稀土球化剂知道
稀土球化剂的作用是什么

稀土球化剂的作用是什么
稀土球化剂是指由一种或多种稀土元素组成的球化剂。
在工业上广泛应用于铁路、航空、航天、汽车、电子、建筑、医药等行业,其作用主要有以下几个方面。
改善铁矿石烧结性能
铁矿石烧结是钢铁生产的基础工艺之一,其烧结性能往往影响着钢铁生产效率
和钢材质量。
稀土球化剂能够改善铁矿石烧结性能,减小烧结结构偏差,提高结晶度,使所得的烧结矿块度大幅提高,降低硬塊矿的含量,从而提高铁矿石的利用率。
促进工业废渣回收
稀土球化剂还可应用于工业废渣回收。
其中钢厂工业废渣是一种很常见的工业
废料,铁水中含有大量碳和杂质元素,需要通过球团制备冶炼锭,实现资源的综合利用。
稀土球化剂能够稳定住成品对;促进球化和烧结,使得工业废渣的回收利用率得到了显著提高。
抑制汽车尾气的有害物质排放
来自汽车尾气的有害物质,如氮氧化物还会排放大量反应利用率不高,不仅浪
费燃料,还会形成严重的环境污染。
稀土球化剂通过在排气管中添加稀土元素,可抑制有害物质生成,降低排放浓度,有效改善了汽车排放污染问题。
用于陶瓷材料的改性
稀土元素在陶瓷材料中具有很高的应用价值。
稀土球化剂可通过与其他原料一
起混合,对陶瓷材料进行改性,使其具有良好的物理、化学性能,如较高的硬度、密度、均匀性和耐火性等,从而应用于陶瓷、建筑、造纸等行业。
综上所述,稀土球化剂在工业应用中具有广泛的作用,能够对改善工艺性能、
实现资源综合利用和降低环境污染等方面做出积极贡献。
随着科技进步,稀土球化剂也必将不断得到推广和应用。
重稀土球化剂

超厚断面大吨位铸件用钇基重稀土球化剂(DY)一、产品特点及应用范围:该产品与轻稀土同类产品相比,具有抗衰退、抗石墨畸变、抗干扰元素能力强,无球化衰退之忧,能确保铸件性能表里如一,且适用的原料范围宽、不回硫、使磷共晶减少并弥散等特点。
是目前解决由于衰退引起的厚大断面铸件质量不高,特别是本体心部质量不高及质量不稳定,成品率低这一国际铸造难题理想的球化剂。
该产品适用于超厚大断面铸件的生产,其处理工艺与轻稀土球化剂基本一致,适用于铁液温度1400-1550℃,普通冲入法球化,加入量为1.0-1.8%(根据铁液杂质含量高低而定),球化剂入包后上面覆盖硅铁或铁屑、铁板,无需采取专门的脱硫、冷却措施。
球化反应后,无球化衰退现象,且球化率>80%,石墨圆整度好。
二、产品标准1、物理状态⑴产品断面应呈银灰色;⑵产品粒度范围为5-30mm,小于5mm和大于30mm,各不应超过总量的5%;⑶需方对化学成份和粒度有特殊要求,可由供需双方另行协商。
2、包装、标志和质量证明书⑴包装、标志:产品采用内衬塑料袋的双层编织袋包装,有明确的名称和数量标志,25kg/袋,也可根据用户要求选择包装方式;⑵质量证明书:出具符合用户要求并与产品相符的产品质量证明书。
风力发电机关键零部件专用重稀土球化剂(FD)一、产品特点及应用范围:◆抗球化衰退、抗石墨畸变及抗干扰元素能力显著,与公司配套孕育剂联合使用,确保断面>180mm铸件心部球化3级以内,石墨球数>200个/mm2,球化率>85%,可以提高抗低温冲击韧性和抗拉强度值;◆采用特殊工艺和高纯原料生产,元素偏差值小,纯度高,干扰球化的微量元素少而低;◆能适当放宽球墨铸造生铁原料要求,打破以往采用高纯生铁生产该类铸件的传统思路,简便地生产出表里如一的高品质铸件,从而大幅度节约成本;◆残余稀土的范围较普通稀土球化剂宽,具有白口倾向小的优势,且可简化加冷铁等强制冷却工艺;◆适用于电炉铁水工艺,最佳球化温度1420-1450℃,堤坝包冲入法球化,加入量为1.0-1.6%。
球化剂生产质量控制要点浅析
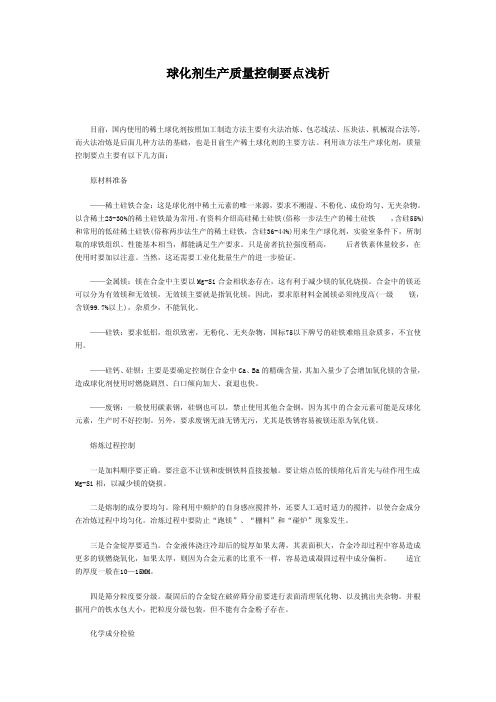
球化剂生产质量控制要点浅析目前,国内使用的稀土球化剂按照加工制造方法主要有火法冶炼、包芯线法、压块法、机械混合法等,而火法冶炼是后面几种方法的基础,也是目前生产稀土球化剂的主要方法。
利用该方法生产球化剂,质量控制要点主要有以下几方面:原材料准备——稀土硅铁合金:这是球化剂中稀土元素的唯一来源,要求不潮湿、不粉化、成份均匀、无夹杂物。
以含稀土23-30%的稀土硅铁最为常用。
有资料介绍高硅稀土硅铁(俗称一步法生产的稀土硅铁,含硅55%)和常用的低硅稀土硅铁(俗称两步法生产的稀土硅铁,含硅36-44%)用来生产球化剂,实验室条件下,所制取的球铁组织、性能基本相当,都能满足生产要求。
只是前者抗拉强度稍高,后者铁素体量较多,在使用时要加以注意。
当然,这还需要工业化批量生产的进一步验证。
——金属镁:镁在合金中主要以Mg-Si合金相状态存在,这有利于减少镁的氧化烧损。
合金中的镁还可以分为有效镁和无效镁,无效镁主要就是指氧化镁,因此,要求原材料金属镁必须纯度高(一级镁,含镁99.7%以上),杂质少,不能氧化。
——硅铁:要求低铝,组织致密,无粉化、无夹杂物,国标75以下牌号的硅铁难熔且杂质多,不宜使用。
——硅钙、硅钡:主要是要确定控制住合金中Ca、Ba的精确含量,其加入量少了会增加氧化镁的含量,造成球化剂使用时燃烧剧烈、白口倾向加大、衰退也快。
——废钢:一般使用碳素钢,硅钢也可以,禁止使用其他合金钢,因为其中的合金元素可能是反球化元素,生产时不好控制。
另外,要求废钢无油无锈无污,尤其是铁锈容易被镁还原为氧化镁。
熔炼过程控制一是加料顺序要正确。
要注意不让镁和废钢铁料直接接触。
要让熔点低的镁熔化后首先与硅作用生成Mg-Si相,以减少镁的烧损。
二是熔制的成分要均匀。
除利用中频炉的自身感应搅拌外,还要人工适时适力的搅拌,以使合金成分在冶炼过程中均匀化。
冶炼过程中要防止“跑镁”、“棚料”和“碰炉”现象发生。
三是合金锭厚要适当。
铸造用稀土球化剂

铸造用稀土球化剂铸造是一种非常重要的制造工艺,可以生产许多日常所需的物品,如汽车零件、家电、建筑材料等。
随着现代科技的发展,铸造工艺也在不断创新和改进。
其中,使用稀土球化剂是一种有效的新型铸造材料,在铸造中发挥着重要作用。
一、什么是稀土球化剂稀土球化剂,就是一种由稀土金属组成的铸造材料。
利用它可以使铸造铁水的温度降低,使铸件的质量得到提高。
使用稀土球化剂可以使铸件表面更光滑,且无缺陷、无孔洞,其性能得到了很大的提升。
二、稀土球化剂的制备1、选料:稀土球化剂由多种稀土金属组成。
在选用稀土金属时,需要考虑到其化学元素的比例、纯度以及触媒活性等因素。
2、混料:将选用的各种稀土金属按照确定的配方进行混合。
混合时需要注意配比的准确性和混合的均匀性。
3、烧结:将混料烧结后成为稀土球化剂。
烧结过程需要保证炉温的稳定,烧结温度也需要根据不同的材料进行调整。
合适的烧结温度可以提高球化剂的质量。
三、稀土球化剂的应用稀土球化剂主要用于铸造中对铸件的加工和制造。
一方面,可以使铸件的表面及内部更加光滑,去除可能存在的气孔,并增强铸件的强度、硬度及表面质量;另一方面,可以省略预处理的洗涤工序,进一步提升了生产效率。
因此,稀土球化剂在钢铁、铸铁等领域得到广泛应用。
四、稀土球化剂的优点1、可增加铸件的硬度与强度,保证产品质量。
2、提高了铸件表面的光洁度,使其质量更为优异。
3、可以降低铸造中的操作温度,从而降低能源消耗,提高了生产效率。
4、稀土球化剂的制备过程对环境影响较小,对环境的污染很少。
在未来,稀土球化剂的应用前景看好,因为其具有优良的性能,也符合环保的发展要求。
我们需要继续深入研究,探索其更广泛的应用场景,以便更好地满足各种铸造需求。
钇基重稀土球化剂牌号

钇基重稀土球化剂牌号钇基重稀土球化剂是一种高效的催化剂,广泛应用于金属冶炼、化工、环保等领域。
本文将从以下几个方面介绍钇基重稀土球化剂的牌号、特点、应用及发展趋势。
一、钇基重稀土球化剂的牌号目前市场上常见的钇基重稀土球化剂牌号有Y-1、Y-2、Y-3、Y-4等。
其中,Y-1牌号适用于冶金行业;Y-2牌号适用于化工行业;Y-3牌号适用于环保行业;Y-4牌号适用于电子行业。
二、钇基重稀土球化剂的特点1.催化效果好:钇基重稀土球化剂具有较高的催化活性和选择性,能够有效促进反应速率,提高产品质量。
2.稳定性高:钇基重稀土球化剂具有良好的热稳定性和耐腐蚀性,能够在高温、强酸、强碱等恶劣环境下长期稳定运行。
3.使用寿命长:钇基重稀土球化剂具有较长的使用寿命,能够降低生产成本,提高经济效益。
三、钇基重稀土球化剂的应用1.金属冶炼领域:钇基重稀土球化剂广泛应用于钢铁、铜、铝、镁等金属冶炼行业,可用于去除金属中的杂质,提高产品质量。
2.化工领域:钇基重稀土球化剂可作为催化剂用于有机合成反应中,如烷基化、酯化、羰基化等反应,能够提高反应速率和产物纯度。
3.环保领域:钇基重稀土球化剂可用于废水处理、废气治理等环保领域,能够有效降解有害物质,净化环境。
4.电子领域:钇基重稀土球化剂可用于制备光学玻璃、磁性材料等电子材料,提高产品的性能和品质。
四、钇基重稀土球化剂的发展趋势1.多元化应用:随着科技的不断发展,钇基重稀土球化剂将会在更多领域得到应用,如新能源、新材料等领域。
2.绿色环保:未来钇基重稀土球化剂的发展将更加注重环保和可持续性,在产品研发、生产过程中将会更加注重环保和资源节约。
3.提高产品质量:钇基重稀土球化剂的研发将更加注重提高产品质量和催化效率,以满足市场需求。
总之,钇基重稀土球化剂是一种具有广泛应用前景和发展潜力的高新技术产品,未来将在更多领域得到应用,并不断提高产品质量和催化效率,为推动经济发展和环境保护做出积极贡献。
轻稀土球化剂中稀土含量的测定

轻稀土球化剂中稀土总量的测定
一、试剂
硝酸:(1M:6.5ml浓硝酸用水稀释到100ml)、(1+1)
高氯酸;氢氟酸;EDTA溶液:0.02M;H2O2:30%;
稀土标准溶液100 ug/m(La30%+Ce70%含硝酸5%),用水稀至10ug/ml;
偶氮胂Ⅲ:0.1%;无水乙醇;
纯铁溶液1mg/ml(称0.1g 加5ml浓硝酸,加热溶解后定容100ml), 100ug/ml现配现用(取母液5ml,用水稀释10倍)。
二、分析步骤
称取试样0.1000g置于聚四氟乙烯烧杯中,加浓硝酸5.0 ml,加热破坏碳化物,然后慢慢滴加氢氟酸,待氮氧化物黄烟全部逸出,再快速滴加氢氟酸(共滴加3ml),加热,待试样溶清,加高氯酸2 ml,加热至高氯酸冒烟后,蒸发近干,冷却,加入(1+1)硝酸10 ml,溶解后转入100 ml 容量瓶中,加水稀释至刻度,摇匀。
分取上述试液10ml用水稀释至100ml, 摇匀待测。
取稀释液5 ml(含RE0~45ug)置于25 ml比色管中,加入0.5ml EDTA,2.5 ml偶氮胂Ⅲ,10 ml无水乙醇,0.5 ml 1M硝酸,摇匀,加水稀释至刻度,用1cm比色皿,在波长648nm处,以试剂空白为参比,测定其吸光度。
用同类稀土硅镁合金与试样同时测试或制作工作曲线(分别取稀土标准0、1 、2、4 ml于一系列25 ml比色管中,各加入100ug/ml纯铁2 ml,以下同试样)。
电炉冶炼用稀土镁硅铁合金球化剂

电炉冶炼用稀土镁硅铁合金球化剂电炉冶炼用稀土镁硅铁合金球化剂:提升冶炼效率的利器概念与背景电炉冶炼作为一种常见的冶金工艺,其在金属冶炼和炉内炉外各个环节中都发挥着重要作用。
球化剂是一种能够提高铁合金的球化率和脱硫率的添加剂,能够使铁合金颗粒呈现出球形,提高铁合金的溶解度和液态脱硫的效果,从而提高冶炼效率和冶炼质量。
稀土镁硅铁合金是一种常用的球化剂,具有优异的球化效果和脱硫效果。
稀土镁硅铁合金由稀土、镁、硅和铁组成,其中稀土元素的添加能够降低合金的熔点和提高球化效果,镁元素能够提高合金的热稳定性和球化效果,硅元素能够提高合金的脱硫效果。
稀土镁硅铁合金在电炉冶炼中被广泛应用,成为一种重要的冶炼辅助剂。
优点与应用1. 提高球化率:稀土镁硅铁合金作为球化剂能够使铁合金颗粒呈现出球形,提高球化率,减少合金中的脆性组织,提高合金的强度和塑性。
2. 提高脱硫效果:稀土镁硅铁合金中的稀土元素具有很强的脱硫能力,能够加速脱硫反应,降低合金中的硫含量,提高合金的纯度和质量。
3. 降低热稳定性:稀土镁硅铁合金中的镁元素能够提高合金的热稳定性,减少合金的热脆性,提高合金的耐热性和耐蚀性。
稀土镁硅铁合金球化剂的应用非常广泛,特别是在高炉冶炼、转炉冶炼和电炉冶炼中,能够有效提高冶炼效率和冶炼质量。
稀土镁硅铁合金球化剂可用于冶炼各类铸造铁、钢铁和铸钢等金属材料,其应用范围广泛,效果显著。
个人观点与理解稀土镁硅铁合金球化剂的应用为电炉冶炼带来了许多优势。
稀土镁硅铁合金球化剂能够提高球化率,使铁合金颗粒呈现出球形,提高合金的力学性能,提高铸件的质量,降低产品的缺陷率。
稀土镁硅铁合金球化剂能够提高脱硫效果,加速脱硫反应,降低硫含量,提高合金的纯度,改善合金的性能。
稀土镁硅铁合金球化剂中的镁元素能够提高合金的热稳定性,减少合金的瓦斯冒口和热脆性。
总结与回顾电炉冶炼用稀土镁硅铁合金球化剂是一种重要的冶炼辅助剂,其应用在电炉冶炼中具有重要意义。
球墨铸铁用稀土球化剂

球墨铸铁用稀土球化剂稀土球化剂是玄武岩、珍珠岩、田黄石等矿石中所含的稀土元素经过分离与提纯后加入球墨铸铁中,使铸铁中的石墨球化,因此也称石墨球化剂。
球墨铸铁是一种高强度、高韧性、高耐腐蚀性和变形性的铁合金,具有良好的机械性能和加工性能。
球墨铸铁的制造过程中加入适量的稀土球化剂,可以改善铸铁的组织结构,精细化石墨,提高铸铁的抗拉强度、塑性和韧性。
球墨铸铁的优点1.高强度:球墨铸铁的拉伸强度最高可达700MPa,是一般灰铸铁的2倍以上,可以满足复杂应用场合的高强度要求。
2.良好的韧性:球墨铸铁的断裂韧性高,抗震性能良好,可以防止零部件在疲劳循环作用下断裂。
3.耐腐蚀性强:球墨铸铁具有环境适应性强、抵抗腐蚀和疲劳的能力,可以在恶劣的环境中保持较长的使用寿命。
4.高温性能好:球墨铸铁可以在高温下长时间保持良好的机械性能和变形性能,可以适应高温工况下的应用需求。
球墨铸铁的生产工艺球墨铸铁的生产工艺主要包括融化、置球、浇注、冷却等步骤。
其中,置球工艺是球墨铸铁生产中重要的一个环节。
置球工艺分为两种方法:静态处理和动态处理。
静态处理是在高温下加入球化剂,然后静置一段时间,等待球化发生;动态处理是在高温下加入球化剂,然后通过搅拌和钛加入等方式促进球化的发生。
球化剂的作用1.改善石墨的形态:稀土元素可以与石墨相互作用,形成稳定的一层覆盖物,使石墨颗粒细小化,直径一般不超过10um,从而提高铸铁的强度和韧性。
2.提高铸铁的抗脆性:稀土元素可以改变铁素体和针状母体的比例,形成更为均匀的铁素体,提高铸铁的延展性和韧性。
3.促进铁素体的析出:稀土元素可以促进铁素体的析出,从而提高球墨铸铁的硬度和耐磨性。
球化剂的种类和作用球化剂的种类主要有钙基球化剂、铝基球化剂、锆基球化剂、镁基球化剂、稀土球化剂等。
稀土球化剂是目前广泛使用的一种球化剂,主要由稀土元素组成,具有良好的石墨球化效果和机械性能提高效果。
球化剂的使用技术及注意事项球化剂的使用技术需要注意以下几个问题:1.球化剂的选择:不同类型的球化剂有着不同的石墨球化效果和机械性能提高效果,应根据具体用途和要求选择合适的球化剂。
- 1、下载文档前请自行甄别文档内容的完整性,平台不提供额外的编辑、内容补充、找答案等附加服务。
- 2、"仅部分预览"的文档,不可在线预览部分如存在完整性等问题,可反馈申请退款(可完整预览的文档不适用该条件!)。
- 3、如文档侵犯您的权益,请联系客服反馈,我们会尽快为您处理(人工客服工作时间:9:00-18:30)。
稀土球化剂知道稀土球化剂的质量和选用球墨铸铁现在几乎在所有的铸铁厂都有生产,而作为生产球墨铸铁必不可少的球化剂亦越来越受到普遍关注。
本文从球化剂的上产和使用两个角度来探讨说明什么样的球化剂是好的,应该在铸造过程中热核选用球化剂,也就是球化极品值得的判定和选用问题。
1、球化剂及球化元素的作用尽管国外球化剂的种类很多,但在我们国目前应用最多的还是稀土镁类合金,现主要论述该类合金及其球化元素的作用。
1、1球化元素及反球化元素1、1、1球化元素的作用素。
球化元素一般有以下共同性质:(1)元素最外电子层上有一个或两个价电子,次层有8个电子。
这种电子结构使元素与硫、氧和碳有较强的亲和力,反映产物稳定,能显著减少贴水中的硫和氧。
(2)元素在铁水中溶解度低,凝固过程中有显著偏析倾向。
(3)虽然和碳有一定亲和力,但在石墨晶格溶解度低。
根据以上特点,Mg,Ce,Y,Ca属于有效球化元素。
度比铁水小,熔点650度,沸点1108度,在铁水的处理温度下,镁产生的蒸气压力很高(超过 1Mpa).镁的熔解热为21J/g,蒸发潜热为406J/g。
因此,镁加入铁水时,要产生汽化,使铁水翻腾。
二是与硫、氧有很强的亲和力。
所生成的 MgO和MgS熔点高,密度也远小于铁,容易与铁水分离,因此镁处理后的铁水,硫和氧的含量都很低;三是在铁水凝固过程中有偏析于石墨的倾向,当其在铁水中的残留量超过0.035%时,使末就可以球化,但当镁残留量超过0.07%时,一部分镁偏析于晶界,并于晶界中的碳、磷等发生放热反应,生成MgC2、 Mg2C3、Mg3P2等。
残留镁量更多时,晶间碳化物增多。
稀土族元素对石墨球化有显著作用的是轻稀土元素中的铈和重稀土中的钇。
一是稀土元素的沸点均比镁高,加入铁水中时,不会引起铁水的翻腾和喷溅;二是铈和钇基稀土元素有比镁更强的脱硫脱氧能力,生成的硫化稀土、氧化稀土等化合物熔点高、稳定性好;三是稀土元素与铁水中的球化干扰元素也能形成稳定的化合物,因此含稀土的球化剂比镁球化剂的抗干扰能力强。
稀土元素残留量对石墨球化有明显的影响。
轻稀土处理过共晶铁水,当残留铈含量0.04%时,石墨就可以球化,而且很稳定;处理亚共晶铁水时,轻稀土加入量要增加。
轻稀土处理得球铁,石墨圆整度比镁处理得球铁要差,并出现碎块状石墨;另外轻稀土处理得球铁白口倾向大,因此需要控制其加入量。
重稀土钇本身熔点高,其脱氧除硫产生的氧化物、硫化物在高温下比较稳定,因此其抗球化衰退能力很强。
1400度的铁水保温1小时,球化率降低不超过10%,含硫0.06% 的铁水,用钇基重稀土合金处理后,能得到完整的球状石墨。
铁水中残留钇0.10—0.15%,石墨球化良好;低于此限度,随钇量减少一次出现不规则石墨和蠕虫状石墨;残留钇超过0.15而低于0.30%时,白口倾向逐渐增大,石墨圆整度变差,并在更高残留量时出现YTe4。
和硫的结合而间接实现的。
与镁相比,钙与硫、氧的亲和力更强,能够有效的脱硫除氧。
钙残留量很低时,石墨分枝倾向增加,残留量较多时,可是使石墨尺寸减小,分枝倾向降低。
钙残留量达到0.2%时,白口倾向明显加大。
1、1、2反球化元素(球化干扰元素)的作用该类元素主要是指破坏和阻碍使石墨球化的元素,按其作用机理大概可以分三类:一是消耗型反球化元素,如硫、氧、硒、碲等,它们与镁、稀土元素生成化合物,通过消耗球化元素来阻止球状石墨的形成。
二是境界偏析的球化干扰元素,包括锡、锑、砷、铜、硼、钛、铝等,这些元素富集到晶界,促使碳在共晶后期结晶时,形成畸形的枝晶状石墨,如果这些元素含量较高,也可在共晶中期促成石墨畸变,形成团状或厚片状石墨。
三是一些中间球化干扰元素,如铝、铋,它们在含量较低时主演通过偏析作用促成石墨畸变,含量较高时也能消耗球化元素。
另外,反球化元素对球铁基体也有不同的影响。
Te\B强烈促进白口的形成,As\Sn\Sb\Pb\Bi稳定珠光体,Al\Zr促进铁素体形成,Se 无影响。
1、2球化元素的配置和球化剂的种类镁、稀土和钙,是目前公认的有促进石墨球化的能力,但如何结合工业生产实际来制备和使用,既保证球化剂的球化能力,又要在生产中容易制取,原料经济,使用方便,便成为配制和使用球化剂的的原则。
1、2、1球化元素的配置——成分配制原则和特点:要有强烈的球化能力,这显然要以镁为主,镁的沸点低,加入铁水中可以使铁水剧烈翻腾,反应上下均匀;配成合金后增加比重,使其在铁水中不易上浮,可以减少镁的氧化和烧损。
——消化中和反球化元素能力,稀土元素有很强的脱硫除气、净化铁水和消除反球化元素的能力,而且我国稀土资源丰富,获取原料成本较低。
——球化剂反应平稳,易于操作。
钙虽然不能作为球化剂单独使用,但用它和和镁、稀土配成复合球化剂,就既可以减少球化剂中MgO的含量,使球化处理平稳,还可以减少因稀土造成的较大白口倾向。
因此,配制球化剂成分的原则和特点,就是要发挥各种球化元素的长处,来提高球化效果,并通过调整球化元素的含量来满足不同生产条件、不同结构铸件的需求。
1、2、2球化剂的种类按照球化和反球化元素配置的原则,国外曾先后开发了多种球化剂,大体上有以下几种:————纯镁:这是国外常用的球化剂,国应用比较少。
压力加镁制取球铁,优点和缺点同样明显。
————铜镁、镍镁:我国早期使用的该合金,但成本高,回炉料中铜和镍积累难以控制,造成韧性下降。
————硅镁铁合金:一般镁含量最低3.5—4.5%,最高10—15%,常用的合金是镁5—10%、硅42—47%,其余为铁。
含镁量越低,球化反应越平稳,镁回收率越高(含镁4%的能比9%个合金镁回收率提高10%),但是低镁球化剂是铁水的增硅量加大。
该球化剂是用于处理硫和反球化元素含量较低的铁水,浇注中等断面厚度的铸件。
目前在国要大批量用于制造球墨铸铁将会与我国铸造企业的生产条件和原材料采购产生一定的矛盾。
————稀土镁类合金:包括稀土硅镁、稀土钙镁、稀土铜镁等合金,是我国工程技术人员立足我国实际,在六十年代初研制开发的稀土镁类系列合金球化剂,它们综合了各种球化元素的优缺点,尤其是稀土镁钙合金,是目前国应用量大面广的主要球化剂,从而走出了一条适合我国国情的球墨铸铁制造技术道路。
2、球化剂质量的生产控制要点目前,国使用的稀土球化剂按照加工制造方法主要有火法冶炼、包芯线法、压块法、机械混合法等,而火法冶炼是后面几种方法的基础,也是生产稀土球化剂的主要方法。
利用该方法生产球化剂,质量控制要点主要有以下几方面:2、1原材料准备——稀土硅铁合金:这是球化剂中稀土元素的唯一来源,要求不潮湿、不粉化、成份均匀、无夹杂物。
以含稀土23-30%的稀土硅铁最为常用。
有资料介绍高硅稀土硅铁(俗称一步法生产的稀土硅铁,含硅55%)和常用的低硅稀土硅铁(俗称两步法生产的稀土硅铁,含硅36-44%)用来生产球化剂,实验室条件下,所制取的球铁组织、性能基本相当,都能满足生产要求。
只是前者抗拉强度稍高,后者铁素体量较多,在使用时要加以注意。
当然,这还需要工业化批量生产的进一步验证。
——金属镁:镁在合金中主要以Mg-Si合金相状态存在,这有利于减少镁的氧化烧损。
合金中的镁还可以分为有效镁和无效镁,无效镁主要就是指氧化镁,因此,要求原材料金属镁必须纯度高(一级镁,含镁99.7%以上),杂质少,不能氧化。
——硅铁:要求低铝,组织致密,无粉化、无夹杂物,国标75以下牌号的硅铁难熔且杂质多,不宜使用。
——硅钙、硅钡:主要是要确定控制住合金中Ca、Ba的精确含量,其加入量少了会增加无效氧化镁的含量,造成球化剂使用时燃烧剧烈、白口倾向加大、衰退也快。
——废钢:一般使用碳素钢,硅钢也可以,禁止使用其他合金钢,因为其中的合金元素可能是反球化元素,生产是不好控制。
另外,要求废钢无油无锈无污责,尤其是铁锈容易被镁还原为氧化镁。
2、2熔炼过程控制一是加料顺序要正确。
要注意不让镁和废钢铁料直接接触。
要让熔点低的镁熔化后首先与硅作用生成Mg-Si相,以减少镁的烧损。
二是熔制的成分要均匀。
除利用中频炉的自身感应搅拌外,还要人工适时适力的搅拌,以使合金成分在冶炼过程中均匀化。
冶炼过程中要防止“跑镁”、“棚料”和“碰炉”现象发生。
三是合金锭厚要适当。
合金液体浇注冷却后的锭厚如果太薄,其表面积大,合金冷却过程中容易造成更多的镁燃烧氧化,如果太厚,则因为合金元素的比重不一样,容易造成凝固过程中成分偏析。
适宜的厚度一般在10—15MM。
四是筛分粒度要分级。
凝固后的合金锭在破碎筛分前要进行表面清理氧化物、以及挑出夹杂物。
并根据用户的铁水包大小,把粒度分级包装,但不能有合金粉子存在。
2、3化学成分检验一个合格的球化剂,除了外观致密、没有夹杂物等之外,更重要的还是其化学成分的含量及均匀性。
球化剂中,除了常规的Re,Mg,Si,Ca等元素的分析之外,生产厂和使用厂常常忽略了对合金中MgO的分析。
这也与没有统一的MgO国家分析标准有关,同一种合金在不同的厂家用不同的分析方法,得出的成分结论不一样。
这就要求合金生产厂和铸造厂用户要达成一个统一的验收分析标准来共同遵守。
3、球化剂质量的评价什么样的球化剂是最好的?这往往会成为诸多铸造厂的常年话题。
其实,可以说,球化剂没有最好的,只有适合的,适合自己的就是最好的。
那么,到底该如何评价球化剂的质量哪?有资料从球化元素在铁液中的反应热力学、反应动力学和球化剂生产过程质量影响因素、铸造厂使用过程工艺影响因素,提出了判定球化剂质量的标准如下:(1)球化元素与铁水中硫、氧等元素的亲和力。
亲和力强,并与之形成化合物,作为铁液凝固过程中的外来核心,如稀土、镁、钙等球化元素。
(2)球化元素改变石墨形态由片状变为球状的能力。
(3)球化剂的密度、沸点均低于铁液。
密度小能够在铁液中自动上浮,沸点低于铁液处理温度,镁能在该处理温度下转化为气态,有自搅拌作用,从而改善球化效果。
(4)球化剂中氧化镁含量等于镁含量的10%左右。
(5)球化剂致密、无偏析、无缩孔缩松、不粉化。
(6)球化剂粒度分布均匀,无粉状合金,钝角多变形颗粒为好。
(7)球化剂不同批次的成分波动要小。
上述条件基本涵盖了球化剂生产和使用过程中的质量要求,因此可以作为供需双方判定质量的统一标准。
4、球化剂的选用以上球化剂的质量评价标准,也可以说就是我们选用球化剂的依据,但那是按照普遍原理、普遍现象来说明,具体到球化剂的选用问题,现按照我们铸造厂的习惯来进行分析。
铸造厂在球化剂使用中遇到最多的普遍问题主要有:(1)球化剂成分不准,并且波动。
(2)球化剂粉化合金粒度不合要求。
(3)球化剂不致密、上浮快,烧损严重。
(4)MgO含量过高,反应过于激烈,球化处理不良,球化剂加入量过大。
(5)球化处理后衰退快。
(6)球化后白口倾向大。