各大钢厂高性能钢材组织性能控制与品种开发
日本高性能特殊钢介绍

为适应冷镦(锻)的高速化和复杂部件的延展变形化,日本神户制钢开发出增加变形能力的KECH系列钢。其特点是:用超低碳化增加变形能量;添加Si和Nb来保证钢的强度。采用KECH系列钢可省略冷镦前的球化退火(CO2减排),并可实现复杂零部件的延展变形化大批量生产。
表1 TNH线材与硬钢线材焊接性评价对比
钢种
焊接区软化热处理
拉伸试验
90°弯曲试验
抗拉强度/MPa
断口位置
熔合线
HAZ
TNH线材
无
1422
HAZ
良好
良好
有
1191
HAZ
良好
良好
硬钢线材
有
1393
HAZ
裂纹
裂纹
有
1152
HAZ
良好
良好
b.抗弹性衰减性用松弛试验(JIS Z2276标准)对TNH钢丝线材的抗弹性衰减性进行评价,常温下TNH线材的钢丝比硬钢线材的抗弹性衰减性约提高40%。
① TNH线材钢的化学成分
通过低碳化(0.12%-0.14%C)提高焊接性和拉拔加工性,添加0.8%-0.9%Si进行固溶强化提高抗弹性衰减性;添加1.5%-2.0%Mn和0.45%-0.60%Cr提高淬透性。此外,为使组织细化和保证焊接区的韧性,还添加了Nb和Ti元素。
②TNH线材的主要特性
a.焊接性TNH线材与硬钢线材相比,见表1数据所示:TNH线材焊接区韧性好,既使焊前不预热,焊后不热处理,焊接区(HAZ、熔合线)也不会产生裂纹。因此,可以提高焊接区的保证强度。
在此之后,日本神户制钢又陆续开发出各种新型钢材,见表2,其中有可降低成本的硼钢,可使零件轻量化的高强度螺栓用钢KNDS系列钢,可降低生产成本并减排CO2的非调质线材KNCH系列钢,可提高模具寿命的KTCH系列钢,可增加变形能力的KECH系列钢等。
大型钢铁生产质量控制措施
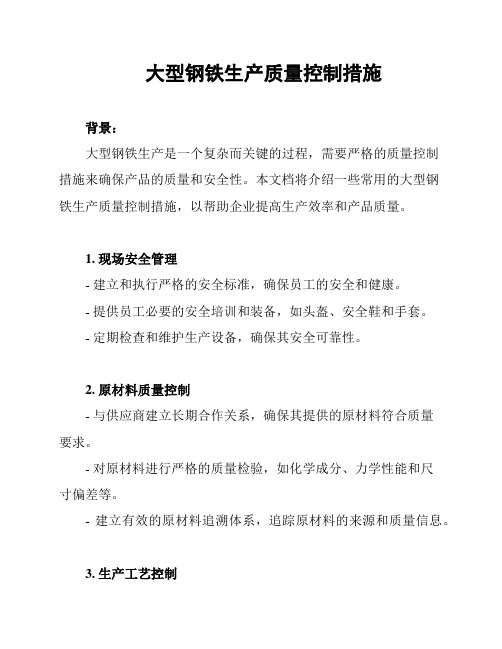
大型钢铁生产质量控制措施背景:大型钢铁生产是一个复杂而关键的过程,需要严格的质量控制措施来确保产品的质量和安全性。
本文档将介绍一些常用的大型钢铁生产质量控制措施,以帮助企业提高生产效率和产品质量。
1. 现场安全管理- 建立和执行严格的安全标准,确保员工的安全和健康。
- 提供员工必要的安全培训和装备,如头盔、安全鞋和手套。
- 定期检查和维护生产设备,确保其安全可靠性。
2. 原材料质量控制- 与供应商建立长期合作关系,确保其提供的原材料符合质量要求。
- 对原材料进行严格的质量检验,如化学成分、力学性能和尺寸偏差等。
- 建立有效的原材料追溯体系,追踪原材料的来源和质量信息。
3. 生产工艺控制- 设计和实施合理的生产工艺流程,确保产品的一致性和稳定性。
- 建立严格的生产标准和操作规程,指导员工操作和控制质量。
- 定期监测和检测生产过程中的关键参数,如温度、压力和速度等。
4. 产品质量检验- 建立完善的产品质量检验流程,确保产品符合相关标准和规范。
- 使用先进的检测设备和技术,如金相显微镜和超声波探伤仪等。
- 进行全面的产品检验,包括外观检查、尺寸测量和性能测试等。
5. 不良品处理- 建立及时的不良品处理机制,包括分类、记录和追溯等。
- 分析不良品的原因,采取措施避免类似问题再次发生。
- 合理利用可回收材料,减少废品产生对环境的影响。
6. 质量管理体系- 建立和执行ISO 9001等质量管理体系,确保持续改进和客户满意度。
- 进行内部和外部的质量审核,识别潜在问题并及时纠正。
- 培养员工的质量意识和质量管理能力,推动全员参与质量控制和改进。
结论:大型钢铁生产质量控制措施是确保产品质量和安全的关键环节,企业应重视质量管理和持续改进。
本文介绍了一些常用的质量控制措施,但具体措施应根据企业的实际情况和需求进行调整和完善。
通过有效的质量控制,企业能够提高生产效率、降低成本,并获得竞争优势。
钢铁行业的创新案例新产品和解决方案

钢铁行业的创新案例新产品和解决方案钢铁行业的创新案例:新产品和解决方案钢铁行业一直是全球制造业的重要支柱,然而,在不断变化的市场环境下,钢铁企业面临着各种挑战。
为了应对市场需求的变化和环境问题的关注,钢铁行业积极推动创新,开发新产品和解决方案。
本文将介绍几个钢铁行业的创新案例,探讨其对行业发展的影响。
一、高强度钢的创新应用高强度钢具有优异的机械性能和轻量化的特点,受到汽车制造、建筑工程等领域的青睐。
一家钢铁企业在钢铁行业中率先推出了一种高强度钢,该钢能够满足汽车工程领域对材料强度和安全性的要求。
同时,该钢的轻量化特性还能减少车辆重量,提高燃油利用效率。
该高强度钢的应用,对于钢铁企业来说意味着新的市场机会。
它不仅满足了汽车制造业对材料强度和安全性的需求,还推动了钢铁企业的产能扩张和市场份额的增加。
此外,高强度钢在建筑工程领域的应用也得到了推广,为建筑领域的轻量化、高效性提供了解决方案。
二、绿色生产技术的应用随着环保意识的提高,钢铁行业也面临着压力,需要减少碳排放和对环境的影响。
为了实现绿色生产,一些钢铁企业采用了先进的环保技术,推动了行业的可持续发展。
例如,一家钢铁企业引入了炼铁过程中的废气循环利用技术,将废气转化为能源的一部分。
通过这种技术的应用,企业不仅降低了碳排放,还实现了能源的回收利用,提高了资源利用效率。
此外,该企业还改良了废水处理技术,将废水处理成可循环使用的水源,减少了对水资源的消耗。
这些绿色生产技术的应用为钢铁企业带来了多重好处。
首先,企业降低了环境风险和环保成本,提升了企业的社会形象。
其次,环保技术的应用也为企业带来了新的商机,满足了市场对绿色产品的需求。
三、数字化技术的创新应用随着信息技术的快速发展,数字化技术逐渐渗透到各个行业中,钢铁行业也不例外。
钢铁企业通过数字化技术的创新应用,实现了生产过程的高效管理和智能化控制。
一家钢铁企业引入了物联网技术,将生产设备和机器连接到互联网上,实现了实时监控和远程操作。
日本JFE公司开发和应用的中厚板制造技术介绍

日本JFE钢铁公司开始开发采用水淬火的热机械控制工艺(TMCP),作为高强度、高韧性,具有优良焊接性能钢板生产技术的核心技术。
下面简单介绍由JFE钢铁公司开发和应用的中厚板制造技术,包括超级-OLAC技术,一种新的中厚板加速冷却技术以及HOP技术(热处理在线工艺),一种加速冷却后的在线热处理工艺。
同时,下面还介绍Easyfab钢板制造技术,即通过应用具有新功能的冷矫直机将中厚板中残余应力降至零。
一、新加速冷却技术——“超级-OLAC”技术的开发与控制轧制技术一起,加速冷却技术是TMCP工艺的核心技术。
JFE钢铁公司是世界上首家开发并成功在中厚板生产中应用在线加速冷却技术的钢铁企业。
在上世纪90年代初,采用加速冷却技术制造的TMCP钢实现了提高钢板强度、改进焊接性能的目的,从而有助于焊接结构建筑用钢使用的合理化和提高建筑的安全性,并开始用于造船业。
然而,最近几年对钢板质量的要求日趋严格,如减少强度下降等。
为了满足新的要求,基于一个全新的概念,JFE钢铁公司进行了大量研究以获得解决与传统冷却技术问题相关的方案,并开发出新一代加速冷却工艺,称之为超级-OLAC工艺,并应用于JFE钢铁公司西日本钢厂。
当中厚板进行水淬火时出现的热传递和沸腾现象可以大致分为两种方式,即核胞沸腾和薄膜沸腾。
在前一种沸腾中,冷却水直接与钢接触,热量通过产生的泡传递。
相比之下,后一种沸腾中在钢与冷却水间形成一个蒸汽薄膜,热量是通过蒸汽薄膜传递。
核胞沸腾的冷却能力比薄膜沸腾更高。
在中厚板冷却开始时,中厚板表面温度较高,薄膜沸腾起主导作用。
然而,随着中厚板表面温度的下降,蒸汽薄膜变得不稳定,冷却水开始局部上直接与中厚板接触,沸腾逐渐转向核胞沸腾。
此外,在瞬时沸腾状态下,当薄膜沸腾和核胞沸腾共存时,随着冷却的继续,冷却能力提高。
采用传统冷却方法,如喷淋冷却和层流冷却时,如果冷却水流量提高以强化冷却,冷却迅速地转换成瞬时沸腾,是核胞沸腾和薄膜沸腾的混合。
首钢热轧双相钢DP580的热轧工艺与组织性能分析

S h o u g a n g 1 5 8 0 mm h o t r o l l i n g mi l 1 .T h e r e s u l t s s h o we d t h a t t h e r e a s o n a b l e d e s i g n o f i f n i s h r o l l i n g
三段式冷却模式 和低温 卷取 ,成 功实 现了在 1 5 8 0 mm机组上工业试生产 D P 5 8 0 。结果表 明,通过合理 的终 轧温度 、冷却速度 、中间温度和空冷 时间配合 ,D P 5 8 0可 获得 比例适 合 的铁素体 和马 氏体 双相 组织 ,力学
性能 满足设计要求 。
l o w— t e mp e r a t u r e c o i l i n g ,t h e h o t — r o l l e d d u a l p h a s e s t e e l D P 5 8 0 w a s s u c c e s s f u l l y p r o d u c e d b y
t e mp e r a t u r e ,c o o l i n g s p e e d,i n t e r me d i a t e h o l d i n g t e mp e r a t u r e a n d a i r c o o l i n g t i me we r e t h e k e y
高品质特殊钢技术开发的背景与目标_陈思联

58 600 超临界和超超临界机用钢材经十多年的运 行已经可以满足使用 要求, 正在研制 650 蒸汽 温度参数机组用耐热 钢, 预研 700 蒸汽温度参 数机组用耐热钢。 耐热钢的发展水平, 决定了不同时期的火电 机组运行参数, 在 20世纪 20 年代使用碳钢 , 蒸汽 压力 4 M Pa, 温度 370 。随着 M o 钢的出现 , 参 数提高到 10 M Pa 和 480 。直到 20 世纪 50 年 代 , 由于 Cr M o 钢的应用, 参数 提高到 17 M Pa 和 566 。 20 世纪 70 年代能源危机, 为了提高热效 率 , 使美、 日、 欧各国重新开始对高参数用钢的开 发 , 重点发展导热系数大, 热膨胀系数小的铁素体 型 ( 马氏体 ) 钢, 尤 其是 9 % ~ 12% C r 钢的研 究, 替代奥氏体钢。图 2 示出了 600 、 10 h 下耐热 钢持久强度发展的进程。
0 前言 特殊钢是重大装备制造和国家重点工程建设 所需的关键材料 , 是钢铁材料中的高技术含量产 品 , 其生产和应用代表了一个国家的工业化发展 水平。特殊钢占钢总量的比重、 特殊钢产品结构、 质量和应用等是反映一个国家钢铁工业发展水平 的重要标志。近年来 , 在我国社会和经济快速发 展的带动下 , 我国特殊钢生产和市场发展迅速 , 特 殊钢生产装备和工艺技术不断提高 , 特殊钢产量 和产品质量持续 提高, 市场满足程度不 断增长。 但是, 相比我国快速发展的普通钢行业, 我国特殊 钢行业技术发展速度还是慢一些 , 与国际先进水 平的差距也比普通钢行业大。 我国特殊钢板带材、 管材、 棒线材、 锻材、 线材 专业化生产线正在逐步形成, 拥有了较先进的特 殊钢生产装备。特殊钢技术不断发展 , 先进的特 殊钢冶炼和精炼工艺技术可以准确地将化学成分 控制在较窄的范围内, 特殊钢的凝固工艺技术可 以保证钢坯 ( 锭 ) 的化学成分和组织的高均匀度, 变形工艺技术能够满足钢材精确形状尺寸和组织 状态的控制要求 , 热处理工艺技术可以精确控制 钢材和部件的组织和性能。提高生产工艺技术水 平 , 可以改善特殊钢产品的纯净度、 化学成分控制 精确度、 组织均匀性、 性能的稳定性、 尺寸精度、 表 面质量、 包装质量等。 相比普通钢 , 特殊钢中的合金元素含量高 , 生 产工艺较复杂, 并且需要热处理 , 因此资源和能源 消耗相对较大。例如 , 我国铁素体不锈钢仅占不 锈钢总产量的 25 % 左右 (日本为 40 % , 各工业化 国家均有较大比重 ) , 以 C r- N i系奥氏体钢为主 要品种的我国不锈钢产业, 每年消耗大量的金属 镍资源 ; 我国需要研发满足高效率火电锅炉用耐
高性能金属功能材料表面质量及微观组织控制成形新技术
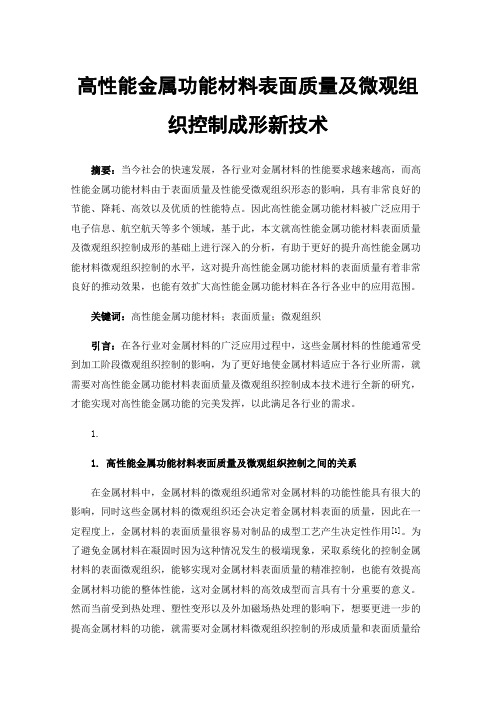
高性能金属功能材料表面质量及微观组织控制成形新技术摘要:当今社会的快速发展,各行业对金属材料的性能要求越来越高,而高性能金属功能材料由于表面质量及性能受微观组织形态的影响,具有非常良好的节能、降耗、高效以及优质的性能特点。
因此高性能金属功能材料被广泛应用于电子信息、航空航天等多个领域,基于此,本文就高性能金属功能材料表面质量及微观组织控制成形的基础上进行深入的分析,有助于更好的提升高性能金属功能材料微观组织控制的水平,这对提升高性能金属功能材料的表面质量有着非常良好的推动效果,也能有效扩大高性能金属功能材料在各行各业中的应用范围。
关键词:高性能金属功能材料;表面质量;微观组织引言:在各行业对金属材料的广泛应用过程中,这些金属材料的性能通常受到加工阶段微观组织控制的影响,为了更好地使金属材料适应于各行业所需,就需要对高性能金属功能材料表面质量及微观组织控制成本技术进行全新的研究,才能实现对高性能金属功能的完美发挥,以此满足各行业的需求。
1.1.高性能金属功能材料表面质量及微观组织控制之间的关系在金属材料中,金属材料的微观组织通常对金属材料的功能性能具有很大的影响,同时这些金属材料的微观组织还会决定着金属材料表面的质量,因此在一定程度上,金属材料的表面质量很容易对制品的成型工艺产生决定性作用[1]。
为了避免金属材料在凝固时因为这种情况发生的极端现象,采取系统化的控制金属材料的表面微观组织,能够实现对金属材料表面质量的精准控制,也能有效提高金属材料功能的整体性能,这对金属材料的高效成型而言具有十分重要的意义。
然而当前受到热处理、塑性变形以及外加磁场热处理的影响下,想要更进一步的提高金属材料的功能,就需要对金属材料微观组织控制的形成质量和表面质量给予不断的成型技术创新支持,才能有效促使高性能金属功能材料在各行业中的应用。
2.高性能金属功能材料微观组织控制成像的全新技术要求2.1外加磁场热处理在高性能金属功能材料微观组织控制成像的技术中,外加磁场热处理组织的控制方式需要借助超导材料的方式,从而获取强大的磁场所需。
钢铁品种开发方案
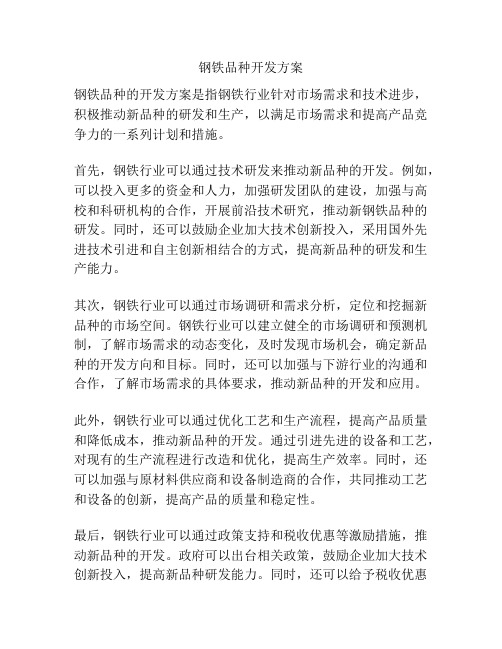
钢铁品种开发方案
钢铁品种的开发方案是指钢铁行业针对市场需求和技术进步,积极推动新品种的研发和生产,以满足市场需求和提高产品竞争力的一系列计划和措施。
首先,钢铁行业可以通过技术研发来推动新品种的开发。
例如,可以投入更多的资金和人力,加强研发团队的建设,加强与高校和科研机构的合作,开展前沿技术研究,推动新钢铁品种的研发。
同时,还可以鼓励企业加大技术创新投入,采用国外先进技术引进和自主创新相结合的方式,提高新品种的研发和生产能力。
其次,钢铁行业可以通过市场调研和需求分析,定位和挖掘新品种的市场空间。
钢铁行业可以建立健全的市场调研和预测机制,了解市场需求的动态变化,及时发现市场机会,确定新品种的开发方向和目标。
同时,还可以加强与下游行业的沟通和合作,了解市场需求的具体要求,推动新品种的开发和应用。
此外,钢铁行业可以通过优化工艺和生产流程,提高产品质量和降低成本,推动新品种的开发。
通过引进先进的设备和工艺,对现有的生产流程进行改造和优化,提高生产效率。
同时,还可以加强与原材料供应商和设备制造商的合作,共同推动工艺和设备的创新,提高产品的质量和稳定性。
最后,钢铁行业可以通过政策支持和税收优惠等激励措施,推动新品种的开发。
政府可以出台相关政策,鼓励企业加大技术创新投入,提高新品种研发能力。
同时,还可以给予税收优惠
和财务支持,降低企业的研发成本和经营风险,促进新品种的开发和推广。
总之,钢铁行业开发新品种是提高产品竞争力和满足市场需求的重要举措。
通过加大技术研发力度,深入挖掘市场需求,优化工艺流程,政策支持和激励措施,可以推动新品种的开发和推广,促进钢铁行业的发展。
- 1、下载文档前请自行甄别文档内容的完整性,平台不提供额外的编辑、内容补充、找答案等附加服务。
- 2、"仅部分预览"的文档,不可在线预览部分如存在完整性等问题,可反馈申请退款(可完整预览的文档不适用该条件!)。
- 3、如文档侵犯您的权益,请联系客服反馈,我们会尽快为您处理(人工客服工作时间:9:00-18:30)。
各大钢厂高性能钢材组织性能控制与品种开发近年来,通过加强对碳锰钢、微合金钢及合金钢在轧制与冷却过程中的晶粒细化、析出与相变等的组织性能控制的基础与应用研究,在细晶高强钢、高级管线钢、高性能中厚板及特厚板、取向硅钢及先进汽车板等高性能冷轧带钢、新型铁素体不锈钢及双相不锈钢、高性能长材及管材等的工艺控制技术与产品开发方面取得了一大批重要成果,为轧制钢材的品质提升和国家经济建设作出了重大贡献。
1轧制过程组织性能控制研究及应用1.1细晶和超细晶钢的研究开发及应用近年的“新一代钢铁材料重大基础研究”项目以细晶和超细晶钢的研究开发为目标,该项目通过结合轧制生产线装备和工艺实际,开展了大量的理论和试验研究与探索,其中包括:①铁素体+珠光体(F+P)碳素钢或低合金钢采用强力轧制、形变诱导铁素体相变(DIFT)以及形变和相变耦合的组织超细化理论和技术;②结合奥氏体再结晶和未再结晶控制轧制和加速冷却(RCR+ACC)控制的晶粒适度细化理论和技术;③基于过冷奥氏体热变形的低碳钢组织细化一形变强化相变(DEFT)理论和技术;④基于薄板坯连铸连轧流程(TSCR)的奥氏体再结晶细化+冷却路径控制的低碳钢组织细化与强化理论与技术;⑤针对低(超低)碳微合金贝氏体钢的中温转变组织细化的TMCP+RPC理论与技术等。
这些理论与技术研究在长材、板带材和中厚板的强度翻番或升级,以及新产品开发中发挥重大的作用和显著的效果,近年已大批量地生产出细晶和超细晶钢。
1.2钢在形变、相变中的析出行为研究与控制钢在形变、相变中的析出行为研究与控制是钢的组织性能控制的一个重要方面。
通过大量的试验研究和生产实践证明,采用合理的冶金成分设计和轧制、冷却工艺控制,可以在钢中使大量的纳米尺寸粒子析出,使钢的强韧性得到显著提高。
珠钢及涟钢等企业同高校合作,在TSCR线上通过实施高温大变形再结晶细化+冷却路径控制,实现晶粒细化与纳米粒子析出与分布控制,进而形成不同强韧化效果的组织性能柔性控制,开发生产出具有高成形性的低碳高强汽车大梁钢510L、550L、屈服强度500MPa~700MPa级钛微合金化高强耐候钢、600MPa和700MPa级低碳贝氏体工程机械用钢等系列高强韧钢,并进行了大批量生产和应用。
经分析,微合金化高强钢中纳米粒子析出强化的贡献可达到150MPa~300MPa。
2 2250热连轧生产高级别管线钢的技术开发中国近年先后投产的11套2000mm 以上宽带钢热连轧生产线为高级别管线钢等高性能高强钢产品开发提供了关键设备条件。
2007年以来,首钢、太钢、马钢等钢铁企业利用2250热连轧生产线成功开发并大批量生产出18.4mm厚X80高级别管线钢。
采用低C-高Mn-高Nb-少Mo-微V,或低C-高Mn-高Nb+适量Cr-Ni-Mo-Cu的成分体系设计,结合优化的TMCP 轧制工艺和低温或超低温卷取控制,获得以针状铁素体为主的高级管线钢复相组织,确保了厚规格产品的高强韧性和耐蚀性,保证了带钢全长组织性能的均匀性及良好的板形。
2008年,首钢、太钢、马钢的2250热连轧生产线共生产了73.5万t X80管线钢,在中国的西气东输二线管线工程建设中发挥了关键作用。
3高性能高强度中厚板品种开发3.1新型桥梁用钢的开发及应用近年,武钢、鞍钢等企业采用TMCP技术开发了满足高强度、较低屈强比、焊接性、耐候性及低温冲击韧性要求的系列新型桥梁用钢,并应用于南京大胜关长江大桥等几十座跨江、跨海、铁路和公路桥梁建设。
武钢开发生产的WNQ570、WNQ690、14MnNbq桥梁钢的特点是:高强度,屈服强度大于等于420MPa;高韧性,-40℃Akv≥120J;良好焊接性,60mm以上厚钢板埋弧焊不预热;耐候性,WNQ570钢与09CuPCrNi相当;最大板厚68mmWNQ570钢12mm~68mm不区分板厚效应;屈强比小于等于0.88。
京沪高速铁路南京大胜关长江大桥建造采用了WNQ570钢1.3万t,应用于打捞“南海一号”的亚洲最大的起重工程船悬臂梁采用了WNQ690钢制造。
鞍钢将FH550级TMCP超高强船板制造技术成功用于80mm厚高强度桥梁钢Q420qE、Q500qE制造,其主要特点是:①通过超低碳微合金化成分设计(0.045%C-Mn-Mo-Nb-0.75%Cu-Ni),实现特厚板连续冷却组织均匀并提高耐大气腐蚀性能,增加钢板的低温韧性;②全均质贝氏体钢组织有利于提高耐大气腐蚀性能;超高强度船板FH500、FH550的耐大气腐蚀性能优于传统耐候钢09CuPCrNi,应用于桥梁钢,使厚规格桥梁钢具有耐大气腐蚀性能;③Cu在连续冷却和等温过程中纳米析出的控制能够强化特厚超高强桥梁板的芯部性能;80mm厚FH550钢板近表面组织为细化的板条贝氏体、粒状贝氏体和针状铁素体,1/4和1/2厚度处组织为准多边形铁素体和针状铁素体,强韧性满足要求;④通过TMCP轧制工艺调控,使原奥氏体晶粒尺寸细化到20μm~50μm;通过3阶段TMCP轧制工艺,实现了特厚桥梁板原奥氏体晶粒细化,进一步保证了1/2厚度处的强韧性要求。
3.2高强韧低碳贝氏体非调质钢开发结合鞍钢2300中板机组和4300厚板机组的特点,采用超低碳贝氏体钢成分设计(加入提高淬透性和析出强化元素Mn、Cu、Ni、Mo、Nb、B等)和中温组织超细化技术(TMCP+RPC 技术),获得各种形态的超细贝氏体组织,生产出屈服强度500MPa、550MPa、620MPa、690MPa和800MPa 5个强度级别超低碳贝氏体钢中厚板,板材厚度为16mm~60mm。
主要应用于工程机械和煤机等领域,工艺路线为:超低碳-洁净钢质-微合金化-控制轧制-控制冷却(中温转变组织超细化)-(厚板回火)。
使高性能钢由调质处理向不调质、不回火、降低贵重合金元素使用量方向发展。
所开发的高强韧超细组织低碳贝氏体钢的系列产品分别销售到北京煤机厂和郑州煤机厂、四川长江起重机公司等工程机械用户。
3.3大厚度大单重优质特厚钢板技术开发舞钢开发的屈服强度390MPa~460MPa(Q390~Q460)级高层建筑结构钢先后应用于国家游泳中心、国家体育场鸟巢等奥运工程以及中央电视台新台址、国家大剧院工程等大型建筑工程。
①Q390~Q460厚板的主要技术指标特点:成品板最大厚度达到135mm,晶粒细化、组织均匀性高;-40℃低温韧性远高于标准值,最大厚度135mm时的冲击值富裕量较大;Z35抗层状撕裂性能均超过了35%,保证安全性能;低碳当量(Ceq=0.44%~0.48%)保证焊接性能;低屈强比(Rp0.2/Rm≤0.80)保证抗震性。
②特厚板生产工艺技术的主要特点:独特的微合金化成分设计及洁净钢冶炼保证了大厚度钢板的内部质量、各项力学性能及焊接性能;特有的大钢锭无缺陷浇铸工艺保证了110mm厚Q460E-Z35的成功开发;正火轧制和控制冷却并用,保证了钢板的抗震性能;独特的热处理设备(常化+控冷)突破了原有设备的厚度热处理极限。
③舞钢生产特厚板的主要装备及产品特点(见图1和表1)。
在国家体育场鸟巢和中央电视台新台址的结构建设中大量采用了舞钢开发生产的Q390~Q460级特厚高强钢板。
3.4高强、超高强船体及海洋工程结构用钢系列产品开发鞍钢采用TMCP技术开发生产出具有Z15~Z35性能的高强度、超高强度系列船体及海洋工程结构用钢,表2为鞍钢船板钢的产品牌号及规格等主要指标。
到2009年,鞍钢已累计生产了各类船板1000多万t。
鞍钢船板TMCP技术集成主要包括:成分设计,复合微合金化;冶炼,转炉纯净钢冶炼、炉外精炼、高精度目标成分控制、夹杂物形态控制;连铸,板坯成分均匀化控制、降低板坯中心偏析、300mm厚无缺陷连铸板坯控制技术等;轧制,板坯加热温度控制、TMCP轧制工艺(4300厚板生产线)、钢板厚度及板形高精度控制、加速冷却技术等。
4.1取向硅钢制造技术与品种开发1)武钢取向硅钢制造技术与品种开发武钢已形成了取向硅钢的冶炼、连铸、热轧、冷轧及热处理等工艺与质量控制技术,实现了取向硅钢制造技术的工程化与产业化,主要技术进步包括:复吹工艺等技术,使取向硅钢冶炼成分命中率达到98%以上;连铸技术,建立一套完整的取向硅钢连铸工艺,提高了生产效率和铸坯质量;热轧技术,重点是加热炉温度制度和辊形制度,解决了炉内断坯、粗轧带坯断裂、精轧边裂断带事故,使每边热轧板边裂减少到5mm~20mm,成材率提高3.5%;硅钢厂酸洗线HiB常化炉改造及工艺,有效控制了AlN等抑制剂的合适尺寸及分布,提高了HiB钢的牌号合格率5%以上;森吉米尔轧机HGO钢高温轧制技术,研究出了HGO钢高温轧制的典型工艺,基本全部实现高温轧制,提高了HGO钢的牌号合格率5%以上;冷轧工艺,提出改进轧制规程和提高生产率的方法;串联式退火脱碳工艺,发明了中间完全脱碳退火技术、成品厚度钢板初次再结晶、脱碳退火技术及改善取向硅钢涂层质量的工艺技术等。
2007年,武钢取向硅钢产量达27万t,牌号几乎覆盖所有级别,产品性能与质量达到国际先进水平,产品用于三峡工程、青藏铁路工程、神六载人飞船工程等国家重要工程项目。
武钢取向硅钢在市场占有率由2003年的29.9%提高到2007年的52%,到2010年武钢取向硅钢的产量将达到50万t。
2)宝钢取向硅钢制造技术与品种开发。
宝钢历时10年自主研发取向硅钢技术,自主集成生产线,成功实现高品质取向硅钢产品批量生产。
2008年~2009年,宝钢普通取向硅钢(CGO)、高磁感取向硅钢(NSGO)、薄规格(0.27mm以下)激光刻痕取向硅钢等高等级取向硅钢产品投产。
目前,宝钢已经具备20余个取向硅钢牌号的批量生产能力,典型牌号如表3所示。
宝钢取向硅钢产品的主要关键技术如下:a)品种开发:开发出采用低温板坯加热技术的高磁感、低铁损取向硅钢。
b)炼钢工序:成分高精度控制技术,关键元素含量按10 级控制。
c)热轧工序:低温板坯加热技术;低温降控制技术;带钢边裂控制、高精度厚度及板形控制技术;采用适应硅钢生产的板坯异步装炉与交叉轧制技术,建立适应交叉轧制的高精度控制模型等。
d)冷轧工序:高精度板形控制技术;渗氮控制技术、高精度炉温控制技术。
e)激光刻痕技术:在涂敷绝缘涂层的取向硅钢板表面,采用激光器对硅钢板进行刻蚀,细化磁畴,降低硅钢片的铁损。
宝钢取向硅钢产品已成功应用于500kV、48万kV A及以上电压等级大型交流变压器和直流换流变压器制造,高磁感产品已供应30家大中型变压器厂。
4.2冷轧高品质汽车板技术进步近年来,宝钢、鞍钢、武钢等大型钢铁企业为满足快速增长的汽车发展需求,开发生产出冷轧深冲及超深冲系列、镀层系列、高强及超高强系列汽车板。