金属切削原理()
金属切削原理

金属切削原理一、引言金属切削是一种重要的加工方法,广泛应用于机械制造、航空航天、汽车制造等领域。
金属切削的原理是将金属材料通过刀具的切削力和磨擦力进行去除,从而得到所需形状和尺寸的工件。
本文将详细介绍金属切削的原理。
二、金属材料的物理特性金属材料具有高强度、高硬度、高塑性等特点。
在进行切削加工时,需要考虑到这些特性对加工过程和结果的影响。
1.硬度硬度是指材料抵抗外界力量侵蚀和破坏的能力。
在进行金属切削时,硬度会影响到刀具对材料的切削深度和速度。
硬度越大,材料越难被去除,需要采用更高强度和更耐磨损的刀具。
2.韧性韧性是指材料抵抗断裂和变形的能力。
在进行金属切削时,韧性会影响到刀具对材料的变形程度和断裂情况。
韧性越大,材料越容易被刀具弯曲和拉伸,需要采用更大的切削力和更耐磨损的刀具。
3.塑性塑性是指材料在受到外力作用下发生变形的能力。
在进行金属切削时,塑性会影响到材料的变形程度和表面质量。
塑性越大,材料越容易被切削并留下较光滑的表面。
三、切削力的产生金属切削过程中,主要有三种力对工件进行去除:正向切削力、侧向切削力和径向切削力。
这些力产生的原因如下:1.正向切削力正向切削力是指沿着工件表面方向施加在主轴上的推进力。
它是由于主轴上旋转的刀具与工件之间产生了摩擦而引起的。
2.侧向切削力侧向切削力是指垂直于工件表面方向施加在主轴上的推进力。
它是由于主轴上旋转的刀具与工件之间产生了摩擦而引起的。
3.径向切削力径向切削力是指垂直于工件表面方向施加在主轴上的推进力。
它是由于主轴上旋转的刀具与工件之间产生了摩擦而引起的。
四、切削过程中的热效应金属切削过程中,由于摩擦和变形,会产生大量的热量。
这些热量会对材料和刀具造成影响。
1.材料的热变形在金属切削过程中,由于高速旋转的刀具与工件之间产生了摩擦,会使得材料表面温度升高。
当温度达到一定值时,材料就会发生热变形,导致尺寸和形状发生变化。
2.材料的热软化在金属切削过程中,由于高速旋转的刀具与工件之间产生了摩擦,会使得材料表面温度升高。
金属切削原理

三、切削层参数
•切削层厚度hD 垂直于正在加工的表面(过渡表面)度量 的切削层参数。 hD=f•sinκ r •切削层宽度bD 平行于正在加工的表面(过渡表面)度 量的切削层参数。 bD=ap/sinκ r •切削层横截面积AD 在切削层参数平面内度量的横截面 积。 AD=hD•bD=ap•f
常用刀具材料有碳素工具钢(如T10A、T12A)、合金工具钢 (如9SiCr、CrWMn)、高速钢、硬质合金、陶瓷、金刚石、 立方炭化硼等。
二、常用刀具材料
常用刀具材料的种类及其特性 • 碳素工具钢 • 高速钢 • 硬质合金 • 其它刀具材料(涂层刀具、陶瓷、金刚石、立方氮
化硼 )
• 优点、缺点、种类、常用牌号、应用等
1. 金属切削过程
刀具从工件上切除多余的金属的过程,并使工件得到符 合图纸要求的尺寸、形状和表面质量。
必须具备以下三个条件: 1.工件和刀具之间要有相对运动及,即切削运动; 2.刀具材料必须具备一定的切削性能; 3.刀具必须有合理的几何参数,即切削角度等。
一、切削运动与切削用量 1.工件加工表面
在切削过程中,工件上存在三个不断变化的表面:
上述公式中可看出 hD、bD均与主偏角有关,但切削层 横截面积 AD 只与 hD、bD 或 f、ap有关。
§1-2 刀具材料
•刀具材料通常是指刀具切削部分的材料。 •加工质量、加工效率、加工成本,在很大程度上取决于 刀具材料的合理选择。因此,材料、结构和几何形状是决 定刀具切削性能的主要因素。 •金属切削过程除了要求刀具具有适当的几何参数外,还 要求刀具材料具备一定性能。
金属切削原理与刀具

金属切削原理与刀具金属切削是指通过刀具对金属材料进行加工削除的过程,是金属加工领域中常见且基础的一种加工方式。
人们在制造和加工各种金属制品的过程中,常常需要通过切削来将金属材料加工成所需的形状和尺寸。
本文将深入探讨金属切削的原理以及相关的刀具类型。
一、金属切削原理金属切削的原理是利用刀具对金属工件进行力学削除材料的过程。
主要原理可以归纳为以下几点:1. 刀具与工件的相互作用力:切削过程中,刀具施加在工件上的作用力可以分为切割力、摩擦力、压力等。
切割力使刀具沿着切削方向削除金属,摩擦力影响工件表面的质量,而压力则有助于防止振动和提高切削质量。
2. 刀具与工件的接触面积:切削过程中,刀具与工件的接触面积较小,集中在切削刃上。
通过提高切削刃的硬度和耐磨性,可以减少切削面的磨损,延长刀具的使用寿命。
3. 金属切削时的切削角度:切削角度是指刀具切削刃与工件表面法线之间的夹角。
合理选择切削角度可以使切削过程更加顺利,减少切削力和切削温度。
二、常见的刀具类型不同的金属切削需求需要选择不同类型的刀具。
以下将介绍几种常见的刀具类型及其特点:1. 钻头:用于钻孔加工的刀具,主要特点是具有较高的刚性和旋转精度。
根据孔径的大小,可以选择不同类型的钻头,如常规钻头、中心钻头和孔径加工钻头等。
2. 铣刀:用于面铣、端铣、槽铣等加工的刀具,形状像一把小锯齿,可通过旋转进行切削。
铣刀可分为平面铣刀、球头铣刀、棒铣刀等多种类型,适用于不同形状和尺寸的金属切削。
3. 刀片:用于车削加工的刀具,通常由硬质合金制成,具有较高的耐磨性。
刀片形状多样,如可直线切削的刀片、可拐弯切削的刀片等,适用于不同形状和尺寸的车削加工。
4. 锯片:用于锯切金属材料的刀具,常用于金属管、金属板的切割。
根据不同的锯片规格和齿型,可以实现不同精度和效率的锯切加工。
5. 切割刀具:包括切割刀片和切割车刀等,主要用于金属材料的切割和切断。
根据切割的需求和要求,选择合适的切割刀具可以提高加工效率和切割质量。
金属切削原理与刀具的刀具径向载荷分析

金属切削原理与刀具的刀具径向载荷分析金属切削是工业加工中常见的一种加工方式,广泛应用于机械制造、汽车制造、航空航天等领域。
刀具作为金属切削的主要工具,在实际加工过程中承受着巨大的载荷。
一、金属切削原理金属切削是指利用刀具对金属工件进行切削加工,通过切削过程中产生的力将金属材料削除,实现工件的形状、尺寸和表面粗糙度的精确控制。
金属切削过程主要包括切削区的成型与变形以及金属材料的剥离。
切削区的成型与变形涉及刀具与工件间的相互作用,包括刀具的切削边与工件之间的相对运动和切削力的形成。
金属材料的剥离则是指切削过程中,利用刀具对工件进行局部剪切,使得金属材料在一定条件下从工件上剥离。
刀具径向载荷是指切削过程中刀具在径向方向所承受的力。
它对刀具的选用和加工效果具有重要影响。
二、刀具径向载荷的分析1. 切削力的来源在金属切削过程中,切削力主要来源于切削区的成型与变形。
当刀具与工件之间沿着切削方向产生相对运动时,切削边沿着工件表面切削金属材料,形成切屑。
在这个过程中,刀具与工件之间发生了相互作用,产生了切削力。
切削力的大小与多个因素相关,包括切削速度、切削深度、进给量、刀具材料和切削区温度等。
其中,切削深度和进给量对切削力的影响最为显著。
2. 刀具径向载荷的影响因素刀具径向载荷的大小受多个因素影响,主要包括切削力的大小和方向、刀具的几何形状、刀具材料和刀具的磨损情况等。
切削力的大小直接决定了刀具径向载荷的大小。
切削力越大,刀具在径向方向所承受的力也越大。
切削力的方向与工件表面之间的相对运动方向相反。
刀具的几何形状对径向载荷有着重要影响。
刀具的刃角、切削刃长度、后角等参数都会影响切削力的大小和方向,进而影响刀具的径向载荷。
刀具材料是另一个影响刀具径向载荷的因素。
不同材料的刀具具有不同的硬度、强度和刚度等特性,不同材料的刀具在切削过程中对切削力的抵抗能力也不同。
刀具的磨损情况也会对刀具径向载荷产生影响。
刀具表面的磨损会导致切削力的增加,从而使刀具在径向方向所承受的载荷增大。
金属切削原理

金属切削原理金属切削是一种常见的金属加工方法,通过切削工具对金属材料进行加工,以获得所需形状和尺寸的工件。
金属切削原理是指在切削过程中,切削刀具对工件进行切削,形成切屑并使工件形成所需形状和尺寸的过程。
金属切削原理的理解对于提高切削加工效率、提高加工质量具有重要意义。
首先,金属切削原理的基本过程是切削刀具对工件进行切削。
在切削过程中,切削刀具与工件之间产生相对运动,切削刀具对工件表面进行切削,形成切屑。
切削刀具的刀尖与工件接触处称为刀尖触点,刀尖触点是切削过程的关键部位,刀尖触点的运动状态直接影响着切削过程的稳定性和加工质量。
其次,金属切削原理的关键参数包括切削速度、进给量和切削深度。
切削速度是切削刀具在单位时间内对工件进行切削的速度,通常用米/分钟表示;进给量是切削刀具在单位时间内对工件进行进给的距离,通常用毫米/转表示;切削深度是切削刀具在切削过程中对工件进行切削的深度,通常用毫米表示。
这三个参数的选择直接影响着切削过程的效率和加工质量。
另外,金属切削原理的切削力是切削过程中的重要参数。
切削力的大小和方向直接影响着切削刀具和工件的磨损情况、加工精度和加工表面质量。
切削力的大小受到切削条件、切削刀具和工件材料等因素的影响,合理控制切削力是提高切削加工效率和加工质量的关键。
最后,金属切削原理的切削热是切削过程中的重要问题。
切削热的产生直接影响着切削刀具和工件的温度、切削刀具的寿命和加工表面质量。
切削热的产生受到切削速度、切削深度、切削方式和切削刀具材料等因素的影响,合理控制切削热是提高切削加工效率和加工质量的关键。
总之,金属切削原理是切削加工的基础,对于提高切削加工效率、提高加工质量具有重要意义。
合理控制切削条件、切削力和切削热是提高切削加工效率和加工质量的关键。
只有深入理解金属切削原理,才能更好地应用于实际生产中,提高加工效率,降低成本,提高产品质量。
金属切削原理与刀具的基本概述
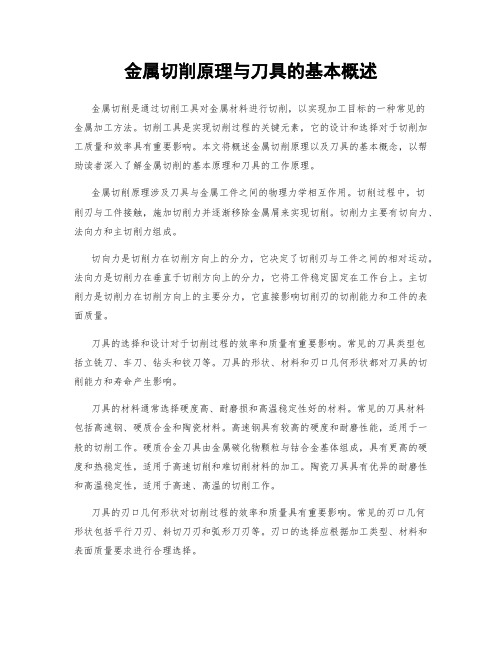
金属切削原理与刀具的基本概述金属切削是通过切削工具对金属材料进行切削,以实现加工目标的一种常见的金属加工方法。
切削工具是实现切削过程的关键元素,它的设计和选择对于切削加工质量和效率具有重要影响。
本文将概述金属切削原理以及刀具的基本概念,以帮助读者深入了解金属切削的基本原理和刀具的工作原理。
金属切削原理涉及刀具与金属工件之间的物理力学相互作用。
切削过程中,切削刃与工件接触,施加切削力并逐渐移除金属屑来实现切削。
切削力主要有切向力、法向力和主切削力组成。
切向力是切削力在切削方向上的分力,它决定了切削刃与工件之间的相对运动。
法向力是切削力在垂直于切削方向上的分力,它将工件稳定固定在工作台上。
主切削力是切削力在切削方向上的主要分力,它直接影响切削刃的切削能力和工件的表面质量。
刀具的选择和设计对于切削过程的效率和质量有重要影响。
常见的刀具类型包括立铣刀、车刀、钻头和铰刀等。
刀具的形状、材料和刃口几何形状都对刀具的切削能力和寿命产生影响。
刀具的材料通常选择硬度高、耐磨损和高温稳定性好的材料。
常见的刀具材料包括高速钢、硬质合金和陶瓷材料。
高速钢具有较高的硬度和耐磨性能,适用于一般的切削工作。
硬质合金刀具由金属碳化物颗粒与钴合金基体组成,具有更高的硬度和热稳定性,适用于高速切削和难切削材料的加工。
陶瓷刀具具有优异的耐磨性和高温稳定性,适用于高速、高温的切削工作。
刀具的刃口几何形状对切削过程的效率和质量具有重要影响。
常见的刃口几何形状包括平行刀刃、斜切刀刃和弧形刀刃等。
刃口的选择应根据加工类型、材料和表面质量要求进行合理选择。
此外,切削参数的选择也是确保切削过程顺利进行的关键因素。
切削参数包括切削速度、进给速度和切削深度等。
切削速度决定了刀具与工件之间的相对运动速度,进给速度则决定了切削刃每分钟移除的金属量,切削深度是切削刃切入工件的深度。
在切削过程中,润滑和冷却也是必不可少的。
刀具和工件之间的摩擦和热量会导致刀具磨损和工件热变形。
金属切削原理的基本原理与应用探析

金属切削原理的基本原理与应用探析金属切削是指在机械加工过程中,通过刀具对金属材料进行切削加工的一种方法。
切削加工是现代工业生产中非常重要的一环,广泛应用于制造业的各个领域,如汽车制造、航空航天、机械制造等。
本文将探析金属切削原理的基本原理和应用。
一、金属切削原理的基本原理1. 切削力与材料性质的关系切削力是刀具和工件之间产生的力,它直接影响到切削加工的效率和质量。
切削力与金属材料的性质有密切关系,例如硬度、韧性和塑性等特性。
一般来说,材料硬度越高,切削力越大。
2. 切削热的生成与影响在切削过程中,由于刃口与工件接触产生摩擦,会产生大量的切削热。
切削热的大小和分布对切削加工有着重要影响。
过高的切削热可能导致刀具磨损加剧、工件变形,甚至热裂纹的产生。
因此,有效控制切削热对于提高切削加工质量至关重要。
3. 切削液的作用切削液在切削过程中起到冷却、润滑和防腐的作用。
通过降低切削热,它可以有效地控制切削加工过程中的温度,减少工件表面的热变形,提高切削加工质量和效率。
4. 切削刃部分的结构与刀具磨损切削刃是切削工具的重要部分,其结构设计直接影响到切削加工的效果。
一般来说,切削刃的设计要使切削力分布均匀,降低切削热和切削力,延长切削工具的寿命。
此外,选择合适的材料和硬度对切削刃的寿命也有很大影响。
二、金属切削的应用探析1. 汽车制造汽车制造是金属切削应用的重要领域之一。
在汽车制造中,金属切削广泛应用于发动机、底盘、车身等零部件的加工。
通过金属切削,可以精确加工出复杂形状的零部件,提高汽车的质量和性能。
2. 航空航天工业航空航天工业对金属切削的要求更为严格。
在航空航天工业中,金属切削应用于航空发动机、机翼、航天器等部件的加工。
金属切削技术的发展和应用,推动了航空航天工业的进步和发展。
3. 机械制造金属切削在机械制造领域中扮演着重要角色。
在机械制造中,金属切削应用于制造各种机床、工具以及零部件等。
通过金属切削技术,可以提高机械制造的精度和效率,满足不同行业和领域的生产需求。
金属切削原理的基本概述

金属切削原理的基本概述金属切削是一种常见的金属加工技术,广泛应用于制造业和机械加工领域。
金属切削的原理是通过切削工具对金属材料施加力量,以去除材料表面的金属层,实现工件的加工和成形。
金属切削原理可以分为以下几个方面:1. 切削力:在金属切削过程中,切削工具施加力量以去除金属材料。
切削力是指切削工具对工件施加的力的大小和方向。
切削力的大小取决于刀具的几何形状、切削速度、切削深度、切削角度等因素。
在金属切削中,通常会产生切向力(与切削方向垂直的力)和径向力(指向工件中心的力)。
2. 切削削角:切削削角是切削刀具与工件表面之间的夹角。
切削削角的大小和形状会影响切削力的大小、切削刃的寿命和切削表面的质量。
常见的切削削角有前角、主削角、副削角等。
3. 切削速度:切削速度是指切削工具和工件相对运动的线速度。
切削速度的选择会影响切削力、切削表面的质量和刀具的寿命。
过低的切削速度可能导致刀具与工件之间产生太多的摩擦热,使刀具磨损加快;而过高的切削速度则可能导致工件表面粗糙、切削力过大。
4. 切削深度:切削深度是指切削工具将金属材料削除的深度。
切削深度的选择取决于工件的要求和切削工具的强度。
过大的切削深度可能导致切削力过大,增加切削工具的磨损和变形的风险;而过小的切削深度则可能导致加工效率低。
5. 切削热效应:切削过程中,因为摩擦和形变,切削区域会产生热量。
切削热效应可能对切削工具和工件产生不良影响,如切削刃磨损、加工表面质量下降等。
因此,在金属切削过程中,需要采取适当的切削冷却液和润滑剂等措施来降低切削热效应。
总结起来,金属切削原理是通过切削工具施加力量,削除金属材料表面的方法。
切削力、切削削角、切削速度、切削深度和切削热效应是决定切削过程中刀具寿命、工件表面质量和加工效率的重要因素。
掌握金属切削原理,对于提高金属加工的质量和效率具有重要意义。
- 1、下载文档前请自行甄别文档内容的完整性,平台不提供额外的编辑、内容补充、找答案等附加服务。
- 2、"仅部分预览"的文档,不可在线预览部分如存在完整性等问题,可反馈申请退款(可完整预览的文档不适用该条件!)。
- 3、如文档侵犯您的权益,请联系客服反馈,我们会尽快为您处理(人工客服工作时间:9:00-18:30)。
它是用于调整机床,计算切削力、切削功率,核算
工序成本等所必需的重要参数。
故常称之为切削用量三要素。
1.切削速度v 切削速度v——主运动的线速度。 其单位为m/min或m/s。 ●主运动为旋转运动时,如外圆车削时的切 削速度为:
v
式中
d n
1000
dω——待加工表面的直径(mm); n——工件转速(r/min或r/s)
加工表面(过渡表面)——工件上切削刃正在切削
的表面;
已加工表面——工件上切削后形成的新表面。
图2-2
切削运动和工件表面
1.主运动——切削运动中速度最高、消耗功率最大, 并担负主要切削任务的运动为主运动。
主运动既可由工件来实现,也可由刀具
来实现。 2.进给运动——使材料不断投入切削的运动为进给 运动。进给运动既可由工件来实现,也 可由刀具来实现。进给运动既可以是连 续的,也可以是间歇的。
五、切削层参数
切削层——工件上正在切削的一层材料。
在外圆加工时,就是工件每转一周,主切削刃相 邻两个位置之间的一层材料。 为计算方便我们取垂直于切削速度方向的剖面 (基面)进行研究。 切削厚度——ac 切削层包括 切削宽度——aw 切削面积——Ac
图2-3
外圆纵切时的切削层参数
1.切削厚度ac
●主运动为往复直线运动时,如平面刨削时的
切削速度为:
2Ln z v 1000
式中 L——往复运动行程长度(mm); nz——单位时间内主运动的往夏次数 (str/min或str/s)。
2.进给量 f
进给量 f——每一个工作循环中,刀具与工件的相对移动量。 ●外圆车削——工件转一转,刀具在进给方向的移动距离,其 单位为mm/r ●刨削——刀具往复一次,工件移动的距离,单位为mm/str。 ●铣削——由于铣刀是多齿刀具,所以规定了每齿的进给量af , 其单位为mm/z 还有单位时间的进给量(进给速度)vf ,其单位为mm/min 或mm/s。其大小为:
上面讲述的切削面积Ac ,是理论切除面积,如图
中的ABCD部分,而实际切削面积为 :Ace=Ac-ΔAc
由于刀具结构的关系还有部分残留面积ΔAc。残留
面积是指刀具副偏角krˊ≠0时,切削刃从位置Ⅰ移至位
置Ⅱ后,残留在已加工表面上的不平部分的剖面面积。
如图所示,实际切除面积为AECD部分。残余面积的
3.举例
加工方法 车 削 主运动 工件旋转 进给运动 刀具连续移动
钻 削 铣 削 镗 削
刀具旋转 刀具旋转 刀具旋转
刀具连续移动 工件连续移动 工件连续移动 工件间歇移动
刀具间歇移动 工件旋转及往复运动
刨削(牛头刨床) 刀具往复运动
磨 削 刀具旋转
四、切削用量
切削用量——切削加工过程中切削速度、进给量和
一、切削加工的种类 1. 车削: 车外圆、车端面、车床镗孔 2. 钻削:钻孔 3. 镗削:镗床镗孔 4. 铣削: 端铣铣平面、立铣铣槽、周铣铣平面 5. 刨削:刨床刨平面 6. 插削:插床插槽 7. 拉削:拉床拉圆孔 8. 磨削:外圆磨床磨外圆
2-1 切削加工的种类
二、切削加工的特点 1.受被加工材料性质的限制较少。 2.基本不受零件形状的限制。 3.切削加工可得到很高的加工精度和表面质量。 4.切除单位体积材料所消耗的能量较小。 5.切削时会产生切屑,这不仅浪费了材料,而且 增加了清理切屑的困难。 6.切削时会产生切削力,从而使工艺系统(机床、 夹具、刀具、工件)产生变形和振动,降低加工精 度。 7.由于切削力和切削热的影响,已加工表面层会 因塑性变形、弹性变形的作用而形成加工变质层, 造成加工表面质量下降;使刀具磨损等。
2.常用刀具材料 工具钢 碳素工具钢 合金工具钢 高速钢 硬质合金 钨钴(YG)合金 钨钛(YT)合金 钨钛钽(铌)(Yw)合金 其他刀具材料 陶瓷 金刚石 立方氮化硼 涂层刀具 常用磨料 普通磨料 超硬磨料
v f f n a f zn
式中 z——铣刀齿数; n——主运动(工件、钻头、铣刀)转速(r/min)。
3.切削深度(背吃刀量)ap
切削深度ap——待加工面和已加工面之间的垂直距离, 其单位为mm。外圆车削时的切削深度为:
d d m ap 2
式中 dm——已加工表面直径(mm)。 切削用量反映了刀具与工件相互作用的条件和 相对应关系,是影响工件加工质量和生产率的重要因 素。
大小将影响到已加工表面的质量。
六、切除率zw 切除率zw——单位时间内切除材料的多少为切除
率(mm3/s)
切除率直接反映切削效率的高低。用下面的
关系式表示:
2.2 刀具材料及构造
一. 刀具材料
1.对刀具材料的性能要求 ①较高的硬度——硬度要高于工件材料的硬度,常温下一般要 大于HRC60。 ②足够的强度与韧性——以承受切削力和冲击振动。 ③较好的耐磨性——以抵抗切削过程中的磨损,具有一定的耐 用度。 ④较高的耐热性——在高温下仍能切削,耐热性又称红硬性。 ⑤较好的工艺性——以便于制造各种形状的刀具和进行热处 理。 ⑥较好的传热性——避免刀尖过热而降低刀具的使用寿命。 ⑦较好的经济性——价格昂贵,使用受限(不能广泛使用)。
进行外圆车削时,工件转一周在垂直于切削速度方向的剖 面(基面)上所测的两个相邻加工表面之间的垂直距离即为切 削厚度(mm)。
a c f sin k r
2.切削宽度aw
即切削层宽度。它也代表主切削刃的长度(mm)。以车 削为例: ap
a Βιβλιοθήκη sin k r3.切削面积Ac
切削层垂直于切削速度方向的截面积为切削面积(mm2)。 以车削为例: Ac a c a f a p
表2-1
单位体积材料所消耗的能量 加工方法 所需能量/ (J•mm-3) 电火花加工 102-103 超声波加工 102-103 电子束加工 105 激光加工 105
所需能量/ 加工方法 (J•mm-3) 切削 1-10 磨削 10-102 电解磨削 1-10 电解加工 1-102
三、切削运动
切削运动——刀具与工件之间的相对运动 刀具的每一个行程中 ,工件上都有三个变化着的表面 待加工表面——工件上即将被切除金属层的表面;