阶梯轴加工工艺过程
阶梯轴单件小批量生产机械加工工艺过程卡片

产品型号
零(部)件图号
共一页
产品名称
零(部)件名称
阶梯轴
第一页
材料牌号
45#
毛坯种类
棒料
毛坯外形尺寸
Φ57×90
毛坯件数
1
每台
件数
1
备注
工序号
工序
名称
工序内容
车间
工段
加工设备
工艺装备
工时(min)
夹具名称
及型号
刀具名称
及型号
量具与检测
10
车
夹毛坯外圆一端:
①车端面
②钻中心孔
调头,夹毛坯外圆另一端:
铣床通用夹具
键槽铣刀
游标卡尺0-150
6
编制(日期)
审核(日期)
会签(日期)
标记
处数
更改文件号
签字
日期
表1阶梯轴单件小批量生产机械加工工艺过程卡片
表2阶梯轴中批量生产机械加工工艺过程卡片
机械加工工艺过程卡片
产品型号
零(部)件图号
共一页
产品名称
阶梯轴
零(部)件名称
阶梯轴
第一页
材料牌号
45#
毛坯种类
锻件
毛坯外形尺寸
毛坯件数
1
每台
件数
1
备注
工序号
工序
名称
工序内容
车间
工段
加工设备
工艺装备
工时(min)
夹具名称
及型号
道具名称
及型号
量具与检测
10
铣
①铣两端面
②钻中心孔
1
1
铣端面钻中心孔机床
专用铣夹具
阶梯轴加工工艺过程

阶梯轴加工工艺过程
阶梯轴加工工艺是机械加工中常见的一种加工工艺。
它主要应用
于制造汽车发动机、机床、航空航天设备等需要旋转部件的行业。
下
面将详细介绍阶梯轴加工工艺的过程。
第一步,确定加工工艺。
在加工阶梯轴前,首先要制定详细的工
艺流程。
这个过程需要考虑到加工材料的硬度、形状和尺寸等因素。
根据实际需要,选择合适的加工刀具和工艺参数,预估加工时间和成
本等。
第二步,准备工件。
在进行阶梯轴加工之前,需要准备工具和工件。
建议使用高精度数控机床或大型车床进行加工,以确保加工精度
和效率。
在加工之前要根据设计要求检查工件的尺寸和锁紧螺栓是否
紧固。
第三步,粗加工。
在进行阶梯轴的粗加工前,选用合适的切削刀
具和工艺参数,使用刀具将工件的直径挖掉一定的深度。
然后再根据
具体要求挖掉阶梯形,从而形成阶梯形的轴。
第四步,精加工。
在粗加工完成后,进行阶梯轴的精加工。
这个
过程需要使用更精细的刀具,并且要保持加工速度和压力的恒定。
在
轴表面进行光洁度的加工,用检测仪测量轴直径和形状是否符合要求。
第五步,检验工件。
在加工完成后,要对工件进行检验,以确保其符合设计要求和制造标准。
这将有助于保证阶梯轴的使用寿命和性能。
综上所述,阶梯轴加工工艺过程是一个非常复杂的过程,需要专业的技术人员进行处理。
但只要严格遵守加工流程和注意加工安全,就可以成功地加工出高质量的阶梯轴。
数控加工程序编制数控车阶梯轴程序编制
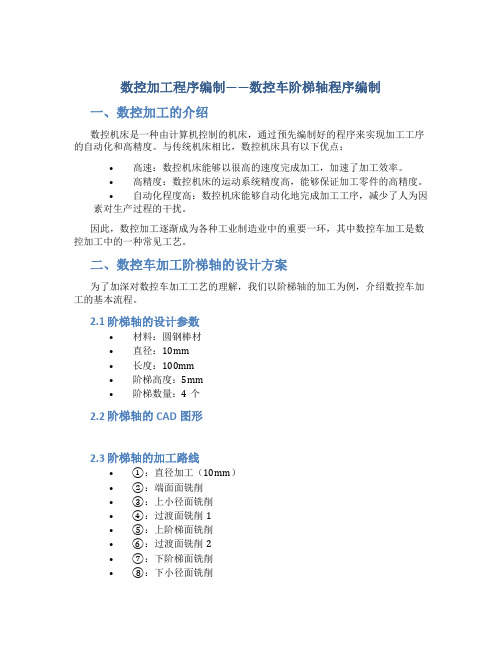
数控加工程序编制——数控车阶梯轴程序编制一、数控加工的介绍数控机床是一种由计算机控制的机床,通过预先编制好的程序来实现加工工序的自动化和高精度。
与传统机床相比,数控机床具有以下优点:•高速:数控机床能够以很高的速度完成加工,加速了加工效率。
•高精度:数控机床的运动系统精度高,能够保证加工零件的高精度。
•自动化程度高:数控机床能够自动化地完成加工工序,减少了人为因素对生产过程的干扰。
因此,数控加工逐渐成为各种工业制造业中的重要一环,其中数控车加工是数控加工中的一种常见工艺。
二、数控车加工阶梯轴的设计方案为了加深对数控车加工工艺的理解,我们以阶梯轴的加工为例,介绍数控车加工的基本流程。
2.1 阶梯轴的设计参数•材料:圆钢棒材•直径:10mm•长度:100mm•阶梯高度:5mm•阶梯数量:4个2.2 阶梯轴的CAD图形2.3 阶梯轴的加工路线•①:直径加工(10mm)•②:端面面铣削•③:上小径面铣削•④:过渡面铣削1•⑤:上阶梯面铣削•⑥:过渡面铣削2•⑦:下阶梯面铣削•⑧:下小径面铣削•⑨:倒角三、数控车阶梯轴程序编制3.1 G-code编写规范G-code是数控编程语言的一种,它是一种基于ASCII码的简单且通用的编程语言。
在数控车加工阶梯轴的程序编制中,我们需要规范化地编写G-code,以确保程序能够正确执行。
以下是G-code编写的常用规范:•每行不超过80个字符,以大写字母开头。
•数值统一使用绝对值模式。
•插补方式使用G01、G02、G03等。
•转速、进给速度、工具槽号计划时要使用变量,不要使用常量。
•在程序的起始位置加入T、S、F等代码,分别表示刀具、主轴转速、进给速度。
•在程序开头应该有G90和G54,分别表示绝对模式、坐标系的选择。
3.2 程序编制过程3.2.1 直径加工(10mm)首先,我们需要使用G00命令进行快速定位,然后使用G01命令进行慢速切割加工。
这个步骤是阶梯轴的第一步,也是整个加工过程中最简单的一步。
阶梯轴加工工艺设计毕业论文

G00 G97 S500 Z50.0;
切换工件转速,线速度500r/min
G28 U0 W0 T0 M05;
N2;
工序(二)外圆粗加工
G00 S400 T0202 M04 F0.25;
X67.0 Z1.0;
刀具定位至粗车循环点
G71 U2.0 R0.5;
G71 P10 Q11 U0.4 W0.1;
X67.0 Z1.0;
刀具定位至精车循环点
G96 S150;
G70 P10 Q11;
G00 G97 S600 X100.0;
G28 U0 W0 T0 M05;
N4;
工序(四)切槽加工
GOO S300 T0606 M04 F0.05;
X31.0 Z-29.0;
G01 X26.0;
G01 X31 F0.2;
1.选择夹具
车削工序需要用三爪自定心卡盘
2.对刀点的选择
对刀点就是刀具相对工件运动的起点。在编程时不管实际是刀具相 对工件移动,还是工件相对刀具移动,都是把工件看作静止,而刀具在运 动。 (0. 0)
六、工件基准的分析
1.选择粗基准:φ60的外圆面和φ60的端面
选择理由:①余量均匀原则;
②保证不加工面位置正确的原则;
N10 G00 G42 X0;
G01 Z0;
G03 X20.0 Z-10.0 R10.0;
G01 Z-15.0;
X30.0;
Z-46.0 R3.0;
X40.0;
Z-66.0;
X61.0;
N11 G01 G40 X65.0;
G28 U0 W0 T0 M05;
N3;
工序(三)外圆精加工
G00 S600 T0404 M04 F0.1;
阶梯轴加工工艺过程

阶梯轴加工工艺过程引言阶梯轴在机械工程中起着重要的作用,广泛应用于各种工业领域。
阶梯轴加工工艺过程是指通过一系列的工艺步骤将原料加工成阶梯状的轴,以满足设计要求。
本文将详细介绍阶梯轴加工工艺过程的各个环节,包括材料选择、加工工艺优化、精确测量等。
材料选择在阶梯轴加工工艺过程中,材料选择是非常重要的一步。
材料的性能将直接影响最终产品的质量和使用寿命。
常用的阶梯轴材料包括碳钢、合金钢、不锈钢等。
在选择材料时,需要考虑以下几个方面:1.强度要求:根据设计要求确定所需的材料强度,以确保阶梯轴能够承受预期的载荷。
2.耐磨性:阶梯轴通常会接触到摩擦面,因此需要选择具有良好耐磨性的材料,以延长产品的使用寿命。
3.加工性能:材料的加工性能也是选择的重要考虑因素之一。
需要选择易于切削加工和热处理的材料,以便进行后续工艺步骤。
加工工艺优化加工工艺优化是确保阶梯轴加工质量和效率的关键环节。
通过优化加工工艺,可以减少加工时间、降低成本,提高产品的质量。
以下是一些常用的加工工艺优化方法:1.刀具选择:根据阶梯轴的设计要求和材料特性,选择合适的刀具进行加工。
选用合适的刀具可以降低切削力和切削温度,减少刀具磨损。
2.加工路径规划:通过合理规划加工路径,减少刀具空走时间和重复移动,提高加工效率。
合理的加工路径还能够减少切削震动,提高加工精度。
3.切削参数设置:根据不同材料的性质和加工要求,设置合适的切削参数,如切削速度、进给量和切削深度等。
合适的切削参数可以减少加工时间,并保证加工质量。
4.冷却润滑剂的使用:在加工过程中适当使用冷却润滑剂,可以降低切削温度,减少切削力和切削热,延长刀具寿命。
精确测量精确测量是保证阶梯轴加工质量的关键环节。
通过精确测量,可以确保产品尺寸和几何形状的准确性。
以下是一些常用的精确测量方法:1.比较测量:使用游标卡尺、千分尺等工具进行尺寸的比较测量。
将测量结果与设计要求进行比较,判断是否符合要求。
2.CMM测量:使用三坐标测量机进行精确测量。
《台阶轴车削加工》课件

切削深度的选择
切削深度
根据台阶轴的直径、材质和加工要求等因素 综合考虑,选择合适的切削深度。切削深度 过小可能导致加工效率低下,切削深度过大 则可能导致刀具磨损和工件表面质量下降。
参考切深范围
根据实际加工需求和刀具性能,确定切削深 度的参考范围,如0.1-0.5毫米。
05
台阶轴车削加工质量检测与控制
质量检测方法与工具
检测工具
卡尺、千分尺、百分表、千分表等测量工具用于测量台阶轴的尺寸、形位公差等参数。
检测方法
采用直接测量法、比较测量法、间接测量法等多种方法进行检测,确保测量结果的准确性和可靠性。
质量控制措施与改进
提高机床精度
定期对机床进行维护和保养, 确保机床精度和稳定性。
持续改进工艺
不断优化工艺参数,提高加工 效率和产品质量。
主偏角和副偏角
影响切削刃工作长度、切削深度和 切削宽度,从而影响切削力、切削热 和表面粗糙度。
刃倾角
控制切屑流向,影响切削刃的锋利 程度和受力方向。
车刀的刃磨与维护
刃磨
定期对车刀进行刃磨,以保持其锋利的切削 刃和合适的几何参数。
维护
使用专用的润滑剂和冷却液,保持车刀清洁 ,避免与坚硬物质接触以防损坏。
《台阶轴车削加工》PPT课件
目 录
• 台阶轴车削加工简介 • 台阶轴车削加工设备 • 台阶轴车削加工刀具 • 台阶轴车削加工工艺参数 • 台阶轴车削加工质量检测与控制 • 台阶轴车削加工实例分析
01
台阶轴车削加工简介
台阶轴车削加工的定义
台阶轴车削加工是一种机械加工方法 ,主要用于生产具有阶梯形状的轴类 零件。
03
台阶轴车削加工刀具
车刀的种类与用途
阶梯轴加工讲解课件
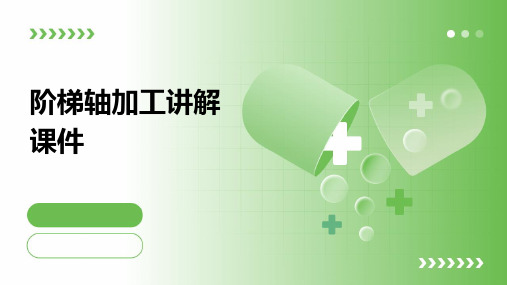
实例二:电机转子阶梯轴加工
总结词
高效率、高精度
详细描述
电机转子阶梯轴加工需要高效率和高精度的加工设备,以确保阶梯轴的尺寸精 度和形位公差。同时,由于电机转子的转速高,阶梯轴的平衡性和稳定性也需 要特别关注。
实例三:减速器阶梯轴加工
总结词
大批量、高效率
详细描述
减速器阶梯轴加工通常是大批量生产,需要高效率的加工设备和工艺流程。为了满足市 场需求,需要不断提高加工精度和生产效率,同时还需要关注阶梯轴的表面质量和耐腐
总结词
阶梯轴加工常用的材料包括碳钢、合金钢、不锈钢和有色金属等。
详细描述
碳钢和合金钢具有较好的机械性能和加工性能,是阶梯轴的主要加工材料。不锈钢具有较好的耐腐蚀性,适用于 在腐蚀环境下工作的阶梯轴。有色金属如铜、铝等则具有较轻的重量和良好的导热性能,适用于特定场合的阶梯 轴。
02
阶梯轴加工技术
车削技术
表面粗糙度检测
表面粗糙度检测是衡量阶梯轴表面质量的重要 指标,主要检测阶梯轴表面的粗糙程度是否符 合设计要求。
常用的检测方法有光干涉法、触针法等,这些 方法能够通过仪器自动测量阶梯轴表面的粗糙 度,并将结果以数值形式显示出来。
表面粗糙度对阶梯轴的耐磨性、抗疲劳强度等 机械性能有重要影响,因此需要严格控制其检 测质量。
解决方案:为提高表面质量,可以采取以下措施
详细描述:在加工过程中,可能由于切削液使用不当、 刀具磨损或冷却不充分等原因,导致阶梯轴表面质量不 佳。
1. 使用合适的切削液,保持切削液的清洁和浓度。
2. 定期检查和更换刀具,确保刀具锋利。
3. 控制切削参数,如切削速度、进给量和切深等。
形位公差超差问题及解决方案
磨削技术适用于加工高精度、高 质量的阶梯轴,如精密传动轴或
阶梯轴零件加工工艺设计

阶梯轴零件加工工艺设计阶梯轴是一种特殊形状的轴类零件,具有不同直径的多个台阶。
其加工工艺设计是确保零件质量、提高生产效率的重要环节。
下面将介绍阶梯轴零件加工工艺设计的一般步骤和注意事项。
一、阶梯轴零件加工工艺设计步骤:1.工艺分析:对零件的形状、尺寸、材料进行分析,确定工艺方案的基本要求。
2.切削工艺设计:选定切削工艺,包括车削、镗削、铣削、磨削等工艺。
根据零件的形状、要求等进行选择,并确定工艺的刀具参数、切削速度等。
3.工序分解:将整个加工过程按照不同的工序进行分解,确定每个工序的加工内容和工具。
4.切削参数的选定:根据刀具材料、工件材料、切削速度等,选定适当的切削参数。
包括进给速度、主轴转速、切削深度等。
5.夹具设计:根据零件的形状和加工要求进行夹具设计,确保工件夹紧可靠、加工精度高。
6.检验方法设计:确定合适的检验方法和测量工具,确保零件加工的精度。
7.工艺文件编制:根据以上步骤编制工艺文件,包括工艺卡、工艺路线图、加工刀具清单等。
二、阶梯轴零件加工工艺设计的注意事项:1.确保加工精度:阶梯轴是一个复杂的零件,各个台阶之间的尺寸差异要求较高。
在设计加工工艺时,要注意选用合适的切削工艺和刀具,确保加工精度。
2.避免变形和裂纹:由于阶梯轴零件的形状特殊,易产生变形和裂纹。
在工艺设计中,要合理控制切削参数,避免过大的切削力和热量造成变形和裂纹。
3.确保工艺稳定性:阶梯轴零件的切削过程比较复杂,容易产生工艺不稳定现象,如振动、共振等。
在工艺设计中,要选择合适的切削速度和进给速度,避免产生不稳定。
4.合理选择刀具:阶梯轴零件的加工比较复杂,需要使用多种刀具进行加工。
在选择刀具时,要考虑刀具的材料、刃型、刃数等因素,以保证加工质量和效率。
5.合理设计夹具:阶梯轴零件的形状复杂,要确保工件在加工过程中的位置固定,不产生松动和偏移。
在夹具设计中,要考虑到工艺要求和工件形状,选择合适的夹具形式。
- 1、下载文档前请自行甄别文档内容的完整性,平台不提供额外的编辑、内容补充、找答案等附加服务。
- 2、"仅部分预览"的文档,不可在线预览部分如存在完整性等问题,可反馈申请退款(可完整预览的文档不适用该条件!)。
- 3、如文档侵犯您的权益,请联系客服反馈,我们会尽快为您处理(人工客服工作时间:9:00-18:30)。
轴类零件的定位基面,最常用的是两中心孔。因为轴类零件各外圆表面、螺纹表面的同轴度及端面对轴线的垂直度是相互位置精度的主要项目,而这些表面的设计基准一般都是轴的中心线,采用两中心孔定位就能符合基准重合原则。而且由于多数工序都采用中心孔作为定位基面,能最大限度地加工出多个外圆和端面,这也符合基准统一原则。
但下列情况不能用两中心孔作为定位基面:
(1)粗加工外圆时,为提高工件刚度,则采用轴外圆表面为定位基面,或以外圆和中心孔同作定位基面,即一夹一顶。
(2)当轴为通孔零件时,在加工过程中,作为定位基面的中心孔因钻出通孔而消失。为了在通孔加工后还能用中心孔作为定位基面,工艺上常采用三种方法。
①当中心通孔直径较小时,可直接在孔口倒出宽度不大于2mm的60o内锥面来代替中心孔;
4.热处理工序的安排
该轴需进行调质处理。它应放在粗加工后,半精加工前进行。如采用锻件毛坯,必须首先安排退火或正火处理。该轴毛坯为热轧钢,可不必进行正火处理。
5.加工顺序安排
除了应遵循加工顺序安排的一般原则,如先粗后精、先主后次等,先加工大直径外圆,然后再加工小直径外圆,以免一开始就降低了工件的刚度。
一、阶梯轴加工工艺过程分析
图6—34为减速箱传动轴工作图样。表6—13为该轴加工工艺过程。生产批量为小批生产。材料为45热轧圆钢。零件需调质。
(一)结构及技术条件分析
该轴为没有中心通孔的多阶梯轴。根据该零件工作图,其轴颈M、N,外圆P,Q及轴肩G、H、I有较高的尺寸精度和形状位置精度,并有较小的表面粗糙度值,该轴有调质热处理要求。
(3)轴上的螺纹一般有较高的精度,如安排在局部淬火之前进行加工,则淬火后产生的变形会影响螺纹的精度。因此螺纹加工宜安排在工件局部淬火之后进行。
(2)轴上的花键、键槽等表面的加工应在外圆精车或粗磨之后,精磨外圆之前。
轴上矩形花键的加工,通常采用铣削和磨削加工,产量大时常用花键滚刀在花键铣床上加工。以外径定心的花键轴,通常只磨削外径,而内径铣出后不必进行磨削,但如经过淬火而使花键扭曲变形过大时,也要对侧面进行磨削加工。以内径定心的花键,其内径和键侧均需进行磨削加工。
②当轴有圆柱孔时,可采用图6—35a所示的锥堵,取1∶500锥度;当轴孔锥度较小时,取锥堵锥度与工件两端定位孔锥度相同;
③当轴通孔的锥度较大时,可采用带锥堵的心轴,简称锥堵心轴,如图6—35b所示。
使用锥堵或锥堵心轴时应注意,一般中途不得更换或拆卸,直到精加工完各处加工面,不再使用中心孔时方能拆卸。
(二)加工工艺过程分析
1.确定主要表面加工方法和加工方案。
传动轴大多是回转表面,主要是采用车削和外圆磨削。由于该轴主要表面M,N,P,Q的公差等级较高(IT6),表面粗糙度值较小(Ra0.8μm),最终加工应采用磨削。其加工方案可参考表3-14。
2.划分加工阶段
该轴加工划分为三个加工阶段,即粗车(粗车外圆、钻中心孔),半精车(半精车各处外圆、台肩和修研中心孔等),粗精磨各处外圆。各加工阶段大致以热处理为界。