生产线模式的选择
几种生产模式的区别学习资料
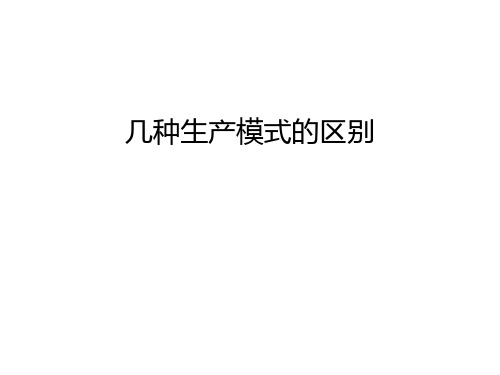
3.2 大量生产方式
1913年产生于美国福特汽车公司流水生产线
流水生产线——大量生产方式的典型运作模式
流水生产方式“拉开了现代工业生产的序幕”, 使制造业发生了革命性变化。以流水生产线为代表 的大批量生产方式主导了制造业近百年,对于人类 的进步做出了巨大贡献。大批量生产方式虽然目前 已日渐退出历史舞台,但流水生产线作为大批量生 产方式的早期运作模式却在不断发展、衍化和革新。
根据产品生产的重复程度和工作地的专业化程 度,可以把生产方式分为大量生产、单件生产和成 批生产类型。
大量生产——重复性生产,产品品种单一、产量大, 生产重复程度高。
成批生产——“成批轮番生产” ,产品品种较多,各 种产品, 在计划期内成批轮番生产。
单件生产——产品品种繁多,每种产品数量很少, 生产重复程度很低。产品专用件很多, 标准件和通用件所占比重很小。
下表1: 连续性生产与离散性生产特征
特征
连续性生产
离散性生产
用户数量 产品品种数 产品差别 自动化作业 设备布置的性质 设备布置的柔性 生产能力 扩充能力的周期 对设备可靠性要求 维修的性质 原材料品种数 能源消耗 在制品库存 副产品
较少
较多
较少
较多
有较多标准产品 有较多用户要求的产品
较易实现
较难实现
一、 流水生产的基本原理
+ 劳动分工原理
作业标准化原理
流水线生产
使用大型设备且 多台机器联用
生产力
支撑
管理技术 加工技术 自动控制技术
技术的进步
人类对产品的需求数 量大,且复杂性增加
市场的变化
二 、流水生产的特征
按照设计好的工艺流程顺序地通过每个工作地, 并按照统一的生产速度完成每道工序的加工作业任 务,是一个连续的不断重复的生产过程。其主要特 征是:
工业生产线故障模式与效果分析FMEA

工业生产线故障模式与效果分析FMEA工业生产线作为现代工业生产的重要组成部分,扮演着关键的角色。
然而,由于生产设备的复杂性和运行环境的变化,故障已经成为了生产线正常运行的主要威胁之一。
为了提高生产线的可靠性和稳定性,故障模式与效果分析(FMEA)成为了工业界广泛采用的一种方法。
本文将对工业生产线故障模式与效果分析进行探讨,并分析其在生产线优化中的应用。
一、FMEA概述故障模式与效果分析(FMEA)是一种通过系统性地识别、评估和优化潜在故障模式,从而改进产品或过程设计,提高系统可靠性的方法。
它通过从历史故障中学习,在设计阶段预测和控制潜在故障,以提高产品的质量和可靠性。
FMEA包括三个主要步骤:故障模式识别、故障后果评估和故障影响分析。
二、工业生产线故障模式分析在工业生产线中,常见的故障模式包括设备磨损、电磁干扰、电力供应中断、过载和过热等。
首先,设备磨损是导致设备失效的主要原因之一。
使用寿命过长或缺乏维护会导致设备部件磨损,从而引发故障。
其次,电磁干扰也是工业生产线中常见的故障模式。
电磁干扰可能来自外部电源或其他设备,对设备正常运行产生影响,甚至引发故障。
此外,电力供应中断也是导致生产线故障的主要原因之一。
电力供应中断会导致设备停机,造成生产线的停产。
最后,过载和过热也是工业生产线故障的常见模式。
设备超出额定负荷或长时间高温运行会导致设备过载和过热,加速设备寿命的衰退,增加故障发生的概率。
三、工业生产线故障效果评估故障效果评估是对故障发生的后果进行全面评估的过程。
根据故障类型和严重性,故障效果可以分为安全、环境和经济效果等。
首先,安全效果评估是对故障对操作人员和环境安全的潜在影响进行评估。
例如,机械设备故障可能导致人身伤害,而电力故障可能引发火灾等安全事故。
其次,环境效果评估是对故障对环境的潜在影响进行评估。
例如,设备故障可能导致污染物泄漏,对环境造成污染。
最后,经济效果评估是对故障对生产线正常运营和成本的影响进行评估。
钢材加工自动化生产线设计与优化
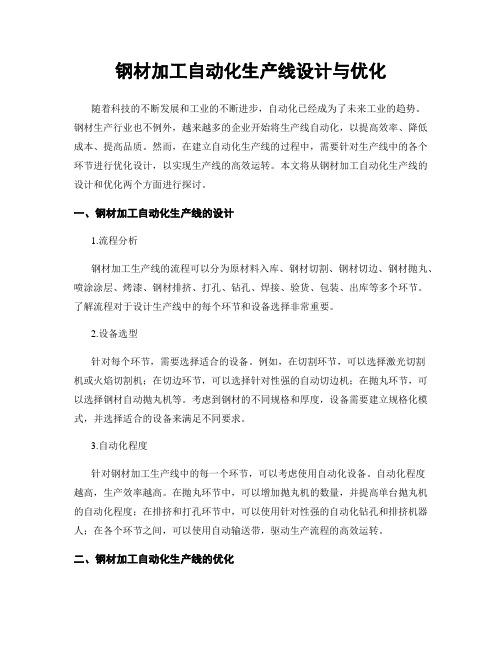
钢材加工自动化生产线设计与优化随着科技的不断发展和工业的不断进步,自动化已经成为了未来工业的趋势。
钢材生产行业也不例外,越来越多的企业开始将生产线自动化,以提高效率、降低成本、提高品质。
然而,在建立自动化生产线的过程中,需要针对生产线中的各个环节进行优化设计,以实现生产线的高效运转。
本文将从钢材加工自动化生产线的设计和优化两个方面进行探讨。
一、钢材加工自动化生产线的设计1.流程分析钢材加工生产线的流程可以分为原材料入库、钢材切割、钢材切边、钢材抛丸、喷涂涂层、烤漆、钢材排挤、打孔、钻孔、焊接、验货、包装、出库等多个环节。
了解流程对于设计生产线中的每个环节和设备选择非常重要。
2.设备选型针对每个环节,需要选择适合的设备。
例如,在切割环节,可以选择激光切割机或火焰切割机;在切边环节,可以选择针对性强的自动切边机;在抛丸环节,可以选择钢材自动抛丸机等。
考虑到钢材的不同规格和厚度,设备需要建立规格化模式,并选择适合的设备来满足不同要求。
3.自动化程度针对钢材加工生产线中的每一个环节,可以考虑使用自动化设备。
自动化程度越高,生产效率越高。
在抛丸环节中,可以增加抛丸机的数量,并提高单台抛丸机的自动化程度;在排挤和打孔环节中,可以使用针对性强的自动化钻孔和排挤机器人;在各个环节之间,可以使用自动输送带,驱动生产流程的高效运转。
二、钢材加工自动化生产线的优化1.提高生产效率钢材加工生产线中,提高生产效率是企业追求的目标之一。
通过钢材加工自动化生产线中的设备自动化程度的升级,减少生产过程中的人工操作。
同时,可优化各个工作环节之间的搭配和组合,降低生产流程中的等待时间,进一步提高生产效率。
2.降低人工成本钢材加工生产线中最高的成本之一是人工成本。
通过降低人工成本,降低生产成本显得尤为重要。
自动化设备替代人工操作能够有效降低人工成本,并降低由于人工操作操作所产生的误差和损失。
3.提高产品品质自动化生产线的建立不仅能够提高生产效率和降低生产成本,还能够保证产品质量。
多生产方法及混合模式差异

多生产方法及混合模式差异在现代工业生产中,有许多不同的生产方法和混合模式可以应用于不同的行业和制造过程。
这些方法和模式有着各自的特点和优势,可以根据实际需求进行选择和组合,以最大限度地提高效率和质量。
以下将详细介绍一些常见的生产方法及混合模式,并比较它们之间的差异。
1.原子(ATOM)生产方法:原子生产方法是一种以精确度和高度自动化为目标的生产方式。
它运用了最先进的技术和设备,通过高度集成的自动化系统,将整个生产过程分解成最小的原子操作单元,实现高度精确和高速度的生产。
2.分散(TOCTOM)生产方法:分散生产方法是一种较为灵活的生产方式,它将生产过程分散到不同的地点或部门进行,每个部门负责一部分工序。
这种分散的方式可以提高生产效率,减少生产线的浪费,并且可以更加灵活地调整生产的规模和产能。
3.现场(TSMPM)生产方法:现场生产方法是一种将生产过程直接搬到现场进行的生产方式。
在现场生产中,产品通常是根据客户的需求进行定制,并且在生产过程中可以及时做出调整。
这种生产方式可以更好地满足客户的需求,但也需要更多的人力和物力投入。
4.混合生产模式:混合生产模式是一种将不同的生产方法和模式进行组合的生产方式。
在混合生产模式中,可以根据具体情况选择最适合的生产方法和模式,以达到最佳的生产效果。
例如,可以将高自动化的原子生产方法与灵活性较高的分散生产方法相结合,形成一个混合生产模式。
这样可以同时享受高度精确和高速度的优势,又能够根据需要进行调整。
以上所述的生产方法和模式在很大程度上取决于生产过程的需求和特点。
原子生产方法适用于需要高精确度和高速度的生产过程,分散生产方法适用于具有较高灵活性要求的生产过程,现场生产方法适用于需要定制和及时调整的生产过程。
而混合生产模式则可以根据实际需求灵活选择和组合不同的生产方法和模式,以最大程度地发挥其优势。
总而言之,不同的生产方法和混合模式在应用于不同的行业和制造过程中有着各自的特点和优势。
柔性生产和传统生产的比较

柔性生产和传统生产的比较在工业制造领域中,随着科技的不断发展,柔性生产已经逐渐成为了一种趋势,并在许多领域中占据重要的地位。
柔性生产是一种新型的制造模式,它采用各种高度自适应的技术,具有较高的生产效率和灵活性。
与此相对比,传统生产则是一种相对较为固定的生产方式,它依赖特定的生产线和设备,常常需要大量的人工干预。
本文将比较分析柔性生产和传统生产各自的优点和缺点,并探讨未来制造产业的发展趋势。
一、柔性生产的优点1. 生产效率高:柔性生产模式中,生产设备可以自动化、智能化,可以在短时间内完成复杂的生产工序,从而提高了制造效率。
同时,生产过程中的数据可以通过智能化的系统进行及时监控,以便及时调整生产计划。
2. 生产成本低:柔性生产能够实现线上智能化监控,也能够有效降低人力和物流成本,进而控制生产成本。
同时,生产设备可以灵活选择,根据需求调整生产线并增加自动化程度,因此也可以节省系统维护成本。
3. 生产灵活性强:柔性生产模式中,生产系统可以根据市场需求进行调整,适应产品品种和数量的生产。
这样生产运作的灵活性就可以得到保证。
4. 生产质量高:在柔性生产中,可以使用智能化的系统对生产过程进行监控,及时发现和解决问题,大大提高了生产过程的可靠性。
同时,柔性为产品生产提供了一些功能,比如对于错误的纠正,提高产品质量。
二、柔性生产的缺点1. 技术更新周期短:由于柔性生产的快速发展,新的技术不仅出现频繁,而且更新周期较短,制造企业必须需要不断的在新技术领域中进行创新和变革。
2. 设备投资大:相对于传统生产设备,柔性生产设备的投资是相对较大的,对于小型或初创制造企业而言,成本压力较大。
3. 计算机系统影响:柔性生产依赖于大量计算机系统,在出现故障或计算机病毒时,生产系统可能会受到严重影响。
4. 生产管理困难:柔性生产模式下,由于设备的柔性和多样性,生产过程需要更为频繁的调整和管理,这种管理难度较大。
三、传统生产的优点1. 设备成熟稳定:相对于柔性生产中的快速创新,传统生产中的设备和技术是成熟稳定的,因此可以更好地控制风险。
生产线外包方案
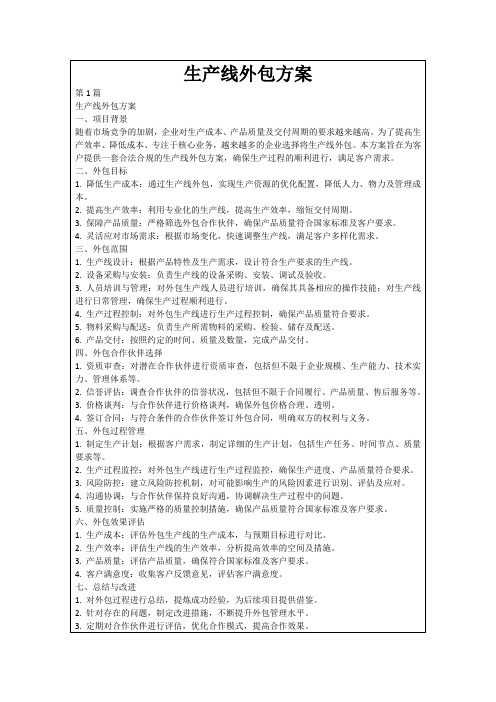
3.保障产品质量:严格筛选外包合作伙伴,确保产品质量符合国家标准及客户要求。
4.灵活应对市场需求:根据市场变化,快速调整生产线,满足客户多样化需求。
三、外包范围
1.生产线设计:根据产品特性及生产需求,设计符合生产要求的生产线。
2.设备采购与安装:负责生产线的设备采购、安装、调试及验收。
5.质量控制:实施严格的质量控制措施,确保产品质量符合国家标准及客户要求。
六、外包效果评估
1.生产成本:评估外包生产线的生产成本,与预期目标进行对比。
2.生产效率:评估生产线的生产效率,分析提高效率的空间及措施。
3.产品质量:评估产品质量,确保符合国家标准及客户要求。
4.客户满意度:收集客户反馈意见,评估客户满意度。
3.合作关系深化:与优质合作伙伴建立长期战略关系,共同发展。
本方案旨在为公司提供一套全面、严谨的生产线外包计划,通过专业化的管理和人性化的语言,确保方案的实施能够达到预期效果,助力公司持续发展。
四、外包合作伙伴选择
1.资质审查:对潜在合作伙伴进行资质审查,包括但不限于企业规模、生产能力、技术实力、管理体系等。
2.信誉评估:调查合作伙伴的信誉状况,包括但不限于合同履行、产品质量、售后服务等。
3.价格谈判:与合作伙伴进行价格谈判,确保外包价格合理、透明。
4.签订合同:与符合条件的合作伙伴签订外包合同,明确双方的权利与义务。
2.能力评估:通过现场考察、技术交流等方式,评估合作伙伴的生产管理能力和质量控制水平。
3.商务谈判:进行价格、交期、服务等多方面的商务谈判,确保合作条款的公平合理。
4.合同签订:与选定的合作伙伴签订正式外包合同,明确双方的权利、义务和责任。
生产线布局(超详细)全解
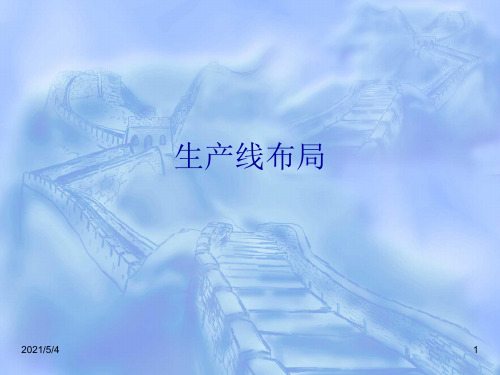
2021/5/4
44
产品原则布局
▪ 第四步:选择作业分配 工作
(以后续作业数量多少安 排作业)
2021/5/4
作业 A
B/D C/E F/G/H/I
J K
后续作业数量 6 5 4 2 1 0
45
产品原则布局
▪ 第五步对工作站安排作业,工作站周期:50.4秒
工作站 作业 时间(S)
工作站1 A
45
二、运输中的浪费
具有代表性的是,有些项目总是无工作性质地移动,时间 花费了在路途中,这是浪费。
2021/5/4
8
鉴别七大浪费
三、来自库存的浪费
库存代表着某些项目正等待某些事情的发生,这里的浪 费表现在:和保存着这些项目来等待有关联的成本,对 这些项目无增值而导致时间的损失。
安全库存是为了保证生产部门的正常运作和弥补不良品 的损失而存在的,但是安全库存不能够超出它们的正常 需要。
▪ 问:
• 金额如何计算出来的? • 组合布局方法或排列有多少种? • 如何排列的才是有效的?
2021/5/4
23
工艺原则布局
▪ 成本矩阵——方案一,总成本合计3474
11 2 3 4 5 6 7 82021/5/4
2
3
175 50
0
4
5
6
7
0
60 400 60
100 150 180 240
17 88 125 198
▪ 使用范围:
• 批量小 • 体积大
▪ 布局特点
• 以产品为中心 • 不考虑物流成本和复杂程度
2021/5/4
18
工艺原则布局
▪ 定义:
• 将相似的设备或功能集中放在一起的布局方式 • 也称车间布局,如车床车间
几种生产模式的区别-

劳动制度、岗位设置、 生产计划、工艺纪律、 质量管理、设备操作 维护规程、安全规程、 生产集成决策等。
企业生产类型
连续性生产和离散性生产 备货型生产和订货型生产 大量生产、成批生产和单件生产
2.1 连续性生产和离散性生产
根据生产对象在生产过程中运动得连续程
度,可以把企业分为连续性生产和离散性生产。
采用专用工装
每个工作地定期轮 番生产,每个工作 地专业化程度不高 一部分设备按机群 式布置,一部分设备 按部工分艺采过用程专布用置工装, 主要为通用工装
每个工作地完成多 种产品的生产,每个 工作地专业化程度很低
通用设备,按机群式布置
通用工装
生产对象 移 动方式
平行移动,少数用平 行顺序移动
平行顺序移动
单件生产
大量生产
多品种小批量生产
动因
生产力的发展 技术的进步 市场的变化
图1 生产方式得演变
3.1 单件生产方式
19世纪以前——手工作坊方式运作
19世纪初到20世纪20年代——作坊式单件生产 组织方式(“技艺”性运作方式)
目前, 这种生产模式主要针对消费需求中豪 华得、性能各异或独特得单件产品上,使用高度熟 练得技工、先进得生产设备,来满足大量生产方式 无法向消费者提供个性化产品得要求。——家庭 装饰业、Hi-End音响业、高档艺术品。
下表1: 连续性生产与离散性生产特征
特征
连续性生产
离散性生产
用户数量 产品品种数 产品差别 自动化作业 设备布置的性质 设备布置的柔性 生产能力 扩充能力的周期 对设备可靠性要求 维修的性质 原材料品种数 能源消耗 在制品库存 副产品
较少
较多
较少
较多
有较多标准产品 有较多用户要求的产品
- 1、下载文档前请自行甄别文档内容的完整性,平台不提供额外的编辑、内容补充、找答案等附加服务。
- 2、"仅部分预览"的文档,不可在线预览部分如存在完整性等问题,可反馈申请退款(可完整预览的文档不适用该条件!)。
- 3、如文档侵犯您的权益,请联系客服反馈,我们会尽快为您处理(人工客服工作时间:9:00-18:30)。
也谈生产线模式的选择
市场要求在变,生产模式也要变,只有适应市场才能拥有市场。
谈到生产模式的转变,其实有很多新的研究和理念不断出台,以生产线的布置来说,就经历了作坊,木板拉,流水线等模式,随后又出现了单元生产,单人生产,单件流生产,台车生产以及综合生产等新的生产模式。
但具体谈到某一公司的产品和市场,到底采取何种生产方式则需进行综合的评估才能做出合适的决择。
我们可以先对各种生产方式作一比较:
了解了各种生产模式的特点,还应分析本公司产品的下面三个特征,以便进一步选择合适的生产模式:
1P-Q分布2产品类型3工序复杂程度
1,P-Q分布指的公司产品的订单数与订单量的分布状态,如20%订单完成80%的产品,则这部分订单适合大量连续生产,同时说明另80%订单完成20%的产品,适合少量间断生产,可采取综合生产模式。
2,产品类型指其体积,重量,状态等特征适合哪一种模式。
如体积小,重量轻的可用单元式,单人式,而重型,大型组件则可籍流水线,
单件流,台车等协助移动。
3,工序复杂程度。
如本来就很简单的工序,就不必一定要流水线生产。
对于比较复杂的制程,可考虑适当细分,以尽量减少半成品种类,减少物流距离,减少搬运取放为目的。
针对具体的产品考虑上述因素,综合分析,才能选择出最适合的生产模式而不致盲目跟从,舍本逐末。
0%的产品,则这部分订单适合大量连续生产,同时说明另80%订单完成。