紫铜管开裂原因分析
关于铜管线伤产生原因及预防措施的探讨

关于铜管“线伤”产生原因及预防措施的探讨一、概述铜管厂生产的铜管,尤其是用于空调的蒸发器和冷凝器的内螺纹薄壁铜管,在用户加工使用中经常出现铜管发生开裂的质量事故,统称为“线伤”缺陷。
而且这些缺陷有时很难通过普通的涡流探伤机检测到。
用户为此退货不断,经常对公司处以高额罚款,甚至花费了千辛万苦才进入的用户转眼间就宣布无限期地停止供货。
对生产厂的声誉和经济利益均造成很大影响和损失。
因此有必要对这种缺陷产生的原因进行分析,找出其规律性,并采取针对性措施进行预防和纠正。
二、“线伤”的表现形式1、在制作两器时扩口开裂2、在涨管时开裂3、在气压试验局部泄露或整机泄露4、出厂时的铜管的抗拉强度和延伸率都很低,延伸率一般小于40%。
三、缺陷产生的原因1、工艺原因A、连铸坯表面裂纹是线伤产生的原因之一,尤其是拉停产生的裂纹。
该裂纹在铣面时如未铣净,在轧制时则产生表面“蜂窝”状折叠,随后拉拔则产生线伤。
B、连铸时内表面产生的蜂窝状结晶会导致管体拉拔后产生内表线伤。
C、连铸管坯内孔大于芯棒直径4mm以上时产生的空减径裂纹造成内表线伤。
D、管坯表面的缩孔(钻头孔)在轧制后出现折叠状线伤。
E、未铣净的有氧化色的管坯表面导致轧后出现线伤。
F、铣后管坯表面粘有碎铜屑或碎铜屑压入管坯表面都会在轧后形成缺陷,这些缺陷拉拔后形成局部线伤。
G、三辊行星轧机轧制时三个轧辊未在一个平面所轧制铜管形成亮线(碎铜带)形成线伤。
H、三辊行星轧机轧制时一冷水温度低于25℃,同时水量又大于4000L/min,造成变形区温度不到750℃,轧辊打滑形成管坯表面金属折叠造成线伤。
I、高速盘拉中,铜管开卷时的相互碰撞以及铜管与导卫辊的撞击形成的伤点经拉拔后成为“蜂窝状”线伤。
(拉拔速度由700m/min降到300m/min,打标点明显减少)。
J、在倒立式盘拉机上拉伸铸轧管坯的第1-2道次时,由于来料管坯硬化不够,被排料环擦伤铜管外表,形成连续线伤。
同时铜管与铜管之间的摩擦使这种伤痕更加严重,形成典型的线伤。
26432117_TP2紫铜管弯制开裂原因分析

均匀(在此状态下进行弯制!铜管不会开裂(
图8 "*#$##% g 退火后的外表面金相组 织( 该组织 为 无 方 向 性 块 状 较 粗 大! 相 M 少 量 粒 状 ! 相!晶粒清 晰 可 见 且 开 始 长 大! 组 织 形 貌 正 常( 在此状态下进行弯制!铜管不会开裂)9*(
开始出现!与该状态下的外表面金相组织一致( 将图 & 与 图 $ 进 行 对 比 可 看 出$ 在 原 始 状 态
下!外表面金相组织与内部金相组织的差异较大! 外表面的拉拔痕迹明显!组织织构程度严重!在此 状态下进行弯制!铜管一定会开裂&在!7% g退火 后!内部金相组织形貌回复较好!但外表面金相组 织仍存在一定的拉拔痕迹和位相!在此状态下进行 弯制!铜管仍会开裂&在##%g'9%%g'9#%g' 7#% g退火后!内部金相组织与外表 面金相组织 基 本一致!外表面的拉拔痕迹消失!在此状态下进行 弯制!铜管不会开裂&在大于9#% g退火后!晶粒
某产品需要加工不同批次的 LH$ 铜管!对弯 制区域先进行火工!再进行弯制(由于原材料铜管 的热处理状态不明确!因此采用相同的工艺进行弯 制后!有的铜管弯曲状态好!有的铜管开裂(铜管 在生产过程中经多道次拉拔产生加工硬化!塑性较 差!不利于后续弯制成型工艺的进行!需要进行退 火处理改善其微观组织及性能(为解决铜管弯制开 裂问题!进行一系列的退火'力学性能和金相组织
第!"卷第#期 ! $%$&年&%月 文章编号&%%%;8:7:"$%$&#%#;%%#%;%!
T2紫铜工艺品热变形脆裂分析_张智强

某厂使用的 T 2紫铜板 , 厚 1. 0mm , 退火状态。 工艺品生产的工艺流程为紫铜板 →下料→ 木炭加热 700 ~ 800 ° C → 热冲压成形。 在工艺品冲压成形过程中 , 出现了大量的脆裂 现象 。图 1为工艺品“大象” 开裂形貌 , 其冲压变形率 < 20 %。
张智强等 : T 2紫铜工艺品热变形脆裂 分析
表 1 紫铜板原材料杂质含量测定结果 ( w / % )
元素 标准值 原材料
[ 1]
Pb 0. 005 0. 002
Fe 0. 005 0. 0014
Bi 0. 001 0. 0006
Sb 0. 002 0. 0007
As 0. 002 0. 001
氧含量 (× 10- 6 ) 62 14 13 12 木炭加热后弯曲 1 6 10 9 1 8 7 1 9 7 1 7 10 11 箱式炉加热后弯曲 4 7 8 10 6 7 8 10 6 9 10 13 7 8 9 11
5 结论
( 1) 符合 GB5231- 85标准的 T 2紫铜板 , 当氧 - 5 含量高于 10 时 , 用还原性气氛加热 , 将出现脆裂 现象 。因此 , 必须选用含氧量极低的无氧铜板 ( T U1 , T U2 )。 ( 2) 如选用含氧量较高的紫铜板采用氧化气氛 加热 , 是解决紫铜工艺品热冲压脆裂的有效途径。 参 考 文 献
Yang Zhong Zhang Zhiqiang
( Luo Y ang Copper Gro up Co , Ltd. ) s brittle cracking during ho tfo rming wa s a naly zed. It was concluded Abstract The coppe r ( T 2) ar t wo rk that the tr ace element ox yg en in red co pper could be reduced by ca rbo n mo no xide in hig h tempera tur e, caused inter cry sta lline cracking.
空调制冷铜管“铜铝渗蚀”开裂失效分析
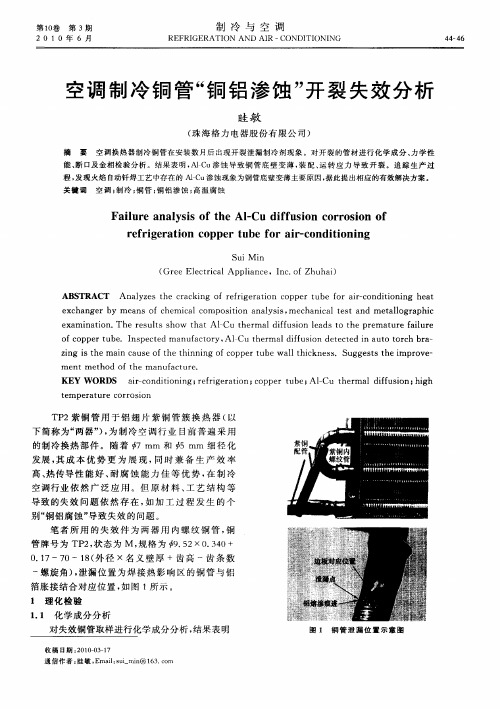
e c n e y m e n f c m ia omp ii n a l i , c n c l t s nd me a lg a i x ha g r b a s o he c lc osto nayss me ha i a e t a t lo r ph c e m i to Ther s ls s w h tA1Cu t e ma f u i n l a st h e t r al r xa na i n. e u t ho t a 一 h r ldif so e d o t e pr ma u e f iu e ofc p rt be ns e t d ma uf c o y, he ma if i n d t c e n a t o c r — o pe u .I p c e n a t r A1Cu t r ld fuso e e t d i u o t r h b a zn st i a eo h hi ni fc pp rt e walt i k s .Su e t h m p o e i g i hema n c us ft e t n ng o o e ub l h c ne s gg s st ei r v —
第1卷 第 3 0 期 2 0 1 0年 6月
制 冷 与 空 调
REFRI GERAT 1 N N D I —C0N DI 0 NI G 0 A A R T1 N 44 4 —6
空 调 制冷 铜 管 “ 铝 渗 蚀 " 裂 失 效 分 析 铜 开
眭 敏
( 海 格 力 电 器 股 份 有 限公 司 ) 珠
m e tm e h d o hem a f c u e n t o ft nu a t r .
KEY ORDS ar c nd ton n r fi e a i n; o e ub A1Cu t r ld fuso hi h W i— o ii i g; e rg r to c pp r t e; 一 he ma if i n; g
紫铜色氧化膜破裂的根源及防止措施
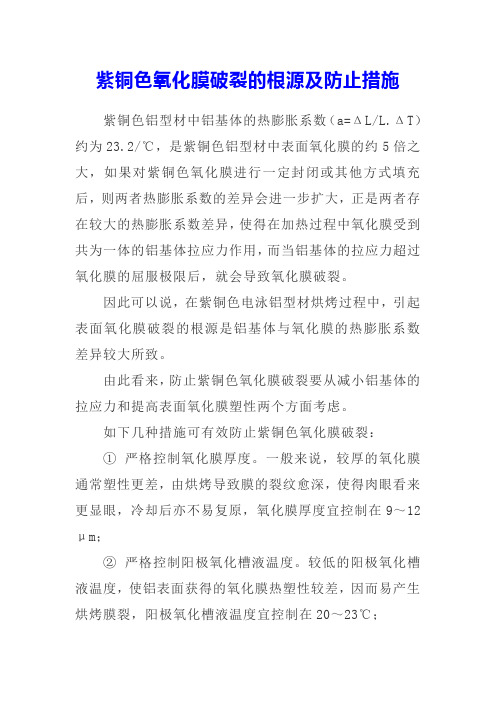
紫铜色氧化膜破裂的根源及防止措施紫铜色铝型材中铝基体的热膨胀系数(a=ΔL/L.ΔT)约为23.2/℃,是紫铜色铝型材中表面氧化膜的约5倍之大,如果对紫铜色氧化膜进行一定封闭或其他方式填充后,则两者热膨胀系数的差异会进一步扩大,正是两者存在较大的热膨胀系数差异,使得在加热过程中氧化膜受到共为一体的铝基体拉应力作用,而当铝基体的拉应力超过氧化膜的屈服极限后,就会导致氧化膜破裂。
因此可以说,在紫铜色电泳铝型材烘烤过程中,引起表面氧化膜破裂的根源是铝基体与氧化膜的热膨胀系数差异较大所致。
由此看来,防止紫铜色氧化膜破裂要从减小铝基体的拉应力和提高表面氧化膜塑性两个方面考虑。
如下几种措施可有效防止紫铜色氧化膜破裂:①严格控制氧化膜厚度。
一般来说,较厚的氧化膜通常塑性更差,由烘烤导致膜的裂纹愈深,使得肉眼看来更显眼,冷却后亦不易复原,氧化膜厚度宜控制在9~12μm;②严格控制阳极氧化槽液温度。
较低的阳极氧化槽液温度,使铝表面获得的氧化膜热塑性较差,因而易产生烘烤膜裂,阳极氧化槽液温度宜控制在20~23℃;③严格控制电泳漆膜厚度。
较厚的漆膜需要较长的烘烤时间,对抑制膜裂不利,电泳漆膜厚度宜控制在9~12μm;④严格控制半封闭工艺。
在控制好褪色情况下,尽量减弱封闭程度,应控制好封闭工艺参数,封闭速度不宜太快;⑤适当降低烘烤升温速度和烘烤温度。
如烘烤时升温速度越快、温度越高,则氧化膜所受到铝基体的拉应力及由拉应力产生的惯性力会愈大,就愈容易超过氧化膜的屈服极限而导致膜裂。
一般控制烘烤温度为160~170℃,烘烤保温时间为30~40min。
最好从室温或<50℃开始升温,从<50℃升至170℃宜控制在约60min,烘烤升温快、温度高亦易导致紫铜色褪色;⑥优先选用“二次电解着色法”抑制褪色。
该措施不会降低紫铜色氧化膜的热塑性,是一种既能有效防止褪色又不引发膜裂倾向的双优措施;⑦在产品标准要求许可的情况下,适当减薄基材(即铝基体)厚度,以减小紫铜色电泳铝型材烘烤时铝基体对氧化膜的拉应力。
铜管焊接后断裂原因

铜管焊接后断裂原因铜管焊接后断裂是一种常见的焊接缺陷,可能导致工件的破裂和损坏。
本文将探讨导致铜管焊接后断裂的原因,并提出预防措施。
铜管焊接后断裂的原因之一是焊接材料的选择不当。
在焊接过程中,如果使用的焊丝或焊条与铜管的材质不匹配,就会导致焊缝的脆化和断裂。
因此,选择合适的焊接材料对于确保焊接质量至关重要。
焊接工艺参数的控制不当也是铜管焊接后断裂的常见原因之一。
焊接过程中,如果焊接电流过大或过小,焊接速度过快或过慢,都会导致焊缝的强度不够,从而引起断裂。
因此,合理调整焊接工艺参数,确保焊接过程的稳定性和一致性,对于避免断裂问题具有重要意义。
焊接操作的技术水平也会影响铜管焊接后是否会发生断裂。
焊工的焊接技术熟练程度、焊接操作的规范性和严谨性都会对焊接质量产生重要影响。
不正确的焊接操作,如焊接过程中的晃动、停顿、过度加热等,都可能导致焊缝的质量下降,从而引起断裂。
焊接前的准备工作也是影响铜管焊接后是否会断裂的因素之一。
焊接前应对铜管进行充分的清洁和除氧处理,以去除表面的脏物和氧化物,保证焊接区域的纯净度。
如果焊接前的准备工作不充分,铜管焊接后易出现气孔和夹杂物,进而导致焊缝的强度下降,增加断裂的风险。
焊接过程中的热应力也是导致铜管焊接后断裂的重要原因之一。
焊接过程中,由于铜管在受热和冷却的过程中会发生体积变化,导致焊缝附近产生应力集中。
如果焊接过程中的热应力超过了铜管的承受能力,就会导致断裂。
因此,控制焊接过程中的温度变化和热应力分布,可以有效预防铜管焊接后的断裂问题。
铜管焊接后断裂的原因可能包括焊接材料选择不当、焊接工艺参数控制不当、焊接操作技术水平低、焊前准备不充分以及焊接过程中的热应力等。
为了预防铜管焊接后的断裂问题,我们应选择合适的焊接材料,合理控制焊接工艺参数,提高焊接操作技术水平,确保焊前准备工作的充分性,并控制焊接过程中的热应力。
只有这样,才能确保铜管焊接后的质量和可靠性,避免断裂问题的发生。
T3紫铜输油管断裂原因分析

T3紫铜输油管断裂原因分析王凡;刘素芬;张志伟;刘晓斌;赵豫东;温铁丽【摘要】某电厂用T3紫铜输油管使用约半年时间发生断裂失效。
采用宏观检验、断口微观分析、能谱分析、金相检验的方法,对该紫铜输油管的断裂原因进行了分析。
结果表明:输油管的断裂类型属于应力腐蚀开裂;管内的长效润滑油中含有应力腐蚀敏感介质硫和氯元素,且输油管弯曲部位存在较大拉应力,导致该紫铜输油管发生应力腐蚀开裂。
%One T3 red copper oil pipe of a power plant fractured after used for half a year.The fracture reasons of the red copperoil pipe were analyzed by methods of macrographic examination,fracture micro analysis, energy spectrum analysis and metallographic examination.The results show that:the fracture type of the oil pipe was stress corrosion cracking;the long-term lubricating oil contained the medium of chlorine and sulfur sensitive to the stress corrosion,and the tensile stress existed in the bending position of the oil pipe,and those factors resulted in the stress corrosion cracking of the red copper oil pipe.【期刊名称】《理化检验-物理分册》【年(卷),期】2017(053)001【总页数】3页(P70-72)【关键词】紫铜;输油管;腐蚀介质;拉应力;应力腐蚀开裂【作者】王凡;刘素芬;张志伟;刘晓斌;赵豫东;温铁丽【作者单位】中国兵器工业第五二研究所,包头 014034;中国兵器工业第五二研究所,包头 014034;中国兵器工业第五二研究所,包头 014034;中国兵器工业第五二研究所,包头 014034;中国兵器工业第五二研究所,包头 014034;中国兵器工业第五二研究所,包头 014034【正文语种】中文【中图分类】TG146.1+1紫铜以其优良的耐蚀性、耐高温、耐高压和易于弯曲变形、安装等特点,被广泛用作油管材料。
TP2铜螺旋管裂纹产生原因分析

理化检验-物理分册P TCA(PAR T:A P H YS1TEST1)2009年 第45卷 3质量控制与失效分析TP2铜螺旋管裂纹产生原因分析尚延伟,赵梅春,陈伟锋(浙江省绍兴市制冷配件检测中心,绍兴312500)摘 要:采用宏观观察、化学成分分析、扫描电镜断口观察及显微组织检验等方法对出现裂纹的TP2铜螺旋管进行了分析。
结果表明:多次冷变形使铜管处于加工硬化状态,内应力集中于肋片部位而导致裂纹产生。
并提出了改进措施。
关键词:螺旋管;化学成分;应力集中;裂纹中图分类号:T G146.1+1 文献标志码:A 文章编号:100124012(2009)0320172203Crack Analysis of TP2Copper H elical PipeSHANG Yan2w ei,ZHAO Mei2chun,CHEN Wei2feng(Testing Center for Ref rigeration Fitting of Shaoxing,Shaoxing312500,China)Abstract:The macroscopic analysis,chemical composition analysis,SEM observation and metallographic examination were to analyze cracks of the TP2copper helical pipe.The results showed that multiple deformations made the products in a work2hardening state during the cold forming,so internal stress concentrated in the fin2site lead to cracks.And the improved measures were also brought forward.K eyw ords:helical pipe;chemical composition;stress concentration;crack 紫铜管具有优良的导热性、耐蚀性及塑性,广泛用作空调、冰箱和热水器等家电产品的热交换器材料。
- 1、下载文档前请自行甄别文档内容的完整性,平台不提供额外的编辑、内容补充、找答案等附加服务。
- 2、"仅部分预览"的文档,不可在线预览部分如存在完整性等问题,可反馈申请退款(可完整预览的文档不适用该条件!)。
- 3、如文档侵犯您的权益,请联系客服反馈,我们会尽快为您处理(人工客服工作时间:9:00-18:30)。
涂在紫铜管表面的新型油胶中的氯离子是导致 紫铜管局部应力腐蚀开裂的主要因素。
参 考 文 献
1 托马晓夫. 金属腐 蚀及其保护 的理论. 北京: 机 械工业出版社, 1965. 214
2 北京 航空 学院 102 教研 室. 金属 的 断裂 故障 分 析 ( 上册) . 北京: 北京航空学院, 1976. 209-210
Keywords P ur e copper tube Oil g lue St ress co r ro sion cracking
1 概况
某冰箱厂原使用的 制冷紫铜管质量一直很稳 定, 但在采用新型油胶后, 出现了制冷剂( 弗里昂) 渗 漏现象, 为此我们对该批铜管进行了检验分析。
2 宏观检验
Tan Ying Wu Ji nye Chen Min
( G uang zho u Ent ry -Ex it Inspect ion & Quar antine Bur eau)
Abstract T he cracked pur e co pper tube w as analy zed by the metallo gr aphy, SEM and ED S. Cl element
w as detected in t he co rr osiv e pr oduct s. Cl io n was also fo und in oil g lue by chemical ana ly sis m ethod. It w as concluded that t he Cl io n in the oil g lue r esulted in st ress co r ro sion cracking of the pure copper t ube.
5 油胶检验
将油胶放入 A gN O 3 溶液中浸泡一段 时间, 发
现溶液浑浊, 出现白色沉淀物。氯离子与 A gN O 3 反
应 生 成 A gCl 白 色 沉 淀, 即 A gN O 3 + Cl-
A gC l↓+
N
O
3
,
由此确认油胶中含有氯离子。
6 讨论
上述检验结果表明, 紫铜管表面的腐蚀和裂纹 均出现在涂有油胶的部位, 而检验中未发现紫铜管 有冶金缺陷, 但在紫铜管表面的腐蚀孔洞中发现了 氯离子, 其它部位却未见氯离子, 这说明氯离子是一 种腐蚀促进剂[ 1] 。在对油胶的检验中也发现了氯离 子, 因此可以推断, 在油胶与紫铜管的接触中, 油胶 中的氯离子吸附在紫铜管的氧化膜上, 并替代了氧 化膜中的氧离子, 这样吸附在铜管上的氯离子与其 生成了金属的可溶性氯化物, 而使这个区域出现孔 洞[ 1] 。通常孔洞出现在表面晶界处能量较高的部位, 成为化学腐蚀电池的阳极( 在氧化膜未破坏的区域 为阴极) , 再加上紫铜管加工残余应力在腐蚀孔洞处 形成应力集中, 促进腐蚀的继续进行, 导致裂纹沿晶 扩展, 最后造成沿晶开裂的应力腐蚀破坏, 其断口形 貌为岩石状特征[ 2] 。
第 36 卷第 11 期 2000 年 11 月
失效分析
理化检验—物理分册
PTCA ( PA RT A : P HY Sபைடு நூலகம்CA L T EST I NG )
V ol. 36 N o . 11 No v. 2000
紫铜管开裂原因分析
谭 莹 吴敬艳 陈 明
( 广东出入境检验检疫局化矿金检测中心 广 州 510075)
收稿日期: 2000-02-22
·5 17 ·
4 金相检验
·51 6·
图 1 裂纹形貌 7×
图 2 岩石状特征 500×
谭 莹等: 紫铜管开裂原因分析
图 3 表面腐蚀孔 50×
图 6 再结晶组织 400×
图 4 腐蚀孔部位
图 5 未腐蚀区域
在裂纹附近未腐蚀区域截取金相试样, 抛光后 观察, 未见夹杂物和针孔。试样经侵蚀后观察, 组织 为再结晶 A单相固溶体, 见图 6。未见试样边缘组织 有异常现象。
摘 要 采用光学显微镜、扫描电镜及能谱仪对冰箱用紫铜管渗漏失效进行了分析。结果表明, 紫铜管渗漏系腐蚀引发裂纹所致, 而涂在铜管表面的油胶中的氯离子是引起紫铜管应力腐蚀开裂 的主要因素。
主题词 紫铜管 油胶 应力腐蚀开裂
CRACKIN G A NAL YSIS OF PU RE COP PER T U BE
紫铜管表面光滑, 局部涂有油胶。在体视显微镜 下观察, 发现在涂有油胶的部位出现裂纹。裂纹细 长, 呈黑色状, 见图 1。
3 电镜分析
将裂纹部位的油胶清洗干净并打断, 用扫描电 镜观察, 裂纹源产生于铜管外表面, 在其周围有腐蚀 痕迹, 裂纹表面的腐蚀较内部严重, 裂纹沿晶开裂呈 岩石状特征, 见图 2。裂纹附近有许多腐蚀孔洞弥散 分布在铜管的外表面, 见图 3。用能谱仪分析, 孔洞 处有氯元素存在( 见图 4) , 而未腐蚀的部位未发现 氯元素( 见图 5) 。