首先需要根据门板的设计要求确定其尺寸、形状和材质。
然后根据这些参数来确定冲压工艺的具体流程和步骤,包括拉伸、冲裁、弯曲等。
接下来是模具设计。
模具设计是冲压工艺中非常重要的一环,其质量和精度直接影响到产出产品的质量和成本。
在进行模具设计时,首先需要根据门板的形状和工艺要求来确定模具的结构和尺寸。
然后根据这些参数来设计模具的具体形状和结构,包括上模、下模、剪切模、冲压模等。
在完成模具设计后,需要进行模具加工和调试。
模具加工是指根据设计图纸来制作模具的具体零部件,包括机加工、热处理、组装等。
而模具调试是指在完成模具加工后,需要对模具进行调试和试验,以确保其能够满足冲压工艺的要求。
最后,经过上述步骤,我们就可以将汽车门板的冲压工艺和模具设计完成。
这样一来,我们就可以通过冲压工艺来生产出符合设计要求的汽车门板,从而满足市场需求并获得经济效益。
这也充分体现了冲压工艺与模具设计在制造业中的重要性和应用价值。
冲压工艺与模具设计在汽车制造中的应用非常广泛,因为许多汽车零部件都需要使用冲压工艺来生产,其中汽车车门板就是一个非常典型的例子。
通过冲压工艺,可以使车门板具有良好的强度和表面质量,并且可以大大提高生产效率。
接下来我们将深入探讨汽车门板的冲压工艺与模具设计的相关内容。
首先我们要了解汽车门板的冲压工艺。
汽车门板常常采用多工序冲压工艺来完成,主要包括拉伸、冲裁、弯曲等工序。
在进行冲压工艺设计时,需要充分考虑材料的特性和板料的变形规律。
比如在进行拉伸工序时,需要注意材料的延展性和变形能力,确保拉伸后的板料能够满足设计要求。
在冲裁工序中,需要考虑板料的裁剪力和裁剪形状,以及切边拉伸等问题。
在弯曲工序中,需要考虑板料的抗弯性能和成形效果等因素。
只有理解和掌握了这些特性,才能够设计出合理的冲压工艺流程。
冲压工艺的基础知识及实例PPT课件
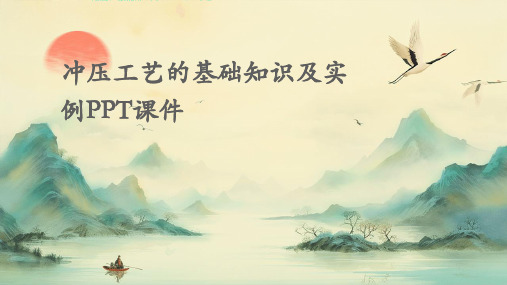
五金零件的冲压工艺通常包括落 料、弯曲、拉伸、成形等工序, 根据零件的不同要求,可以选择 不同的冲压工艺和模具结构。
家用电器外壳的冲压工艺
家用电器外壳是指家用电器产品的外壳 和支架,通常由金属材料制成。
冲压工艺是制造家用电器外壳的主要方 家用电器外壳的冲压工艺通常包括落料、 法之一,通过模具对金属材料进行冲压, 拉伸、成形等工序,同时还需要考虑到
精度、效率和质量。
环保与可持续发展
随着全球环保意识的不断提高, 未来的冲压工艺将更加注重环保 和可持续发展,如采用环保材料、 节能技术等,推动冲压行业实现
绿色发展。
跨领域合作
未来的冲压工艺将更加注重与其 他领域的合作,如与新材料、新 工艺、智能制造等领域进行交叉 融合,推动冲压工艺的创新发展。
THANKS
冲压
通过模具和冲压设备对板料进 行塑性变形,使其成为所需形
状和尺寸的零件。
下料
将冲压完成的零件从模具中取 出,并进行必要的检查和修整
。
质量检测
对冲压完成的零件进行质量检 测,确保其符合要求。
冲压后的处理
清理
对零件进行清洗,去除表面的 油污、毛刺和氧化皮等。
校正
对零件的形状和尺寸进行校正 ,确保其符合最终要求。
冲压工艺的市场前景
汽车行业需求
随着汽车轻量化、安全性要求的 提高,冲压工艺在汽车行业的应
用将更加广泛。
电子产品制造
随着电子产品更新换代加速,精密、 小型化的冲压件需求将持续增长。
航空航天领域
随着航空航天技术的进步,高性能、 高精度的冲压件需求也将增加。
06
结论
总结冲压工艺的重要性和应用
重要性
冲压工艺是一种重要的金属加工技术,广泛应用于汽车、电子、航空航天等制造业领域。通过冲压工 艺可以制造出各种形状复杂、精度要求高的零部件,对提高产品质量、降低生产成本具有重要意义。
冲压磨具结构实用案例分享深入了解成功之道

冲压磨具结构实用案例分享深入了解成功之道在工业制造领域,冲压磨具是一种常用的工具,用于加工金属板材或条材。
它们的结构设计和使用方式对于冲压过程的高效性和成品质量有着重要的影响。
本文将通过分享几个冲压磨具的实用案例,深入探讨成功的结构设计和使用方法,以期提供一些有益的参考和启示。
案例一:模具结构的细节设计在冲压磨具的设计中,模具结构的细节决定了其加工精度和稳定性。
一家汽车零部件制造厂对其模具结构进行了优化设计,以提高冲压生产线的效率和产品质量。
首先,他们对冲压模具的支撑结构进行了改进。
通过增加支撑点和设置辅助支撑装置,提高了模具在冲压过程中的稳定性,降低了变形和振动的风险。
其次,他们增加了模具的导向装置,使其在加工过程中的移动更加平稳。
通过合理设置滑动道、导向柱和导向套,成功减少了磨具的摩擦和卡紧现象,提高了冲压的精度和效率。
此外,他们还优化了模具的冲堵结构。
通过减小冲孔套的直径和增加冲头的冲击力,他们成功解决了冲堵现象,提高了模具的使用寿命和生产效率。
案例二:磨具材料的选择和应用另一个成功的案例来自一家金属制造企业,他们通过合理选择和应用磨具材料,实现了高效的冲压加工。
首先,他们使用了高硬度和抗磨损的钢材作为磨具的工作面材料。
这种材料具有优异的耐磨性和耐冲击性,能够有效减少磨具在加工过程中的磨损和损坏,提高了使用寿命和生产效率。
其次,他们采用了表面涂层技术来增加磨具的表面硬度和润滑性。
通过使用钛涂层或氮化处理等方法,他们成功减少了磨具与金属板材之间的摩擦力,提高了冲压的稳定性和精度。
此外,他们还使用了先进的磨具润滑剂,以减少磨具与材料之间的摩擦和热量积聚。
这种润滑剂能够有效降低冲压过程中的摩擦阻力,减少磨具的磨损和形变,提高加工的质量和效率。
结论通过以上案例的分享,我们可以看出冲压磨具的结构设计和使用方法对于提高生产线的效率和产品质量至关重要。
在模具结构的设计中,我们应注重细节并进行优化,例如增加支撑点、优化导向装置和冲堵结构等。
冲 压 工 艺 设 计 及 案 例 分 析

如 分 离 工 序 中 的 冲 孔 、 落 料 、 切边 , 成 形 工 序 中 的 弯 曲、翻边、拉深等。工序性质的确定主要取决于冲压 件 的 结 构 形 状 、 尺寸 精 度 , 同 时 需 要 考 虑 工 件 的 变 形 性 质和具体的生产条件。 • 工序性质的确定,应遵循以下原则。
上一页 下一页 返回
学习单元一 工艺方案的制定
• 2) 工 序 性 质 应 保 证 变 形 区 为 弱 区 • 弱 区 : 是 指 变 形 抗 力 小 的 区 域 , 根 据 阻 力 最 小 定 律 ,应
使 变 形 区 为 弱 区 , 以 达 到 变 形 容易 , 同 时 又 保 证 不 变 形 区的相对稳定。 • 如 图 8-2 所 示 的 起 伏 件 , 若 外 形 有 效 尺 寸 D 很 大 , 则 平 板 外 圈 部 分 与 所 要 胀 出 的 凸 起内 圈 相 比 强 弱 明 显 , 起 伏时外缘就不会发生收缩变形。若D很小,则不能保 证 不 变 形 区 的稳 定 , 只 好 改 变 工 序 性 质 。 • 有时变形区与非变形区强弱对比不明显,为了使变形 区 为 弱 区 , 就 需 要 增 加 工 序 。 如图 8-3 所 示 的 冲 压 件 , 外 径 尺 寸 是 100 mm, 翻 边 时 产 生 收 缩 变 形 。 当 改 为 115 mm 时 ,翻 边 时 外 径 不 再 收 缩 , 最 后 切 边 保 证 外 径 尺 寸 100 mm, 切 边 工 序 就 是 附 加 的 工 序。
• 3) 工 序 性 质 应 保 证 零 件 的 质 量 • 冲压件的几何形状或尺寸精度要求较高时,必须增加
校 形 工 序 或 其 他 工 序 。例 如 , 如 图 8-3 所 示 , 若 竖 边 的 厚 度 不 允 许 变 薄 , 就 不 能 采 用 翻 边 工 序 。 又 如 图 8- 5所 示 的 平 板 压 筋 件 , 由 于 筋 离 平 板 边 缘 很 近 , 将 使 压 筋 变 形 不 均 匀 , 制 件 产 生 较 大 的 翘 曲 或皱 折 , 因 而 必 须 增加拉深工序,提高制件周边的刚度后再压筋,压筋 后 则 需 修 边 。 这 里 拉 深和 修 边 工 序 便 是 保 证 零 件 质 量 而 增加的工序。
- 1、下载文档前请自行甄别文档内容的完整性,平台不提供额外的编辑、内容补充、找答案等附加服务。
- 2、"仅部分预览"的文档,不可在线预览部分如存在完整性等问题,可反馈申请退款(可完整预览的文档不适用该条件!)。
- 3、如文档侵犯您的权益,请联系客服反馈,我们会尽快为您处理(人工客服工作时间:9:00-18:30)。
一、冲压制造案例分析和讲解
图1所示冲裁件,材料为Q235,厚度为1mm,大批量生产。
试制定工件冲压工艺规程、设计其模具、编制模具零件的加工工艺规程。
零件名称:1#件
生产批量:中批量
材料:Q235
一、冲压件工艺分析
2. 工艺方案及模具结构类型
3. 排样设计
4.冲压力与压力中心计算
工件如图找到坐标计算得
24*12+60*0+24*12+14.5*24+38.6*27.97+14.5*24+31.4*12+31.4*12
Y= ——————————————————————————————=2.5 24+60+24+14.5+38.5+14.5+34.1+31.4
X=8.3
5.工作零件刃口尺寸计算
落料部分以落料凹模为基准计算 ,落料凸模按间隙值配制;冲孔部分以冲孔凸模为基准计算,冲孔凹模按间隙值配制。
既以落料凹模、冲孔凸模为基准,凸凹模按间隙值配制。
刃口尺寸计算见表1。
表 1 刃口尺寸计算
6.工作零件结构尺寸
7.其它模具零件结构尺寸
根据倒装复合模形式特点: 凹模板尺寸并查标准JB/T-6743.1-94,确定其它模具模板尺寸列于表2:
根据模具零件结构尺寸 ,查标准GB/T2855.5-90选取后侧导柱125×25标准模架一副。
8.冲床选用
根据总冲压力 F总=352KN,模具闭合高度,冲床工作台面尺寸等,并结合现有设备,选用J23-63开式双柱可倾冲床,并在工作台面上备制垫块。
其主要工艺参数如下:公称压力:1630KN
滑块行程: 120mm
行程次数: 60 次∕分
最大闭合高度: 140mm
连杆调节长度: 50mm
工作台尺寸(前后×左右): 63*63
9.冲压工艺规程
切料63*25的板料
排样图设计
10.模具总装配图
图 4 模具装配图11.模具零件图
上模座
下模座
凹模
凸模垫板
下模座板
卸料板
卸料螺钉
挡料销
螺钉
导套
凹模垫板
1. 主要模具零件加工工艺过程
落料凹模加工工艺过程
材料 :Gr12 硬度 : 60 ~ 64 HRC
冲孔凸模加工工艺过程
材料: T10A 硬度: 56 ~ 60HRC
凸凹模加工工艺过程
材料 :Gr12 硬度 : 60 ~ 64 HRC
凸模固定板加工工艺过程
材料 :45# 硬度 : 24 ~ 28 HRC
凸凹模固定板加工工艺过程
材料 :45# 硬度 : 24 ~ 28 HRC
卸料板加工工艺过程
材料 :45# 硬度 : 24 ~ 28 HRC
上垫板加工工艺过程
材料 :T8A 硬度 : 54 ~ 58 HRC
下垫板加工工艺过程
材料 :T8A 硬度 : 54 ~ 58 HRC
空心垫板加工工艺过程
材料 :45# 硬度 : 24 ~ 28 HRC
上模座加工工艺过程
材料 :HT200
下模座加工工艺过程
材料: HT200
推件块加工工艺过程
材料 :45# 硬度 : 24 — 28 HRC
2. 加工过程:详见素材资源库中的视频。