注塑不良原因改善对策实例分析)
注塑品质问题总结范文

一、前言注塑工艺在塑料制品的生产中占据着重要的地位,然而,在注塑生产过程中,品质问题时有发生,严重影响了产品的质量和企业的声誉。
为了提高注塑产品的品质,减少品质问题的发生,现将我司近期注塑品质问题进行总结分析,并提出改进措施。
二、品质问题总结1. 产品外观缺陷(1)表面有油污、划痕、气泡等。
(2)产品尺寸不稳定,存在较大公差。
2. 产品内部缺陷(1)产品内部有空洞、缩孔、熔接痕等。
(2)产品内部有冷料、飞边等杂质。
3. 材料问题(1)原材料质量不稳定,导致产品性能波动。
(2)材料配比不当,影响产品性能。
4. 设备问题(1)模具设计不合理,导致产品缺陷。
(2)设备磨损严重,影响产品质量。
5. 操作问题(1)操作人员技能水平不足,导致产品品质下降。
(2)生产过程不规范,存在安全隐患。
三、原因分析1. 原材料问题:原材料质量不稳定,供应商管理不到位。
2. 设备问题:设备维护保养不及时,模具设计不合理。
3. 操作问题:操作人员技能水平不足,生产过程不规范。
4. 管理问题:品质管理制度不完善,缺乏有效的监督机制。
四、改进措施1. 优化原材料采购流程,提高原材料质量。
2. 加强设备维护保养,确保设备正常运行。
3. 提高操作人员技能水平,规范生产过程。
4. 完善品质管理制度,加强监督机制。
5. 加强与供应商的沟通与合作,提高原材料质量。
五、总结通过本次注塑品质问题总结,我司将针对存在的问题,采取有效措施进行改进。
在今后的生产过程中,我们要高度重视注塑品质问题,不断提高产品质量,以满足客户需求,提升企业竞争力。
同时,要加强员工培训,提高整体素质,确保生产过程规范化、标准化。
相信在全体员工的共同努力下,我司的注塑品质一定会得到全面提升。
注塑缺陷的原因及解决方法

表面起膜树脂的添加剂流经产品表面时,形成的白色、灰色的蔓延现象被称为表面起膜。
产生的主要原因:1、树脂内部的添加剂是主要原因1、造成过度应力的注塑条件等也是引发原因飞边产生的主要原因1、注塑机加工不良2、注塑机容量不足3、加工条件不良4、锁模力不足5、模具贴得不紧6、模具的变形7、树脂流动太好8、Gas V ent过大9、注塑压力较大10、模具面上存在异物透明性低下PPS、SAN等透明产品出现的透明性低下的现象产生的主要原因1、脱模剂使用过多2、混入其它树脂3、混入其它型号4、模具的加工状态,模具温度等加工条件不合适。
异色、褪色产品的颜色与标准颜色不同的现象。
树脂颜色不同为异色;注塑后颜色发生改变的现象为变色。
产生的主要原因1、着色错误2、树脂污染3、过多使用粉碎品4、注塑机污染5、树脂的热化等表面突起产生的主要原因1、原料内混入异物2、颜料未分散3、模具加工状态4、使用再利用原料未填满树脂没有填满Cavity的全部,冷却凝固后成型品的一部分出现不足的现象。
1.进料调节不当A缺料B多料2.注射压力不妥3.料量过低4.模具温度低或温度分布不合理5.塑料流动性高6.喷嘴配合不良7.塑料熔块堵塞加料通道8.喷嘴冷料入模9.模具设计不合理10.模具浇注系统有缺陷流痕树脂的流动痕迹在产品表面表现出来的现象。
产生的主要原因1、绝大部分是由于树脂填充到模具内时树脂温度降低。
2、混入其它树脂。
3、树脂的分解。
4、模具的排气不良。
黑线产品表面形成黑色线条的现象挥发物润滑剂或脱膜剂树脂的热化黑色颜料注塑要清洁不良模具表面受到污染(油、油脂等异物)排气不良成型机的老化及损伤过多使用再利用原料成型收缩对成型品的尺寸产生影响的因素多种多样,其主要变数有模具、产品形状、成型条件及后工程、树脂的种类等。
(a)随模具的设计及成型品的形状而产生的差异。
随Gate的位置、形状、面积、尺寸会有所不同通常Gate附近所承受的注塑压较高,因此收缩较小。
注塑生产中15种注塑缺陷不良原因分析和对策
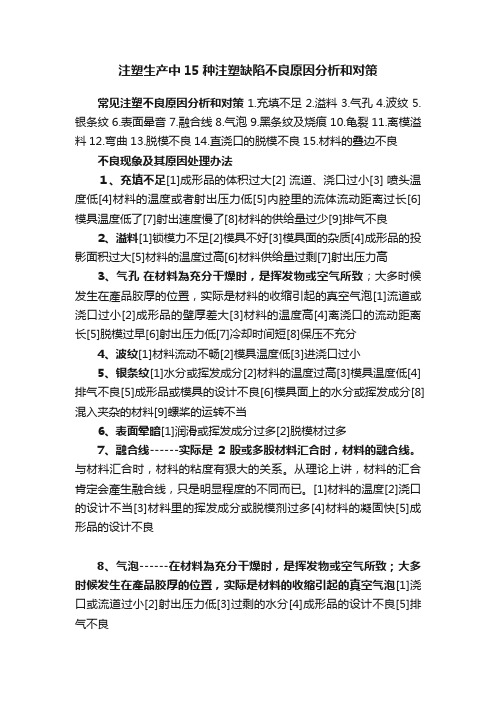
注塑生产中15种注塑缺陷不良原因分析和对策常见注塑不良原因分析和对策1.充填不足2.溢料3.气孔4.波纹5.银条纹6.表面晕音7.融合线8.气泡9.黑条纹及烧痕10.龟裂11.离模溢料12.弯曲13.脱模不良14.直浇口的脱模不良15.材料的叠边不良不良现象及其原因处理办法1、充填不足[1]成形品的体积过大[2] 流道、浇口过小[3] 喷头温度低[4]材料的温度或者射出压力低[5]内腔里的流体流动距离过长[6]模具温度低了[7]射出速度慢了[8]材料的供给量过少[9]排气不良2、溢料[1]锁模力不足[2]模具不好[3]模具面的杂质[4]成形品的投影面积过大[5]材料的温度过高[6]材料供给量过剩[7]射出压力高3、气孔在材料為充分干燥时,是挥发物或空气所致;大多时候发生在產品胶厚的位置,实际是材料的收缩引起的真空气泡[1]流道或浇口过小[2]成形品的壁厚差大[3]材料的温度高[4]离浇口的流动距离长[5]脱模过早[6]射出压力低[7]冷却时间短[8]保压不充分4、波纹[1]材料流动不畅[2]模具温度低[3]进浇口过小5、银条纹[1]水分或挥发成分[2]材料的温度过高[3]模具温度低[4]排气不良[5]成形品或模具的设计不良[6]模具面上的水分或挥发成分[8]混入夹杂的材料[9]螺桨的运转不当6、表面晕暗[1]润滑或挥发成分过多[2]脱模材过多7、融合线------实际是2股或多股材料汇合时,材料的融合线。
与材料汇合时,材料的粘度有狠大的关系。
从理论上讲,材料的汇合肯定会產生融合线,只是明显程度的不同而已。
[1]材料的温度[2]浇口的设计不当[3]材料里的挥发成分或脱模剂过多[4]材料的凝固快[5]成形品的设计不良8、气泡------在材料為充分干燥时,是挥发物或空气所致;大多时候发生在產品胶厚的位置,实际是材料的收缩引起的真空气泡[1]浇口或流道过小[2]射出压力低[3]过剩的水分[4]成形品的设计不良[5]排气不良9、黑条纹及烧痕------实际是材料受到高温、高压的作用出现分解烧焦的现象。
塑胶注塑不良的分析以及处理措施

尺寸标准
对比设计图纸,检查塑胶制品的关键 尺寸是否在允许的公差范围内。
性能标准
根据塑胶制品的具体用途,评估其物 理性能和化学性能是否满足使用要求 。
安全标准
确保塑胶制品在使用过程中不会对人 体造成伤害,符合相关国家和地区的 法律法规。
检测与评估工具
放大镜
用于观察塑胶制品的细 微缺陷。
卡尺
用于测量塑胶制品的尺 寸。
注射压力、温度、时间等参数设置不合理, 影响塑料的流动和成型。
塑料材料问题
塑料材料性能不佳,如收缩率大、流动性差 等,导致成型不良。
模具保养不当
模具保养不善,如清洁不彻底、润滑不足等 ,影响塑料的流动和成型。
02
塑胶注塑不良的检测与评估
检测方法
目视检测
通过观察塑胶制品的外观,检 查是否存在缺料、缩水、气泡
02
塑胶注塑不良的原因多种多样,如模 具设计不合理、塑料材料选择不当、 注塑工艺参数设置不正确等。针对不 同类型的不良现象,需要采取不同的 处理措施。本文对各种不良现象进行 了分类和总结,并详细介绍了相应的 处理方法,有助于提高生产效率和产 品质量。
03
本文还对塑胶注塑技术的发展趋势进 行了展望。随着科技的不断发展,新 型塑料材料和加工技术不断涌现,注 塑技术将朝着高效、环保、智能化的 方向发展。未来,注塑技术将更加注 重节能减排、提高生产效率、降低成 本等方面,为工业生产带来更多的便 利和效益。
案例三:某产品内部气孔问题
总结词
内部气孔是指产品内部存在大小不一的气孔,影响产品的机械性能和外观。
详细描述
气孔通常分布在产品内部,形状不规则。可能的原因包括塑料原料中含有水分或挥发性物质、模具排气不良、塑 料熔体流动不均匀等。
注塑缺陷原因分析与解决方案
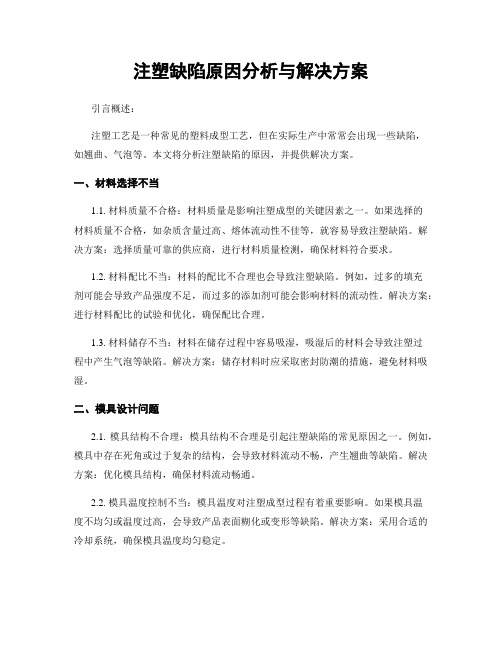
注塑缺陷原因分析与解决方案引言概述:注塑工艺是一种常见的塑料成型工艺,但在实际生产中常常会出现一些缺陷,如翘曲、气泡等。
本文将分析注塑缺陷的原因,并提供解决方案。
一、材料选择不当1.1. 材料质量不合格:材料质量是影响注塑成型的关键因素之一。
如果选择的材料质量不合格,如杂质含量过高、熔体流动性不佳等,就容易导致注塑缺陷。
解决方案:选择质量可靠的供应商,进行材料质量检测,确保材料符合要求。
1.2. 材料配比不当:材料的配比不合理也会导致注塑缺陷。
例如,过多的填充剂可能会导致产品强度不足,而过多的添加剂可能会影响材料的流动性。
解决方案:进行材料配比的试验和优化,确保配比合理。
1.3. 材料储存不当:材料在储存过程中容易吸湿,吸湿后的材料会导致注塑过程中产生气泡等缺陷。
解决方案:储存材料时应采取密封防潮的措施,避免材料吸湿。
二、模具设计问题2.1. 模具结构不合理:模具结构不合理是引起注塑缺陷的常见原因之一。
例如,模具中存在死角或过于复杂的结构,会导致材料流动不畅,产生翘曲等缺陷。
解决方案:优化模具结构,确保材料流动畅通。
2.2. 模具温度控制不当:模具温度对注塑成型过程有着重要影响。
如果模具温度不均匀或温度过高,会导致产品表面糊化或变形等缺陷。
解决方案:采用合适的冷却系统,确保模具温度均匀稳定。
2.3. 模具磨损严重:模具长时间使用后会出现磨损,磨损严重的模具会导致产品尺寸不准确或表面粗糙等缺陷。
解决方案:定期检查和维护模具,及时更换磨损严重的模具部件。
三、注塑工艺参数设置不当3.1. 注射压力过高或过低:注射压力是影响注塑成型的关键参数之一。
如果注射压力过高,会导致产品变形或开裂,而注射压力过低则会导致产品表面光洁度不高。
解决方案:根据产品要求和材料特性,合理设置注射压力。
3.2. 注射速度不合理:注射速度对产品的充填和冷却过程有着重要影响。
如果注射速度过快,会导致产品内部产生气泡或短射,而注射速度过慢则会导致产品表面瑕疵。
注塑产品缺陷产生原因及处理方法(五篇模版)

注塑产品缺陷产生原因及处理方法(五篇模版)第一篇:注塑产品缺陷产生原因及处理方法注塑产品缺陷产生原因及处理方法在注塑成型加工过程中可能由于原料处理不好、制品或模具设计不合理、操作工没有掌握合适的工艺操作条件,或者因机械方面的原因,常常使制品产生注不满、凹陷、飞边、气泡、裂纹、翘曲变形、尺寸变化等缺陷。
对塑料制品的评价主要有三个方面,第一是外观质量,包括完整性、颜色、光泽等;第二是尺寸和相对位置间的准确性;第三是与用途相应的机械性能、化学性能、电性能等。
这些质量要求又根据制品使用场合的不同,要求的尺度也不同。
生产实践证明,制品的缺陷主要在于模具的设计、制造精度和磨损程度等方面。
但事实上,塑料加工厂的技术人员往往苦于面对用工艺手段来弥补模具缺陷带来的问题而成效不大的困难局面。
生产过程中工艺的调节是提高制品质量和产量的必要途径。
由于注塑周期本身很短,如果工艺条件掌握不好,废品就会源源不绝。
在调整工艺时最好一次只改变一个条件,多观察几回,如果压力、温度、时间统统一起调的话,很易造成混乱和误解,出了问题也不知道是何道理。
调整工艺的措施、手段是多方面的。
例如:解决制品注不满的问题就有十多个可能的解决途径,要选择出解决问题症结的一、二个主要方案,才能真正解决问题。
此外,还应注意解决方案中的辨证关系。
比如:制品出现了凹陷,有时要提高料温,有时要降低料温;有时要增加料量,有时要减少料量。
要承认逆向措施的解决问题的可行性。
1.6.1 塑料成型不完整这是一个经常遇到的问题,但也比较容易解决。
当用工艺手段确实解决不了时,可从模具设计制造上考虑进行改进,一般是可以解决的。
一、设备方面:(1)注塑机塑化容量小。
当制品质量超过注塑机实际最大注射质量时,显然地供料量是入不敷出的。
若制品质量接近注塑机实际注射质量时,就有一个塑化不够充分的问题,料在机筒内受热时间不足,结果不能及时地向模具提供适当的熔料。
这种情况只有更换容量大的注塑机才能解决问题。
注塑成型不良问题分析及解决
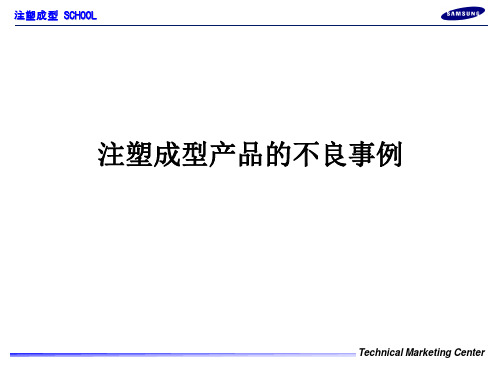
注塑成型 SCHOOL
Crack
1. Item: Monitor Front Cabinet 2. 原料: VH-0810 3. 不良类型: -Crack
4. 问题原因 : Chemical Attack 紫外线露出使用,保管环境
Technical Marketing Center
注塑成型 SCHOOL
差异发生。
[图 1.]
[图 2.]
Technical Marketing Center
注塑成型 SCHOOL
3. 改善对策
✓ 模具修正 - 在不改变Design的范围内,修正为各个部分之间的厚度偏差最小化。
✓ Boss 部位的形象变更 - 除去Boss部位的Guide, Sink mark 最小化。
5.措施 : 自制IPA和Methanol的使用和使用最小量涂布 有关树脂 : 需要改善耐化学性 Technical Marketing Center
注塑成型 SCHOOL
Crack (Folder 寿命 test)
1.Item : Front dummy hinge crack 2.原料 : HF-1023IM/G7630 3.不良类型 : Hinge dummy动作部位folder寿命试验时的crack
Technical Marketing Center
注塑成型 SCHOOL
2. 主要不良现象
1) 两边终端部的Sink mark
2) Center Hole 部位发生白化
Technical Marketing Center
注塑成型 SCHOOL
1) 两边终端部的Sink mark
- 因设置在后面的Boss引起的部分厚度的偏差而发生。
注塑成型类产品常见不良分析案例

注塑成型不良的案例分析一、飞边(披锋)系指从模具分型面拼出熔融树脂的现象,在成形作业当中属于最恶劣的情况,特别是当飞边粘在模具面上,残留下来,直接锁模的话,则损伤模具分型面。
一旦出现这种情况,该损伤部分又会导致产生新的飞边,怎么也没办法,所以需特别注意不要出现飞边,1、不得施加过高的射出压力熔融粘度低的树脂,如尼龙、聚丙烯、聚乙烯、聚苯乙烯等,流动性好,往往从模具缝隙出现“边缘鼓出”现象,因此,不得施加过高的射出压力和保压压力。
当有出现飞边的倾向时,应尽早让保压转换用限位开关动作,减少计量。
降低射出压力。
另外,保压压力也有过高的时候,对于这些流动好的树脂,不要从一开始就施加高保压压力。
应边观察成形品的状况,边一点一点提高压力。
2、最初锁模力不足时,当然会产生飞边,不了解所用模具所需锁模力究竟有多大,就不可能作出断。
先利用锁模力调整手柄,增加锁模力试试看。
上图为在模具接触面(分型面)形成的飞边。
飞边主要是发生在分型面,但其它如在小顶杆周围、抽芯周围有时也出现飞边。
所谓纵向飞边,几乎均起因于模具精度不够。
象尼龙之类熔融粘度低的树脂,特别容易产生飞边,如聚碳酸酯之类粘度高的树脂则难于产生飞边。
以最大锁模力锁模,仍然出现飞边时,则应考虑是否是机械能力不足。
此时的判断方法是,当模腔内的压力乘以模腔、流道的投影面积所得的数值未超过机械是大锁模力的话,则不属于机械能力不足。
但需正确估计模腔内压力,然而不能把产品目录所列出的射出压力看作是模腔压力。
射出压力充其量是料筒内的理论压力,树脂流入模具,即被冷却,压力急剧下降。
平均压力从低粘度部件250kg/cm2到高粘度工业部件800kg/cm2左右,这种压力很难估计,虽然大体上有个基准,但要想保证估计精度,还需要凭经验。
3、在模具接触面产生了伤痕、夹有脏东西或是模具平行度差,当然会产生飞边,模具保管不善,则会使安装面打上伤痕,或是生锈,这样都会导致产生飞边。
所以应该养成习惯妥善保管模具。
- 1、下载文档前请自行甄别文档内容的完整性,平台不提供额外的编辑、内容补充、找答案等附加服务。
- 2、"仅部分预览"的文档,不可在线预览部分如存在完整性等问题,可反馈申请退款(可完整预览的文档不适用该条件!)。
- 3、如文档侵犯您的权益,请联系客服反馈,我们会尽快为您处理(人工客服工作时间:9:00-18:30)。
主讲:洪奕春
1
讲师简介
讲师简介:洪奕春:国内屈指可数的顶尖注塑技术专家、著名的高级注塑培训 师。20多年来一直在注塑行业工作,是国内第一代注塑专业人才,长期在深圳、 香港、东莞、广州、昆山、上海等地的多家大型日资、港资、台资及民营企业任 职,历任注塑工程师、注塑生产经理、生产副总等职务。多次受委派到柯尼卡美能达,日本东芝、韩国LG等著名注塑生产企业、注塑机厂进行参观和学习。 精通注塑工艺,实操经验丰富,注重系统分析,擅长快速换模具项目推进,机 械手治具设计制作,氮气辅助注塑等先进技术…尤其对注塑缺陷原因分析与解决、 问题模具的分析改进有一套独特方法,并且对各种注塑机械和塑料材料具有丰富 的实操经验和独到的分析能力。 辅导过的部分知名企业有:苏州万达汽车内饰件厂、宁波库贴汽车塑料公司、 江苏泗阳意达铝制品厂、上海科世达-华阳汽车电器公司、北京龙轩橡塑公司、 北京嘉润粉末注射技术公司、武汉中恒科技公司、广州旭东阪田电子公司、广东 东菱凯琴集团、浙江正泰电器集团、柳州方鑫汽车装饰件公司、烟台汽车内饰件 总厂、烟台海瀚电子、淇杰电子、烟台爱开天隆、苏州宝德强科技、惠州TCL集 团、重庆海尔集团、重庆双英汽配、广州本田汽车、风神汽车、重庆长安汽车集 团、威海威高集团、威海兴友精密注塑、汕头益发塑胶实业、东莞金城电业、康 佳集团、新东江集团、长春伟巴斯特、无锡伟盈汽车部件、慈溪皇冠电子、台州 诺信模塑、浙江万安科技、苏州丰武光电,法可赛(太仓)汽车配件、深圳兴日 生实业、青岛胜汇塑胶、济南优百科等数百家企业。
力又会造成机械的损耗和模具
的损伤,这个合理的锁模力是
经过材料和模具型腔面积来计
算的。
用ZRCAE软件对注塑机模板进行有限元分析
20
锁模力的计算与制品投影面积
2)多段锁模力和速度控制: 锁模一般可分为四个阶段,开始和第二阶段后
采用快速移动模板,这是为了节省周期循环时间; 当模具即将闭合时,为了保护模具,这时要将锁模 压力降低,调节压力可在15吨以下,当模面完全闭 合,即动模和定模型面接触时,需要增加压力来达 到预期的高压锁模力。
冷却时间
模内冷却时间
辅助时间----开模、顶出、取出制 件、喷脱模剂、放嵌件、合模等
6
注塑机结构
1 定模座班板 4 熔胶 7 原料
2 推杆固定板 5 分流梭 8 顶杆
3 注塑件 6 柱塞 9 型芯
7
回料
螺杆头和止逆阀
射胶
滑套式 止逆阀
8
螺杆示意图
9
什么叫螺杆的压缩比?
• 螺杆的螺纹部分中,加料段第一个螺纹槽容积与均化段最后 一个螺纹槽容积的比值,叫螺杆的压缩比。
槽,做偏心铣斜度),加深螺杆螺槽的深度
• 2.产品发黄、有黑点:
• 螺杆料管磨损,根据磨损情况换相应的螺杆或料管 • 螺杆组件有死角。重新更换相应的专用螺杆或三小件 • 螺杆被原料碳化。使用防腐性好一点的螺杆材料 • 射嘴孔过小。将射嘴小孔重新钻大 • 螺杆压缩比过大。换相应的压缩比螺杆 • 螺杆温度过高包料。螺杆芯部打冷却深孔 • 产品塑化不良,原料在螺杆里面不能充分融化。提高料管的温度,使
(注:1Kg/(cm2)=14.3Psi,1bar=1.02Kg/ cm2 )
19
锁模力的计算与制品投影面积
1) 锁模力的设定:
调校锁模力的原因是因为
在成形的过程中,塑料高压射
出,如果没有合适的锁模压力
下,塑料就会冲出型腔造成模
具损坏和产品的毛边等不良现
象,高压锁模力的作用就是高
压紧闭模具。但过大的锁模
顺畅结构的小三件 • 杂物掉进料筒。取出异物
15
制品重量与理论射胶量的换算关系
1)理论射胶容积 V=π/4*Ds²* S(公式1) V:理论射胶容积cm³ Ds:螺杆直径cm S:射胶行程cm
2)理论射胶量等于理论射胶容积乘以塑料在常温下 的密度,即﹕ G=V*ρ(公式2) G:理论射胶量g V:理论射胶容积cm³ ρ:常温下的塑料密度g/cm³
18
背压的作用与调节
1)把挥发性气体,包括空气排出料筒外; 2)把添加剂(如色粉、色种、防静电剂、滑石粉等)与熔料均匀地混合; 3)有助于流经不同螺杆位置的熔料均匀化; 4)提供均匀稳定的熔胶位置,获得精确的成品重量。
塑料
推荐的熔料背压压力 备注
GPPS,ABS,HIPS, 100-200bar (1450-
• 压缩段—底径变化,主要作用是压实、熔融物料, 建立压力。参数压缩比ε=h1/h3及L2。准确应以 渐变度A=(h1-h3)/L2。
• 均化段(计量段)—将压缩段已熔物料定量定温 地挤到螺杆最前端、参数(L3,h3), h3=(0.05-0.07)D。
12
注塑螺杆料筒故障排除1
• 1.不下料:
• 螺杆断裂。换新的螺杆 • 料斗架“桥”。把“桥”弄塌 • 料管进料段温度过高。重设进料段温度,保证运水畅通运行 • 粉碎料颗粒过大,将原料重新破碎,改变料管进料口的设计(内壁拉
23
压力单位换算
1Kg/(cm2)=14.3Psi(磅平方英寸,即 Pounds per square inch) 1Psi=0.07Kg/cm2 1Mpa=10.2Kg/cm2 1Kg/cm2=98000Pa 1Kg/cm2=98.067KPa=0.9806bar 1bar=1.02Kg/cm2
16
注射压力的计算
1)最大注射压力
PO
( d ) 2. .P D
PO 最大注射压力(Mpa) d 油缸活塞直径(cm) D 螺杆直径(cm) p 油缸表压(Mpa)
17
注射压力的计算
2)注射压力
PI
FO .PO FS
PI 注射压力(Mpa) FO 油缸总截面积(cm2) FS 机筒内孔截面积(cm2) PO 工作油压力(Mpa)
24
材料温度的设定原则
• 一般材料宜用中等的温度成型,如ABS、PS、PP、 PE
• 容易过火或较脆的材料宜用稍低的温度,如POM、 PVC
• 流动性极差的材料宜用稍高的温度,如PC • 模具温度低时可适当调高料温来弥补
• 在等距渐变型螺杆中,也可近似理解为:加料段第一个螺槽 深h1与均化段最后一个螺槽深h3的比值,即压缩比=h1 / h3。
• 压缩比对塑料注射成型工艺控制有重要影响,不同的塑料, 根据塑料的物理性能选择螺杆的压缩比。下表列出了不同塑 料所用螺杆的压缩比值。
计量段 压缩段 加料段
10
不同塑料的螺杆压缩比
BDS,ASA
2,900psi)
PA6,PA66,PBT,PA 10-19bar(14511,PA12,PETP 1,305psi)
LDPE,HDPE,PP, 100-300bar(1450EVA,PP-EPDM 4,350psi)
PMMA,SAN,MBS, 120-4型螺杆
13
注塑螺杆料筒故障排除2
• 3.产品混色不均:
• 螺杆混炼效果不好。用高混炼螺杆 • 射胶终点不稳定。过胶圈左右活动间隙过大,重新更换活动间隙小的
过胶圈 • 过胶圈和介子配合不好。换外径和端面垂直度好的圈和介子;过胶圈
和料管间隙过大,更换相应的磨损零件 • 料管和法兰接触点容易漏胶。料管和法兰两端面未贴紧,检修两工件
2
课程简介 • 《注塑不良原因、改善对策实例分析》,是
洪奕春老师的主打精品课程,它融合了洪老师20 年的注塑生产经验总结,以及10多年的注塑不良 案例集合,其丰富的知识量、生动的案例,以及 精心设计的内容,一定会让您受益匪浅!
3
第一章、注塑成型概述
注塑成型简述1
• 注塑成型是一种注射兼模塑的成型方法,又称注射成型。 • 塑化:通用注塑方法是将聚合物组分的粒料或粉料放入注
的内外止口长度;法兰的端面和外止口不垂直,检修两工件的内外止 口和端面的垂直度 • 螺杆或料管抗拉强度不够。用12.9级螺杆,用调过质的料管(12.9级 螺丝通常指采用SCM435合金钢材料制造,其最小抗拉强度达到 1220Mpa,硬度达到39~44HRC的超高强度螺杆 )
• 4.螺杆后退困难:
• 进料段温度偏高。设置合理的参数 • 破碎料过大。重新破碎更小原料 • 背压设置过大;减小背压 • 料筒进料段设置不合理;设计合理的进料口。 • 螺杆与料筒的间隙过小、间隙过大。更换新的螺杆料筒;
14
注塑螺杆料筒故障排除3
• 5.制品有气泡: • 背压太低;加大背压 • 压缩比太小。选择大一点压缩比的螺杆 • 射速太慢,模温过高。设置合理的工艺参数 • 6.螺杆有异响: • 料管没装配到位。检查各档尺寸,重新安装 • 料筒料口档尺寸太小。修改尺寸 • 螺杆柄部直径太小。修改直径尺寸 • 螺杆直线度不好。重做螺杆 • 螺杆出料设计不够顺畅。流动性不好的原料生产时用出料
塑机的料筒内,经过加热、压缩、剪切、混合和输送作用, 使物料进行均化和熔融,这一过程又称塑化。 • 注射:然后再借助于螺杆向熔化好的聚合物熔体施加压力, 高温熔体便通过料筒前面的喷嘴和模具的浇道系统射入预 先闭合好的低温模腔中。 • 冷却:再经冷却定型,就可打开模具,顶出制品,得到具 有一定几何形状和精度的塑料制品。
PVC,RTPU,CP, CPVC
100-300bar(14504,350psi)
背压不足易引起注件的浇焦现象(成 因是熔料内含有空气或其他气体) 需要精确地设定背压以获得正确的 熔料均匀度
正确背压的设定可减少成品重量的 变化 背压过低时,熔料和成品可能有气泡
这些塑料对热量很敏感,需要小心设 定背压数值
开模也可分为四个阶段,原因是为减少机械的 震动,在开模时,动模的移动比较慢,其原因是成 形制件还在型腔内,如果速度太快,会破坏制品和 产生震动,为了缩短周期循环时间,在开模的中途 阶段,模板会快速移动直到动模在接近开模终止位 置时才减速度,最后慢速、终止动作。