塑料模具设计说明书实例
塑料模具设计说明书实例
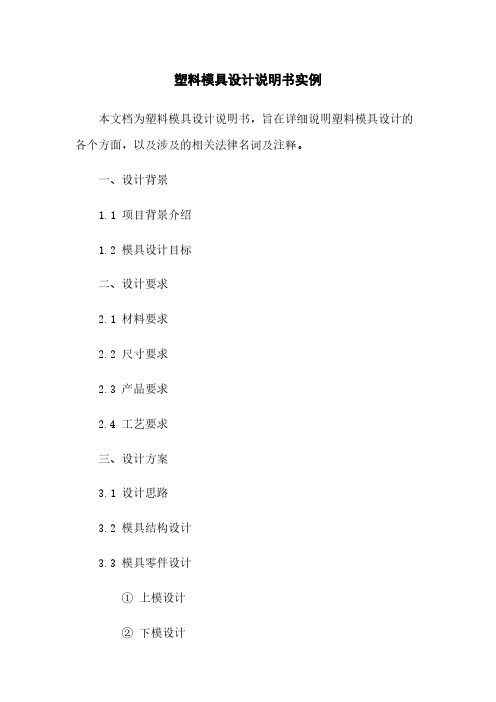
塑料模具设计说明书实例本文档为塑料模具设计说明书,旨在详细说明塑料模具设计的各个方面,以及涉及的相关法律名词及注释。
一、设计背景1.1 项目背景介绍1.2 模具设计目标二、设计要求2.1 材料要求2.2 尺寸要求2.3 产品要求2.4 工艺要求三、设计方案3.1 设计思路3.2 模具结构设计3.3 模具零件设计①上模设计②下模设计③滑动模设计④顶针设计3.4 模具槽设计3.5 模具总体设计四、零件加工与装配4.1 零件加工工艺4.2 模具装配工艺五、设计验证与修改5.1 模具样品检验5.2 修改方案六、其他设计考虑6.1 模具标准件选用6.2 模具自动化程度6.3 模具维修保养附件:详细图纸及说明法律名词及注释:1.模具:指用于制造特定形状、尺寸和表面质量的工业品的工具或设备。
2.材料要求:涉及模具所使用的材料的性能、可加工性和稳定性等方面的要求。
3.尺寸要求:模具设计需要满足的产品尺寸精度和公差要求。
4.产品要求:对模具加工后产品的外观、性能、规格等方面的要求。
5.工艺要求:模具设计中需要考虑的制造工艺、表面处理工艺等要求。
6.模具结构设计:根据产品形状和要求,设计模具的整体结构和组成方式。
7.模具零件设计:对模具的各个零部件进行细化设计,包括上模、下模、滑动模、顶针等。
8.模具槽设计:对模具槽的形状、尺寸和位置等进行设计。
9.模具样品检验:对模具制作完成后的样品进行外观质量、尺寸精度等方面的检验。
10.修正方案:根据样品检验结果,对模具进行必要的修改和调整。
塑料水杯注塑模具设计说明书

目录1 塑件的成型工艺分析 (3)1.1 塑件的原材料分析 (3)1.2 塑料件的尺寸分析 (3)1.3 塑件表面质量分析 (3)1.4 塑件结构工艺性分析 (4)1.5 成形工艺参数、工艺卡 (4)1.5.1 塑件的体积及质量 (4)1.5.2 选用注射机 (4)1.5.3 塑件注射成型工艺参数 (5)2 模具结构方案的确定 (6)2.1 型腔数目的确定 (6)2.2 分型面的选择 (7)2.3 浇注系统的设计 (8)2.3.1主流道的设计 (8)2.3.2 浇口的设计 (9)2.4 侧向抽芯系统设计 (10)2.4.1 侧向分型抽芯距的确定 (10)2.4.2 侧向分型抽芯力的计算 (10)2.4.3 斜导柱的设计 (11)2.4.4 斜导柱的材料及安装配合 (11)2.5 推出机构设计 (12)2.5.1 设计原则 (12)2.5.2 推杆材料 (12)2.5.3 推杆的形式 (12)2.5.4 推杆的导向 (13)2.5.5 推杆的复位 (13)2.6 标准模架的选择 (13)2.7 排气温控系统设计 (14)3 成型零件工作尺寸的计算 (14)3.1 成型零部件的磨损 (15)3.2 成型零部件的制造误差 (15)3.3 塑件的基本尺寸计算 (15)3.3.2 型腔深度 (15)3.3.3 型芯高度 (15)3.3.4 壁厚 (16)3.3.5 圆角 (16)3.3.6 柄长 (16)4 注射机有关工艺参数的校核 (17)4.1 注射量的校核 (17)4.2 注射压力的校核 (17)4.3 锁模力的校核 (17)4.4 装模部分有关尺寸的校核 (18)4.4.1 模具闭合高度的校核 (18)4.4.2 模具安装部分的校核 (18)4.4.3 模具开模行程的校核 (18)4.4.4 顶出部分的校核 (18)1、塑件的成型工艺分析1.1 塑件的原材料分析塑件原材料为PP 中文名: 聚丙烯表1.1 塑件的原材料分析结论:干燥处理:如果储存适当则不需要干燥处理。
塑料模具设计说明书(参考)
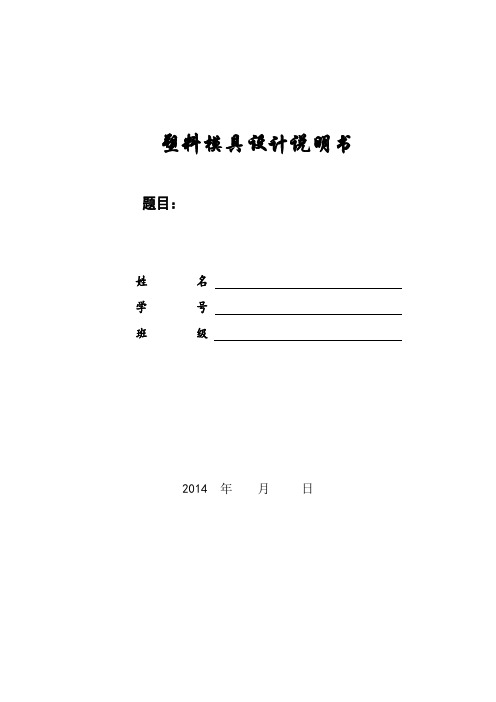
塑料模具设计说明书题目:姓名学号班级2014 年月日目录第一章塑件的工艺分析1.1 任务要求1.2 原料ABS的成型特性和工艺参数1.3 塑件的结构工艺性第二章注射设备的选择2.1 注射成型工艺条件2.2 选择注射机第三章型腔布局与分型面的选择3.1 塑件的布局3.2 分型面的选择第四章浇注系统的设计4.1主流道和定位圈的设计4.2 分流道设计4.3 浇口的设计4.4冷料穴的设计4.5 排气系统的分析第五章主要零部件的设计计算5.1 型芯、型腔结构的确定5.2 成型零件的成型尺寸第六章成型设备的校核6.1、注射成型机注射压力校核6.2、注射量的校核6.3、锁模力的校核相关零件图第一章塑件的工艺分析1.1 任务要求图1 盒盖1.2原料ABS的成型特性和工艺参数ABS是目前产量最大、应用最广的工程塑料。
ABS是不透明非结晶聚合物,无毒、无味,密度为 1.02~1.05 g/cm3。
ABS 具有突出的力学性能,坚固、坚韧、坚硬;具有一定的化学稳定性和良好的介电性能;具有较好尺寸稳定性,易于成型和机械加工,成型塑件表面有较好光泽,经过调色可配成任何颜色,表面可镀铬。
其缺点是耐热性不高,连续工作温度约为70℃,热变形温度约为93℃,但热变形温度比聚苯乙烯、聚氯乙烯、尼龙等都高;耐候性差,在紫外线作用下易变硬发脆。
可采用注射、挤出、压延、吹塑、真空成型、电镀、焊接及表面涂饰等多种成型加工方法。
ABS的成型特性:(1)ABS易吸水,成型加工前应进行干燥处理,表面光泽要求高的塑件应长时间预热干(2)流动性中等,溢边值0.04 mm左右。
(3)壁厚、熔料温度对收缩率影响极小,塑件尺寸精度高。
(4)ABS比热容低,塑化效率高,凝固也快,故成型周期短。
(5)ABS的表观黏度对剪切速率的依赖性很强,因此模具设计中大都采用点浇口形式。
(6)顶出力过大或机械加工时塑件表面会留下白色痕迹,脱模斜度宜取2°以上。
(7)易产生熔接痕,模具设计时应注意尽量减少浇注系统对料流的阻力。
塑料模具毕业设计说明书

1绪论1.1引言模具是制造业的一种基本工艺装备,它的作用是控制和限制材料(固态或液态)的流动,使之形成所需要的形体。
用模具制造零件以其效率高,产品质量好,材料消耗低,生产成本低而广泛应用于制造业中。
模具工业是国民经济的基础工业,是国际上公认的关键工业。
模具生产技术水平的高低是衡量一个国家产品制造水平高低的重要标志,它在很大程度上决定着产品的质量,效益和新产品的开发能力。
振兴和发展我国的模具工业,正日益受到人们的关注。
早在1989年3月中国政府颁布的《关于当前产业政策要点的决定》中,将模具列为机械工业技术改造序列的第一位。
模具工业既是高新技术产业的一个组成部分,又是高新技术产业化的重要领域。
模具在机械、电子、轻工、汽车、纺织、航空、航天等工业领域里,日益成为使用最广泛的主要工艺装备,它承担了这些工业领域中60%~90%的产品的零件,组件和部件的生产加工。
目前世界模具市场供不应求,模具的主要出口国是美国、日本、法国、瑞士等国家。
中国模具出口数量极少,但中国模具钳工技术水平高,劳动成本低,只要配备一些先进的数控制模设备,提高模具加工质量,缩短生产周期,沟通外贸渠道,模具出口将会有很大发展。
研究和发展模具技术,提高模具技术水平,对于促进国民经济的发展有着特别重要的意义。
1.2课题研究的目的与意义塑料模具产业近年来在我国发展很快,随之而来的是日益激烈的市场竞争,加入WTO后,外国模具厂家进入国内市场,要在激烈的竞争中脱颖而出,发展模具标准件实施模具的专业化生产至关重要。
现代产品生产中,模具由于其加工效率高,互换性好,节约原材料,所以得到很广泛的应用。
模具的用途广泛,模具的种类繁多,科学地进行模具分类,对有计划地发展模具工业,系统地研究、开发模具生产技术,促进模具设计、制造技术的现代化,充分发挥模具的功能和作用;对研究、制订模具技术标准,提高模具标准化水平和专业化协作生产水平,提高模具生产效率,缩短模具的制造周期,都具有十分重要的意义。
塑料模具设计说明书(参考)
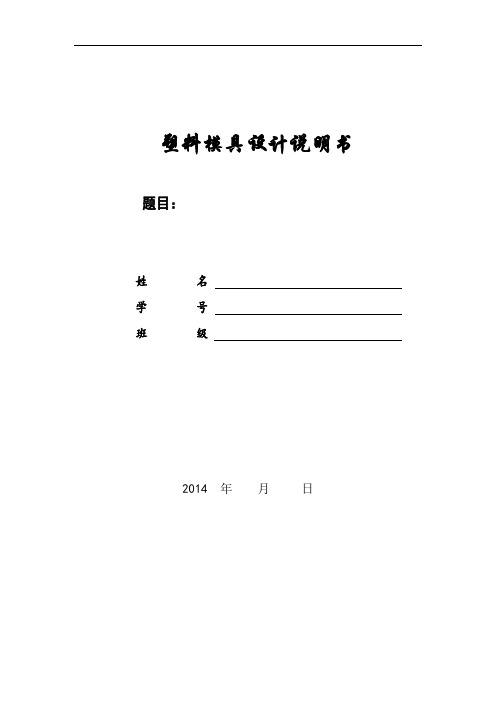
塑料模具设计说明书题目:姓名学号班级2014 年月日目录第一章塑件的工艺分析1.1 任务要求1.2 原料ABS的成型特性和工艺参数1.3 塑件的结构工艺性第二章注射设备的选择2.1 注射成型工艺条件2.2 选择注射机第三章型腔布局与分型面的选择3.1 塑件的布局3.2 分型面的选择第四章浇注系统的设计4.1主流道和定位圈的设计4.2 分流道设计4.3 浇口的设计4.4冷料穴的设计4.5 排气系统的分析第五章主要零部件的设计计算5.1 型芯、型腔结构的确定5.2 成型零件的成型尺寸第六章成型设备的校核6.1、注射成型机注射压力校核6.2、注射量的校核6.3、锁模力的校核相关零件图第一章塑件的工艺分析1.1 任务要求图1 盒盖1.2原料ABS的成型特性和工艺参数ABS是目前产量最大、应用最广的工程塑料。
ABS是不透明非结晶聚合物,无毒、无味,密度为 1.02~1.05 g/cm3。
ABS 具有突出的力学性能,坚固、坚韧、坚硬;具有一定的化学稳定性和良好的介电性能;具有较好尺寸稳定性,易于成型和机械加工,成型塑件表面有较好光泽,经过调色可配成任何颜色,表面可镀铬。
其缺点是耐热性不高,连续工作温度约为70℃,热变形温度约为93℃,但热变形温度比聚苯乙烯、聚氯乙烯、尼龙等都高;耐候性差,在紫外线作用下易变硬发脆。
可采用注射、挤出、压延、吹塑、真空成型、电镀、焊接及表面涂饰等多种成型加工方法。
ABS的成型特性:(1)ABS易吸水,成型加工前应进行干燥处理,表面光泽要求高的塑件应长时间预热干(2)流动性中等,溢边值0.04 mm左右。
(3)壁厚、熔料温度对收缩率影响极小,塑件尺寸精度高。
(4)ABS比热容低,塑化效率高,凝固也快,故成型周期短。
(5)ABS的表观黏度对剪切速率的依赖性很强,因此模具设计中大都采用点浇口形式。
(6)顶出力过大或机械加工时塑件表面会留下白色痕迹,脱模斜度宜取2°以上。
(7)易产生熔接痕,模具设计时应注意尽量减少浇注系统对料流的阻力。
(完整)注塑模具课程设计说明书范文+模版
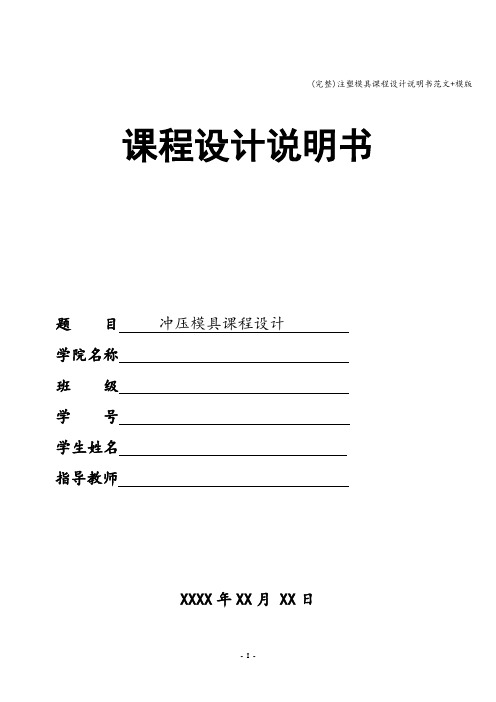
(完整)注塑模具课程设计说明书范文+模版课程设计说明书题目冲压模具课程设计学院名称班级学号学生姓名指导教师XXXX年XX月 XX日(完整)注塑模具课程设计说明书范文+模版摘要本文主要是关于酒瓶塞子的注塑工艺的分析及模具设计。
首先,对注塑工件进行了结构和工艺分析,确定了最佳成形方案;对整个塑件成形过程进行了模拟分析,预测了成形过程中可能出现的问题.根据分析结果,利用CAD等软件,完成了酒瓶塞子注塑模设计。
关键词;酒瓶塞子,CAD,注塑模(完整)注塑模具课程设计说明书范文+模版目录第一章概论 (1)1。
1 课题背景及意义 (1)1.2我国塑料模具现状及发展方向 (1)1.2。
1我国塑料模具的发展现状 (1)1。
2。
2我国塑料模具的发展方向 (3)第二章塑件工艺分析 (4)2.1塑件的工艺分析 (4)2。
1。
1分型面的选择 (5)2。
2塑件的材料分析 (5)2。
3塑件的表面分析 (1)2.4塑件的尺寸精度 (1)2。
5塑件的壁厚分析 (1)2.6塑件的脱模角度分析 (1)2.7塑件的圆角分析 (1)2。
8塑件的孔尺寸设计 (1)2。
9塑件的注塑工艺参数设置 (1)第三章模具设计 (3)3.1整体设计 (3)3.1.1模架结构选择 (3)3.1。
2注塑机的选择 (3)3.2系统设计 (4)3.2.1 浇注系统设计 (4)3。
2.2排气系统设计 (20)3。
2.3模温系统设计 (20)3。
3合模导向机构的设计 (21)3.3.1导套 (21)3。
3.2导柱 (22)3。
4侧向分型抽芯机构 ......................... 错误!未定义书签。
3.4.1抽芯距S .............................. 错误!未定义书签。
3.4。
2侧抽芯力FC .......................... 错误!未定义书签。
3.4.3斜导柱设计........................... 错误!未定义书签。
塑料模具设计说明书实例

塑料模具设计说明书目录1. 塑件成型工艺性分析 (2)1.1塑件的分析 (2)1.2 PS塑料的性能分析 (3)1.3 PS的注射成型过程及工艺参数 (3)2 模具的基本结构及模架选择 (4)2.1 模具的基本结构 (4)2.1.1 确定成型方法 (4)2.1.2 型腔布置 (4)2.1.3 确定分型面 (5)2.1.4 选择浇注系统 (5)2.1.5 确定推出方式 (6)2.1.6 侧向抽芯机构......................................................................... 错误!未定义书签。
2.1.7 模具的结构形式 (6)2.1.8 选择成型设备 (6)2.2 选择模架 (7)2.2.1 模架的结构 (7)2.2.2 模架安装尺寸校核 (8)3 模具结构、尺寸的设计计算 (8)3.1 模具结构设计计算 (8)3.1.1 型腔结构 (8)3.1.2 型芯结构 (9)3.1.3 斜导柱、滑块结构................................................................. 错误!未定义书签。
3.1.4 模具的导向结构 (9)3.1.5 结构强度计算(略) (9)3.2 模具成型尺寸设计计算 (9)3.2.1 型腔径向尺寸 (9)3.2.2 型腔深度尺寸 (10)3.2.3 型芯径向尺寸 (10)3.2.4 型芯高度尺寸 (10)3.3 模具加热、冷却系统的计算 (10)3.3.1 模具加热 (10)3.3.2 模具冷却 (11)4. 模具主要零件图及加工工艺规程 (12)4.1 模具定模板(中间板)零件图及加工工艺规程............................ 错误!未定义书签。
4.2 模具侧滑块零件图及加工工艺规程................................................ 错误!未定义书签。
塑料模具毕业设计说明书例子

第三章成型设备的选用3.1 注塑机的选择塑件在分型面上的投影面积:1.754mm2塑件体积: V=1.168mm3塑件密度: =1.0g/cm3所以塑件的质量: m = 1.168×1.0=1.168g根据任务书的要求,该塑件采用侧浇口形式,并且采用一模两腔的形式,加上浇注系统及冷凝料材料体积约为?cm3。
所以初选设备为G54-S200/400其主要技术规格见表3.1。
表3.1 G54-S200/400设备主要技术规格3.2模架的选择通过塑件的分析,以及注塑机的技术规格要求,选用A2型模架,该模架各模板以及相关尺寸见图3.1、表3.2和表3.3。
图3.1 P2型模架示意图表3.2 模架各板厚尺寸表3.3模架孔位置尺寸H1=36㎜;A=56㎜;B=46㎜;H2=46㎜;C=76㎜;H3=36㎜;所以模具的总厚度为:36+56+46+46+76+36=296mm,在注塑机的装模行程之内。
3.3模具参数的校核(1)注射量的校核要求注射量不超过注射机的最大注射量,在注塑生产中,注塑机每一个成型周期向模具腔内注入的塑料熔体体积或质量称为塑件的注射量,其中包括浇注系统内所存留的塑料熔体体积,选择注塑机时,必须保证塑件的注射量小于注塑机的最大注射量的(80~85)%,最小注射量不小于注塑机注射量的20%,根据式kMmax≥M,M=n∑M i+m式中 Mmax-----注塑机最大注射量/ cm3;Mi-----浇注系统凝料的质量或体积/ cm3;m-----单个制件质量或体积/ cm3;n-----型腔数目/个;k-----注射机最大注射量利用系数,一般取0.8。
0.8×320≥2×5.8+4.33≈15.93 cm3。
故:注射机注射量满足要求。
(2)注射压力的校核塑料成型所需要的注射压力是由塑料品种、注射机类型、喷嘴形式、塑件形状以及浇注系统的压力损失等因素决定的。
注射压力的校核是检验注射机的最大注射压力能否满足制品的成型要求。
- 1、下载文档前请自行甄别文档内容的完整性,平台不提供额外的编辑、内容补充、找答案等附加服务。
- 2、"仅部分预览"的文档,不可在线预览部分如存在完整性等问题,可反馈申请退款(可完整预览的文档不适用该条件!)。
- 3、如文档侵犯您的权益,请联系客服反馈,我们会尽快为您处理(人工客服工作时间:9:00-18:30)。
塑料模具设计说明书实例标准化管理部编码-[99968T-6889628-J68568-1689N]塑料模具设计说明书姓名吴高安班级模具1301塑料模具设计说明书目录1. 塑件的工艺分析塑件的成型工艺性分析塑件如图1所示。
图1 塑件图产品名称:套管产品材料:ABS产品数量:较大批量生产塑件尺寸:如图1所示塑件重量:25克塑件颜色:红色塑件要求:塑件外侧表面光滑,下端外沿不允许有浇口痕迹。
塑件允许最大脱模斜度°塑件材料ABS的使用性能可参考《简明塑料模具设计手册》P30表1-13综合性能较好,冲击韧度、力学强度较高,尺寸稳定,耐化学性、电气性能良好;易于成形和机械加工,与有机玻璃的熔接性良好,可作双色成形塑件,且表面可镀铬。
适于制作一般机械零件、减摩耐磨零件、传动零件和电信结构零件。
塑件材料ABS的加工特性可参考《简明塑料模具设计手册》P32表1-14无定型塑料,其品种很多,各品种的机电性能及成形特性也各有差异,应按品种确定成形方法及成形条件。
吸湿性强,含水量应小于%,必须充分干燥,要求表面光泽的塑件应要求长时间预热干燥。
流动性中等,溢边料 mm左右(流动性比聚苯乙烯,AS差,但比聚碳酸酯、聚氯乙烯好)。
比聚苯乙烯加工困难,宜取高料温、模温(对耐热、高抗冲击和中抗冲击型树脂,料温更宜取高)。
料温对物性影响较大、料温过高易分解(分解温度为250℃左右,比聚苯乙烯易分解),对要求精度较高塑件,模温宜取50~60℃,要求光泽及耐热型料宜取60~80℃。
注射压力应比加工聚苯乙烯稍高,一般用柱塞式注塑机时料温为180~230℃,注射压力为100~140 MPa,螺杆式注塑机则取160~220℃,70~100 MPa为宜。
模具设计时要注意浇注系统,选择好进料口位置、形式。
推出力过大或机械加工时塑件表面呈现“白色”痕迹(但在热水中加热可消失)。
脱模斜度宜取2℃以上。
塑件的成型工艺参数确定可参考《简明塑料模具设计手册》P54表1-18查手册得到ABS塑料的成型工艺参数:适用注射机类型螺杆式密度~ g/cm3;收缩率~ % ;预热温度 80C°~ 85C°,预热时间 2 ~ 3 h ;料筒温度后段150C°~170C°,中段180C°~200C°,前段160C°~180C°;喷嘴温度 170C°~ 180C°;模具温度 50C°~ 80C°;注射压力 60 ~ 100 MPa ;成型时间注射时间20 ~ 90s ,保压时间0 ~ 5s ,冷却时间20 ~ 120s 。
2 模具的基本结构及模架选择模具的基本结构确定成型方法塑件采用注射成型法生产。
为保证塑件表面质量,使用直浇口成型,因此模具应为单分型面注射模。
型腔布置塑件形状较简单,重量较轻,生产批量较大。
所以模具采用一模二腔、平衡布置。
这样模具尺寸较小,制造加工方便,生产效率高,塑件成本较低。
其布置如图2所示。
图2 型腔布置确定分型面塑件分型面的选择应保证塑件的质量要求的同时要塑件脱模方便。
因此塑件选择如图3所示的分面。
图3分型面选择选择浇注系统塑件采用直浇口成型,其浇注系统如图4所示。
点浇口直径为Φ,点浇口长度为1mm,头部球~2mm。
分流道采用半圆截面流道,其半径R为3~。
主流道为圆锥形,锥角α为6,上部直径与注射机喷嘴相配合,下部直径Φ6~8mm。
图4点浇口浇注系统确定推出方式由于塑件形较小,使用推杆推出。
这种方法结构简单、拆装方便,推出可靠。
模具的结构形式模具结构为双分型面注射模,如图5所示。
图5双分型面注射模模具结构1—拉杆2—导套3—定模板(中间板)4—螺钉5—推件板6—复位杆7—动模板8—支承板9—推杆固定板10—推板11—垫块12—动模座板13—导柱14—导套15—导套16—定模做板17—脱出板18—导套19—导柱20—限位螺钉选择成型设备“注射机的选用”可参考《简明塑料模具设计手册》P133,P128表3-4选用G54-S200/400型卧式注射机,其有关参数为:额定注射量200/400cm3;注射压力109MPa;锁模力2540kN;最大注射面积645cm2;模具厚度165~406mm;最大开合模行程260mm;喷嘴圆弧半径18mm;喷嘴孔直径4mm;拉杆间距:290×368mm。
选择模架模架的结构可参考《简明塑料模具设计手册》P418表10-1—10-6模架的结构如图6所示。
图6模架模架安装尺寸校核模具外型尺寸为,长300mm、宽250mm、高345mm,小于注射机拉杆间距和最大模具厚度,可以方便地安装在注射机上。
3模具结构、尺寸的设计计算模具结构设计计算型腔结构见装配图所示,型腔由定模板4、定模镶件26和滑块19共三部分组成。
定模板4和滑块19构成塑件的侧壁,定模镶件26成型塑件的顶部,而且点浇口开在定模镶件上,这样使加工方便,有利于型腔的抛光。
定模镶件可以更换,提高了模具的使用寿命。
型芯结构见装配图所示,型芯由动模板16上的孔固定。
型芯于推件板18采用锥面配合,以保证配合紧密,防止塑件产生飞边。
另外,锥面配合可以减少推件板在推件运动时与型芯之间的磨损。
型芯中心开有冷却水孔,用来强制冷却型芯。
斜导柱、滑块结构见装配图。
模具的导向结构为了保证模具的闭合精度,模具的定模部分与动模部分之间采用导柱1和导套2导向定位。
推件板18上装有导套6,推出时,导套6在导柱1上运动,保证了推件板的运动精度。
定模座板上装有导柱30,为点浇口凝料推板24和定模板4的运动导向。
结构强度计算(略)模具成型尺寸设计计算可参考《简明塑料模具设计手册》P110表2-55取ABS的平均成型收缩率为%,塑件未注公差按照SJ1372中8级精度公差值选取。
塑件尺寸如图1所示。
型腔径向尺寸模具最大磨损量取塑件公差的1/6;模具的制造公差δz=Δ/3;取x=。
1)Φ40+→Φ)R25+→型腔深度尺寸模具最大磨损量取塑件公差的1/6;模具的制造公差δz=Δ/3;取x=。
1)50+→)45+→型芯径向尺寸模具最大磨损量取塑件公差的1/6;模具的制造公差δz=Δ/3;取x=。
1)Φ+→Φ+2)Φ10+→Φ10+型芯高度尺寸模具最大磨损量取塑件公差的1/6;模具的制造公差δz=Δ/3;取x=。
1)+→+2)15+→15+模具加热、冷却系统的计算模具加热一般生产ABS材料塑件的注射模具不需要外加热。
模具冷却模具的冷却分为两部分,一部分是型腔的冷却,另一部分是型芯的冷却。
型腔的冷却是由在定模板(中间板)上的两条ф10mm的冷却水道完成,如图7所示。
图7定模板冷却水道型芯的冷却如图8所示,在型芯内部开有ф16mm的冷却水孔,中间用隔水板2隔开,冷却水由支承板5上的ф10mm冷却水孔进入,沿着隔水板的一侧上升到型芯的上部,翻过隔水板,流入另一侧,再流回支承板上的冷却水孔。
然后继续冷却第二个型芯,最后由支承板上的冷却水孔流出模具。
型芯1与支承板5之间用密封圈3密封。
图8型芯的冷却1—型芯2—隔水板3—密封圈4—动模板(型芯固定板)5—支承板4.模具主要零件图及加工工艺规程模具定模板(中间板)零件图及加工工艺规程定模板(中间板)零件图如图9所示。
图9定模板(中间板)零件图定模板(中间板)的加工工艺:(1)以基准角定位,加工ф52+和ф+的型腔孔,可以采用坐标镗床或加工中心完成。
(2)以基准角定位,加工宽32mm、长40mm、深25mm及宽10mm、深的装配侧滑块孔,可以采用铣床或加工中心完成。
(3)以基准角定位,加工宽32mm、长20mm、深40mm的斜楔装配孔及其上的M8螺钉沉孔,可以采用铣床和钻床完成。
(4)钳工研配侧滑块和斜楔。
(5)将侧滑块装入定模板侧滑块孔内锁紧固定,共同加工ф15mm的斜导柱孔,可以采用铣床或钻床完成。
(6)以基准角定位,加工4-ф16mm孔,可以采用钻床或铣床完成。
(7)加工2-ф10mm冷却水孔,由钻床或深孔钻床完成。
模具侧滑块零件图及加工工艺规程侧滑块零件图如图10所示。
图10侧滑块零件图侧滑块加工工艺如下:(1)加工外形尺寸,由铣床或加工中心完成。
(2)钳工研配,首先与推件板研配侧滑块的滑道部分,要求滑动灵活,无晃动间隙;其次研配侧滑块与型芯及定模板的配合,要求配合接触紧密,注射成型时不产生飞边;最后研配斜楔,要求斜楔在注射成型时锁紧侧滑块。
(3)与定模板配钻斜导柱孔。
(4)加工侧滑块的两个ф3mm定位凹孔。
模具动模板(型芯固定板)零件图及加工工艺规程动模板(型芯固定板)零件图如图11所示。
图11动模板(型芯固定板)零件图动模板(型芯固定板)加工工艺如下:(1)以基准角定位,加工ф50+和ф60mm的型芯固定孔,可以采用坐标镗床或加工中心完成。
(2)以基准角定位,加工4-ф21mm孔,可采用镗床或钻床完成。
(3)钳工装配型芯。
5模具总装图及模具的装配、试模模具总装图图12为模具的总体装配图。
图12模具图1—导柱2—导套3—拉杆4—定模板(中间板)5—螺钉6—导套7—复位杆8—动模座板9—螺钉10—推板11—推杆固定板12—垫块13—支承板14—密封圈15—隔水板16—动模板(型芯固定板)17—定位珠18—推件板19—侧滑块20—斜楔21—斜导柱22—型芯23—螺钉24—脱出板25—定模座板26—定模镶件27—拉料杆28—定位圈29—浇口套30—导柱31—导套32—导套33—限位螺钉模具的安装试模试模是模具制造中的一个重要环节,试模中的修改、补充和调整是对于模具设计的补充。
试模前的准备试模前要对模具及试模用的设备进行检验。
模具的闭合高度,安装与、于注射机的各个配合尺寸、推出形式、开模距、模具工作要求等要符合所选设备的技术条件。
检查模具各滑动零件配合间隙适当,无卡住及紧涩现象。
活动要灵活、可靠,起止位置的定位要正确。
各镶嵌件、紧固件要牢固,无松动现象。
各种水管接头、阀门、附件、备件要齐全。
对于试模设备也要进行全面检查,即对设备的油路、水路、电路、机械运动部位、各操纵件和显示信号要检查、调整,使之处于正常运转状态。
模具的安装及调试模具的安装是指将模具从制造地点运至注射机所在地,并安装在指定注射机的全过程。
模具安装在注射机上要注意以下方面:1)模具的安装方位要满足设计图样的要求。
2)模具中有侧向滑动结构时,尽量使其运动方向为水平方向。
3)当模具长度与宽度尺寸相差较大时,应尽可能使较长的边与水平方向平行。
4)模具带有液压油路接头、气路接头、热流道元件接线板时,尽可能放置在非操作一侧,以免操作不方便。
模具在注射机上的固定多采用螺钉、压板的形式,如图13所示。
一般采用4-8块压板,对称布置。