Q345钢焊接裂纹原因分析
焊缝横向裂纹产生的原因和解决方法
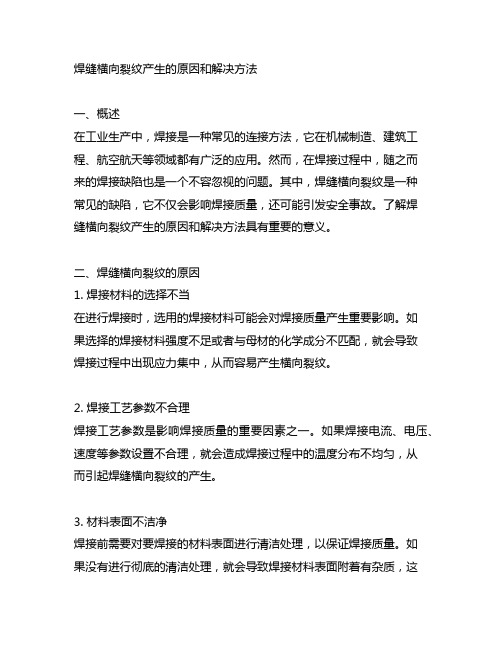
焊缝横向裂纹产生的原因和解决方法一、概述在工业生产中,焊接是一种常见的连接方法,它在机械制造、建筑工程、航空航天等领域都有广泛的应用。
然而,在焊接过程中,随之而来的焊接缺陷也是一个不容忽视的问题。
其中,焊缝横向裂纹是一种常见的缺陷,它不仅会影响焊接质量,还可能引发安全事故。
了解焊缝横向裂纹产生的原因和解决方法具有重要的意义。
二、焊缝横向裂纹的原因1. 焊接材料的选择不当在进行焊接时,选用的焊接材料可能会对焊接质量产生重要影响。
如果选择的焊接材料强度不足或者与母材的化学成分不匹配,就会导致焊接过程中出现应力集中,从而容易产生横向裂纹。
2. 焊接工艺参数不合理焊接工艺参数是影响焊接质量的重要因素之一。
如果焊接电流、电压、速度等参数设置不合理,就会造成焊接过程中的温度分布不均匀,从而引起焊缝横向裂纹的产生。
3. 材料表面不洁净焊接前需要对要焊接的材料表面进行清洁处理,以保证焊接质量。
如果没有进行彻底的清洁处理,就会导致焊接材料表面附着有杂质,这些杂质会影响焊接的质量,增加裂纹的产生可能性。
4. 焊接残余应力在焊接过程中,由于温度的变化和热量的不均匀分布,容易产生残余应力。
这些残余应力会导致焊接部位的局部变形,最终导致焊缝横向裂纹的产生。
5. 设计缺陷在一些情况下,焊接工件的设计本身存在缺陷,比如焊缝的设计不合理、板材的厚度悬殊等,都会增加焊缝横向裂纹的发生。
三、焊缝横向裂纹的解决方法1. 优化焊接材料的选择在进行焊接前,需对焊接材料进行严格的选择,确保其与母材的化学成分匹配,且具有足够的强度。
对于使用对焊材料的情况,需要对搭铁焊接材和母材的化学成分及性能进行检测。
2. 合理设置焊接工艺参数合理设置焊接工艺参数是避免焊缝横向裂纹产生的重要手段。
在进行焊接前,需要根据具体的情况合理地设置焊接电流、电压、速度等参数,确保温度的均匀分布和焊接的质量。
3. 加强材料表面清洁处理在进行焊接前,需要对焊接材料表面进行严格的清洁处理。
Q345C钢板弯曲裂纹原因分析及应对措施

表 1 Q345C 化学成分(%)
元素 C
Mn
Si
P
S
Al
V
Nb
Ti
含量 燮 0.20 燮 1.70 燮 0.55 燮 0.035 燮 0.035 叟 0.015 0.02-0.15 0.015-0.060 0.02-0.20
1.2 板材轧制方向的影响 Q345C 钢板由钢坯加热轧制而成,轧制就是将
拉伸试验。从表 2 Q345C 钢板拉伸试验数据可以看 出,钢板横向与纵向的机械性能有一定的差别,钢板 横向的塑性和韧性性能低于纵向 4 %左右。
表 2 Q345C 拉伸数据
板厚(mm) 10 20
轧制方向 横向 纵向 横向 纵向
抗拉强度(Mpa) 525-540 535-550 495-515 510-535
刺或者对有毛刺的弯曲部分进行退火处理,提高其 塑性。
(3)超过厚板弯曲极限而又要弯曲成小半径时, 采用附加反压法。该方法是自由弯曲模中,下模使用 强力顶料板,其能在弯曲过程中对板的变形部分增 加压缩应力,从而可以使最小弯曲半径显著减小,防 止裂纹的产生。
(4)如要加工图 1(a)中的折弯,可以将曲线从 毛坯断面后移(2t+R),或者将弯曲线对齐毛坯断面, 则须制出(1.5-2.0t+R)的空槽。图 1(b)中进行中空弯 曲加工时,首先要考虑冲出大于板厚 2-3 倍的槽,然 后就行弯曲;或者在前道工序中开出圆形的工艺孔, 而后进行冲裁(切口)- 弯曲加工。
对下好料的钢板进行 900 ℃正火处理。正火可 以细化晶粒,均匀组织,改善钢板的综合机械性能, 在不降低强度的条件下,提高钢板的塑性和韧性。
取压弯成型时在压弯处有裂纹的零件,制成拉 伸试样,采用 900 ℃空冷正火处理后进行拉伸试验, 表 2 为拉伸试验数据,从表 3 正火态 Q345C 钢板拉 伸试验数据可以看出,强度基本没有变化,但伸长率 横向与纵向变化很大,和热轧态相比,提高了 10 %左 右,而且横向与纵向的伸长率基本相同,因此热处理 后的钢板塑性和韧性提高很多。基本能够满足弯曲 要求。对发现裂纹的零件,进行了 900 ℃正火处理, 在处理后进行压弯成型,未发现裂纹。
Q345B板材弯折开裂原因分析

Q345B钢板伸长率不合的原因分析摘要通过对Q345B钢板伸长率影响因素的分析和研究,表明钢中夹杂物、异常组织及带状组织是Q345B钢板伸长率不合的主要原因。
并提出了工艺改进等相关措施,改善并提高了钢板伸长率性能。
0 前言Q345B钢板是低合金高强度结构钢,广泛用于制造各类结构件。
最近在对天津钢铁公司一批Q345B钢板进行力学性能检测时,发现伸长率明显偏低,规格集中在厚度30 mm以上,严重影响该产品的正常生产和合同交货期。
本文利用光学金相、扫描电镜分析等手段,对Q345B钢板拉伸断口试样进行显微组织、断口形貌、夹杂物类型分析,找出了造成Q345B钢板伸长率偏低的原因。
1 试验材料成分及力学性能选用的试验材料是Q345B钢板,加工好的试样在常温条件下进行拉伸试验。
其化学成分及力学性能检测结果见表1和表2。
通过对比分析伸长率合格与不合试样的成分,发现两者并无明显差别,但钢板伸长率性能相差很大,说明化学成分不是造成产品伸长率偏低的主要原因。
2试验结果及分析2.1金相分析从伸长率不合的1#试样钢板上取纵向试样,进行磨制、抛光,在光学金相显微镜下观察评定钢中夹杂物,发现钢中夹杂物主要以A类(硫化物)和B类(硅酸盐)为主,且试样中夹杂物级别较高,A类为细系2.5,B类为细系2.0。
D类和DS类夹杂物级别一般,D类为细系1.0,DS类为·39·第18卷第3期2012年6月宽厚板WIDE AND HEAVY PLATEVol.18,No.3June 20120.5,且由于尺寸较小,分布较为弥散,因此,A类和B类夹杂物对塑性指标的影响较大。
用4%硝酸酒精侵蚀后,观察其金相组织,见图1。
图1 1#试样板厚1/2处显微组织从金相结果来看,板厚1/2处金相组织为铁素体、珠光体和少量针状铁素体,试样心部存在贝氏体,这两类组织可降低钢板的塑性指标,此外,心部还有微裂纹;带状组织级别为2.5~3.0级,导致钢板横向性能变差,并在拉伸过程中产生木纹状断口,影响伸长率指标[1];晶粒度级别为7.5~8级。
Q345B钢板冷弯开裂原因分析及改进措施

Doi :10.3969/j .issn .l 006-110X .2018.z l .012Q 345B 钢板冷弯开裂原因分析及改进措施李惠娟0天津钢铁集团有限公司产品质量部,天津%〇〇%〇〇[摘要]通过采用宏观检验、化学成分分析、力学性能检测以及金相检测等方法对Q 345B 钢板冷弯开裂样品进行分析。
结果表明,冷弯开裂的主要原因是硫化物夹杂过多。
硫化物夹杂在冷弯过程中易碎裂或与基体组织分离产 生孔隙并成为裂纹源,且硫化物夹杂易导致轧钢过程中出现带状组织,而严重的带状组织也加剧了宏观裂纹的形成。
提出了采用铁水预处理脱硫、增加吹氩强度、保证吹氩时间、增大轧制冷却速度等方法改善Q 345B 钢板的塑性和韧 性,降低冷弯开裂的几率的建议。
[关键词]冷弯裂纹;硫化物夹杂;带状组织Cause Analysis and Improvement Measures of Cold BendingCracking of Q345B Steel PlateLI Hui-juan(Tianjin Iron and Steel Group Co ., Ltd . Tianjin 300301, China )Abstract The cold bending cracking samples of Q 345B steel plate were analyzed by macroscopical examination , chemical composition analysis , mechanical property test and metallographic examination . The results showthatthemainreason ofcoldbending cracking istoomansulphide inclusions are prone to break or separate from the matrix to form pores and become the source of cracks during cold bending , and the inclusion of sulfides can lead to the appearance of banded structures during rolling , and the formation of macroscopic cracks is aggravated by the serious banded structure . Some suggestionsareputforward toimprove theductility and toughness of Qand reduce the probability of cold bending cracking by means of desulphurizing pretreatment of molten iron , increasing argon blowing strength , ensuring argon blowing time and increasing rolling cooling rate . Key words cold bending crack , sulphide inclusion , banded structure〇引言Q 345B 钢板综合性能好,广泛应用于桥梁、车 辆、船舶、建筑、压力容器等行业,但在加工使用过 程中偶有冷弯开裂现象。
焊接裂纹产生原因及防治

焊接裂纹产生原因及防治背景焊接裂纹就其本质来分,可分为热裂纹、再热裂纹、冷裂纹、层状撕裂等。
下面仅就各种裂纹的成因、特点和防治办法进行具体的阐述。
1.热裂纹在焊接时高温下产生的,故称热裂纹,它的特征是沿原奥氏体晶界开裂。
根据所焊金属的材料不同(低合金高强钢、不锈钢、铸铁、铝合金和某些特种金属等),产生热裂纹的形态、温度区间和主要原因也各不相同。
目前,把热裂纹分为结晶裂纹、液化裂纹和多边裂纹等三大类。
1)结晶裂纹主要产生在含杂质较多的碳钢、低合金钢焊缝中(含S,P,C,Si缝偏高)和单相奥氏体钢、镍基合金以及某些铝合金焊缝中。
这种裂纹是在焊缝结晶过程中,在固相线附近,由于凝固金属的收缩,残余液体金属不足,不能及时添充,在应力作用下发生沿晶开裂。
防治措施:在冶金因素方面,适当调整焊缝金属成分,缩短脆性温度区的范围控制焊缝中硫、磷、碳等有害杂质的含量;细化焊缝金属一次晶粒,即适当加入Mo、V、Ti、Nb等元素;在工艺方面,可以通过焊前预热、控制线能量、减小接头拘束度等方面来防治。
2)近缝区液化裂纹是一种沿奥氏体晶界开裂的微裂纹,它的尺寸很小,发生于HAZ近缝区或层间。
它的成因一般是由于焊接时近缝区金属或焊缝层间金属,在高温下使这些区域的奥氏体晶界上的低熔共晶组成物被重新熔化,在拉应力的作用下沿奥氏体晶间开裂而形成液化裂纹。
这一种裂纹的防治措施与结晶裂纹基本上是一致的。
特别是在冶金方面,尽可能降低硫、磷、硅、硼等低熔共晶组成元素的含量是十分有效的;在工艺方面,可以减小线能量,减小熔池熔合线的凹度。
3)多边化裂纹是在形成多边化的过程中,由于高温时的塑性很低造成的。
这种裂纹并不常见,其防治措施可以向焊缝中加入提高多边化激化能的元素如Mo、W、Ti等。
2、再热裂纹通常发生于某些含有沉淀强化元素的钢种和高温合金(包括低合金高强钢、珠光体耐热钢、沉淀强化高温合金,以及某些奥氏体不锈钢),他们焊后并未发现裂纹,而是在热处理过程中产生了裂纹。
钢结构焊接裂纹的产生及预防

钢结构焊接裂纹的产生及预防摘要:指出了焊接接头的含氢量、材质的淬硬倾向和约束应力的影响是焊接裂纹特别是冷裂纹产生的主要原因,提出通过采用预热和后热、保持焊条的干燥和清洁、合理的焊缝设计和焊接工艺方法耒预防裂纹的产生。
关键词:焊接裂纹;氢含量;淬硬;约束应力;焊接工艺1 引言钢结构具有强度高、重量轻、塑性和韧性好,且工业化程度高,可以成批大件生产、施工速度快等特点。
在工程中特别是电厂得到广泛应用和迅速发展。
近年来,低合金高强钢中厚板在工程中使用趋于普遍,但较厚的钢板与较薄板比较,由于钢板厚度加大时存在冶金缺陷的成分可能加大,同时厚板辊轧次数减少,颗粒一般较薄板粗糙,所以中厚板在焊接中就会带来一系列问题,较为严重而又十分普遍的就是裂纹。
2 焊接裂纹的产生裂纹是焊接连接中最危险的缺陷。
按产生的时间不同,可分为热裂纹和冷裂纹,前者是在焊接时产生的,后者是焊缝冷却过程中或冷却后产生的。
在电厂钢结构中,使用过程中产生冷裂纹往往是很严重的质量问题。
冷裂纹的产生和发展一般都比较隐蔽、时间较长,平时不会引起操作人员的注意,但一旦发生其后果却是灾难性的。
在焊接生产过程中,由于采用的焊接材料不同,结构类型、刚度以及施工、安装的具体条件不同,可能出现各种形态的冷裂纹,比较常见的有焊趾裂纹、焊道裂纹、根部裂纹等。
冷裂纹大多数具有一定的延时性即是一种延迟裂纹,一般是在有载荷的使用过程中产生的,裂纹发生之前有一段潜伏期,然后是裂纹的扩展,最后发生脆性断裂,因此危害性很大。
大量的实践和理论研究表明,冷裂纹产生的原因主要有以下几种:焊接接头含氢量、材质的淬硬倾向现象以及约束应力的影响等。
2.1 氢对焊缝的影响焊接时,焊接材料中的水分、电弧周围空气中的水蒸气、焊丝和母材表面上的铁锈油污等杂质,在施焊时经电弧热分解而给焊缝中带入氢,而氢是引起焊接延迟裂纹的主要因素之一。
焊接时,在高温条件下,大量的氢溶解在溶池中,在随后的冷却过程中,由于溶解度的急剧降低,氢将极力逸出,但因焊接时冷速过快,使氢来不及逸出而保留在焊缝金属中,焊缝中的氢处于过饱和状态,因而氢要极力扩散,焊缝中的含氢量是随时间而变化的。
焊接裂纹产生原因及防治措施

焊接裂纹产生原因及防治措施焊接裂纹是指在焊接过程中,焊缝或焊接接头出现的裂纹现象。
焊接裂纹的产生原因有很多,主要包括材料选择不当、焊接工艺参数不合理、应力集中、焊接变形等因素。
为了防止焊接裂纹的产生,需采取相应的防治措施。
一、材料选择不当是造成焊接裂纹的主要原因之一。
不同材料的热膨胀系数、熔点和强度等性质差异较大,若选择不当,会导致焊接时产生较大的残余应力,从而引发焊接裂纹。
因此,在焊接前应对材料进行仔细选择,确保焊接材料的相容性和相似性。
二、焊接工艺参数不合理也是引起焊接裂纹的重要原因。
焊接过程中,焊接电流、电压、速度等参数的选择不当,容易造成焊接热输入过大或过小,从而导致焊接裂纹的产生。
因此,需要根据焊接材料的厚度、形状和焊接位置等因素,合理调整焊接工艺参数,以减少焊接残余应力的产生。
三、应力集中也是焊接裂纹的重要原因之一。
焊接过程中,由于材料的热膨胀和收缩不均匀,会导致焊接接头处应力集中,从而造成焊接裂纹的产生。
为了减少应力集中,可以采取适当的预热和后热处理措施,使焊接接头的温度均匀分布,减少残余应力的产生。
四、焊接变形也是引起焊接裂纹的常见原因。
焊接过程中,由于热膨胀和收缩的影响,焊接接头会发生一定的变形,如果变形过大,就会产生焊接裂纹。
为了控制焊接变形,可以采用适当的夹具和焊接顺序,使焊接接头得到良好的约束,减少变形的发生。
为了预防焊接裂纹的产生,可以采取以下防治措施:1.合理选择焊接材料,确保材料具有相似的熔点和热膨胀系数,减少焊接时的残余应力。
2.合理调整焊接工艺参数,根据焊接材料的特性和焊接位置,确定合适的焊接电流、电压和速度等参数,以减少焊接热输入和残余应力。
3.采取适当的预热和后热处理措施,使焊接接头的温度均匀分布,减少应力集中和残余应力的产生。
4.采用适当的夹具和焊接顺序,控制焊接变形,减少焊接裂纹的发生。
5.进行焊接前的材料表面处理,确保焊接接头的清洁度和表面质量,减少焊接缺陷的产生。
Q345H型钢焊接开裂原因分析-大冶金

68
������������������������������������������������������
4
2) 改变焊缝的施焊顺序。组装定位完成后进 行焊接时, 先焊接连接板与翼缘板的纵向角焊缝, 再焊接端部的封口焊缝。先焊接纵向角焊缝时, 由 于端部封口位置焊缝还没有焊接, 纵向角焊缝焊接 时处于自由状态, 纵焊缝受力状态良好; 最后焊接 端部封口焊缝时, 由于纵向角焊缝焊接过程中的纵 向收缩已经完成, 封口焊缝不再承受因纵焊缝收缩 对它施加的拉力, 受力状态得到极大改善。 3) 焊接过程要严格按规范和设计要求进行施 焊。一是定位焊缝焊接时, 要严格遵守国家相关规 范规定, 定位焊缝的长度应≥40 mm, 且焊脚尺寸最 小不得<3 mm (有的规范规定为最大不超过主焊缝 焊高的 2/3) 。二是端部封口焊缝焊接时, 一定要满 足设计要求的焊脚尺寸。大的焊脚尺寸增大了焊 接时的线能量输入, 降低了焊缝冷却速度, 有利于 改善焊缝组织成分, 提高焊缝的强度。
第 36 卷 第 2 期 2014 年 4 月
������������ ������������������������������������������������������
山
东
冶
金
Shandong Metallurgy
Vol.36 No.2 April 2014
1 前 言
在某工程施工过程中, 材质为 Q345 的热轧 H 型 钢 (规格 400×400×13×21) 钢柱在焊接过程中出 现了严重的焊接开裂, 致使多件构件报废。根据现 场实际情况分析, 首先排除了焊材、 母材因素对产 生裂纹的影响, 然后从引起焊缝开裂的焊缝金属的 组织成分、 焊接完成后焊缝内应力、 定位焊缝焊脚 尺寸 3 个方面进行分析。分析得出, 在 H 型钢焊接 过程中, 由于定位焊缝位置选择不正确、 焊脚尺寸 过小, 造成焊接完成后焊缝内部产生严重的质量缺 陷, 从而导致了焊缝开裂。
- 1、下载文档前请自行甄别文档内容的完整性,平台不提供额外的编辑、内容补充、找答案等附加服务。
- 2、"仅部分预览"的文档,不可在线预览部分如存在完整性等问题,可反馈申请退款(可完整预览的文档不适用该条件!)。
- 3、如文档侵犯您的权益,请联系客服反馈,我们会尽快为您处理(人工客服工作时间:9:00-18:30)。
艺应做 相应的调整 ,需 X ,  ̄ Q 3 4 5 钢板焊前预热,
以减 少焊 缝 开 裂 的可 能性 。
该试样断 口处枝 品状形态 比较的明显 ,断
口处疏松 比较 的严重 ,开裂为沿 晶特征。
3 - 2 母材中有害元素P 含量较高 ,极易形成液态
综上所述 ,该焊接件母材 n , ' j c 元素 、c 当量
素结构钢相 比 ,具有强度高 、耐腐蚀性好 、用 于工程结构制 造重量轻 、低 温性 能好等特点 , 在液压支架 的生产 中广泛使用 ,在焊接过程 中 出现裂纹 的现象也较为普遍 。因此 ,针对Q 3 4 5 钢分析其焊接裂纹也就十分有必要 。
图 1 焊接裂纹位置示意图
进行母 材化学成 分检验 、金相组织检验 、硬度
i
忘 , Ⅷ m
Q3 4 5  ̄ R 焊 接 裂 纹原 因分 析
枷 s i s◎ 4 屯 @ @ l Ⅱ g Cr oc k
何志松 张俊峰 文/ 郑州四维机 电设备制造 有限公司 吕海洋 贺 睿
摘 要 :本文通过对Q 3 4 5 钢焊接裂纹处母材化学成分检验、金相组织检验 、硬度检测及断口扫描分
2 . 3 硬 度 检测
( a ) 焊缝裂纹始端显徽组织l O 0 x ( h ) 焊缝 裂纹 未端显微 ̄ l t L q l O O ×
针对焊接接 头试样 ,分别对其 上的母材 、 热影响 以及焊缝 一个 域进行硬度检测 。检
图2 焊缝 裂纹处金相组织示意网
测使用 维氏硬度 计,实验力 为4 9 . 0 3 N,保持时
断提高 ,液压支架 的承载重量及稳定性要求也
越来越高 ,液压支架开始朝着大配套、大阻力 、
焊丝 J 焊丝直径 l 焊接电流 l 焊接电 压 l 焊接速度 牌号 l ( m m) I ( A) l ( v) l( r a m / a r i n )
1 . 2 l 2 8 0 ~ 3 0 0 I 2 9 ~ 3 1 f 3 0 0 ~ 3 5 0
为1 5 5 。愉测结果见表3 。 从表3 可以看 出,焊缝区和热影 ̄ l a j l  ̄ - 的硬度
高于 母材 。而在正常情况下 ,该处 的硬度值高
于母材。 2 . 4 断 口扫 描 分析
.
清洁断 口表面后进行断 口扫描分析 ,如 图
3 N示 。
『 矧 3 断 口扫描形貌示 意
表3 焊接接头硬度检测结果 【 HB )
其它元素则符合标准值。
2 _ 2 金 相 组 织检 验
f : ; = 测位 I 母材I x 2 l 热影n l  ̄ l , I x 2 f 焊缝I x 2
检测值 I 1 9 9 ;1 9 5 ;1 9 5 l 2 6 5 ;2 9 9 ; 3 2 8 l 2 7 4 ;2 4 1 ;2 4 1
将焊接裂纹位置制成T 型接头,并对裂纹处
作者简介 .吕海洋 ( 1 9 8 4 一),男 ,河南科技 大学材料成型及控制工程专业毕业 ,工艺院结构件所所长 ,焊接工程师 ,目前从事煤矿机械焊接工艺研究工作 。
现代焊接 2 0 1 4 年 第1 期 总第1 3 3 期 J 一4 1 , 9
意
金相试样采川4 %的硝酸酒精溶液腐蚀。
对该 试样 进 行 金相 显微 组织 观 察 ,如 图2 所
示 ,焊缝区组织 为柱状枝品组织 (氏组织 .焊缝开 裂在两侧枝品凝同的最后位置 ,垂直枝晶生长 的方向, 且断 口末端有 明显的疏松现象。
析 ,分析出Q 3 4 5  ̄ ] 焊接裂纹是 由于母材C当量较高,其可焊性较差 ,需对Q 3 4 5 钢板进行焊前预热 , 可有效避免焊接裂纹 的产生。
关键 词 :Q3 4 5 钢 ;焊接裂纹 :焊前预热
随着煤矿开采设备 的生产能力和可靠性不
1 Q3 4 5 钢富氩气体保护焊接工艺规范
薄膜,增加结晶裂纹倾向,应控制母材的P 含量
接近或高于G B f 1 5 9 1 — 2 0 0 8 q  ̄ Q 3 4 5 规定值的上限
检测及断 口扫描分析 。
1 检验材料 与方法
生产过程 中 ,Q 3 4 5 钢焊接工艺为富氩气体
2 试验结果及分析
2 . 1 母材化学成分检验
保护焊接 ,其工艺规范见表1 。 针对 生产过程 中焊接裂纹位置进行取样 ,
如图1 所示。
从焊接板母材上 随机取样进行化学成分检 验 ,其结果见表2 。 由表2 可见 ,该母材 中的c 元素 、c 当量 已 经超 出了标 准值 的上 限 ,而且其P 含量也较高,
高可靠性方向发展 ,因此对液压 支架结 构件 的
焊接要求也越来越 高 。焊接裂纹是接头中局 部区域 的金属原子结合遭到破坏而形成 的缝隙, 缺 口尖锐 、长宽 比大 ,在结构工作过程中会扩 大 ,甚至会使结构突然断裂 ,所以裂纹是焊接
接头中最危险的缺陷 。 Q 3 4 5 钢是低合金结构钢的一种 ,与普通碳
f : ; = 验项 日 杯准f f [ 愉验f f { ( : ≤0 - 2 0 0 _ 2 l 2 S i ≤( ) . 5 0 n, ’ 0 Mn ≤1 7 0 1 . 4 4 4 P ≤0 . 0 3 5 0 . 0 2 9 S ≤0 . 0 3 5 0 . 0 l l ( : l ≤0 . 3 0 0 . 0 6 5 N i ≤0 . 5 0 0 . 0 l 4 ( : I I ≤0 . 3 0 0 . ( ) l 4 MI 1 ≤( ) . 1 0 ( ) . 0 0 2 、 ≤( ) . 1 5 0 . 0 0 6 ( : E 、 ≤0 . 4 f 】 . 4 7