冲压模具制作技术要求
毕业设计冲压模具设计

毕业设计冲压模具设计冲压模具设计是指根据零部件的形状和要求,通过模具设计软件对压制工艺和模具结构进行详细设计并完成加工制造的过程。
本文将以零部件的冲压模具设计为例,详细介绍冲压模具设计的步骤和关键技术。
一、冲压模具设计的步骤1.零件分析与加工工艺确定:首先对待设计的零件进行分析,了解其形状、材料及加工工艺要求。
通过对零件的尺寸测量、材料分析和工艺流程确定,确定适宜的冲压模具设计方案。
2.模具结构确定:根据零件形状和工艺要求,确定模具的基本结构形式,包括上、下模块的形状和结构、导向方式以及顶出装置的设计。
3.模具零件设计:根据模具的结构形式,对上、下模板、定位销、导柱、导套、顶出器等模具零件进行详细设计,并确定其尺寸、形位公差和表面粗糙度。
4.模具装配设计:根据模具零件的设计,进行模具的装配设计,确定模具各零件的加工工艺和装配工艺。
5.3D模型的建立:采用模具设计软件对模具的各个零件进行建模,并对其进行装配,实现模型的全面展示和动态演示。
6.模具结构的强度分析:采用有限元分析法对模具结构进行强度分析,确定模具零件的受力状态,从而提高模具的刚度和寿命。
7.模具工艺文件的编制:编制模具的工艺文件,包括工艺流程、工装设计和使用说明,为模具的制造和使用提供详细的技术支持。
二、冲压模具设计的关键技术1.零件厚度均衡设计:保证冲压零件的均衡受力,在模具的设计中尽量避免出现片厚不均的问题,从而避免在冲压过程中产生变形或裂纹等缺陷。
2.弹性顶出设计:在模具设计中合理设置顶针或顶出器,以保证冲压零件在顶出过程中不会卡死或破碎,从而提高冲压的质量和效率。
3.导向方式优化设计:合理选择导向方式,减小模具的摩擦阻力,从而提高模具的导向精度和工作寿命。
4.材料选择与热处理:合理选择模具材料,并根据工艺要求进行适当的热处理,以提高模具的硬度和耐磨性,延长模具的使用寿命。
5.模腔润滑与冷却设计:在模具设计中设置合理的润滑和冷却装置,以提高冲压的质量和效率,并减少模具的磨损和热变形。
冲压工艺技术要求

冲压工艺技术要求冲压工艺技术要求冲压工艺技术是一种利用模具和压力将板材或线材形成所需形状和尺寸的金属加工工艺。
在冲压过程中,材料经过剪切、变形、伸长等加工过程,逐渐形成零件。
冲压工艺技术的要求主要包括以下几个方面:1. 设计要求:在进行冲压工艺设计时,要根据产品的要求和使用情况,确定最佳的材料、厚度、模具形状和结构等。
同时,还应考虑到材料的可行性、加工精度和生产效率等因素。
2. 材料要求:冲压工艺过程中所使用的材料应具备良好的可塑性和可加工性。
常用的冲压材料有钢板、铝板、铜板等,其材料性能应满足产品的使用要求,并具有良好的机械性能和耐腐蚀性。
3. 模具要求:模具是冲压工艺的关键设备,其质量直接影响到冲压零件的质量和生产效率。
模具应具备高强度、高硬度、耐磨性和尺寸稳定性等特性。
同时,还要具备良好的导向、抛光和冷却性能,以确保冲压过程的稳定性和质量。
4. 机械设备要求:冲压工艺需要使用冲床或其他冲压设备。
机械设备的性能和稳定性是冲压过程能否顺利进行的关键。
设备应具备足够的强度和刚性,能够承受所需的压力和冲击力,同时具备良好的运行速度和控制精度。
5. 工艺参数要求:冲压工艺的实施需要合理的工艺参数和操作方法。
工艺参数包括冲程、冲次、冲液量、冲针直径等。
这些参数的合理设置可以提高冲压效果、减少能耗和生产成本。
6. 质量控制要求:冲压工艺过程中,对产品的质量和尺寸要求非常严格。
在冲压过程中,应对每个工序进行严格的检验和控制,及时发现和解决问题,以确保零件的质量和性能符合要求。
7. 安全要求:冲压工艺需要使用大量的机械设备和工具。
为了确保操作人员的安全,要进行必要的安全防护措施,并对操作人员进行安全培训。
同时,应检查和保养设备,确保设备的正常运行。
冲压工艺技术要求的主要目标是提高产品质量、降低生产成本、提高生产效率和保障操作人员的安全。
通过合理的冲压工艺设计和控制,可以提高产品的外观质量和工作性能,达到客户的要求,并在市场竞争中取得优势。
冲压件技术要求范文
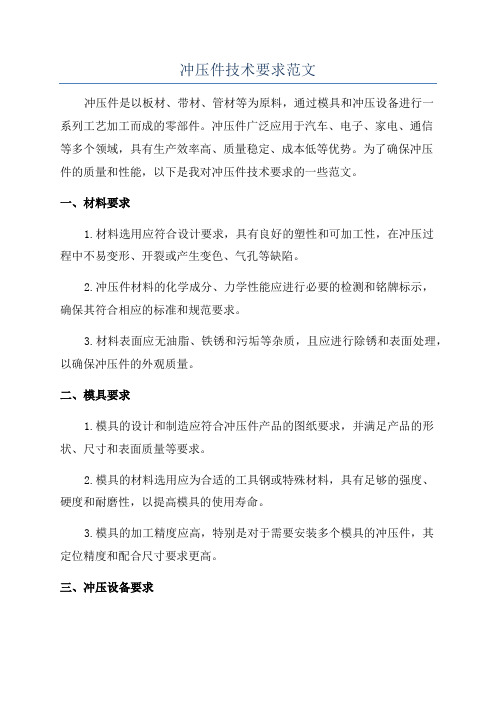
冲压件技术要求范文冲压件是以板材、带材、管材等为原料,通过模具和冲压设备进行一系列工艺加工而成的零部件。
冲压件广泛应用于汽车、电子、家电、通信等多个领域,具有生产效率高、质量稳定、成本低等优势。
为了确保冲压件的质量和性能,以下是我对冲压件技术要求的一些范文。
一、材料要求1.材料选用应符合设计要求,具有良好的塑性和可加工性,在冲压过程中不易变形、开裂或产生变色、气孔等缺陷。
2.冲压件材料的化学成分、力学性能应进行必要的检测和铭牌标示,确保其符合相应的标准和规范要求。
3.材料表面应无油脂、铁锈和污垢等杂质,且应进行除锈和表面处理,以确保冲压件的外观质量。
二、模具要求1.模具的设计和制造应符合冲压件产品的图纸要求,并满足产品的形状、尺寸和表面质量等要求。
2.模具的材料选用应为合适的工具钢或特殊材料,具有足够的强度、硬度和耐磨性,以提高模具的使用寿命。
3.模具的加工精度应高,特别是对于需要安装多个模具的冲压件,其定位精度和配合尺寸要求更高。
三、冲压设备要求1.冲压设备应具备一定的生产能力,能够满足冲压件的生产需求,同时具有稳定的性能和可靠的操作。
2.冲压设备操作人员应受过专业培训,熟悉设备的操作规程和安全操作要求。
3.冲压设备的维护保养应及时进行,定期检查和更换易损件,确保设备的正常运行和延长设备的使用寿命。
四、工艺要求1.冲压件的加工工艺应合理安排,包括材料的选取、切割、热处理、冲压、整形、表面处理等环节,以保证冲压件的尺寸精确和表面质量。
2.冲压件的加工过程应控制加工温度、冲压速度、冲压压力等参数,确保冲压件的加工质量。
3.对于特殊形状和质量要求较高的冲压件,应进行工艺试验和工艺评定,确保冲压件的稳定批量生产。
同时,应建立相应的工艺文件,便于工艺操作和质量控制。
五、质量要求1.冲压件的尺寸精确度应符合设计要求,并进行必要的检验记录,确保冲压件的尺寸和几何形状的一致性。
2.冲压件表面质量应平整、光洁,不应有划痕、凹陷和缺陷等不良现象。
冲压件技术要求

模具设计制造技术要求一、总体要求设计和制造K综合车架增加的冲压件模具。
生产纲领:年产3万辆,双班制。
模具使用寿命30万次。
二、模具规格1.模具结构形式(1)模具结构形式为钢板式结构或框架式结构,所有尺寸及零部件:选用及加工均采用公制。
模具本体为钢板式结构:参照《中国机械工业标准模具卷》钢板模架标准进行设计,应保证模具的强度、钢度和外观质量。
材质为45号钢。
模具本体为框架式结构:模板选用(汽车冲模标准汇编)模架标准,材质为ZG45。
(2)导柱,导套采用压入式结构。
选用(汽车冲模标准汇编)QM1201、QM1221标准。
拉延模可采用导板导向,导板采用自润滑式导板。
(3)所有模具凸凹模工作部位局部或整体淬火后,不允许出现软点、烧伤、裂纹。
(4)模具图中应反映模具的进、出料方向,气顶杆位置,闭合高度。
(5)模具定位要操作方便、可靠,模具上、下模前端标记处明显。
(6)修边废料可以人工收集,易于拿取;废料不能滑出工作台,原则上采用废料盒装置,装入量应不小于80件废料。
废料盒要取放方便。
(7)拉延模和整形模要设置到底标记,左右合模件设置左右标记L、R;标记安装在模具上模上。
(8)起吊装置采用(汽车冲模标准汇编)QM标准,便于模具的起吊、翻转;设置上、下连接板。
(9)模具结构设计要便于工人操作,保证操作者人身、设备及模具安全。
(10)以上所述内容及其它未说明内容参阅(汽车冲模标准汇编)、(中国机械工业标准模具篇)。
2. 模具工作部位材料(1)拉延模:凸、凹模及压边圈采用Cr12MoV,整体淬火,其硬度不低于HRC55。
(2)修边冲孔落料模:a.修边刃口采用T10A,整体淬火,其硬度为HRC60±2;b.冲头采用Cr12MoV,球锁式快换冲头,对于特殊结构由会签时确定。
c.凹模套采用Cr12MoV甲方认可的标准凹模套(保证同轴度且具有互换性)凹模套的防转方法采用甲方认可的Φ4mm的防转销。
(3)弯曲成形模:凸凹模采用Cr12MoV。
冲压工艺技术要求

冲压工艺技术要求一、冲压工艺参数控制:1.上冲臂和下冲臂的长度应适当,以保证冲裁件在冲裁过程中的稳定性。
2.冲裁速度应适当,既要保证冲裁质量和工艺要求,又要考虑生产效率。
3.冲裁时的液压系统应保持稳定,并且能够方便地进行调整。
二、模具设计与制造:1.冲压模具应具备足够的强度和刚度,能够承受冲压过程中产生的冲击负荷,并保持高精度。
2.冲压模具的导向系统应设置合理,以确保冲裁件的准确位置和尺寸。
3.冲压模具应具备良好的冷却系统,以防止模具过热。
三、冲压材料选择:1.冲压材料应具备良好的塑性变形能力和可靠的强度。
2.冲压材料应有足够的导热性,以便迅速排出冲裁过程中产生的热量。
四、冲压质量控制:1.冲裁件的尺寸公差应在允许范围内,并且保证其功能和装配的要求。
2.冲裁件的表面质量应达到要求,不得有明显的划痕、氧化等缺陷。
3.冲裁件的强度和硬度应符合设计要求,并通过必要的检验手段进行检测。
五、冲压设备维护与保养:1.冲压设备的润滑系统应良好运行,以保证设备的正常运转和寿命。
2.冲压设备的气动系统应经常检查,以确保气动元件的正常工作。
3.冲压设备的电气系统应保持良好的绝缘,以避免电气故障。
六、人员技术要求:1.冲压工艺技术人员应具备良好的技术素养和操作技能,能够准确理解和执行工艺要求。
2.冲压工艺技术人员应经常进行培训和学习,掌握新的冲压技术和设备。
总之,冲压工艺技术要求的目的是为了保证冲压件的质量、尺寸和功能要求,并提高生产效率和设备寿命。
只有按照冲压工艺技术要求进行操作和管理,才能保证冲压加工的顺利进行。
冲压模具制造检验技术要求
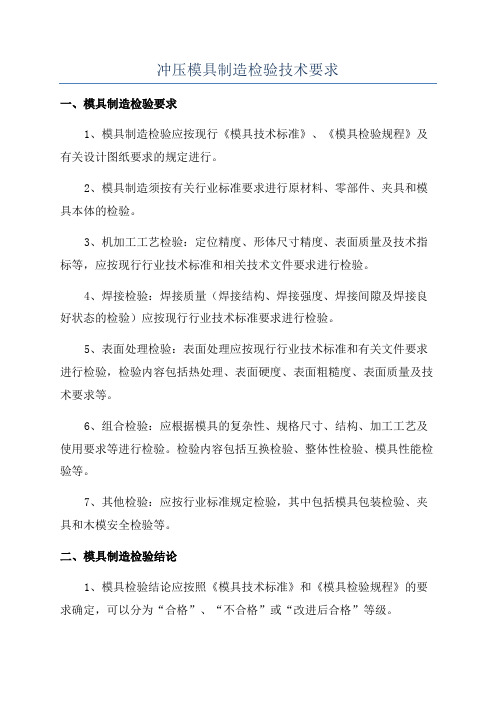
冲压模具制造检验技术要求
一、模具制造检验要求
1、模具制造检验应按现行《模具技术标准》、《模具检验规程》及有关设计图纸要求的规定进行。
2、模具制造须按有关行业标准要求进行原材料、零部件、夹具和模具本体的检验。
3、机加工工艺检验:定位精度、形体尺寸精度、表面质量及技术指标等,应按现行行业技术标准和相关技术文件要求进行检验。
4、焊接检验:焊接质量(焊接结构、焊接强度、焊接间隙及焊接良好状态的检验)应按现行行业技术标准要求进行检验。
5、表面处理检验:表面处理应按现行行业技术标准和有关文件要求进行检验,检验内容包括热处理、表面硬度、表面粗糙度、表面质量及技术要求等。
6、组合检验:应根据模具的复杂性、规格尺寸、结构、加工工艺及使用要求等进行检验。
检验内容包括互换检验、整体性检验、模具性能检验等。
7、其他检验:应按行业标准规定检验,其中包括模具包装检验、夹具和木模安全检验等。
二、模具制造检验结论
1、模具检验结论应按照《模具技术标准》和《模具检验规程》的要求确定,可以分为“合格”、“不合格”或“改进后合格”等级。
冲压模具设计规范
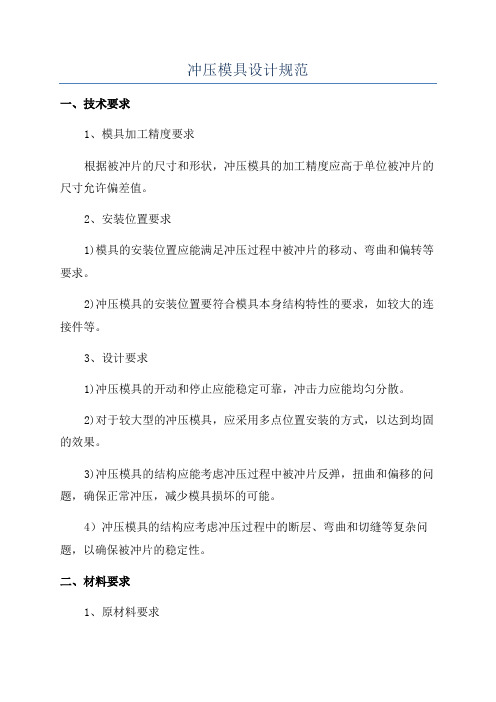
冲压模具设计规范
一、技术要求
1、模具加工精度要求
根据被冲片的尺寸和形状,冲压模具的加工精度应高于单位被冲片的尺寸允许偏差值。
2、安装位置要求
1)模具的安装位置应能满足冲压过程中被冲片的移动、弯曲和偏转等要求。
2)冲压模具的安装位置要符合模具本身结构特性的要求,如较大的连接件等。
3、设计要求
1)冲压模具的开动和停止应能稳定可靠,冲击力应能均匀分散。
2)对于较大型的冲压模具,应采用多点位置安装的方式,以达到均固的效果。
3)冲压模具的结构应能考虑冲压过程中被冲片反弹,扭曲和偏移的问题,确保正常冲压,减少模具损坏的可能。
4)冲压模具的结构应考虑冲压过程中的断层、弯曲和切缝等复杂问题,以确保被冲片的稳定性。
二、材料要求
1、原材料要求
1)冲压模具原材料应根据被冲片的材料特性、冲压工艺及模具的使用
寿命等因素确定,一般采用合金钢等。
2)冲压模具的原材料应考虑冲压过程中对其断裂、变形、冲击力以及
模具热处理等要求。
3)冲压模具的原材料质量应符合国家标准要求,保证模具的正常使用。
2、表面处理要求
冲压模具的表面处理要根据不同应用环境确定。
冲压模具技术经验要求
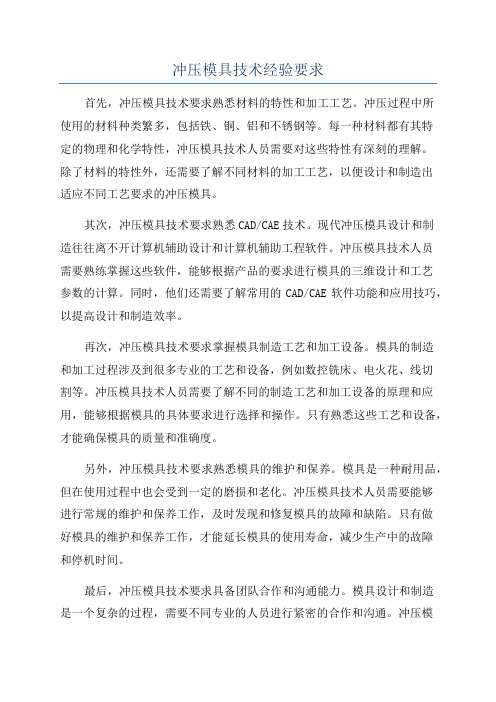
冲压模具技术经验要求首先,冲压模具技术要求熟悉材料的特性和加工工艺。
冲压过程中所使用的材料种类繁多,包括铁、铜、铝和不锈钢等。
每一种材料都有其特定的物理和化学特性,冲压模具技术人员需要对这些特性有深刻的理解。
除了材料的特性外,还需要了解不同材料的加工工艺,以便设计和制造出适应不同工艺要求的冲压模具。
其次,冲压模具技术要求熟悉CAD/CAE技术。
现代冲压模具设计和制造往往离不开计算机辅助设计和计算机辅助工程软件。
冲压模具技术人员需要熟练掌握这些软件,能够根据产品的要求进行模具的三维设计和工艺参数的计算。
同时,他们还需要了解常用的CAD/CAE软件功能和应用技巧,以提高设计和制造效率。
再次,冲压模具技术要求掌握模具制造工艺和加工设备。
模具的制造和加工过程涉及到很多专业的工艺和设备,例如数控铣床、电火花、线切割等。
冲压模具技术人员需要了解不同的制造工艺和加工设备的原理和应用,能够根据模具的具体要求进行选择和操作。
只有熟悉这些工艺和设备,才能确保模具的质量和准确度。
另外,冲压模具技术要求熟悉模具的维护和保养。
模具是一种耐用品,但在使用过程中也会受到一定的磨损和老化。
冲压模具技术人员需要能够进行常规的维护和保养工作,及时发现和修复模具的故障和缺陷。
只有做好模具的维护和保养工作,才能延长模具的使用寿命,减少生产中的故障和停机时间。
最后,冲压模具技术要求具备团队合作和沟通能力。
模具设计和制造是一个复杂的过程,需要不同专业的人员进行紧密的合作和沟通。
冲压模具技术人员需要能够与其他工程师、技术人员和操作人员进行有效的沟通,理解他们的需求和要求,并及时解决技术上的问题和困难。
只有团队合作和良好的沟通,才能保证模具设计和制造的顺利进行。
综上所述,冲压模具技术要求经验非常丰富。
冲压模具技术人员需要具备熟悉材料特性和加工工艺、掌握CAD/CAE技术、熟悉模具制造工艺和加工设备、了解模具的维护和保养,以及具备团队合作和沟通能力等多方面的知识和技能。
- 1、下载文档前请自行甄别文档内容的完整性,平台不提供额外的编辑、内容补充、找答案等附加服务。
- 2、"仅部分预览"的文档,不可在线预览部分如存在完整性等问题,可反馈申请退款(可完整预览的文档不适用该条件!)。
- 3、如文档侵犯您的权益,请联系客服反馈,我们会尽快为您处理(人工客服工作时间:9:00-18:30)。
冲压模具制作技术要求 This manuscript was revised by the office on December 10, 2020.附件二:冲压模具制作技术要求1、基本要求1.1、基准体系:采用GD&T图规定的定位基准。
模具以设计基准点为主基准,保证设计、制造、检测基准三者相统一。
1.2、所有工艺方案图、模具图可采用2D或3D进行设计,文件类型为*.dwg或*.prt、*.CATPart格式;1.3、视图投影法:优先采用第一角法;1.4、图幅要求:最大采用A0号图纸(图幅可加长);1.5、图型比例:1:1、1:2、1:3、1:4;1.6、图面文字:中文;1.7、尺寸表示:公制;1.8、标题栏和明细表:投标方的标准;1.9、上模画法和方向:翻转向右;1.10、对镶拼结构的镶块资料应单独出图,并标识清楚;2、工艺方案图及模具结构图2.1、工艺方案图2.1.1 能充分反映冲压零件各工序的工作内容、冲压方向、送料方向,以及各工序所使用压机的规格等;2.1.2 标示出各工序冲压方向、模具基准点、零件车身坐标值。
当冲压方向相对零件车身坐标发生旋转时,应注明清楚;2.1.3 各工序零件送出料方向及拉延工序补充部份的详细结构;2.1.4 拉延(整形)工序CH孔、到位标记位置;2.1.5 零件板材毛坯尺寸标注,中间工序的切边线;2.1.6 废料切刀的布置位置及切边、冲孔废料的排除方式;2.1.7 斜楔加工方向、加工范围;2.1.8 顶杆布置图、废料流向示意及方案图中各种符号说明。
2.1.9 标明零件材料利用率。
2.2、模具结构图2.2.1 模具图应充分表达模具的工作状态,反映零件的送出料方向、所用的压机型号、顶杆位置与顶杆行程等。
2.2.2 模具图应准确注明模具中心、机床中心。
模具中心应加注车身坐标系坐标值。
2.2.3 每工序模具图应有工序内容简图。
2.2.4 模具结构中含弹簧/氮气缸的应有弹力工作示意图。
2.2.5 模具使用斜楔机构的应做出斜楔行程图及斜楔断面图。
2.2.6 模具如果配备气缸顶出机构,模具图中应附加气路图。
2.2.7 工艺方案图、模具图及数模文件的命名规则如下:×××(项目代号) -×××(零件代号) -×××(零件版本) – OPx/y(x表示10、20…;y表示总工序数,如共五序则为50)。
3、工艺数模3.1、依据冲压零件3D数模,按冲压工艺方案图建立各工序的工艺数模,工艺数模中须完整表示出各工序线(如分模线、切边线、翻边线等),产品面与工艺补充面要用颜色或图层加以区分。
3.2、产品3D数据以CATIA V5 R18版本格式提供。
投标方工艺数模提供的3D 数据格式为*.CATPart、*.prt或IGES。
3.3、所有零件在建模中的坐标要与工艺方案一致。
3.4、拉延成形零件须用Autoform或Dynaform分析软件对其进行CAE成形分析。
复杂零件应对后工序进行回弹方面的仿真分析。
对于外板零件要有合适的变形量(大于3%),CAE成形分析的最终结果由招标方确认。
4、模具结构通用要求4.1、冲压模具必须按照招标方冲压生产线设备参数进行设计和制造。
对于自动化生产线能实现自动夹紧、板料及零件的自动传输、零件连动生产等全自动生产过程;手工生产线,要保证取送件容易,操作安全方便。
4.2、在正常使用状态下,按5000件冲次为期限定期维护为前提。
模具按30万件进行设计、制造。
4.3、模具高度模具闭高尽量相同。
4.4、自动化生产用的传感器和气缸式顶升装置的气源接头规格要与压机相匹配。
4.5、模具的压力中心应与压机中心一致。
4.6、模具上应有模具代号文字标识符,送料方向及模具前后方向标识符,拉延模须有顶杆布置标牌。
4.7、铸造模具表面不允许有铸造缺陷,如无砂眼、疏松、缩孔、气泡、夹渣等。
交验的模具表面应清洁,无切削、焊渣、尘砂、油污、锈蚀、杂物等。
4.8、模具须合理设计排水孔,在选择电器元件及设计排水孔时要满足模具清洗的需要。
14.9、拉延模型面贴合率要求:外板≥90%、内板≥80%。
4.10、模具需要考虑噪音问题,对于厚板料需采用阶梯式凸模及波浪形刃口等方式。
4.11、零件、废料退出凸、凹模无任何滞阻和粘附现象。
手工生产线模具要求设计安装上下料架。
4.12、起重装置4.12.1 铸造模具采用铸入式起重臂或插销式吊耳,插销式超重吊耳应配有自锁功能起重棒。
4.12.2 凡冲模零件超过15Kg或取放不方便的冲模零件,均设置起重螺孔或起重孔。
4.12.3 模具重心和多副模具组合在模板上的组合重心与模具的几何中心应尽量重合。
4.13、安全装置4.13.1 冲压模具需加装自由状态下的存放限位装置,要设有安全平台,安全平台尺寸150mm×150mm,考虑防反措施。
4.13.2 上模压料器应有安全侧销或安全螺钉,上模销钉应有防落措施。
4.13.3 上下模相对活动部份及外露的活动部件须设有防护装置。
4.13.4 模具须加装运输时用的连接板。
4.13.5 不易区分的左右零件上应有“L”、“R”标记区分。
4.14、导向装置4.14.1 模具导向型式:带冲裁的拉延模:采用导板+导柱复合导向方式;冲裁类模具须有导柱导向,如有侧向力应采用导板+导柱复合导向方式;整形类模具采用导板导向形式。
有侧向力的需设计反侧机构;退料(压料)板采用导板或导柱导向。
4.14.2 模具的导柱、导套要求采用植入式带锁紧结构,导套选用自润滑式。
4.14.3 模具存放时,上下导向部分接触面不小于导向面的1/3。
4.14、模具的定位及U型槽结构、位置尺寸应与压机相匹配。
4.15、拉延模工作部分采用MoCr铸铁或球铁,硬度HRC50以上。
厚板(t≥1.2)零件,高强度板(σs≥210)零件工作部分(压边圈压料面和上模压料面) 采用Cr12MoV材料拼镶结构。
拉延深度超过180mm零件,零件工作部分须进行TD处理。
基座用HT300。
4.16、切边模、翻边模料厚t<1.2mm的零件,镶块材料为ICD5或7CrSiMnMoV,硬度HRC 50-55;厚板(t≥1.2)零件,高强度板(σs≥210)零件,镶块材料为SKDⅡ或Cr12MoV,硬度HRC 58-62。
上下模座采用FC300或HT300。
4.17、模具标准件须得到招标方的确认。
4.18、模具外观及标志4.18.1 模具本体及部件涂色标准由招标方提供。
4.18.2 使用气垫的模具,按招标方要求安装顶杆布置铭牌。
4.18.3 对于拆卸件、镶块,须刻印出安装位置的对应标记(字母或数字),模具各部分(包括镶块)均要用标准字头刻、铸出材质牌号。
4.18.4 铸造模具的铸字内容包括项目代号、零件名称、零件代号、工序号、工序内容、模具重量(上下模重量及总重量)等,具体由招标方确认。
5、拉延模5.1 平衡垫块:保证所有平衡垫块均能与上模接触。
5.2 排气管采用铜弯管,排气孔位置应合理设置,不得影响制件表面质量,外板件上模应考虑防尘措施。
5.3 压边圈应使用标准安全螺栓。
5.4 为便于人工取件,可在压边圈上四角加弹顶销,但不得影响制件的成形。
5.5顶杆行程:要小于机床气垫最大行程50mm。
5.6 采用到位标识,标记深度为0.3mm以内,尽可能设置在废料上。
5.7 限位装置:采用限位安全档块或带套管式标准限位螺钉。
5.8 定位装置:制件在模具上采用可调式边定位块定位。
6、切边冲孔模6.1 冲裁部分结构:6.1.1 上、下模刃口为镶块结构,具有防侧向力功能,并便于更换与维修。
6.1.2 冲孔采用镶块时应考虑维修更换方便,原则上刃口处为镶块结构,易磨损部位及立切部位采用易换的小镶块结构。
6.1.3 废料刀应具有防侧向力功能,依托本体作靠背。
6.2 废料排出6.2.1 废料刀的布置,根据工序安排适当处理,废料的最大对角线长度不允许超过600mm,要求手工线废料滑出模具区,自动化线废料要滑出机床。
6.2.2 废料滑板超出冲模底板以外时采用可叠式。
废料滑板采用厚度为2.0mm以上的钢板制作,两侧要求有翻边。
废料滑槽一级滑槽的角度不小于25度。
6.2.3 直径小于20mm或最大对角线小于20mm的废料不能滑出工作台前后时,可采用废料盒盛装,且废料盒容量不少于1000冲次,1000次冲压后废料的重量(带废料盒)应在15kg以下,保证操作的方便。
6.2.4 自动化生产线上生产的模具尽量少使用废料盒。
废料盒要求抽取方便,且能够自锁。
6.2.5 废料滑出工作台时,滑槽应有收口,让开操作空间,应满足废料滑出安全可靠,不飞溅,不妨碍冲压操作。
6.2.6 废料滑道终端宽度会签图纸时确认。
6.2.7 可以利用的冲压边料,在模具结构上采用从侧面取出的方式。
6.3 凸模:6.3.1 有形状的凸模或镶块应有防转的锁紧装置。
6.3.2 薄板件侧冲孔应选用顶料型凸模。
6.3.3 尽量采用长度为80mm的凸模。
6.3.4 对特殊结构会签时确定。
6.4 凹模:6.4.1 凹模套须选用带止转销形式。
6.4.2 凹模选用可换式的标准件(工作边距、孔距较小者除外)。
6.5 废料刀:6.5.1 废料刀与凹模刃口随形。
6.5.2 废料刀要有足够的刃口长度和强度,材质与上下切刀相同。
废料刀的布置要便于废料流出。
6.6 镶块:6.6.1 切边凹模刃口采用镶块结构,凸模刃口采用镶块式或整体结构,直线段的镶块长度不大于500mm,形状复杂部位的拼块长度图纸会签时确定。
6.6.2 在镶块受侧向力的方向设置挡墙或挡键。
6.7 对于侧围门框、行李箱边框装胶条的部位,尽量采取整形后修边的方式,确保修边线的精度。
7、翻边整形模7.1 凸模及压料板原则上采用整体结构,形状复杂受力较大易磨损处,应采用镶块结构。
7.2 整形处受力较大易磨损部位的压料板,应采用镶块结构。
7.3 要保证冲压零件脱模顺畅,脱模困难处应设置刮料或顶出装置。
7.4 所有的翻边镶块均应设有挡块或背托,不能仅用销钉。
7.5 易损部件要拆卸方便。
7.6 整形模具必须设置到位标记。
8、斜楔模8.1 非标斜楔应设计强制回位机构。
8.2 非标斜楔回位,弹簧力应充分,设计时根据实际情况决定是否采用氮气弹簧。
8.3 斜楔导向部位应采用自润滑结构。
8.4 斜楔驱动器的位置不得影响制件的进出。
8.5 斜楔机构优先采用标准件。
8.6 斜楔尽可能设置在模具两侧非操作区,确因冲压工艺和模具结构需要设置在操作区时,采用吊楔结构。
8.7 斜楔机构的驱动块和滑块的初始接触面积不小于整个斜面的1/3。
8.8 斜楔必须设置有防脱落的安全装置。