凸轮机构基本参数的设计
凸轮机构的设计和计算详解

凸轮机构的设计和计算详解1. 引言凸轮机构是一种常见的机械传动装置,通过凸轮的运动来实现对其他部件的控制和驱动。
凸轮机构广泛应用于发动机、机械加工、自动化设备等领域。
在本文中,我们将详细介绍凸轮机构的设计和计算方法。
2. 凸轮机构的基本原理凸轮机构由凸轮、从动件和控制件组成。
凸轮通过旋转或移动的方式,驱动从动件进行线性或旋转运动。
不同凸轮形状和运动方式将实现不同的功能。
3. 凸轮的设计要点凸轮的设计涉及凸轮形状、凸轮面积、凸轮运动规律等方面。
在进行凸轮设计时,需要考虑以下要点:•运动要求:根据从动件需要的运动类型(线性或旋转)、速度和加速度要求,确定凸轮的形状和运动规律。
•动态负载:凸轮在运动过程中所承受的动态负载应被考虑在内,以确保凸轮的强度和耐久性。
•材料选择:根据凸轮的工作条件和负载要求,选择适当的材料来制造凸轮,以保证其可靠性和寿命。
4. 凸轮机构的计算方法4.1 凸轮剖面的计算凸轮剖面的计算是凸轮机构设计中的重要一环。
根据凸轮的运动规律和从动件的运动要求,可以进行凸轮剖面的计算。
常用的凸轮剖面计算方法有:•凸轮剖面生成法:根据从动件的运动要求,通过几何构造和插值计算,生成凸轮剖面。
•凸轮运动分析法:通过分析凸轮的运动规律和从动件的运动要求,推导出凸轮剖面的数学表达式。
4.2 凸轮机构的运动学分析凸轮机构的运动学分析是确定凸轮机构各部件的运动规律和参数的过程。
通过运动学分析,可以计算凸轮机构的几何关系、速度和加速度等。
常用的凸轮机构运动学分析方法有:•图形法:通过绘制凸轮机构的运动示意图和运动曲线,分析凸轮机构的运动规律。
•解析法:通过建立凸轮机构的运动学方程,推导出各部件的运动参数,并进行计算。
4.3 凸轮机构的强度计算凸轮机构的强度计算是为了确定凸轮所承受的载荷是否安全,并选择适当的材料和结构来满足设计要求。
在强度计算中,需要考虑凸轮的静载荷、动载荷和疲劳载荷等。
常用的凸轮机构强度计算方法有:•静态强度计算:通过分析凸轮在静态载荷下的应力和变形情况,确定凸轮的强度和刚度。
凸轮设计标准
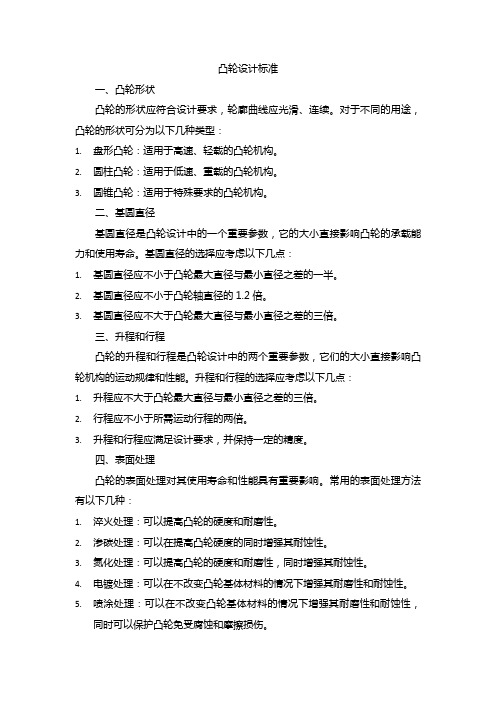
凸轮设计标准一、凸轮形状凸轮的形状应符合设计要求,轮廓曲线应光滑、连续。
对于不同的用途,凸轮的形状可分为以下几种类型:1.盘形凸轮:适用于高速、轻载的凸轮机构。
2.圆柱凸轮:适用于低速、重载的凸轮机构。
3.圆锥凸轮:适用于特殊要求的凸轮机构。
二、基圆直径基圆直径是凸轮设计中的一个重要参数,它的大小直接影响凸轮的承载能力和使用寿命。
基圆直径的选择应考虑以下几点:1.基圆直径应不小于凸轮最大直径与最小直径之差的一半。
2.基圆直径应不小于凸轮轴直径的1.2倍。
3.基圆直径应不大于凸轮最大直径与最小直径之差的三倍。
三、升程和行程凸轮的升程和行程是凸轮设计中的两个重要参数,它们的大小直接影响凸轮机构的运动规律和性能。
升程和行程的选择应考虑以下几点:1.升程应不大于凸轮最大直径与最小直径之差的三倍。
2.行程应不小于所需运动行程的两倍。
3.升程和行程应满足设计要求,并保持一定的精度。
四、表面处理凸轮的表面处理对其使用寿命和性能具有重要影响。
常用的表面处理方法有以下几种:1.淬火处理:可以提高凸轮的硬度和耐磨性。
2.渗碳处理:可以在提高凸轮硬度的同时增强其耐蚀性。
3.氮化处理:可以提高凸轮的硬度和耐磨性,同时增强其耐蚀性。
4.电镀处理:可以在不改变凸轮基体材料的情况下增强其耐磨性和耐蚀性。
5.喷涂处理:可以在不改变凸轮基体材料的情况下增强其耐磨性和耐蚀性,同时可以保护凸轮免受腐蚀和摩擦损伤。
6.其他处理方法:如离子注入、激光熔覆等新型表面处理方法可以提高凸轮的性能和使用寿命。
在选择表面处理方法时,应根据实际需求和使用条件进行选择。
7.精度要求:凸轮的精度对其运动规律和性能具有重要影响。
根据不同的用途和使用条件,凸轮的精度要求可分为以下几种等级:8.一般用途凸轮:精度要求较低,适用于一般机械传动系统中的凸轮机构。
9.高精度凸轮:精度要求较高,适用于精密机械传动系统中的凸轮机构,如钟表、光学仪器等。
机械原理大作业凸轮机构设计

机械原理大作业凸轮机构设计一、凸轮机构概述凸轮机构是一种常见的传动机构,它通过凸轮的旋转运动,带动相应零件做直线或曲线运动。
凸轮机构具有结构简单、运动平稳、传递力矩大等优点,在各种机械设备中得到广泛应用。
二、凸轮基本结构1. 凸轮凸轮是凸起的圆柱体,通常安装在主轴上。
其表面通常为圆弧形或其他曲线形状,以便实现所需的运动规律。
2. 跟随件跟随件是与凸轮配合的零件,它们通过接触面与凸轮相互作用,并沿着规定的路径做直线或曲线运动。
跟随件可以是滑块、滚子、摇臂等。
3. 连杆连杆连接跟随件和被驱动部件,将跟随件的运动转化为被驱动部件所需的运动。
连杆可以是直杆、摇杆等。
三、凸轮机构设计要点1. 几何参数设计设计时需要确定凸轮半径、角度和曲率半径等参数,这些参数的选择将直接影响凸轮机构的运动规律和性能。
2. 运动规律设计根据被驱动部件的运动要求,选择合适的凸轮曲线形状,以实现所需的运动规律。
3. 稳定性设计在设计凸轮机构时,需要考虑其稳定性。
例如,在高速旋转时,可能会发生跟随件脱离凸轮或者产生振动等问题,因此需要采取相应措施提高稳定性。
4. 材料和制造工艺设计在材料和制造工艺方面,需要考虑凸轮机构所承受的载荷和工作环境等因素,选择合适的材料和制造工艺。
四、几种常见凸轮机构及其应用1. 摇臂式凸轮机构摇臂式凸轮机构由摇臂、连杆和被驱动部件组成。
它通常用于实现直线运动或旋转运动,并且具有结构简单、运动平稳等优点。
摇臂式凸轮机构广泛应用于各种机械设备中,如发动机气门控制系统、纺织设备等。
2. 滑块式凸轮机构滑块式凸轮机构由凸轮、滑块、连杆和被驱动部件组成。
它通常用于实现直线运动,并且具有结构简单、运动平稳等优点。
滑块式凸轮机构广泛应用于各种机械设备中,如冲压设备、印刷设备等。
3. 滚子式凸轮机构滚子式凸轮机构由凸轮、滚子、连杆和被驱动部件组成。
它通常用于实现圆弧形运动,并且具有运动平稳、传递力矩大等优点。
滚子式凸轮机构广泛应用于各种机械设备中,如汽车发动机气门控制系统等。
凸轮机构的主要参数
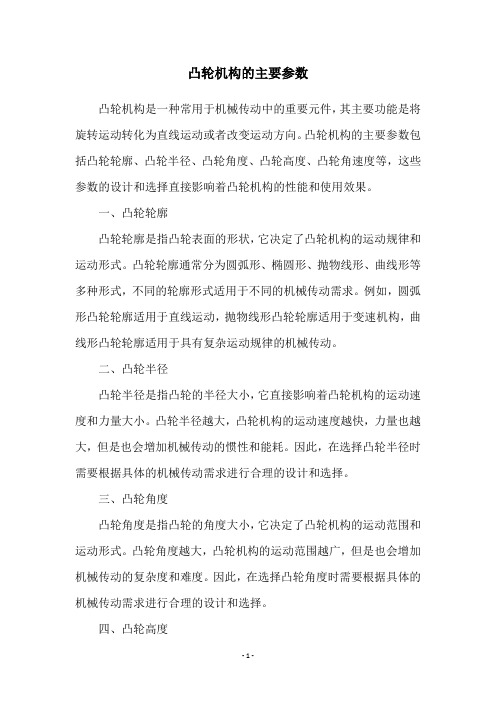
凸轮机构的主要参数凸轮机构是一种常用于机械传动中的重要元件,其主要功能是将旋转运动转化为直线运动或者改变运动方向。
凸轮机构的主要参数包括凸轮轮廓、凸轮半径、凸轮角度、凸轮高度、凸轮角速度等,这些参数的设计和选择直接影响着凸轮机构的性能和使用效果。
一、凸轮轮廓凸轮轮廓是指凸轮表面的形状,它决定了凸轮机构的运动规律和运动形式。
凸轮轮廓通常分为圆弧形、椭圆形、抛物线形、曲线形等多种形式,不同的轮廓形式适用于不同的机械传动需求。
例如,圆弧形凸轮轮廓适用于直线运动,抛物线形凸轮轮廓适用于变速机构,曲线形凸轮轮廓适用于具有复杂运动规律的机械传动。
二、凸轮半径凸轮半径是指凸轮的半径大小,它直接影响着凸轮机构的运动速度和力量大小。
凸轮半径越大,凸轮机构的运动速度越快,力量也越大,但是也会增加机械传动的惯性和能耗。
因此,在选择凸轮半径时需要根据具体的机械传动需求进行合理的设计和选择。
三、凸轮角度凸轮角度是指凸轮的角度大小,它决定了凸轮机构的运动范围和运动形式。
凸轮角度越大,凸轮机构的运动范围越广,但是也会增加机械传动的复杂度和难度。
因此,在选择凸轮角度时需要根据具体的机械传动需求进行合理的设计和选择。
四、凸轮高度凸轮高度是指凸轮表面的高度大小,它直接影响着凸轮机构的运动速度和力量大小。
凸轮高度越大,凸轮机构的运动速度越快,力量也越大,但是也会增加机械传动的惯性和能耗。
因此,在选择凸轮高度时需要根据具体的机械传动需求进行合理的设计和选择。
五、凸轮角速度凸轮角速度是指凸轮旋转的角速度大小,它直接影响着凸轮机构的运动速度和力量大小。
凸轮角速度越大,凸轮机构的运动速度越快,力量也越大,但是也会增加机械传动的惯性和能耗。
因此,在选择凸轮角速度时需要根据具体的机械传动需求进行合理的设计和选择。
综上所述,凸轮机构的主要参数包括凸轮轮廓、凸轮半径、凸轮角度、凸轮高度、凸轮角速度等,这些参数的设计和选择直接影响着凸轮机构的性能和使用效果。
机械原理 凸轮机构基本参数设置_OK
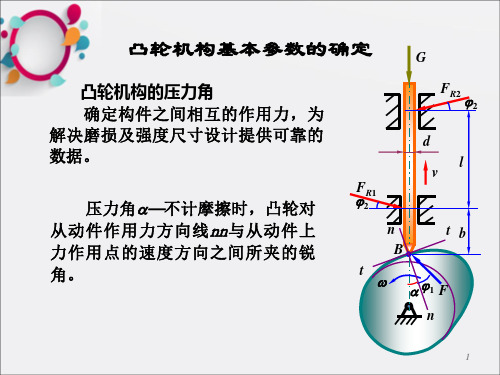
3
盘形凸轮机构参数的确定 (一) 移动从动件盘形凸轮机构
基本尺寸的设计 1. 压力角与凸轮基圆的关系
压力角对凸轮机构的受力状况有 直接影响,在运动规律选定之后, 它主要取决于凸轮机构的基本结构 尺寸。
第4.4节(凸轮机构基本尺寸的设计)

第四节 凸轮机构基本尺寸设计无论是作图法还是解析法,在设计凸轮廓线前,除了需要根据工作要求选定从动件的运动规律外,还需要确定凸轮机构的一些基本参数,如基圆半径b r 、偏距e 、滚子半径r r 等。
一般来讲,这些参数的选择除了应保证从动件能够准确地实现预期的运动规律外,还应当使机构具有良好的受力状况和紧凑的结构。
本节讨论凸轮机构基本尺寸设计的原则和方法。
一、移动滚子从动件盘形凸轮机构1. 压力角同连杆机构一样,压力角也是衡量凸轮机构传力特性好坏的一个重要参数。
所谓凸轮机构的压力角,是指在不计摩擦的情况下,凸轮对从动件作用力的方向线与从动件上力作用点的速度方向之间所夹的锐角。
对于图4-22所示的移动滚子从动件盘形凸轮机构来说,过滚子中心所作理论廓线的法线nn 与从动件运动方向之间的夹角α就是压力角。
(1)压力角与作用力的关系 由图4-22可以看出,凸轮对从动件的作用力F 可以分解成两个分力,即沿着从动件运动方向的分力F '和垂直于运动方向的分力F ''。
只有前者是推动从动件克服载荷的有效分力,而后者将增大从动件与导路间的摩擦,它是一种有害分力。
压力角α越大,有害分力越大。
当压力角α增大到某一数值时,有害分力所引起的摩擦阻力将大于有效分力F ',这时无论凸轮给从动件的作用力有多大,都不能推动从动件运动,即机构将发生自锁。
因此为减小侧向推力,避免自锁,压力角α应越小越好。
图4-22 凸轮机构的压力角(2)压力角与机构尺寸的关系 设计凸轮时,除了应使机构具有良好的受力状况外,还希望机构结构紧凑。
而凸轮尺寸的大小取决于凸轮基圆半径的大小。
在实现相同运动规律的情况下,基圆半径越大,凸轮的尺寸也越大。
因此,要获得轻便紧凑的凸轮机构,就应当使基圆半径尽可能地小。
但是基圆半径的大小又和凸轮机构的压力角有直接的关系。
下面以图4-22为例来说明这种关系。
图中,过滚子中心B 所作理论廓线的法线nn 与过凸轮轴心0A 所作从动件导路的垂线交于P 点,由瞬心定义可知,该点即为凸轮与从动件在此位置时的瞬心,且ϕωd ds v P A ==0。
凸轮机构的设计毕业设计
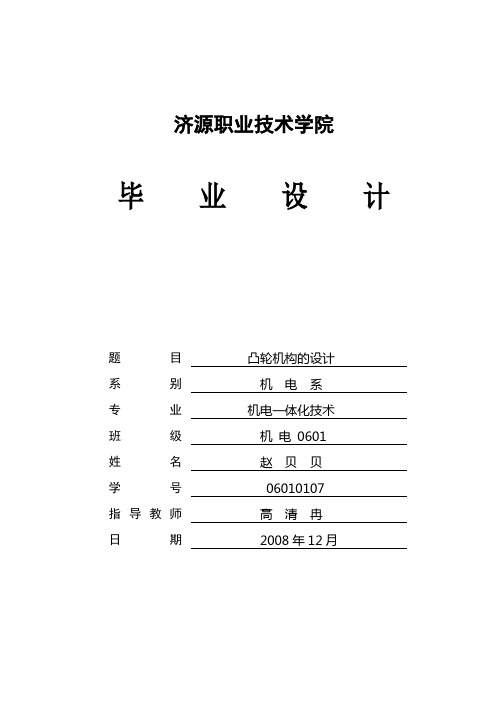
济源职业技术学院毕业设计题目凸轮机构的设计系别机电系专业机电一体化技术班级机电0601姓名赵贝贝学号06010107指导教师高清冉日期2008年12月设计任务书设计题目:凸轮机构的设计设计要求:原始条件:内燃机中的凸轮,该凸轮满足以下条件。
凸轮以等角速度逆时针回转,及基圆半径rb=30mm,及从动件滚子圆半径rt=8mm。
应完成的任务: 1、凸轮轮廓设计 2、凸轮零件图设计进度要求:第一周:确定题目;第二周:搜集凸轮机构相关资料及前期准备工作;第三周:凸轮曲线设计及计算;第四周:初步拟定设计的草稿;第五周:毕业论文的整体校核、修改;第六周:论文完善、定稿及打印装订;第七周:毕业答辩。
指导教师(签名):摘要在各种机器中,特别是自动化机器中,为实现某些特殊或复杂的运动规律,常采用凸轮机构。
凸轮机构通常是由原动件凸轮、从动件和机件组成。
其功能是将凸轮的连续转动或移动转换为从动件的连续或不连续的移动或摆动。
与连杆机构相比,凸轮机构便于准确的实现给定的运动规律。
所以凸轮机构被广泛地应用,以实现各种复杂的运动要求。
本设计主要设计内燃机中的凸轮机构,内燃机中的凸轮以等角速度回转,其轮廓驱使从动件(阀杆)按预期的运动规律启闭阀门,以控制可燃物进入汽缸或排除废气。
至于气阀开启或关闭时间的长短及其速度的变化规律,则取决于凸轮轮廓线的形状。
根据从动件运动规律,来设计内燃机中滚子盘形凸轮,使其得到预期的运动规律。
关键词:凸轮机构分类,从动件运动规律,位移曲线,轮廓曲线,结构及材料目录设计任务书 (I)摘要 (II)1凸轮机构的应用及分类 (1)1.1凸轮机构的应用 (1)1.2凸轮机构的分类 (1)2 从动件常用运动规律 (3)2.1 凸轮机构的基本参数 (3)2.2 从动件常用的运动规律 (4)3盘形凸轮轮廓曲线的设计 (8)3.1凸轮廓线设计的基本原理 (8)4凸轮机构的结构及材料 (11)4.1 凸轮的结构 (11)4.2从动件结构 (11)4.3凸轮和滚子的材料 (11)4.4凸轮的零件图 (13)结论 (14)致谢 (15)参考文献 (16)1凸轮机构的应用及分类1.1凸轮机构的应用(工程应用案例)内燃机中的凸轮机构;自动车床上的走刀机构分度转位机构等。
机械基础-设计凸轮
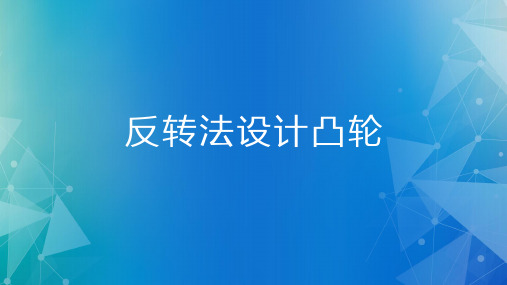
拓展任务
(1)运动失真 从减小接触应力的角度来看,滚子半径越大越好,但是滚子增大后
对凸轮实际轮廓线有很大的影响。 运动失真的概念:凸轮的实际轮廓,不能使从动件实现预期给定的
运动规律的现象。
(2)防止凸轮机构运动失真的条件 ρmin>rT
二、总结
设计基圆半径
凸轮许用压力角 凸轮基圆半径ro
设计凸轮机构
一、设计凸轮
(二)凸轮轮廓曲线的设计
6.凸轮孔及键槽的设计
在凸轮参数中,输入凸
轮半径20mm,孔直径 20mm,凸轮厚度30mm,
勾选“自定义键槽”,在自 定义键槽”对话框中,直径 输入“20”,点击“保存并 退出”。
一、设计凸轮
(三)凸轮设计结果
凸轮对话框
设计结果
拓展任务
设计一尖顶对心直动凸轮机构,实现:水平、垂直推料顶杆作直线往复运
构产生自锁现象。
凸轮压力角
一、设计凸轮
(一)设计基圆半径
1.凸轮许用压力角
(3)许用压力角[α] 最大压力角αmax≤[α]
对于回程,因载荷很小,且从动件在锁合力作用 下返回,不易出现自锁,通常只需校核推程压力角。
一般设计中,直动从动件推程中的 [α]=30º~38º, 摆动从动件推程[α]=40º~45º。
凸轮压力角
一、设计凸轮
(一)设计基圆半径
2.凸轮基圆半径ro
h/r0= 基圆1 半径r0=20
Байду номын сангаас
凸轮模拟图
一、设计凸轮
(二)凸轮轮廓曲线的设计
1.打开插件
打开今日制造插件,点 击“辅助设计工具”,然后 点击“三维设计”,找到凸 轮项目,“打开插件”。
一、设计凸轮
- 1、下载文档前请自行甄别文档内容的完整性,平台不提供额外的编辑、内容补充、找答案等附加服务。
- 2、"仅部分预览"的文档,不可在线预览部分如存在完整性等问题,可反馈申请退款(可完整预览的文档不适用该条件!)。
- 3、如文档侵犯您的权益,请联系客服反馈,我们会尽快为您处理(人工客服工作时间:9:00-18:30)。
凸轮机构基本参数的设计前节所先容的几何法和解析法设计凸轮轮廓曲线,其基圆半径r0、直动从动件的偏距e或摆动从动件与凸轮的中心距a、滚子半径rT等基本参数都是预先给定的。
本节将从凸轮机构的传动效率、运动是否失真、结构是否紧凑等方面讨论上述参数的确定方法。
1 凸轮机构的压力角和自锁图示为偏置尖底直动从动件盘形凸轮机构在推程的一个位置。
Q为从动件上作用的载荷(包括工作阻力、重力、弹簧力和惯性力)。
当不考虑摩擦时,凸轮作用于从动件的驱动力F是沿法线方向传递的。
此力可分解为沿从动件运动方向的有用分力F'和使从动件紧压导路的有害分力F''。
驱动力F与有用分力F'之间的夹角a(或接触点法线与从动件上力作用点速度方向所夹的锐角)称为凸轮机构在图示位置时的压力角。
显然,压力角是衡量有用分力F'与有害分力F''之比的重要参数。
压力角a愈大,有害分力F''愈大,由F''引起的导路中的摩擦阻力也愈大,故凸轮推动从动件所需的驱动力也就愈大。
当a增大到某一数值时,因F''而引起的摩擦阻力将会超过有用分力F',这时无论凸轮给从动件的驱动力多大,都不能推动从动件,这种现象称为机构出现自锁。
机构开始出现自锁的压力角alim称为极限压力角,它的数值与支承间的跨距l2、悬臂长度l1、接触面间的摩擦系数和润滑条件等有关。
实践说明,当a增大到接近alim时,即使尚未发生自锁,也会导致驱动力急剧增大,轮廓严重磨损、效率迅速降低。
因此,实际设计中规定了压力角的许用值[a]。
对摆动从动件,通常取[a]=40~50;对直动从动件通常取[a]=30~40。
滚子接触、润滑良好和支承有较好刚性时取数据的上限;否则取下限。
对于力锁合式凸轮机构,其从动件的回程是由弹簧等外力驱动的,而不是由凸轮驱动的,所以不会出现自锁。
因此,力锁合式凸轮机构的回程压力角可以很大,其许用值可取[a]=70~80。
2 按许用压力角确定凸循环转中心位置和基圆半径1. 滚子(尖底)直动从动件盘形凸轮机构:过轮廓接触点作公法线n-n,交过点O的导路垂线于P。
该点即为凸轮与从动件的相对速度瞬心,且lop=v/w=ds/df。
由此可得直动从动件盘形凸轮机构的压力角计算公式式中h、d分别为凸轮转向系数和从动件偏置方向系数,其取值与前述相同。
对于滚子(尖底)直动从动件盘形凸轮机构,若hd=1,则称为正配置;否则,若hd=-1,称为负配置。
因推程ds/df≥0,回程ds/df≤0,故凸轮机构按正配置时,可减小推程压力角,但同时使回程压力角增大;而按负配置时,虽可减小回程压力角,但却使推程压力角增大。
在回程不会发生自锁的力锁合式凸轮机构中,一般采用正配置,以减小推程压力角。
由上式可知,当凸轮机构配置情况、偏距e及从动件运动规律确定之后,基圆半径r0愈小,压力角a愈大。
欲结构紧凑应使基圆尽可能小,但基圆太小又会导致压力角超过许用值。
因压力角是机构位置的函数,必有某个位置出现最大压力角amax。
设计时应在amax≤[a]的条件下,选取尽可能小的基圆半径。
当已知凸循环转方向及从动件运动规律s=s(f)时,满足给定推程许用压力角[a]和回程许用压力角[a']的最小基圆半径及最佳偏距可利用上式通过数值法求得,但求解过程复杂。
下面先容一种便于工程应用的解析几何方法。
如图a所示,以从动件尖底初始位置B0为原点建立ds/df-s直角坐标系。
为减小推程压力角,ds/df轴正向取为s轴正向沿凸循环转方向转900的指向,即当凸循环转方向为顺时针(h=1)时,ds/df轴正向在s轴右侧;当凸循环转方向为逆时针(h=-1)时,ds/df轴正向在s轴左侧。
若O点为凸循环转中心,C为ds/df-s曲线上任一点,C在s轴上的投影点为B,则直线OC 与s轴夹角即为从动件尖底运动至B点时的压力角aB。
过O点作ds/df-s曲线的切线,切点分别为C1、C2,那么OC1、OC2与s轴夹角分别为推程最大压力角amax和回程最大压力角a'max。
而OB0线与s轴夹角为推程初始压力角aB0。
显然,只要aB0≤[a]、amax≤[a]、a'max≤[a'],那么其余位置的压力角必小于许用压力角。
因此,如图b所示,假如在ds/df轴正侧(对应于推程)以tg(900-[a])为斜率作ds/df-s曲线的切线L1,切点为C1;在ds/df轴负侧(对应于回程)以tg(900+[a])为斜率作ds/df-s曲线的切线L2,切点为C2;再过点B2作斜率为tg(900+[a])的直线L3,那么L1、L2、L3与s轴的夹角分别为[a]、[a']和[a]。
显然,L1、L2、L3三条直线下方的公共部分即为满足推程压力角不超过[a]和回程压力角不超过[a']时凸循环转中心O的可取区域。
若L1与L2的交点记为O12,L1与L3的交点记为O13,则当O13点在O12点下方时,最小基圆半径为r0min=lB0O13,对应的最佳偏距e0为O13点至s轴的间隔;当O12点在O13点下方时,r0min=lB0O12,e0为O12点至s轴的间隔。
满足许用压力角的最小基圆半径及最佳偏距即可按此进行计算。
2. 滚子(尖底)摆动从动件盘形凸轮机构在图所示摆动从动件盘形凸轮机构中,过接触点作法线n-n,交连心线于点P,该点即为凸轮与从动件的相对速度瞬心,且式中h、d分别为凸轮转向系数和从动件推程摆动方向系数,其取值与前述相同。
由直角三角形PDB得综合式(a)、(b),得计算任意位置压力角的一般公式:式中y0为从动件初位角,可由下式计算:由上可以看出,影响压力角a的因素较多,且关系较为复杂。
但若hd=-1且acos(y0+y)>l或acosy0当从动件长度l和运动规律y=y(f)给定之后,压力角a的大小取决于基圆半径r0和中心距a。
设计时可将推程和回程许用压力角作为约束条件,用优化的方法求得最小基圆半径及相应的中心距。
3. 圆柱凸轮机构:圆柱凸轮机构中圆柱凸轮的均匀圆柱半径rm也可以根据许用压力角加以确定。
图示为摆动从动件圆柱凸轮机构凸轮理论轮廓曲线的展开图。
在速度三角形中有式中v1=w1r m,v B=w1l AB|dy/df|推程时e=1,回程时e=-1。
将v1、v B代进上式得由上式可知,压力角a随均匀圆柱半径rm的增大而减小,故圆柱凸轮机构中圆柱凸轮均匀半径与直动从动件盘形凸轮机构的凸轮基圆半径具有相似的特点。
对于直动从动件圆柱凸轮机构,利用从动件的运动特点,由式(8.15)得压力角关系为若给定许用压力角[a],则有:3 按轮廓曲线全部外凸的条件确定平底从动件盘形凸轮机构凸轮的基圆半径对于平底直动从动件盘形凸轮机构,凸轮轮廓曲线与平底接触处的公法线永远垂直于平底,压力角恒即是零。
显然,这种凸轮机构不能按照压力角确定其基本参数。
但是,平底从动件有一个特点,它只能与外凸的轮廓曲线相作用,而不答应轮廓曲线有内凹,这样才能保证凸轮轮廓曲线上的所有点都能与从动件平底接触。
由实例发现,基圆半径过小时,用作图法绘制平底从动件盘形凸轮机构的凸轮,不仅会出现轮廓曲线内凹,而且同时会出现包络线相交,如图所示。
在实际加工时,这种现象将造成过度切割,使包络线交点左侧的轮廓曲线全部被切掉,从而导致从动件运动失真。
因此,欲避免运动失真,就必须保证轮廓曲线全部外凸。
通过推导,可得平底凸轮轮廓曲线上一点的曲率半径为只要保证r>0,即可获得外凸轮廓曲线。
但曲率半径太小时,轻易磨损,故通常设计时规定一最小曲率半径rmin,使轮廓曲线各处满足r≥rmin。
当运动规律确定之后,每个位置的s和d2s/df2均为已知,总可以求出(d2s/df2+s)min。
显然,取基圆半径为r0≥r min-(d2s/df2+s)min可保证所有位置都满足r≥r min的条件。
因r0和s恒为正值,可以看出,只有当d2s/df2为负值且|d2s/df2|>r0+s时,才出现轮廓曲线内凹。
4 滚子半径的确定理论轮廓曲线求出之后,如滚子半径选择不当,实在际轮廓曲线也会出现过度切割而导致运动失真。
如图所示,r为理论轮廓曲线上某点的曲率半径,r'为实际轮廓曲线上对应点的曲率半径,rT为滚子半径。
当理论轮廓曲线内凹时,如图中点A所示,r'=r+rT,可以得出正常的实际轮廓曲线。
当理论轮廓曲线外凸时,如图中点B所示,r'=r-rT,它可分为三种情况:1) r>rT,r'>0,这时也可以得出正常实际轮廓曲线;2) r=rT,r'=0,这时实际轮廓曲线变尖,这种轮廓曲线极易磨损,不能付之实用;3) r<rt,如图中点c所示,这时r'为负值,实际轮廓曲线已相交,交点以外的轮廓曲线事实上已不存在,因而导致从动件运动失真。
综上所述可知,滚子半径rT必须小于理论轮廓曲线外凸部分的最小曲率半径rmin。
设计时建议取rT≤0.8rmin。
由高等数学可知,以参数方程x=x(f)、y=y(f)表示的平面曲线,其上任一点曲率半径的计算公式为式中用计算机对凸轮理论轮廓曲线逐点计算其曲率半径,即可获得rmin。
(end)</rt,如图中点c 所示,这时r'为负值,实际轮廓曲线已相交,交点以外的轮廓曲线事实上已不存在,因而导致从动件运动失真。