基于PLC的液压绞车电气控制系统设计概述
矿用液压绞车电控系统说明书
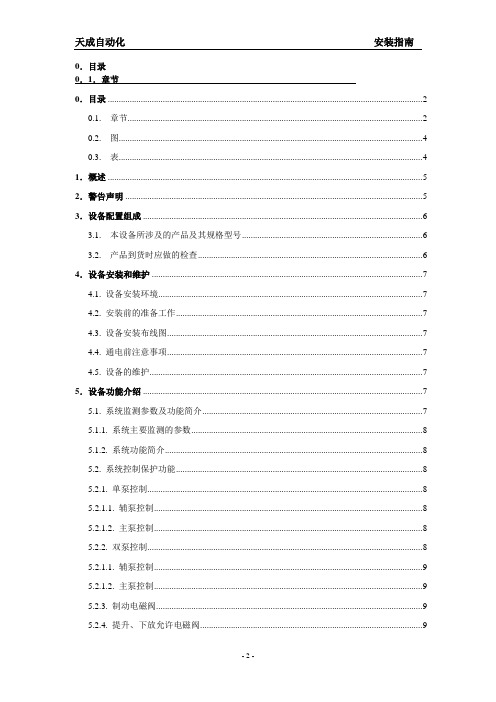
0.目录0.1.章节0.目录 (2)0.1. 章节 (2)0.2. 图 (4)0.3. 表 (4)1.概述 (5)2.警告声明 (5)3.设备配置组成 (6)3.1. 本设备所涉及的产品及其规格型号 (6)3.2. 产品到货时应做的检查 (6)4.设备安装和维护 (7)4.1. 设备安装环境 (7)4.2. 安装前的准备工作 (7)4.3. 设备安装布线图 (7)4.4.通电前注意事项 (7)4.5. 设备的维护 (7)5.设备功能介绍 (7)5.1. 系统监测参数及功能简介 (7)5.1.1. 系统主要监测的参数 (8)5.1.2. 系统功能简介 (8)5.2. 系统控制保护功能 (8)5.2.1. 单泵控制 (8)5.2.1.1. 辅泵控制 (8)5.2.1.2. 主泵控制 (8)5.2.2. 双泵控制 (8)5.2.1.1. 辅泵控制 (9)5.2.1.2. 主泵控制 (9)5.2.3. 制动电磁阀 (9)5.2.4. 提升、下放允许电磁阀 (9)5.2.5. 限速电磁阀 (10)5.2.6. 急停 (10)5.2.7. 后备保护装置 (10)5.3. 系统故障监测及对应的处理方法 (11)5.3.1. “过卷”故障 (11)5.3.2. “机械深度指示失效”故障 (11)5.3.3. “超速”故障 (11)5.3.4. “脚刹”故障 (11)5.3.5. “松绳”故障 (11)5.3.6. “减速区超速”故障 (11)5.3.7. 进入上“减速区”后显示“注意减速” (11)5.3.8.“闸瓦间隙磨损”故障 (11)5.3.9.“补油欠压”故障 (11)5.4. 应急开车 (12)5.5. 系统的初始化校验 (12)5.6. 触摸屏的画面显示功能 (12)5.7. 附加说明 (12)6.矿用绞车操作规程 (14)7.设备常见故障及解决方案 (15)7.1. 屏幕上无速度(或是深度)显示 (15)7.2. 深度显示与实际较大误差 (15)7.3. PLC与触摸屏无法通讯 (15)7.4. 主运行画面上显示机械深度指示失效故障,且频发 (15)7.5. 主、辅电机无法启动 (15)a. 主、辅电机都无法启动 (15)b.辅电机能够启动,但主电机不能启动 (15)c.绞车运行过程中,主电机正常运转,但辅电机突然跳停 (15)7.6. 主运行画面上出现故障无法复位 (16)7.7. 闸瓦磨损故障 (16)7.8. 绞车只能提升不能下放,或只能下放不能提升 (16)7.9. 减速区内不能减速或刚到减速区绞车突然不能运转 (16)7.10. 后备过卷故障 (16)0.2.图图1 电气系统原理图 (17)图2 电气系统接线端子图 (18)图3 现场安装布局框图 (19)图4 操作台与电控箱实物接线图 (20)图5 主辅泵与电控箱实物接线图 (21)图6 电磁阀与电控箱实物接线图 (22)图7 闸瓦间隙保护实物接线图 (23)图8 轴编码器与电控箱实物接线图 (24)图9 过卷保护、减速保护与电控箱实物接线图 (25)图10 松绳保护与电控箱实物接线图 (26)图11 信号与电控箱实物接线图 (27)0.3.表表1 FX2N一般技术指标 (5)表2 PLC电控箱配置清单 (6)表3 液压绞车触摸屏清单 (7)1.概述本套矿用液压绞车电控系统采用日本三菱公司的FX2N系列可编程控制器,此类PLC采用的是一体化结构,其基本单元将所有的电路,含CPU、存储器、输入输出接口及电源等都装在一个模块内,是一个完整的控制装置。
基于PLC的液压机控制系统设计

基于PLC的液压机控制系统设计刘俊,李文(大连交通大学电气信息学院,辽宁大连116028)摘 要:针对传统液压机控制系统的不足,为使其拥有更好的性能和人性化操作界面,构建了基于PLC与工业触摸屏的电气控制系统整体结构,设计采用三菱FX1N PLC作为主控核心,实现的功能分别为与上位机的数据交换,对液压机外围硬件电路以及内部阀体控制和对压力、位移、温度的数据检测。
并给出相应的PLC程序及部分上位机界面设计。
应用结果表明,与传统设计相比,该系统既可以实现自动优化运行,又可以满足手动控制的操作要求,提高了工作效率,是机电一体化的典型应用。
关键词:液压控制;电气控制;可编程逻辑控制器;数据检测;人机界面中图分类号:TH137;TM57 文献标志码:B 文章编号:1671 5276(2011)01 0157 04Control Syste m Design of Hydraulic Press Based on PLCL I U Jun,L IW en(E l e ctrica l and Infor m a tion I nstit u t e,Da lian Jiao t ong Un ive rsity,Da li a n116028,Ch ina)Abstrac t:To m ake up f or t he short age in t he traditional control sys t e m f or hydr auli c pr ess,t his paper constructs t he overall s truc t ure of e l e ctrical contr o l sys t e m based on PL C and indus trial touch screen.I n or der t o m ake t his sys t e m has bett er perf or mance and hu manized operati o n int erf ace,M it sub i s hi FX1N PLC is used as the core t o rea lize its f unction data exchange w ith PC,t he contro l of the peripheral hard w ar e c ircuits and int ernal valves,and t he data de t ec tion i n t he pressure,displace ment and t e mperat ure.And ita lso of f ers the des i g n o f t he corr espond i n g PL C procedure and part o f t he PC int erf ace des ign.Runn i n g result sho w s that co m pared w ith t he trad iti o nal des ign,the syst em not on l y can r eali z e the aut omatic op tm i al oper a ti o n,but also can mee t t he perf or mance require ment s f or manual contr o l and m i prove work effi c iency.This is a typica l appli c ati o n ofmechanical and elec trica l int egrati o n.K ey word s:hydraulic contr o;l e l e ctrical contro;l PL C;dat a det ecti o n;HM I(H u manM achine Int erf ace)0 引言转向架可以说是铁道车辆上最重要的部件之一,它直接承载车体质量,保证车辆顺利通过曲线。
基于PLC的绞车液压控制系统设计
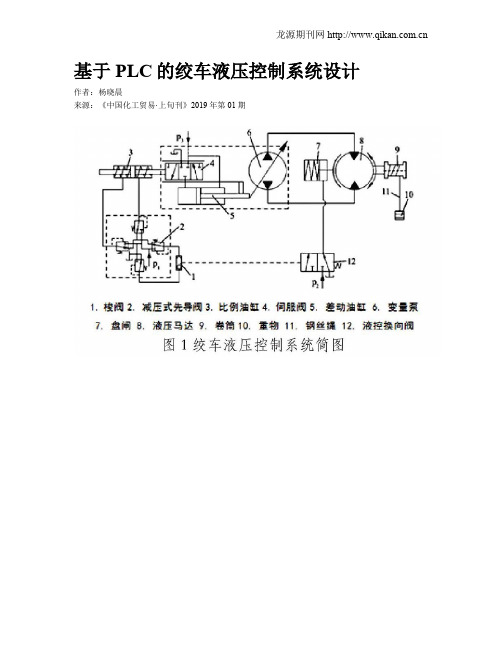
基于PLC的绞车液压控制系统设计作者:杨晓晨来源:《中国化工贸易·上旬刊》2019年第01期摘要:为了增加矿井使用绞车的自动化水平,减少事故发生,在基于PLC基礎上,对绞车控制系统进行了设计,设计的系统能够实现对运行速度、里程精准控制,具有较强的实用价值。
关键词:PLC;绞车;控制系统绞车是矿井井下生产的重要设备,绞车的正常运行对保证矿井高效生产具有重要意义。
目前井下绞车的控制方式主要分为液压控制以及电液控制两种方式。
将液压控制系统与绞车进行配合使用,构建新的运输提升设备,其中最为重要的是,液压控制系统,对保证整个设备的正常运转、调节及保护起着重要作用[l-4]。
文中针对目前液压绞车控制中常见的问题,设计了一种新型液压控制系统,利用PLC控制器来实现对绞车进行控制,从而提升绞车的工作效率,提升绞车运行的稳定。
1液压绞车问题分析1.1速度控制问题现阶段,液压绞车最常用的控制调速方式为容积调速,通过采用改变液压绞车变量泵的角度来实现对绞车运行速度的控制,井下应用最广泛的BYT绞车为例,具体的液压控制系统如图1所示。
当控制系统中的变量泵伺服阀处于中位时,绞车的运行速度保持不变,需要对绞车的运行速度进行调节时,控制手柄,主泵将液压油泵送到油缸内,推动液压活塞上升,提升斜盘的角度,从而实现对绞车速度的控制。
绞车减速过程与调速过程相反。
对绞车运转速度的控制需要采用手动方式进行,这也是整个速度控制的安全隐患,当井下工作人员操控经验不足时容易引起矿井事故发生。
1.2超速保护采用液压绞车对材料进行运输时,随着动力马达运转速度的逐步加大,其最终的运转速度会超过主油泵最大的供给速度,这种情况下,动力马达会改变主油泵的主从控制方式,驱动马达带动主油泵进行运转,电动机转变成为发电反馈模式,产生系统控制力矩,会逐渐的产生超速现象。
若不对超速控制状态下的控制方式进行必要的防护,很容易就会出现超速现象,不对控制系统进行保护,极容易发生安全事故,目前采用的保护装置主要是通过离心力断开连接点,实现液压绞车的紧急制动。
液压系统plc控制实例精解

液压系统plc控制实例精解液压系统是一种重要的动力传动方式,广泛应用于各个领域。
而PLC(Programmable Logic Controller,可编程逻辑控制器)作为一种现代化的控制设备,能够对液压系统进行智能化的控制和管理。
本文将通过一个实例,详细介绍液压系统PLC控制的具体过程和应用。
我们来了解一下液压系统的基本原理。
液压系统通过液体的流动和压力传递来实现力的传递和工作机构的运动控制。
它由液压泵、执行元件、控制元件和液压储能装置等组成。
液压泵将机械能转化为液压能,通过液压管路将液压能传递给执行元件,从而实现工作机构的运动。
而PLC作为控制元件,通过对液压系统的各个部分进行控制和监测,实现对工作机构的精确控制。
接下来,我们以一个自动压力控制系统为例,详细介绍液压系统PLC控制的实现过程。
该系统主要包括液压泵、液压缸、电磁阀和传感器等组成。
其中,液压泵负责提供压力源,液压缸负责执行工作,电磁阀负责控制液压流向,传感器负责监测压力信号。
PLC作为控制中心,通过对传感器信号的采集和处理,以及对电磁阀的控制,实现对液压系统的自动控制。
PLC需要通过输入模块对传感器信号进行采集。
传感器安装在液压缸的压力管路上,能够实时监测液压系统的压力变化。
当压力达到设定的上下限时,传感器会将信号传递给PLC。
PLC通过输入模块接收到传感器信号后,会对信号进行处理和判断,判断液压系统的压力是否需要调整。
然后,PLC会根据预设的控制逻辑和算法进行计算和判断,确定是否需要调整液压系统的工作状态。
当判断需要调整时,PLC会通过输出模块对电磁阀进行控制。
电磁阀负责控制液压系统的流向,通过开启或关闭液压管路,实现对液压缸的运动控制。
当电磁阀被控制为开启状态时,液压泵提供的液压能够进入液压缸,使其产生相应的运动。
当液压系统的压力达到设定值时,传感器会再次将信号传递给PLC。
PLC会根据信号进行判断,如果压力已经达到设定值,则关闭电磁阀,停止液压泵的工作,从而实现对液压系统的自动控制。
液压机械手PLC控制系统的设计

液压机械手PLC控制系统的设计概述本文档旨在介绍液压机械手PLC(可编程逻辑控制)控制系统的设计。
液压机械手是一种常见的工业设备,通过液压系统实现运动控制,而PLC作为控制系统的核心,负责控制信号的处理和输出。
设计要求液压机械手PLC控制系统的设计要满足以下要求:1. 稳定性:系统必须具有高稳定性,以确保机械手的运动精准度和安全性。
2. 功能性:系统需要具备多种功能,如位置控制、速度调节等,以满足不同场景的需求。
3. 可扩展性:系统应具备良好的可扩展性,以便于将来的升级和功能增加。
4. 易维护性:设计应考虑到系统的维护和故障排除,以便于后续维护工作的进行。
硬件设计液压机械手PLC控制系统的硬件设计包括以下方面:1. 选型:选择适合的PLC设备,根据需求选用不同型号和规格的PLC,确保其性能和稳定性。
2. 传感器:选择合适的传感器,如位移传感器、压力传感器等,用于采集机械手运动状态和环境信息。
3. 执行器:选择合适的液压阀、液压泵等执行器,保证系统能够精确控制机械手的各项动作。
4. 电气线路:设计合理的电气线路,确保信号传输的可靠性和稳定性。
软件设计液压机械手PLC控制系统的软件设计包括以下方面:1. PLC程序设计:使用PLC编程软件,根据机械手的运动逻辑和控制要求,编写PLC程序,实现各项功能。
2. 信号处理:对传感器采集的信号进行处理和分析,以获取机械手的状态信息。
3. 控制算法:设计合理的控制算法,根据机械手的控制需求,实现位置控制、速度调节等功能。
4. 用户界面:设计友好的用户界面,方便操作人员对机械手进行参数设置和监控。
系统测试与调试设计完成后,需要进行系统测试与调试,以验证系统的功能和性能:1. 单元测试:对各个模块进行单元测试,确保其功能正常。
2. 组装测试:将各个模块组装成完整的系统,对整个系统进行综合测试。
3. 调试优化:根据测试结果进行系统调试和优化,确保系统的稳定性和性能满足设计要求。
基于PLC的液压闸控制系统

目录前言 (1)1 S7-200PLC可编程控制器简介 (2)1.1概述 (2)1.1.1什么是可编程控制器—PLC (2)1.1.2 PLC发展历程 (2)1.1.3 PLC的发展趋势 (2)1.2 可编程控制器的结构 (3)1.2.1 PLC的基本组成及其相应的作用 (3)1.2.2 PLC的工作原理 (4)1.2.3 PLC的编程语言 (6)1.2.4 S7-200 PLC特点 (6)2.1 闸门概述 (8)2.2 液压系统动态特性简介 (8)2.3 液压系统基本组成 (9)2.3.1 主液压系统 (9)2.3.2 转向液压系统 (9)3 液压闸控制系统硬件设计 (9)3.1 系统硬件 (9)3.1.1 系统总体构造 (10)3.1.2 系统组成 (10)3.1.3 硬件简介 (11)3.2 测量仪器的选择 (12)4 PLC编程设计 (12)4.1 闸门开度设计 (12)4.2 上下水位调节 (13)4.3 PLC的编程 (13)5 总结与展望 (16)5.1 总结 (16)5.2 展望 (17)参考文献 (18)致谢 (19)基于PLC的液压闸控制前言目前在国内污水处理厂和自来水厂,水源均来自外部,经处理后再输送出去,电力则为厂里的动力源。
国内的进厂水源闸门距离水处理厂一般较远,在实际工作中,因外部与内部的水经加工后水质发生了变化,随时都可能发生断电现象。
然而,在断电故障发生情况下,采用手动控制闸门往往不能及时切断进厂水源,尤其是在夜晚,很容易因工作人员疲倦而发生悲剧的现象,造成很大经济损失。
但是,当前国内水处理厂所安装的及时切断进厂水源的设备都是引进国外的设备。
所以,开发液压闸控制系统将有利于保证水处理厂的安全、正常运行,具有很大的意义和经济价值。
同时,我们开发了能及时切断进厂水源的设备,赶上了国际先进水平,证明了我国在先进科技水平上的实力。
当然,这不仅解决了燃眉之急,也对我国的环境,经济也有不可磨灭的长远意义。
基于PLC的液压泵站远程控制系统的设计与实现

4、上位机:选择性能稳定、易于操作的上位机,用于监控和控制配料过程。
参考内容二
引言
液压施工升降机是一种广泛应用于建筑工程的垂直运输设备,其安全性和效率 对于整个工程的进度和成本具有重要影响。为了提高液压施工升降机的安全性 和效率,本次演示将介绍一种基于PLC(可编程逻辑控制器)及触摸屏的液压 施工升降机控制系统设计。
6、易于集成到现有的工业自动化系统中。由于PLC是工业自动化领域广泛使用 的控制器,因此基于PLC的液压泵站远程控制系统可以方便地与其他工业设备 或系统进行集成,从而实现整个工厂或车间的自动化和智能化。
7、系统安全性高。在数据传输过程中采用了加密技术等安全措施,确保数据 的安全性和完整性;同时对操作人员的操作权限进行了严格的控制和管理,避 免了误操作和恶意操作的可能性。
4、系统测试与调试:在完成硬件连接和软件设计后,进行系统测试和调试。 首先,检查硬件连接是否正常,确保传感器和执行器能正确地与PLC进行通讯。 其次,对PLC程序进行在线调试,检查程序逻辑是否正确,并优化程序以改善 控制效果。最后,对触摸屏的操作界面进行测试,确保操作简便、直观。
谢谢观看
二、系统实现
在系统实现方面,首先需要根据实际需求选择合适的PLC控制器和液压泵站设 备,然后进行硬件和软件的配置和设计。
硬件方面,需要将液压泵站的运行状态、压力、流量等信号接入PLC控制器, 同时将PLC控制器通过通讯模块接入互联网,以便远程控制。软件方面,需要 编写PLC控制程序,实现液压泵站的自动控制和远程控制。
此外,还需要开发一套远程控制系统软件,用于发送控制指令和接收设备运行 状态信息。该软件可以采用B/S或C/S架构,支持多种通讯协议,如Modbus、 Profinet等。
基于PLC的液压机控制系统设计

基于PLC的液压机控制系统设计文章主要介绍了液压机系统的工作原理、特点以及研究现状。
从设计角度出发,分析液压系统的工艺流程;根据液压系统的工艺特点设计电气控制系统,分析在电气控制与液压系统的自动、手动控制方式,编写PLC程序,最终由PLC 程序控制液压系统形成一个统一的控制系统整体,达到利用自动化手控制液压系统完成特定的工作行程。
系统通过程序指令控制电路,执行速度快,克服了电磁继电器动作时间长触点抖动的缺点。
并达到所需精度,改善了控制效果,提高了设备的可靠性。
标签:液压传动;PLC控制;液压机1 概述液压传动与控制是以液体作为介质来实现各种机械量的输出(力、位移或速度等)的。
它与单纯的机械传动、电气传动和气压传动相比,其单位重量的输出功率和单位尺寸输出功率大;液压传动装置体积小、结构紧凑、布局灵活,易实现无级调速,调速范围宽,便于与电气控制相配合实现自动化[1,2];易实现过载保护与保压,安全可靠;元件易于实现系列化、标准化、通用化;液压易与微机控制等新技术相结合,构成“机-电-液-光”一体化便于实现数字化[3,4]。
因此,其广泛应用于各种机械设备及精密的自动控制系统,发展速度迅速[5]。
液压机就是该控制理论一个典型应用。
液压机工艺用途广泛,适用于弯曲、翻边、拉伸、成型和冷挤压等冲压工艺,也可适用于校正和压装等工艺。
PLC 以其高可靠性、强抗干扰性、良好的通用性等优点在工业控制的各个领域得到日益广泛的应用[6,7]。
特别是在液压机的液压控制系统中,PLC已得到普遍应用和发展,而且这一趋势仍将继续。
2 工艺流程铝型材液压机是一种把铝或铝合金棒料挤压成各种规格型材的机器液压机工作时,铝棒坯料由加热炉加热到所需挤压温度,然后送至供锭器中,供锭器自动把坯料和挤压垫送至模筒口,由工作缸活塞推模筒直至模口,并在快速推料过程中,供锭器自动复位,同时,挤压筒及模具进行预热,最后,由工作缸进行挤压加工。
在挤压过程中,棒料靠装在挤压筒内的电热元件保持一定的温度挤压结束后,由剪切装置将制品与压余分离,剩料和压垫掉人残料溜槽,压机各部件全部复原,一次挤压加工结束。
- 1、下载文档前请自行甄别文档内容的完整性,平台不提供额外的编辑、内容补充、找答案等附加服务。
- 2、"仅部分预览"的文档,不可在线预览部分如存在完整性等问题,可反馈申请退款(可完整预览的文档不适用该条件!)。
- 3、如文档侵犯您的权益,请联系客服反馈,我们会尽快为您处理(人工客服工作时间:9:00-18:30)。
基于PLC的液压绞车电气控制系统设计概述
摘要随着科学技术发展,液压绞车逻辑编程系统逐渐转换为PLC电气控制系统,新型电气控制系统使液压绞车系统变得更加稳定,精确度较高,能够满足现阶段煤矿安全生产,并提升生产效率,符合煤矿厂家需求,本文针对液压绞车电气控制系统的设计方案进行研究分析。
关键词液压绞车;控制系统;设计
绞车不止应用在煤炭厂家,对于大多数重工业都有涉及,应用较为广泛,能够起到的作用为运输物体以及牵引,并能够根据动力来源将绞车划分为手动和电动以及液压三种工作类型,在煤矿厂工作的绞车主要是液压绞车以及电控绞车,本文主要从液压绞车电气控制系统设计进行研究分析,将系统部件进行改装重组,从而提升工作效率,使绞车工作更具稳定性和安全性以及精确性。
1 液压绞车电气控制系统工作原理
本文设计的液压绞车由于应用于矿山挖煤,所以电机选择防爆型,仪器仪表为安全火花型,这两种系统能够根据不同情况作转换,保障日常工作。
两种系统选择的电机主回路需要660V,主泵电机功率在132kv和160kv,电机型号一般是使用JBO355M-6型以及JBO355S-6型。
主泵电机在使用时还会配备辅助电机,此时会将防爆电动机功率调整为10kW。
若控制主泵起动机型号为DQBH-660/220时,辅助电动机控制防爆电磁铁磁力启动器需要使用QC83-30型号,电源开关为DW80-350型號,所选控制回路为安全火花型。
若防爆液压绞车启动器型是DQBH-660/200时,则将安全火花型作为控制回路,需要将安全火花型回路电阻设定为29,经过试验分析得知,安全火花型控制系统电阻一般都在29以内。
电气控制系统的使用能够使液压绞车使用安全性能进一步提升,尤其是在欠压、超速、过卷、油压开关以及松绳等方面提升较为明显。
并且电气系统在漏电保护工作上做得较好,通过借助变电所方式防止漏电,使生产成本节约。
2 可编程序控制器设计分析
电气控制系统设计一般会采用S7-200小型可编程序控制器。
这种程序控制器能适应整个控制系统,应用较为广泛。
一般STEP7-Micro/WIN32编程软件建立基础为WINDOWS系统的S7-200PLC程序软件。
所以STEP7-Micro/WIN32系统功能较S7-200PLC优势更大,在系统中的作用是开发和程序监控。
STEP7-Micro/WIN32程序模块主要由程序块、数据块、系统块、状图块以及符号表、通信组件等构成。
其中通信组件起到的作用是将PLC和计算机间的消息传递,将PLC所存有的数据、程序等传递给计算机,将计算机中的数据程序等回传给PLC,两者之间的消息传递通过PC/PPI通信电缆完成。
STEP7-Micro/WIN32编程软件功能较多,可以在脱机情况下完成建立、编辑以及修改用户程序等工作,还可以设置PLC参数、工作方式以及程序监控等[1]。
3 绞车控制系统设计-基于PLC控制系统
3.1 系统构架
操作台是系统中人机互动的装置,在结构上主要包括数字显示仪、状态指示灯以及主令开关三个部分。
防爆控制箱中设置可编程控制器、本安电源、继电器以及比例输出放大板等设备。
控制台分为两个界面操作板块,其中斜面板包括LED指示灯以及数字显示表等,能够反映出绞车行驶速度和补油油压以及控制油压等相关数字显示,斜面板最主要的功能便是显示,清晰地将设备运行情况反馈,使操作人员能够清晰了解设备运行情况。
而平面面板则是属于一种指令性面板,指令面板上安装了较多的控制按钮和转换开关等,能够通过自动控制的方式实施指令,或者可以通过检修控制制定和半自动控制指令完成工作。
(1)自动控制指令
若系统设置为自动控制指令时,用户能够通过相对简单的操作,将工作所需信息提取,将开关转换,再按下“启动”按钮后,液压防爆绞车可以自行按照系统指定开展工作,并在完成工作后将制定停止。
并且自动控制指令中有一个“急停”设置,按下按钮后,能够使绞车工作停止,这个设置是为了防止出现意外情况设计的。
系统自动控制设计
①启动
绞车控制台控制开关改变为“自动”模式后,系统会按照要求选择提人或物,经过此番设置好的电气液系统能够进行自动化工作。
其他启动方式在自动指令装置情况下直接启动即可。
②停车
液压绞车系统在运行过程停车条件分为两种,第一是系统不具备开车条件,第二是容器上限。
停车会出现紧急停车问题,这种问题针对特殊原因或故障,控制系统度需要根据系统异常情况,通过人为按下“急停”按钮将绞车停止,故障原因一般是绞车超速、卷筒过卷、主泵电机、辅助电机断电。
(2)半自动控制指令
半自动控制制定所具有的功能与自动控制制定基本一致,启动过程完全一致,两者所存在的差异部分是停车过程。
绞车在采用半自动控制指令后,操作人
员能够给根据指示按下停止按钮帮助绞车停止,若绞车停车时间过长,可以将主泵电机以及辅助电机关闭。
系统半自动控制设计
①启动
系统在运行时启动半自动控制系统,绞车在工作前会对将控制开关调整掉“半自动”位置,工作人员可以按照工作所需对系统提人或提物进行设定,设定完毕后系统具备半自动控制工作条件。
操作员在工作过程中只要按下“开闸”和“启动”按钮便可以开展工作。
②停车
若操作员看到减速提示灯闪烁时,可以按下“停止”按钮使绞车停止,操作台斜面板显示合闸后,工作人员将“闸关”按下,使工作平稳结束。
紧急停车情况与自动控制过程一致[2]。
4 结束语
液压绞车在我国重工业使用较多,但是总体发展较发达国家相比较慢,液压绞车系统构架较为复杂,若使用不当会使工作受到影响,也可能导致部件损坏,维修较为缓慢,只能依靠人工,通过上述电气控制通分析能够发现PLC电控系统运用于液压绞车系统上能大幅提高系统稳定性,便于维修,适合工厂生产使用值得大范围推广。
参考文献
[1] 李明.一种液压绞车电气控制系统的设计[J].煤炭技术,2013,32(03):62-64.
[2] 丁玉圣. 液压防爆绞车电气控制系统的研究[D].济南:山东科技大学,2014.。