塑料模具设计中有关金属嵌件的优化设计
基于Moldflow的带金属嵌件汽车安全带卡扣浇口优化设计
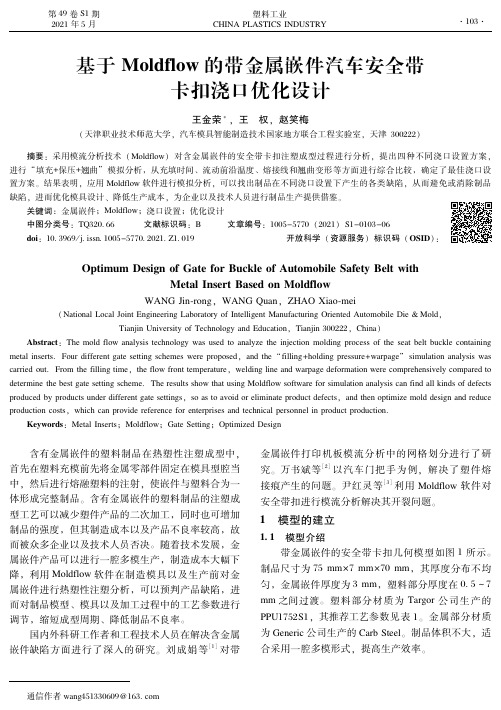
进行双层面网格划分ꎬ 修复不合格网格ꎬ 修复工作完
径小、 易加工、 浇口位置不受限制、 浇口附近残留应
成后ꎬ 对塑料部分进行 3D 网格划分ꎬ 厚度方向最小
力小、 在塑件上浇口残留不明显等优点ꎬ 在生产当中
单元数为 6ꎬ 最大边长为 1 212 mmꎬ 塑料部分最大
纵横比为 26 17ꎬ 最小纵横比为 1 04ꎬ 平均纵横比为
P
>
EN
Q
>>
UFXQ
UH
QE>
=
?L GFN
DY
N
FX>
FY
Q
XH
T
PY
FT>
=
IEN
H
Q
=
F? H
?H
N
R>
=
>Z
H
?Y
=
?D H
N
NW=
?D>FYDP
Y
P
Z
Q
>
VT
FDEZ
P
D [R VT
FDEZ
Q
>E?DP
TD=
Y
Y
P
T
P
?QLH
Q
P>
P
Q
Q
=
?L>
! >
FH
>Q
FH
SF=
D FTP
N
=
I=
得到分析结果ꎬ 对四种方案各个结果进行对比ꎮ
3 方案对比及分析
3 1 充填时间
填充时间是指熔融的塑胶充满整个型腔的时间ꎮ
充填时间可以用于查看整个塑件充填情况、 充填时间
及查看塑件有无发生短射、 迟滞现象ꎮ 充填时间短可
某医疗器械带金属嵌件塑件的注塑模具设计

加工设备与应用CHINA SYNTHETIC RESIN AND PLASTICS合 成 树 脂 及 塑 料 , 2021, 38(2): 622016年以来,随着健康中国的实施,中国医疗器械产业进入黄金发展期,已成为世界医疗器械的主要生产国和主要消费国之一。
医疗器械行业是技术密集型科技行业,集电子、机械、化工、医药、塑料多种行业于一体[1-4]。
本工作涉及的带金属嵌件塑件是一次性包皮切割缝合器核心部件之一,在开发过程中,遇到一些难以用传统注塑模具成型方法解决的问题,通过改进模具浇注系统、成型零件、脱模推出机构、注塑机工作台等,以满足客户对产品的生产和质量要求。
1 塑件分析带金属嵌件塑件的结构见图1,塑件中镶有嵌件刀片。
目前,按照客户需要,共生产12种规格产品。
产品规格按刀片内径确定,包括12,15,18,20,22,24,25,29,30,32,34,36 mm共12种规格。
塑件呈漏斗状,由斗颈、斗身、斗尾等组成,材料为奇美实业股份有限公司提供的质量分数为20%玻璃纤维改性的丙烯腈-丁二烯-苯乙烯共聚物。
塑件内外表面美观,无飞边及熔接痕等缺陷。
嵌件刀片是薄壁套类金属零件,嵌件与塑件配合有同轴度要某医疗器械带金属嵌件塑件的注塑模具设计徐自明(常州工业职业技术学院,江苏 常州 213164)摘要:以某医疗器械带金属嵌件塑件为研究对象,运用注塑成型技术进行注塑模具设计。
针对产品的多规格及系列化特点,创新设计了浇注系统,可以根据需求成型不同规格产品。
通过分析塑件的结构特征,设计了组合式型芯、哈夫机构、推出机构,实现嵌件刀片的精准定位,完成塑件成型和自动脱模。
将立式注塑机工作台,由一个工位改造成两个工位,既能方便地取出成型塑件,又能安全地将嵌件装入型芯。
模具经生产验证,产品质量稳定,外观和形状尺寸精度能满足客户要求。
关键词:注塑模具 医疗器械 金属嵌件中图分类号:TQ 320.662 文献标志码:B 文章编号:1002-1396(2021)02-0062-05Design of injection mold for plastic part with metal insert for medical deviceXu Ziming(Changzhou Institute of Industry Technology,Changzhou 213164,China)Abstract:The injection mold of plastic part with metal insert for medical device was designed via plastic molding. A novel gating system was designed to meet the requirements of the multi-specification and serialization of the product,which can be used to form different specifications according to the demands. The combined core,half mechanism,and ejection mechanism were designed by analyzing the characteristic structure of the plastic part,achieving the precise positioning of the insert blades,the plastic part molding and automatic demolding. The original one station of the vertical injection molding machine table was transformed into two stations,which can easily remove the molded plastic parts and can safely insert the inserts into the core. The mold has been verified in practice,and the product quality is stable,whose appearance and size accuracy meet requirements of customers.Keywords:injection mold; medical device; metal insertDOI:10.19825/j.issn.1002-1396.2021.02.15收稿日期:2020-09-27;修回日期:2020-12-26。
模具“三流”优化(料流、热流、气流)(一)
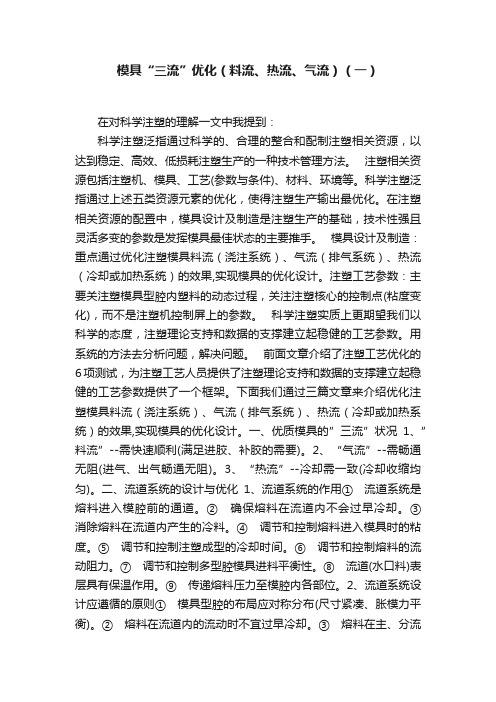
模具“三流”优化(料流、热流、气流)(一)在对科学注塑的理解一文中我提到:科学注塑泛指通过科学的、合理的整合和配制注塑相关资源,以达到稳定、高效、低损耗注塑生产的一种技术管理方法。
注塑相关资源包括注塑机、模具、工艺(参数与条件)、材料、环境等。
科学注塑泛指通过上述五类资源元素的优化,使得注塑生产输出最优化。
在注塑相关资源的配置中,模具设计及制造是注塑生产的基础,技术性强且灵活多变的参数是发挥模具最佳状态的主要推手。
模具设计及制造:重点通过优化注塑模具料流(浇注系统)、气流(排气系统)、热流(冷却或加热系统)的效果,实现模具的优化设计。
注塑工艺参数:主要关注塑模具型腔内塑料的动态过程,关注注塑核心的控制点(粘度变化),而不是注塑机控制屏上的参数。
科学注塑实质上更期望我们以科学的态度,注塑理论支持和数据的支撑建立起稳健的工艺参数。
用系统的方法去分析问题,解决问题。
前面文章介绍了注塑工艺优化的6项测试,为注塑工艺人员提供了注塑理论支持和数据的支撑建立起稳健的工艺参数提供了一个框架。
下面我们通过三篇文章来介绍优化注塑模具料流(浇注系统)、气流(排气系统)、热流(冷却或加热系统)的效果,实现模具的优化设计。
一、优质模具的”三流”状况1、”料流”--需快速顺利(满足进胶、补胶的需要)。
2、“气流”--需畅通无阻(进气、出气畅通无阻)。
3、“热流”--冷却需一致(冷却收缩均匀)。
二、流道系统的设计与优化1、流道系统的作用①流道系统是熔料进入模腔前的通道。
②确保熔料在流道内不会过早冷却。
③消除熔料在流道内产生的冷料。
④调节和控制熔料进入模具时的粘度。
⑤调节和控制注塑成型的冷却时间。
⑥调节和控制熔料的流动阻力。
⑦调节和控制多型腔模具进料平衡性。
⑧流道(水口料)表层具有保温作用。
⑨传递熔料压力至模腔内各部位。
2、流道系统设计应遵循的原则①模具型腔的布局应对称分布(尺寸紧凑、胀模力平衡)。
②熔料在流道内的流动时不宜过早冷却。
带金属嵌件的圆珠笔管注塑模模具设计

带金属嵌件的圆珠笔管注塑模模具设计注塑模具是现代工业生产中常用的模具之一,广泛应用于各行各业。
本文将针对带金属嵌件的圆珠笔管注塑模具的设计进行详细介绍。
一、需求分析在进行注塑模具设计之前,首先需要了解产品的需求以及相关要求,以便更好地进行设计。
对于带金属嵌件的圆珠笔管来说,主要需求如下:1.笔管材料:一般使用工程塑料进行注塑成型,如ABS、PC等。
2.笔管形状:一般为圆柱形状,但也有可能有其他特殊形状的设计需求。
3.金属嵌件:金属嵌件一般用于笔夹、转盘等位置,需要考虑金属与塑料的嵌接方式和固定方式。
4.模具寿命:模具的设计应该考虑到产品的预期寿命,以便保证模具能够有足够的使用寿命。
二、模具设计过程1.确定产品结构和尺寸:根据需求确定圆珠笔管的结构和尺寸,包括笔管的长度、直径等。
同时,还需要确定金属嵌件的形状、材料等。
2.设计注塑模具的结构:根据产品的结构和尺寸,设计注塑模具的结构。
注塑模具主要由模具座、上模板、下模板、模腔、模芯等部分组成。
在设计时,还需要考虑到模具的开合方式以及相关的润滑、冷却等措施。
3.设计模具零件:根据注塑模具的结构,设计模具的各个零件。
例如,模具座可以设计为整体结构,上模板和下模板可以设计成可拆卸的形式,模腔和模芯可以分别设计成可更换的结构,以便方便维修和更换。
4.设计金属嵌件的固定方式:根据金属嵌件的形状和要求,设计金属嵌件的固定方式。
一般可以采用螺纹连接、卡榫固定等方式。
同时,还需要考虑到金属与塑料的嵌接方式,可以采用机械固定、热熔嵌接等方式。
5.添加冷却系统:注塑模具在工作过程中会产生大量的热量,如果不能有效地散热,会导致产品质量下降和模具寿命的减少。
因此,在设计模具时,需要添加冷却系统,以便快速、均匀地散热。
6.进行模具设计验证:完成模具设计后,需要进行模具设计验证,以验证模具设计的合理性和可行性。
常用的验证方法有流动分析、疲劳分析等,可以通过模拟模具工作过程,检查模具是否符合要求。
金属嵌件成型的处理方法

金属嵌件成型的处理方法
金属嵌件成型是指在模具内装入预先准备的异材质嵌件后,在注入树脂,熔融的材料与嵌件接合固化,制成一体化注塑件产品的成型方法。
目前很多国内注塑加工厂在金属嵌件方面还有所欠缺。
金属嵌件成型相对比较简单,但是产生的成型收缩率也比较不均一,在产品注塑加工之前应做重要部位的外形、尺寸精度的极限实验。
注塑过程中金属嵌件容易发生变形和移位等情况,故设计的时候应充分考虑模具结构和容易保持金属嵌件的模具形状。
对于金属嵌件形状比较难改变的产品,事先应该做足充足的实验准备。
模具浇口位置方式、成型周期等制约模具构造的可预测事项,尽可能事先解决或有相对应的改善对策。
应确认金属嵌件是否需要预热或干燥处理,目的在于保证产品的质量和成型的稳定性。
为了避免金属嵌件、成型品的细微片堆积在模腔内,有必要的话可组装气吹装备。
决定金属嵌件的成型率、生产性和成型成本条件的因素有很多,如:金属嵌件品的精度、嵌件的形状、模具是否有利于嵌件成型和成型品形状等。
注射机、模具、自动化装置的有效组合和如何在短时日内发挥出其优秀的性能,是决定自动嵌件成型系统的关键。
江苏恒太电子塑胶自2004年以来,一直为美国一家客户生产多种汽车和工业用传感器注塑件,这些注塑件感器外壳都需要运用各种材质的金属插针,金属插针的表面有别出心裁的电镀要求(包括镀金、镀镍、镀锡等)。
金属嵌件注塑成型技术特点及二次注塑加工注意事项

金属嵌件注塑成型技术特点及二次注塑加工注意事项一、金属嵌件注塑成型技术特点1.注塑成型技术的基本原理注塑成型技术是一种以热塑性塑料为原料,利用注塑机将熔融的塑料注入模具中,经冷却后形成所需的塑件的工艺。
而金属嵌件注塑成型技术则是在注塑成型的基础上,将金属嵌件注入到塑件中,使其具有更强的机械性能和耐腐蚀性能。
2.金属嵌件注塑成型技术的优点金属嵌件注塑成型技术相比传统的注塑成型技术具有以下优点:(1)提高了塑件的强度和硬度,增强了其耐磨性和耐腐蚀性能;(2)减小了塑件的膨胀系数,使其更加稳定和可靠;(3)金属嵌件可以帮助塑件更好地固定在特定的部件上,提高了整体装配的可靠性;(4)金属嵌件还可以在塑件上形成导热凸起,提高塑件的散热性能。
3.金属嵌件注塑成型技术的应用领域金属嵌件注塑成型技术在各个领域都有广泛的应用,尤其在汽车零部件、电子电器、航空航天等领域有着重要的应用价值。
在汽车零部件中,金属嵌件注塑成型技术可以帮助提高汽车零部件的机械性能和耐久性,同时还可以减轻零部件的重量,提高汽车整体的燃油效率。
在电子电器领域,金属嵌件注塑成型技术可以帮助提高电子产品的散热性能和抗干扰能力,同时还可以减小产品的体积,提高产品的性能密度。
二、二次注塑加工注意事项1.注塑成型前的金属嵌件处理在进行二次注塑加工前,需要对金属嵌件进行表面处理,以提高其与塑料的粘接性。
一般采用喷砂、化学处理或表面镀层等方法对金属嵌件进行表面处理,以增加其表面粗糙度和粘着力。
2.注塑成型过程中的温度控制在进行二次注塑加工时,需要对注塑成型设备的温度进行严格控制,以保证金属嵌件和塑料之间的粘接效果。
通常需要根据金属嵌件和塑料的材质特性,合理设置注塑成型设备的温度参数,以确保金属嵌件和塑料之间的粘接效果稳定和可靠。
3.注塑成型后的金属嵌件检测在进行二次注塑加工后,需要对金属嵌件进行严格的质量检测,以确保其粘接效果和尺寸精度符合要求。
一般需要采用金属嵌件的拉伸试验、弯曲试验、硬度测试等方法进行检测,以保证金属嵌件的质量合格。
塑料制品铜嵌件埋入方式设计

塑料制品铜嵌件埋入方式设计·热熔螺母热熔埋置是最常见、最通常的埋入方式,一般以热熔机及手工电烙铁埋钉。
·注塑螺母 注塑成型埋置一般对螺母的孔径要求很严格,孔径管控在0.05mm以内,因为产品以Molding Pin固定后放置于射出成型模具中,螺母孔径要以注塑成型机的PIN针的大小来管控。
·超声螺母超声埋置是一种通过超声振动,使螺母与工件表面及内在分子间的磨擦而使传处到接口的温度升高,当温度达到此工件自身的软化温度时,将螺母埋植于胶件中,当震动停止,工件同时在一定的压力下冷却定形。
塑胶孔设计与螺母选择螺母基本尺寸塑胶基本尺寸注:D:螺母外径L:螺母长度d:螺母底座C:塑胶孔径W:塑胶孔壁厚Y:塑胶孔深塑胶孔与螺母的选择参数1、d 尺寸为螺母底座,也称导向定位部分,在埋入前与塑胶C 部分配合,因此 螺母底端d 部分要比塑胶BOSS 内孔径C 尺寸小,以方便定位;2、D 尺寸为螺母外径,它与塑胶BOSS 内孔径C 尺寸相配,一般手机螺母塑胶 内孔径比螺母外径小约0.25-0.3mm ;3、L 尺寸为螺母长度,它与塑胶BOSS 孔深度Y 尺寸配合,一般塑胶孔深比螺 母高(长)度大0.5-1.0mm 的深度用于储胶;4、W 为塑胶孔壁厚,一般塑胶BOSS 孔肉厚为0.8-1.0mm 以上,螺母尺寸规格 越大,肉厚越大。
(见下表参数)塑胶孔径螺牙Thread外径D长度L 直径C 深度Y 塑胶肉厚W2.03.02.53.53.04.0M1.2*0.252.33.5 2.04.50.82.03.02.5 3.53.04.0M1.2*0.252.53.5 2.24.50.81.8 2.82.03.02.53.5M1.4*0.32.33.02.04.00.82.03.02.53.53.04.0M1.4*0.32.354.02.15.00.82.03.0M1.4*0.32.52.52.23.50.83.04.03.54.52.03.02.53.53.04.0M1.4*0.32.73.52.34.50.81.82.82.03.02.53.53.04.03.54.5M1.6*0.352.5 4.02.25.01.02.03.02.53.53.04.03.54.5M1.6*0.352.7 4.02.35.0 1.02.03.02.53.53.04.03.5 4.5M1.6*0.353.04.0 2.65.0 1.02.0 3.02.5 3.53.0 4.03.5 4.5M1.7*0.353.04.0 2.65.0 1.22.03.02.53.53.04.03.54.5M1.8*0.353.04.02.65.01.2备注:以上皆为建议数据,如有其它所需尺寸将可另行制作!塑胶BOSS孔尺寸开立大小的影响若:塑胶与螺母选择上无问题,螺母埋入塑胶后标准状态如图(一)所示:若:螺母尺寸太小,塑胶BOSS孔太大,螺母埋入塑胶后吃不到胶,会产生扭拉力不足现象如图(二)所示:若:螺母尺寸太大,BOSS孔太小,会产生溢胶或者爆裂现象如图(三)所示:如螺母尺寸与塑胶尺寸都没有问题,还有异常现象发生,那我们通常会考虑通过一些优化设计来改善;例1、塑胶BOSS孔深较浅,会产生扭拉力不足由于BOSS孔深度较浅,如选择双斜纹的螺母,在螺母各尺寸比例调配下,特别是压花上,压花段差较短,这样的螺母埋入塑胶后,压花吃胶面的塑胶太少,会产生扭拉力不足现象,所以一般建议,将BOSS孔深设在2.5mm以上,螺母尺寸长度一般建议做2.0mm以上。
带金属嵌件的圆珠笔管注塑模模具设计
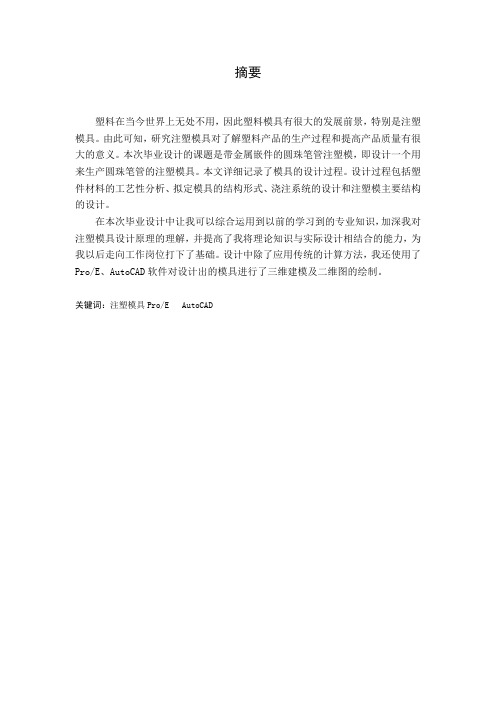
关键词:注塑模具Pro/E AutoCAD
摘要
塑料在当今世界上无处不用,因此塑料模具有很大的发展前景,特别是注塑模具。由此可知,研究注塑模具对了解塑料产品的生产过程和提高产品质量有很大的意义。本次毕业设计的课题是带金属嵌件的圆珠笔管注塑模,即设计一个用来生产圆珠笔管的注塑模具。本文详细记录了模具的设计过程。设计过程包括塑件材料的工艺性分析、拟定模具的结构形式、浇注系统的设计和注塑模主要结构的设计。
ABSTRACT
Plastic is nowhere in the world today,so the plastic mold has great prospects for development,especially the injection mold.Thus we can see,It is of great significance to study the injection molds to understand the production process of plasticproducts and improve the quality of the products.The subject of this graduation project isinjection molded mold with ball - point pen with metal insert, that is, the design of a ballpoint pen for the production of injection mold. This paper records the design process of the mold in detail. The design process includes the technical analysis of the plastic parts, the design of the mold, the design of the pouring system and the design of the main structure of the injection mold.
- 1、下载文档前请自行甄别文档内容的完整性,平台不提供额外的编辑、内容补充、找答案等附加服务。
- 2、"仅部分预览"的文档,不可在线预览部分如存在完整性等问题,可反馈申请退款(可完整预览的文档不适用该条件!)。
- 3、如文档侵犯您的权益,请联系客服反馈,我们会尽快为您处理(人工客服工作时间:9:00-18:30)。
详细说明改进前的设计改进后的设计
1.尽量采用不通孔或不穿的螺纹孔,这样可在设计模具时采用插
入式解决嵌件的定位
2.嵌件表面需滚花或开设沟槽时,一般小嵌件的沟槽,深为1~
2mm,宽为2~3mm,转角处为圆弧,滚花为菱形;齿高1~2mm如
零件受力很小时,可只采用菱形滚花,不开沟槽
3.条件许可时,金属嵌件应凸起或凹入1.5~2mm,以保证嵌件稳
定
4.布置在凸耳或凸起部分的嵌件,应比凸耳或凸起部分长一些,
以提高零件的机械强度
5.尽量避免采用片状、细长的嵌件。
当必须采用膜片、细长的嵌
件时,为防止成型时塑料对嵌件冲击而造成弯曲变形,应采用销钉
支承或打孔A通流
6.螺杆嵌件的光杆部分与模具应为H8/f9配合。
为防止塑料沿螺
纹部分溢料,螺纹部分应留在塑料外面,如右图所示
7.螺纹通孔嵌件高度应低于成型高度0.05mm。
嵌件过高易产生变
形
8.嵌件的装夹定位部分应具有H8/f9配合,以保证金属嵌件能精
确地固定在模具中
9.圆柱形或套筒形嵌件推荐结构尺寸如右图,在特殊情况下H可
加大,但不得大于2D
10.板形、片状金属嵌件可采用右图方式固定。
当嵌件厚度小于
0.5mm时,最好不用孔固定结构,而采用切口或折弯的方法固定
11.金属嵌件周围的塑料不能太薄,否则塑料会因冷却收缩而破
裂。
右图列出了嵌件周围塑料层的推荐尺寸
/mm
D h c
≤41 1.5
>4~8 1.5 2.0
>8~12 2.0 3.0
>12~16 2.5 4.0
>16~25 3.0 5.0
塑料模具设计中有关金属嵌件的优化设计。