简单液压系统设计实例
液压系统设计计算实例

12.13,液压缸的工况图如图12.8所示。
➢ 设计内容与方法
4.拟定液压系统原理图
➢ 设计内容与方法 5.液压元件选择
(1)选择液压泵 ①液压泵最高工作压力 管路总压力损失ΣΔp初步按
0.6MPa估算,有Pp≥pmax+ΣΔp=(4.5+0.6)MPa=5.1MPa ②液压泵最大供油量 取K=1.1,有
➢ 设计内容与方法
3.液压缸参数确定
(5) 采最用低无稳杆定腔速进度油验,算单向最行低程速调度速为阀工调进速时,vm查in=得5最0m小m稳/m定in流,量工进时,
qmin=0.1×10-3m3/min,则
A1≥ qmin 0.1106
vm in
ቤተ መጻሕፍቲ ባይዱ
50
mm2=2 000mm2 满足最低速度要求。
(6) 绘制液压缸工况图 计算各工况下的压力、流量和功率汇总于表
液压与气动控制
F 33667 p 4.5106
4A 4 7482106
3.14
➢ 设计内容与方法
3.液压缸参数确定
( (12) )选 确4 定 定工 液作 压4压 缸力 有效p 工根作据面表积1A2.3和表12.4,初选工作压力p=4.5MPa。
4
4
A= 4 m24=7 482×10-6m2
(3)确定缸筒内径D、活塞杆直径d
➢ 设计内容与方法 5.液压元件选择
①油管 初步选取v=4m/s,则d=m=14.5×103m=14.5mm 查手册确定采用φ18×1.5的紫铜管。 ②滤油器 采用XU-J40×80型过滤器。 ③油箱容积的确定 V=(5~7)qP=(5~7)×20L=(100~140)L
➢ 设计内容与方法
液压系统设计计算实例
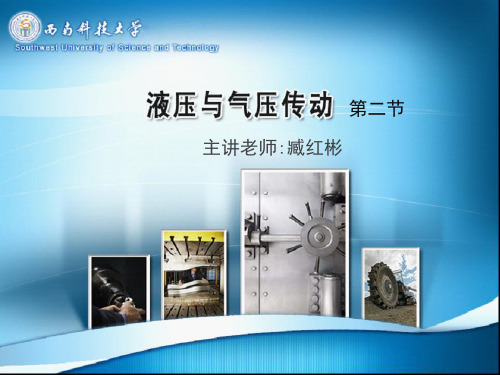
A1=F/(p1-0.5p2)=35511/(4×106-0.5×0.6×106)cm2 ≈96cm2
液压缸内径D就为:D= 4 A= 1 4 ×=9161.06cm
对D圆整,取D=110mm。由dp=0.707Dp,经圆整得 d=80mm。计算出液压缸的有效工作面积A1=95cm2, A2=44.77 cm2。 工进时采用调速阀调速,其最小稳定流量
则液压泵输出压力为2.05MPa。液压泵的总效率ηp=0.8,液压泵流量 40L/min,则液压泵驱动调集所需的功率为:
P=ppqp/ηp=2.05×106×40×10-3W=1708W 据此选用Y112M—6—B5立式电动机,其额定功率为2.2kW,转速为 940r/min,液压泵输出流量为33.84L/min、5.33L/min,仍能满足系统要求 。
1.负载分析与速度分析
1)负载分析
由工作负载Fw =30kN,重力负载FG=0,按启动换向时间和 运动部件重量(F·t=m(v2–v1))计算得到惯性负载Fa=1000N,摩擦 阻力Ff=1960N。
取液压缸机械效率ηm =0.9,则液压缸工作阶段的负载值见表 。
2)速度分析
由快进、快退速度为6m/min,工进速度范围为 20mm/min~120mm/min按上述分析可绘制出负载循环图和速度循环 图(略)。
2.确定参数
1)初选液压缸的工作压力
由最大负载值查教材中表9-3,取液压缸工作压力为4MPa。
2)计算液压缸结构参数
为使液压缸快进与快退速度相等,选用单出杆活塞缸差动连接的方 式实现快进,设液压缸两有效面积为A1和A2,且A1=2 A2,即 d=0.707D。为防止钻通时发生前冲现象,液压缸回油腔背压p2取 0.6MPa,而液压缸快退时背压取0.5MPa。
液压课程设计-卧式钻、镗组合机床液压系统

设计一台卧式钻、镗组合机床液压系统1.液压系统用途(包括工作环境和工作条件)及主要参数:1)工作循环:“快进—工进—死挡铁停留—快退—原位停止”。
组合机床动力滑台工作循环2)工作参数轴向切削力12000N,移动部件总重10000N,工作循环为:“快进——工进——死挡铁停留——决退——原位停止”。
行程长度为0.4m,工进行程为0.1,快进和快退速度为0.1m/s,工过速度范围为0.0003~0.005,采用平导轨,启动时间为0.2s。
要求动力部件可以手动调整,快进转工进平稳、可靠。
2.执行元件类型:液压油缸设计内容1. 拟订液压系统原理图;2. 选择系统所选用的液压元件及辅件;3. 验算液压系统性能;4. 编写计算说明书。
目录序言: (5)1 设计的技术要求和设计参数 (6)2 工况分析 (6)2.1确定执行元件 (6)2.2分析系统工况 (6)2.3负载循环图和速度循环图的绘制 (8)2.4确定系统主要参数2.4.1初选液压缸工作压力 (9)2.4.2确定液压缸主要尺寸 (9)2.4.3计算最大流量需求 (11)2.5拟定液压系统原理图2.5.1速度控制回路的选择 (12)2.5.2换向和速度换接回路的选择 (12)2.5.3油源的选择和能耗控制 (13)2.5.4压力控制回路的选择 (14)2.6液压元件的选择2.6.1确定液压泵和电机规格 (16)2.6.2阀类元件和辅助元件的选择 (17)2.6.3油管的选择 (19)2.6.4油箱的设计 (20)2.7液压系统性能的验算2.7.1回路压力损失验算 (22)2.7.2油液温升验算 (22)序言作为一种高效率的专用机床,组合机床在大批、大量机械加工生产中应用广泛。
本次课程设计将以组合机床动力滑台液压系统设计为例,介绍该组合机床液压系统的设计方法和设计步骤,其中包括组合机床动力滑台液压系统的工况分析、主要参数确定、液压系统原理图的拟定、液压元件的选择以及系统性能验算等。
小型液压机的液压系统课程设计

小型液压机的液压系统课程设计攀枝花学院学生课程设计(论文)题目:小型液压机的液压系统学生姓名: vvvvvv 学号:vvvvvvvv 所在院(系):机械工程学院专业:班级:指导教师:vvvvvv 职称:vvvv2014 年06 月15 日攀枝花学院教务处制课程设计(论文)指导教师成绩评定表攀枝花学院本科学生课程设计任务书目录前言 (10)一设计题目 (11)二技术参数和设计要求 (11)三工况分析 (11)四拟定液压系统原理 (12)1.确定供油方式 (12)2.调速方式的选择 (12)3.液压系统的计算和选择液压元件 (13)4.液压阀的选择 (15)5.确定管道尺寸 (15)6.液压油箱容积的确定 (16)7.液压缸的壁厚和外径的计算 (16)8.液压缸工作行程的确定 (16)9.缸盖厚度的确定 (16)10.最小寻向长度的确定 (16)11.缸体长度的确定 (17)五液压系统的验算 (18)1 压力损失的验算 (18)2 系统温升的验算 (20)3 螺栓校核 (21)总结 (22)参考文献 ................................................................................................... 错误!未定义书签。
前言液压传动是以流体作为工作介质对能量进行传动和控制的一种传动形式。
利用有压的液体经由一些机件控制之后来传递运动和动力。
相对于电力拖动和机械传动而言,液压传动具有输出力大,重量轻,惯性小,调速方便以及易于控制等优点,因而广泛应用于工程机械,建筑机械和机床等设备上。
作为现代机械设备实现传动与控制的重要技术手段,液压技术在国民经济各领域得到了广泛的应用。
与其他传动控制技术相比,液压技术具有能量密度高﹑配置灵活方便﹑调速范围大﹑工作平稳且快速性好﹑易于控制并过载保护﹑易于实现自动化和机电液一体化整合﹑系统设计制造和使用维护方便等多种显著的技术优势,因而使其成为现代机械工程的基本技术构成和现代控制工程的基本技术要素。
液压系统设计计算与应用实例

自动化焊接设备中液压驱动方案设计
焊接机器人
采用液压驱动可实现高精 度、高速度的焊接作业, 提高生产效率和焊接质量。
焊接变位机
通过液压缸和马达的驱动, 实现工件的快速翻转和精 确定位,方便焊接操作。
焊接夹具
利用液压缸的夹紧力,保 证工件在焊接过程中的稳 定性和精度。
总装线上举升、翻转机构实现方式
举升机构
环保型液压油
使用生物可降解液压油,减少 对环境的影响和污染。
能量回收技术
利用液压蓄能器等元件回收系 统中的能量,提高能量利用率 。
智能化节能控制系统
通过传感器和控制系统实时监 测和调整液压系统的运行状态
,实现智能化节能控制。
06 故障诊断与维护保养策略
常见故障类型及诊断方法
液压泵故障
检查泵的运转声音、温度和输出压力,判断 是否需要更换或维修。
定期清洗液压油箱和滤网,保持油液的清 洁度。
检查液压泵和马达
校验压力和流量
定期检查液压泵和马达的运转情况,及时 发现并处理异常。
定期校验系统的压力和流量,确保系统工作 正常。
应急处理措施和备件库存管理建议
应急处理措施
制定针对不同故障的应急处理预案, 包括临时替代方案、现场快速维修方 法等。
备件库存管理建议
液压油缸故障
检查油缸的密封件是否损坏,活塞杆是否弯 曲或磨损。
液压阀故障
观察阀的工作状态和油液流动情况,检查阀 芯是否卡滞或磨损。
液压管路故障
检查管路的连接是否松动或泄漏,判断是否 需要更换或紧固。
预防性维护保养计划制定
定期更换液压油
清洗液压油箱和滤网
根据设备使用情况和厂家建议,制定合理 的液压油更换周期。
液压系统设计计算实例

液压系统设计计算实例——250克塑料注射祝液压系统设计计算大型塑料注射机目前都是全液压控制。
其基本工作原理是:粒状塑料通过料斗进入螺旋推进器中,螺杆转动,将料向前推进,同时,因螺杆外装有电加热器,而将料熔化成粘液状态,在此之前,合模机构已将模具闭合,当物料在螺旋推进器前端形成一定压力时,注射机构开始将液状料高压快速注射到模具型腔之中,经一定时间的保压冷却后,开模将成型的塑科制品顶出,便完成了一个动作循环。
现以250克塑料注射机为例,进行液压系统设计计算。
塑料注射机的工作循环为:合模→注射→保压→冷却→开模→顶出│→螺杆预塑进料其中合模的动作又分为:快速合模、慢速合模、锁模。
锁模的时间较长,直到开模前这段时间都是锁模阶段。
1.250克塑料注射机液压系统设计要求及有关设计参数1.1对液压系统的要求⑴合模运动要平稳,两片模具闭合时不应有冲击;⑵当模具闭合后,合模机构应保持闭合压力,防止注射时将模具冲开。
注射后,注射机构应保持注射压力,使塑料充满型腔;⑶预塑进料时,螺杆转动,料被推到螺杆前端,这时,螺杆同注射机构一起向后退,为使螺杆前端的塑料有一定的密度,注射机构必需有一定的后退阻力;⑷为保证安全生产,系统应设有安全联锁装置。
1.2液压系统设计参数250克塑料注射机液压系统设计参数如下:螺杆直径40mm 螺杆行程200mm最大注射压力153MPa 螺杆驱动功率5kW螺杆转速60r/min 注射座行程230mm注射座最大推力27kN 最大合模力(锁模力) 900kN开模力49kN 动模板最大行程350mm快速闭模速度0.1m/s 慢速闭模速度0.02m/s快速开模速度0.13m/s 慢速开模速度0.03m/s注射速度0.07m/s 注射座前进速度0.06m/s注射座后移速度0.08m/s2.液压执行元件载荷力和载荷转矩计算2.1各液压缸的载荷力计算⑴合模缸的载荷力合模缸在模具闭合过程中是轻载,其外载荷主要是动模及其连动部件的起动惯性力和导轨的摩擦力。
液压与气压传动液压系统设计实例
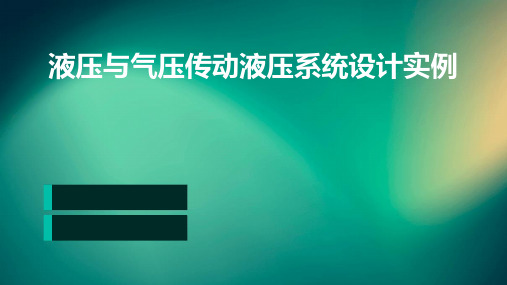
根据系统的工作环境和要求,选择合适的液压介质,如矿 物油、合成油、水等,并确定其清洁度和粘度等参数。
选择合适元件和连接方式
01
选择液压泵和液压马达
根据系统的负载和运动参数,选择合适的液压泵和液压马达,确保其能
够提供足够的流量和压力,并满足系统的效率和精度要求。
02
选择液压缸和阀门
其他常见问题及相应解决方案
气穴现象
产生原因是油液中溶解的气体在低压区析出并形成气泡。解决方案 是减小吸油管路的阻力,避免产生局部低压区。
压力冲击
产生原因是液压阀突然关闭或换向,导致系统内压力急剧变化。解 决方案是在液压阀前设置蓄能器或缓冲装置,吸收压力冲击。
爬行现象
产生原因是液压缸或马达摩擦阻力不均、油液污染等。解决方案是改 善液压缸或马达的润滑条件,使用干净的油液。
关键技术应用
节能环保措施
采用负载敏感技术、电液比例控制技术等 ,提高挖掘机液压系统的控制精度和响应 速度。
通过优化系统设计和选用高效节能元件,降 低挖掘机液压系统的能耗和排放,提高环保 性能。
压力机液压系统性能评估方法论述
评估方法介绍
采用实验测试、仿真分析等方法对压力机 液压系统进行性能评估,获取系统在不同
明确系统的设计目标和约束条件
根据实际需求,明确系统的设计目标,如高效率、 低能耗、高精度等,并考虑成本、空间、重量等 约束条件。
确定系统方案和布局
制定系统原理图
根据设计要求和目标,制定液压系统的原理图,包括液压 缸、液压马达、液压泵、油箱、阀门等元件的连接方式和 控制逻辑。
确定系统布局和安装方式
根据机械设备的结构和空间要求,确定液压系统的布局和 安装方式,包括元件的布置、管路的走向和固定方式等。
液压课程设计--设计一台卧式钻孔组合机床的液压系统

目录0.摘要 (1)1.设计要求 (2)2.负载与运动分析 (2)2.1负载分析 (2)2.2快进、工进和快退时间 (3)2.3液压缸F-t图与v-t图 (3)3.确定液压系统主要参数 (4)3.1初选液压缸工作压力 (4)3.2计算液压缸主要尺寸 (4)3.3绘制液压缸工况图 (5)4.拟定液压系统的工作原理图 (7)4.1拟定液压系统原理图 (7)4.2原理图分析 (8)5.计算和选择液压件 (8)5.1液压泵及其驱动电动机 (8)5.2阀类元件及辅助元件的选 (10)6.液压系统的性能验算 (10)6.1系统压力损失验算 (10)6.2系统发热与温升验算 (11)7.课设总结 (12)0.摘要液压传动技术是机械设备中发展最快的技术之一,特别是近年来与微电子、计算技术结合,使液压技术进入了一个新的发展阶段,机、电、液、气一体是当今机械设备的发展方向。
在数控加工的机械设备中已经广泛引用液压技术。
作为机械制造专业的学生初步学会液压系统的设计,熟悉分析液压系统的工作原理的方法,掌握液压元件的作用与选型是十分必要的。
液压传动在国民经济的各个部门都得到了广泛的应用,但是各部门采用液压传动的出发点不尽相同:例如,工程机械、压力机械采用液压传动的主要原因是取其结构简单、输出力大;航空工业采用液压传动的主要原因取其重量轻、体积小;机床上采用液压传动的主要原因则是取其在工作过程中能无级变速,易于实现自动化,能实现换向频繁的往复运动等优点。
关键词:钻孔组合机床卧式动力滑台液压系统1.设计要求设计一台卧式钻孔组合机床的液压系统,要求完成如下工作循环式:快进→工进→快退→停止。
机床的切削力为25000N ,工作部件的重量为9800N ,快进与快退速度均为7m/min ,工进速度为0.05m/min ,快进行程为150mm ,工进行程40mm ,加速、减速时间要求不大于0.2s ,动力平台采用平导轨,静摩擦系数为0.2,动摩擦系数为0.1 。
- 1、下载文档前请自行甄别文档内容的完整性,平台不提供额外的编辑、内容补充、找答案等附加服务。
- 2、"仅部分预览"的文档,不可在线预览部分如存在完整性等问题,可反馈申请退款(可完整预览的文档不适用该条件!)。
- 3、如文档侵犯您的权益,请联系客服反馈,我们会尽快为您处理(人工客服工作时间:9:00-18:30)。
怎样阅读液压系统原理图 组合机床液压系统 液压系统中的干涉防止
怎样阅读液压系统原理图
了解机械或设备的功能、工况、特殊要求、工作环境等系统信息
了解设备哪些功能的运动是由哪种液压执行元件(或元件组)来实现 的,这些运动对力、速度和位置的定性(变化范围、精度等)和定量 要求
在了解泵源的组成与特点的基础上。将系统划分成以实现各功能运动 的执行元件(元件组)为核心的若干功能分系统
两腔压力比较大,而液控单向阀
的面积比小于液压缸两腔面积
比时便无法使液控单向阀打开
解决:在选用这种回路时要对
液控单向阀的控制压力进行校
核或选用先导式液控单向阀
精品课件文档,欢迎下载,下 载后可以复制编辑。
更多精品文档,欢迎浏览。
高速电主轴在卧式镗铣床上的应用 越来越 多,除 了主轴 速度和 精度大 幅提高 外,还 简化了 主轴箱 内部结 构,缩 短了制 造周期 ,尤其 是能进 行高速 切削, 电主轴 转速最 高可大10000r/min以 上。不 足之处 在于功 率受到 限制, 其制造 成本较 高,尤 其是不 能进行 深孔加 工。而 镗杆伸 缩式结 构其速 度有限 ,精度 虽不如 电主轴 结构, 但可进 行深孔 加工, 且功率 大,可 进行满 负荷加 工,效 率高, 是电主 轴无法 比拟的 。因此 ,两种 结构并 存,工 艺性能 各异, 却给用 户提供 了更多 的选择 。
现在,又开发了一种可更换式主轴 系统, 具有一 机两用 的功效 ,用户 根据不 同的加 工对象 选择使 用,即 电主轴 和镗杆 可相互 更换使 用。这 种结构 兼顾了 两种结 构的不 足,还 大大降 低了成 本。是 当今卧 式镗铣 床的一 大创举 。电主 轴的优 点在于 高速切 削和快 速进给 ,大大 提高了 机床的 精度和 效率。
夹紧回路与主回路之间的干涉
问题:1为夹紧缸,在其 夹紧后系统压力升高而使 4打开。若此时3瞬时切换 会引起1瞬时失压而工件 松夹和事故
原因:顺序阀在打开状态 时,进出口压力几乎相等, 由于换向阀的瞬时切换而 使顺序阀阀芯瞬时不平衡
解决:在顺序阀与换向阀 5之间加一个单向阀
2
1
3
5
4
多级压力调压回路
当今,落地式铣镗床发展的最大特点是 向高速 铣削发 展,均 为滑枕 式(无 镗轴)结 构,并 配备各 种不同 工艺性 能的铣 头附件 。该结 构的优 点是滑 枕的截 面大, 刚性好 ,行程 长,移 动速度 快,便 于安装 各种功 能附件 ,主要 是高速 镗、铣 头、两 坐标
双摆角铣头等,将落地铣镗床的工艺 性能及 加工范 围达到 极致, 大大提 高了加 工速度 与效率 。
组合机床液压系统
组合机床概述 YJ4564动力滑台液压系统 YT4543动力滑台液压系统
YJ4564动力滑台液压系统 工作原理和特点
工作原理
1DT
2DT
行程阀
快进
-
+
+
工进
-
+
-
快退
+
-
-
停止
-
-
-
特点:
采用限压式变量叶片泵加进油路调速阀的联合调速 调速平稳性好、速度换接平缓精度高,系统效率高,适用于功率较
传统的铣削是通过镗杆进行加工, 而现代 铣削加 工,多 由各种 功能附 件通过 滑枕完 成,已 有替代 传统加 工的趋 势,其 优点不 仅是铣 削的速 度、效 率高, 更主要 是可进 行多面 体和曲 面的加 工,这 是传统 加工方 法无法 完成的 。因此 ,现在 ,很多 厂家都 竞相开 发生产 滑枕式 (无镗 轴)高速 加工中 心,在 于它的 经济性 ,技术 优势很 明显, 还能大 大提高 机床的 工艺水 平和工 艺范围 。同时 ,又提 高了加 工精度 和加工 效率。 当然, 需要各 种不同 型式的 高精密 铣头附 件作技 术保障 ,对其 要求也 很高。
问题:在换向阀向中位切换的动态过程中,由于阀的结构原因可 能造成无任何油路处于接通状态而使液压泵发生超压
解决:使让一只溢流阀直接与液压泵的出口相连
B A
用液控单向阀的锁紧回路
问题:若液压缸两腔的面积比较
A1 A1:A2=6
大时,当换向阀切换至右位时发
生液控单向阀无法打开
A2
原因:在液控单向阀未打开时,
用电液换向阀的换向回路 夹紧回路与主回路之间的干涉 多级压力调压回路 用液控单向阀的锁紧回路
用电液换向阀的换向回路
问题:电液换向阀失控现象 原因:当电液换向阀处于中
位时,液压泵卸荷而使先导 换向控制油路失压,因此先 导电磁换向阀切换后不能推 动主阀芯,使电液换向阀失 控 解决:在系统的回油路上加 入一背压阀
工艺特点
高速铣削给落地式铣镗床带来了结构 上的变 化,主 轴箱居 中的结 构较为 普遍, 其刚性 高,适 合高速 运行。 滑枕驱 动结构 采用线 性导轨 ,直线 电机驱 动,这 种结构 是高速 切削所 必需的 ,国外 厂家在 落地式 铣镗床 上都已 采用, 国内同 类产品 还不
多见,仅在中小规格机床上采用线性 导轨。 高速加 工还对 环境、 安全提 出了更 高的要 求,这 又产生 了宜人 化生产 的概念 ,各厂 家都非 常重视 机床高 速运行 状态下 ,对人 的安全 保护与 可操作 性,将 操作台 、立柱 实行全 封闭式 结构, 既安全 又美观 。
大的组合机床
YT4543动力滑台液压系统
YT4543动力滑台液压系统 工作原理
1YA
2YA
3YA 行程阀
DP
快进
&工进
+
-
-
+
-
二工进
+
-
+
+
-
止挡块停
+
-
+
+
+
留
快退
-
+
-
+-
-
原位停止
-
-
-
-
-
YT4543动力滑台液压系统 组成
容积节流调速回路:限压式变量叶片泵+进
油路节流调速+背压阀
快速运动回路:差动连接 换向回路:电液阀 快速运动和工作进给的换接回路:行程阀、
液控顺序阀
两种工作进给的换接回路:两个调速阀
YT4543动力滑台液压系统 特点
调速范围大,低速稳定性好 充分利用能源,系统效率高 快、慢速度的换接平稳,换接的位置精
度较高 换向平稳,启动时冲击小
液压系统中的干涉防止
对每一分系统进行分析,由哪些控制阀组成哪些基本回路,各控制元 件的作用及分系统与泵源的联系。对照电磁铁动作表和相应执行元件 的动作,深入分析与动作对应的油液流动线路及特点
分析系统对各分系统之间动作的顺序、联动、互锁、同步、抗干扰等 方面的要求和实现方法,理解各分系统是如何组成整个系统的
综合归纳以上的分析,总结系统在性能、操作、环境、安全等方面的 要求和特点,达到对系统工作原理和性能的全面清晰的理解
卧式镗铣床运行速度越来越高,快速 移动速 度达
到25~30m/min,镗杆 最高转 速6000r/min。 而卧式 加工中 心的速 度更高 ,快速 移动高 达50m/min, 加速度5m/s2, 位置精 度0.008~0.01m m, 重复定 位精度 0.004~ 0.005mm。
落地式铣镗床铣刀
由于落地式铣镗床以加工大型零件 为主, 铣削工 艺范围 广,尤 其是大 功率、 强力切 削是落 地铣镗 床的一 大加工 优势, 这也是 落地铣 镗床的 传统工 艺概念 。而当 代落地 铣镗床 的技术 发展, 正在改 变传统 的工艺 概念与 加工方 法,高 速加工 的工艺 概念正 在替代 传统的 重切削 概念, 以高速 、高精 、高效 带来加 工工艺 方法的 改变, 从而也 促进了 落地式 铣镗床 结构性 改变和 技术水 平的提 高。