轴承磨工工艺学99页PPT
合集下载
磨削加工工艺过程与主要工序 PPT课件
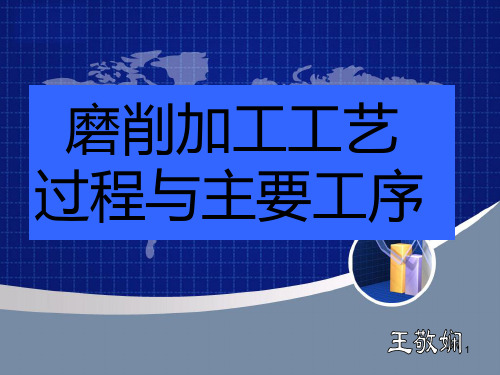
效果。但对于不对称磨削即两端面磨削面积
不相等(如圆锥滚子轴承的套圈)的情况来
说,则必须使磨大端面的砂轮转速高于磨小
端面的砂轮转速,才能实现两端面的磨削量
相等。一般选择磨大端面的砂轮转速与小端
面的砂轮转速之比为1-4(当比值为1时,即
为对称磨削)。
7
(2)立轴平面磨削 立轴平面磨削主要采用立轴圆台平面磨床, 属于单面磨削,对于套圈两个端面,需要 两次定位,两次磨削。由于砂轮回转平面 与工作面不平行、磁台不平、磁力吸紧变 形以及其他因素(比如残磁影响等)而产 生的加工误差会累计叠加,因而套圈宽度 变动量一般较大。磨削套圈时,一般分为 两个工步:先磨非基准面,后磨基准面, 以保证后续加工工序具有良好的工艺基准。
4、磨沟(滚)道
内圈沟(滚)道一般采用的定位与磨削方式为 “支沟(滚)道磨沟(滚)道”,由于支承面和磨10
相同,没有支承面形状误差的影响,所以加工 精度较高。外圈滚道一般采用“支外径磨沟 (滚)道”,由于将外径面作为支承面,其形 状误差会不同程度地反映到沟(滚)道上来, 称为误差复映,因此加工精度受到一定影响。 5、磨挡边
3、磨内径
与外圈外径面一样,内圈(轴圈)内径面也是轴 承的安装配合基准,而且由于主机使用中对其配合 性质(通常为过盈配合或过渡配合)和工作性能 (通常内圈旋转)的要求,对内圈内径面的尺寸与 形位公差,一般均较外圈外径面更为严格。
内圈内径磨削大都采用电磁无心夹具,由于是 用经过磨削或研磨的外圆定位磨削内圆,因此内、 外圆的同心(轴)度较高,加工误差很小。
14
15
三.、轴承套圈的磨加工技术要求
(1)尺寸偏差:主要是外径、内径、外沟 道(滚道)直径,内沟(滚)道直径尺寸 偏差、套圈高度尺寸偏差。
轴承基本知识演示幻灯片
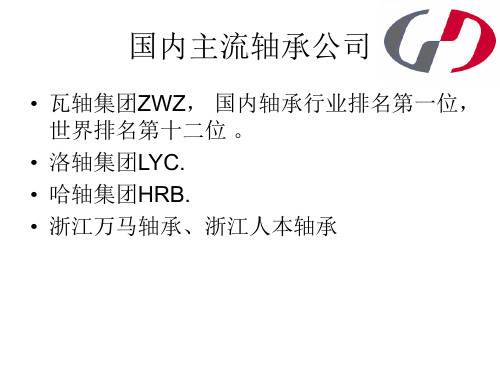
国内主流轴承公司
• 瓦轴集团ZWZ, 国内轴承行业排名第一位, 世界排名第十二位 。
• 洛轴集团LYC. • 哈轴集团HRB. • 浙江万马轴承、浙江人本轴承
一 SKF公司简介
Nearly 100 years of technology progress and innovations 将近百年的技术发展和创新的历史
自动调心球轴承
• 是所有轴承类型中摩擦最低的。具有很好 的调心能力。外圈滚道为球面,可以承受 内外圈之间的角度误差。
自动调心球轴承 受力分析
• 可以承受轻至中等的径向负荷和极轻的轴 向负荷。
自动调心球轴承安装
自动调心球轴承 前、后缀
前缀
后缀 2Z 2RS1 TN9 M MA C3 K K30 E
SKF的五个工程技术平台-润滑系统
SKF的五个工程技术平台-机电一体化产品
SKF的五个工程技术平台-服务
SKF平台
传动产品
轴承的作用
• 减少摩擦 • 承载负荷 • 引导运动
轴承的发展
滑动摩擦
加入滚动体
加入硬化的内圈 和外圈、保持架
轴承的组成
一般的滚动轴承是由内圈、外圈、滚 动体和保持架而组成。某些轴承可根据应用 的需要而配上密封或防尘盖。
单列深沟球轴承
• 单列深沟球轴承设计简单,不可分离,适 用于高转速和,
• 并且非常耐用,无需经常维护。
带密封的深沟球
深沟球轴承中最常用的尺寸,还提供一侧或两侧带防尘盖 或接触密封件的密封型轴承。
➢两侧装有防尘盖或密封件的轴承为终身润滑的免维护产品。 ➢此类轴承不能清洗,温度也不能超过摄氏80度。 ➢油脂的充填量为轴承内自由空间的25%至35%。 ➢带防尘盖轴承主要用于内圈旋转的应用。如果外圈旋转,在高速应用 条件下有漏脂的危险。 ➢标准密封件使用带钢骨架的丁腈橡胶(NBR)制造。这类密封件的允 许运行温度为摄氏零下40至零上100度,短时间内可高达摄氏120度。
• 瓦轴集团ZWZ, 国内轴承行业排名第一位, 世界排名第十二位 。
• 洛轴集团LYC. • 哈轴集团HRB. • 浙江万马轴承、浙江人本轴承
一 SKF公司简介
Nearly 100 years of technology progress and innovations 将近百年的技术发展和创新的历史
自动调心球轴承
• 是所有轴承类型中摩擦最低的。具有很好 的调心能力。外圈滚道为球面,可以承受 内外圈之间的角度误差。
自动调心球轴承 受力分析
• 可以承受轻至中等的径向负荷和极轻的轴 向负荷。
自动调心球轴承安装
自动调心球轴承 前、后缀
前缀
后缀 2Z 2RS1 TN9 M MA C3 K K30 E
SKF的五个工程技术平台-润滑系统
SKF的五个工程技术平台-机电一体化产品
SKF的五个工程技术平台-服务
SKF平台
传动产品
轴承的作用
• 减少摩擦 • 承载负荷 • 引导运动
轴承的发展
滑动摩擦
加入滚动体
加入硬化的内圈 和外圈、保持架
轴承的组成
一般的滚动轴承是由内圈、外圈、滚 动体和保持架而组成。某些轴承可根据应用 的需要而配上密封或防尘盖。
单列深沟球轴承
• 单列深沟球轴承设计简单,不可分离,适 用于高转速和,
• 并且非常耐用,无需经常维护。
带密封的深沟球
深沟球轴承中最常用的尺寸,还提供一侧或两侧带防尘盖 或接触密封件的密封型轴承。
➢两侧装有防尘盖或密封件的轴承为终身润滑的免维护产品。 ➢此类轴承不能清洗,温度也不能超过摄氏80度。 ➢油脂的充填量为轴承内自由空间的25%至35%。 ➢带防尘盖轴承主要用于内圈旋转的应用。如果外圈旋转,在高速应用 条件下有漏脂的危险。 ➢标准密封件使用带钢骨架的丁腈橡胶(NBR)制造。这类密封件的允 许运行温度为摄氏零下40至零上100度,短时间内可高达摄氏120度。
轴承加工工艺流程教材(共 37张PPT)

加工成品角时需注意的事项
• 及时修磨刀具,保持刀具的锋利程度,以增
•
•
加其表面光洁度及减少毛刺 适当提高主轴旋转速度,确保主轴旋转精度 及刚性 严格控制导轨与拖板间隙,以减少毛刺边的 产生
车加工的主要报废品及产生原因
直径变动量超差Байду номын сангаас原因:
1、套圈毛坯装夹表面直径变动量大,夹料时 产生弹性变形 2、夹具调心性不好,使夹具与工件的接触点 减少 3、毛坯壁厚变动量过大,使切削不均匀 4、主轴径向摆动过大 5、夹紧力过大
测量内径示意图
3、宽度
定义:套圈两端面之间的距离 测量内容:宽度尺寸、平面度、平行差、表面
粗糙度 测量工具:G903、标准件、百分表、刀口尺 测量方法:(见下图)
测量宽度示意图
软磨端面
加工设备:MZ7650双端面磨床 产生报废主要原因: 1、宽度变动量过大 2、平面度不好,表面有凹凸现象 3、产品烧伤 (前两项指标是磨削加工中常见报废产生的 主要因素,也是后序加工中定位不好的主 要原因,因此必须严格控制)
密封槽
• 密封槽的车加工是成品轴承的最终工序, 其质量的好坏直接影响轴承的装配,它 的要求项目比较复杂,不同的客户有不 同的要求,因此,密封槽加工应当作为 车加工的重要项目来控制。必须掌握正 确的检测手段和检测方式。由于密封槽 无法返工,因此要合理利用资源,将调 节过程尽量缩短,减少产品报废数量。
形位公差分为形状公差和位置公差 注:形状公差是指实际单一要素的形状所允许的变动量 位置公差是指实际关联要素的位置对基准所允许的 变动量
各工序检查部位及项目
检验部位 外 径 内 径 宽 度 沟 道 密封槽 挡 边 标识槽 检查项目 外径尺寸、圆度、锥度、壁厚差、表面粗糙度 内径尺寸、圆度、锥度、壁厚差、垂直度 宽度尺寸、平面度、平行度、表面粗糙度 沟径、沟曲率、沟位、侧摆、圆度、壁厚差 口径、底径、中宽、槽形、圆度、壁厚差 直径、挡边宽度、圆度、壁厚差 槽直径、全槽宽、槽位置、圆度、壁厚差 备注 1 2 3 4 5 6 7
模板轴承制造工艺流程.ppt

9
油 孔 油孔直径、油孔位置
10 缺 口 缺口弧半径、缺口最大直径、缺口角度
11
成品角 角圆弧R、轴向/径精向心整尺理寸、轴向/径向装配角
备注
精心整理
练习
精心整理
精心整理
1、外径
定义:包含外表面的圆柱体的理论直径 测量内容:外径尺寸、圆度、锥度、垂直
差、壁厚差、表面粗糙度。 测量工具:D913、标准件、百分表。 测量方法方法
沟曲率过大或者过小,主要是由刀具原因, 应采取重磨或修磨加以调整 沟径超差,可调整进刀量加以解决 沟位不好,可调整拖板以达到加工要求 侧摆超差,可采取调整工装夹具加以解决 圆度、壁厚差不好,可调整工装夹具、主轴 精度予以解决
精心整理
沟道振纹产生的原因及解决方法
精心整理
精心整理
轴承加工中常见形位公差分类及表示符号
形位公差分为形状公差和位置公差 注:形状公差是指实际单一要素的形状所允许的变动量 位置公差是指实际关联要素的位置对基准所允许的 变动量
精心整理
各工序检查部位及项目
序号 检验部位
检查项目
1
外 径 外径尺寸、圆度、锥度、壁厚差、表面粗糙度
2
产生原因: 1、进给量太大 2、刀具锋利程度不够 3、刀具装夹不牢固 4、机床刚性或者旋转精度不够
解决办法: 1、合理安排进给量 2、改变刀具的锋利风度(修磨或者更换) 3、保持刀具装夹的牢固性 4、增加机床的刚性或主轴的旋转精度
精心整理
沟道刀具的安装
车刀不能伸出刀具太长,防止振纹产生或者崩刀 车刀刀尖与工件中心等高,或者车外圈时,允许
▪ 密封槽形状一般由刀具本身确定,因此刀 具质量是保证产品质量的前提,使用者必 须正确刃磨、安装并及时修磨,保证刀具 的锋利状态,密封槽刀具一般有圆片刀、 成型刀、线切割刀机加刀片等,但主要采 用成型刀为主。磨刀时主要磨前刀面和刃 刀面,刃倾角的大小会影响密封槽的形状 和角度。
轴承制造工艺流程(PPT37页)

1、外径变动量过大 2、圆度误差过大 3、垂直差过大 4、锥度过大或过小 5、外径磨伤
2、内径
定义:包含圆柱孔内表面的圆柱体的理论直径 测量内容:内径尺寸、圆度、锥度、壁厚差、
垂直度 测量工具:D923、标准件、百分表 测量方法:(见下图)
测量内径示意图
3、宽度
▪ 定义:套圈两端面之间的距离 ▪ 测量内容:宽度尺寸、平面度、平行差、表面
沟道振纹产生的原因及解决方法
产生原因: 1、进给量太大 2、刀具锋利程度不够 3、刀具装夹不牢固 4、机床刚性或者旋转精度不够
解决办法: 1、合理安排进给量 2、改变刀具的锋利风度(修磨或者更换) 3、保持刀具装夹的牢固性 4、增加机床的刚性或主轴的旋转精度
沟道刀具的安装
车刀不能伸出刀具太长,防止振纹产生或者崩刀 车刀刀尖与工件中心等高,或者车外圈时,允许
5、密封槽
测量内容:口径、底径、中宽、槽形、 圆度、壁厚差、平行差
测量工具:自制表座、标准件、千分尺、 百分表、形状测量仪
测量方法:(见下图)
密封槽宽度的测量方法
密封槽宽度测量方法有测量中宽和测量单边两种 方式,无优劣之分,只是根据情况采用不同的测 量途径
不合格分析: 1、中宽、单边过大,说明密封槽宽度偏窄,应增 加大拖板的轴向进给量以增加槽宽 2、中宽、单边过小,说明密封槽宽度偏宽,应减 小大拖板的轴向进给量以增加槽宽
密封槽振纹产生的原因及解决方法
产生原因: 1、进给量太大 2、刀具锋利程度不够 3、刀具装夹不牢固 4、机床刚性或者旋转精度不够
解决办法: 1、合理安排进给量 2、改变刀具的锋利风度(修磨或者更换) 3、保持刀具装夹的牢固性 4、增加机床的刚性或主轴的旋转精度
密封槽车刀的种类及修磨
2、内径
定义:包含圆柱孔内表面的圆柱体的理论直径 测量内容:内径尺寸、圆度、锥度、壁厚差、
垂直度 测量工具:D923、标准件、百分表 测量方法:(见下图)
测量内径示意图
3、宽度
▪ 定义:套圈两端面之间的距离 ▪ 测量内容:宽度尺寸、平面度、平行差、表面
沟道振纹产生的原因及解决方法
产生原因: 1、进给量太大 2、刀具锋利程度不够 3、刀具装夹不牢固 4、机床刚性或者旋转精度不够
解决办法: 1、合理安排进给量 2、改变刀具的锋利风度(修磨或者更换) 3、保持刀具装夹的牢固性 4、增加机床的刚性或主轴的旋转精度
沟道刀具的安装
车刀不能伸出刀具太长,防止振纹产生或者崩刀 车刀刀尖与工件中心等高,或者车外圈时,允许
5、密封槽
测量内容:口径、底径、中宽、槽形、 圆度、壁厚差、平行差
测量工具:自制表座、标准件、千分尺、 百分表、形状测量仪
测量方法:(见下图)
密封槽宽度的测量方法
密封槽宽度测量方法有测量中宽和测量单边两种 方式,无优劣之分,只是根据情况采用不同的测 量途径
不合格分析: 1、中宽、单边过大,说明密封槽宽度偏窄,应增 加大拖板的轴向进给量以增加槽宽 2、中宽、单边过小,说明密封槽宽度偏宽,应减 小大拖板的轴向进给量以增加槽宽
密封槽振纹产生的原因及解决方法
产生原因: 1、进给量太大 2、刀具锋利程度不够 3、刀具装夹不牢固 4、机床刚性或者旋转精度不够
解决办法: 1、合理安排进给量 2、改变刀具的锋利风度(修磨或者更换) 3、保持刀具装夹的牢固性 4、增加机床的刚性或主轴的旋转精度
密封槽车刀的种类及修磨
最新滚动轴承磨加工工艺流程与过程控制学习课件.ppt

砂轮、油石
砂轮 砂轮的基本特性和分类 砂轮的选用 砂轮好坏的辨别 油石 油石的基本我和分类 油石的选用 油石好坏的辨别
精品
精品
无心工序
外圆磨质量问题
尺寸:可能引起的原因有1、导轮不圆、2、导轮旋转时有 跳动 3、磨削轮磨钝4、磨削轮轴振动
圆度:椭圆度、棱圆度1、工件中心高不合适、斜角过大、 磨削余量过大、磨削轮不平衡等
振纹:磨削轮不平衡、磨削轮磨钝、托板太薄或斜角过大、 工件中心过高等
粗糙度:磨粒太粗或金刚石笔磨钝、导板位置没有调好、 工件纵向速度太快、导轮速度过高。0.32um
圆度(椭圆度、棱圆度)支承偏心量未调、支承磨损严重或角度不对、 工件轴砂轮轴跳动精度不高
烧伤:冷却液变质或冷却不充足、进给量分配不均、进给速度太大、 金刚石笔太钝、砂轮太硬、磁力不足、工件转速过低等
粗糙度差:磨削速度太快、光磨时间太短、靠山磨损、、工件转速过 高、修整器速度过快、金刚石笔太钝、砂轮过软等
A
磨 内 径
磨
小
沟
T
精品
工艺流程与过程控制
A
磨 内 径
磨
小
沟
T
精品
超精工序
砂轮花:超精深度不够、(超精时间太短、油石太硬、 压力不够、中心太高、参数设置不匹配、等)油石摆 角太小、油石宽度太窄(沟边)、油石粘铁、
划伤:油石粘铁、切削液太脏有杂质、油石压力太大 油石磨粒太小不均 、材料有夹杂物。油石包角过大 切屑磨粒排不出引起的划伤
由自己去总结,烧伤是砂轮选择不当、进给量 不均匀切削液不足或变质等
端面工序对下工序的影响
精品
工艺流程与过程控制
A
磨 内 径
轴承加工工艺流程PPT课件
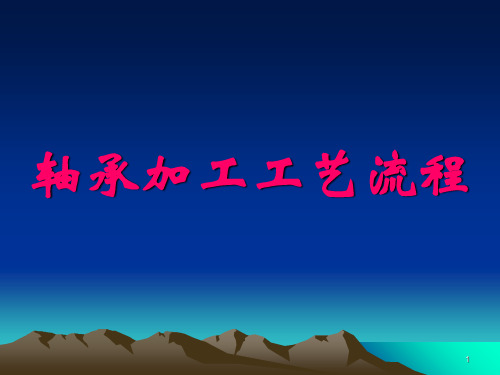
26
沟曲率的检测方式及确定方法
沟曲率用刮色球刮色判定,当小范刮色时 沟道底部白两边红,当大范刮色时底部红 两边白。则判定为沟曲率合格,反之就判 定为不合格。 若大范刮色时底部呈白色,则表示沟曲率 过大; 若小范刮色时两边呈白色,则表示沟曲率 偏小。
27
沟道加工中易出现的废品及解决方法
沟曲率过大或者过小,主要是由刀具原因, 应采取重磨或修磨加以调整 沟径超差,可调整进刀量加以解决 沟位不好,可调整拖板以达到加工要求 侧摆超差,可采取调整工装夹具加以解决 圆度、壁厚差不好,可调整工装夹具、主轴 精度予以解决
注释:形状公差是指实际单一的形状所允许的变动量 位置公差是指实际关联要素的位置对基准所允许的变动量
11
各工序检查部位及项目
序号 检验部位
检查项目
备注
1
外 径 外径尺寸、圆度、锥度、壁厚差、表面粗糙度
2
内 径 内径尺寸、圆度、锥度、壁厚差、垂直度
3
宽 度 宽度尺寸、平面度、平行度、表面粗糙度
4
沟 道 沟径、沟曲率、沟位、侧摆、圆度、壁厚差
轴承加工工艺流程
1
2
轴承的组成元素
轴承内部一般由外圈、内圈、滚动体和保 持架组成------通常称为四大件
对于密封轴承,再加上润滑剂和密封圈 (或防尘盖)------又称为六大件
3
成品轴承
4
轴承结构
(深沟球轴承)
密封件 外圈
滚动元件 保持架
内圈 密封件
5
6
7
基本工序的基本参数
外径:包含外径尺寸、圆度、锥度、垂直差、壁厚差、表 面粗糙度
9
轴承加工中常见形位公差分类及表示符号
形位公差分为形状公差和位置公差 注:形状公差是指实际单一要素的形状所允许的变动量 位置公差是指实际关联要素的位置对基准所允许的 变动量
沟曲率的检测方式及确定方法
沟曲率用刮色球刮色判定,当小范刮色时 沟道底部白两边红,当大范刮色时底部红 两边白。则判定为沟曲率合格,反之就判 定为不合格。 若大范刮色时底部呈白色,则表示沟曲率 过大; 若小范刮色时两边呈白色,则表示沟曲率 偏小。
27
沟道加工中易出现的废品及解决方法
沟曲率过大或者过小,主要是由刀具原因, 应采取重磨或修磨加以调整 沟径超差,可调整进刀量加以解决 沟位不好,可调整拖板以达到加工要求 侧摆超差,可采取调整工装夹具加以解决 圆度、壁厚差不好,可调整工装夹具、主轴 精度予以解决
注释:形状公差是指实际单一的形状所允许的变动量 位置公差是指实际关联要素的位置对基准所允许的变动量
11
各工序检查部位及项目
序号 检验部位
检查项目
备注
1
外 径 外径尺寸、圆度、锥度、壁厚差、表面粗糙度
2
内 径 内径尺寸、圆度、锥度、壁厚差、垂直度
3
宽 度 宽度尺寸、平面度、平行度、表面粗糙度
4
沟 道 沟径、沟曲率、沟位、侧摆、圆度、壁厚差
轴承加工工艺流程
1
2
轴承的组成元素
轴承内部一般由外圈、内圈、滚动体和保 持架组成------通常称为四大件
对于密封轴承,再加上润滑剂和密封圈 (或防尘盖)------又称为六大件
3
成品轴承
4
轴承结构
(深沟球轴承)
密封件 外圈
滚动元件 保持架
内圈 密封件
5
6
7
基本工序的基本参数
外径:包含外径尺寸、圆度、锥度、垂直差、壁厚差、表 面粗糙度
9
轴承加工中常见形位公差分类及表示符号
形位公差分为形状公差和位置公差 注:形状公差是指实际单一要素的形状所允许的变动量 位置公差是指实际关联要素的位置对基准所允许的 变动量
轴承加工工艺流程教材.pptx
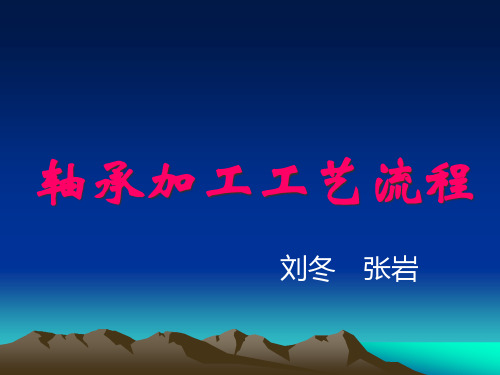
4、沟道
测量内容:沟曲率、沟径、沟位(含对称)、 侧摆、圆度、壁厚差
测量工具:⑴内圈 刮色球、D022、标准件、 百分表
⑵外圈 刮色球、D012、标准件、 百分表
测量方法:(见下图)
测量宽度示意图
刮色球大小范的确定
• 大范半径为沟曲率最大极限半径; • 小范半径为沟曲率最小极限半径。
沟曲率的检测方式及确定方法
轴承加工工艺流程
刘冬 张岩
轴承的组成元素
轴承内部一般由外圈、内圈、滚动体和保 持架组成------通常称为四大件
对于密封轴承,再加上润滑剂和密封圈 (或防尘盖)------又称为六大件
成品轴承
轴承结构
(深沟球轴承)
密封件 外圈
滚动元件 保持架
内圈 密封件
轴承加工中常见形位公差分类及表示符号
备注
练习
1、外径
定义:包含外表面的圆柱体的理论直径 测量内容:外径尺寸、圆度、锥度、垂直
差、壁厚差、表面粗糙度。 测量工具:D913、标准件、百分表。 测量方法:(见下图)
测量外径示意图
软磨外径
▪ 加工设备:M1083外圆磨床 ▪ 对于软磨外径,尺寸公差及公称尺寸易于
控制,形位公差不易控制,常见的形位公 差超差主要原因有:
成品角
产品角是轴承的最终工序,主要是轴承使用时便 于装配对正,其形状由刀具形状保证
成品角轴向尺寸可通过调节大拖板进行改变 成品角径向尺寸可通过调节小拖板进行改变
成品角的检测可以通过卡板的透光度来判定, 透光度越小,成品角的精度越高,反之,精度越 小
6、成品角
测试内容:角圆弧、轴向尺寸、径向尺寸、 轴向装配角、径向装配角
4
沟 道 沟径、沟曲率、沟位、侧摆、圆度、壁厚差
- 1、下载文档前请自行甄别文档内容的完整性,平台不提供额外的编辑、内容补充、找答案等附加服务。
- 2、"仅部分预览"的文档,不可在线预览部分如存在完整性等问题,可反馈申请退款(可完整预览的文档不适用该条件!)。
- 3、如文档侵犯您的权益,请联系客服反馈,我们会尽快为您处理(人工客服工作时间:9:00-18:30)。
打印 热处理 硬磨 超精加工 (腐蚀字)
线材 棒料 棒料
冷镦 热镦 退火
锉削 软磨 (光磨) 热处理 硬磨 (强化处理) 抛光 (精研)
线材 棒料
冷镦 车削
热处理 磨削 超精加工
保持架
冲压
实体
带料 板料
棒料、锻坯、 铸坯
冲压
车削
成型 拉方孔或钻孔
表面处理 表面处理
终检
分类 装配,成品检查,清洗防锈封存,包装
3类 向心球面滚子轴承 4类 长圆柱滚子和滚针轴承 5类 螺旋滚子轴承 6类 角接触轴承 7类 圆锥滚子轴承 8类 推力球轴承和推力向心轴承 9类 推力滚子轴承和推力向心滚子轴承
滚动轴承产品性能要求
滚动轴承应具备:高寿命、低的噪音、小的旋转力 矩和高的可靠性等基本性能
在制定工艺上要求对旋转精度、尺寸精度、粗糙度、 尺寸稳定性、防锈能力、振动及噪音、残磁等进行 控制
高质快速发展阶段(1978~)
轴承行业已建立较完备的工业体系。
滚动轴承基本识
滚动轴承是将运转的轴与轴座之间的滑动摩擦变 为滚动摩擦,从而减少摩擦损失的一种精密机悈 元件
滚动轴承一般由内圈、外圈、滚动体(球和滚 子)、保持架、油脂组成。
滚动轴承十大类型
0类 深沟球轴承 1类 向心球面球轴承 2类 向心短圆柱滚子轴承
3、能加工各种材料 ,适应性强,运用广泛。 4、在一次行程中能切除极薄的金属表层,在小余量切削中 运用广泛。 磨削加工的运用:用于精加工,特别是高硬度、小余量加工
磨削加工的发展:高速磨削、强力磨削、沙带磨削,可以同 时满足效率和精度的要求
第三节磨床简介和型号编制
磨床根据用途不同分类:
通用磨床 外圆磨床、内圆磨床、
2、进给运动:使刀具和工件之间产生附加的相对运动, 使刀具可以连续切削,获得需要的加工表面。
主运动与进给运动之间的关系:
1、主运动高于进给运动, 2、主运动只有1个,而进给运动可能有几个;加工方
法不同,进给方式也不同。
第二节 磨削加工的运动和特点
磨削加工
用磨具以较高的线速度对工件表面进行加工的切削 方法。
第一讲 滚动轴承的发展 第二讲 金属切削基本概念 第三讲 磨削加工的运动和特点 第四讲 磨床简介和型号编制 第五讲 磨削用量 第六讲 切削液 第七讲 防锈知识 第八讲 磨床的维护和保养 第九讲 砂轮知识
滚动轴承的发展 滚动轴承的产生
早期滚动摩擦的运用 滚动轴承的出现 滚动轴承制造工业的诞生
世界轴承工业的发展过程(三个阶段)
轴承零件的加工特点
1、精密加工 磨加工尺寸和几何精度用UM为单位 2、多工序加工 套圈加工到装配有20-40到工序,短圆柱 滚子轴承有74到工序 3、成型加工 零件的工作表面都是回转成型面。
滚动轴承三大特性:专业化、自动化、先进性
滚动轴承生产的一般工艺过程
套圈
钢球
滚子
棒料 管料
棒料 锻造
车削 (软磨)
磨床根据用途不同分类:
通用磨床:
平面磨床 、多用磨床 (M7130H)
(2MA9125)
第三节磨床简介和型号编制
磨床根据用途不同分类:
专用磨床 球轴承套圈沟道磨床(3MK1410B) 、滚子 轴承套圈滚道磨床、超精机床(3MZ323A)等
滚动轴承零件加工工艺特点
轴承零件的结构特点
1、回转表面 工作表面大多都是回转体表面; 2、短而薄 回转体表面通常都是短而薄的; 可分析出: 1、回转表面多 加工机床就比较单一,大多采用车床、磨床。 2、零件短 轴向刚度好,轴向变形就非常小。 3、壁厚薄 径向刚度差,夹紧方法就需要特别注意。
滚动轴承零件加工工艺特点
套圈内沟道磨削的运动
一、主运动: 砂轮的高速旋转运动;
二、进给运动: 1、工件旋转(工件的旋转运动)
2、工件沿自身轴线做直线运动(工件相对砂轮的纵向 进给运动)
3、工件在垂直于砂轮轴线方向的移动(工件的横向进 给运动)
磨削加工的特点
1、砂轮的切削速度很高,目前大多采用45米/秒的高速磨削;
2、可以获得很高的加工精度和很细的表面粗糙度 ,一般可 达公差等级IT4~IT6,表面粗糙度Ra值达1.25~0.08 µm,而镜 面磨削Ra值能达0.010µm,圆度误差0.1 µm。
世界轴承工业的初创阶段 世界轴承工业的成长阶段 世界轴承工业的发展阶段
中国轴承行业的发展(三个阶段)
奠基阶段(1949~1957年)
初步形成了瓦房店、哈尔滨、洛阳、 上海四个主要生产基地
体系形成阶段(1958~1977年)
建立起了五个生产基地和众多制造企业、综合性的科研与工厂 设计机构、工艺装备与测试仪器专业厂,形成了布局基本合理、 科研生产和后勤保障较完善的轴承工业体系。
逆磨:砂轮旋转方向与工件旋转方向相反,一般中心夹具磨
削时使用。
工件
工件
砂轮
砂轮
顺磨
逆磨
平面磨削的运动
一、主运动: 两砂轮的高速旋转运动;
二、进给运动: 1、工件的直线往复运动(工件的纵向进给运动)
2、砂轮沿自身轴线方向的运动(相对工件的横向进给 运动),周期性进给,完成一个单向行程后进给
3、砂轮垂直于工作表面方向的移动(砂轮垂直进给运 动),砂轮平面磨削一遍后进给一次。
几种磨削加工方法
外圆磨削的运动
一、主运动: 砂轮的高速旋转运动; 二、进给运动: 1、工件的旋转运动
2、工件沿自身轴线方向的直线往复运动 (纵向进给运动) 3、砂轮垂直于工件轴线方向的移动(横 向进给运动)
内圆磨削的运动
磨削运动与外圆磨削一样,但砂轮旋转方向与之相反。
顺磨:砂轮旋转方向与工件旋转方向相同,一般无心夹具磨 削时使用。
磨削加工的特点
1、加工精度可达到千分之一毫米
2、Ra能达到1.25~~0.010um
第一节 金属切削基本概念
金属切削加工
是用刀具从零件毛 坯上切除多余的金 属,使其在形状、 尺寸、精度和表面 粗糙度等方面都达 到规定要求的加工 过程。
切削实现的条件: 刀具与工件产生相对运动
运动的分类:
1、主运动:使刀具和工件之间产生相对运动,从而使 刀具前面接近工件的运动。
检查
轴承磨加工的重要地位
轴承套圈在精加工前经过热处理后,表面硬度大大提高,用 车削等其它加工方法已经不能满足轴承加工精度的要求,也 不能满足大批量生产的要求,因此在精加工时必须进行磨加 工;
轴承生产中,磨削加工占总劳动量的60%,所用磨床数量占 全部切削机床的60%,加工成本占总成本的15%。对高精度 轴承其比例更高。
线材 棒料 棒料
冷镦 热镦 退火
锉削 软磨 (光磨) 热处理 硬磨 (强化处理) 抛光 (精研)
线材 棒料
冷镦 车削
热处理 磨削 超精加工
保持架
冲压
实体
带料 板料
棒料、锻坯、 铸坯
冲压
车削
成型 拉方孔或钻孔
表面处理 表面处理
终检
分类 装配,成品检查,清洗防锈封存,包装
3类 向心球面滚子轴承 4类 长圆柱滚子和滚针轴承 5类 螺旋滚子轴承 6类 角接触轴承 7类 圆锥滚子轴承 8类 推力球轴承和推力向心轴承 9类 推力滚子轴承和推力向心滚子轴承
滚动轴承产品性能要求
滚动轴承应具备:高寿命、低的噪音、小的旋转力 矩和高的可靠性等基本性能
在制定工艺上要求对旋转精度、尺寸精度、粗糙度、 尺寸稳定性、防锈能力、振动及噪音、残磁等进行 控制
高质快速发展阶段(1978~)
轴承行业已建立较完备的工业体系。
滚动轴承基本识
滚动轴承是将运转的轴与轴座之间的滑动摩擦变 为滚动摩擦,从而减少摩擦损失的一种精密机悈 元件
滚动轴承一般由内圈、外圈、滚动体(球和滚 子)、保持架、油脂组成。
滚动轴承十大类型
0类 深沟球轴承 1类 向心球面球轴承 2类 向心短圆柱滚子轴承
3、能加工各种材料 ,适应性强,运用广泛。 4、在一次行程中能切除极薄的金属表层,在小余量切削中 运用广泛。 磨削加工的运用:用于精加工,特别是高硬度、小余量加工
磨削加工的发展:高速磨削、强力磨削、沙带磨削,可以同 时满足效率和精度的要求
第三节磨床简介和型号编制
磨床根据用途不同分类:
通用磨床 外圆磨床、内圆磨床、
2、进给运动:使刀具和工件之间产生附加的相对运动, 使刀具可以连续切削,获得需要的加工表面。
主运动与进给运动之间的关系:
1、主运动高于进给运动, 2、主运动只有1个,而进给运动可能有几个;加工方
法不同,进给方式也不同。
第二节 磨削加工的运动和特点
磨削加工
用磨具以较高的线速度对工件表面进行加工的切削 方法。
第一讲 滚动轴承的发展 第二讲 金属切削基本概念 第三讲 磨削加工的运动和特点 第四讲 磨床简介和型号编制 第五讲 磨削用量 第六讲 切削液 第七讲 防锈知识 第八讲 磨床的维护和保养 第九讲 砂轮知识
滚动轴承的发展 滚动轴承的产生
早期滚动摩擦的运用 滚动轴承的出现 滚动轴承制造工业的诞生
世界轴承工业的发展过程(三个阶段)
轴承零件的加工特点
1、精密加工 磨加工尺寸和几何精度用UM为单位 2、多工序加工 套圈加工到装配有20-40到工序,短圆柱 滚子轴承有74到工序 3、成型加工 零件的工作表面都是回转成型面。
滚动轴承三大特性:专业化、自动化、先进性
滚动轴承生产的一般工艺过程
套圈
钢球
滚子
棒料 管料
棒料 锻造
车削 (软磨)
磨床根据用途不同分类:
通用磨床:
平面磨床 、多用磨床 (M7130H)
(2MA9125)
第三节磨床简介和型号编制
磨床根据用途不同分类:
专用磨床 球轴承套圈沟道磨床(3MK1410B) 、滚子 轴承套圈滚道磨床、超精机床(3MZ323A)等
滚动轴承零件加工工艺特点
轴承零件的结构特点
1、回转表面 工作表面大多都是回转体表面; 2、短而薄 回转体表面通常都是短而薄的; 可分析出: 1、回转表面多 加工机床就比较单一,大多采用车床、磨床。 2、零件短 轴向刚度好,轴向变形就非常小。 3、壁厚薄 径向刚度差,夹紧方法就需要特别注意。
滚动轴承零件加工工艺特点
套圈内沟道磨削的运动
一、主运动: 砂轮的高速旋转运动;
二、进给运动: 1、工件旋转(工件的旋转运动)
2、工件沿自身轴线做直线运动(工件相对砂轮的纵向 进给运动)
3、工件在垂直于砂轮轴线方向的移动(工件的横向进 给运动)
磨削加工的特点
1、砂轮的切削速度很高,目前大多采用45米/秒的高速磨削;
2、可以获得很高的加工精度和很细的表面粗糙度 ,一般可 达公差等级IT4~IT6,表面粗糙度Ra值达1.25~0.08 µm,而镜 面磨削Ra值能达0.010µm,圆度误差0.1 µm。
世界轴承工业的初创阶段 世界轴承工业的成长阶段 世界轴承工业的发展阶段
中国轴承行业的发展(三个阶段)
奠基阶段(1949~1957年)
初步形成了瓦房店、哈尔滨、洛阳、 上海四个主要生产基地
体系形成阶段(1958~1977年)
建立起了五个生产基地和众多制造企业、综合性的科研与工厂 设计机构、工艺装备与测试仪器专业厂,形成了布局基本合理、 科研生产和后勤保障较完善的轴承工业体系。
逆磨:砂轮旋转方向与工件旋转方向相反,一般中心夹具磨
削时使用。
工件
工件
砂轮
砂轮
顺磨
逆磨
平面磨削的运动
一、主运动: 两砂轮的高速旋转运动;
二、进给运动: 1、工件的直线往复运动(工件的纵向进给运动)
2、砂轮沿自身轴线方向的运动(相对工件的横向进给 运动),周期性进给,完成一个单向行程后进给
3、砂轮垂直于工作表面方向的移动(砂轮垂直进给运 动),砂轮平面磨削一遍后进给一次。
几种磨削加工方法
外圆磨削的运动
一、主运动: 砂轮的高速旋转运动; 二、进给运动: 1、工件的旋转运动
2、工件沿自身轴线方向的直线往复运动 (纵向进给运动) 3、砂轮垂直于工件轴线方向的移动(横 向进给运动)
内圆磨削的运动
磨削运动与外圆磨削一样,但砂轮旋转方向与之相反。
顺磨:砂轮旋转方向与工件旋转方向相同,一般无心夹具磨 削时使用。
磨削加工的特点
1、加工精度可达到千分之一毫米
2、Ra能达到1.25~~0.010um
第一节 金属切削基本概念
金属切削加工
是用刀具从零件毛 坯上切除多余的金 属,使其在形状、 尺寸、精度和表面 粗糙度等方面都达 到规定要求的加工 过程。
切削实现的条件: 刀具与工件产生相对运动
运动的分类:
1、主运动:使刀具和工件之间产生相对运动,从而使 刀具前面接近工件的运动。
检查
轴承磨加工的重要地位
轴承套圈在精加工前经过热处理后,表面硬度大大提高,用 车削等其它加工方法已经不能满足轴承加工精度的要求,也 不能满足大批量生产的要求,因此在精加工时必须进行磨加 工;
轴承生产中,磨削加工占总劳动量的60%,所用磨床数量占 全部切削机床的60%,加工成本占总成本的15%。对高精度 轴承其比例更高。