180T转炉课程设计说明书
转炉炼钢课程设计
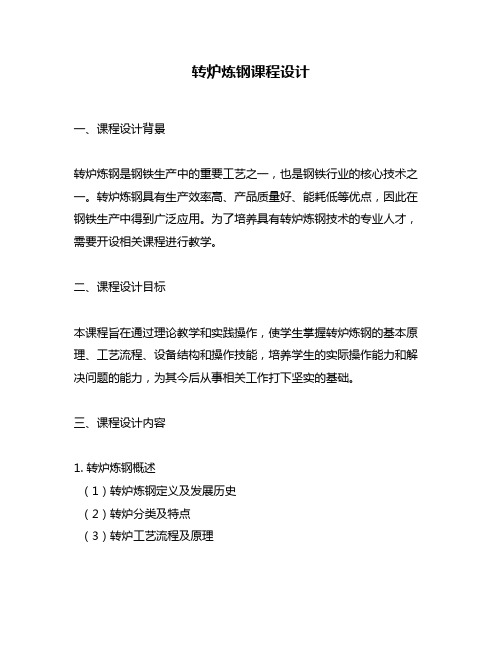
转炉炼钢课程设计一、课程设计背景转炉炼钢是钢铁生产中的重要工艺之一,也是钢铁行业的核心技术之一。
转炉炼钢具有生产效率高、产品质量好、能耗低等优点,因此在钢铁生产中得到广泛应用。
为了培养具有转炉炼钢技术的专业人才,需要开设相关课程进行教学。
二、课程设计目标本课程旨在通过理论教学和实践操作,使学生掌握转炉炼钢的基本原理、工艺流程、设备结构和操作技能,培养学生的实际操作能力和解决问题的能力,为其今后从事相关工作打下坚实的基础。
三、课程设计内容1. 转炉炼钢概述(1)转炉炼钢定义及发展历史(2)转炉分类及特点(3)转炉工艺流程及原理2. 转炉结构与设备(1)转炉结构及组成部分(2)各部位功能及作用介绍(3)常见故障及处理方法3. 转炉操作技能(1)转炉操作前准备工作(2)转炉开炉及加料操作(3)钢水出钢及出渣操作(4)转炉关炉及清理工作4. 转炉生产管理(1)生产计划编制及执行(2)设备维护保养及安全管理(3)质量控制及环境保护5. 实践操作(1)模拟实验:转炉开、关炉操作演练(2)现场实习:参观钢厂,观摩现场生产过程四、教学方法本课程采用多种教学方法,包括理论讲解、案例分析、模拟实验和现场实习等。
其中,模拟实验是本课程的重要组成部分,通过对转炉开、关炉等操作的演练,使学生能够真正掌握相关技能。
五、考核方式本课程考核方式包括平时成绩和期末考试两部分。
平时成绩占总成绩的30%,主要评估学生的出勤情况、课堂表现和模拟实验成绩;期末考试占总成绩的70%,主要考核学生对转炉炼钢原理、设备结构和操作技能的掌握程度。
六、教学资源本课程需要的教学资源包括课件、实验器材、教材和参考书籍等。
其中,教材应选用权威性强、内容全面、易于理解的转炉炼钢专业书籍;参考书籍应包括转炉炼钢技术及相关领域的最新进展。
七、教学团队本课程需要一支专业素质高、经验丰富的教师团队。
其中,主讲教师应具备扎实的专业知识和丰富的实践经验,能够灵活运用多种教学方法,激发学生学习兴趣和积极性;助教应能够协助主讲教师进行模拟实验和现场实习等工作,提供必要的技术支持。
180t顶吹氧转炉炉型尺寸计算

转炉炉型设计转炉是转炉炼钢车间的核心设备。
转炉炉型及其主要参数对转炉炼钢的生产率、金属收得率等经济指标都有直接的影响,其设计是否合理也关系到冶炼工艺能否顺利进行,车间主厂房高度与转炉配套的其他相关设备的选型。
所以,设计一座炉型结构合理,满足工艺要求的转炉是保证车间正常生产的前提,而炉型设计又是整个转炉车间设计的关键。
(一)转炉公称容量及其表示方法公称容量(T),是对转炉容量大小的称谓,即平时所说的转炉的吨位。
它是转炉生产能力的主要标志和炉型设计的重要依据。
目前国内外对公称容量的含义的解释还很不统一,归纳起来,大体上有以下三种表示方法:1)以平均金属装入量(t)表示;2)以平均出钢量(t)表示;3)以平均炉产良坯量(t)表示。
在一个炉役期内,炉役前期和后期的装入量或出钢量不同,随着吹炼的进行,炉衬不断地受到侵蚀,熔池不断扩大,装入量增大,所以三种表示方法都是以其平均容量来表示。
这三种表示方法各有其优缺点,以平均金属装入量表示公称容量,便于进行物料平衡和热平衡计算,换算成新炉装入量时也比较方便。
以平均炉产良坯量表示公称容量,便于车间生产规模和技术经济指标的比较,但是在进行炉型设计时需做较复杂的换算。
以平均出钢量表示公称容量则介于两者之间,其产量不受操作方法和浇铸方法的影响,便于炼钢后步工序的设计,也比教容易换算成平均金属装入量和平均炉产良坯量。
设计的公称容量与实际生产的炉产量基本一致。
所以在进行炉型设计时采用以平均出钢量表示公称容量比较合理。
所以在本文中所设计中的180t转炉,其炉役期内的平均出钢量为180t,即此处公称容量(T)取180t。
(二)转炉炉型的选择转炉是转炉炼钢车间的核心设备。
炉型及其主要参数对转炉炼钢的生产率、金属收得率、炉龄等技术经济指标都有着直接的影响。
炉型设计的是否合理关系到冶炼工艺能否顺利进行的问题,如喷溅问题,除与操作因素有关外,炉型设计是否合理也是个重要因素。
并且车间的主厂房高度以及主要设备,像除尘设备,倾动机构设备等都与炉型尺寸密切相关。
王超20110017课程设计说明书修改 最新
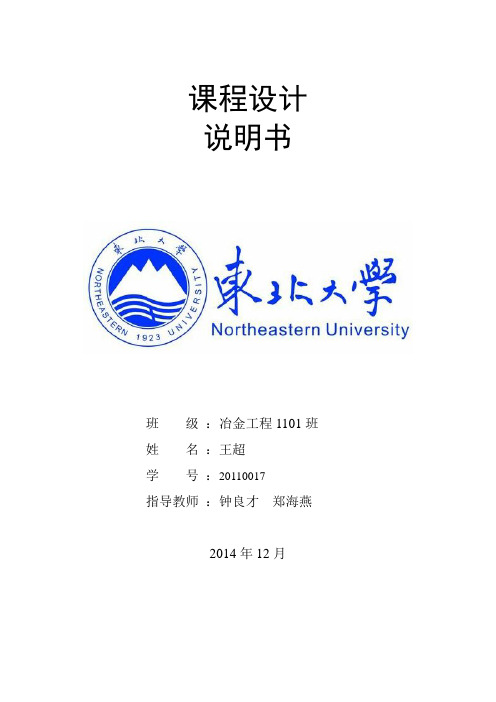
课程设计说明书班级:冶金工程1101班姓名:王超学号:20110017指导教师:钟良才郑海燕2014年12月设计任务书设计题目:800万吨良坯转炉综合计算与转炉设计设计条件:1)年产量:800万吨2)工作方式:3吹33)铁水条件:[Si] 0.43%;[P] 0.065%;[C] 4.5%;[Mn] 0.44%;[S] 0.008%;温度1300℃;设计内容:1)物料平衡计算;2)转炉炼钢车间的年产刚水量;3)转炉炼钢车间的年出钢炉数;4)转炉平均出钢量;5)转炉炉型设计计算;6)底吹供气元件设计;7)转炉炉衬设计;800万吨良坯转炉综合计算与转炉设计摘要炼钢厂设计的目的是要建设新的生产厂,扩建或改建旧有企业使之更适合国民经济发展的需要,提高产量和质量,改善生产环境。
而扎转炉的设计是炼钢厂设计的重要部分。
本文在设计过程中,首先根据铁水成分和目标钢种的组成等物料和热量条件,进行物料平衡与热平衡计算。
通过物料和热量平衡计算,初步确定设计转炉的操作工艺制度(包括物料加入比例)和合理的设计参数。
然后分别对转炉座数及工程容量、转炉炉型及主要设计参数、转炉炉衬及炉壳、转炉高径比校核等四部分进行设计。
物料平衡与热平衡计算是氧气转炉工艺设计的一项基本内容,是建立在物质与能量守恒的基础上。
其以氧气转炉作为对象,根据装入转炉内参与炼钢过程的全部物料数据和炼钢过程的全部产物数据进行无聊的质量和热量的计算。
转炉用于盛装高温金属液和熔渣,在炼钢过程中,需要向前倾动一定角度,进行兑铁、加废钢、倒渣操作,向炉后倾动可实现出钢操作。
目前转炉已经大型化,转炉设计一般采用顶底复合吹工艺。
设计过程中,根据设定指标确定转炉座数和转炉的公称容量。
而转炉炉型根据目前实践进行选定,主要设计参数包括熔池直径和深度、炉身尺寸、炉帽尺寸、出钢口直径和角度、炉容比和有效体积、底部供气元件尺寸和布置等。
目前转炉炉衬只有工作层和永久层,转炉炉壳紧贴永久层,由钢板成型后焊接成整体。
转炉设计

180t 顶底复吹转炉设计一、转炉炉型设计原始条件: 炉子平均出钢量180t 。
金属收得率取92%,最大废钢比取20%,采用废钢矿石冷却,铁水采用P08低磷生铁{w (si )≤0.85%,w (p )≤0.2%,w (s )≤0.05%}1、熔池形状确定转炉炉型有筒球型、锥球型、截锥型,熔池形状选用截锥型。
为了满 足顶底复吹的要求,炉型趋于矮胖型,由于在炉底上要设置底吹喷嘴,炉底为平底,所以熔池为截锥形。
2、炉容比确定炉容比系指转炉有效容积t V 与公称容量T 之比值。
t V 系炉帽体积帽V 、炉身体积身V 、和容池体积c V 三个内腔容积之和。
由于顶底复吹转炉吹炼过程比较平稳,产生泡沫渣的量比顶吹转炉要少得多,喷溅较少,因此其炉容比比顶吹转炉小,但比底吹转炉要大。
根据冶炼条件取炉容比为0.95m 3/t 。
3、熔池尺寸的确定熔池是容纳金属并进行一系列复杂物理化学反应的过程,其主要尺寸有熔池 直径和熔池深度。
设计时,应根据装入量、供氧强度、喷嘴类型、冶金动力学条件以及炉衬蚀损的影响综合考虑。
截锥型熔池尺寸如图(1)所示:则其体积为: )(12h2112d Dd D V ++=π熔(1) 熔池直径D :熔池直径通常指熔池处于平静状态时金属液面的直径。
D=Kt G =1.63×15180=5.646m 式中G ——炉子公称容量,180t ;t ——平均每炉钢纯吹氧时间,取15分钟; K ——比例系数,根据炉子容量取1.63; (2)熔池深度h :根据经验,取D d 7.01== 3.952m其中熔池体积38.268.6180m GV c ===ρ故熔池深度: 20.574c V h D == 2646.5574.08.26⨯=1.465m校核26.0646.5465.1/==D h 符合要求 4、炉帽尺寸的确定(1)炉帽倾角θ:本计算中取θ=65度(2)炉口直径d :炉口直径为熔池直径的43~53%,本计算中取48%则 d=48%D=0.48×5.646=2.710m(3)炉帽高度H 帽:炉帽高度是截椎体高度与炉口直线段高度值和。
180t顶吹氧转炉炉型设计1

学号:河北联合大学成人教育课程设计说明书180t顶吹氧气转炉炉型设计课程设计题目:学院:专业:班级:姓名:指导教师:2013年10月20日一、设计任务:1、原始条件炉子的平均出钢量为180t,钢水的收得率为92%,最大废钢比去20%,采用废钢矿石冷却,铁水采用P08低磷生铁[W(Si)≤ 0.85%, W(P)≤0.2%, W(S) ≤2、炉型选择:转炉炉型是指转炉炉膛的几何尺寸。
设计一座炉型结构合理,满足工艺要求的转炉是保证车间正常生产的前提,而炉型设计又是整个转炉设计的关键。
目前,转炉大体上归为以下三种炉型:筒球形、截锥形、锥球形。
为了满足顶吹的要求,炉型趋于矮胖型,且炉底为弧底,所以选筒球形。
3、炉容比:由于顶吹转炉吹炼过程中比较中稳,产生泡沫渣的量较多,因此炉容比的量较多,因此炉容比比顶吹炼的稍大,一般可选用0.90--- m333/t4、熔池尺寸计算中国设计部门推荐采用公式:D=D-熔池直径,m;G-新炉金属装入量,T; t-吹氧时间,min K-比例系数,(如表3-5所示)表3-5 不同吨位下的推荐K值吨位/t <20 30~50 50~120 200 250大容量取下限,小炉子取上限K此处根据180t 吨位取K 值为1.6。
老炉比新炉多产刚系数,一般B=10%~40%,大型转炉取下限,小型转炉取上限,此处取15%; a 、确定初期金属装入量G : 212T G B η=•=+金2×1802+0.15 ×10.92 =182(t) 根据熔池的定义,熔池体积V 池应等于金属液体积V 金。
即V 池=V 金; 式中 V 金-新炉金属装入量占有的体积,V 金=G 初/ρ金,【 ρ金:钢液密度33。
】熔池体积V 池 : V 池=V 金= G 初/ρ金=1826.83;b 、确定吹氧时间(t )=吨钢耗氧量(m 3/t )供氧强度[m 3/(t·min)];根据生产实践经验,供氧强度,一般低磷铁水为50~57 ,高磷铁水为62~69 m 3/ t 钢,本设计采用的是低磷铁水,取吨钢耗氧量为51m 3/ t 钢,而吹氧时间的选择如表表3-6 吹氧时间推荐值转炉吨位/t <50 50~80 >120 时间t/min12~1614~1816~20此处根据转炉吨位180t ,选择吹氧时间的推荐值为16min 。
转炉课程设计 - 副本
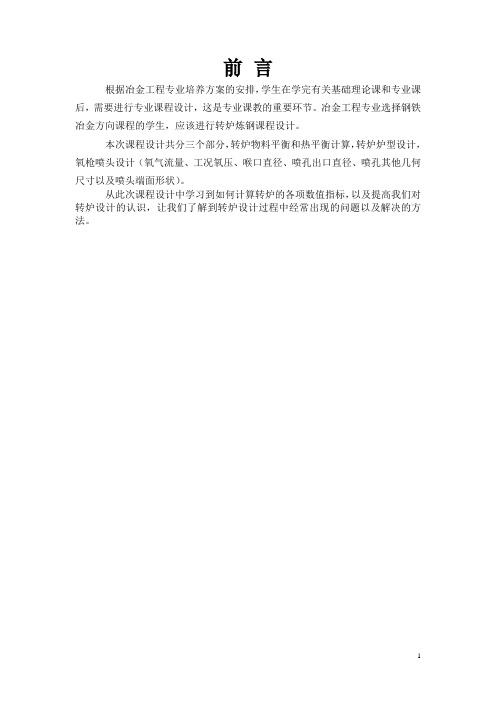
前言根据冶金工程专业培养方案的安排,学生在学完有关基础理论课和专业课后,需要进行专业课程设计,这是专业课教的重要环节。
冶金工程专业选择钢铁冶金方向课程的学生,应该进行转炉炼钢课程设计。
本次课程设计共分三个部分,转炉物料平衡和热平衡计算,转炉炉型设计,氧枪喷头设计(氧气流量、工况氧压、喉口直径、喷孔出口直径、喷孔其他几何尺寸以及喷头端面形状)。
从此次课程设计中学习到如何计算转炉的各项数值指标,以及提高我们对转炉设计的认识,让我们了解到转炉设计过程中经常出现的问题以及解决的方法。
目录1转炉物料平衡与热平衡计算------------------------------------------------------------31.1原始数据选取--------------------------------------------------------------------------31.2未加废钢和合金的物料平衡计算--------------------------------------------------51.3热平衡计算---------------------------------------------------------------------------111.4吨钢物料平衡------------------------------------------------------------------------15 2转炉炉型设计----------------------------------------------------------------------------162.1转炉炉型选择------------------------------------------------------------------------162.2转炉炉容比与高宽比---------------------------------------------------------------162.3转炉主要尺寸确定------------------------------------------------------------------162.4转炉炉体结构图---------------------------------------------------------------------19 3氧枪及底部供气构件设计-------------------------------------------------------------203.1原始条件------------------------------------------------------------------------------203.2计算氧气流量------------------------------------------------------------------------203.3喷孔出口直径------------------------------------------------------------------------213.4喷孔其他几何尺寸------------------------------------------------------------------213.5枪身各层钢管------------------------------------------------------------------------21 参考文献----------------------------------------------------------------------------------------231 转炉物料平衡与热平衡计算物料平衡是计算转炉炼钢过程中加入炉内与参与炼钢的全部物料(如铁水、废钢、氧气、冷却剂、渣料、合金添加剂、被侵蚀的炉衬等)和炼钢过程的产物(如钢水、炉渣、炉气、烟尘等)之间的平衡关系。
钢铁冶金专业毕业设计一80吨转炉
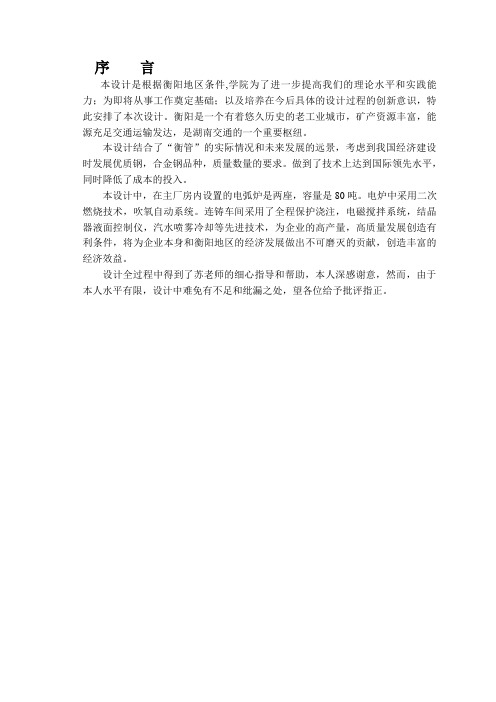
序言本设计是根据衡阳地区条件,学院为了进一步提高我们的理论水平和实践能力;为即将从事工作奠定基础;以及培养在今后具体的设计过程的创新意识,特此安排了本次设计。
衡阳是一个有着悠久历史的老工业城市,矿产资源丰富,能源充足交通运输发达,是湖南交通的一个重要枢纽。
本设计结合了“衡管”的实际情况和未来发展的远景,考虑到我国经济建设时发展优质钢,合金钢品种,质量数量的要求。
做到了技术上达到国际领先水平,同时降低了成本的投入。
本设计中,在主厂房内设置的电弧炉是两座,容量是80吨。
电炉中采用二次燃烧技术,吹氧自动系统。
连铸车间采用了全程保护浇注,电磁搅拌系统,结晶器液面控制仪,汽水喷雾冷却等先进技术,为企业的高产量,高质量发展创造有利条件,将为企业本身和衡阳地区的经济发展做出不可磨灭的贡献,创造丰富的经济效益。
设计全过程中得到了苏老师的细心指导和帮助,本人深感谢意,然而,由于本人水平有限,设计中难免有不足和纰漏之处,望各位给予批评指正。
1 设计概述1.1 设计依据根据冶金工程教研室下达的任务书。
1.2 设计原则和指导思想对设计的总要求是技术先进,工艺上可行;经济上合理。
所以,设计应遵循的原则和指导思想是:1)遵守国家的法律、法规,执行行业设计有关标准、规范和规定,严格把关,精心设计;2)设计中对主要工艺流程进行多方案比较,以确定最佳方案;3)设计中应充分采用各项国内外成熟的新技术,因某种原因暂时不上的新技术要预留充分的可能性。
所采用的新工艺、新设备、新材料必须遵循经过工业性试验或通过技术鉴定的原则;4)要按照国家有关劳动安全、工业卫生及消防的标准及行业设计规定进行设计;5)在学习、总结国内外有关厂家的生产经验的基础上,移植适用可行的先进技术;6)设计中应充分考虑节约能源、节约用地,实行资源的综合利用,改善劳动条件以及保护生态环境。
1.3 厂址及建厂条件论证湘潭位于湖南中部,地处湘中中游。
气候温和,土地肥沃,物产丰富。
转炉炼钢课程设计
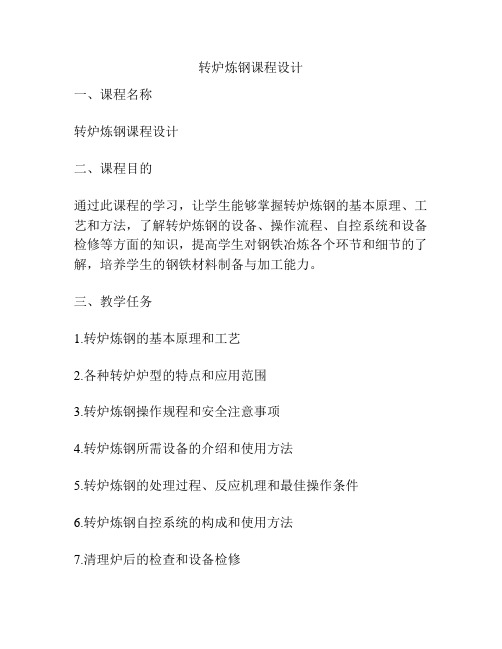
转炉炼钢课程设计一、课程名称转炉炼钢课程设计二、课程目的通过此课程的学习,让学生能够掌握转炉炼钢的基本原理、工艺和方法,了解转炉炼钢的设备、操作流程、自控系统和设备检修等方面的知识,提高学生对钢铁冶炼各个环节和细节的了解,培养学生的钢铁材料制备与加工能力。
三、教学任务1.转炉炼钢的基本原理和工艺2.各种转炉炉型的特点和应用范围3.转炉炼钢操作规程和安全注意事项4.转炉炼钢所需设备的介绍和使用方法5.转炉炼钢的处理过程、反应机理和最佳操作条件6.转炉炼钢自控系统的构成和使用方法7.清理炉后的检查和设备检修四、教学内容1.转炉炼钢的基本原理和工艺(1)转炉炼钢钢种和质量要求(2)在转炉炼钢中应用的基本原理(3)转炉炼钢工艺的基本流程2.各种转炉炉型的特点和应用范围(1)各种转炉炉型的特点(2)各种转炉炉型的应用范围3.转炉炼钢操作规程和安全注意事项(1)操作规程的概述(2)操作指导(3)操作注意安全事项4.转炉炼钢所需设备的介绍和使用方法(1)转炉炼钢所需主要设备的特点和作用(2)如何操作转炉所需设备5.转炉炼钢的处理过程、反应机理和最佳操作条件(1)转炉炼钢的主要处理过程(2)转炉炼钢的反应机理(3)转炉炼钢的最佳操作条件6.转炉炼钢自控系统的构成和使用方法(1)转炉炼钢的自控系统构成(2)使用方法7.清理炉后的检查和设备检修(1)清理炉后的检查(2)设备检修五、教学方法1.教学以理论课为主,结合实际案例进行分析2.采用讲述和互动交流相结合的方法,让学生能够更好的理解和掌握内容3.采取课堂讨论和研究报告相结合的方式,让学生主动参与和发言六、教材及参考书目教材:《钢铁原理》,邹国华、徐福坦参考书目:1.《钢铁冶炼技术手册》,吕永卫、沈友智2.《钢铁冶炼学》,邵益民3.《钢铁大全》,付继红4.《现代钢铁工程》,陈洛南、彭元锋七、考核评价考核方式:1.平时成绩(作业、课堂表现、实验)2.期末考试3.论文报告评价标准:1.学生是否能够掌握理论和实践知识2.学生是否能够独立思考问题并做出自己的解决方案3.学生是否能够有效地表达自己的观点和意见4.学生是否能够遵守学习纪律和考试要求5.学生是否能够积极参加课程的讨论和研究活动八、课程总结通过这门课程的学习,学生将深入了解和掌握转炉炼钢的基本知识和技能,能够熟练掌握钢铁冶炼中的各个环节和要素,为未来的学习和工作奠定坚实的基础。
- 1、下载文档前请自行甄别文档内容的完整性,平台不提供额外的编辑、内容补充、找答案等附加服务。
- 2、"仅部分预览"的文档,不可在线预览部分如存在完整性等问题,可反馈申请退款(可完整预览的文档不适用该条件!)。
- 3、如文档侵犯您的权益,请联系客服反馈,我们会尽快为您处理(人工客服工作时间:9:00-18:30)。
内蒙古科技大学冶金工程课程设计说明书180t氧气转炉设计学生姓名顼鑫班级10级冶金6班学号1076806630 指导老师富晓阳冶金工程年月日目录1转炉物料平衡与热平衡计算---------------------------------------------------------11.1原始数据选取---------------------------------------------------------------------11.2未加废钢和合金的物料平衡计算---------------------------------------------31.3热平衡计算-----------------------------------------------------------------------91.4加废钢和合金的物料平计算--------------------------------------------------12 2转炉炉型设计----------------------------------------------------------------------------152.1转炉炉型选择--------------------------------------------------------------------152.2转炉炉容比与高宽比-----------------------------------------------------------152.3转炉主要尺寸确定--------------------------------------------------------------152.4转炉炉体结构图-----------------------------------------------------------------18 参考文献-------------------------------------------------------------------------------------21转炉物料平衡与热平衡计算物料平衡是计算转炉炼钢过程中加入炉内与参与炼钢的全部物料(如铁水、废钢、氧气、冷却剂、渣料、合金添加剂、被侵蚀的炉衬等)和炼钢过程的产物(如钢水、炉渣、炉气、烟尘等)之间的平衡关系。
热平衡是计算转炉炼钢过程的热量收入(如铁水物理热、化学热)和热量支出(如钢水、炉渣、炉气的物理热、冷却剂溶化和分解热)之间的平衡关系。
下面我以Q235钢为例,其规格成分为(%):C 0.14~0.22,Si 0.12~0.30,Mn 0.40~0.65,P≤0.045,S≤0.0501.1 原始数据的选取1.1.1 原材料成分(表1-1~表1-5)表1-1 铁水、废钢成分(%)注:《C》和《Si》按实际上生产选取;《Mn》《P》《S》分别按铁水中相应成分的30%,10%,60%留在钢水中设定表1-2 渣料和炉衬(原材料)材料成分(%)表1-3 铁合金成分(分子)及其回收率(分母)1--4假设条件(工艺参数设定值)1.2冶炼钢种及规格成分要求冶炼低碳钢,以Q235钢为例,其规格成分为(%):C 0.14~0.22,Si 0.12~0.30,Mn 0.40~0.65,P≤0.045,S≤0.0501.2 未加废钢和合金的物料平衡计算物料平衡基本项目:(1)收入项:铁水、废钢、溶剂(石灰、萤石、白云石)、氧气、炉衬蚀损、铁合金。
(2)支出项:钢水、炉渣、烟尘、渣中铁珠、炉气、喷溅。
1.2.1渣量及其成分计算根据铁水、渣料质量及其冶炼钢种的要求,采用单渣法操作。
为了简化运算,以100 kg铁水为计算基础。
(1)铁水中元素氧化量(表1-6)氧化量=元素在铁水中的含量–元素在钢水中的含量表1-6 铁水中的元素氧化量由表1-6知:脱磷率= 0.099 / 0.11×100% =90%;脱硫率 =0.012 /0.03×100% =40%;钢中残锰量 =0.09 /0.3×100% =30%.(2) 各元素耗氧量及氧化产物量(表1-7)表1-7 铁水中元素氧化量、氧化产物量注意*:1.假定炉内气化脱硫1/3;铁的氧化由表1-13得出。
(2).由CaO还原出的氧量;消耗的CaO量=0.0096×56/32=0.0168 kg(3) 渣料的加入量1) 萤石加入量:在本设计中,取萤石加入量为:100×0.25%=0.25 kg,其成分质量计算见表1-9. (质量计算中各成分质量百分数见表1-2)表1-9 萤石加入量及成分其中:2[P]+5/2O2=P2O5(P2O5)生成量 = 0.001×142/62 = 0.002 kg3) 白云石加入量 :为了提高转炉寿命,采用白云石造渣,根据已投产转炉的经验,在本设计中为:100×2.5%= 2.5 kg ,其成分质量计算见表1-10。
(质量计算中各成分质量百分数见表1-2)表1-10 生白云石加入量及成分其中:烧减是白云石中33CaCO MgCO 分解产生的2CO 气体。
4)炉衬侵蚀量:转炉炉衬在炉渣作用下,将被侵蚀和冲刷进入渣中,本设计中取铁水量的0.3%,即100×0.3% = 0.3 kg ,其成分质量计算见表1-11. (质量计算中各成分质量百分数见表1-2)表1-11 炉衬侵蚀量及成分其中:炉衬中碳的氧化与金属中氧化生成的CO 和CO 2比例相同。
即: [C]+1/2O 2=CO :氧化产物CO 量为:0.045×90%×28/12 =0.0945kg 耗氧量为:0.045×90%×16/12 = 0.054kg [C]+O 2=CO 2:氧化产物CO 2量为:0.045×10%×44/12 = 0.0165kg 耗氧量为:0.0165×32/44 = 0.012kg共消耗氧量=0.054+0.012 = 0.066kg5) 石灰加入量:根据铁水成分,取终渣碱度R=3.8,石灰加入量计算如下:∑(SiO2)=铁水[Si]生成(SiO2)+ 炉衬、白云石、萤石、矿石带入的(SiO2)=1.5+ 0.0051 + 0.011 + 0.014+0.015 =1.545kg∑(CaO)=白云石、炉衬、矿石带入(CaO)—铁水、矿石中S消耗CaO量=1.328 + 0.00357 +0.003—0.008-0.003×56/32=1.321kg石灰加入量 = {∑w(SiO2)×R - ∑w(CaO)}/wCaO有效×100%= (1.545×3.8 –1.321)/(90%–3.8×2.3%) ×100%= 5.599 kg注意:w CaO有效=w(CaO石灰)-R×w (SiO2石灰)其成分质量计算见表1-12. (质量计算中各成分质量百分数见表1-2)表1-12 石灰加入量及成分其中:[S]+(CaO)=(CaS)+[O]生成的(CaS) = 0.0045×72/32 = 0.010 kg6) 渣中的铁氧化物:对于冶炼Q235钢,根据已投产转炉渣中含∑(FeO)量,取(FeO)= 8.25%,(Fe2O3)= 5%。
7)终渣总量及成分:根据表1-7~表1-12中的数据,确定终渣总量及成分,见表1-13,若不计(FeO)、(Fe2O3),由表1-13中可得:CaO+MgO+SiO2+P2O5+MnO+Al2O3+CaF2+CaS=6.374+1.05+1.674+0.229+0.271+0.133+0.218+0.038=9.987kg已知(FeO)= 8.25%,(Fe2O3)= 5%,则其余渣应占渣量总数的86.75%。
故总渣量为9.987/86.75% = 11.512 kg由此可知:(FeO)= 11.512× 8.25% = 0.950 kg,(Fe2O3)= 11.512 × 5% = 0.704kg。
由于矿石和炉衬中带入部分(FeO)和(Fe2O3),其含量参见表1-2和1-10,实际铁氧化物为:(FeO)= 0.950— 0.143 = 0.807 kg ;其值列入表1-7.(Fe2O3)= 0.704 — 0.319— 0.002= 0.383 kg .其值列入表1-7表1-13 终渣总量及成分冶炼中的吹损计算1.2.2根据假设条件,渣中铁珠量为渣量的6%,喷溅损失为铁水量的1%,烟尘损失为铁水量的1.5%。
故可得到:渣中铁珠量 = 11.641× 6% = 0.698 kg喷溅损失量 = 100 × 1% = 1.0 kg烟尘铁损失量 = 100 × 1.5%×(75%×56/72 + 20%×112/160)= 1.085 kg 元素氧化损失 =6.891 kg (见表1-7)吹损总量 = 0. 698+ 1.0 + 1.085 + 6.891 = 9.665 kg钢水量 = 100 —9.665 = 90.335 kg .1.2.3 氧气消耗量计算1)元素氧化耗氧 =7.003kg(见表1-7);2)烟尘铁氧化耗氧 =100×1.5%(75%×16/72 + 20%×48/160)= 0.341 kg;3) 炉衬中碳氧化耗氧 = 0.066kg(见表1-10下)。
4)炉气自由氧含量=0.054kg故总耗氧量 = 6.605 + 0.341 + 0.066 +0.054 = 7.464kg.换算为标准体积为:7.464×22.4/32 = 5.225 m3即冶炼100 kg 铁水需要4.9013m氧气。
取氧气利用率为80%,则冶炼1 t 铁水的实际供氧量为:5.225/80%×10 = 65.313m3 /t由于氧气不纯,含有0.4%的氮气,故供氧时带入的氮气为:7.464× 0.4% = 0.028 kg其体积量为:0.028 ×22.4/28 = 0.023m3,则冶炼 1 t 铁水将会带入0.023 m3的氮气。
1.2.4炉气量及成分计算炉内产生的炉气由CO、CO2、SO2、H2O、N2和自由 O2组成。
其中:CO来源于铁水和炉衬中的碳氧化;CO2来源于铁水、炉衬中碳氧化,以及白云石和石灰石中的烧减量;SO2来源于铁水中硫氧化;H2O来源于矿石和萤石中;N2来源于供氧时被带入。