尿素生产工艺设计
年产20万吨尿素生产工艺设计

尿素是一种重要的氮肥,使用广泛。
设计年产20万吨尿素的生产工艺需要考虑以下几个方面:原料选择、反应工艺、分离工艺以及能耗控制等。
1.原料选择:尿素生产的主要原料是氨气和二氧化碳。
需要考虑原料的供应稳定性和成本优势。
一般来说,可以选择从天然气中制取氢气,然后与氮气反应生成氨气。
另外,可从化肥厂的氨、尿素等副产物中回收再利用。
2.反应工艺:尿素的生产通常采用尿素合成反应,即将氨气和二氧化碳在催化剂的作用下生成尿素。
反应温度一般在140-180℃之间,催化剂常用铁和钴。
反应过程需要对压力、温度、氨气和二氧化碳的流量进行严格控制,以提高反应效率和产量。
3.分离工艺:尿素合成反应生成的产物中包含大量的不纯物质,需要进行分离和纯化。
一般通过蒸发-结晶法进行尿素精制,利用尿素在溶液中的溶解度变化特性进行分离。
分离工艺需要考虑能耗控制和产品质量保证。
4.能耗控制:尿素生产工艺中能耗较高,因此需要采取措施进行能耗控制和能源回收。
可以通过优化反应条件、改进分离工艺、采用废热回收和再利用等措施来降低能耗。
总之,设计年产20万吨尿素的生产工艺需要考虑原料选择、反应工艺、分离工艺以及能耗控制等多个方面。
这些方面的综合考虑将有助于提高生产效率、降低成本,并确保产品质量。
尿素生产原理、工艺流程及工艺指标

尿素生产原理、工艺流程及工艺指标1.生产原理尿素是通过液氨和气体二氧化碳的合成来完成的,在合成塔D201中,氨和二氧化碳反应生成氨基甲酸铵,氨基甲酸铵脱水生成尿素和水,这个过程分两步进行。
第一步:2NH3,CO2 NH2COONH4,Q第二步:NH4COONH2 CO(NH2)2,H2O,Q第一步是放热的快速反应,第二步是微吸热反应,反应速度较慢,它是合成尿素过程中的控制反应。
1、2工艺流程:尿素装置工艺主要包括:CO2压缩和脱氢、液氨升压、合成和气提、循环、蒸发、解吸和水解以及大颗粒造粒等工序。
1、2、1 二氧化碳压缩和脱氢从合成氨装置来的CO2气体,经过CO2液滴分离器与来自空压站的工艺空气混合(空气量为二氧化碳体积4%),进入二氧化碳压缩机。
二氧化碳出压缩机三段进脱硫、脱氢反应器,脱氢反应器内装铂系催化剂,操作温度:入口?150?,出口?200?。
脱氢的目的是防止高压洗涤器可燃气体积聚发生爆炸。
在脱氢反应器中H2被氧化为H2O,脱氢后二氧化碳含氢及其它可燃气体小于50ppm,经脱硫、脱氢后,进入压缩机四段、五段压缩,最终压缩到14.7MPa(绝)进入汽提塔。
二氧化碳压缩机设有中间冷凝器和分离器,二氧化碳压缩机压缩气体设有三个回路,以适应尿素生产负荷的变化,多余的二氧化碳由放空管放空。
2 液氨升压 1、2、液氨来自合成氨装置氨库,压力为2.3 MPa(绝),温度为20?,进入液氨过滤器,经过滤后进入高压氨泵的入口,液氨流量在一定的范围内可以自调,并设有副线以备开停车及倒泵用.主管上装有流量计.液氨经高压氨泵加压到18.34 MPa(绝),高压液氨泵是电动往复式柱塞泵,并带变频调速器,可在20—110%的范围内变化,在总控室有流量记录,从这个记录来判断进入系统的氨量,以维持正常生产时的原料N/C(摩尔比)为2.05:1。
高压液氨送到高压喷射器,作为喷射物料,将高压洗涤器来的甲铵带入高压冷凝器,高压液氨泵前后管线均设有安全阀,以保证装置设备安全。
年产20万吨尿素生产工艺设计
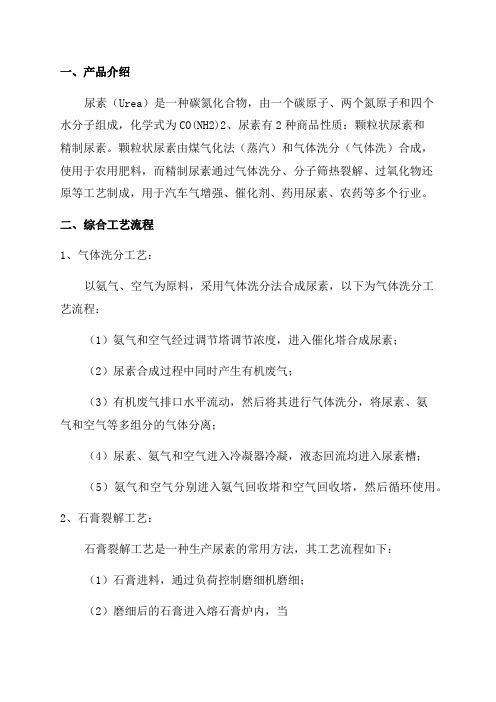
一、产品介绍
尿素(Urea)是一种碳氮化合物,由一个碳原子、两个氮原子和四个
水分子组成,化学式为CO(NH2)2、尿素有2种商品性质:颗粒状尿素和
精制尿素。
颗粒状尿素由煤气化法(蒸汽)和气体洗分(气体洗)合成,
使用于农用肥料,而精制尿素通过气体洗分、分子筛热裂解、过氧化物还
原等工艺制成,用于汽车气增强、催化剂、药用尿素、农药等多个行业。
二、综合工艺流程
1、气体洗分工艺:
以氨气、空气为原料,采用气体洗分法合成尿素,以下为气体洗分工
艺流程:
(1)氨气和空气经过调节塔调节浓度,进入催化塔合成尿素;
(2)尿素合成过程中同时产生有机废气;
(3)有机废气排口水平流动,然后将其进行气体洗分,将尿素、氨
气和空气等多组分的气体分离;
(4)尿素、氨气和空气进入冷凝器冷凝,液态回流均进入尿素槽;
(5)氨气和空气分别进入氨气回收塔和空气回收塔,然后循环使用。
2、石膏裂解工艺:
石膏裂解工艺是一种生产尿素的常用方法,其工艺流程如下:
(1)石膏进料,通过负荷控制磨细机磨细;
(2)磨细后的石膏进入熔石膏炉内,当。
尿素生产工艺设计
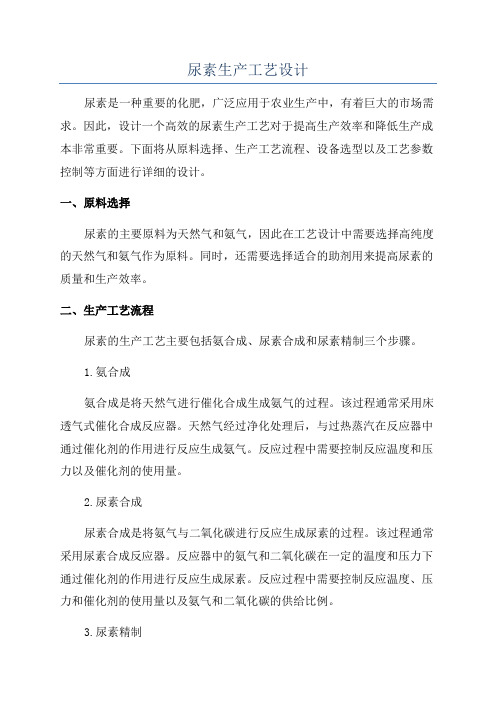
尿素生产工艺设计尿素是一种重要的化肥,广泛应用于农业生产中,有着巨大的市场需求。
因此,设计一个高效的尿素生产工艺对于提高生产效率和降低生产成本非常重要。
下面将从原料选择、生产工艺流程、设备选型以及工艺参数控制等方面进行详细的设计。
一、原料选择尿素的主要原料为天然气和氨气,因此在工艺设计中需要选择高纯度的天然气和氨气作为原料。
同时,还需要选择适合的助剂用来提高尿素的质量和生产效率。
二、生产工艺流程尿素的生产工艺主要包括氨合成、尿素合成和尿素精制三个步骤。
1.氨合成氨合成是将天然气进行催化合成生成氨气的过程。
该过程通常采用床透气式催化合成反应器。
天然气经过净化处理后,与过热蒸汽在反应器中通过催化剂的作用进行反应生成氨气。
反应过程中需要控制反应温度和压力以及催化剂的使用量。
2.尿素合成尿素合成是将氨气与二氧化碳进行反应生成尿素的过程。
该过程通常采用尿素合成反应器。
反应器中的氨气和二氧化碳在一定的温度和压力下通过催化剂的作用进行反应生成尿素。
反应过程中需要控制反应温度、压力和催化剂的使用量以及氨气和二氧化碳的供给比例。
3.尿素精制尿素精制是将合成的尿素进行脱水、结晶和干燥等处理,提高尿素的纯度和产品的质量。
该过程需要通过脱水塔、结晶塔和干燥器等设备进行操作。
脱水塔用来去除尿素中的水分,结晶塔用来将脱水后的尿素进行结晶,干燥器用来将结晶的尿素进行干燥处理。
三、设备选型在尿素生产工艺中,需要选用合适的反应器、分离塔和干燥器等设备。
反应器和分离塔通常采用不锈钢材料,具有耐腐蚀性和耐高温的特点。
干燥器通常采用旋转式干燥器或流化床干燥器,具有较好的干燥效果和操作性能。
四、工艺参数控制在尿素生产工艺中,需要对反应温度、压力、催化剂的使用量以及原料供给比例等工艺参数进行控制。
通过合理地控制工艺参数,可以提高尿素的合成速度和产品质量。
综上所述,设计一个高效的尿素生产工艺需要从原料选择、生产工艺流程、设备选型以及工艺参数控制等方面进行综合考虑。
产万吨水溶液全循环法生产尿素工艺设计方案

摘要由于具有生产工艺简单,生产操作易于掌握;生产设备容易制造,投资较省;施用后见效快,增产显著等特点,尿素在各种肥料新品种不断涌现的情况下产销量仍持高不下。
本设计介绍了尿素的性质、用途、生产方法和发展状况,详细描述了水溶液全循环法生产尿素的工艺流程,重点介绍了尿素的工业生产的过程,并对单位质量参加反应的原料进行物料衡算和热量衡算,以期获得低耗能、低污染、高产出的尿素生产工艺。
关键词:尿素,全循环,发展,工艺流程一、概述(一)尿素的物理化学性质和用途1.尿素的物理性质分子式:CO(NH2)2,分子量60.06,因最早由人类及哺乳动物的尿液中发现,故称尿素。
纯净的尿素为无色、无味针状或棱柱状晶体,含氮量为46.6%,工业尿素因含有杂质而呈白色或浅黄色,工业或农业品为白色略带微红色固体颗粒无臭无味。
密度1.335g/cm3。
熔点132.7℃。
超过熔点则分解。
尿素较易吸湿,贮存要注意防潮。
尿素易溶于水和液氨,其溶解度随温度升高而增大。
2.尿素的化学性质易溶于水、醇,不溶于乙醚、氯仿。
呈微碱性。
可与酸作用生成盐。
有水解作用。
在高温下可进行缩合反应,生成缩二脲、缩三脲和三聚氰酸。
加热至160℃分解,产生氨气同时变为氰酸。
因为在人尿中含有这种物质,所以取名尿素。
尿素含氮(N)46%,是固体氮肥中含氮量最高的。
尿素在酸、碱、酶作用下(酸、碱需加热)能水解生成氨和二氧化碳。
对热不稳定,加热至150~160℃将脱氨成缩二脲。
若迅速加热将脱氨而三聚成六元环化合物三聚氰酸。
(机理:先脱氨生成异氰酸(HN=C=O),再三聚)。
在氨水等碱性催化剂作用下能与甲醛反应,缩聚成脲醛树脂。
与水合肼生成氨基脲2NH3+CO2→NH2COONH4→CO(NH2)2+H2O粒状尿素为粒径1~2毫米的半透明粒子,外观光洁,吸湿性有明显改善。
20℃时临界吸湿点为相对湿度80%,但30℃时,临界吸湿点降至72.5%,故尿素要避免在盛夏潮湿气候下敞开存放。
年产10万吨尿素工艺设计
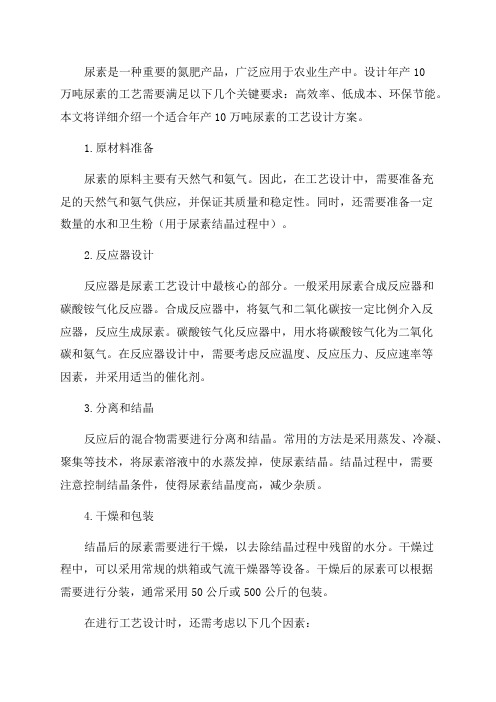
尿素是一种重要的氮肥产品,广泛应用于农业生产中。
设计年产10万吨尿素的工艺需要满足以下几个关键要求:高效率、低成本、环保节能。
本文将详细介绍一个适合年产10万吨尿素的工艺设计方案。
1.原材料准备尿素的原料主要有天然气和氨气。
因此,在工艺设计中,需要准备充足的天然气和氨气供应,并保证其质量和稳定性。
同时,还需要准备一定数量的水和卫生粉(用于尿素结晶过程中)。
2.反应器设计反应器是尿素工艺设计中最核心的部分。
一般采用尿素合成反应器和碳酸铵气化反应器。
合成反应器中,将氨气和二氧化碳按一定比例介入反应器,反应生成尿素。
碳酸铵气化反应器中,用水将碳酸铵气化为二氧化碳和氨气。
在反应器设计中,需要考虑反应温度、反应压力、反应速率等因素,并采用适当的催化剂。
3.分离和结晶反应后的混合物需要进行分离和结晶。
常用的方法是采用蒸发、冷凝、聚集等技术,将尿素溶液中的水蒸发掉,使尿素结晶。
结晶过程中,需要注意控制结晶条件,使得尿素结晶度高,减少杂质。
4.干燥和包装结晶后的尿素需要进行干燥,以去除结晶过程中残留的水分。
干燥过程中,可以采用常规的烘箱或气流干燥器等设备。
干燥后的尿素可以根据需要进行分装,通常采用50公斤或500公斤的包装。
在进行工艺设计时,还需考虑以下几个因素:1.优化反应条件反应条件的优化可以提高反应速率和反应转化率,从而提高尿素的产量和质量。
常见的优化方法包括改变反应温度和压力、增加催化剂用量等。
2.持续监测和控制在工艺运行过程中,需要持续监测反应温度、压力、氨气和二氧化碳的用量等指标。
通过及时调整反应条件,保证工艺的稳定运行。
3.节能减排尿素工艺设计中需要考虑节能减排的问题。
可以采用余热回收技术,利用反应过程中产生的余热进行发电或供暖。
同时,还要考虑废水和废气的处理,以达到环境保护的要求。
4.安全措施工艺设计时需要充分考虑安全因素。
包括防火、防爆等设施的建立,并制定相应的应急预案,以应对可能发生的安全事故。
尿素生产工艺流程
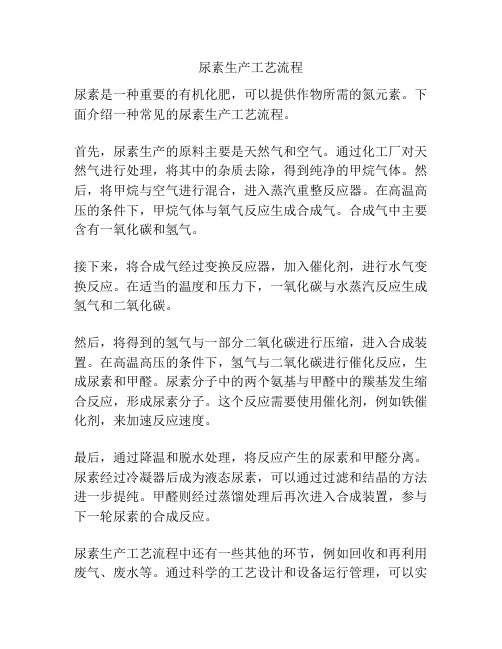
尿素生产工艺流程
尿素是一种重要的有机化肥,可以提供作物所需的氮元素。
下面介绍一种常见的尿素生产工艺流程。
首先,尿素生产的原料主要是天然气和空气。
通过化工厂对天然气进行处理,将其中的杂质去除,得到纯净的甲烷气体。
然后,将甲烷与空气进行混合,进入蒸汽重整反应器。
在高温高压的条件下,甲烷气体与氧气反应生成合成气。
合成气中主要含有一氧化碳和氢气。
接下来,将合成气经过变换反应器,加入催化剂,进行水气变换反应。
在适当的温度和压力下,一氧化碳与水蒸汽反应生成氢气和二氧化碳。
然后,将得到的氢气与一部分二氧化碳进行压缩,进入合成装置。
在高温高压的条件下,氢气与二氧化碳进行催化反应,生成尿素和甲醛。
尿素分子中的两个氨基与甲醛中的羰基发生缩合反应,形成尿素分子。
这个反应需要使用催化剂,例如铁催化剂,来加速反应速度。
最后,通过降温和脱水处理,将反应产生的尿素和甲醛分离。
尿素经过冷凝器后成为液态尿素,可以通过过滤和结晶的方法进一步提纯。
甲醛则经过蒸馏处理后再次进入合成装置,参与下一轮尿素的合成反应。
尿素生产工艺流程中还有一些其他的环节,例如回收和再利用废气、废水等。
通过科学的工艺设计和设备运行管理,可以实
现对环境的保护和资源的循环利用。
总的来说,尿素的生产工艺流程包括甲烷气体的处理、合成气的产生、水气变换反应、尿素的合成反应、尿素和甲醛的分离等步骤。
这个工艺流程是高温高压条件下的复杂化学反应过程,需要依靠先进的设备和催化剂来保证反应效率和产品质量。
年产10万吨尿素工艺设计

尿素是一种重要的氮肥和化工原料,广泛应用于农业和化工领域。
设
计年产10万吨尿素的工艺需要考虑原料选择、反应工艺、蒸发结晶和提
纯工艺等方面。
以下是一个可能的工艺设计方案。
1.原料选择
尿素的主要原料是氨和二氧化碳。
氨可以选择来自合成氨厂的合成氨,而二氧化碳可以来自空分装置的尾气或煤炭燃烧废气。
此外,还需要选择
一些辅助原料,如催化剂和溶剂。
2.反应工艺
尿素的合成主要通过尿素合成反应实现,该反应是氨和二氧化碳在合
适温度和压力下经过催化剂催化生成尿素。
反应工艺中需要优化的参数包
括反应温度、反应压力、氨和二氧化碳的摩尔比等。
反应器可以选择尿素
液相反应器或气相反应器。
3.蒸发结晶
尿素合成反应后得到的尿素溶液需要进行蒸发结晶,将水分去除,得
到固体尿素产品。
蒸发结晶工艺中需要控制的参数包括蒸发温度、蒸发压力、溶液浓度等。
4.提纯工艺
获得的尿素产品通常需要进行再次提纯,以去除杂质。
提纯工艺可以
包括溶剂结晶、溶剂洗涤等步骤。
通过适当的提纯工艺,可以得到符合特
定要求的尿素产品。
5.产品后处理
设计工艺时还需要考虑尿素产品的后处理工艺,包括干燥、包装和储存等。
这些环节需要确保产品的质量和稳定性。
此外,工艺设计还需要考虑废气处理、废水处理等环保措施,并确保工艺的高效可行性和安全性。
以上是一个简要的年产10万吨尿素工艺设计方案,具体的工艺设计需要根据实际情况进行详细研究和优化。
- 1、下载文档前请自行甄别文档内容的完整性,平台不提供额外的编辑、内容补充、找答案等附加服务。
- 2、"仅部分预览"的文档,不可在线预览部分如存在完整性等问题,可反馈申请退款(可完整预览的文档不适用该条件!)。
- 3、如文档侵犯您的权益,请联系客服反馈,我们会尽快为您处理(人工客服工作时间:9:00-18:30)。
第一章 尿素生产概述1.1尿素生产的原理尿素的合成原料是氨和二氧化碳,这两种原料均来自合成氨装置。
尿素合成的条件为:188℃,15.6MPa ,进料氨与二氧化碳的物质的量比是3.6,水与二氧化碳的物质的量比是0.67[2]。
一般认为在合成塔尿素的反应分以下两部进行第一步,氨基甲酸铵的生成。
反应式为:324212()()()NH l CO g NH COONH l Q ++第二步,氨基甲酸铵脱水。
反应式为:422222()()()()NH COONH l CO NH l H O l Q +-1.2尿素生产的方法由于这两个反应都是可逆反应,因此氨与二氧化碳不可能全部转化为尿素。
在工业生产条件下,二氧化碳转化率仅在50%-70%之间[3]。
为了分离和回收未反应的氨和二氧化碳,可将合成熔融物加热分解,使气体逸出。
但要将逸出的氨与二氧化碳全部或部分返回合成塔重新合成尿素,这就出现了各种不同的流程。
有循环法,半循环法和全循环法。
全循环法又可以分为热气全循环法、矿物油全循环法、气体分离全循环法、水溶液全循环法及汽提全循环法。
气提全循环法又可以分为二氧化碳汽提法、氨汽提法和双汽提法。
第二章 斯那姆氨汽提工艺2.1工艺基本原理汽提是使尿液中的甲铵按下述反应分解为3NH 和2CO 的过程:4232()2()()NH COONH l NH g CO g Q +-这是一个可逆体积增大的反应[4]。
我们只要能够供给热量,降低压力或降低气相中3NH 和2CO 某一组分的分压都可使反应向右方进行,以达到分解甲铵的目的。
汽提法是在保持压力与合成塔相同的条件下,在给热量的同时采用降低气相中3NH 和2CO 某一组分的过程。
当温度为T ℃时,纯态甲铵的离解压力与各组分(3NH 和2CO )的分压的关系按以上化学方程式可作如下表示:设总压力为P s 则从反应式中可以看到氨分压为2/3P s 二氧化碳分压为1/3P s 如反应式在温度为t ℃时的平衡常数为K t ,则:23(2/3)(1/3)4/27t s s s K P P P ==假如氨和二氧化碳之比不是按2:1状态存在,在温度仍为t ℃时,它的总压力为P ,其各组分的分压为:3NH 的分压33NH NH P X =⨯⨯总压氨的分子数=P2CO 的分压232CO NH P X =⨯⨯总压二氧化碳的分子数P3NH X 和2CO X 分别为气体中氨,二氧化碳的分子分数这样反应式在温度为t ℃时平衡常数应为:3232232()()NH CO NH CO Kt P X P X P X X =⋅⋅⋅=⋅⋅ 温度相同,平衡常数应相等,所以当温度为t ℃323334/27NH CO Ps P X X =⋅⋅⇒23s P =但纯甲胺在某一固定温度下离解力为不变的常数C ,所以P =从此式可以看出,当趋近于1时,则3NH X 必趋近于0,就趋近于0,则2CO X 趋近于无限大,就是说当甲铵液用二氧化碳气体通入,气相中几乎全为二氧化碳时(2CO X =1)P 趋于无限大,即甲铵的离解压力近于无限大,我们知道如果甲铵在某温度下的离解压力大与操作压力,甲铵就会得到分解,现分解压力为无限大,大于固定操作压力,所以液相中甲铵就进行分解,这就是二氧化碳气提法分解甲铵的理论基础[5]。
2.2工艺特点(1)高32/NH CO 高转化率合成塔入口物料中32/NH CO 为3.3-3.6,塔内操作温度186-189℃,操作压力约15.5MPa ,2CO 的单程转化率可达65-67%。
(2)热利用率高能耗低a.采用钛材的降模式氨气提塔,操作温度高达205℃左右,气体效率高,从而减轻了下游工序的分解负荷,降低了共用物料的消耗。
b.中压分解气的冷凝热,用于真空预浓缩器蒸发尿液;低压分解气和解吸气在液氨预热器加热液氨;蒸汽冷凝液用于高压甲铵泵后加氨液加热。
这些措施相当于节省蒸汽约400kg/t 尿素。
使蒸汽和冷却水的消耗降低。
另外,工艺冷凝液经处理后,可直接作为锅炉给水使用,也相应减少了操作费用。
(3)操作弹性大年运转率高[6]由于该装置的防腐性能好,可在40%的生产负荷下稳定运行,封塔时间可达4天也不需要排放,事故排除后即可快速开车,提高了装置的运转率。
本装置的年运转天数可达340天左右。
(4)设备水平布置尿素合成工段采用了高压喷射器作为抽吸循环甲铵液的动力,使得合成塔高压设备直接坐落于地面上,无需高层框架。
使安装和维修费用降低。
(5)操作安全性强气提塔使用钛材以及反应物料中较高的32/NH CO ,使得系统中需加入的防腐空气量减少,这样,在中低压系统排出的混合气中含量较低,避免生成爆炸性混合气体。
同时,也相应减少了惰性气中的氨损失。
(6)污染小经高效解吸和深度水解后,液体排放物得到净化处理,工艺冷凝液中铵和尿素含量降至1ppm 以下,可直接回收利用,同时,由于采用高质量的造粒喷头及自然通风技术,造粒排放气体中尿素粉尘含量在20kg/3m 以下,对周边环境造成的污染变得很薄弱。
(7)流程长,设备多,相互制约性强,控制点多,技术素质要求高[7]。
2.3工艺流程图工艺流程图见图2-12.4工艺流程简介2.4.1原料供给本装置的两种原料均来自合成氨装置。
液氨压力不低于2.2MPa,温度40℃。
进入尿素界去的液氨存贮在液氨贮槽V105(通过位于其上的氨 回收塔C105喷洒下来),再经过两台串联的泵打如高压系统。
第一台是氨升压泵P105,出口压力2.2MPa ,第二台是氨高压泵P101(两级离心泵),进一步加压到高压系统所需压力。
高压液氨在氨预热器E107中预热至95℃,同时回收了低压气体的冷凝热。
预热后的高压液氨压力为21.9MPa ,作为氨基甲酸铵喷射器L101的动力,将循环的氨基甲酸铵液(氨基甲酸铵分离器V101压力为14.7MPa )一并带入尿素合成塔R101底部。
从合成氨装置进入界区的二氧化碳气体,温度不高于40℃,压力为0.4MPa ,经二氧化碳压缩机入口液滴分离罐V111分离清除雾滴后进入由蒸汽透平驱动的双缸四段离心式二氧化碳压缩机K101,加压至15.9MPa 。
段与段之间有中压冷凝器,但末级出来的二氧化碳气不经冷却直接送入尿素合成塔R101。
在二氧化碳压缩机入口分离器V111后的管线时,加入一定量的空气,以钝化高压系统不锈钢设备的表面,使其免受反应物和产物的腐蚀[8]。
2.4.2高压合成、汽提、回收尿素合成条件为:188℃,15.6 MPa ,精料氨与二氧化碳的物质的量之比是3.6,水与二氧化碳的物质的量之比是0.67。
略高于物料计算值(氨与二氧化碳的物质的量比是3.5,水与二氧化碳的物质的量比是0.66[9])。
尿素合成塔内发生如下的化学反应:R101-合成塔 V101-甲铵分离器 E101-汽提塔 E104-甲铵冷凝器 V102-中压分离器 E102-中压分解器 C101-中压吸收塔 V103-低压分离器 V106-碳铵液槽 C-101-中压吸收塔 C-103中压惰洗塔 C105-氨回收塔 C103-中压惰洗塔 V104-真空预浓缩分离器 E113-真空预浓缩器 V107-第一真空分离器 V108-第二真空分离器 C102-解吸塔 E116-解吸塔预热器 E117-水解器预热器 R102-水解器 P115-水解器给料泵 P106-尿素溶液泵 P108-尿素熔融泵 P101-高压氨泵 P105-氨升压泵 P107-氨液泵 E103-低压分解图2-1 氨汽提尿素工艺流程图Fig2-1 The figure of urea ammonia stripping process5324212()()()NH l CO g NH COONH l Q ++ 422222()()()()NH COONH l CO NH l H O l Q +-在此条件下反应在液相进行,以原料二氧化碳利用率表示转化率约60-65%[10]。
为了回收未反应物,离开尿素合成塔的反应混合物流入与合成塔同压的氨气提塔E101。
混合液向下流动时因受热而有氨逸出,利用逸出的氨作为汽提剂,又是二氧化碳逸出。
分解与汽化所需热量,由饱和蒸汽供给,压力为2.20-2.40MPa 。
由气去汽提塔E101出来的气体,与中压系统返回的碳铵液(先经高压碳铵液泵P102增压并在预热器E105预热)汇合,一并进入高压氨基甲酸铵冷凝器E104,在此几乎全部冷凝下来。
其冷凝热用于副产0.35MPa 蒸汽。
氨基甲酸铵冷凝器E104出来的混合物进入氨基甲酸铵分离器V101进行气液分离。
液相称氨基甲酸铵液,经喷射器L101返回合成塔。
未冷凝的气体主要是惰气(空气),亦含有一定量的氨和二氧化碳,在压力控制下送往中压分解器E102A/B 的下部。
高压系统主要设备是合成塔R101、气提塔E101、氨基甲酸铵冷凝器E104和氨基甲酸氨分离器V101。
2.4.3中压回收离开汽提塔底部的尿液,虽已经汽提出相当数量的未反应物3NH 和2CO ,但还需要进一步回收和提纯.本流程回收提纯系统分三级,即中压 1.8MPa (绝压)级低压 0.45MPa (绝压)级真空 0.035MPa (绝压)级[11]离开气提塔底部的尿液减压到1.7MPa ,进入降膜式中压分解器E102,同时,高压系统少量未冷凝气体(自分离器V101)亦进入E102A/B 的下部。
中压分解器E102分两部分:尿液减压首先进入它的顶部分离器V102,将闪蒸出来的气体排走,然后流体流入未于其下的管束,即分解部分,使残留的氨基甲酸铵受热而继续分解。
所需热量来自两部分:壳体上部(E102A )是0.47MPa 、160℃的蒸汽[12];壳体下部(E102B )是来自汽提塔壳侧的2.2MPa 蒸汽冷凝液,并补充有一定量同压蒸汽,以满足热量要求。
离开中压分解器E102的液体送低压系统。
离开中压分解器顶部E102的气体与来自低压系统的碳铵液(经中压碳铵液泵P103加压)汇合,然后送往真空预浓缩器E113的管间部分,在此进行气体的吸收,而放出的吸收和冷凝热用来蒸发尿液。
离开真空预浓缩器E113管间部分的气液混合物,送往中压冷凝器E106进一步冷却。
此时放出的热量已无法利用,被冷却水带走。
离开中压冷凝器E106的气液混合物进入中压吸收塔C101。
塔的下部是鼓泡段,在此用碳铵液吸收。
未被吸收的气体继续上升到蒸馏段,与喷淋下来的液氨(来自氨贮槽V105)和氨水(来自中压降膜吸收塔E111)相遇。
几乎全部被吸收下来。
塔顶得到纯的气氨,但包括进入系统的惰性气体和微气体中的CO2(20-100mL/m3)。
塔底溶液经P102升压,再经高压预热器E105预热,送往高压系统。
量CO2中压吸收塔C101顶部出来的气氨和惰气进入氨冷凝器E109并进入液氨贮槽V105。