采场顶板控制及其检测技术标准版本
采场顶板控制及其检测技术
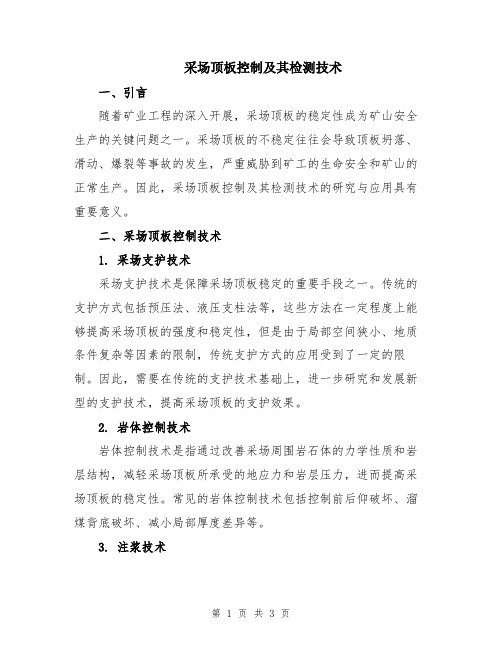
采场顶板控制及其检测技术一、引言随着矿业工程的深入开展,采场顶板的稳定性成为矿山安全生产的关键问题之一。
采场顶板的不稳定往往会导致顶板坍落、滑动、爆裂等事故的发生,严重威胁到矿工的生命安全和矿山的正常生产。
因此,采场顶板控制及其检测技术的研究与应用具有重要意义。
二、采场顶板控制技术1. 采场支护技术采场支护技术是保障采场顶板稳定的重要手段之一。
传统的支护方式包括预压法、液压支柱法等,这些方法在一定程度上能够提高采场顶板的强度和稳定性,但是由于局部空间狭小、地质条件复杂等因素的限制,传统支护方式的应用受到了一定的限制。
因此,需要在传统的支护技术基础上,进一步研究和发展新型的支护技术,提高采场顶板的支护效果。
2. 岩体控制技术岩体控制技术是指通过改善采场周围岩石体的力学性质和岩层结构,减轻采场顶板所承受的地应力和岩层压力,进而提高采场顶板的稳定性。
常见的岩体控制技术包括控制前后仰破坏、溜煤背底破坏、减小局部厚度差异等。
3. 注浆技术注浆技术是指通过将固体颗粒或液体材料注入到岩体中,提高岩体的强度和稳定性,从而减轻采场顶板的应力并防止岩体的侧向运动。
常用的注浆材料有水泥浆、乳化液、填充土等。
三、采场顶板检测技术采场顶板的稳定性往往要通过对其进行实时监测来进行评估。
传统的采场顶板检测技术主要包括倒垮煤柱法、岩体温度测量法、地缝测量法等,这些方法存在检测周期长、准确度低等问题。
近年来,随着科学技术的发展,新型的采场顶板检测技术不断涌现。
1. 声波检测技术声波检测技术是指通过对采场顶板产生的声波信号进行分析和处理,来判断采场顶板的稳定性。
声波检测技术具有非接触、实时、准确度高的特点,能够快速检测采场顶板的状况,提供及时的预警信息,从而保障矿山的安全生产。
2. 摄像监测技术摄像监测技术是指通过摄像设备对采场顶板进行实时监测,获取顶板的图像信息,并进行图像处理和分析,判断采场顶板的稳定性。
该技术具有全天候、非接触等特点,能够高效地监测采场顶板的变形和位移,为采场顶板的安全控制提供重要数据支持。
采面支护质量与顶板监测制度范本
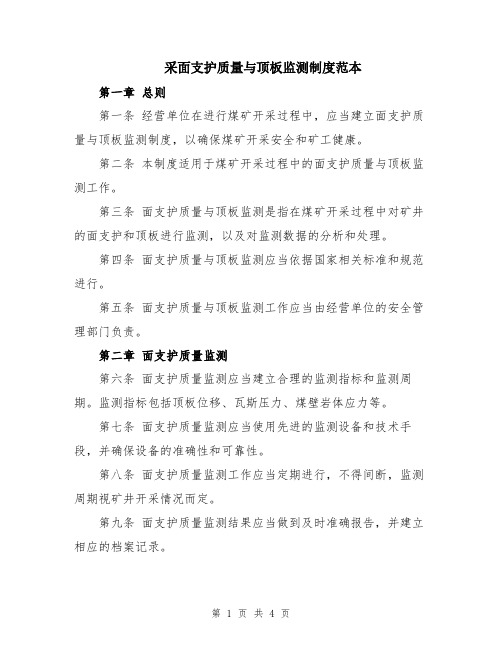
采面支护质量与顶板监测制度范本第一章总则第一条经营单位在进行煤矿开采过程中,应当建立面支护质量与顶板监测制度,以确保煤矿开采安全和矿工健康。
第二条本制度适用于煤矿开采过程中的面支护质量与顶板监测工作。
第三条面支护质量与顶板监测是指在煤矿开采过程中对矿井的面支护和顶板进行监测,以及对监测数据的分析和处理。
第四条面支护质量与顶板监测应当依据国家相关标准和规范进行。
第五条面支护质量与顶板监测工作应当由经营单位的安全管理部门负责。
第二章面支护质量监测第六条面支护质量监测应当建立合理的监测指标和监测周期。
监测指标包括顶板位移、瓦斯压力、煤壁岩体应力等。
第七条面支护质量监测应当使用先进的监测设备和技术手段,并确保设备的准确性和可靠性。
第八条面支护质量监测工作应当定期进行,不得间断,监测周期视矿井开采情况而定。
第九条面支护质量监测结果应当做到及时准确报告,并建立相应的档案记录。
第十条面支护质量监测结果应当及时进行分析和处理,对不合格的支护措施应当立即采取补救措施。
第十一条面支护质量监测结果应当定期评估,对评估结果进行总结和分析,提出改进意见和措施。
第十二条经营单位应当配备专业技术人员进行面支护质量监测工作,并定期进行培训。
第三章顶板监测第十三条顶板监测应当包括顶板位移、顶板压力、顶板裂缝等方面的监测。
第十四条顶板监测工作应当使用合适的监测设备,确保监测数据的准确性和可靠性。
第十五条顶板监测工作应当进行定期检查和维护,确保设备正常运行。
第十六条顶板监测结果应当及时报告,并建立相应的档案记录。
第十七条顶板监测结果应当进行分析和处理,对不安全的顶板区域应当采取相应的措施进行加固和处理。
第十八条经营单位应当配备专业技术人员进行顶板监测工作,并定期进行培训。
第四章法律责任第十九条对于违反本制度的行为,经营单位应当根据相关法律法规进行处罚。
第二十条发生煤矿事故,如果监测工作不到位或者监测结果没有及时报告,经营单位应当承担相应的法律责任。
采场顶板控制及其检测技术

采场顶板控制及其检测技术采煤行业是我国经济和能源发展的重要支柱产业,如何保障煤炭采掘作业的安全高效进行是一个重大问题。
顶板事故是煤矿生产中的一大难题,为此,我们需要实现对煤矿顶板的控制和检测,以保障采煤作业的顺利进行。
一、采场顶板的控制技术1. 顶板预支护技术顶板预支护技术是目前采场顶板控制的重要手段之一,它能够有效防止顶板垮落事故的发生。
该技术所采用的预支护结构包括了半拱形钢支架、约束钢管和支撑预应力锚杆,通过这些支撑结构与原有支架和网架相结合,形成支撑系统,从而保证顶板的安全。
2. 顶板水平预紧技术顶板水平预紧技术是一种较新的顶板控制技术。
通过调整顶板下倾造成的顶板轴向主应力,减小顶板的挤压变形,从而达到控制顶板移动和防止顶板离层的目的。
该技术具有结构简单、操作便利、效果显著等优点。
3. 顶板注浆技术顶板注浆技术是将高压注浆机注入混合材料,通过填充隙缝的方式,增强顶板的强度和稳定性。
该技术适用于顶板厚,散状岩层面积大,顶板条件无法通过其他方式得到保护的情况。
二、采场顶板的检测技术1. 顶板颤动监测技术顶板颤动监测技术可以从顶板的自由振动情况中,了解到顶板的应变和变形情况,从而预测顶板破坏的概率以及获取到煤巷的安全度量。
该技术可通过振动传感器、数据采集设备、数据分析软件等设备完成。
2. 顶板位移监测技术顶板位移监测技术是一种通过测量顶板位移来判断顶板稳定性的技术。
该技术可以通过激光位移监测系统、电子测距系统等设备来完成测量,同时还可以通过数据分析软件来分析和处理数据,得到相关的结论。
3. 顶板应变分析技术顶板应变分析技术是一种通过分析顶板的应变情况,来判断顶板稳定性的技术。
该技术可通过应变传感器和数据采集设备等设备完成,同时可以通过数据分析软件来分析和处理数据,达到预测顶板稳定性的目的。
三、采场顶板控制和检测技术的应用采场顶板控制和检测技术,是随着我国煤炭工业的不断发展而不断完善和提高的。
它的应用范围很广,除了可以应用于顶板控制和安全检测外,还可以应用于煤矿巷道和井下隧道的控制和检测、地铁隧道的施工和检测以及天然气储藏库等工程的安全控制等领域。
顶板控制及监测

2.综采压垮型冒顶的控制措施
支架的可缩量应适应垮落带老顶的下沉。 最大控顶距时,顶梁末端顶板最大下沉量计算图。
2.综采压垮型冒顶的控制措施
2.综采压垮型冒顶的控制措施
采场最大控顶距处的最大下沉量
—最大控顶距(煤壁至液压支架后端的距离);
01
—老顶周期来压步距,一般按实际或10m;
02
H —裂隙带老顶断块触矸处的下沉量。
03
2.综采压垮型冒顶的控制措施
对厚层难冒顶板,采用钻爆或注水法,松动碎裂2~3倍采高岩层(直接顶+老顶)。一般应提前进行碎裂。 当厚层难冒顶板不大时,只处理下部部分厚度,余下部分转变为裂隙带岩层。 将处理部分顶板岩层视为垮落带岩层。
3.综采推垮型冒顶的控制措施
上下位岩层间的摩擦阻力防推。
切断直接顶的厚度不超过2.5~3.0m。 无直接顶,切断老顶厚度不超过2.0~2.5m。 单体面,若需要切断下位老顶,则需要切顶墩柱。初撑力计算方法同前。但需要:一是调整有关岩重的计算,二是老顶的极限悬顶应采用实际数据。 参考数据:1.5m厚的老顶,悬3.0m。2.0m厚的老顶,悬5.0m。2.5m厚的老顶,悬7.0m。 所需初撑力是墩柱间距与单位密集柱初撑力的乘积。
控顶原则之二:预防漏冒型冒顶
综采时,如果直接顶比较软弱,液压支架应在掩护式或支撑掩护式中选用,且端面距不宜超过340mm。
1
单体支柱工作面,如果直接顶比较软弱,支柱必须带顶梁,顶梁上还须背板,甚至背严。柱距小于0.7m,同时端面距小于200mm 。
2
综采支架的初撑力应保证端面冒高不超过300mm;单体支柱的初撑力应保证端面冒高不超过200mm。
已知量:顶梁长度与排距,与采煤进度与采煤机截深一并考虑。控顶距与放顶距。
第二篇:采场顶板控制及监测03

第二节 采场支护参数
一、单体支柱工作面的支护参数
采场中用支护强度(支架对单位面积顶板提 供的工作阻力,KN/m2)平衡顶板压力。顶板压 力的大小是通过支护强度的大小来表示的。 为保证采面正常生产,支架必须有一定的支 护强度。与支护强度有关的支护参数单体支柱面 与综采面不同。 ① 支护参数:支柱初撑力、支柱密度、支护 系统刚度(单位顶板下沉量的工作阻力增量)。 ② 关系:初撑力越大,支柱密度越大,支护 系统刚度越大,采场支护强度就越大。 ③ 顶板压力是可变的。
2、按裂隙带老顶的下沉量估算
采场最大控顶距处的最大下沉量
HL'D h Llz
L —最大控顶距(煤壁至密集、墩柱、或末排
柱的距离) Llz —老顶周期来压步距。 H —裂隙带老顶断块触矸处的下沉量。 生产实践表明,控顶范围内,顶底板移近 量每米采高不超过100mm时,顶板状态是好 的,也容易控制。
1)在各测线量测第一排和末前排支柱初撑力、 工作阻力、采高及活柱高度。 ① 若初撑力不够,须在测线上下5m范围内棵 棵检测并补液整改,使其达到要求。 ② 对测线上下的密集各抽查一棵,若不够,须 棵棵检测并补液整改,使其达到要求。 2)钻底量,只对末前排在平时和来压期间各统 计观测一次。底板变化时再次测量。 3)对两端四对八梁,只抽查一对前梁三棵柱的 初撑力。 4)对特殊地点,初撑力棵棵监测。并记录该地 点长度、支柱数量,初撑力不合格等情况, 对断层产状要量测记录。
③个别底板特软情况下,用降低初撑力加大支柱密 度以保证支柱不钻底。
二、综采工作面的支护参数
1、与支护强度有关的只有初撑力。因支 架密度一定,支护系统刚度也不能调整。 2、软底时,应选择底座大的液压支架, 保证支架的钻底量不超过一定值。 3、提高支护强度,就只能提高支架的初 撑力。 4、液压支架的额定初撑力与额定工作阻 力的比值比单体支柱的大。
采面支护质量与顶板监测制度(通用版)

( 安全管理 )单位:_________________________姓名:_________________________日期:_________________________精品文档 / Word文档 / 文字可改采面支护质量与顶板监测制度(通用版)Safety management is an important part of production management. Safety and production are inthe implementation process采面支护质量与顶板监测制度(通用版)一、采工作面支护质量与顶板监测主要内容、指标、测站布置、方法1、采工作面日常支护质量与顶板动态监测主要内容和基本要求:液压支柱支撑有力与铰链梁能够有效控制围岩,减少冒顶事故,提高工作面支撑功效,保证安全生产。
2、主要监测指标分为支护监测指标、围岩状态指标和两巷超前支护质量指标。
(1)支护质量监测指标:①关键指标:1、初撑力2、端面距②辅助指标:1、支柱工作阻力2、液压支柱与铰链梁工作空间几何状态。
3、液压系统工况(泵站压力、液压管路和密封件完好状况)4、采高。
(2)采工作面围岩状态指标:端面顶板冒高、冒宽、冒区长度,煤壁片帮深度,片帮区长度。
(3)两巷超前支护质量指标:煤壁超前20m范围内支护完整,巷高不小于1.6m,有0.8m行人通道。
按照作业规程规定加强端头及超前支护。
3、采面矿压及支护质量观测测站布置:每隔20液压支柱安1台矿压观测表。
4、采工作面日常矿压观测方法:(1)支架阻力观测:直接读取压力表读数。
(2)顶板动态观测:在各测线处对顶板状态作统计观测,记录采高、初撑力、二次补液状况等。
(3)支柱几何参数观测:采用目测普查,超标明显处用工具进行测记,包括顶梁走向角及倾角、顶梁错差。
(4)两巷超前支护质量监测测量单体液压支柱的初撑力或工作阻力。
二、采煤工作面支护质量与顶板动态监测数据收集、分析、处理制度1、采煤队负责进行现场支护质量与动态监测数据收集工作,每天监测一次。
采场顶板控制及其检测技术模版

采场顶板控制及其检测技术模版一、引言采场顶板控制及其检测技术在矿井安全生产中起着重要的作用。
随着矿业的发展,采场顶板的稳定性成为矿井安全生产的关键问题之一。
为了确保工人的安全以及矿井设备的正常运行,必须对采场顶板进行有效的控制和检测。
本文将介绍一种采场顶板控制及其检测技术模版,旨在提供一种系统化、科学化的方法来确保采场顶板的稳定性。
二、采场顶板控制技术1.适用范围采场顶板控制技术适用于煤矿、金属矿山、隧道工程等采掘作业中的顶板控制。
通过对采场顶板的稳定性进行分析和评估,确定合适的控制措施,并采取相应的措施来保证采场顶板的稳定性。
2.控制措施在采场顶板控制中,可以采取以下措施来确保顶板的稳定性:(1)支护措施:采用木栓、钢撑、锚杆、预应力锚杆等支护方式,增强采场顶板的强度和稳定性。
(2)顶板压力分散:通过设置合理的水平支护和维护顶板的平整度,使采场顶板的压力能够均匀分散,减少局部聚集的压力。
(3)控制采场进度:根据采场的稳定状况,在适当的时机停止或调整采掘活动,避免过度开采导致顶板失稳。
(4)定期检测和维护:建立定期检测制度,对采场顶板进行维护和修复,确保采场顶板的稳定性。
三、采场顶板检测技术1.适用范围采场顶板检测技术适用于对采场顶板进行定期检测和评估。
通过对采场顶板的变形情况、应力分布、岩层结构等进行分析,可以判断顶板的稳定性,并及时采取相应的措施进行修复和加固。
2.检测方法(1)应力测量:通过安装应力传感器或应变计等测量设备,实时监测采场顶板的应力情况,并进行数据分析。
(2)位移监测:通过安装位移传感器或测量仪器,测量采场顶板的变形情况,判断顶板的稳定性。
(3)地形测量:利用激光测距仪等测量设备,对采场顶板的地形进行测量,了解顶板的平整度和变形情况。
(4)岩层结构分析:通过岩心分析、钻孔测试等方法,对采场顶板所在的岩层结构进行分析,评估顶板的稳定性。
四、技术模版应用案例以某煤矿采场顶板控制及其检测技术模版为例,介绍其应用情况。
采场顶板控制及其检测技术

根据采场地质条件和开采技术,选择合适的支护方式,确保顶板稳 定。
加强顶板监测
采用先进的监测技术,实时监测顶板变形、下沉等情况,及时预警并 采取相应措施。
事故应急处理方案
立即撤人
发生顶板事故时,立即停止作 业,迅速撤离危险区域。
启动应急预案
根据事故情况启动相应的应急 预案,组织救援力量进行抢险 救援。
检测技术发展
近年来,随着科技的进步,采场顶板检测技术得到了显著的发展。从传统的观测方法到现代的智能化监测技术,检测 精度和效率都得到了大幅提升。
控制策略优化
基于现场实践和理论研究,采场顶板的控制策略不断优化。通过引入先进的支护技术和管理方法,顶板 稳定性得到了显著提高。
未来研究方向展望
智能化监测技术
评价方法选择
综合指数法
将各评价指标进行无量纲化处理 ,通过加权平均等方法计算综合 指数,对采场顶板控制效果进行 评价。
模糊综合评价法
运用模糊数学理论,将评价指标 进行模糊化处理,通过建立隶属 度函数和模糊关系矩阵,对采场 顶板控制效果进行综合评价。
神经网络评价法
利用神经网络模型对评价指标进 行学习训练,通过模型的输出结 果对采场顶板控制效果进行评价 。
生影响。例如,不合理的开采顺序和过大的开采高度都可能导致顶板的
失稳。
02
采场顶板控制技术
支护技术
锚杆支护
通过锚杆将不稳定岩层与 稳定岩层连接,形成整体 支护结构,提高顶板的稳 定性。
支架支护
采用液压支架、单体支柱 等支护设备,支撑采场顶 板,防止冒顶事故发生。
注浆加固
向破碎或松散的岩体中注 入水泥浆等胶结材料,提 高岩体的整体性和稳定性 。
- 1、下载文档前请自行甄别文档内容的完整性,平台不提供额外的编辑、内容补充、找答案等附加服务。
- 2、"仅部分预览"的文档,不可在线预览部分如存在完整性等问题,可反馈申请退款(可完整预览的文档不适用该条件!)。
- 3、如文档侵犯您的权益,请联系客服反馈,我们会尽快为您处理(人工客服工作时间:9:00-18:30)。
文件编号:RHD-QB-K1053 (解决方案范本系列)编辑:XXXXXX查核:XXXXXX时间:XXXXXX采场顶板控制及其检测技术标准版本采场顶板控制及其检测技术标准版本操作指导:该解决方案文件为日常单位或公司为保证的工作、生产能够安全稳定地有效运转而制定的,并由相关人员在办理业务或操作时进行更好的判断与管理。
,其中条款可根据自己现实基础上调整,请仔细浏览后进行编辑与保存。
岩层:由同一岩性组成的基本均一的受两个平行或近于平行界面所限制的层状岩石。
分层:分层是指同一岩性的整体岩层或同一岩性较厚岩层中的一部分或由下“硬”上“软”不同岩性组成的岩层组。
老顶:厚度大于1.5m~2m、较坚硬的岩层直接顶:厚度小于1.5m~2m、较软弱、下面又无老顶的岩层伪顶:煤层与老顶或直接顶之间厚度小于0.5m 随采随冒的软弱岩层碎胀性:掩饰破碎后的体积比整体状态下的大、碎胀系数:破碎后体积与整体之比软化性:岩石浸水后强度降低软化系数:水饱和与干燥试件单向抗压强度比裂隙带:位于冒落带上方,以产生裂隙为主要特征的那部分岩层。
冒落带:直接位于煤层上方发生冒落的那部分岩层。
假说:压力拱假说,悬臂梁假说,铰接岩块假说,预成裂隙假说,砌体梁假说砌体梁结构:采场上覆岩层的岩体结构骨架是覆岩中的坚硬岩层,可将上覆岩层划分为若干组,每组以坚硬岩层为底层,其上部的软弱岩层可视为直接作用于骨架上的载荷工作阻力:支柱受顶板压力作用所反映出的力初撑力:支柱刚架设时对顶板产生的支撑力。
单体液压支柱:外注式、内注式。
与悬臂梁、铰接顶梁配合关系老顶的初次来压:工作面回采以来老顶第一次大规模来压周期来压:工作面内周期性的出现老顶来压现象端面距:顶梁前端到煤壁之间的距离。
控顶距:从煤壁至密集支柱(墩柱)或采空区顶梁末端的距离。
支护强度:支架对单位面积顶板提供的工作阻力;支护系统刚度:单位顶板下沉量所对应的支柱工作阻力。
支撑式支架:可适应中等稳定或完整的直接顶板,但支架漏、窜矸问题较大,不能抵抗来自沿层面方向的推力。
掩护式支架:能适应松软破碎的直接顶板,具有抵抗来自沿层面方向的推力的能力,但靠采空区的支撑力较小,不能适应老顶下沉来压的顶板。
支撑掩护式:既能适应松软破碎的直接顶板,又能适应老顶下沉来压的顶板,具有抵抗来自沿层面方向的推力的能力。
什么是伪顶?其对控制顶板设计有什么影响:伪顶是指在煤层与直接顶或之间有时存在厚度小于0.5m,极易跨落且随采随冒的软弱岩层。
在控制顶板设计中,伪顶冒落以后若抛弃在采空区,则控顶设计中直接顶的厚度应包括伪顶厚度,若随煤炭一起外运,控顶设计中煤层采高应包括伪顶高度。
简述直接顶、老顶与“三带”的关系:由采矿引起的上覆岩层破坏并向采空区跨落的岩层称为垮落带。
很多情况下跨落带是由直接顶跨落后形成的。
当直接顶较薄而老顶分层厚度又较小时,与直接顶毗邻的一部分老顶也可能进入跨落带。
裂隙带是指位于冒落带上方,以产生裂隙为主要特征的那部分岩层。
弯曲下沉带指位于裂缝带上方、直至地表的那部分岩层。
裂隙带主要是由老顶组成,弯曲下沉带全是由老顶组成。
采场顶板事故类型:采场顶板事故按力学原因划分如下:压垮型冒顶:1.垮落带老顶岩块压坏采场支架导致的冒顶;2.垮落带老顶岩块冲击压坏采场支架导致的冒顶;3.垮落带或裂隙带老顶旋转下沉时压坏采场支架导致的冒顶。
漏冒型冒顶:1.大面积漏垮型冒顶;2.靠煤壁附近局部冒顶;3.采场两端局部冒顶;4.放顶线附近局部冒顶。
推垮型冒顶:1.金属网下推垮型冒顶;2.采空区冒矸冲入采场的推垮型冒顶。
综合类型冒顶:1.厚层难冒顶板导致的冒顶;2.地质破坏带附近的局部冒顶;3.大块游离顶板导致的冒顶。
压垮型冒顶:由垂直于层面方向的顶板力压坏采场支架而导致的冒顶。
条件:1直接顶薄,厚度小于采高的2~3倍。
2煤层或直接顶上面存在老顶,分层厚度小于4m。
机理:(1)垮落带老顶岩块压坏支架导致冒顶:垮落带老顶岩块全部重量均由采场支架承受,若支架支撑力不够,就会压坏而冒顶。
(2)垮落带老顶岩块冲击压坏支架导致冒顶:初撑力不足,垮落带离层老顶岩块冲击采场支架,冲击压坏而冒顶。
(3)裂隙带老顶压坏采场支架导致冒顶:裂隙带老顶断裂、下沉、旋转、触矸时,若支架的可缩量不足,可能压坏导致冒顶。
预防冒顶的措施: 1)支架支撑力应能平衡垮落带直接顶及老顶岩层重量。
2)采场支架的初撑力应能保证直接顶与老顶之间不离层。
3)采场支架的可缩量应能满足裂隙带老顶下沉的要求。
前兆:1煤壁片帮。
2顶板下沉速度急剧增加。
3支柱载荷急剧增加。
金属液压支柱出现明显下缩并发出响声;支架安全阀开启。
4有时能听到顶板深处断裂声。
靠煤壁顶板顶板掉碴、断裂。
5信号柱折断发生劈裂声。
6摩擦支柱放炮。
漏冒型冒顶:由于采场直接顶软弱易破碎。
大面积漏垮型冒顶条件:直接顶异常破碎;煤层倾角较大。
机理:支护系统中若某处失效发生局部冒顶,破碎顶板就可能从该处沿工作面向上全部漏空,使支架失稳,漏垮工作面。
预防措施:1)使支护系统有足够的支撑力与可缩量。
2)顶板必须背严背实、梁头顶紧煤壁,采煤后及时支护、甚至要掏梁窝。
3)严防放炮、移溜等工序弄倒支架发生冒顶。
靠煤壁附近局部冒顶:顶板由于被裂隙切割,存在镶嵌型游离岩块或端面距过大或放炮崩倒支柱所致。
预防措施:综采面:提高初撑力控制端面冒高;及时支护方式,控制端面距;采高大于2.5~3.0m时,加护帮装置,避免端面距扩大;控制顶板(如固结碎顶)。
单体面:及时支护,端面距不超过200mm。
采用正悬臂交错顶梁,正倒悬臂错梁直线柱支护。
采场两端局部冒顶(单体面):机头机尾处是因移溜时支护操作不当(先拆后支),导致碎顶冒落。
措施:用“四对八梁”支护,或用双楔铰接顶梁支护。
工作面与巷道交接处是因交接处需去掉原巷道支架一个腿,如果支护操作不当,可导致碎顶冒落。
措施:交接处宜用一对迈步抬棚。
放顶线附近的局部冒顶(单体面):是因人工回柱时,顶板冒落伤人。
特别是分段回柱回最后一棵柱时。
措施:应在有支护的地点远距离操作后采用墩柱支护。
推垮型冒顶:由平行于层理方面的顶板力推到采场支架而导致的冒顶。
金属网下推垮型冒顶:条件:1煤层倾角在20°以上。
2网上是悬浮顶板,岩层间有空隙。
3单体工作面。
网下推垮分两个阶段。
1)形成网兜。
原因是工作面内某位置的支护失效。
当支架稳定性好时,不会推垮。
2)推垮工作面。
原因是网上碎矸与上位岩层之间有空隙,支架不稳定,网兜向下拉力拉倒支架,造成推垮型冒顶。
预防措施:提高初撑力,增加支架稳定性。
1)单体液压支柱工作面:①采用内错式布置切眼,提高支柱的初撑力,避免形成网上空隙,严防支护失效。
②当垂直布置切眼时,初放阶段用“整体支架”。
2)摩擦支柱工作面。
采用“整体支架”支护。
3)内错式布置切眼时,初放前要剪网,保证将金属网放到底板。
4)采用伪斜布置工作面。
采空区冒矸冲入采场的推垮型冒顶:发生机理:当顶板呈大块在采空区垮落时,可能顺着已垮落的矸石堆冲入采场,推倒采场支架(从柱根推倒),导致事故。
预防措施:(1)用切断墩柱的初撑力切断顶板(减小冒落顶板的块度),并将冒矸挡在采空区。
(2)当顶板分层过厚切不断时,用挑顶法,使冒矸超过采高。
综合类型冒顶:厚层难冒顶板冒顶:条件:1煤层倾角在20°以上。
2网上是悬浮顶板,岩层间有空隙。
3单体工作面。
机理1)岩体在自重作用下,拉断形成小裂缝,然后裂缝贯穿,发生大断裂,导致冒顶。
切断。
2)煤柱上的顶板岩层内产生强大的切应力,顶板被切断,导致冒顶。
剪断。
措施:1)用挑(钻爆法或高压注水)松散碎裂2~3倍采高顶板(包括直接顶在内)。
把“挑”的部分看成是垮落带岩层,即可按常规法防压、漏、推。
综采面:一般应超前工作面碎裂。
单体面:考虑到冒矸块度大,放顶线上支柱应有足够的支撑力与稳定性,条件允许时用墩柱。
2)若有可能(即厚层顶板分层不太厚),挑顶一部分,令剩余部分转变为裂隙带老顶。
复合顶板”推垮型冒顶:当游离岩块处在工作面中,厚0.5~3.0m,而沿岩块倾斜下方又有让岩块向下运动的空间时,岩块可能推倒单体支架,导致“复合顶板”推垮型冒顶。
机理为出现离层(支柱初撑力小)、断裂、去路和倾角、推力大于阻力等现象。
措施:1)尽量避免出现游离岩块①提高支架或支柱的初撑力,使下位顶板不离层,并不沿煤壁断裂。
②不在计划的工作面范围内开巷道。
(2)已出现游离岩块时在游离岩块范围内不正常回柱,加强支护,用木支柱替换金属支柱,当游离岩块都进入采空区时,再用绞车回柱。
(3)当游离岩块可能发生“复合顶板”推垮型冒顶时应使用支架或支柱的初撑力防推。
(4)当工作面使用初撑力极低的摩擦支柱时,只能用“整体支架”防“复合顶板”推垮型冒顶(5)采用伪斜工作面布置。
(实际答题时,只要答2~3点即可。
复合顶板推垮型冒顶特点:1)压力小、支架没有变形、损坏和明显下缩。
2)离层后,形成不稳定结构,有横向移动倾向;沿煤壁断裂;3)冒顶后支护以倾倒为主;4)冒顶后上部岩块大面积悬露,个别冒落。
5)多发生在切眼附近。
6)没有明显征兆,来势猛、速度快、人力无法抗拒。
采场中易发生推冒顶的地点:1)开切眼附近2)地质破坏带附近3)尖灭构造附近4)旧巷附近5)掘进上下平巷时破坏了复合顶板的地点6)局部冒顶区附近7)倾角大的地段8)顶板岩层含水的地段对采场支架的基本要求:1采场支架对顶板应能支得起,就是要求支架在其工作全过程都能够支承住顶板所施加的压力,否则就会导致压垮型冒顶事故。
2采场支架对顶板应能护的好,就是要求采场支架能控制住工作空间的顶板,使其一点不冒落,如果护的不好,则可能会发生漏冒型冒顶。
3采场支架对顶板应能稳得住,就是要求支架具有抵抗来自层面方向推力的能力,如果采场支架对顶板稳不住,则可能会导致推垮型冒顶。
预防冒顶事故控顶设计的原则:1防压工作阻力支撑住垮落带的直接顶与老顶。
2防漏综采面对软弱顶板选用掩护式或支撑掩护式支架。
用及时支护方式,端面距小于340mm。
采高大时,应又护帮装置。
必要时固结顶板单体面对软弱顶板支柱上应又顶梁、背板、甚至背严及掏梁窝,柱距小于0.7m,端面距小于200mm。
工作面两端用“四对八梁”或双楔交接顶梁。
3单体面或不用端头支架的综采面,面巷交接处用一对迈步抬棚。
最小控顶距的确定方法:从采煤生产要求出发,大多数工作面最小控顶距是三排,即机道、人行道与材料道。
有些情况下需要用四排柱子,比如老顶来压期间可扩大一排控顶距,从而缓和老顶初次来压的威胁,复合顶板初次垮落期间,也可扩大一排控顶距以增加支护的稳定性。
当出现地质破坏带或因矿井瓦斯涌出量较大时,需较大的通风断面来满足通风要求时,也需要采用四排柱子。
顶板状态参数:薄及中厚煤层开采时,最重要的顶板状态参数有顶底板移近量,端面冒高,顶板台阶下沉量,网兜高度四个参数。