典型轴类零件加工工艺标准规范标准分析
轴类零件加工及工艺分析

内江职业技术学院序言数控加工是机械制造中的先进的加工技术是一种高效率,高精度与高柔性特色的自动加工方法,数控加工技术可有效解决复杂、精细、小批多变部件的加工问题,充足适应了现代化生产的需要,制造自动化是先进制造技术的重要构成部分,其核心技术是数控技术,数控技术是综共计算机、自动技术、自动检测及精细机械等高新技术的产物,它的出现及所带来的巨大利益,已惹起了世界各国技术与工业界的广泛重视,目前,国内数控机床使用愈来愈普及,怎样提高数控加工技术水平已成为事不宜迟,跟着数控加工的日趋普及,愈来愈多的数控机床用户感觉,数控加工工艺掌握的水平是限制手工编程与 CAD/CAM 集成化自动编程质量的重点要素。
数控加工工艺是数控编程与操作的基础,合理的工艺是保证数控加工质量发挥数控机床的前提条件,从数控加工的适用角度出发,以数控加工的实质生产为基础,以掌握数控加工工艺为目标,在介绍数控加工切削基础,数控机床刀具的采纳,数控加工的定位与装夹以及数控加工工艺基础等基本知识的基础上,剖析了数控车削的加工工艺。
I内江职业技术学院目序言第一章纲要⋯⋯⋯⋯⋯⋯⋯⋯⋯⋯⋯⋯⋯⋯⋯⋯⋯. 1第一目及目的⋯⋯⋯⋯⋯⋯⋯⋯⋯⋯⋯⋯⋯⋯⋯ 1 第二用件⋯⋯⋯⋯⋯⋯⋯⋯⋯⋯⋯⋯⋯⋯⋯⋯.1 第二章体⋯⋯⋯⋯⋯⋯⋯⋯⋯⋯⋯⋯⋯⋯⋯⋯. 2 第一CAXA 平面的制⋯⋯⋯⋯⋯⋯⋯⋯⋯⋯⋯⋯⋯ .2第二部件体的结构⋯⋯⋯⋯⋯⋯⋯⋯⋯⋯⋯⋯⋯⋯ ..4 第三章工剖析⋯⋯⋯⋯⋯⋯⋯⋯⋯⋯⋯⋯⋯⋯⋯⋯. 7 第一部件工剖析⋯⋯⋯⋯⋯⋯⋯⋯⋯⋯⋯⋯⋯⋯⋯.. 8 第二刀具的⋯⋯⋯⋯⋯⋯⋯⋯⋯⋯⋯⋯⋯⋯⋯⋯.. 9 第三刀具卡片⋯⋯⋯⋯⋯⋯⋯⋯⋯⋯⋯⋯⋯⋯⋯⋯⋯..10 第四确定工件的定位与具方案⋯⋯⋯⋯⋯⋯⋯⋯⋯..10 第五确定走刀序和路⋯⋯⋯⋯⋯⋯⋯⋯⋯⋯⋯⋯..11 第六切削用量的⋯⋯⋯⋯⋯⋯⋯⋯⋯⋯⋯⋯⋯⋯..15 第七数控加工工文件的填写⋯⋯⋯⋯⋯⋯⋯⋯⋯⋯ ..16第八保加工精度的方法⋯⋯⋯⋯⋯⋯⋯⋯⋯⋯⋯⋯⋯ 17第四章数控加工程序⋯⋯⋯⋯⋯⋯⋯⋯⋯⋯⋯⋯⋯⋯18 第五章部件仿真加工⋯⋯⋯⋯⋯⋯⋯⋯⋯⋯⋯⋯⋯⋯23 第一仿真件介⋯⋯⋯⋯⋯⋯⋯⋯⋯⋯⋯⋯⋯⋯⋯ . 23第二仿真加工程⋯⋯⋯⋯⋯⋯⋯⋯⋯⋯⋯⋯⋯⋯⋯25⋯⋯⋯⋯⋯⋯⋯⋯⋯⋯⋯⋯⋯⋯⋯⋯⋯⋯⋯⋯⋯⋯⋯⋯30II参照文件⋯⋯⋯⋯⋯⋯⋯⋯⋯⋯⋯⋯⋯⋯⋯⋯.. 31III纲要:本次设计主假如对数控加工工艺进行剖析与详细部件图的加工,第一对数控加工技术进行了简单的介绍,而后依据部件图进行数控加工剖析。
轴类零件加工工艺规程设计

三、零件的结构工艺性好差对比实例
三、零件的结构工艺性好差对比实例
三、零件的结构工艺性好差对比实例
三、零件的结构工艺性好差对比实例
三、零件的结构工艺性好差对比实例
三、零件的结构工艺性好差对比实例
2、工艺规程的作用:
1)是指导生产的主要技术文件。 2)是生产组织和管理工作的基本依据。 3)是新建和扩建工厂的基本资料。
五、机械加工工 艺规程
3、工艺规程的形式: 机械加工工艺规程主
要有机械加工工艺过程卡 片和机械加工工序卡片两 类。
机械加工工艺过程卡 片的格式如右表。
过程卡片适合于所有 零件。
五、机械加工工艺规程
6、机械加工工艺规程制订的步骤:
1)看零件图和产品装配图,对被加工零件进行工艺分析 2)确定毛坯种类 3)拟定零件加工工艺路线 4)工序设计:
确定各工序的加工余量,计算工序尺寸及公差。确定各工序的技术要求 及检验方法;
选择各工序所用机床设备、工艺装备(含刀具、夹具、量具、辅具等)、 切削液种类。
课后作业:
1、P76 1、2 2、完成工作页中的作业。
▪
每一次的加油,每一次的努力都是为 了下一 次更好 的自己 。20.12.820.12.8Tues day, December 08, 2020
▪
天生我材必有用,千金散尽还复来。08:15:3008:15:3008:1512/8/2020 8:15:30 AM
三、机械加工工艺过程及其组成
1、工序: 工序是指一个(或一组)工人在一个工作地点(如一
台机床或一个钳工台),对一个(或同时对几个)工件连 续完成的那部分工艺过程。
轴类零件机械加工工艺规程及其设计

轴类零件机械加工工艺规程及其设计轴类零件是机械制造中广泛应用的零部件之一,其机械加工工艺规程的设计对于产品的质量和生产效率具有重要的意义。
本文将从轴类零件的加工工艺特点、机械加工工艺规程的设计方法、常见加工工艺及其应用、及加工工艺中的注意事项等方面对轴类零件机械加工工艺规程及其设计进行详细介绍。
一、轴类零件的加工工艺特点轴类零件在机械加工中属于细长杆状物的一类,其加工过程中需要考虑材料的变形、热影响、残余应力等问题,同时也需要考虑其使用过程中所承受的载荷作用,因此对于轴类零件的制造要求十分严格。
其加工工艺特点主要包括以下几点:1.加工工艺要求高精度:轴类零件的尺寸精度要求高,常见的加工公差在0.01mm以下,加工过程中需要采用高精度的机床和刀具、合理的加工参数,严格控制加工误差。
2.加工难度大:由于轴类零件的材料变形大、容易产生撞刀和毛刺,因此在加工过程中需要采用特殊的切削方法和切削工艺,如采用高速切削、切削流线型、刀具较小的切槽等。
3.轴向精度要求高:轴类零件是与轴心对称的,在加工过程中需要控制好轴向误差,以保证其在使用时能够平稳转动。
二、机械加工工艺规程的设计方法机械加工工艺规程的设计是制定出一套完整的工艺措施,通过对产品加工过程中各种工艺因素的控制,实现产品尺寸、结构、性能等方面的要求。
机械加工工艺规程的设计方法主要包括以下几点:1.确定加工工艺目标:在制定工艺规程前,需要明确产品的要求,包括加工精度、表面光洁度、机械性能等方面。
2.制定加工工艺流程:制定加工工艺流程是整个工艺规程中最为关键的一步,需要根据产品的结构和要求,确定各个加工步骤的顺序和方法。
3.确定加工参数:加工参数是指加工过程中需要调整的各种参数,包括切削速度、切削深度、切削力等,这些参数的调整需要根据实际情况进行。
4.选择合适的加工设备和刀具:不同的加工设备和刀具适用于不同的加工需求,因此在制定工艺规程时需要根据产品要求选择合适的加工设备和刀具。
典型零件加工与工艺分析
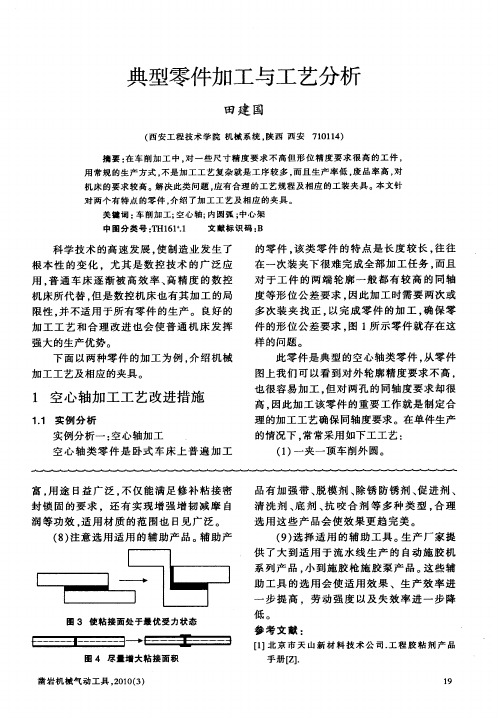
处。
( ) 连 杆 时 , 须 保 证 轴 线 与 工 件 轴 2 装 必
图 3
线平 行 。 ( ) 板 导 轨 要 与工 件 轴 线 平 行 , 的 3 托 它 摇 动用 于控 制 每次 的切 削 深度 。
如果 在 车床 上 安 装一 个 支 点 . 用 一个 再
【】 陆 英 . T rz 与 技 能 训 练 【 . 动 与 社 会 保 障 1孟 车 J劳 】
的零 件 。 类 零 件 的特 点 是 长 度 较 长 , 往 该 往
在一 次 装夹 下 很 难 完 成 全部 加 工任 务 , 而且
对 于 工 件 的 两 端 轮廓 一般 都 有 较 高 的 同轴 度 等 形 位公 差 要 求 , 因此 加 工 时需 要 两 次或 多 次装 夹 找 正 , 完 成 零 件 的加 工 , 保 零 以 确
V
● _ _
8 0 + :
8o o .
8 ( 0 二 三 o
图 1
◎ . A O2 0
( ) 四爪 , 软爪 夹 持一 端 , 2用 或 一端 搭 中
心架 , 以外 圆作 为 基 准 , 正 后 粗 精 加 工 一 找
端 内孔 。
床精度要求高 、 正麻烦 。 找 很难 能保 证 产 品
2 0
① 因两支撑架在第一次调整后 , 后续加
工过 程 中不 再调 整 。 以加 工 时能始 终 保 证 所
凿 岩 机械 气 动 工 具 .0 0 3 21()
两 中心 架 三爪 中心 在 同一 轴 线 上 , 决 了调 解 头 时存在不 同心 的问题 , 保证 了 同轴度 要求 。
轴类零件的加工工艺及技术要求
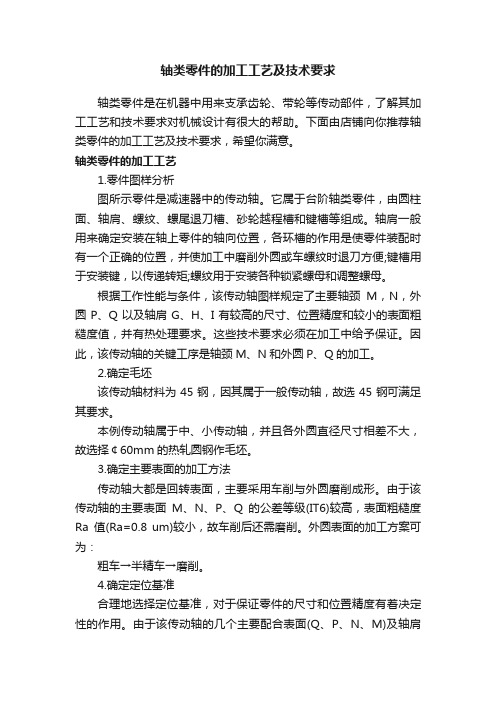
轴类零件的加工工艺及技术要求轴类零件是在机器中用来支承齿轮、带轮等传动部件,了解其加工工艺和技术要求对机械设计有很大的帮助。
下面由店铺向你推荐轴类零件的加工工艺及技术要求,希望你满意。
轴类零件的加工工艺1.零件图样分析图所示零件是减速器中的传动轴。
它属于台阶轴类零件,由圆柱面、轴肩、螺纹、螺尾退刀槽、砂轮越程槽和键槽等组成。
轴肩一般用来确定安装在轴上零件的轴向位置,各环槽的作用是使零件装配时有一个正确的位置,并使加工中磨削外圆或车螺纹时退刀方便;键槽用于安装键,以传递转矩;螺纹用于安装各种锁紧螺母和调整螺母。
根据工作性能与条件,该传动轴图样规定了主要轴颈M,N,外圆P、Q以及轴肩G、H、I有较高的尺寸、位置精度和较小的表面粗糙度值,并有热处理要求。
这些技术要求必须在加工中给予保证。
因此,该传动轴的关键工序是轴颈M、N和外圆P、Q的加工。
2.确定毛坯该传动轴材料为45钢,因其属于一般传动轴,故选45钢可满足其要求。
本例传动轴属于中、小传动轴,并且各外圆直径尺寸相差不大,故选择¢60mm的热轧圆钢作毛坯。
3.确定主要表面的加工方法传动轴大都是回转表面,主要采用车削与外圆磨削成形。
由于该传动轴的主要表面M、N、P、Q的公差等级(IT6)较高,表面粗糙度Ra值(Ra=0.8 um)较小,故车削后还需磨削。
外圆表面的加工方案可为:粗车→半精车→磨削。
4.确定定位基准合理地选择定位基准,对于保证零件的尺寸和位置精度有着决定性的作用。
由于该传动轴的几个主要配合表面(Q、P、N、M)及轴肩面(H、G)对基准轴线A-B均有径向圆跳动和端面圆跳动的要求,它又是实心轴,所以应选择两端中心孔为基准,采用双顶尖装夹方法,以保证零件的技术要求。
粗基准采用热轧圆钢的毛坯外圆。
中心孔加工采用三爪自定心卡盘装夹热轧圆钢的毛坯外圆,车端面、钻中心孔。
但必须注意,一般不能用毛坯外圆装夹两次钻两端中心孔,而应该以毛坯外圆作粗基准,先加工一个端面,钻中心孔,车出一端外圆;然后以已车过的外圆作基准,用三爪自定心卡盘装夹(有时在上工步已车外圆处搭中心架),车另一端面,钻中心孔。
典型零件的机械加工工艺分析.doc

第4章典型零件的机械加工工艺分析本章要点本章介绍典型零件的机械加工工艺规程制订过程及分析,主要内容如下:1.介绍机械加工工艺规程制订的原则与步骤。
2.以轴类、箱体类、拨动杆零件为例,分析零件机械加工工艺规程制订的全过程。
本章要求:通过典型零件机械加工工艺规程制订的分析,能够掌握机械加工工艺规程制订的原则和方法,能制订给定零件的机械加工工艺规程。
§4.1 机械加工工艺规程的制订原则与步骤§4.1.1机械加工工艺规程的制订原则机械加工工艺规程的制订原则是优质、高产、低成本,即在保证产品质量前提下,能尽量提高劳动生产率和降低成本。
在制订工艺规程时应注意以下问题:1.技术上的先进性在制订机械加工工艺规程时,应在充分利用本企业现有生产条件的基础上,尽可能采用国内、外先进工艺技术和经验,并保证良好的劳动条件。
2.经济上的合理性在规定的生产纲领和生产批量下,可能会出现几种能保证零件技术要求的工艺方案,此时应通过核算或相互对比,一般要求工艺成本最低。
充分利用现有生产条件,少花钱、多办事。
3.有良好的劳动条件在制订工艺方案上要注意采取机械化或自动化的措施,尽量减轻工人的劳动强度,保障生产安全、创造良好、文明的劳动条件。
由于工艺规程是直接指导生产和操作的重要技术文件,所以工艺规程还应正确、完整、统一和清晰。
所用术语、符号、计量单位、编号都要符合相应标准。
必须可靠地保证零件图上技术要求的实现。
在制订机械加工工艺规程时,如果发现零件图某一技术要求规定得不适当,只能向有关部门提出建议,不得擅自修改零件图或不按零件图去做。
§4.1.2 制订机械加工工艺规程的内容和步骤1.计算零件年生产纲领,确定生产类型。
2.对零件进行工艺分析在对零件的加工工艺规程进行制订之前,应首先对零件进行工艺分析。
其主要内容包括:(1)分析零件的作用及零件图上的技术要求。
(2)分析零件主要加工表面的尺寸、形状及位置精度、表面粗糙度以及设计基准等;(3)分析零件的材质、热处理及机械加工的工艺性。
典型轴类零件数控加工工艺分析
典型轴类零件数控加工工艺分析摘要: 随着数控技术的不断发展和应用领域的扩大,数控技术的应用给传统制造业带来了革命性的变化,因为效率、质量是先进制造业的主体。
高速、高精加工技术可极大地提升效率,提高产品的品质,缩短生产周期和提高市场竞争能力。
而对于数控加工,无论是手工编程还是自动编程,在编程前都要对所加工的零件进行工艺分析,制定合理的加工方案,选择合适的道具,确定科学的切削用量,对一些工艺问题(如对刀点、加工路线等)也需做一些分析处理。
并在加工过程掌握控制精度的方法,才能加工出合格的产品。
关键词: 工艺分析;加工方案;加工路线;控制尺寸一、零件加工工艺分析图1-1 典型轴类零件图1、零件技术要求(1)锐角倒钝;(2)未注形位公差应符合GB1184-80的要求;(3)未注长度尺寸运供需偏差±0.2mm;(4)不准使用锉刀、纱布进行修磨工件表面。
该零件由圆柱、圆弧、圆锥、槽、螺纹、内孔等表面组成。
选用毛培为45#钢,Φ50×130m m,无热处理和硬度要求。
2、确定加工方法加工方法的选择原则是保证加工表面的加工精度和表面粗糙度的要求。
由于获得同一级精度及表面粗糙度的加工方法一般有许多,因而在实际选择时,要结合零件的形状、尺寸大小和形位公差要求等全面考虑。
考虑加工的效率和加工的经济性,最理想的加工方式为车削,采用数控车床。
3、分析图样尺寸考虑到采用数控车床,在图样中有几个点的坐标值要加以确定如图1-2所示:需要确定的坐标有a点、b点、c点。
在确定三点坐标之前,先确定工件坐标系。
暂时以工件的右端面回转中心为工件坐标系的坐标原点O。
A点的计算 z值-13,x值23(半径值)B点的计算 z值(13+L1),x值13L1值的计算:462 -132 = L1 2 L1=18.973B点z值=(13+L1)=13+18.9763=31.973B点坐标Z-31.973 , X13C点的计算Z值-42, X值(23-L2)L2值的计算:cos10。
典型零件加工工艺分析
套筒类零件的安装
§6.2.3 套类零件孔的加工方法
套类零件的孔加工方法常用的有:钻孔、扩孔、 镗孔、车孔、铰孔、磨孔、拉孔、珩孔、研磨孔 及孔表面滚压加工。其中钻孔、扩孔、镗孔、车 孔常作为粗加工与半精加工;而铰孔、磨孔、拉 孔、珩孔、研磨孔及孔表面滚压加工作为精加工 方法。
1. 磨孔 内圆磨削具有以下特点:
(1) 孔与外圆的精度要求。 (2) 几何形状精度要求。 (3) 相互位置精度要求。
3、套筒类零件的材料及毛坯
材料 套类零件一般用钢、铸铁、青铜、黄铜制成。有 些滑动轴承可选用双金属结构,对一些强度和硬度要求 较高的套类零件(如镗床主轴套筒、伺服阀套),可选用 优质合金钢(38CrMoALA、18CrNiWA)。
深孔钻削
深孔镗削
浮动镗孔
深孔加工
精细镗孔 珩磨内孔 内孔研磨 滚压孔
精加工
§6.3 齿轮加工
§6.3.1 概述
齿轮的功用
圆柱齿轮是机械传动中的重要零件,其功用是按规 定的传动比传递运动和动力。它具有传动比准确、 传动力大、效率高、结构紧凑、可靠性好等优点, 广泛应用于各种现代机器和仪表中。
圆柱齿轮的结构与分类
• 圆柱齿轮可以看成由齿圈和轮体两部分所构成,
在轮圈上切出直齿、斜齿或人字齿(图6-9)等就 形成了齿轮。 • 按齿形曲线性质可分为渐开线、摆线、鼓形和圆 弧等。 • 齿轮的结构分类常以轮体结构的形状为依据,即 可分为单联齿轮、双联齿轮、三联齿轮、连轴齿轮、 内齿轮、装配齿轮、齿条及扇形齿轮等(图6-10)
图c) • 4 以顶尖孔安装——顶尖孔定心、定位。图d)
图6-12 齿形加工安装实例
• 二 齿坯的加工方式 • 1 内孔安装 控制端面跳动与内径公差。
轴类零件加工工艺
• 一、箱体零件的功用、结构及技术要求
1.功用、结构
功用:将机器中有关部件的轴、套、齿轮等相关零件连接成 一个整体,使这些零件保持正确的相对位置,并按一定的传动关 系协调地工作。
结构:形状复杂,壁薄且不均匀,内部呈腔形,既有精度要求 较高的孔系和平面,也有许多精度要求较低的紧固孔。
a)
b)
a)齿轮油泵箱体 b)齿轮减速箱箱体
Hale Waihona Puke 2.防止套类零件变形的工艺措施套类零件一般都存在壁较薄、径向刚度较差、容易变形等缺点。
套类零件变形的原因及工艺措施
导致变形的因素
工艺措施
夹紧力
(1)使夹紧力均匀分布,如图a所示 (2)变径向夹紧为轴向夹紧,如图b所示 (3)增加套筒毛坯的刚度,如图c所示
外力
切削力
重力 离心力
(1)增大刀具的主偏角 (2)内、外表面同时加工,如图c所示 (3)粗、精加工分开进行 增加辅助支承 配重
套类零件的毛坯类型与所用材料、结构形状和尺寸大小有关, 常采用型材、锻件或铸件。
毛坯内孔直径小于φ20mm时大多选用棒料,孔径较大、长度 较长的零件常用无缝钢管或带孔的铸、锻件。
• 三、套类零件的加工工艺分析
1.保证相互位置精度的工艺措施
轴承套毛坯采用“4件合一”的方 式加工:指棒料按四个轴承套零件尺 寸下料,四件同时加工
传动轴是轴类零件中使 用最多、结构最为典型的一 种阶梯轴,所示。该轴为小 批量生产,材料选择45钢, 淬火硬度40~45HRC。试分 析其加工工艺过程。
1.结构分析
主要结构要素有内外圆柱面、螺纹、键槽等,该轴为典型的 阶梯轴结构,有两个支承轴颈。
2.技术要求
两端轴颈的尺寸精度为IT7,表面粗糙度Ra值为0.8μm; 用于安装齿轮的轴颈的尺寸精度主IT7,表面粗糙度Ra值为 1.6μm; 右端轴颈外圆上规定了圆柱度为0.02mm; 左端轴颈外圆上规定了圆柱度为0.02mm; 轴上各配合面对两端轴颈的公共轴线的径向跳动为0.02mm, 可保证齿轮平稳传动。
轴类零件的加工工艺分析与实例
18 外磨 精磨、工件装夹于二顶尖间 M1432A
精磨2-φ30 至尺寸,注意形位公差
19 内磨 工件装在V型夹具中,以1–ф30外圆为基准,精磨莫氏3号内锥孔(卸堵,以2–ф30js5外圆定位),涂色检查接触面大于80%,注意技术要求“1”“2” MG1432A
4 车 一夹一顶 CA6140
<1> 车M30×1.5–6g左螺纹大径及ф30JS5处至
Φ30
<2> 车φ25至φ25 、长43
<3> 车φ35至φ35
<4> 车砂轮越程槽
5 车 调头,一夹一顶
5.螺纹因淬火后,在车床上无法加工,如先车好螺纹后再淬火,会使螺纹产生变形。因此,螺纹一般不允许淬硬,所以在工件中的螺纹部分的直径和长度上必需留去碳层。对于内螺纹,在孔口也应留出3mm去碳层。
6.为保证中心孔精度,工件中心孔也不允许淬硬,为此,毛坯总长放长6mm。
7.为保证工件外圆的磨削精度,热处理后须安排研磨中心孔的工序,并要求达到较细的表面粗糙度。外圆磨削时,影响工件的圆度主要是由于二顶尖孔的同轴度,及顶尖孔的圆度误差。
14 研 研中心孔Ra0.8
15 外磨 工件装夹于二顶尖间
<1> 精磨φ40及φ35φ25外圆至尺寸
<2> 磨M30×1.5 M30×1.5左螺纹大径至30
<3> 半精磨ф30js5二处至ф30
<3> 锪孔口60°中心孔
<4> 调头套钻套钻孔ф10.5×25(螺纹不改)
<5> 锪60°中心孔,表面精糙度0.8 60°锪钻
- 1、下载文档前请自行甄别文档内容的完整性,平台不提供额外的编辑、内容补充、找答案等附加服务。
- 2、"仅部分预览"的文档,不可在线预览部分如存在完整性等问题,可反馈申请退款(可完整预览的文档不适用该条件!)。
- 3、如文档侵犯您的权益,请联系客服反馈,我们会尽快为您处理(人工客服工作时间:9:00-18:30)。
阶梯轴加工工艺过程分析图6—34为减速箱传动轴工作图样。
表6—13为该轴加工工艺过程。
生产批量为小批生产。
材料为45热轧圆钢。
零件需调质。
(一)结构及技术条件分析该轴为没有中心通孔的多阶梯轴。
根据该零件工作图,其轴颈M、N,外圆P,Q及轴肩G、H、I有较高的尺寸精度和形状位置精度,并有较小的表面粗糙度值,该轴有调质热处理要求。
(二)加工工艺过程分析1.确定主要表面加工方法和加工方案。
传动轴大多是回转表面,主要是采用车削和外圆磨削。
由于该轴主要表面M,N,P,Q的公差等级较高(IT6),表面粗糙度值较小(Ra0.8μm),最终加工应采用磨削。
其加工方案可参考表3-14。
2.划分加工阶段该轴加工划分为三个加工阶段,即粗车(粗车外圆、钻中心孔),半精车(半精车各处外圆、台肩和修研中心孔等),粗精磨各处外圆。
各加工阶段大致以热处理为界。
3.选择定位基准轴类零件的定位基面,最常用的是两中心孔。
因为轴类零件各外圆表面、螺纹表面的同轴度及端面对轴线的垂直度是相互位置精度的主要项目,而这些表面的设计基准一般都是轴的中心线,采用两中心孔定位就能符合基准重合原则。
而且由于多数工序都采用中心孔作为定位基面,能最大限度地加工出多个外圆和端面,这也符合基准统一原则。
但下列情况不能用两中心孔作为定位基面:(1)粗加工外圆时,为提高工件刚度,则采用轴外圆表面为定位基面,或以外圆和中心孔同作定位基面,即一夹一顶。
(2)当轴为通孔零件时,在加工过程中,作为定位基面的中心孔因钻出通孔而消失。
为了在通孔加工后还能用中心孔作为定位基面,工艺上常采用三种方法。
①当中心通孔直径较小时,可直接在孔口倒出宽度不大于2mm的60o内锥面来代替中心孔;②当轴有圆柱孔时,可采用图6—35a所示的锥堵,取1∶500锥度;当轴孔锥度较小时,取锥堵锥度与工件两端定位孔锥度相同;③当轴通孔的锥度较大时,可采用带锥堵的心轴,简称锥堵心轴,如图6—35b所示。
使用锥堵或锥堵心轴时应注意,一般中途不得更换或拆卸,直到精加工完各处加工面,不再使用中心孔时方能拆卸。
4.热处理工序的安排该轴需进行调质处理。
它应放在粗加工后,半精加工前进行。
如采用锻件毛坯,必须首先安排退火或正火处理。
该轴毛坯为热轧钢,可不必进行正火处理。
5.加工顺序安排除了应遵循加工顺序安排的一般原则,如先粗后精、先主后次等,还应注意:(1)外圆表面加工顺序应为,先加工大直径外圆,然后再加工小直径外圆,以免一开始就降低了工件的刚度。
(2)轴上的花键、键槽等表面的加工应在外圆精车或粗磨之后,精磨外圆之前。
轴上矩形花键的加工,通常采用铣削和磨削加工,产量大时常用花键滚刀在花键铣床上加工。
以外径定心的花键轴,通常只磨削外径,而内径铣出后不必进行磨削,但如经过淬火而使花键扭曲变形过大时,也要对侧面进行磨削加工。
以内径定心的花键,其内径和键侧均需进行磨削加工。
(3)轴上的螺纹一般有较高的精度,如安排在局部淬火之前进行加工,则淬火后产生的变形会影响螺纹的精度。
因此螺纹加工宜安排在工件局部淬火之后进行。
二、带轮轴加工工艺过程分析图 6 — 36 为带轮轴工作图样。
带轮轴中的主要技术条件有两项:一为渗碳层深度,应控制在 1.2— 1.5 mm 范围内;二为外圆¢22 f 7 需经渗碳淬火,其硬度为HRC58 ~63 。
可以看出只有¢22 f 7 处需渗碳处理,其余部分均不可渗碳。
零件上不需渗碳的部分,可用加大余量待渗碳后车去渗碳层或在不需渗碳处涂防渗材料。
加工余量应单面略大于渗碳深度,故右端直径取¢25 mm ,单面去碳余量为2.5 mm ,总长两端也应放去渗碳余量各 3 mm 。
在磨外圆前由于已经过淬火工序,两端中心孔在淬火时易产生氧化皮及变形,故增加一道研磨中心孔的工序。
表 6 — 14 为带轮轴的加工工艺过程。
三、细长轴加工工艺特点(一)细长轴车削的工艺特点1 .细长轴刚性很差,车削时装夹不当,很容易因切削力及重力的作用而发生弯曲变形,产生振动,从而影响加工精度和表面粗糙度。
2 .细长轴的热扩散性能差,在切削热作用下,会产生相当大的线膨胀。
如果轴的两端为固定支承,则工件会因伸长而顶弯。
3 .由于轴较长,一次走刀时间长,刀具磨损大,从而影响零件的几何形状精度。
4 .车细长轴时由于使用跟刀架,若支承工件的两个支承块对零件压力不适当,会影响加工精度。
若压力过小或不接触,就不起作用,不能提高零件的刚度;若压力过大,零件被压向车刀,切削深度增加,车出的直径就小,当跟刀架继续移动后,支承块支承在小直径外圆处,支承块与工件脱离,切削力使工件向外让开,切削深度减小,车出的直径变大,以后跟刀架又跟到大直径圆上,又把工件压向车刀,使车出的直径变小,这样连续有规律的变化,就会把细长的工件车成“竹节”形,如图6 — 37 所示。
(二)细长轴的先进车削法——反向走刀车削法图6––38 为反向走刀车削法示意图,这种方法的特点是:1 .细长轴左端缠有一圈钢丝,利用三爪自定心卡盘夹紧,减小接触面积,使工件在卡盘内能自由地调节其位置,避免夹紧时形成弯曲力矩,在切削过程中发生的变形也不会因卡盘夹死而产生内应力。
2 .尾座顶尖改成弹性顶尖,当工件因切削热发生线膨胀伸长时,顶尖能自动后退,可避免热膨胀引起的弯曲变形。
3 .采用三个支承块跟刀架,以提高工件刚性和轴线的稳定性,避免“竹节”形。
4 .改变走刀方向,使床鞍由主轴箱向尾座移动,使工件受拉,不易产生弹性弯曲变形。
轴类零件加工工艺传动轴机械加工工艺实例轴类零件是常见的典型零件之一。
按轴类零件结构形式不同,一般可分为光轴、阶梯轴和异形轴三类;或分为实心轴、空心轴等。
它们在机器中用来支承齿轮、带轮等传动零件,以传递转矩或运动。
台阶轴的加工工艺较为典型,反映了轴类零件加工的大部分内容与基本规律。
下面就以减速箱中的传动轴为例,介绍一般台阶轴的加工工艺。
1.零件图样分析图A-1 传动轴图A-1所示零件是减速器中的传动轴。
它属于台阶轴类零件,由圆柱面、轴肩、螺纹、螺尾退刀槽、砂轮越程槽和键槽等组成。
轴肩一般用来确定安装在轴上零件的轴向位置,各环槽的作用是使零件装配时有一个正确的位置,并使加工中磨削外圆或车螺纹时退刀方便;键槽用于安装键,以传递转矩;螺纹用于安装各种锁紧螺母和调整螺母。
根据工作性能与条件,该传动轴图样(图A-1)规定了主要轴颈M,N,外圆P、Q以及轴肩G、H、I有较高的尺寸、位置精度和较小的表面粗糙度值,并有热处理要求。
这些技术要求必须在加工中给予保证。
因此,该传动轴的关键工序是轴颈M、N和外圆P、Q的加工。
2.确定毛坯该传动轴材料为45钢,因其属于一般传动轴,故选45钢可满足其要求。
本例传动轴属于中、小传动轴,并且各外圆直径尺寸相差不大,故选择¢60mm的热轧圆钢作毛坯。
3.确定主要表面的加工方法传动轴大都是回转表面,主要采用车削与外圆磨削成形。
由于该传动轴的主要表面M、N、P、Q的公差等级(IT6)较高,表面粗糙度Ra值(Ra=0.8 um)较小,故车削后还需磨削。
外圆表面的加工方案(参考表A-3)可为:粗车→半精车→磨削。
4.确定定位基准合理地选择定位基准,对于保证零件的尺寸和位置精度有着决定性的作用。
由于该传动轴的几个主要配合表面(Q、P、N、M)及轴肩面(H、G)对基准轴线A-B均有径向圆跳动和端面圆跳动的要求,它又是实心轴,所以应选择两端中心孔为基准,采用双顶尖装夹方法,以保证零件的技术要求。
粗基准采用热轧圆钢的毛坯外圆。
中心孔加工采用三爪自定心卡盘装夹热轧圆钢的毛坯外圆,车端面、钻中心孔。
但必须注意,一般不能用毛坯外圆装夹两次钻两端中心孔,而应该以毛坯外圆作粗基准,先加工一个端面,钻中心孔,车出一端外圆;然后以已车过的外圆作基准,用三爪自定心卡盘装夹(有时在上工步已车外圆处搭中心架),车另一端面,钻中心孔。
如此加工中心孔,才能保证两中心孔同轴。
5.划分阶段对精度要求较高的零件,其粗、精加工应分开,以保证零件的质量。
该传动轴加工划分为三个阶段:粗车(粗车外圆、钻中心孔等),半精车(半精车各处外圆、台阶和修研中心孔及次要表面等),粗、精磨(粗、精磨各处外圆)。
各阶段划分大致以热处理为界。
6.热处理工序安排轴的热处理要根据其材料和使用要求确定。
对于传动轴,正火、调质和表面淬火用得较多。
该轴要求调质处理,并安排在粗车各外圆之后,半精车各外圆之前。
综合上述分析,传动轴的工艺路线如下:下料→车两端面,钻中心孔→粗车各外圆→调质→修研中心孔→半精车各外圆,车槽,倒角→车螺纹→划键槽加工线→铣键槽→修研中心孔→磨削→检验。
7.加工尺寸和切削用量传动轴磨削余量可取0.5mm,半精车余量可选用1.5mm。
加工尺寸可由此而定,见该轴加工工艺卡的工序内容。
车削用量的选择,单件、小批量生产时,可根据加工情况由工人确定;一般可由《机械加工工艺手册》或《切削用量手册》中选取。
8.拟定工艺过程定位精基准面中心孔应在粗加工之前加工,在调质之后和磨削之前各需安排一次修研中心孔的工序。
调质之后修研中心孔为消除中心孔的热处理变形和氧化皮,磨削之前修研中心孔是为提高定位精基准面的精度和减小锥面的表面粗糙度值。
拟定传动轴的工艺过程时,在考虑主要表面加工的同时,还要考虑次要表面的加工。
在半精加工¢52mm、¢44mm 及M24mm外圆时,应车到图样规定的尺寸,同时加工出各退刀槽、倒角和螺纹;三个键槽应在半精车后以及磨削之前铣削加工出来,这样可保证铣键槽时有较精确的定位基准,又可避免在精磨后铣键槽时破坏已精加工的外圆表面。
在拟定工艺过程时,应考虑检验工序的安排、检查项目及检验方法的确定。
综上所述,所确定的该传动轴加工工艺过程见表A-1。