熔模铸造常见缺陷及防止方法
不锈钢熔模铸造缺陷分析及质量控制
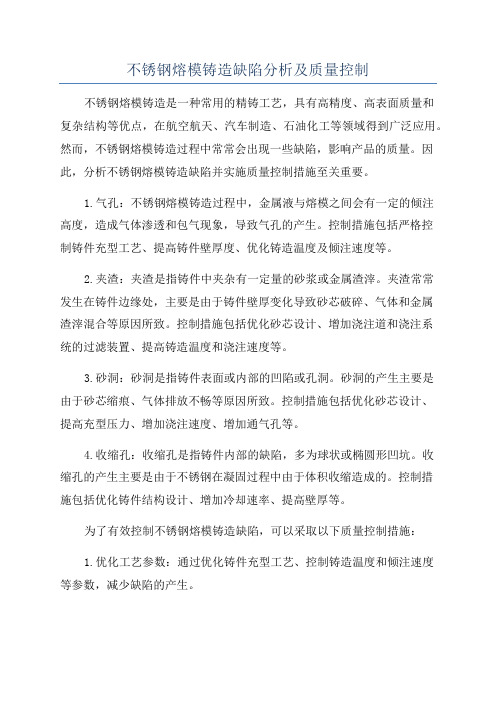
不锈钢熔模铸造缺陷分析及质量控制不锈钢熔模铸造是一种常用的精铸工艺,具有高精度、高表面质量和复杂结构等优点,在航空航天、汽车制造、石油化工等领域得到广泛应用。
然而,不锈钢熔模铸造过程中常常会出现一些缺陷,影响产品的质量。
因此,分析不锈钢熔模铸造缺陷并实施质量控制措施至关重要。
1.气孔:不锈钢熔模铸造过程中,金属液与熔模之间会有一定的倾注高度,造成气体渗透和包气现象,导致气孔的产生。
控制措施包括严格控制铸件充型工艺、提高铸件壁厚度、优化铸造温度及倾注速度等。
2.夹渣:夹渣是指铸件中夹杂有一定量的砂浆或金属渣滓。
夹渣常常发生在铸件边缘处,主要是由于铸件壁厚变化导致砂芯破碎、气体和金属渣滓混合等原因所致。
控制措施包括优化砂芯设计、增加浇注道和浇注系统的过滤装置、提高铸造温度和浇注速度等。
3.砂洞:砂洞是指铸件表面或内部的凹陷或孔洞。
砂洞的产生主要是由于砂芯缩痕、气体排放不畅等原因所致。
控制措施包括优化砂芯设计、提高充型压力、增加浇注速度、增加通气孔等。
4.收缩孔:收缩孔是指铸件内部的缺陷,多为球状或椭圆形凹坑。
收缩孔的产生主要是由于不锈钢在凝固过程中由于体积收缩造成的。
控制措施包括优化铸件结构设计、增加冷却速率、提高壁厚等。
为了有效控制不锈钢熔模铸造缺陷,可以采取以下质量控制措施:1.优化工艺参数:通过优化铸件充型工艺、控制铸造温度和倾注速度等参数,减少缺陷的产生。
2.加强设备管理:定期检查和维护熔模设备,确保各项设备的正常运行。
3.严格原材料控制:对原材料进行检验,确保其质量合格。
4.检测和分析技术:采用非破坏性检测技术,如X射线检测、超声波检测等,对铸件进行缺陷检测和分析,及时发现和解决问题。
5.过程控制和持续改进:建立严格的质量控制流程,持续跟踪和改进生产过程中的关键环节,提高产品质量和生产效率。
综上所述,通过分析不锈钢熔模铸造缺陷并实施相应的质量控制措施,可以有效降低缺陷的发生率,提高产品的质量和可靠性。
熔模铸件缺陷分析及对策

熔模铸件缺陷分析及对策 熔模铸造(又称失蜡铸造),它是一种 近净形成形的先进工艺。熔模铸造的工艺特 点归纳起来为三点: ① 使用可熔(溶)性一次模和一次型 (芯),不用开型起模,无分型面。
② 采用涂料浆制型壳,涂层对蜡模(易熔 模)复印性好。 ③ 采用热壳浇注,金属液充型性好。
因此,熔模铸造可以制造尺寸精度高 (CT4-6),表面粗糙度低(Ra0.8-3.2μ)的 复杂铸件。
① 硅溶胶和硅酸乙酯水解液粘结剂本身粘度小,故配
制的面层涂料粉液比较高,如配锆英粉涂料时粉液比
可达4以上,配刚玉粉涂料时粉液比也可在3.2以上,配
石英粉涂料时可达2.2左右。 ② 水玻璃粘结剂因自身粘度高,故水玻璃涂料粉液 比很低,配石英粉涂料时,粉液比常为:1.0—1.1。但 也可以通过降低水玻璃密度:1.26—1.28g/cm3,模数
3、金属液精确复型的影响因素
⑴ 合适的型壳温度:
薄壁件及小件要求型壳经焙烧后,尽可能的保证有足够 高的型壳温度迅速浇注。因为提高型壳温度对改善金属液流 动能力、复型能力有良好的效果。过高的合金熔炼温度常因 增加金属液的吸气量,减少结晶形核基底等因素,而对材质 产生不利影响。 厚大件要求型壳温度较低为好,冷却速度快,减少形成 缩孔、缩松的缺陷倾向。 硅溶液、硅酸乙酯型壳的焙烧温度为 1050-1100℃ ,水 玻璃型壳焙烧温度为850℃,出炉后迅速浇注。
罩密封,使铸件在还原气氛中冷却。
⑵ 清理对熔模铸件表面粗糙度的影响
清理对熔模铸件表面粗糙度的影响也很大,应
注意以下几个方面: ① 喷砂清理的方法比喷丸清理铸件表面粗糙度 好2级以上。
② 采用高压水力清砂是保证铸件表面粗糙度较
好的方法。
③ 整组铸件组振壳后,先喷丸再切割,个别清不到的
[熔模铸造蜡模表面欠注等缺陷的应对分析]表面缺陷有哪些
![[熔模铸造蜡模表面欠注等缺陷的应对分析]表面缺陷有哪些](https://img.taocdn.com/s3/m/fc58f72e657d27284b73f242336c1eb91a373388.png)
[熔模铸造蜡模表面欠注等缺陷的应对分析]表面缺陷有哪些熔模铸造蜡模表面欠注等缺陷的应对分析1提出问题熔模铸造的蜡基模料种类繁多、配比多样;但是由于石蜡—硬脂酸蜡料具有取材容易、价格便宜,以及流动性好、配制简单、回用性好、两者的互溶性好等一系列优点而得到广泛的应用。
当蜡模存在欠注、冷隔和鼓泡等表面缺陷时,不仅浪费了人工和生产时间,有时会影响到生产进度。
因此,应及时有效地解决蜡模上述的缺陷。
2缺陷概述2.1缺陷种类一般情况下,蜡模表面的缺陷主要有:欠注、冷隔和鼓泡三种。
2.2外部特征欠注:蜡模局部欠注处,呈现圆弧状的表面。
冷隔:在蜡模上,蜡料的交汇处出现圆滑的沟槽。
鼓泡:蜡模的表面上有局部、空心、大小不等的圆弧凸起。
3欠注3.1产生原因3.1.1注蜡时,压型或蜡料的温度太低,蜡料的流动性差,充填能力低。
压型温度和蜡料温度是制模工艺的主要参数之一。
压制蜡模时,由于压型的温度低或蜡料的温度低,降低了蜡料的流动性和充填能力,使蜡料不易快速充填压型的型腔,造成蜡模欠注。
3.1.2注蜡压力小,注射速度太低,或注蜡中断。
注射压力是制模工艺的主要参数之一。
压制蜡模时,由于注射的压力小,注射的速度低,或注蜡中断,降低了蜡料的流动性和充填能力,造成蜡模欠注。
3.1.3注蜡孔的位置不合理,或注蜡孔的截面太小。
注蜡孔位置的设置和注蜡孔截面尺寸是压型设计的重要参数,注蜡孔位置设置不当,使蜡料在压型中的流程过长,不利于蜡料充填压型;注蜡孔的截面太小,注入的蜡料量不够,难以充填满压型的型腔;造成蜡模欠注。
3.1.4压型的排气不良。
压型的排气不良,阻碍了蜡料充填压型,导致蜡模欠注。
3.2防止措施3.2.1注蜡时,适当的提高压型或蜡料的温度。
注蜡温度一般选用45℃~48℃;压型的温度一般选用20℃~25℃,以提高蜡料的流动性和充填能力。
3.2.2适当的提高注蜡压力与速度。
当选用气动压蜡机注射蜡料时,对于硬脂酸蜡料,由于其粘度低、流动性好,而常用注射压力为0.2MPa~0.6MPa(根据蜡模的大小、形状等因素而选择)。
常见铸造缺陷产生的原因及防止方法

常见铸造缺陷产生的原因及防止方法铸件缺陷种类繁多,产生缺陷的原因也十分复杂.它不仅与铸型工艺有关,而且还与铸造合金的性制、合金的熔炼、造型材料的性能等一系列因素有关.因此,分析铸件缺陷产生的原因时,要从具体情况出发,根据缺陷的特征、位置、采用的工艺和所用型砂等因素,进行综合分析,然后采取相应的技术措施,防止和消除缺陷.一、浇不到1、特征铸件局部有残缺、常出现在薄壁部位、离浇道最远部位或铸件上部.残缺的边角圆滑光亮不粘砂.2、产生原因1 浇注温度低、浇注速度太慢或断续浇注;2 横浇道、内浇道截面积小;3 铁水成分中碳、硅含量过低;4 型砂中水分、煤粉含量过多,发气量大,或含泥量太高,透气性不良;5 上砂型高度不够,铁水压力不足.3、防止方法1 提高浇注温度、加快浇注速度,防止断续浇注;2 加大横浇道和内浇道的截面积;3 调整炉后配料,适当提高碳、硅含量;4 铸型中加强排气,减少型砂中的煤粉,有机物加入量;5 增加上砂箱高度.二、未浇满1、特征铸件上部残缺,直浇道中铁水的水平面与铸件的铁水水平面相平,边部略呈圆形.2、产生原因1 浇包中铁水量不够;2 浇道狭小,浇注速度又过快,当铁水从浇口杯外溢时,操作者误认为铸型已经充满,停浇过早.3、防止方法1 正确估计浇包中的铁水量;2 对浇道狭小的铸型,适当放慢浇注速度,保证铸型充满.三、损伤1、特征铸件损伤断缺.2、产生原因1 铸件落砂过于剧烈,或在搬运过程中铸件受到冲撞而损坏;2 滚筒清理时,铸件装料不当,铸件的薄弱部分在翻滚时被碰断;3 冒口、冒口颈截面尺寸过大;冒口颈没有做出敲断面凹槽.或敲除浇冒口的方法不正确,使铸件本体损伤缺肉.3、防止方法1 铸件在落砂清理和搬运时,注意避免各种形式的过度冲撞、振击,避免不合理的丢放;2 滚筒清理时严格按工艺规程和要求进行操作;3 修改冒口和冒口颈尺寸,做出冒口颈敲断面,正确掌握打浇冒口的方向.四、粘砂和表面粗糙1、特征粘砂是一种铸件表面缺陷,表现为铸件表面粘附着难以清除的砂粒;如铸件经清除砂粒后出现凹凸不平的不光滑表面,称表面粗糙.2、产生原因1 砂粒太粗、砂型紧实度不够;2 型砂中水分太高,使型砂不易紧实;3 浇注速度太快、压力过大、温度过高;4 型砂中煤粉太少;5 模板烘温过高,导致表面型砂干枯;或模板烘温过低,型砂粘附在模板上.3、防止方法1 在透气性足够的情况下,使用较细原砂,并适当提高型砂紧实度;2 保证型砂中稳定的有效煤粉含量;3 严格控制砂水分;4 改进浇注系统,改进浇注操作、降低浇注温度;5 控制模板烘烤温度,一般与型砂温度相等或略高.五、砂眼1、特征在铸件内部或表面充塞有型砂的孔眼.2、产生原因1 型砂表面强度不够;2 模样上无圆角或拔模斜度小导致钩砂、铸型损坏后没修理或没修理好就合箱;3 砂型在浇注前放置时间过长,风干后表面强度降低;4 铸型在合箱时或搬运过程中损坏;5 合箱时型内浮砂未清除干净,合箱后浇口杯没盖好,碎砂掉进铸型.3、防止方法1 提高型砂中粘士含量、及时补加新砂,提高型砂表面强度;2 模样光洁度要高,并合理做出拔模斜度和铸造圆角.损坏的铸型要修好后再合箱;3 缩短浇注前砂型的放置时间;4 合箱或搬运铸型时要小心,避免损坏或掉入砂型腔砂粒;5 合箱前清除型内浮砂,并盖好浇口.六、披缝和胀砂1、特征披缝常出现在铸件分型面处,是垂直于铸件表面,且厚薄不均匀的薄片状金属突起物. 胀砂是铸件内、外表面局部胀大,形成不规则的瘤状金属突起物.2、产生原因1 紧实度不够或不匀;2 面砂强度不够、或型砂水分过高;3 液态金属压头过大、浇注速度太快.3、防止方法1 提高铸型紧实度、避免局部过松;2 调整混砂工艺、控制水分,提高型砂强度;3 降低液态金属的压头、降低浇注速度.七、抬箱1、特征铸件在分型面处有大面积的披缝,使铸型外形尺寸发生变化.抬箱过大,造成跑火——铁水自分型面外溢,严重时造成浇不足缺陷.2、产生原因1 砂箱未紧固、压铁质量不够或去除压铁过早;2 浇注过快,冲击力过大;3 模板翅曲.3、防止方法1 增加压铁重量,特铁水凝固后再去除压铁;2 降低浇包位置,降低浇注速度;3 修正模板.八、掉砂1、特征铸件表面上出现的块状金属突起物,其外形与掉落的砂块很相似.在铸件其它部位,则往往出现砂眼或残缺.2、产生原因1 模样上有深而小的凹槽,同于结构特征或拔模斜度小,起模时将砂型带坏或震裂;2 紧实度不匀,铸型局部强度不足;3 合箱、搬运铸型时,不小心使铸型局部砂块掉落.3、防止方法1 模样拔模斜度要合适、表面光洁;2 铸型紧实度高且均匀;3 合箱、搬运过程中,操作小心.九、错型错箱1、特征铸件的一部分与另一部分在分型面的接缝处错开,发生相对位移,使铸件外形与图纸不相符合.2、产生原因1 模样制作不良,上下模没有对准或模样变形;2 砂箱或模板定位不准确,或定位销松动;3 挤压造型机上零件磨损,例如正压板下衬板、反压板轴承的磨损等;4 浇注时用的套箱变形,搬运、围箱时不注意,使上下铸型发生位移.3、防止方法1 加强模板的检查和修理;定2 经常检查砂箱、模板的定位销及销孔、并合理地安装;3 检查挤压造型机的有关零件,及时调整,磨损大的要更换;4 定期对套箱整形.脱箱后的铸型在搬运时要小心.在面浇注的砂型,应该做一排砂型围一排.十、灰口和麻点1、特征铸件断口呈灰黑色或出现黑色小点,中心部位较多,边部较少,金相观察可见到片状石墨.2、产生原因1 铁水化学成分不合要求,碳、硅含量过高;2 炉前孕育的铋加入浇包内过早或过迟,或是铋量不足.3、防止方法1 正确选择化学成分,合理配料,使铁水中碳、硅量在规定范围内;2 增加铋的加入量并严格炉前孕育工艺.十一、裂纹热裂、冷裂1、特征铸件外部或内部有穿透或不穿透的裂纹.热裂时带有暗色或黑色的氧化表面断口外形曲折.冷裂是较干净的脆性裂纹,断口较平,具有金属光泽或轻微的氧化色泽.2、产生原因1 铁水中碳、硅含苞欲放量过低,含硫量过高;2 浇注温度过高;3 冒口颈过大、过短,造成局部过热严重,或重口太小,补缩不好;4 铸件在清理、运输过程中,受冲击过大.3、防止方法1 控制铁水化学成分在规定的范围内;2 降低浇注温度;3 合理设计冒口系统;4 铸件在清理、运输过程中避免过度冲击.十二、气孔1、特征气孔的孔壁光滑明亮,形状有圆形、梨形和针状,孔的尺寸有大有小,产生在铸件表面或内部.铸件内部的气孔在敲碎后或机械加工时才能被发现.2、产生原因1 小炉料潮湿、锈蚀严重或带有油污,使铁水含气量太多、氧化严重;2 出铁孔、出铁槽、炉衬、浇包衬未洪干;3 浇注温度较低,使气体来不及上浮和逸出;4 炉料中含铝量较高,易造成氢气孔;5 砂型透气性不好、型砂水分高、含煤粉或有机物较多,使浇注时产生大量气体且不易排出.3、防止方法1 炉料要妥善管理,表面要清洁;2 炉缸、前炉、出铁口、出铁槽、浇包必须烘干;3 提高浇注温度;4 不使用铝量过高的废钢;5 适当降低型砂的水分、控制煤粉加入量,扎通气孔等.十三、缩松、疏松1、特征分散、细小的缩孔,带有树枝关结晶的称缩松,比缩松更细小的称疏松.常出现在热世部位.2、产生原因1 铁水中碳、硅含量过低,收缩大;2 浇注速度太快、浇注温度过高,使得液态收缩大;3 浇注系统、冒口设计不当,无法实现顺序凝固;4 冒口太小,补缩不充分.3、防止方法1 控制铁水的化学成分在规定范围内;2 降低浇注速度和浇注温度;3 改进浇冒口系统,利用顺序凝固;4 加大冒口体积,保证充分补缩.十四、反白口1、特征铸件断口内部出现白口组织,边缘部分出现灰口.2、产生原因1 碳、硅含量较高的铁水,含氢量过高;2 炉料中带入的铬等白口形成元素过多;3 元素偏析严重;3、防止方法1 控制化学成分、碳、硅含量不宜过高;2 炉衬、包衬要烘干;型砂水分不宜过高;3 加强炉料管理,减少带入白口化元素.。
模具铸造五大缺陷及解决对策

缺陷一:铸造缩孔主要原因有合金凝固收缩产生铸造缩孔和合金溶解时吸收了大量的空气中的氧气、氮气等,合金凝固时放出气体造成铸造缩孔。
解决的办法:1)放置储金球。
2)加粗铸道的直径或减短铸道的长度。
3 )增加金属的用量。
4)采用下列方法,防止组织面向铸道方向出现凹陷。
a.在铸道的根部放置冷却道。
b.为防止已熔化的金属垂直撞击型腔,铸道应成弧形。
C.斜向放置铸道。
缺陷二:铸件表面粗糙不光洁缺陷型腔表面粗糙和熔化的金属与型腔表面产生了化学反应,主要体现出下列情况。
1)包埋料粒子粗,搅拌后不细腻。
2)包埋料固化后直接放入茂福炉中焙烧,水分过多。
3)焙烧的升温速度过快,型腔中的不同位置产生膨胀差,使型腔内面剥落。
4)焙烧的最高温度过高或焙烧时间过长,使型腔内面过于干燥等。
5 )金属的熔化温度或铸圈的焙烧的温度过高,使金属与型腔产生反应,铸件表面烧粘了包埋料。
6)铸型的焙烧不充分,已熔化的金属铸入时,引起包埋料的分解,发生较多的气体,在铸件表面产生麻点。
7)熔化的金属铸入后,造成型腔中局部的温度过高,铸件表面产生局部的粗糙。
解决的办法:a.不要过度熔化金属。
b.铸型的焙烧温度不要过高。
C.铸型的焙烧温度不要过低(磷酸盐包埋料的焙烧温度为800度-900 度)。
d.避免发生组织面向铸道方向出现凹陷的现象。
e.在蜡型上涂布防止烧粘的液体。
缺陷三:铸件发生龟裂缺陷有两大原因,一是通常因该处的金属凝固过快,产生铸造缺陷(接缝);二是因高温产生的龟裂。
1)对于金属凝固过快,产生的铸造接曜,可以通过控制铸入时间和凝固时间来解决。
铸入时间的相关因素:蜡型的形状。
铸到的粗细数量。
铸造压力(铸造机)。
包埋料的透气性。
凝固时间的相关因素:蜡型的形状。
铸圈的最高焙烧温度。
包埋料的类型。
金属的类型。
铸造的温度。
2)因高温产生的龟裂,与金属及包埋料的机械性能有关。
下列情况易产生龟裂:铸入温度高易产生龟裂;强度高的包埋料易产生龟裂;延伸性小的银烙合金及钻烙合金易产生龟裂。
304不锈钢熔模铸造中缩孔、缩松的几种防止措施

熔模铸造中缩松的几种特有解决方案
缩松是铸造最常见的缺陷之一,是铸件在冷却过程中热节或远浇口部位得不到有效的补缩而产生的细小分散的孔洞。
熔模铸造因为热壳浇注的特点,在浇注系统设计时大大地限制了冒口、冷铁对于缩松的处理,但是却有一系列独特的解决方案。
1、型壳底部淬水
部位:铸件浇注位置底部。
铸件浇注位置底部远离浇冒口,补缩通道过长,如果铸件较高或底部有热节,就容易产生缩松。
原理:通过淬水使型壳底部温度迅速降低,对铸件起到底部激冷的作用。
操作:热壳浇注后,型壳立刻淬水,视铸件薄厚在水中停顿1-3秒,深度为易缩松的位置。
案例1圆环产品,材质304不锈钢,浇注温度1640℃
此产品组树后高度方向尺寸较大,见图1和图2,浇注后于圆环浇注位置的下半圆A处容易出现缩松,如图1,经分析认为补缩通道过长导致下半圆凝固时钢水得不到有效补缩,从而产生缩松。
工艺改进为型壳底部淬水,深度如图2所示,效果良好,基本解决下半圆的缩松问题。
图1 圆环剖面图图2 圆环组树淬水示意图
2、喷水激冷
3、局部补砂泥
4、中空型壳
5、加保温棉
6、工艺散热冷铁
7、冷铁、热贴。
熔模铸件之常见熔模铸造缺陷的防止
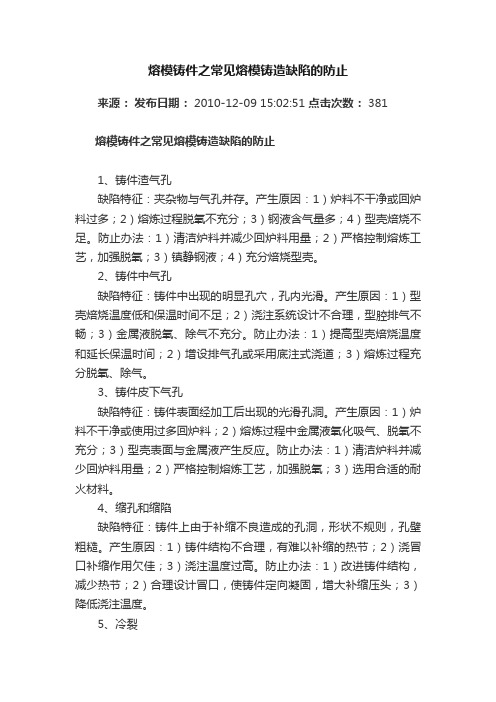
熔模铸件之常见熔模铸造缺陷的防止来源:发布日期: 2010-12-09 15:02:51 点击次数: 381熔模铸件之常见熔模铸造缺陷的防止1、铸件渣气孔缺陷特征:夹杂物与气孔并存。
产生原因:1)炉料不干净或回炉料过多;2)熔炼过程脱氧不充分;3)钢液含气量多;4)型壳焙烧不足。
防止办法:1)清洁炉料并减少回炉料用量;2)严格控制熔炼工艺,加强脱氧;3)镇静钢液;4)充分焙烧型壳。
2、铸件中气孔缺陷特征:铸件中出现的明显孔穴,孔内光滑。
产生原因:1)型壳焙烧温度低和保温时间不足;2)浇注系统设计不合理,型腔排气不畅;3)金属液脱氧、除气不充分。
防止办法:1)提高型壳焙烧温度和延长保温时间;2)增设排气孔或采用底注式浇道;3)熔炼过程充分脱氧、除气。
3、铸件皮下气孔缺陷特征:铸件表面经加工后出现的光滑孔洞。
产生原因:1)炉料不干净或使用过多回炉料;2)熔炼过程中金属液氧化吸气、脱氧不充分;3)型壳表面与金属液产生反应。
防止办法:1)清洁炉料并减少回炉料用量;2)严格控制熔炼工艺,加强脱氧;3)选用合适的耐火材料。
4、缩孔和缩陷缺陷特征:铸件上由于补缩不良造成的孔洞,形状不规则,孔壁粗糙。
产生原因:1)铸件结构不合理,有难以补缩的热节;2)浇冒口补缩作用欠佳;3)浇注温度过高。
防止办法:1)改进铸件结构,减少热节;2)合理设计冒口,使铸件定向凝固,增大补缩压头;3)降低浇注温度。
5、冷裂缺陷特征:裂纹大多穿过晶粒,表面光亮。
产生原因:1)铸件结构不合理;2)浇注系统设计不合理;3)铸件在搬运和清砂过程中受撞击;4)铸件在矫正时操作不当或未退火。
防止办法:1)改进铸件结构和浇注系统设计,减小收缩应力;2)避免撞击和抛甩铸件;3)矫正前进行退火,并改进矫正操作;4)减少型壳层数,并改善退让性;5)降低铸件的冷却速度,例如型壳可改用填砂浇注。
6、热裂缺陷特征:裂纹沿晶界生长,表面有氧化颜色。
产生原因:1)铸型温度低,冷却速度过快;2)型壳退让性差,阻碍收缩;3)铸件结构不合理,壁厚相差悬殊,过渡突变,应力过大;4)浇注补缩系统设计不合理,造成铸件局部过热或收缩受阻。
常见铸件缺陷及其预防措施

铸件缺陷常见铸件缺陷及其预防措施1).冷紋:原因:熔汤前端的温度太低,相叠时有痕迹.改善方法:1.检查壁厚是否太薄(設計或制造) ,较薄的区域应直接充填.2.检查形狀是否不易充填;距离太远、封閉区域(如鳍片(fin) 、凸起) 、被阻挡区域、圆角太小等均不易充填.並注意是否有肋点或冷点.3.缩短充填时间.缩短充填时间的方法:…4.改变充填模式.5.提高模温的方法:…6.提高熔汤温度.7.检查合金成分.8.加大逃气道可能有用.9.加真空裝置可能有用.2).裂痕:原因:1.收缩应力.2.頂出或整缘时受力裂开.改善方式:1.加大圆角.2.检查是否有热点.3.增压时间改变(冷室机).4.增加或缩短合模时间.5.增加拔模角.6.增加頂出銷.7.检查模具是否有錯位、变形.8.检查合金成分.3).气孔:原因:1.空气夾杂在熔汤中.2.气体的来源:熔解时、在料管中、在模具中、离型剂.改善方法:1.适当的慢速.2.检查流道转弯是否圆滑,截面积是否渐減.3.检查逃气道面积是否够大,是否有被阻塞,位置是否位於最后充填的地方.4.检查离型剂是否噴太多,模温是否太低.5.使用真空.4).空蚀:原因:因压力突然減小,使熔汤中的气体忽然膨胀,冲击模具,造成模具損伤.改善方法:流道截面积勿急遽变化.5).缩孔:原因:当金属由液态凝固为固态时所占的空间变小,若无金属补充便会形成缩孔.通常发生在较慢凝固处.改善方法:1.增加压力.2.改变模具温度.局部冷却、噴离型剂、降低模温、.有时只是改变缩孔位置,而非消缩孔.6).脫皮:原因:1.充填模式不良,造成熔汤重叠.2.模具变形,造成熔汤重叠.3.夾杂氧化层.改善方法:1.提早切換为高速.2.缩短充填时间.3.改变充填模式,浇口位置,浇口速度.4.检查模具強度是否足夠.5.检查銷模裝置是否良好.6.检查是否夾杂氧化层.7).波紋:原因:第一层熔汤在表面急遽冷却,第二层熔汤流過未能将第一层熔解,却又有足夠的融合,造成組织不同. 改善方法:1.改善充填模式.2.缩短充填时间.8).流动不良产生的孔:原因:熔汤流动太慢、或是太冷、或是充填模式不良,因此在凝固的金属接合处有孔.改善方法:1.同改善冷紋方法.2.检查熔汤温度是否稳定.3.检查模具温充是否稳定.9).在分模面的孔:原因:可能是缩孔或是气孔.改善方法:1.若是缩孔,減小浇口厚度或是溢流井进口厚度.2.冷却浇口.3.若是气孔,注意排气或捲气問题.10).毛边:原因:1.鎖模力不足.2.模具合模不良.3.模具強度不足.4.熔汤温度太高.11).缩陷:原因:缩孔发生在压件表面下面.改善方法:1.同改善缩孔的方法.2.局部冷却.3.加热另一边.12).积碳:原因:离型剂或其他杂质积附在模具上.改善方法:1.减小离型剂喷洒量.2.升高模温.3.选择适合的离型剂.4.使用软水稀釋离型剂.13).冒泡:原因:气体捲在铸件的表面下面.改善方式:1.減少捲气(同气孔).2.冷却或防低模温.14).粘模:原因:1.鋅积附在模具表面.2.熔汤冲击模具,造成模面损坏.改善方法:1.降低模具温度.2.降低划面粗糙度.3.加大拔模角.4.镀膜.5.改变充填模式.6.降低浇口速度序缺陷名称缺陷特征预防措施1气孔在铸件内部、表面或近于表面处,有大小不等的光滑孔眼,形状有圆的、长的及不规则的,有单个的,也有聚集成片的。
- 1、下载文档前请自行甄别文档内容的完整性,平台不提供额外的编辑、内容补充、找答案等附加服务。
- 2、"仅部分预览"的文档,不可在线预览部分如存在完整性等问题,可反馈申请退款(可完整预览的文档不适用该条件!)。
- 3、如文档侵犯您的权益,请联系客服反馈,我们会尽快为您处理(人工客服工作时间:9:00-18:30)。
型 壳 变 形
型壳变形大多在脱蜡、焙烧或浇注时产生
1涂料的粘度过大,涂层过厚,涂料堆积
2硬化剂浓度低温度低硬化时间太短,硬化不足
3脱蜡水温度低,脱蜡时间过长
4焙烧时型壳受挤压或温度过高
1控制涂料粉液比和粘度
2避免涂料局部堆积
3控制硬化剂浓度,温度和硬化时间
1表面层涂料粘度不要太高,增加涂料流动性2避免蜡模表面及局部涂料堆积,应使涂料分 布均匀
3表面层浸涂料撒砂后,先经一定时间的自然 干燥后,再进行化学硬化
4表面层的化学硬化要充分
型 壳 分 层 和 鼓 胀
1涂料撒砂后,表面有浮砂
2表面层撒砂的粒度过细,砂中粉尘过多或砂 粒受潮含水分过多
3型壳表面层化学硬化后风干时间过短,残留 硬化剂过多
2模料收缩率大或太脆
3压型设计不正确,或起模操作不当
4压型温度过低,使熔模冷却太快
5压注时模料温度偏高
1控制熔模在压型中的冷却时间
2改用收缩率小、韧性好的模料
3改进压型设计,增大圆角或起模斜度,起模 时用力要均匀
4提高压型的工作温度
5降低压注时模料的温度
鼓 包
1模料中搅入了气体
2起模太早,被压缩的气包膨胀
3熔模没有及时冷却,或冷却不充分
4制模室温度过高
1配置模料时应避免裹入过多的气体
2适当延长保压时间
3从压型取出的熔模应及时冷却并控制冷却时 间
4严格控制制模室工作温度
变
形
1起模过早,
2压型设计不良
3熔模存放状态不良,引起变形
4熔模存放温度过高
5熔模存放时间过长
6熔模收缩率偏大
1延长保压时间,或采用校正模
1改进型芯强化工艺,对壁厚差大形状复杂的 型芯可米取局部强化
2选择流动性好的模料,适当降低注射压力
3合理设置注蜡口,避免蜡流直接冲击型芯的 薄弱区域
4限制型芯允许变形量,改进制模时型芯定位 方法,或使用芯撑
5开型起模小心,用力均匀
水玻璃型壳的缺陷及防止方法
缺陷 名称
产生原因
防止措施
表 面 蚁 孔
1涂料中硬脂酸配比过低,蜡模表面未进行脱 脂处理
4缩短脱蜡时间,适当提高脱蜡水温度(95~98
C)
表 面 析 出 物
1氯化铵硬化的型壳,脱蜡后干燥时,型壳内 在硬化反应时生成的盐分及残留的氯化铵硬 化剂,随水分蒸发扩散迁移到型壳表面上来, 并沿析出孔道堆集生长成茸毛状物质,其中
4/5是NaCl,约1/5是NH4CI
流 纹
1分型剂的用量过多,或涂抹不匀2分型剂选择不当或变质
3注射压力小,注射速度太慢
4压型温度低
1分型剂用量应适当涂抹应薄而均匀2合理选择分型剂并确保分型剂质量3提高注射压力和注射速度
4提高压型温度
缩
陷
1注蜡时模料或压型温度过高
2模料的收缩率大
3注射压力小或保压时间不足,模料得不到充 分补偿
4注蜡口小或位置不当
2改进压型设计增加起模装置注意起模操作
3熔模存放状态合理或采用存放胎具
4控制熔模存放温度
5合理按排生产,缩短熔模存放时间
6改用收缩率小的模料
-H-
心
蜡
1模料收缩率较大
2制模时型芯温度和模料温度均偏低
3型面结构有大面积光滑表面
4型芯表面有油污
1选用收缩率小的模料
2压制熔模前将型芯加热至30~50C,或提高模
2涂料润湿性差
3涂料的粉液比低,流杯粘度小,涂层薄,面 层撒砂粒度粗
1模料中硬脂酸配比不能低于50%
2模料进行脱脂处理
Байду номын сангаас3涂料中加入适当配比表面润湿剂
4提咼涂料粉液比,提咼流杯粘度
5降低面层撒砂粒度
表面 圆珠 状小 孔
1表面层涂料搅拌时卷入过多气体而产生气孔2未加消泡剂
1用发泡力低的表面润湿剂
2涂料中加入适量的消泡剂
3用毛笔刷涂或用压缩空气喷吹气泡
橘子皮和皱疤
1熔模表面局部涂料堆积,涂层过厚。且未经 自然干燥。致使涂料在化学硬化时,表层因 硅凝胶形成急剧收缩,而涂料内层未经充分 硬化,故而在表面形成皱皮
2在面层涂料与熔模表面之间常有盐类和水分 浓集,导致硬化不良,脱蜡时型壳内表面松 散并出现突起和凹坑,形似橘皮状
料的压注温度
3起模后立即用手按压有大面积光滑型芯表面
分
离
5熔模存放过程中室温降低
的熔模相应部位
4型芯表面不允许有分型剂等油污
5严格控制制模室温度
断
-I-R心
1陶瓷型芯室温强化不良室温强度低脆性大
2模料流动性差
3注蜡口位置设计不当,模料直接冲击型芯薄 弱处
4型芯已变形,不能与压型吻合,合型时断裂
5打开压型及起模时操作不当,用力过大
熔模常见缺陷及防止方法
缺陷 名称
产生原因
防止方法
表 面 粗 糙
1蜡膏搅拌不充分或温度不均匀2模料压注温度低
3分型剂不均匀或过多
4压注压力不足或中断
5压型温度过低
1充分搅拌蜡膏,延长保温回性时间2严格控制模料压注温度
3分型剂涂抹应薄而均匀
4提高压注压力
5适当提高压型温度
缺 肉
1压型温度或模料温度过低
2压注压力太小,压注速度太慢
4涂料粘度过大涂层过厚,涂层中间未硬化
1表面层撒砂要干燥,无粉尘,水分小
2表面层撒砂粒度不要太细,并防止浮砂堆积
3表面层涂料粘度不宜太大,防止涂料堆积,涂层 要充分硬化
4表面层硬化后的干燥时间要充分,残留硬化剂要 少
5以氯化铝和氯化镁硬化的型壳在浸第一层涂料 前须进行冲水,凉干以增强层间结合
型 壳 裂 纹
5起模早,冷却不充分
6熔模结构设计不和理,壁厚差悬殊
7熔模局部太厚
1降低压型或模料温度
2换用收缩率小的模料
3提高注射压力和延长保压时间,达到充分补 缩
4增大注蜡口或改变位置,以利补缩
5延迟起模,熔模要及时充分冷却
6改进熔模结构设计壁厚应尽量均匀
7在厚大部位预置冷蜡块(又称蜡芯)
裂 纹
1起模时间过长,熔模收缩受阻
1浸涂料后未能撒上砂粒的部位易产生裂纹
2涂料粘度过低,粉料加入量过少,涂层过薄
3涂层未经充分硬化
4脱蜡水温度低,脱蜡时间过长
5水玻璃模数过低,密度小
6型壳层数不足
1控制水玻璃的模数、密度及涂料芬液比和粘 度
2控制硬化剂的浓度、温度及硬化时间等工艺 参数
3提高脱蜡水温度至95~98C,缩短脱蜡时间4适当增加型壳层数
3模料注入口位置不当或注入口的截面积太小
4模料注入量不够
5压型排气不良
1提高压型或模料温度
2提高注射压力和速度
3改进注入口位置,或增大注蜡孔截面积
4增加模料注入量
5增设排气通道
冷 隔
1压型温度和模料温度低
2分型剂太多或不均匀
3注蜡口小或位置不当
1提高压型和模料温度
2分型剂涂抹应薄而均匀
3增大注蜡口或改变模料注入位置