推荐-中频电磁感应加热器设计 精品
中频炉感应圈设计数据
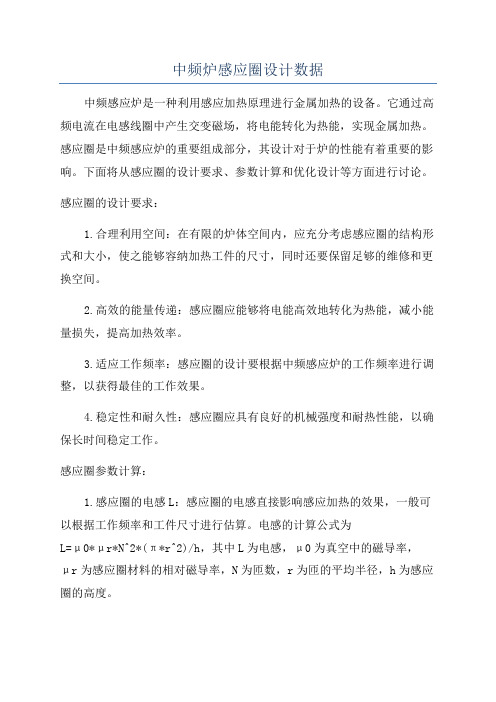
中频炉感应圈设计数据中频感应炉是一种利用感应加热原理进行金属加热的设备。
它通过高频电流在电感线圈中产生交变磁场,将电能转化为热能,实现金属加热。
感应圈是中频感应炉的重要组成部分,其设计对于炉的性能有着重要的影响。
下面将从感应圈的设计要求、参数计算和优化设计等方面进行讨论。
感应圈的设计要求:1.合理利用空间:在有限的炉体空间内,应充分考虑感应圈的结构形式和大小,使之能够容纳加热工件的尺寸,同时还要保留足够的维修和更换空间。
2.高效的能量传递:感应圈应能够将电能高效地转化为热能,减小能量损失,提高加热效率。
3.适应工作频率:感应圈的设计要根据中频感应炉的工作频率进行调整,以获得最佳的工作效果。
4.稳定性和耐久性:感应圈应具有良好的机械强度和耐热性能,以确保长时间稳定工作。
感应圈参数计算:1.感应圈的电感L:感应圈的电感直接影响感应加热的效果,一般可以根据工作频率和工件尺寸进行估算。
电感的计算公式为L=μ0*μr*N^2*(π*r^2)/h,其中L为电感,μ0为真空中的磁导率,μr为感应圈材料的相对磁导率,N为匝数,r为匝的平均半径,h为感应圈的高度。
2.感应圈的匝数N:匝数的选择要根据工作频率和工件尺寸来综合考虑。
一般来说,匝数越多,电感越大,加热效果越好,但也会带来更大的成本和功率损耗。
3.感应圈的截面积A:截面积的大小会影响感应加热的功率密度,一般可以通过感应加热功率和电流密度来计算。
截面积的计算公式为A=P/(k*J*N*f*Bm),其中A为截面积,P为感应加热功率,k为电磁性能系数,J为电流密度,f为工作频率,Bm为最大磁感应强度。
4.感应圈的材料选择:感应圈的材料应具有良好的导电性和磁导率,以提高加热效果和转换效率。
常用的材料有铜、铝等。
感应圈的优化设计:1.引入热分析方法:利用热传递分析软件对感应圈进行热传导分析,优化感应圈的结构设计,降低热损失和温度梯度,提高加热效果。
2.优化匝数和尺寸:根据具体工件尺寸和工作频率,通过优化匝数和尺寸的选择,达到最佳的加热效果和能量利用率。
电磁加热产品设计方案模板

电磁加热产品设计方案模板一、概述本文旨在提供一个电磁加热产品的设计方案模板,以指导设计师和工程师进行产品开发和设计。
电磁加热技术是一种高效、节能的加热方法,在电热水壶、微波炉等家用电器中得到广泛应用。
本设计方案模板将包括产品需求分析、设计原理、材料选择以及制造和测试等方面的内容。
二、产品需求分析在设计电磁加热产品之前,首先需要对产品需求进行分析。
产品需求分析会直接影响到产品功能和特性的设计。
需求分析可以包括以下几个方面:1. 加热效率要求:电磁加热产品主要通过感应加热来实现,因此需要考虑加热效率的要求,即加热效果与消耗的电能之间的比例关系。
2. 加热时间要求:根据产品的使用场景和用途,确定需要加热的时间要求,以便在设计中考虑相应的加热功率和加热面积。
3. 规格和尺寸要求:确定产品的规格和尺寸,包括产品外形尺寸、材料的选择等,以满足用户的需求和产品的设计要求。
4. 安全性要求:考虑产品在工作时的安全性,包括防止过热、漏电等方面的安全保护措施。
5. 使用寿命要求:设计产品的使用寿命,包括材料的选择、制造工艺等,以确保产品的可靠性和耐用性。
三、设计原理电磁加热产品的设计原理基于电磁感应现象,主要包括以下几个方面:1. 电磁感应:通过电磁场的变化产生感应电流,从而实现能量转换和加热效果。
2. 电磁感应加热:利用感应电流在材料内部产生焦耳热,从而使材料加热。
3. 加热功率和效率:加热功率与感应电流的大小和频率有关,加热效率与材料的电磁性能和结构有关。
四、材料选择在电磁加热产品设计中,合理选择材料对于产品的性能和特性具有重要影响。
以下是常用的材料选择原则:1. 导热性:材料应具备良好的导热性能,以加快热量传导和均匀分布。
2. 磁性:材料应具备一定的磁性能,以增强电磁感应效果。
3. 耐高温性:考虑产品在长时间加热情况下的耐高温性,选择适当的高温材料。
4. 绝缘性:对于产品的外壳和其他非加热部分,需要具备良好的绝缘性能,以确保产品的安全性。
中频加热线圈的结构设计

中频加热线圈的结构设计摘要:1.中频加热线圈简介2.中频加热线圈的结构设计要求3.中频加热线圈的选材4.中频加热线圈的制造工艺5.中频加热线圈的应用领域正文:中频加热线圈是一种用于工业加热的电磁线圈,通过中频电流产生磁场,使被加热物体产生涡流,从而实现加热目的。
中频加热线圈的结构设计对其性能有着重要影响,因此,合理的结构设计和选材是提高线圈性能的关键。
一、中频加热线圈简介中频加热线圈,又称为中频感应线圈,是一种用于中频(1-100kHz)电磁感应加热的线圈。
中频加热线圈广泛应用于金属热处理、金属熔炼、化工、纺织、食品等行业。
二、中频加热线圈的结构设计要求1.线圈形状:根据加热设备的结构和使用要求,选择合适的线圈形状,如圆筒形、螺旋形、矩形等。
2.匝数:根据加热设备的功率和频率,合理设计线圈的匝数,以满足加热需求。
3.绝缘材料:选择耐热、耐磨、电绝缘性能好的绝缘材料,如酚醛树脂、环氧树脂等。
4.散热结构:设计合适的散热结构,以保证线圈在工作过程中产生的热量能及时散发,提高线圈的可靠性和使用寿命。
三、中频加热线圈的选材1.电磁线:选择导电性能好、耐热、耐腐蚀的电磁线,如裸铜线、镀锡铜线等。
2.绝缘材料:选择耐热、耐磨、电绝缘性能好的绝缘材料,如酚醛树脂、环氧树脂等。
3.磁性材料:选择高磁导率、高饱和磁密、耐腐蚀的磁性材料,如硅钢片、坡莫合金等。
四、中频加热线圈的制造工艺1.绕制:根据设计要求,将电磁线绕在线圈模具上,注意保持线圈匝间紧密、平整。
2.绝缘:将绝缘材料涂抹在线圈表面,要求厚度均匀、无气泡、无杂质。
3.固化:将线圈放入烘箱中,通过高温固化,使绝缘材料与线圈紧密结合。
4.检测:对线圈进行电气性能、机械性能、耐压性能等方面的检测,确保线圈质量。
五、中频加热线圈的应用领域1.金属热处理:用于工模具、轴承、齿轮等金属零部件的热处理。
2.金属熔炼:用于有色金属、黑色金属的熔炼和铸造。
3.化工:用于反应釜、管道、阀门等设备的加热和保温。
中频感应加热电源的微机控制系统设计

毕业设计说明书题目: 中频感应加热电源的微机系统控制设计学院名称:电气工程学院班级:学生姓名:学号:指导教师:教师职称:教授目次1 概述 (1)1.1 应用背景和意义 (1)1.2 国内外的发展状况 (1)1.3 本课题的设计任务及要求 (1)2 方案论证 (3)2.1 感应加热电源的基本工作原理 (3)2.2 中频感应加热电源的基本结构 (4)2.3 逆变器的选择 (5)3 主电路的设计 (8)3.1 整流电路的设计 (8)3.1.1 整流电路的选择 (8)3.1.2 整流电路的原理 (8)3.2 逆变电路的设计 (10)3.2.1 逆变电路的结构 (10)3.2.2 逆变电路的工作原理 (11)3.2.3 PWM逆变电路的设计 (12)4 控制电路的设计 (13)4.1 控制电路的作用 (13)4.2 控制电路的结构和原理 (14)4.3 控制芯片的设计 (14)4.4 温度传感器设计 (15)4.5 上位机接口模块的设计 (16)4.6 驱动电路的设计 (17)5 控制器软件设置 (19)5.1 单片机软件设置 (19)5.2 定时器捕捉中断方式 (21)总结 (22)致谢 (23)参考文献 (24)附录 A (26)附录 B (27)1 概述二十世纪末感应加热技术才被普遍应用,因为它不仅具有加热速率高、加热效率高、加热均匀等优点,而且还具有可选性、质量高、低污染、可控能力好和生产自动化等特点,因此能够迅速广泛的发展。
1.1 应用背景和意义在国外,感应加热技术已经日益成熟。
在铸造领域,双联熔炼工艺已经得到了快速发展。
在锻造领域,可以利用感应加热完成快速透热热锻,并且材料的利用率高达90%,锻件表面的光滑度可小于40μm。
在焊接领域,国外正大力发展全固态大功率电源。
在我国,因为铸件的使用量大,所以铸造行业正以炉熔炼为主,但是温度及成分控制能力差,废品率高,即使较好的铸造业废品率也只能为5%—16%间,但一般铸造废品率高达20%。
中频感应加热电源的设计

中频感应加热电源的设计
1.电源输出功率和频率:根据加热要求确定电源的输出功率和频率。
输出功率一般由加热负荷大小决定,频率一般选择在1kHz~20kHz之间,
根据不同的加热要求进行调整。
2.电源结构设计:电源的结构设计主要包括整流、逆变、振荡等电路
的设计。
整流电路用于将交流电转换成直流电,逆变电路用于将直流电转
换成交流电,振荡电路用于产生中频振荡信号。
3.电源控制系统设计:电源控制系统主要包括开关控制电路、保护电
路和自动控制电路等。
开关控制电路用于控制电源的开关,保护电路用于
保护电源和负载不受损坏,自动控制电路用于实现加热功率的调节和温度
等参数的监测和控制。
4.效率和功率因数:设计中频感应加热电源时,需要考虑电源的效率
和功率因数,以提高电源的能量利用率和减少对电网的电能需求。
5.冷却系统设计:中频感应加热电源在工作过程中会产生大量的热量,需要通过冷却系统将热量排出,以保证电源的正常工作和寿命。
6.控制方式:中频感应加热电源的控制方式有手动控制和自动控制两种。
手动控制方式需要人工操作电源的开关和参数调节,自动控制方式通
过传感器和控制器实现对加热过程的自动控制。
7.安全性设计:中频感应加热电源设计中需要考虑安全性问题,包括
过载、短路、过流、过热等保护措施的设计,以及对电源和负载的绝缘和
接地等安全措施的实施。
综上所述,中频感应加热电源的设计需要考虑输出功率和频率、电源结构、电源控制系统、效率和功率因数、冷却系统、控制方式、安全性等方面的因素。
通过合理的设计和选择,可以提高电源的性能和工作效率,满足不同加热需求的要求。
基于PLC的中频感应加热炉电源控制系统设计

引言
中频感应加 热炉是一种利 用 电磁感应原理 实现感应加 热的电源装 置 ,由于这种加热 方式是通过 电磁 感应传递 的 , 感 应线 圈与金 属工件 并 非直 接接 触 ,由工件 自身 产 生热 量 ,所 以称之 为感 应加 热 。感应 加 热炉的发展与数 控技术及 计算机技术 的应 用密不可分 ,国外厂商 以 此 取得先机 ,其感 应炉控制 技术先进 , 其 效率高 、可 靠、操作 简便等 特 点已经得 到广泛认可 ,因此大部分铸造厂 普遍应用 了 “ 国外 生产 的感应加热 炉。如何吸收 国外控制技术 的长 处来逐渐 缩小差距 ,利用 P L C简单、精 确的特点 ,来控 制感应加热 ,提 升感应加热 系统的 自动 化水平 具有重要的意义 。
一
界面 的 P L C控制系统一定会为 工业控 制做出巨大贡献 ,本系统设计暂 时没有考虑采 用计 算机作为上位机 , 但 在以后的研究 中会进 一步引入
良好的人机界面 ,期望使系统 的控制 能够更加简 单可 靠。
参考文献 : [ 1 ] 谢鑫 , 王倩 . 工频感应 炉 P L C自动控 制系统的应用 [ M 】 . 鞍 山钢铁 公司设计研究 院 . [ 2 】 吴 中俊 , 黄永 红 . 可编程序控 制器原理及应用 [ M 】 . 机械工业 出版
索工案 收术
1 5 2
基于 P L C的中频感应加热炉 电源控制系统设计
罗继 军
( 陕西国防工业职 Байду номын сангаас技术学院 , 陕西 户县 7 1 0 3 0 0)
摘 要 : 本 文以 P L C 控制 器为核 心,研 究 了中频感应加 热炉控制 系统模型 ,从 系统的需求 出发 ,进行 了设 备硬件 的设计及控制模块 和外 围器件 的选型 ,初步设计 了一种具有较 高的可靠性和抗干扰性 ,为工业生产提供 了一种可行的方案 。 关键词 : P L C 控制 器 ; 中频感应加热 炉 ;电源 ;系统设计
中频加热线圈的结构设计
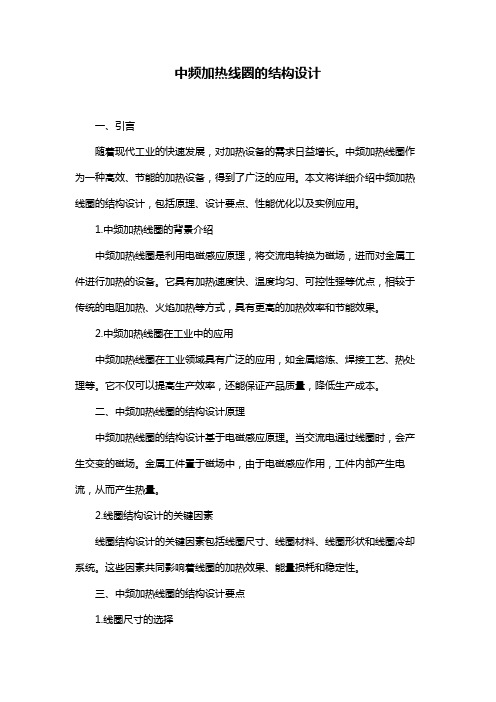
中频加热线圈的结构设计一、引言随着现代工业的快速发展,对加热设备的需求日益增长。
中频加热线圈作为一种高效、节能的加热设备,得到了广泛的应用。
本文将详细介绍中频加热线圈的结构设计,包括原理、设计要点、性能优化以及实例应用。
1.中频加热线圈的背景介绍中频加热线圈是利用电磁感应原理,将交流电转换为磁场,进而对金属工件进行加热的设备。
它具有加热速度快、温度均匀、可控性强等优点,相较于传统的电阻加热、火焰加热等方式,具有更高的加热效率和节能效果。
2.中频加热线圈在工业中的应用中频加热线圈在工业领域具有广泛的应用,如金属熔炼、焊接工艺、热处理等。
它不仅可以提高生产效率,还能保证产品质量,降低生产成本。
二、中频加热线圈的结构设计原理中频加热线圈的结构设计基于电磁感应原理。
当交流电通过线圈时,会产生交变的磁场。
金属工件置于磁场中,由于电磁感应作用,工件内部产生电流,从而产生热量。
2.线圈结构设计的关键因素线圈结构设计的关键因素包括线圈尺寸、线圈材料、线圈形状和线圈冷却系统。
这些因素共同影响着线圈的加热效果、能量损耗和稳定性。
三、中频加热线圈的结构设计要点1.线圈尺寸的选择线圈尺寸直接影响到加热效果和能量损耗。
合理选择线圈尺寸,可以提高加热效率,减小能量损耗。
2.线圈材料的选用线圈材料需要具备良好的导电性和热稳定性。
常用材料有铜、铝等,根据实际应用场景选择合适的材料。
3.线圈形状的设计线圈形状会影响到磁场的分布,从而影响加热效果。
常见的线圈形状有圆形、矩形等,可根据工件形状和加热需求进行设计。
4.线圈冷却系统的设计线圈在高温环境下工作,容易导致线圈过热损坏。
设计合理的冷却系统,可以保证线圈的稳定运行。
四、中频加热线圈的性能优化1.提高加热效率通过优化线圈结构,提高电流密度,从而提高加热效率。
2.减小能量损耗降低线圈的电阻,减少能量损耗。
3.增强线圈的稳定性优化线圈冷却系统,保证线圈在高温环境下的稳定运行。
五、中频加热线圈的实例应用1.金属熔炼中频加热线圈在金属熔炼领域具有广泛的应用。
中频感应器的设计与计算
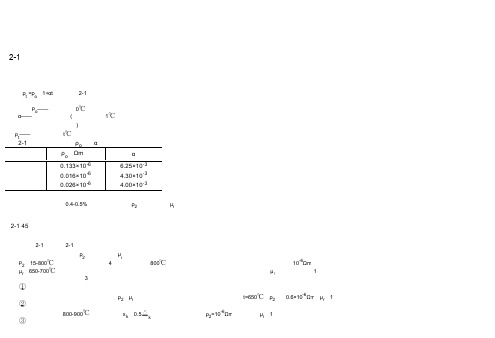
ngj
.wd iare
wd
m o c .
电话
20 :15
29
7 6322
QQ:
73 8719
804
由式(2-11)(2-12),可得:
PT t = C Δ T G
即:
(2-13)
其中:C——坯料的平均比热容。表示单位重量坯料每升温1℃所吸收的热能。单位:KJ/kg℃。
表2-3 几种常见金属的平均比热容值 金属 平均比热容 (KJ/kg℃) 钢 0.3% C 0.700 0.8%C 0.683 1.6%C 0.650 铜 铝
8719738043坯料的电阻和电抗1651241060177105017710502251051072001070277201256105图25计算圆形断面螺旋线圈电感的修正系数曲线2横坐标的值乘101125610509857272098572824771051072001070277209651056坯料的换算系数7坯料的换算电阻0972017710501721052m11741059感应器线圈铜管壁厚0008m根据圆环效应流过感应器中的电流均集中在感应器的内表层可选用靠近坯料一侧为8mm的异形铜管
从图(2-2)我们将PT / P定义为感应器的总效率η,将P2 / P定义为感应器的电效率ηt ,将PT / P2定义为感应器的热效率ηu。 η=PT / P ηt =P2 / P ηu= PT / P2 (2-5) (2-6) (2-7)
即:
式(2-6)乘以式(2-7)则有: ηt ηu = PT / P 可知: η=ηt ηu 从式(2-5)可知: (2-9) (2-8)
中频感
应加
服务 热设备
网专辑
感应加热电流频率、功率、加热时间 的确定与螺线管感应器的参数计算
- 1、下载文档前请自行甄别文档内容的完整性,平台不提供额外的编辑、内容补充、找答案等附加服务。
- 2、"仅部分预览"的文档,不可在线预览部分如存在完整性等问题,可反馈申请退款(可完整预览的文档不适用该条件!)。
- 3、如文档侵犯您的权益,请联系客服反馈,我们会尽快为您处理(人工客服工作时间:9:00-18:30)。
摘要本文以感应加热为研究对象,简要介绍了感应加热的基本原理和特点,阐述了感应加热技术的现状及其发展趋势。
本文主要研究了感应加热器的设计方法。
感应加热器是利用工件中的涡流的焦耳效应将工件加热,这种加热方式具有效率高、控制精确、污染少等特点,在工业生产中得到了广泛的应用。
如何设置感应线圈的参数使之满足被加热工件中性能要求普遍关注的问题。
传统的设计方法是利用线圈在整个电路中的等效电阻地位,利用一系列电磁学公式计算出线圈的性能参数。
然而这种基于实验的系统设计方法却耗时费力,并且测量成本高。
因此,近似模拟方法对于感应加热器的设计和研究具有重要意义。
本文的主要工作是建立感应加热器的近似设计方法。
从感应加热理论的一系列经过实验数据修正过的理论曲线为依据,根据工艺要求得出相关物理参数,并通过计算得到感应器的设计参数。
关键词:第一章绪论1.1 国内外感应加热的发展与现状随着现代科学技术的发展,对机械零件的性能和可靠性要求越来越高,金属零件的性能和质量除材料成分特新外,更与其加热技术密不可分。
例如,加热速度的快慢不仅影响生产效率而且影响产品的氧化程度,局部温度过冷或过热可能导致产品变形甚至损坏等。
由于感应加热具有热效率高,便于控制等优点,目前在金属材料加工,处理等方面得到广泛应用。
在工业发达国家,感应加热研究起步较早,应用也更为广泛。
1890年瑞士技术人员发明了第一台感应熔炼炉——开槽式有芯炉,1916年美国人发明了闭槽式有芯炉,感应加热技术开始进入实用化阶段。
1966年,瑞士和西德开始利用可控硅半导体器件研制感应加热装置。
从此感应加热技术开始飞速发展,并且被广泛用于生产活动中。
在我国,感应加热技术起步比较晚,与世界发达国家相比存在较大的差距。
直到80年代初,感应加热设备才有一定的应用,但因其与其它加热方式相比在节能和无环境污染等方面的显著优势,近几年来得到了长足的发展,已经广泛应用于钢铁、石油、化工、有色金属、汽车、机械、和军工产品的零部件热处理方面,且随着感应加热技术的进一步发展,其市场应用前景将越来越广阔。
金属感应热处理中的加热目标是将金属加热到特定温度分布,比如热轧,不仅要求表面达到一定的温度,而且要求工件加热温度均匀,即工件径向与轴向温差小。
在此特定温度下进行轧制既能保证能源的合理利用,又能使轧制力在正常范围内以方便轧制。
又如在淬火加热中,除了表面温度要求外,对加热层厚度也有不同要求。
所有这些都要求加热功率、加热时间等工艺参数选择合理。
而在实际生产中,生产过程的复杂性以及人工控制的不精确性和随机性,可能就会产生两种不希望出现的情况:一是加热功率过大,加热时间过短。
虽然钢坯的表面温度已达到要求,但钢坯内部却没达到工艺温度分布要求,将会影响后续工艺。
如在轧制过程中,如果钢坯没被加热透,硬度较大,不仅对热成型的成品、半成品的质量造成很大影响,损坏产品信誉,而且会使轧制钢坯的轧锟逐渐产生裂纹,严重缩短轧锟的寿命,导致轧锟仅在短短数月甚至是一个月左右就不能再用。
而轧锟成本一般比较高,会给工厂造成较大的损失;二是加热功率过小,加热时间过长。
这种情况不仅会增加氧化皮含量,而且浪费能源。
在能源价格日益上涨和能源危机日趋严重情况下,应尽可能避免这种现象发生,以节约能源,造福后世。
同时加热时间过长也会降低工厂的生产率,增加产品的成本。
总而言之,加热炉内的加热温度,一方面影响加热炉的能耗和工件烧损,另一方面又影响后续工艺。
将工件温度控制在合理的范围内,既可保证产品的性能,又可使加热炉和后续设备的总能耗最低。
因此,如何在复杂的生产过程中有效地控制加热温度是当前迫切需要解决的问题。
要有效地控制加热温度,其中最关键的是在确定钢坯表面温度的同时,也确定钢坯的芯部温度,然而就目前的测温技术而言,很难用仪器直接测量出被加热钢坯的芯部温度。
目前的做法是热处理完毕之后,在室温状态下通过解剖方法测定组织状态和残留应力分布情况下来进行估算。
这种算法不仅耗费大量人力、物力、和时间,而且所得的仅是某一零件、某一具体工艺条件下的最后情况,很难获得直接推广应用的规律性成果。
故目前感应加热热处理工艺大多数还是建立在定性分析基础上,凭经验制定的,生产力迅速发展要求的高质量、低成本相去甚远。
1.2 感应加热的优点1)加热速度快:用电磁感应加热时,温度上升的速度远比用石油或煤气加热的速度快得多;2)铁屑损耗少:快速加热能有效地降低材料损耗。
而用煤气为燃料的装置,加热速度慢,损耗很大;3)启动快:在有些加热装置中,有很多耐火材料,加热启动时它们吸收热量,即装置的热惯性大。
感应加热不存在这类问题,因而启动快;4)节能:不工作时感应加热电源可以关闭,因为感应加热启动快的特点,而对其他装置来说,由于启动慢,不工作时,也必须维持一定的加热温度;5)生产效率高:由于加热时间短,感应加热可以提高生产效率,降低成本。
除此之外,感应加热还有便于控制、易于实现自动化、减少设备占地面积、工作环境安静、安全、洁净、维护简单等优点。
第二章感应加热基本原理2.1 感应加热原理及主要特点2.1.1 电磁感应与涡流发热感应加热实质是利用电磁感应在导体内产生的涡流发热来加热工件的电加热,它是依靠感应器通过电磁感应把电能传递给被加热的金属,电能在金属内部转变为热能,达到加热金属的目的。
以加热圆柱形工件为例,其原理如图2.1,电流通过线圈产生交变的磁场,当磁场内磁力通过待加热金属工件时,交变的磁力线穿透金属工件形成回路,故在其横截面内产生感应电流,此电流称为涡流,可使待加热工件局部迅速发热,进而达到工业加热的目的。
感应加热基本原理可以用电磁定理和焦耳一楞次定理来描述,电磁感应定理内容为:当穿过任何一闭合回路所限制的面的磁通量随时间发生变化时,在回路上就会产生感应电动势e:dedtφ=-需要加热的金属工件自成回路,在横截面内产生感应电流,此电流称涡流,并用表示fI,其值取决于感应电动势E和涡流回路的阻抗Z:22fLEIZ R X==+式中:E——感应电动势等效值;R——涡流回路内的电阻;LX——涡流回路内的感抗;由于Z值很小,涡流If可以达到很高的数值,在此电流流动时,为克服导体本身的电阻而产生焦耳热,因而能在极短时间里加热工件到很高的温度。
感应电动势使工件导体中产生涡流i,进而产生焦耳热Q。
这一过程可用焦耳一楞次定律表达为:2Q i Rt=(2.3)感应加热的加热过程是电磁感应过程和热传导过程的综合体现,电磁感应过程具有主导作用,它影响并在一定程度上决定着热传导过程。
热传导过程中所需要的热能是由电磁感应过程中所产生的涡流功率提供的。
应当指出,对磁铁材料来讲,除涡流产生热效应外,还有磁滞热效应,但这部分热量比涡流产生的热量小得多,故在以后的讨论中我们将忽略此部分的热量。
2.1.2 集肤效应及透入深度众所周知,直流电流经导体时,电流在导体截面上是均匀分布的,而当给一个圆形断面直导线通以交流电时,这时电流在导体截面上的分布将不再是均匀的,导体表面上各点的电流密度最大,而在导体中心轴线上电流密度最小,由外表面向内层以幂指数规律逐渐递减,这种现象叫做集肤效应,也称表面效应或趋肤效应。
在感应加热中,电源电流是交流电,工件中的感应电流也是交流电流,因此同样具有集肤效应,在此效应作用下,工件中的电流密度分布是不均匀的,以圆柱形工件为例,设表面的电流Io ,沿工件半径方向x 方向的电流密度为:x r D I I e δ-= (2.4)当 x=δ,x D I I e =,即为表面层密度的36.8%,把电流密度为Io/e 的σ层称为电流透入深度。
可以计算出,在σ层中放出的能量为86.5%。
在设计使用时,认为金属被加热的能量先在 层产生,内层金属靠传热传导而被加热。
实际上工件表面σ的地方,电流密度就差不多降到零。
电流透入深度σ可按下式计算:σ式(2.5)中:ρ——工件的电阻率(cm •Ω),一般来说金属的温度越高,其电阻率越大,当温度从0o C 升高到0(850~900)C 时,钢的电阻率增加4~5倍,而且可大致认为,在0(850~900)C温度范围内,各类钢的电阻率几乎相等,约为410cm -•Ω; μ——工件的相对磁导率,真空中和非铁磁性物质其取值1,磁铁性物质在居里点以下时远大于1,居里点以上时接近1;f ——电源频率(Hz ); 由式(2.5)可以看出,电流透入深度取决于电流频率f 、零件材料的电阻率ρ和磁导率μ。
在材料ρ和μ一定时,可以通过调节f 来调节δ,也就是说对于工件的加热厚度可以方便的通过调节电源频率加以控制,频率越高,工件的加热厚度就越薄,这种性质在工业金属热处理方面获得广泛的应用。
需要说明的是,对磁铁物质而言,式2.5表示材料在失磁前的涡流透入深度,称为“冷态的涡流透入深度”,随材料温度的上升,会导致ρ增大和μ下降,从而使涡流分布平缓,透入深度增大。
当温度上升到磁性转变点时,由于其中μ急剧下降,可使涡流透入深度增大几倍至几十倍。
材料在失去磁性后的涡流透入深度称为“热态的涡流透入深度”,对于钢铁材料在0800C 热态时的涡流透入深度δ热可按式2.6求出:δ热2.1.3圆环效应圆环形的导体通过高频(或中频)交变电流时所产生的磁场在环内空间集中,环外分散,见图2.2。
.环内的磁通不仅穿过环外空间,同时也穿过环形导体自身,这样就使环形导体外侧交链的磁通多于内侧,于是环形导体外侧产生较大的感应电动势,迫使电流在环形导体内侧的电流透入深度层中流过,这种现象称为电流的圆环效应或环状效应。
环状效应使感应器上的电流密度集到感应器内侧,对加热零件外表面十分有利,但对加热零件内孔时,此效应使感应器电流远离加热零件表面,是有害的。
如图2.2,在圆环导体中通以交流电时,所产生的磁通在环内空间集中,环外分散,最大电流密度分布在环状导体内侧,这种现象叫环状效应,也叫圆环效应。
圆环效应的实质是环形感应器的临近效应。
图2.2 圆环效应2.1.4 透入式加热和传导式加热当感应线圈刚刚接通电源,工件温度开始明显升高前的瞬间,涡流在零件中的透入深度是符合冷态分布式(2.5)的。
由于越趋近零件表面涡流强度越大,因此表面升温也越快。
当表面出现已超过失磁温度的薄层时,加热层就被拆分成两层:外层的失磁层和与之毗邻的未失磁层。
失磁层内的材料导磁率μ的急剧下降,造成了涡流强度的明显下降,从而使最大的涡流强度出现在失磁层和未失磁层的交界处。
涡流强度分布的变化,使两层交界处的升温速度比表面的升温速度更大,因此使失磁层不断向纵深移动,零件就这样得到逐层而连续的加热,直到热透深度δ为止。
这种加热方式称为透入式加热。
热当失磁的高温层厚度超过热态的涡流透入深度δ后,继续加热时,热量基本上是依靠热在厚度为δ的表层中析出,而在此层内越靠近表面,涡流强度和所得的能量越大。