螺纹模具设计要点
注塑内螺纹直接脱模结构设计方案

注塑内螺纹直接脱模结构设计方案一、整体思路。
咱们得想个办法,让带有内螺纹的塑料制品在注塑完后,能轻松地从模具里脱模,就像从被窝里钻出来一样容易,而且还不能把这个螺纹给搞坏喽。
二、具体结构设计。
1. 螺纹型芯部分。
首先呢,这个螺纹型芯不能是个死脑筋的结构。
咱们可以把它设计成两段式的。
就像火车有车头和车厢一样。
靠近模具型腔内部的那一段螺纹型芯,咱们可以让它稍微细一点,就像小一号的螺丝。
这一段的螺纹是完整的,用来成型产品的内螺纹。
然后外面再套上一段粗一点的“外套”,这个外套和里面的细螺纹型芯之间要有一定的间隙,这个间隙就像两个好朋友之间保持的小距离,不能太大也不能太小,大概在0.1 0.3毫米左右就行。
这个间隙是为了让里面的细型芯在脱模的时候有活动的空间。
2. 脱模动力装置。
为了让螺纹型芯能从产品里退出来,咱们得给它一个动力呀。
这时候可以在模具上安装一个小型的液压或者气动装置。
想象一下,这个装置就像一个小助手,在脱模的时候轻轻地推一下螺纹型芯。
不过这个推力得控制好,不能太猛,不然会把产品给弄坏的。
一般来说,根据产品的大小和材料的特性,这个推力在50 200牛顿之间比较合适。
另外,还可以在螺纹型芯上连接一个旋转机构。
这个旋转机构就像一个小陀螺,在液压或者气动装置推动螺纹型芯往外退的同时,让它慢慢地旋转。
因为内螺纹嘛,要是光直直地往外退,肯定会卡住的,就像你硬要把拧进去的螺丝直接拔出来一样困难。
这个旋转的速度也不能太快,每分钟大概转个5 10圈就差不多了。
3. 导向和限位结构。
在螺纹型芯的周围,要设置一些导向柱。
这些导向柱就像轨道一样,让螺纹型芯在脱模的时候只能按照规定的方向移动。
就像火车只能在铁轨上跑一样。
导向柱的表面要光滑得像溜冰场一样,这样可以减少摩擦,保证螺纹型芯移动得顺畅。
同时呢,还要有限位装置。
这个限位装置就像一个小警察,告诉螺纹型芯你只能移动到这个位置,不能再往前走了。
这样可以防止螺纹型芯过度脱模,把模具或者产品给损坏了。
模具设计原则和核心以及注意事项
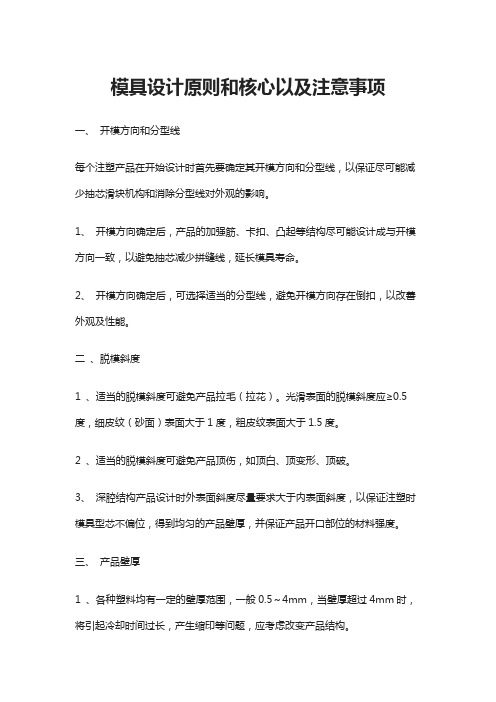
模具设计原则和核心以及注意事项 一、 开模方向和分型线每个注塑产品在开始设计时首先要确定其开模方向和分型线,以保证尽可能减少抽芯滑块机构和消除分型线对外观的影响。
1、 开模方向确定后,产品的加强筋、卡扣、凸起等结构尽可能设计成与开模方向一致,以避免抽芯减少拼缝线,延长模具寿命。
2、 开模方向确定后,可选择适当的分型线,避免开模方向存在倒扣,以改善外观及性能。
二 、脱模斜度1 、适当的脱模斜度可避免产品拉毛(拉花)。
光滑表面的脱模斜度应≥0.5度,细皮纹(砂面)表面大于1度,粗皮纹表面大于1.5度。
2 、适当的脱模斜度可避免产品顶伤,如顶白、顶变形、顶破。
3、 深腔结构产品设计时外表面斜度尽量要求大于内表面斜度,以保证注塑时模具型芯不偏位,得到均匀的产品壁厚,并保证产品开口部位的材料强度。
三、 产品壁厚1 、各种塑料均有一定的壁厚范围,一般0.5~4mm,当壁厚超过4mm时,将引起冷却时间过长,产生缩印等问题,应考虑改变产品结构。
2、壁厚不均会引起表面缩水。
3 、壁厚不均会引起气孔和熔接痕。
四、加强筋1、 加强筋的合理应用,可增加产品刚性,减少变形。
2、 加强筋的厚度必须≤ (0.5~0.7)T产品壁厚,否则引起表面缩水。
3、 加强筋的单面斜度应大于1.5°,以避免顶伤。
五、圆角1、 圆角太小可能引起产品应力集中,导致产品开裂。
2、圆角太小可能引起模具型腔应力集中,导致型腔开裂。
3、 设置合理的圆角,还可以改善模具的加工工艺,如型腔可直接用R刀铣加工,而避免低效率的电加工。
4 、不同的圆角可能会引起分型线的移动,应结合实际情况选择不同的圆角或清角。
六、 孔1 、孔的形状应尽量简单,一般取圆形。
2 、孔的轴向和开模方向一致,可以避免抽芯。
3 、当孔的长径比大于2时,应设置脱模斜度。
此时孔的直径应按小径尺寸(最大实体尺寸)计算。
4 、盲孔的长径比一般不超过4。
防孔针冲弯5 、孔与产品边缘的距离一般大于孔径尺寸。
塑料螺纹瓶盖模具设计
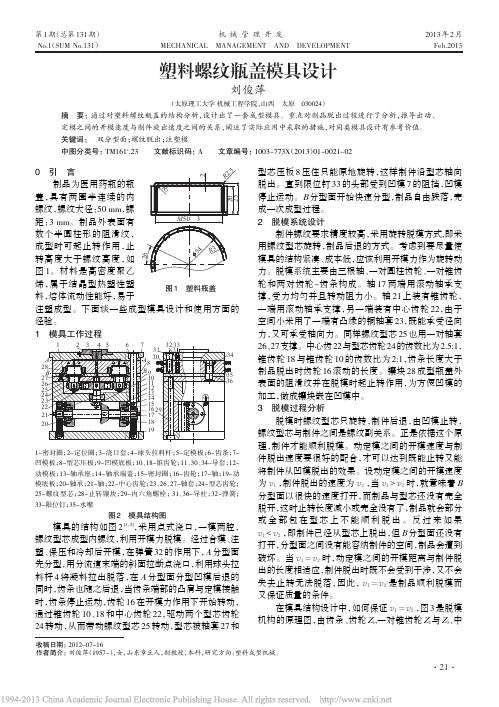
第1期(总第131期)机械管理开发2013年2月No.1(SUM No.131)MECHANICAL MANAGEMENT AND DEVELOPMENT Feb.20130引言制品为医用药瓶的瓶盖,具有两圈半连续的内螺纹,螺纹大径:50mm ,螺距:3mm 。
制品外表面有数个半圆柱形的阻滑纹,成型时可起止转作用,止转高度大于螺纹高度,如图1。
材料是高密度聚乙烯,属于结晶型热塑性塑料,熔体流动性能好,易于注塑成型。
下面谈一些成型模具设计和使用方面的经验。
1模具工作过程1 2 3 4 5 6 78A A B B 92827262524232221201-密封圈;2-定位圈;3-浇口套;4-球头拉料杆;5-定模板;6-齿条;7-凹模板;8-型芯压板;9-凹模底板;10、18-锥齿轮;11、30、34-导套;12-动模板;13-轴承座;14-轴承端盖;15-密封圈;16-齿轮;17-轴;19-动模底板;20-轴承;21-轴;22-中心齿轮;23、26、27-轴套;24-型芯齿轮;25-螺纹型芯;28-止转镶块;29-内六角螺栓;31、36-导柱;32-弹簧;33-限位钉;35-水嘴图2模具结构图模具的结构如图2[1,2],采用点式浇口,一模两腔,螺纹型芯成型内螺纹,利用开模力脱模。
经过合模、注塑、保压和冷却后开模,在弹簧32的作用下,A 分型面先分型,用分流道末端的斜面拉断点浇口,利用球头拉料杆4将凝料拉出脱落,在A 分型面分型凹模后退的同时,齿条也随之后退,当齿条端部的凸肩与定模接触时,齿条停止运动,齿轮16在开模力作用下开始转动,通过锥齿轮10、18和中心齿轮22,驱动两个型芯齿轮24转动,从而带动螺纹型芯25转动,型芯被轴套27和型芯压板8压住只能原地旋转,这样制件沿型芯轴向脱出。
直到限位钉33的头部受到凹模7的阻挡,凹模停止运动。
B 分型面开始快速分型,制品自由跌落,完成一次成型过程。
2脱模系统设计制件螺纹要求精度较高,采用旋转脱模方式,即采用螺纹型芯旋转,制品后退的方式。
17个模具设计注意事项、设计要点

17个模具设计注意事项、设计要点注塑工作常用计算公式(一)一、3D与2D分析1、3D结构的分析。
2、2D图面公差、外观、材质分析。
二、开模方向和分型线每个注塑产品在开始设计时首先要确定其开模方向和分型线,以保证尽可能减少抽芯滑块机构和消除分型线对外观的影响。
1、开模方向确定后,产品的加强筋、卡扣、凸起等结构尽可能设计成与开模方向一致,以避免抽芯减少拼缝线,延长模具寿命。
2、开模方向确定后,可选择适当的分型线,避免开模方向存在倒扣,以改善外观及性能。
三、拔模角度1 、适当的脱模斜度可避免产品拉毛(拉花)。
光滑表面的脱模斜度应≥0.5度,细皮纹(砂面)表面大于2度,粗皮纹表面大于3度。
2 、适当的脱模斜度可避免产品顶伤,如顶白、顶变形、顶破。
3、深腔结构产品设计时外表面斜度尽量要求大于内表面斜度,以保证注塑时模具型芯不偏位,得到均匀的产品壁厚,并保证产品开口部位的材料强度。
4、在进行做拔模的时候,注意2D图面公差尺寸的要求,拔模控制在公差范围以内。
四、产品壁厚1 、各种塑料均有一定的壁厚范围,一般0.5~4mm,当壁厚超过4mm时,将引起冷却时间过长,产生缩印等问题,应考虑改变产品结构。
2 、壁厚不均会引起表面缩水。
3 、壁厚不均会引起气孔和熔接痕。
4、产品壁厚不均匀的情况下,结构上需要做分化,防止表面产品应力痕。
五、加强筋1、加强筋的合理应用,可增加产品刚性,减少变形。
2、加强筋的厚度必须≤ (0.5~0.7)T产品壁厚,否则引起表面缩水。
3、加强筋的单面斜度应大于0.5°,以避免顶伤。
4、正常情况下,为了排气,加强筋在做镶件处理,如果加强筋高度在15MM以上的情况下,在镶件上面加强位,如果能用磨床加工的情况下,可以不做脱模斜度,但模仁一侧的斜度可以做大一点。
六、圆角1、圆角太小可能引起产品应力集中,导致产品开裂。
2、圆角太小可能引起模具型腔应力集中,导致型腔开裂。
3、设置合理的圆角,还可以改善模具的加工工艺,如型腔可直接用R刀铣加工,而避免低效率的电加工。
8塑料制品螺纹结构的设计(精)
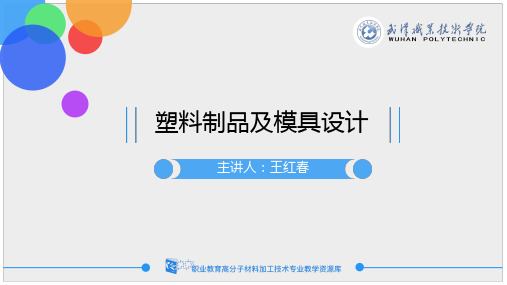
否则模具结构复杂,须采用两次脱模装置,如图2-8-2所示。
THANKS!!!
8
塑料制品螺纹结构的设计
塑料制品螺纹结构的设计要点
(1)塑料螺纹与金属螺纹的配合长度,不应大于螺纹直径的1.5倍。 (2)外螺纹与内螺纹塑件应分别设计成图2-8-1所示的结构,以便于装配并提高螺
牙强度。螺纹始末长度L由表2-8-2选取。
(3)同一塑件上前后两段螺纹,应尽可能使其螺距相等、旋向相同,以便脱模。
X
标 记 与 图 案 的 设 计
Ⅺ
支 承 面 结 构 设 计
目
塑 件 的 尺 寸 及 精 度
tttl
的 设 计
孔 结 构
录
8
塑料制品螺纹结构的设计
塑料制品螺纹结构的加工方法
(1)直接成型 采用螺纹型芯(成型内螺纹)和螺纹型环(成型外螺纹)成型, 成型后使制件与型芯(环)间相对旋转脱出制品。对外螺纹也可采用哈夫模成型。
塑料制品及模具设计 tt
主讲人:王红春
塑料制品设计原则
材料选择、成型方法、模具总体结构
结构合理、造型美观、便于制造
1
2
壁 厚 的 设 计
3
脱 模 斜 度
的 设 计
4
加 强 筋 的 设 计
5 构
的 设 计
8
螺 纹 结 构
的 设 计
9
嵌 件 结 构 的 设 计
对要求不高的软塑料成型的内螺纹,可强制脱螺纹。
(2)机械加工 对生产批量不大的塑件,采用后加工的方法加工螺纹。
(3)采用金属螺纹嵌件 该结构用于经常拆装、精度要求较高和受力较大的场合。
(4)自攻螺纹。
8
塑料制品螺纹结构的设计
冷镦螺栓缩径模具内孔孔型设计
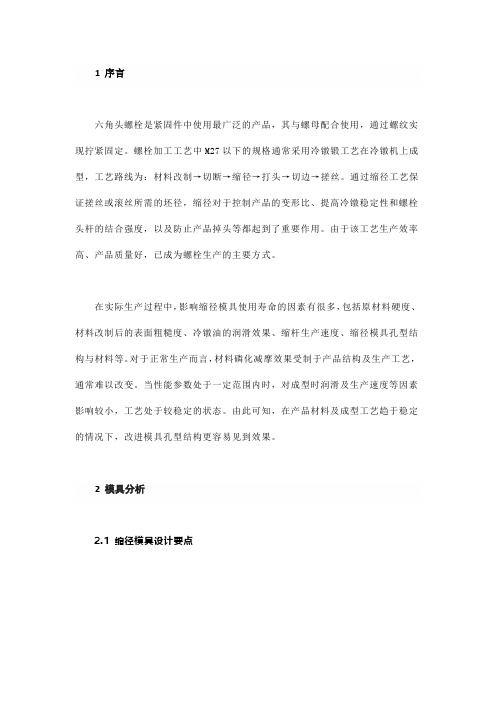
1 序言六角头螺栓是紧固件中使用最广泛的产品,其与螺母配合使用,通过螺纹实现拧紧固定。
螺栓加工工艺中M27以下的规格通常采用冷镦锻工艺在冷镦机上成型,工艺路线为:材料改制→切断→缩径→打头→切边→搓丝。
通过缩径工艺保证搓丝或滚丝所需的坯径,缩径对于控制产品的变形比、提高冷镦稳定性和螺栓头杆的结合强度,以及防止产品掉头等都起到了重要作用。
由于该工艺生产效率高、产品质量好,已成为螺栓生产的主要方式。
在实际生产过程中,影响缩径模具使用寿命的因素有很多,包括原材料硬度、材料改制后的表面粗糙度、冷镦油的润滑效果、缩杆生产速度、缩径模具孔型结构与材料等。
对于正常生产而言,材料磷化减摩效果受制于产品结构及生产工艺,通常难以改变。
当性能参数处于一定范围内时,对成型时润滑及生产速度等因素影响较小,工艺处于较稳定的状态。
由此可知,在产品材料及成型工艺趋于稳定的情况下,改进模具孔型结构更容易见到效果。
2 模具分析2.1 缩径模具设计要点缩径模具采用预应力组合结构,以保证其整体强度;外部模套采用H13碳钢材料,芯部为硬质合金KG5,硬度1250~1340HV模套加热至400℃以上,以过盈配合将模芯压入。
缩径模具孔型结构中最重要的参数是工作带导向角度α和定径带长度L。
工作带导向角度α直接影响缩径力的大小,α过大或过小都会引起缩径力的增加;定径带长度L决定了模具使用寿命的长短,L过长或过短都会降低模具的使用寿命[1]。
定径带后面的孔径与定径带直径之差以0.05~0.07mm为宜,避免工件与模具接触使得摩擦力增加,确保缩径的顺利进行[2]。
2.2 缩径模具孔型结构缩径模具主要结构及参数如图1所示。
工作带是对材料进行挤压缩径的区域,图中α表示工作带导向角度(°);定径带保证缩径后坯料的尺寸精度,d为定径带直径(mm);L为定径带长度(mm)。
图1缩径模具主要结构及参数2.3 缩径变形量ψ缩径变形量为缩径前后线材横截面积的变化,缩径变形程度是缩径工艺设计及计算的重要参数,也是影响缩径模具寿命最重要的因素。
塑件螺纹设计

塑件上的螺纹既可以直接用模具成型,也可以在成型后用机械加工方法成型。
对于需要经常拆装和受力较大的螺纹,应采用金属螺纹嵌件。
塑件上的螺纹一般应选用较大的螺牙尺寸,直径较小时也不宜选用细牙螺纹,否则会影响使用强度。
表3-8列出了塑件螺纹的选用范围。
表1 塑件螺纹的选用范围
螺纹公称直径/mm
螺纹种类
公称标准螺纹1级细牙螺纹2级细牙螺纹3级细牙螺纹4级细牙螺纹
< 3 + - - - -
3~6 + - - - -
6~10 + + - - -
10~18 + + + - -
18~30 + + + + -
30~50 + + + + +
注:表中“+”为建议采用的范围
塑件上螺纹的直经不宜过小,外径不应小于4mm,内径不应小于2mm,精度不超过3级。
如果模具上螺纹的螺距未考虑收缩值,那么塑件螺纹与金属螺纹的配合长度则不能太长,一般不大于螺纹直径的1.5~2倍,否则会因干涉而造成附加内应力,使螺纹连接强度降低。
为了防止螺纹最外圈崩裂或变形,应使螺纹最外圈和最里圈留有台阶,如图3-11和图3-12所示。
a)错误b)正确
图1-1 塑件内螺纹的正误形状
a)错误b)正确
图1-2 塑件外螺纹的正误形状
螺纹的始端和终端应逐渐开始和结束,有一段过渡长度l,其数值可按表3-9选取。
表2 塑件上螺纹始末端的过渡长度
螺纹直径/mm
螺距p/mm
< 0.5 0.5~1 > 1 始末端过渡长度l/mm
≤10 1 2 3 >10~20 2 3 4 >20~34 2 4 6 >34~52 3 6 8 >52 3 8 10。
定模螺纹模具设计
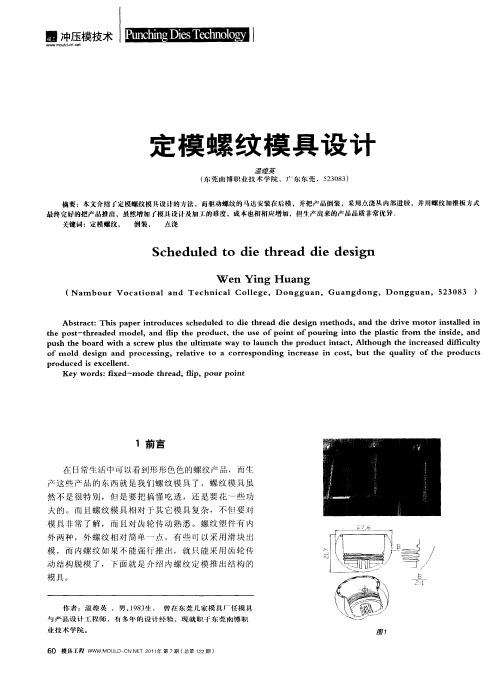
◎
令 . .
⑨
◇
◎《
◎
,
鼹 7A尼 龙 锁模 器
◎
◎
国
毒 函
●◎
j ◎
扳 水 口 摊 扳 Af J 乏 推 扳
B板
力 铁 ‘ J 扳
圈 8 8 杆 拉
62 模 具 1程 V W MOU D— T 2 1年 第 7期 ( : WV L CNNE 0 1 总第 t2期 2
本 模具 由于产品一字形排列 ,而且产 品质量小 ,热 量 也少 ,所 以水路 设计 也 比较 方便 ,因为模仁 长 度有
2 4m 5 m ,所 以怕 钻 头 不 够 长 ,所 以采 用 从 两 端 往 中 间 钻
的方 法 。
根 据 上 面 的分 析 方法 : 模 具 设 计 组 立 图如 下 :
计 包 含 齿 轮 , 轴 承 , 推 板 , 限位 累 丝 , 开 闭器 , 以 及 驱动马达等 。 齿 轮 ,轴 承 是 脱 螺 纹 模 具 的 主 要 零 件 ,如 右 图4 所
不 。
形 能力 ,减小热膨胀系数 。A 的收缩 率约为0 3 0 7 , s . - . % 通 常取0 5 , S . % A 是一种坚硬 材料 。本产 品人 小尺寸 为: 2 . ×2 . ×2 .m , 7 6 7 6 1 7m 模具温度不要超过6  ̄, 0C 因为模 具 温度将直 接影 响制 品的外 观 、收 缩率和弯 曲, 冷却系统
爱 冲压模技术
定 模 螺 纹 模 具 设 计
温 煌 英 ( 莞 南 博 职 业 技 术 学 院 , 广 东 东 莞 ,5 3 8 ) 东 2 0 3
摘要 :本 文介绍 r定模 螺纹模具设计 的方法 ,而驱动螺纹的马达 安装在 后模 ,并把产 品倒 装,采用点浇从 内部进胶 ,并用螺纹加推板方式 最终 完好 的把产 品推 出,虽然增 加 r模 具设计及加工的难度 ,成本 也相相应增 加,但 生产出来的产品品质非常优 异。 关键词 :定模螺纹 , 倒装 . 点浇
- 1、下载文档前请自行甄别文档内容的完整性,平台不提供额外的编辑、内容补充、找答案等附加服务。
- 2、"仅部分预览"的文档,不可在线预览部分如存在完整性等问题,可反馈申请退款(可完整预览的文档不适用该条件!)。
- 3、如文档侵犯您的权益,请联系客服反馈,我们会尽快为您处理(人工客服工作时间:9:00-18:30)。
螺纹模具设计要点
塑胶产品螺纹分外螺纹和内螺纹两种,精度不高的外螺纹一般用哈夫块成型,而内螺纹则大多需要卸螺纹装置。
今天简单介绍内螺纹脱模方法,重点介绍齿轮的计算和选择。
一、卸螺纹装置分类
1、按动作方式分
①螺纹型芯转动,推板推动产品脱离;
②螺纹型芯转动同时后退,产品自然脱离。
2、按驱动方式分
①油缸+齿条
②油马达/电机+链条
③齿条+锥度齿轮
④来福线螺母
ﻫ
二、设计步骤
必须掌握产品的以下数据(见下图)
①“D”——螺纹外
②“P”——螺纹牙距
③“L”——螺纹牙长
④螺纹规格/方向/头数
⑤型腔数量
ﻫ
2、确定螺纹型芯转动圈数:
U=L/P + Us
U螺纹型芯转动圈数
Us 安全系数,为保证完全旋出螺纹所加余量,一般取0.25~1
3、确定齿轮模数、齿数和传动比:
模数决定齿轮的齿厚,齿数决定齿轮的外径,传动比决定啮合齿轮的转速。
在此之前有必要讲一下齿轮的参数和啮合条件。
三、齿轮的参数和啮合条件
模具的卸螺纹机构中大多应用的是直齿圆柱齿轮,而且一般都是渐开线直齿圆柱齿轮,因此下面就以渐开线直齿圆柱齿轮为研究对象。
1 齿轮传动的基本要求
①要求瞬时传动比恒定不变
②要求有足够的承载能力和较长的使用寿命
2、直齿圆柱齿轮啮合基本定律
两齿轮廓不论在何处接触,过接触点所作的两啮合齿轮的公法线,必须与两轮连心线相交于一点“C”,这样才能保证齿轮的瞬时传动比不变。
将所有“C”点连起来就成了2个外切圆,称之为分度圆,分度圆圆心距即齿轮圆心距。
详见下图
ﻫ
3、渐开线直齿圆柱齿轮参数
分度圆直径------“d”表示
分度圆周长--------“S”表示
齿轮齿距--------“p”表示
齿轮齿厚--------“sk”表示
齿轮齿槽宽--------“ek”表示
齿轮齿数--------“z”表示
齿轮模数--------“m”表示
齿轮压力角--------“ɑ”表示
齿轮传动比--------“i”表示齿轮中心距--------“l”表示
4、计算公式如下:
①齿距 = 齿厚 + 齿槽宽即:p = sk + ek
②模数的由来:
因为S = Z x P =π x d
d = P / π x Z
π是无理数,为计算方便,将P / π 规定为常数,即模数,用m 表示,故有公式如下: d =mx z
即:分度圆直径等于模数乘以齿数。
我国规定模数有2个系列,优先采用第一系列。
模数第一系列:1、1.25、1.5、 2、2.5、3、4、5、6 8 、10…
模数第二系列:1.75、2.25、2.75、3.25、3.5、4.5、5.5、7…
③压力角:我国规定:分度圆处的压力角为标准压力角,其值20°。
④传动比:当模数一定时,传动比就等于齿数比,即 i = Z1 / Z 2
⑤中心距:当齿数确定时,中心距I =(Z1+Z2) / 2 * m
5、齿轮啮合条件
模数和压力角相同的齿轮都可以正确啮合。
怎样在实际应用中确定齿轮的模数、齿数和传动比。
1.齿数
当传动中心距一定时,齿数越多,传动越平稳,噪音越低。
但齿数多,模数就小,齿厚也小,致使其弯曲强度降低,因此在满足齿轮弯曲强度条件下,尽量取较多的齿数和较小的模数。
为避免干涉,齿数一般取Z≥17,螺纹型芯的齿数尽可能少,但最少不少于14齿,且最好取偶数。
ﻫ
2.模数
工业用齿轮模数一般取m≥2。
英制齿轮采用径节制,径节齿轮把齿数z与分度圆直径d之比定为径节,以”P”表示,即p =z/d, 1/in
径节与模数的换算公式为m = 25.4/p,mm
3.传动比
传动比在高速重载或开式传动情况下选择质数,目的为避免失效集中在几个齿上。
传动比还与选择哪种驱动方式有关系,比如用齿条+锥度齿或来福线螺母这两种驱动时,因传动受行程限制,须大一点,一般取1≤i≤4;当选择用油缸或电机时,因传动无限制,既可以结构紧凑点节省空间,又有利于降低马达瞬间启动力,还可以减慢螺纹型芯旋转速度,一般取0.25≤i≤1。