Thin wafer grinding 超薄晶圆减薄
一种超薄晶圆减薄以及背面金属蒸镀的工艺方法[发明专利]
![一种超薄晶圆减薄以及背面金属蒸镀的工艺方法[发明专利]](https://img.taocdn.com/s3/m/badea38cc67da26925c52cc58bd63186bceb921c.png)
(19)中华人民共和国国家知识产权局(12)发明专利申请(10)申请公布号 (43)申请公布日 (21)申请号 202011336926.X(22)申请日 2020.11.25(71)申请人 绍兴同芯成集成电路有限公司地址 312000 浙江省绍兴市越城区银桥路326号(原永和酒业)1幢1楼113室(72)发明人 严立巍 文锺 符德荣 (74)专利代理机构 北京同辉知识产权代理事务所(普通合伙) 11357代理人 张明利(51)Int.Cl.H01L 21/683(2006.01)(54)发明名称一种超薄晶圆减薄以及背面金属蒸镀的工艺方法(57)摘要本发明公开一种超薄晶圆减薄以及背面金属蒸镀的工艺方法,包括环状保护、键合、薄化减厚、浸泡脱离、支撑保护和转移蒸镀。
本发明利用外围外环支撑保护结合亚膜可以制作超薄晶圆的研磨蚀刻工艺,既能避免破片,亦能提高最边缘部份的良率;可以使得晶圆薄片可在不受应力的情况下脱胶并传送转移;使得薄晶圆在外加圆环的支撑保护下转移至金属膜环治具上,可以进行镀金属膜的工艺;环状支撑保护相对于周边厚度较厚的硅片或是玻璃载板的方法,成本较低且不会造成晶圆周边良率的损失。
解决了现有技术中研磨后晶圆外围厚度较厚,将会损失最少3‑5%的良率,且最后必须切除外围才能进行切割工艺,增加生产成本,影响加工效率。
权利要求书1页 说明书4页 附图2页CN 112466807 A 2021.03.09C N 112466807A1.一种超薄晶圆减薄以及背面金属蒸镀的工艺方法,其特征在于,包括如下步骤:S1、环状保护将研磨胶带(2)的侧端环绕贴合有金属环(1),形成环状保护;S2、键合将晶圆(3)背面向上,正面与研磨胶带(2)键合;S3、薄化减厚对晶圆(3)的背面进行蚀刻,减少晶圆(3)的厚度,然后解除应力,继续减少晶圆(3)的厚度;S4、浸泡脱离将晶圆(3)与研磨胶带(2)浸泡至有机溶剂中,溶剂从边缘逐渐渗入晶圆(3)与研磨胶带(2)的键合面,去除黏着力后,研磨胶带(2)应重力在溶剂浸泡中脱离;S5、支撑保护将晶圆(3)转移至金属环(1)上,使得晶圆(3)得到金属环(1)的支撑和保护;S6、转移蒸镀将受到金属环(1)支撑保护的晶圆(3)转移走,在晶圆(3)背面镀上金属膜(4)。
晶圆减薄技术
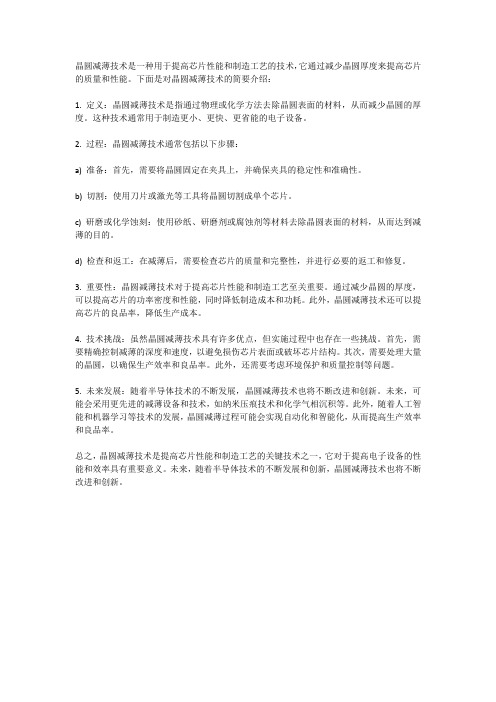
晶圆减薄技术是一种用于提高芯片性能和制造工艺的技术,它通过减少晶圆厚度来提高芯片的质量和性能。
下面是对晶圆减薄技术的简要介绍:1. 定义:晶圆减薄技术是指通过物理或化学方法去除晶圆表面的材料,从而减少晶圆的厚度。
这种技术通常用于制造更小、更快、更省能的电子设备。
2. 过程:晶圆减薄技术通常包括以下步骤:a) 准备:首先,需要将晶圆固定在夹具上,并确保夹具的稳定性和准确性。
b) 切割:使用刀片或激光等工具将晶圆切割成单个芯片。
c) 研磨或化学蚀刻:使用砂纸、研磨剂或腐蚀剂等材料去除晶圆表面的材料,从而达到减薄的目的。
d) 检查和返工:在减薄后,需要检查芯片的质量和完整性,并进行必要的返工和修复。
3. 重要性:晶圆减薄技术对于提高芯片性能和制造工艺至关重要。
通过减少晶圆的厚度,可以提高芯片的功率密度和性能,同时降低制造成本和功耗。
此外,晶圆减薄技术还可以提高芯片的良品率,降低生产成本。
4. 技术挑战:虽然晶圆减薄技术具有许多优点,但实施过程中也存在一些挑战。
首先,需要精确控制减薄的深度和速度,以避免损伤芯片表面或破坏芯片结构。
其次,需要处理大量的晶圆,以确保生产效率和良品率。
此外,还需要考虑环境保护和质量控制等问题。
5. 未来发展:随着半导体技术的不断发展,晶圆减薄技术也将不断改进和创新。
未来,可能会采用更先进的减薄设备和技术,如纳米压痕技术和化学气相沉积等。
此外,随着人工智能和机器学习等技术的发展,晶圆减薄过程可能会实现自动化和智能化,从而提高生产效率和良品率。
总之,晶圆减薄技术是提高芯片性能和制造工艺的关键技术之一,它对于提高电子设备的性能和效率具有重要意义。
未来,随着半导体技术的不断发展和创新,晶圆减薄技术也将不断改进和创新。
晶圆减薄抛光工艺对芯片强度影响的研究

收稿日期:2020-05-09晶圆减薄抛光工艺对芯片强度影响的研究杨生荣1,王海明1,叶乐志2(1.北京中电科电子装备有限公司,北京100176;2.北京工业大学,北京100124)摘要:论述了芯片封装工艺中的减薄、抛光工艺对芯片强度的影响,通过三点弯曲强度测试方法,分析对比减薄工艺以及在减薄后进行化学机械抛光(CMP )和干式抛光(DP )消除应力后芯片强度的分布。
实验表明,晶圆减薄磨削后,对背面磨削面进行去应力抛光,会获得比较高的芯片强度。
关键词:减薄;芯片强度;应力去除;化学机械抛光;干式抛光中图分类号:TN305.2文献标识码:A文章编号:1004-4507(2020)03-0013-04Study on the Influence of Wafer Thinning and PolishingProcess on Chip StrengthYANG Shengrong 1,WANG Haiming 1,YE Lezhi 2(1.CETC Beijing Electronic Equipment Co.,Ltd ,Beijing 100176,China ;2.Beijing University of Technology ,Beijing 100124,China )Abstract:The influence of thinning and polishing process on chip strength in IC packaging process is summarized.By 3-point bending strength test method ,the chip strength distribution after thinning ,CMP(Chemical Mechanical Polishing)and DP (Dry Polishing )stress relief is analyzed and compared.The experiment shows that the chip with high strength can be obtained by stress relief polishing on the back grinding surface after wafer thinning grinding.Key words:Thinning ;Chip strength;Stress relief ;Chemical mechanical polishing (CMP);Dry polishing(DP)随着IC 技术的进步和发展,电子封装需要更薄的芯片来减小封装的体积,并允许多芯片堆叠封装在一个封装体中,这对封装工艺提出了新的挑战。
晶圆减薄研磨工艺
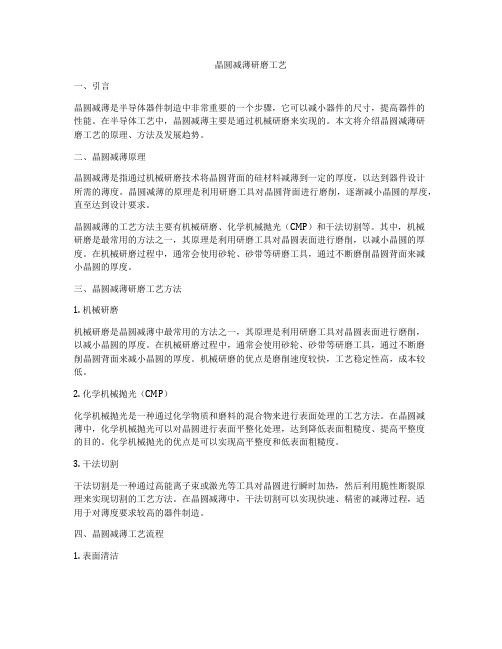
晶圆减薄研磨工艺一、引言晶圆减薄是半导体器件制造中非常重要的一个步骤,它可以减小器件的尺寸,提高器件的性能。
在半导体工艺中,晶圆减薄主要是通过机械研磨来实现的。
本文将介绍晶圆减薄研磨工艺的原理、方法及发展趋势。
二、晶圆减薄原理晶圆减薄是指通过机械研磨技术将晶圆背面的硅材料减薄到一定的厚度,以达到器件设计所需的薄度。
晶圆减薄的原理是利用研磨工具对晶圆背面进行磨削,逐渐减小晶圆的厚度,直至达到设计要求。
晶圆减薄的工艺方法主要有机械研磨、化学机械抛光(CMP)和干法切割等。
其中,机械研磨是最常用的方法之一,其原理是利用研磨工具对晶圆表面进行磨削,以减小晶圆的厚度。
在机械研磨过程中,通常会使用砂轮、砂带等研磨工具,通过不断磨削晶圆背面来减小晶圆的厚度。
三、晶圆减薄研磨工艺方法1. 机械研磨机械研磨是晶圆减薄中最常用的方法之一,其原理是利用研磨工具对晶圆表面进行磨削,以减小晶圆的厚度。
在机械研磨过程中,通常会使用砂轮、砂带等研磨工具,通过不断磨削晶圆背面来减小晶圆的厚度。
机械研磨的优点是磨削速度较快,工艺稳定性高,成本较低。
2. 化学机械抛光(CMP)化学机械抛光是一种通过化学物质和磨料的混合物来进行表面处理的工艺方法。
在晶圆减薄中,化学机械抛光可以对晶圆进行表面平整化处理,达到降低表面粗糙度、提高平整度的目的。
化学机械抛光的优点是可以实现高平整度和低表面粗糙度。
3. 干法切割干法切割是一种通过高能离子束或激光等工具对晶圆进行瞬时加热,然后利用脆性断裂原理来实现切割的工艺方法。
在晶圆减薄中,干法切割可以实现快速、精密的减薄过程,适用于对薄度要求较高的器件制造。
四、晶圆减薄工艺流程1. 表面清洁在进行晶圆减薄之前,首先需要对晶圆表面进行清洁处理,以确保研磨过程中不受到杂质的干扰。
2. 粗磨经过表面清洁处理后,将晶圆放入研磨设备中进行粗磨。
在粗磨过程中,通常会选择适当的研磨工具和磨料,以尽快减小晶圆的厚度。
3. 精磨粗磨完成后,再将晶圆放入研磨设备中进行精磨。
晶圆切割晶圆切割和微加工新技术
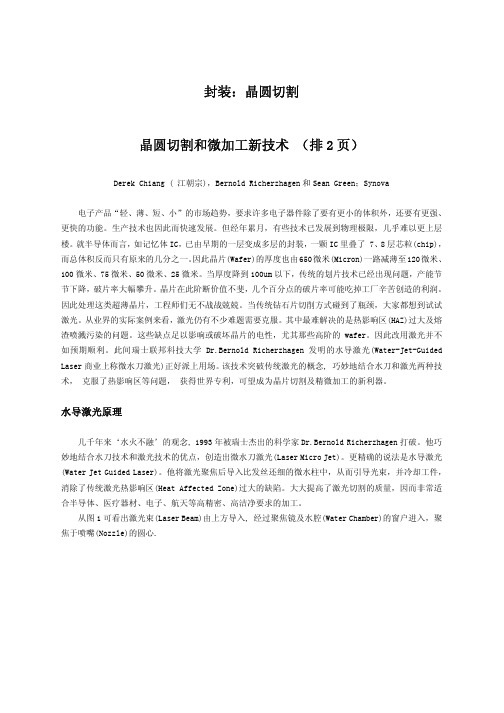
封装:晶圆切割晶圆切割和微加工新技术 (排2页)Derek Chiang ( 江朝宗),Bernold Richerzhagen和Sean Green;Synova电子产品“轻、薄、短、小”的市场趋势,要求许多电子器件除了要有更小的体积外,还要有更强、更快的功能。
生产技术也因此而快速发展。
但经年累月,有些技术已发展到物理极限,几乎难以更上层楼。
就半导体而言,如记忆体IC,已由早期的一层变成多层的封裝,一颗IC里叠了 7、8层芯粒(chip),而总体积反而只有原来的几分之一。
因此晶片(Wafer)的厚度也由650微米(Micron)一路减薄至120微米、100微米、75微米、50微米、25微米。
当厚度降到100um以下,传统的划片技术已经出现问题,产能节节下降,破片率大幅攀升。
晶片在此阶断价值不斐,几个百分点的破片率可能吃掉工厂辛苦创造的利润。
因此处理这类超薄晶片,工程师们无不战战兢兢。
当传统钻石片切削方式碰到了瓶颈,大家都想到试试激光。
从业界的实际案例来看,激光仍有不少难题需要克服。
其中最难解决的是热影响区(HAZ)过大及熔渣喷溅污染的问题。
这些缺点足以影响或破坏晶片的电性,尤其那些高阶的wafer。
因此改用激光并不如预期顺利。
此间瑞士联邦科技大学Dr.Bernold Richerzhagen发明的水导激光(Water-Jet-Guided Laser商业上称微水刀激光)正好派上用场。
该技术突破传统激光的概念, 巧妙地结合水刀和激光两种技术, 克服了热影响区等问题, 获得世界专利,可望成为晶片切割及精微加工的新利器。
水导激光原理几千年来‘水火不融’的观念, 1993年被瑞士杰出的科学家Dr.Bernold Richerzhagen打破。
他巧妙地结合水刀技术和激光技术的优点,创造出微水刀激光(Laser Micro Jet)。
更精确的说法是水导激光(Water Jet Guided Laser)。
半导体封装制程及其设备介绍——【半导体芯片】
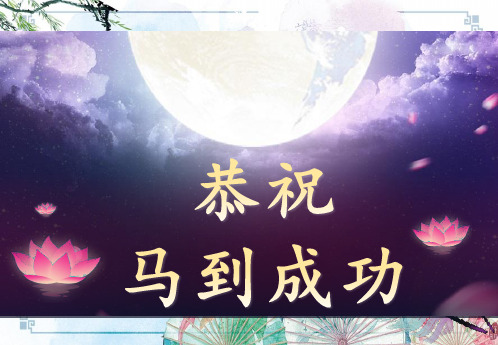
Dual In-line Package
Shape
Typical Features
Material Lead Pitch No of I/O
Ceramic Plastic
2.54 mm (100miles)
8 ~64
SIP
Single In-line Package
Plastic
2.54 mm (100miles) 1 direction
Material Lead Pitch No of I/O
Ceramic
1.27 mm (50miles) j-shape bend 4 direction
lead
18~124
Ceramic
0.5 mm
32~200
SMT (Optional)
Taping (Optional)
Grinding (Optional)
lead
3~25
Through Hole Mount
ZIP
Zigzag In-line Package
S-DIP
Shrink Dual In-line
Package
封裝型式
Shape
Typical Features
Material Lead Pitch No of I/O
Plastic
2.54 mm (100miles) 1 direction
Pack
封裝型式
Shape
Typical Features
Material Lead Pitch No of I/O
Plastic
1.27 mm (50miles) 2 direction
lead
8 ~40
半导体封装制程与设备材料知识简介
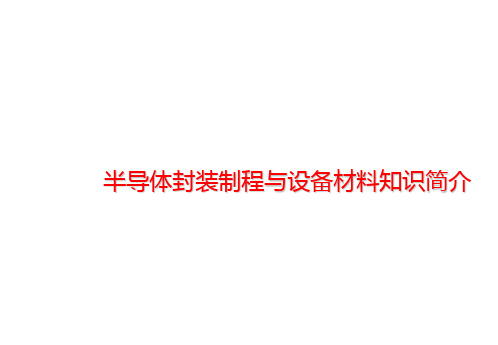
封裝型式
Shape
Typical Features
Materia Lead Pitch No of I/O l
Cerami c
1.27, 0.762 mm
(50, 30miles) 2, 4 direction
lead
20~80
Ceramic
1.27,1.016, 0.762 mm (50, 40, 30
(氧化处理)
Depositio n
(沉积)
WireBondin g
(焊线)
Laser mark (激光印字)
Laser Cut & package saw
(切割成型)
Testin g
(测试)
Lithograp hy
(微影)
Wafer Inspection (晶圆检查) 前段結束
Moldin g
(塑封)
Plastic
1.27 mm (50miles) 2 direction
lead
8 ~40
Plastic
1.0, 0.8, 0.65 mm 4 direction
lead
88~200
Surface Mount
FPG
Flat Package of Glass
LCC
Leadless Chip
Carrier
lead
18~124
Ceramic 0.5 mm
32~200
SMT (Optional)
Taping (Optional)
Assembly Main Process
Grinding (Optional)
Detaping (Optional)
Wafer Mount
晶圆减薄机工作原理
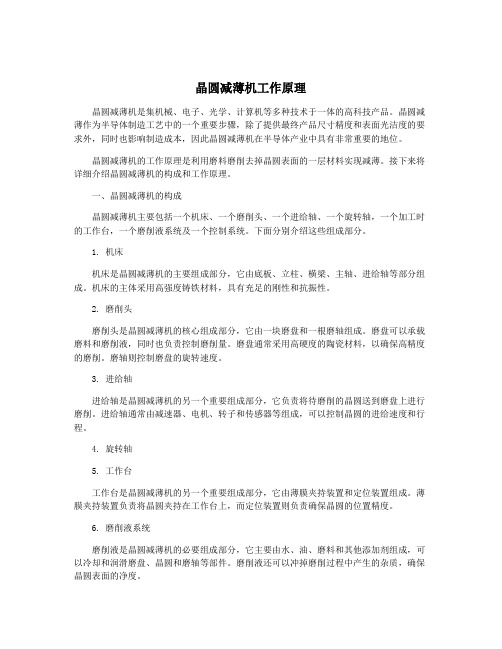
晶圆减薄机工作原理晶圆减薄机是集机械、电子、光学、计算机等多种技术于一体的高科技产品。
晶圆减薄作为半导体制造工艺中的一个重要步骤,除了提供最终产品尺寸精度和表面光洁度的要求外,同时也影响制造成本,因此晶圆减薄机在半导体产业中具有非常重要的地位。
晶圆减薄机的工作原理是利用磨料磨削去掉晶圆表面的一层材料实现减薄。
接下来将详细介绍晶圆减薄机的构成和工作原理。
一、晶圆减薄机的构成晶圆减薄机主要包括一个机床、一个磨削头、一个进给轴、一个旋转轴,一个加工时的工作台,一个磨削液系统及一个控制系统。
下面分别介绍这些组成部分。
1. 机床机床是晶圆减薄机的主要组成部分,它由底板、立柱、横梁、主轴、进给轴等部分组成。
机床的主体采用高强度铸铁材料,具有充足的刚性和抗振性。
2. 磨削头磨削头是晶圆减薄机的核心组成部分,它由一块磨盘和一根磨轴组成。
磨盘可以承载磨料和磨削液,同时也负责控制磨削量。
磨盘通常采用高硬度的陶瓷材料,以确保高精度的磨削。
磨轴则控制磨盘的旋转速度。
3. 进给轴进给轴是晶圆减薄机的另一个重要组成部分,它负责将待磨削的晶圆送到磨盘上进行磨削。
进给轴通常由减速器、电机、转子和传感器等组成,可以控制晶圆的进给速度和行程。
4. 旋转轴5. 工作台工作台是晶圆减薄机的另一个重要组成部分,它由薄膜夹持装置和定位装置组成。
薄膜夹持装置负责将晶圆夹持在工作台上,而定位装置则负责确保晶圆的位置精度。
6. 磨削液系统磨削液是晶圆减薄机的必要组成部分,它主要由水、油、磨料和其他添加剂组成,可以冷却和润滑磨盘、晶圆和磨轴等部件。
磨削液还可以冲掉磨削过程中产生的杂质,确保晶圆表面的净度。
7. 控制系统晶圆减薄机的控制系统负责控制整个机器的运行。
它由一个主控板、外设、传感器和执行器等部分组成。
主控板负责储存和处理代码,控制机器运行;外设可以帮助订单和退出代码;传感器负责检测和反馈磨削过程中的各种参数;执行器则根据控制信号改变机器的运行状态。
- 1、下载文档前请自行甄别文档内容的完整性,平台不提供额外的编辑、内容补充、找答案等附加服务。
- 2、"仅部分预览"的文档,不可在线预览部分如存在完整性等问题,可反馈申请退款(可完整预览的文档不适用该条件!)。
- 3、如文档侵犯您的权益,请联系客服反馈,我们会尽快为您处理(人工客服工作时间:9:00-18:30)。
Flip Chip
Wafer Test
Wafer Mount
Dicing
Die Attach
Wirebond
Encapsulation
Profile of Typical Silicon Wafer
Left side of this wafer was ground.
Grinding Wafers with Bevel
Sam Kao PhD – Tru-Si
Outline
• Introduction • Where does B/G fit in • Why do it • What are some typical problems encountered
• Objective of Presentation • Experimental method
Objective
Evaluate effect of grinding wheel specification on 8” thin wafers for optimum tool selection
> Effectቤተ መጻሕፍቲ ባይዱof grit size and grade ( wheel hardness) on thin wafer
- Wafers were de-taped manually
- Surface finish (Ra, Rt), Wafer Bow and Strength measured
- Chipping was classified as per number and size of chips using a microscope
• Machine used to grind, Wheels used to grind, metrology • equipment,recipe used • Experimental Results 5. Conclusions
Wafer Fabs Work Flow
Wafer Manufacturing
CAD Drawings illustrate the effect of the bevel on grinding thin wafers.
Bevel Full Radius
Thin Wafer with Bevel and Device
1 in
1 in = 200 µm
Device
Close Up of Thin Wafer With Bevel
x = Total Wafer Thickness-Circuitry Thickness y = Function (x)
x
Very Thin
y
0.25 in.
1 in = 200 µm
Thin Wafer Grinding
• Thinner wafers do not have the inherent mass to resist bending stresses due to
• Close up shows that the tip of the thin wafer is very thin. • The thin tip leads to chipping around the edge of the wafer. • The damage propagates around wafer and further into wafer.
> Clean edges : NC (No Chippage at all) > Rough edge with no visible chippage : RE ( Rough Edge) > One chip within 1 x 1 mm : MC (Medium chippage) > More than one chip or one chip bigger than 1 x 1 mm : LC (Large chippage)
Recent Developments in Thin wafer grinding – An Application Review
Thomas Puthanangady, Rama Vedantham, J Ikeda PhD. Saint Gobain Abrasives-Norton
Sal Kassir – Strasbaugh
Grinding Process Demonstration – Equipment used for Tests
Epitaxy
Backgrinding
Back-end
RTP
Ion Implant
Deposition
CMP
SEM Inspect
Spin On
Mask
Etching
Photo
Lithography
Thin Wafer Processing
handling
Back Grind
De Tape
Etch
- Test wheels used to grind 25 nos of 8” wafers each to 125 um thickness on the Strasbaugh 7AF grinder
- The force during grinding, cycle time and the wheel wear rates were monitored.
• Surface stresses • Wafer strength • Surface Roughness characteristics
Final wafer thickness : 125 um
Test Methodoloy
- 8” wafers manually taped using a vacuum chuck
• Gravity • Residual grinding/ machining stresses • This results in Bow and Warp • Creates handling issues and may ultimately result in wafer breakage •This effect is more pronounced in 200mm and larger wafers